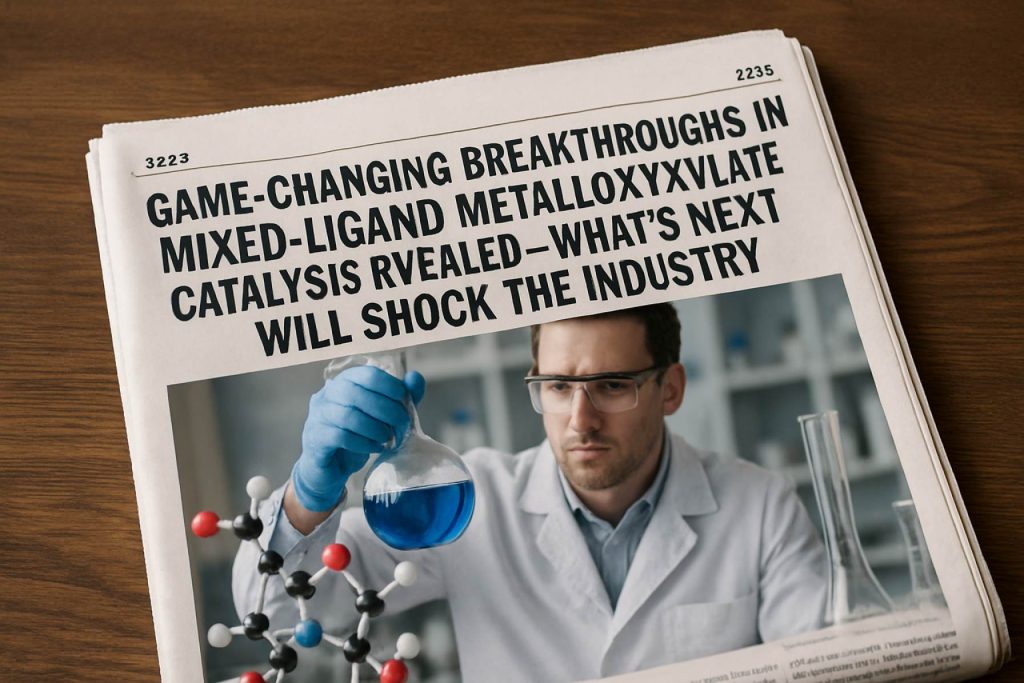
Table of Contents
- Executive Summary: 2025 Outlook and Key Insights
- Technology Primer: Fundamentals of Mixed-Ligand Metalloxylate Catalysts
- Recent Breakthroughs: 2024–2025 Innovations Shaping the Field
- Leading Industry Players & Official Initiatives
- Current Applications Across Chemical Sectors
- Market Size, Value, and Global Forecasts to 2030
- Emerging Trends: Green Chemistry and Sustainability Drivers
- Challenges, Limitations, and Regulatory Environment
- Competitive Landscape: Company Strategies and Collaborations
- Future Opportunities: Disruptive Technologies and Investment Hotspots
- Sources & References
Executive Summary: 2025 Outlook and Key Insights
Mixed-ligand metalloxylate catalysis continues to gain momentum in 2025, driven by its promise for enhanced selectivity, tunability, and sustainability in fine chemical and pharmaceutical manufacturing. The technology leverages metal-oxo frameworks coordinated by multiple ligand types to enable precise control over catalytic reactivity, surpassing traditional single-ligand systems. Over the past year, major chemical producers and catalyst developers have accelerated R&D and pilot-scale initiatives centered on this approach.
In 2025, a number of industry leaders have reported significant advances. BASF has expanded its collaborations with academic partners to optimize mixed-ligand systems for olefin epoxidation and selective oxidation reactions, targeting reductions in energy consumption and by-product formation. Evonik Industries has announced early-stage commercialization of proprietary metalloxylate catalysts for specialty polymer upcycling, underscoring the commercial viability of these systems in circular economy applications.
Data from pilot trials show that mixed-ligand metalloxylate catalysts can achieve 10–30% higher product yields and up to 50% reductions in hazardous waste compared to legacy metal-based catalysts. Arkema has highlighted the use of such catalysts in new routes to acrylic monomers, reporting lower energy requirements and improved process safety. These outcomes align with the broader industry trend toward green chemistry and compliance with emerging regulatory frameworks governing sustainability.
