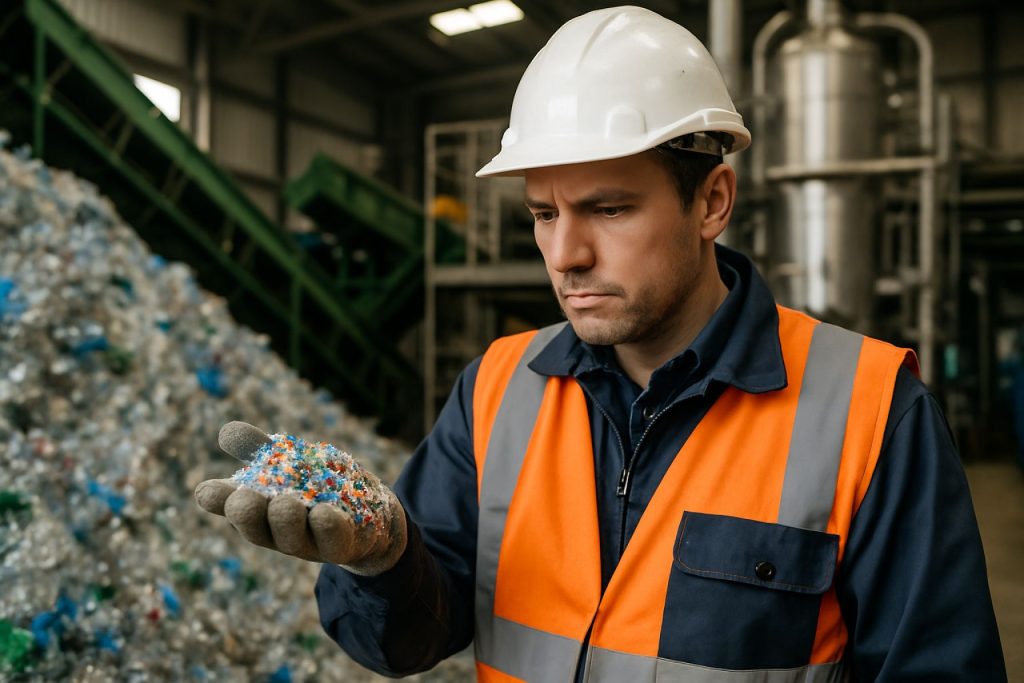
Table of Contents
- Executive Summary: The 2025 Landscape of Solvolysis-Based Polymer Recycling
- Market Size and Forecast: Growth Projections to 2030
- Key Companies and Industry Initiatives: Leaders and Innovators
- Solvolysis Technologies Explained: Chemistry and Process Advances
- Comparison With Alternative Polymer Recycling Methods
- Commercial Scale Deployments: Case Studies and Best Practices
- Policy, Regulation, and Industry Standards Impacting Solvolysis
- Sustainability Metrics and Environmental Impact Assessment
- Investment Trends, Funding, and M&A Activity
- Future Outlook: Challenges, Opportunities, and Next-Gen Innovations
- Sources & References
Executive Summary: The 2025 Landscape of Solvolysis-Based Polymer Recycling
Solvolysis-based polymer recycling technologies are positioned at the forefront of sustainable materials management as 2025 unfolds, responding to mounting global mandates for circularity in plastics. Solvolysis—encompassing processes such as glycolysis, methanolysis, and hydrolysis—breaks down condensation polymers (notably PET, polyamides, and polycarbonates) into their monomeric or oligomeric building blocks. This enables the production of high-quality recycled polymers, often indistinguishable from virgin material. With the European Union’s Packaging and Packaging Waste Regulation and similar policies worldwide setting ambitious recycled content targets, industrial interest and investment have accelerated.
Several companies have scaled or are commissioning commercial solvolysis plants in 2025, reflecting a shift from pilot to industrial production. Eastman Chemical Company is ramping up its polyester renewal technology, with its Kingsport, Tennessee facility targeting a 110,000 ton annual capacity and additional plants under development in France and the U.S. Loop Industries is progressing with its depolymerization plants in North America and Europe, leveraging methanolysis for PET recycling and partnering with global brands for feedstock supply and offtake agreements. Meanwhile, Carbios has inaugurated its first industrial-scale enzymatic PET recycling plant, parallel to its chemical recycling demonstrations, signaling the diversification of solvolytic approaches.
