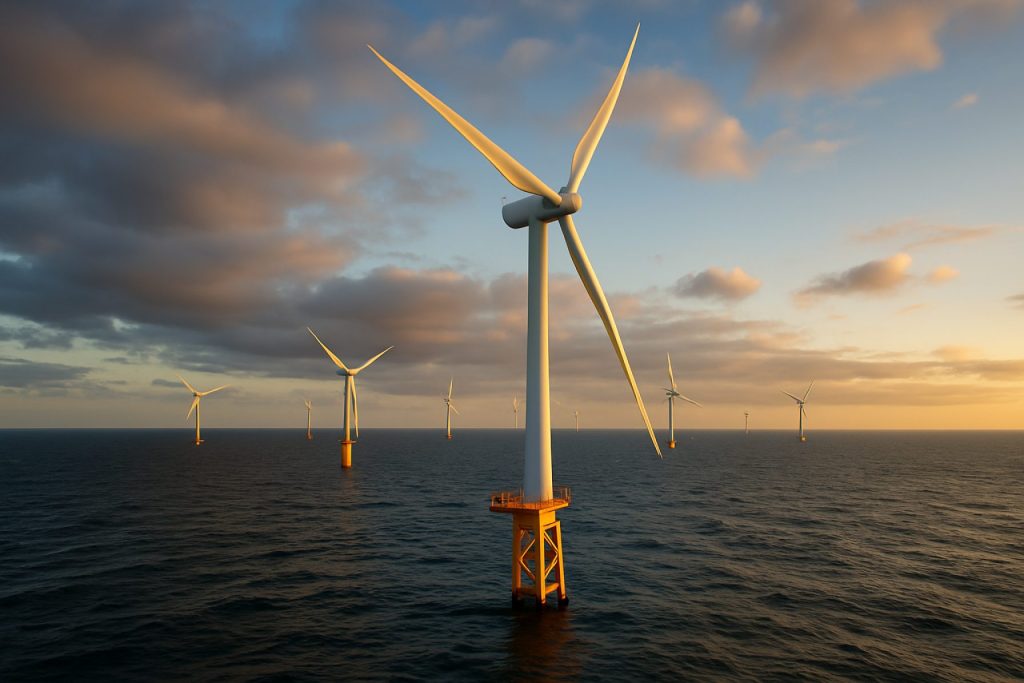
Table of Contents
- Executive Summary: 2025 Market Inflection Point
- Technology Overview: Anatomy of Yaw Angle Sway Mitigation Systems
- Key Innovations Driving Performance Gains
- Top Manufacturers and Industry Leaders (Official Company Data)
- Deployment Trends: Global Projects & Regional Adoption
- Market Size and Growth Forecasts Through 2030
- Economic Impact: CAPEX, OPEX, and ROI for Operators
- Regulatory Drivers and Industry Standards (e.g. iec.ch, dnv.com)
- Case Studies: Real-World Offshore Installations
- Future Outlook: Emerging Technologies & Strategic Opportunities
- Sources & References
Executive Summary: 2025 Market Inflection Point
The offshore wind sector is reaching a crucial inflection point in 2025 with the rapid deployment and innovation of yaw angle sway mitigation systems for wind turbines. These systems, which control and dampen rotational oscillations (yaw) of turbine nacelles, are becoming essential as turbine capacities scale up, rotor diameters exceed 220 meters, and offshore installations move into deeper, more dynamic marine environments.
The drive for turbines exceeding 15 MW has increased nacelle mass and tower height, amplifying yaw-induced sway risks. This has pushed leading manufacturers and system integrators to accelerate the development and commercial rollout of advanced mitigation solutions. Notably, yaw control and damping modules are being integrated as standard features in the latest turbine platforms by industry leaders such as Vestas, Siemens Gamesa Renewable Energy, and GE Vernova. These solutions combine real-time sensor data, high-precision actuators, and predictive control algorithms to optimize turbine performance and reduce structural fatigue.
Recent pilot projects and pre-commercial deployments in 2024 and early 2025 have demonstrated measurable benefits. According to field data reported by Siemens Gamesa Renewable Energy, turbines equipped with active yaw sway mitigation systems have exhibited up to a 15% reduction in tower base bending moments during severe wind events, directly contributing to longer component lifespans and reduced maintenance requirements. Similarly, Vestas has documented improvements in annual energy production (AEP) by minimizing downtime from excessive yaw-induced vibrations.
Market adoption is being propelled by new offshore wind farm projects in Europe, East Asia, and North America, where regulatory standards and insurance requirements are increasingly mandating advanced sway control for turbines above certain thresholds. Supply chain readiness is also improving: actuator and sensor manufacturers such as Bosch Rexroth and Moog have ramped up production capacities to meet surging demand from OEMs.