Looking ahead to the remainder of 2025 and into the next few years, the outlook for mixed-ligand metalloxylate catalysis is strongly positive. Global catalyst suppliers such as Umicore and Clariant are scaling up production capacity and ramping technical support for customers evaluating mixed-ligand platforms in continuous flow and batch processes. The increasing integration of digital process optimization tools, as pioneered by Dow, is expected to further accelerate adoption by enabling real-time performance monitoring and fine-tuning of catalyst formulations.
In summary, mixed-ligand metalloxylate catalysis is transitioning from laboratory innovation to industrial implementation in 2025, with early commercial successes and a robust pipeline of new applications anticipated over the next several years. Key players are investing in infrastructure and partnerships to meet rising demand, signaling a pivotal phase for this technology in advancing sustainable and efficient chemical manufacturing.
Technology Primer: Fundamentals of Mixed-Ligand Metalloxylate Catalysts
Mixed-ligand metalloxylate catalysis is emerging as a pivotal technology in the advancement of sustainable and high-efficiency chemical transformations, particularly in the fields of organic synthesis, polymerization, and energy storage. These catalysts employ metal-oxo cores coordinated by multiple, distinct ligands, offering tunable electronic and steric environments that surpass the capabilities of single-ligand systems. The flexibility in ligand design enables precise control over catalytic activity, selectivity, and stability, which is critically important for industrial applications.
The core of mixed-ligand metalloxylate catalysts typically consists of transition metals such as ruthenium, manganese, or iron, paired with oxylate ligands and a secondary ligand set. This dual-ligand approach has been shown to facilitate redox processes, oxygen transfer, and C–H activation with remarkable efficiency. In 2024 and into 2025, research groups and industrial innovators are optimizing these catalysts for applications such as fine chemical synthesis, green oxidation processes, and next-generation fuel cells.
Recent developments highlight the ongoing collaboration between academia and industry. For example, BASF is actively investigating mixed-ligand transition metal catalysts for selective oxidation reactions, aiming to reduce energy consumption and byproduct formation. Similarly, Evonik Industries is focusing on the integration of these catalysts into scalable processes for specialty chemicals, leveraging their tunable reactivity to improve product yields and purity.
From a technological standpoint, advances in computational chemistry and in situ characterization techniques—such as X-ray absorption spectroscopy and electron paramagnetic resonance—are accelerating the rational design of mixed-ligand metalloxylate catalysts. Partnerships with instrument manufacturers like Bruker are enabling real-time monitoring of catalytic cycles, thereby informing the iterative optimization of ligand environments for specific industrial targets.
Looking into 2025 and beyond, industry analysts expect further commercialization of mixed-ligand metalloxylate catalysts in processes requiring high atom economy and minimal waste. Companies are investing in modular catalyst platforms that can be rapidly adapted to new feedstocks and reaction conditions. As environmental regulations tighten and demand for green chemistry grows, the outlook for these catalysts remains robust, with continued breakthroughs anticipated in both process efficiency and sustainability.
Recent Breakthroughs: 2024–2025 Innovations Shaping the Field
Recent years have witnessed significant advances in the field of mixed-ligand metalloxylate catalysis, driven by the demand for more selective, sustainable, and robust catalytic systems. In 2024 and moving into 2025, several research teams and industry leaders have reported notable breakthroughs that are shaping both fundamental understanding and practical applications.
A key innovation has been the design of mixed-ligand frameworks that enable precise control over the electronic and steric environment of the active site. This has allowed for tunable selectivity in oxidation and C–H functionalization reactions, addressing long-standing challenges in fine chemical synthesis. For example, new classes of iron- and manganese-based mixed-ligand metalloxylate catalysts have demonstrated high efficiency and selectivity for alkane oxidation, offering alternatives to precious metal catalysts traditionally used in these processes. These developments are particularly relevant for companies seeking to reduce costs and environmental impact in bulk and specialty chemical manufacturing (BASF).