Across Asia, Subaru Chemical and other regional players are advancing glycolysis-based PET recycling, with new facilities slated to come online in late 2025. Japan and South Korea are actively supporting such technologies as part of national plastic resource strategies.
Key challenges for solvolysis in 2025 remain: feedstock purity requirements, cost-competitiveness relative to mechanical recycling, and the need for robust logistics to aggregate suitable waste streams. However, the technology’s capacity to upcycle colored, multilayer, or contaminated plastics—problematic for traditional methods—augurs well for its role in a circular economy. The sector is responding by integrating AI-based feedstock sorting, expanding pretreatment capacity, and partnering with consumer brands to secure long-term supply.
Looking ahead, solvolysis-based recycling is forecast to see double-digit annual growth through 2027, with increasing adoption in Europe, North America, and Asia-Pacific. As leading producers like Eastman Chemical Company, Loop Industries, and Carbios demonstrate scalable, economically viable operations, solvolysis is poised to become a core pillar in the global transition to circular plastics in the immediate years ahead.
Market Size and Forecast: Growth Projections to 2030
Solvolysis-based polymer recycling technologies are gaining increasing prominence as industry and regulators worldwide push for scalable solutions to deal with the mounting challenge of plastic waste. As of 2025, the global market for solvolysis-based recycling is in a critical growth phase, bolstered by advancements in chemical depolymerization processes and significant investment from both established chemical producers and innovative start-ups.
The market size for solvolysis-based recycling is anticipated to surpass several hundred million USD in 2025, with expectations for accelerated growth through 2030 as commercial-scale plants come online and regulatory incentives solidify. Companies such as Eastman, Indorama Ventures, and Loop Industries are actively deploying glycolysis, methanolysis, and hydrolysis plants targeting PET and other condensation polymers. For instance, Eastman is investing over $1 billion in a large-scale molecular recycling facility in the United States, with operational launch expected in 2026 and a processing capacity of ~110,000 metric tons per year.
In Europe, Indorama Ventures has ongoing projects to expand PET chemical recycling, with new facilities in France and plans for further expansion across the continent by 2027. These industrial-scale initiatives are expected to catalyze regional market growth, particularly as the European Union intensifies mandates for recycled content in packaging and single-use plastics.
Further, Loop Industries has announced commercial agreements with global brands and is ramping up capacity at its facilities in North America and Europe. With its proprietary methanolysis process, the company aims to produce food-grade recycled PET at scale, with expansion plans through 2030.
The outlook for solvolysis-based recycling technologies to 2030 is robust, with projected compound annual growth rates (CAGR) in the high double digits as new regulatory targets—such as the EU’s 25% recycled content requirement for PET bottles by 2025 and 30% by 2030—drive demand. The entrance of additional players, such as Carbios, which is constructing a first-of-its-kind enzymatic PET recycling plant in France, further underlines the sector’s momentum. Collectively, these developments position solvolysis-based recycling as a pivotal technology in the circular plastics economy, with market size expected to multiply several-fold by 2030 as commercial viability and supply chain integration mature.
Key Companies and Industry Initiatives: Leaders and Innovators
Solvolysis-based polymer recycling technologies, which employ chemical solvents to depolymerize plastics into their monomeric or oligomeric building blocks, are rapidly advancing from pilot-scale demonstration to commercial deployment in 2025. This shift is driven by mounting regulatory pressures, brand-owner commitments to circularity, and the technical limitations of purely mechanical recycling, particularly for challenging polymers such as polyethylene terephthalate (PET), polyamide (PA), and polyurethane (PU).
Several prominent companies are leading the commercialization of solvolysis processes. Eastman has emerged as a global front-runner, investing more than $2 billion in large-scale depolymerization facilities in the United States and France. Their polyester renewal technology utilizes methanolysis to break down PET waste—including colored, multilayer, and post-consumer textiles—into its monomers, which are then purified and repolymerized into virgin-quality plastics. By 2025, Eastman’s Kingsport, Tennessee plant is slated to reach full capacity, processing up to 110,000 metric tons of plastic waste annually, with the planned Normandy, France facility expected to add substantial European capacity in the following years.
Another major player, Loop Industries, utilizes a proprietary low-energy, no-pressure depolymerization process for PET and polyester fibers, targeting applications in food-grade packaging and textiles. Loop’s joint venture with SUEZ in France is anticipated to begin commercial operations in the near term, aiming to process tens of thousands of tons per year and supply recycled monomers to major consumer brands.