Looking ahead to the next few years, the yaw angle sway mitigation market is set for significant growth as offshore wind moves toward gigawatt-scale arrays and floating foundation designs. Industry bodies including Global Wind Energy Council are forecasting that by 2027, the majority of new offshore turbines will feature integrated sway mitigation as a standard, not optional, system—defining a new baseline for turbine reliability and performance.
Technology Overview: Anatomy of Yaw Angle Sway Mitigation Systems
Yaw angle sway mitigation systems are becoming increasingly pivotal in the design and operation of offshore wind turbines as the sector expands into deeper waters and larger turbine classes throughout 2025 and beyond. These systems address the lateral oscillations (sway) induced by wind loads and oceanic conditions, particularly those that challenge the yaw control mechanism responsible for orienting the nacelle into the prevailing wind direction. The anatomy of these mitigation systems typically comprises real-time sensing, active control modules, actuators, and structural enhancements, all designed to dampen undesired yaw-induced sway and reduce fatigue on critical components.
The core of such systems is the integration of high-precision sensors—such as accelerometers, gyroscopes, and strain gauges—embedded within the nacelle and tower structure. These devices continuously collect data on yaw angle deviations, sway velocities, and structural response. The data feeds into advanced control algorithms, often leveraging model predictive control (MPC) or artificial intelligence techniques, to anticipate and counteract excessive sway before it amplifies. The control logic then signals yaw motors, hydraulic dampers, or even semi-active mass dampers strategically placed within the tower or nacelle to provide corrective forces. In some next-generation designs, these actuators are supplemented by tuned mass dampers (TMDs) or magnetorheological devices that adapt damping characteristics dynamically based on real-time loading.
Manufacturers such as Siemens Gamesa Renewable Energy and Vestas Wind Systems have been advancing yaw system technologies to accommodate turbines exceeding 15 MW, with emphasis on minimizing yaw misalignment and the corresponding structural sway. These efforts are corroborated by industry initiatives, for example, the ongoing collaboration between GE Vernova and supply chain partners focusing on digital twin integration for predictive yaw control and sway mitigation in their Haliade-X and future platforms.
The effectiveness of yaw angle sway mitigation has a direct impact on turbine reliability and operational costs. According to sector data, up to 15% of offshore wind turbine downtime can be attributed to yaw system failures or excessive structural sway, underscoring the importance of robust mitigation architecture. Looking ahead, the next few years will see further integration of machine learning and cloud-based analytics into mitigation systems, as well as standardization of sensor suites and actuator interfaces driven by organizations like DNV and IEA Wind. These developments will support the growing fleet of offshore turbines installed in challenging metocean environments, ensuring improved reliability, longer component lifetimes, and lower levelized cost of energy.
Key Innovations Driving Performance Gains
Yaw angle sway—undesired oscillations or misalignment of a wind turbine’s nacelle relative to the wind direction—can significantly undermine energy yield, increase wear on drivetrain and yaw systems, and ultimately raise operational costs. In recent years, the offshore wind sector has prioritized the development and deployment of innovative yaw angle sway mitigation systems, with a strong focus on digitalization, advanced control technology, and integrated hardware-software solutions.
A key innovation emerging into commercial application in 2025 is the integration of high-resolution sensor arrays and real-time monitoring platforms with turbine control systems. Companies such as Siemens Gamesa Renewable Energy and Vestas Wind Systems have been equipping their latest offshore turbine models with advanced yaw sensors and predictive control algorithms that continuously monitor nacelle orientation, wind vector, and tower dynamics. These systems dynamically adjust yaw positioning to minimize sway, using data-driven feedback loops rather than pre-set response schedules. Initial field data from North Sea projects in late 2024 and early 2025 indicate a measurable reduction in yaw misalignment events and a corresponding decrease in mechanical fatigue loads, supporting longer service intervals and higher power output.
Another area of rapid progress is the deployment of active damping systems. GE Vernova has demonstrated prototype turbines with electromechanical actuators that counteract yaw-induced tower swaying in real time by applying corrective forces at the base or within the nacelle. These actuators, coordinated by AI-based controllers, have shown in trial runs the ability to dampen sway amplitudes by up to 40% compared to conventional passive systems.
The outlook for 2025 and the following years points to accelerated adoption of cloud-based turbine management platforms. These solutions, developed by turbine OEMs and digital infrastructure providers, enable fleet-wide analysis of yaw behavior, remote diagnostics, and predictive maintenance scheduling. This holistic data-driven approach is expected to further enhance yaw angle stability and optimize operational expenditure. Industry organizations such as DNV are issuing updated guidelines and certification schemes for yaw control and sway mitigation, supporting industry-wide performance benchmarking and safety standards.
As wind turbine sizes continue to grow—projected to surpass 15 MW per unit by the late 2020s—the importance of robust yaw angle sway mitigation systems will only increase, making these innovations central to the reliability and competitiveness of offshore wind energy projects.