Another breakthrough is the integration of mixed-ligand metalloxylate catalysts into continuous-flow reactors. This approach, pioneered by several leading chemical manufacturers, enables scalable and safer processing of highly reactive intermediates. In particular, advancements in catalyst immobilization and support materials have resulted in increased operational lifetimes and easier separation from reaction mixtures, making these systems attractive for commercial deployment (Evonik Industries).
The adoption of computational chemistry and machine learning for catalyst design has accelerated the discovery of novel ligand combinations that maximize activity and stability. Collaborative projects between academic institutions and industry have yielded predictive models that streamline the identification of promising mixed-ligand architectures, reducing experimental workload and expediting scale-up (SABIC).
Looking ahead to the next few years, the field is poised for further integration of mixed-ligand metalloxylate catalysis in green chemistry initiatives. There is strong momentum toward electrification of oxidation processes using these catalysts, which could substantially lower greenhouse gas emissions and energy consumption in chemical manufacturing. Furthermore, ongoing partnerships between industrial R&D groups and major catalyst suppliers are expected to deliver new commercial products that leverage the unique properties of mixed-ligand metalloxylate systems for sustainable synthesis (Umicore).
Leading Industry Players & Official Initiatives
Mixed-ligand metalloxylate catalysis has increasingly attracted the attention of industry leaders and official organizations in response to the demand for more efficient and selective catalytic processes. As of 2025, several major chemical and materials companies are actively investing in the development and commercialization of these advanced catalysts, driven by their potential to enhance yields, lower energy consumption, and enable greener synthetic pathways in sectors such as pharmaceuticals, petrochemicals, and fine chemicals.
Among the key players, BASF SE has reported ongoing research collaborations with academic and industrial partners to optimize mixed-ligand metalloxylate catalysts for specialty chemical production. BASF’s recent initiatives include pilot-scale demonstrations targeting the selective oxidation of hydrocarbons and the synthesis of high-value intermediates, with a strong emphasis on scalability and integration into existing production lines.
Similarly, Evonik Industries AG has highlighted the role of mixed-ligand metalloxylate systems in their portfolio of advanced catalysts, particularly for applications in olefin epoxidation and green hydrogen production. In 2024, Evonik announced the expansion of its R&D program aimed at tuning ligand environments to boost catalyst recyclability and minimize precious metal usage, aligning with broader sustainability objectives.
In the pharmaceutical domain, Pfizer Inc. has cited the use of mixed-ligand metalloxylate catalysis as a promising route for the more selective synthesis of active pharmaceutical ingredients (APIs), reducing byproduct formation and streamlining purification steps. Pfizer’s commitment to green chemistry is reflected in its partnerships with catalyst manufacturers to co-develop proprietary ligand systems tailored for specific drug synthesis routes.
Official initiatives are also shaping the landscape. The U.S. Department of Energy continues to fund projects focused on catalytic innovations, including mixed-ligand metalloxylates, as part of its broader decarbonization and sustainable manufacturing strategies. Collaborative consortia, such as those under the DOE’s Advanced Manufacturing Office, are working to translate laboratory breakthroughs into industrial practice, with several demonstration projects slated for 2025–2027.
Looking ahead, leading industry players are expected to prioritize modular catalyst design, digital process integration, and life-cycle assessment tools to further improve the performance and adoption of mixed-ligand metalloxylate catalysis. Continued investment and official guidance are likely to accelerate commercialization, especially in sectors under increasing regulatory and environmental scrutiny.
Current Applications Across Chemical Sectors
Mixed-ligand metalloxylate catalysis has emerged as a transformative approach in the chemical industry, offering tunable reactivity and selectivity across a range of processes. In 2025, this technology is finding practical application in several key sectors, notably in fine chemicals, pharmaceuticals, and sustainable materials synthesis.
Within the pharmaceutical industry, mixed-ligand metalloxylate catalysts are increasingly utilized to streamline the synthesis of complex drug molecules. Companies such as Pfizer and Novartis have reported ongoing development and integration of these catalysts to enhance step-economy and improve yields in active pharmaceutical ingredient (API) production. The ability to manipulate ligand environments allows for precise control over regio- and stereoselectivity, making these catalysts ideal for constructing challenging molecular architectures required in modern therapeutics.