Carbios is pioneering enzymatic solvolysis, using engineered enzymes to selectively depolymerize PET under mild conditions. The company’s demonstration plant in Clermont-Ferrand, France, has validated the scalability of the process, and Carbios is collaborating with leading brands to accelerate adoption. Their first industrial-scale facility, developed in partnership with Indorama Ventures, is scheduled to commence operations in 2025, with an initial annual capacity of 50,000 tons.
Looking beyond PET, companies such as DuPont and BASF are exploring solvolysis for polyamide and polyurethane recycling, targeting high-value applications in automotive and electronics. Industry consortia and public-private partnerships are also proliferating to accelerate the industrialization of solvolysis routes and address supply chain, feedstock, and regulatory challenges.
The next few years are expected to see rapid capacity ramp-up, broader polymer scope, and increasing integration of solvolysis into brand-owner and packaging strategies, reinforcing its status as a critical pillar of the emerging circular plastics economy.
Solvolysis Technologies Explained: Chemistry and Process Advances
Solvolysis-based polymer recycling technologies leverage chemical reactions between polymers and solvents—such as water, alcohols, or glycols—to break down plastic waste into valuable monomers or intermediates. Unlike mechanical recycling, which often downgrades material properties, solvolysis offers the potential to recover high-purity raw materials suitable for remanufacture into virgin-quality plastics. Over the past year and into 2025, solvolysis processes have attracted significant attention for their potential to address hard-to-recycle streams, particularly PET (polyethylene terephthalate), polycarbonate, and polyamides.
The core chemistry involves depolymerization via hydrolysis, glycolysis, methanolysis, or aminolysis, depending on the polymer and desired output. For PET, glycolysis is a leading approach: ethylene glycol reacts with PET to yield bis(2-hydroxyethyl) terephthalate (BHET), which can be purified and repolymerized. Methanolysis, using methanol as a reagent, produces dimethyl terephthalate (DMT) and ethylene glycol. Process optimization in 2024–2025 is focused on improving reaction selectivity, reducing catalyst loadings, and lowering energy requirements, with several companies scaling up their proprietary technologies.
Among notable industry players, Eastman has advanced its methanolysis-based “carbon renewal” and “polyester renewal” technologies. The company announced in late 2023 the progress of its molecular recycling facility in Tennessee, targeting a 2025 commissioning date with a capacity to process over 100,000 metric tons of waste annually. This facility is designed to chemically recycle complex polyester-rich streams that are challenging for mechanical methods, converting them back to monomers for use in specialty plastics and fibers.
Similarly, Loop Industries has developed a proprietary low-temperature, low-pressure depolymerization process for PET and polyester fiber waste. In partnership with major consumer brands, Loop’s commercial facility in Canada is expected to be fully operational by 2025, aiming for high yields of recycled monomers with minimal impurities, suitable for food-grade packaging applications.
Europe is also seeing significant activity. Carbios is scaling its enzymatic hydrolysis process—a form of solvolysis using biocatalysts—to industrial scale, with a goal of commissioning a demonstration plant in 2025. Their technology selectively depolymerizes PET into its monomers, terephthalic acid and ethylene glycol, under mild conditions, demonstrating high conversion rates and the ability to process opaque or colored PET streams.
Looking ahead, solvolysis technologies are expected to play a growing role in global plastic recycling infrastructure. Continued advances in catalyst development, process integration, and feedstock flexibility will be crucial for commercial viability. As regulatory pressure mounts and brand owners push for recycled content, the coming years will likely see increased investment and deployment of solvolysis-based solutions, moving them from pilot to industrial scale.
Comparison With Alternative Polymer Recycling Methods
Solvolysis-based polymer recycling technologies—where polymers are depolymerized using chemical solvents—have gained significant momentum as a promising solution for chemical recycling, particularly for polyesters such as PET and polyamides. Compared to traditional mechanical recycling, solvolysis offers the advantage of restoring polymers to their monomeric building blocks, enabling the production of high-purity, virgin-quality plastics even from post-consumer and contaminated waste streams. As of 2025, several commercial-scale projects and pilot facilities are operational or under development, reflecting the sector’s rapid maturation.
In comparison, mechanical recycling remains the most widely implemented method for polymer waste, leveraging established infrastructure, relatively low energy requirements, and cost-effectiveness. However, mechanical recycling is limited by feedstock contamination, polymer degradation, and downcycling, resulting in lower material quality with each recycling cycle. In contrast, solvolysis avoids these issues by chemically breaking down polymers, which facilitates closed-loop recycling. For example, polyethylene terephthalate (PET) solvolysis allows for the recovery of purified terephthalic acid and ethylene glycol, which can be repolymerized into high-quality PET suitable for food-contact applications.
Alternative chemical recycling methods, such as pyrolysis and gasification, differ substantially from solvolysis. Pyrolysis involves high-temperature thermal decomposition in the absence of oxygen, primarily converting polyolefins (like PE and PP) into fuels or chemical feedstocks. While this broadens the types of plastics that can be addressed, pyrolysis typically produces hydrocarbon mixtures rather than monomeric products, and energy consumption is considerably higher. Gasification, on the other hand, generates synthesis gas (syngas) from mixed plastic waste but faces similar challenges regarding energy intensity and product specificity.
Solvolysis-based processes, such as those commercialized by Carbios and Loop Industries, are notable for their selectivity and scalability. Both companies are advancing enzymatic and chemical depolymerization technologies for PET, with Carbios operating a demonstration plant and Loop Industries partnering with major consumer brands to scale up production. Additionally, Evonik Industries is investing in solvolysis routes for polyamide recycling, further diversifying the polymers addressed by this technology.
Looking ahead to the next few years, solvolysis is expected to complement existing recycling strategies rather than replace them outright. Its ability to process contaminated and colored waste streams, and to deliver food-grade output, positions it as a crucial part of the circular economy for plastics. The outlook for 2025 and beyond includes increased integration with sorting and pre-treatment infrastructure, scale-up to commercial production, and broader application to new resin types, helping industry stakeholders address both quality and sustainability challenges in polymer recycling.
Commercial Scale Deployments: Case Studies and Best Practices
Solvolysis-based recycling technologies have transitioned from pilot-scale demonstrations to commercial-scale deployments, particularly over the past two years. As of 2025, these processes—using solvents (often alcohols or glycols) to depolymerize plastics such as polyethylene terephthalate (PET) and polycarbonate—are being adopted by leading materials and chemical companies seeking higher yields, improved feedstock flexibility, and lower carbon footprints compared to traditional mechanical recycling.
A notable example is the commercial operation of PET chemical recycling facilities leveraging glycolysis and methanolysis. Loop Industries has established a large-scale PET upcycling plant in Canada, using its proprietary low-energy, low-pressure depolymerization process. The facility targets an annual output exceeding 70,000 metric tons of recycled PET resin, with expansion plans aligned to rising demand from global consumer brands. The company has secured agreements with major beverage and packaging producers, highlighting growing confidence in solvolysis-derived rPET for food-grade applications.
In Europe, Carbios has advanced its enzymatic solvolysis process and, by 2025, is commissioning its first industrial-scale facility in France. This plant is designed to recycle over 50,000 tons of post-consumer PET waste annually, using enzymes in aqueous solution to depolymerize PET into monomers. Carbios’s partnerships with multinational brands in textiles and packaging underscore the viability of solvolysis for closed-loop recycling.
Meanwhile, Eastman has invested over $250 million to build a commercial-scale polyester renewal facility in the United States. Utilizing methanolysis, Eastman’s plant is expected to process approximately 110,000 metric tons of hard-to-recycle polyester waste per year. The company reports that its process can handle mixed-color and contaminated waste, expanding the range of acceptable feedstock and enhancing circularity for polyester products.
Best practices emerging from these deployments include robust feedstock pre-sorting to optimize process efficiency, strategic offtake partnerships with downstream converters and brand owners, and integration of renewable energy to further lower lifecycle emissions. Companies are also prioritizing process transparency and certification, with several pursuing third-party verification of recycled content and environmental performance.
Looking ahead, these commercial-scale operations are expected to inform the next generation of solvolysis technologies, with further scale-up anticipated in North America, Europe, and Asia by 2027. The entry of new players and cross-sector collaborations signal an accelerating shift toward solvolysis as a mainstream solution for high-quality polymer recycling, positioning the technology as a critical enabler in global efforts to reduce plastic waste and foster a circular economy.
Policy, Regulation, and Industry Standards Impacting Solvolysis
As solvolysis-based polymer recycling technologies progress from pilot to commercial scale, policy frameworks and industry standards are increasingly shaping their deployment and market viability. In 2025, regulatory attention is intensifying around advanced recycling, including solvolysis, with policymakers seeking to balance innovation, environmental safety, and circular economy goals.