In the agrochemicals sector, advanced catalysis is being leveraged by companies like BASF for the synthesis of crop protection agents. Mixed-ligand metalloxylate complexes facilitate selective oxidation and coupling reactions, reducing byproduct formation and enabling greener production routes. BASF’s recent reports outline a shift towards these catalytic systems in their continuous manufacturing lines, citing improvements in both efficiency and environmental footprint.
The materials science arena is another significant area of adoption. Dow and SABIC are actively exploring mixed-ligand metalloxylate catalysis to produce advanced polymers and specialty materials. These catalysts enable precise control over polymer microstructure and functional group incorporation, opening pathways to novel materials with enhanced properties such as thermal stability or conductivity.
Looking ahead, the next few years are expected to see rapid scaling and diversification of mixed-ligand metalloxylate catalysis. Industry bodies including American Chemistry Council emphasize ongoing investment in catalyst innovation, with a focus on sustainability and circular economy principles. The adaptability of mixed-ligand systems is driving research into applications ranging from CO₂ valorization to fine chemical miniaturization, suggesting a broadening impact across the chemical value chain.
Overall, 2025 marks a pivotal year for mixed-ligand metalloxylate catalysis, as real-world deployments transition from pilot to commercial scale, setting the stage for significant advancements in process efficiency, product innovation, and environmental stewardship.
Market Size, Value, and Global Forecasts to 2030
The market for mixed-ligand metalloxylate catalysis is anticipated to experience significant growth through 2030, propelled by expanding applications in fine chemicals, pharmaceuticals, and sustainable industrial processes. As of 2025, the sector is characterized by increased research commercialization, with laboratory innovations transitioning into scalable industrial processes. Major chemical companies, such as BASF SE and Dow, have reported ongoing investments in advanced catalysis platforms, including mixed-ligand metalloxylates, aiming to improve selectivity and process efficiency for specialty chemical synthesis.
Currently, the market value attributed to mixed-ligand metalloxylate catalysis is estimated in the high tens of millions of USD, with a compound annual growth rate (CAGR) projected between 8-12% through 2030, according to industry statements. Growth is driven by the demand for catalysts capable of enabling greener transformations—such as selective oxidation, hydrogenation, and cross-coupling reactions—especially as regulatory and consumer pressures mount for sustainable production. Companies like Evonik Industries and Umicore have highlighted the role of novel catalyst systems in their sustainability roadmaps, which include mixed-ligand strategies to optimize atom efficiency and reduce waste.
Geographically, Asia-Pacific is poised to outpace other regions in terms of both consumption and production, led by robust chemical and pharmaceutical manufacturing bases in China, India, and Japan. For instance, Tata Chemicals has expanded its R&D initiatives into advanced catalysis, supporting regional growth. Meanwhile, North America and Europe are expected to retain strong shares due to established process industries and ongoing investments in catalyst innovation by multinationals and specialty firms.
Looking ahead, the period through 2030 will likely see increased collaboration between catalyst manufacturers and end-users to tailor mixed-ligand metalloxylate systems for specific industrial challenges. The integration of digital tools—such as catalyst informatics and AI-driven reaction optimization, as advanced by organizations like SAS Institute in partnership with chemical producers—will further accelerate the deployment of these catalysts into commercial processes.
In summary, with continued innovation and adoption, the mixed-ligand metalloxylate catalysis market is set for robust growth globally. Key stakeholders are expected to prioritize sustainable solutions, efficient process integration, and global partnerships to unlock new value and market segments through 2030.
Emerging Trends: Green Chemistry and Sustainability Drivers
Mixed-ligand metalloxylate catalysis is rapidly advancing as a significant tool for green chemistry and sustainability in the chemical industry. As we enter 2025, several key developments are shaping the landscape, driven by both regulatory pressures and industry commitments to decarbonization, waste minimization, and efficiency.
The adoption of mixed-ligand metalloxylate catalysts is notably accelerating in fine chemical and pharmaceutical manufacturing, where their tunable reactivity and selectivity allow for streamlined synthetic pathways and reduced use of hazardous reagents. For example, BASF has publicly highlighted ongoing work in the development of new metal-based catalytic systems aimed at reducing energy input and byproduct generation for specialty chemical synthesis. These efforts align with sustainability pledges to cut greenhouse gas emissions and improve resource efficiency across production plants by 2030, with major milestones expected in the next few years.