The European Union remains at the forefront, with its Circular Economy Action Plan and the revision of the Packaging and Packaging Waste Regulation (PPWR), which are set to influence solvolysis adoption. The upcoming regulations are expected to define criteria for “recycled content” and clarify the acceptance of solvolysis-derived polymers for direct food-contact applications—critical for market uptake. The European Chemicals Agency (ECHA) is also engaged in evaluating chemical recycling processes, including solvolysis, to ensure compliance with REACH and CLP regulations, which govern chemical safety and labeling.
In the United States, the Environmental Protection Agency (EPA) is reviewing its stance on advanced recycling, with several states already enacting legislation that distinguishes solvolysis and related processes from traditional incineration or hazardous waste treatment. States like Texas and Illinois have passed laws recognizing solvolysis as a manufacturing process, simplifying permitting for new facilities and encouraging private sector investment. These legal clarifications are expected to accelerate the deployment of commercial-scale plants by companies such as Eastman and Loop Industries, both of which are actively advancing solvolysis-based PET recycling.
Industry standards are also evolving. The International Organization for Standardization (ISO) and CEN (European Committee for Standardization) are working on new standards to define recycled content and traceability in chemically recycled polymers, with input from stakeholders including resin producers, recyclers, and brand owners. Adherence to these standards will be essential for solvolysis-based materials to access high-value applications, such as food-grade packaging, and to meet the requirements of major consumer brands.
Looking ahead to the next few years, the policy landscape is expected to further support solvolysis as governments set mandatory recycled content targets and implement Extended Producer Responsibility (EPR) schemes. The definition and certification of recycled content, as well as harmonization of environmental and safety requirements, will be crucial in determining the competitiveness of solvolysis compared to other recycling technologies. Industry players—including Eastman, Carbios, and Loop Industries—are actively engaging with regulators and standardization bodies to shape these emerging frameworks and ensure market access for solvolysis-based recycled polymers.
Sustainability Metrics and Environmental Impact Assessment
Solvolysis-based polymer recycling technologies are gaining traction as a sustainable alternative to traditional mechanical and thermal recycling methods, particularly for challenging plastic waste streams such as PET, polycarbonate, and polyamide. In 2025, the focus within industry and research has shifted toward quantifiable sustainability metrics and robust environmental impact assessment frameworks to guide technology deployment and investment decisions.
A primary metric used in evaluating solvolysis-based recycling is the reduction in greenhouse gas (GHG) emissions compared to virgin polymer production. Early commercial-scale operations, such as those run by Loop Industries for PET depolymerization, report GHG emissions reductions of up to 60% versus conventional petrochemical routes, taking into account both process emissions and avoided incineration or landfill. Life-cycle assessment (LCA) methodologies, increasingly standardized through bodies like the PlasticsEurope Eco-profile framework, are now widely adopted by solution providers to transparently quantify impacts from feedstock acquisition through to polymer re-synthesis.
Water and energy use are also central sustainability indicators. Solvolytic processes typically operate at moderate temperatures and pressures, offering energy savings over high-temperature pyrolysis. For instance, Carbios’s enzymatic PET recycling process has demonstrated up to 30% lower energy consumption compared to virgin PET synthesis, according to publicly available technical documentation. Moreover, the closed-loop nature of solvent systems in recent pilot plants, such as those developed by gr3n, drastically reduces solvent loss and wastewater generation, improving the overall environmental profile.
A growing area of scrutiny in 2025 is the fate of additives, colorants, and contaminants. Solvolysis technologies are being assessed for their ability to selectively depolymerize target plastics while enabling efficient separation and management of non-polymeric residues. Loop Industries and Carbios have both implemented multi-stage purification steps to ensure high-purity monomers suitable for food-grade resins, an essential requirement for circular packaging applications.
Looking ahead for the next few years, regulatory frameworks in the EU and North America are expected to further incentivize the adoption of advanced recycling technologies that can verifiably demonstrate improved sustainability metrics. Certification schemes and digital traceability solutions are being piloted, often in partnership with organizations like PlasticsEurope, to standardize reporting and build consumer and brand-owner confidence in the environmental benefits of solvolysis-based recycling.
Investment Trends, Funding, and M&A Activity
Investment in solvolysis-based polymer recycling technologies has accelerated markedly entering 2025, driven by the need for scalable, circular solutions for hard-to-recycle plastics such as polyesters, polyamides, and polycarbonates. Strategic funding rounds, joint ventures, and mergers and acquisitions have become key mechanisms for both established chemical companies and innovative startups to expand capacity and bring advanced solvolysis technologies to market.