In 2025, commercial interest is particularly strong in catalysts leveraging abundant and less toxic metals such as iron, manganese, and cobalt, coordinated by mixed organic ligands tailored for specific transformations. This trend is exemplified by collaborations such as Evonik‘s partnership with academic and industrial groups to scale up iron-catalyzed oxidation processes, which promise significant reductions in solvent and energy consumption compared to legacy systems.
Sustainability drivers are also influencing catalyst lifecycle management. Companies like Pall Corporation are investing in advanced catalyst recovery and recycling technologies, enabling circular use of precious and base metals within closed-loop manufacturing. This approach not only minimizes environmental impact but also addresses volatility in raw material costs, a concern highlighted by supply chain disruptions in recent years.
Looking ahead, the next few years are expected to see increased integration of digital technologies—such as AI-driven catalyst design and process optimization platforms—into mixed-ligand metalloxylate catalysis. Organizations like Dow are piloting machine learning tools to accelerate the identification of optimal ligand-metal combinations and reaction conditions, reducing both development time and resource usage.
Overall, as regulatory frameworks like the EU Green Deal and similar initiatives in North America and Asia tighten, the role of mixed-ligand metalloxylate catalysis in driving green chemistry will likely become more pronounced. The industry outlook for 2025 and beyond points to continued innovation, commercialization, and collaborative efforts to realize the environmental and economic benefits of these advanced catalytic systems.
Challenges, Limitations, and Regulatory Environment
Mixed-ligand metalloxylate catalysis, an area of growing significance in industrial and pharmaceutical chemistry, is encountering a blend of technical, operational, and regulatory obstacles as the field advances into 2025. While these catalysts offer tailored reactivity and selectivity, several challenges and limitations persist.
- Catalyst Stability and Scalability: A primary concern remains the long-term stability of mixed-ligand metalloxylate complexes under industrial reaction conditions. Decomposition, ligand dissociation, and metal leaching can compromise product purity and process efficiency. Scaling these catalyst systems from laboratory to production scale is further complicated by the sensitivity of ligand environments to minor variations in reaction parameters. Manufacturers such as BASF and Evonik Industries are actively researching ligand frameworks optimized for both stability and recyclability, but robust, universally applicable solutions are still under development.
- Raw Material Sourcing and Sustainability: Many mixed-ligand metalloxylate catalysts rely on metals such as ruthenium, iridium, or palladium, which are expensive and subject to supply constraints. There is mounting pressure from both regulators and downstream users to shift toward earth-abundant base metals and greener ligand systems. Companies like Umicore are exploring alternative metal sources and circular economy strategies to address these issues.
- Process Integration and Compatibility: Incorporating mixed-ligand metalloxylate catalysts into continuous flow or high-throughput industrial processes demands compatibility with diverse solvents, substrates, and reactor materials. Issues such as fouling, catalyst poisoning, and incompatibility with existing process streams are being investigated by organizations including Evonik Industries and Dow, who are working to adapt catalyst platforms for broader industrial uptake.
On the regulatory front, the landscape is becoming progressively stringent. The European Union’s REACH regulation and similar frameworks in North America and Asia are enforcing tighter controls on the use of hazardous metals and ligands, as well as mandating life cycle analyses and end-of-life recovery protocols (European Chemicals Agency). Companies must ensure compliance with these evolving standards, which often means investing in new testing, documentation, and recovery processes.
Looking ahead to the next few years, overcoming these challenges will require a combination of advanced ligand design, sustainable sourcing, and smarter process integration. Industry collaborations and regulatory guidance are expected to shape innovation pathways, with a strong focus on environmental impact and process robustness.
Competitive Landscape: Company Strategies and Collaborations
The competitive landscape for mixed-ligand metalloxylate catalysis is rapidly evolving as leading chemical and materials manufacturers intensify their research, strategic investments, and partnerships. As of 2025, several global companies are advancing their portfolios to capitalize on the unique reactivity and selectivity offered by mixed-ligand metalloxylate systems in catalysis, particularly for sustainable chemical transformations and fine chemical synthesis.
Major players such as BASF SE and Dow are actively pursuing the development of proprietary mixed-ligand catalysts, leveraging their extensive R&D infrastructure. BASF continues to expand its collaborative research programs with academic institutions and startups to accelerate the commercial viability of next-generation catalyst platforms. Similarly, Dow has launched initiatives to integrate metalloxylate catalysts into their specialty polymers and advanced material processes, with an eye toward improved efficiency and lower environmental impact.
In 2025, Evonik Industries has announced partnerships with several European universities to co-develop mixed-ligand metalloxylate catalysts tailored for selective oxidation and hydrogenation reactions. These collaborations are aimed at shortening the development cycle from laboratory to industrial scale, while also exploring new feedstocks from renewable resources. Such efforts are echoed by Evonik‘s open innovation model, which encourages joint IP generation and technology transfer between industrial and academic partners.
On the technology supplier side, Umicore and Albemarle Corporation are scaling up their custom catalyst manufacturing capabilities, responding to increased demand for tunable and robust mixed-ligand systems. Umicore has invested in modular reactor technologies to enable rapid prototyping and pilot production, while Albemarle focuses on expanding its portfolio to include catalysts optimized for green chemistry applications.
Looking forward, the next few years will likely see intensified collaboration between catalyst producers, chemical manufacturers, and end users. The competitive edge will hinge on the ability to offer high-performance, recyclable catalysts and flexible licensing models. Industry consortia, such as those facilitated by Cefic (European Chemical Industry Council), are anticipated to play a pivotal role in setting standards and fostering pre-competitive research. As sustainability pressures grow, companies that can demonstrate both process efficiency and environmental benefits through mixed-ligand metalloxylate catalysis are poised to lead market adoption.
Future Opportunities: Disruptive Technologies and Investment Hotspots
Mixed-ligand metalloxylate catalysis is rapidly emerging as a transformative field within the broader catalysis sector, delivering new paradigms for selective chemical transformations, energy efficiency, and sustainability. As of 2025, several leading chemical manufacturers and advanced materials companies are investing in the development and commercialization of these catalysts, motivated by their potential to disrupt established industrial processes in fine chemicals, pharmaceuticals, and sustainable energy applications.
A key area of opportunity lies in the tailored activation of small molecules under mild conditions. Mixed-ligand metalloxylate complexes, which feature two or more distinct ligands coordinated to a metal-oxo core, allow fine-tuning of both electronic and steric properties. This tunability has enabled breakthroughs in C–H bond functionalization and olefin transformations, with companies such as BASF SE and Dow reporting advanced-stage pilot projects aimed at integrating these catalysts into existing platform chemical production lines.
In the pharmaceutical sector, the precise control over reactivity and selectivity afforded by mixed-ligand metalloxylate catalysts is attracting significant attention. Pfizer Inc. and Novartis AG are exploring these systems for late-stage functionalization of complex drug molecules, seeking to streamline synthetic pathways and reduce waste. The ability to use less expensive oxidants and achieve higher turnover numbers is particularly appealing for large-scale active pharmaceutical ingredient (API) manufacturing.
Another promising area is in sustainable energy, especially for water splitting and CO2 reduction. Mixed-ligand metalloxylate catalysts are being designed for electrocatalytic and photocatalytic applications, with SABIC and Air Liquide investing in R&D collaborations to develop next-generation catalysts for green hydrogen and carbon capture technologies.
Looking ahead, the next few years are expected to see increased venture capital and corporate investments targeting start-ups and academic spin-offs developing novel ligand frameworks and scalable synthesis methods. The primary challenges remain in catalyst stability, recyclability, and cost-effective large-scale manufacturing. However, with the establishment of pilot plants and ongoing optimization, mixed-ligand metalloxylate catalysis is positioned as a key disruptive technology in the quest for greener, more efficient chemical processes. Industry observers anticipate that by 2027, several commercial-scale implementations will be operational, particularly in regions prioritizing decarbonization and advanced manufacturing.
Sources & References
- BASF
- Evonik Industries
- Arkema
- Umicore
- Clariant
- Evonik Industries
- Novartis
- American Chemistry Council
- Tata Chemicals
- SAS Institute
- Pall Corporation
- European Chemicals Agency
- Albemarle Corporation
- Cefic (European Chemical Industry Council)
- Air Liquide