Several prominent chemical manufacturers continue to make sizable capital commitments to commercialize and scale solvolysis plants. Eastman Chemical Company has sustained momentum in its polyester renewal technology, with ongoing investments in large-scale facilities in the U.S. and Europe. In 2024, the company announced further funding for its planned molecular recycling facility in France, signaling confidence in solvolysis as a viable commercial pathway for polyester circularity. Similarly, SABIC has pursued partnerships to deploy chemical recycling infrastructure, including solvolysis, as part of its TRUCIRCLE™ initiative, aiming for advanced recycling of mixed plastic streams.
Emerging technology firms have attracted notable venture capital and strategic corporate funding. For example, Carbios, a pioneer in enzymatic and solvolytic PET recycling, has secured investment from leading global brands and polymer producers to accelerate commercialization. In 2024-2025, Carbios has expanded its consortium of partners and advanced plans for its first industrial-scale plant. Other companies such as gr3n and Loop Industries have reported successful fundraising rounds to support the construction of demonstration and commercial units, with Loop entering into several joint development agreements with resin producers and packaging companies to secure offtake and supply chain integration.
M&A activity is also gathering pace as global chemical and materials players seek to acquire or invest in innovative solvolysis technologies to enhance their recycling portfolios. Recent years have seen large corporates participate in technology licensing deals, minority investments, and outright acquisitions, aiming to secure early access to novel processes and feedstock streams. The interest is not limited to polymer producers; major waste management and petrochemical companies are increasingly active, seeking to vertically integrate solvolysis-based recycling into their operations.
Looking forward into 2025 and beyond, the sector is poised for increased deal flow as commercialization milestones are reached, regulatory incentives for recycled content strengthen, and brand owners commit to ambitious sustainability targets. The convergence of corporate venture capital, public-private partnerships, and cross-industry alliances points to robust investment activity in solvolysis platforms, with capacity expansions and new plant announcements anticipated in North America, Europe, and Asia.
Future Outlook: Challenges, Opportunities, and Next-Gen Innovations
As solvolysis-based polymer recycling technologies advance through 2025 and into the latter half of the decade, the sector faces a complex mix of challenges and opportunities. This family of technologies—encompassing processes such as glycolysis, methanolysis, and hydrolysis—has rapidly gained momentum as a means to break down post-consumer plastics, especially polyesters like PET, into their constituent monomers for re-polymerization. Leading industry players, including Eastman Chemical Company, Carbios, and Loop Industries, have made substantial investments in scaling and commercializing solvolysis-based recycling plants, with significant milestones projected for 2025 and beyond.
A key challenge lies in the scalability and energy efficiency of solvolysis processes. While pilot and demonstration plants have proven technical viability, the transition to commercial-scale operations requires optimization of reaction conditions, solvent recovery, and feedstock pre-treatment. Additionally, the variability in post-consumer plastic waste streams demands robust sorting and contaminant management. Companies like Eastman Chemical Company are addressing these issues with the construction of large-scale material-to-material recycling facilities in the United States and Europe, targeting hundreds of thousands of metric tons of annual capacity by the mid-2020s.
Another challenge is the need for favorable regulatory frameworks and consistent supply chains for high-quality feedstock. The European Union’s evolving packaging and recycling targets, as well as North American extended producer responsibility (EPR) legislation, are expected to drive demand for recycled content, thereby supporting investment in solvolysis capacity. However, uncertainties around policy implementation and the economics of virgin versus recycled polymers can impact plant utilization rates and long-term project viability.
Opportunities abound in the integration of solvolysis with broader circular economy initiatives. Next-generation innovations focus on expanding the range of polymer types amenable to solvolysis and improving process selectivity. For instance, Carbios is developing enzymatic solvolysis approaches tailored for PET, while Loop Industries has reported advances in depolymerization of low-grade and mixed PET waste. The anticipated commercialization of these technologies in 2025–2027 is expected to boost the supply of food-grade recycled monomers and resins.
Looking ahead, the sector’s outlook is cautiously optimistic. If technical and economic barriers are addressed, solvolysis-based recycling could play a crucial role in closing the loop for plastics and reducing dependency on fossil-based feedstocks. Collaboration between technology providers, brand owners, and policymakers will be essential to accelerate adoption and unlock the full potential of solvolysis recycling by the end of the decade.