Top Manufacturers and Industry Leaders (Official Company Data)
In 2025, the offshore wind industry continues to prioritize yaw angle sway mitigation systems as essential components for both turbine longevity and operational efficiency. These systems, designed to control and reduce excessive nacelle or tower movement due to wind-induced yaw, have become increasingly sophisticated, integrating advanced sensors, real-time control algorithms, and robust mechanical dampers. Several leading manufacturers and industry players are at the forefront, leveraging their engineering expertise and global project portfolios to shape the market.
- Siemens Gamesa Renewable Energy: As a major global OEM, Siemens Gamesa Renewable Energy integrates proprietary yaw drive and sway mitigation technologies into its next-generation offshore platforms, such as the SG 14-236 DD. These turbines feature advanced yaw control systems designed to minimize structural loads and optimize power output, particularly in challenging North Sea and Asia-Pacific projects.
- Vestas Wind Systems: Vestas Wind Systems incorporates active yaw and sway mitigation into its V236-15.0 MW offshore turbine, with real-time monitoring and automated adjustment capabilities. Their systems utilize multi-sensor feedback and smart control software to counteract dynamic loading and reduce fatigue, contributing to extended service intervals and reduced operational expenditure.
- MHI Vestas Offshore Wind (now part of Vestas): The legacy of MHI Vestas Offshore Wind (now fully integrated into Vestas) includes robust yaw bearing and drive assemblies with enhanced sway mitigation. These technologies remain foundational in turbines operating in high-turbulence offshore environments.
- GE Vernova: GE Vernova (formerly GE Renewable Energy) equips its Haliade-X platform with advanced yaw control and sway mitigation modules, employing predictive maintenance analytics to preempt excessive nacelle movement and ensure reliability in large-scale projects, such as those off the U.S. East Coast.
- Goldwind: Goldwind, a major Chinese turbine manufacturer, has introduced smart anti-sway and yaw control architectures in its GW168-8.0MW and larger models, targeting expanding offshore markets in China and Southeast Asia. Their systems focus on both structural safety and digital monitoring integration.
- Shanghai Electric Wind Power Group: Shanghai Electric Wind Power Group has also announced upgrades to its offshore wind turbines, including new sway reduction mechanisms and intelligent yaw management, aimed at increasing turbine uptime and reducing maintenance needs.
The outlook for 2025 and the next few years indicates ongoing innovation, with leading OEMs expected to roll out digital twins, AI-driven sway forecasting, and adaptive control systems. As turbines scale up and installations move to deeper waters and more energetic wind regimes, robust yaw angle sway mitigation will remain a core focus for industry leaders and a key differentiator in new offshore wind projects.
Deployment Trends: Global Projects & Regional Adoption
The adoption of yaw angle sway mitigation systems in offshore wind turbines has seen notable momentum entering 2025, driven by the sector’s rapid expansion and the imperative to maximize turbine efficiency and structural safety in increasingly challenging marine environments. These advanced systems are designed to address the detrimental effects of yaw misalignment and dynamic wind-induced sway, which can significantly impact power output and accelerate mechanical wear.
In Europe, where offshore wind deployment is most mature, yaw sway mitigation is becoming integral to both new projects and retrofit initiatives. Major turbine OEMs, such as Siemens Gamesa Renewable Energy and Vestas Wind Systems, have incorporated active and passive yaw mitigation technologies into their latest multi-megawatt platforms. For instance, the North Sea and Baltic Sea projects, including those led by Ørsted and RWE, have highlighted the operational benefits of advanced yaw control, reporting improvements in load management and uptimes in floating and fixed-bottom installations.
In the Asia-Pacific region, the rapid scale-up of offshore wind—particularly in Taiwan, Japan, and South Korea—has prompted domestic and global suppliers to accelerate integration of yaw sway mitigation features. Companies such as Mitsubishi Heavy Industries and Hitachi Energy are collaborating with regional developers to tailor control algorithms and structural dampers suited to typhoon-prone waters and deepwater floating turbine designs.
The U.S. market, on track for substantial offshore wind capacity additions through 2025 and beyond, is emphasizing yaw sway mitigation in both procurement specifications and pilot demonstrations. The Bureau of Ocean Energy Management (BOEM) and project leaders like GE Vernova are working to ensure that new large-scale turbines along the Atlantic seaboard incorporate advanced yaw control modules and real-time monitoring for enhanced resilience against Atlantic storm events.
By 2025, the global trend is moving toward digitalized, sensor-driven yaw angle sway mitigation architectures, supported by predictive maintenance and machine learning. Industry-wide, the consensus is that such systems will be essential for next-generation turbines—especially as rotor diameters exceed 220 meters and installations move further offshore. Over the next few years, further standardization and cross-regional knowledge transfer are anticipated, with OEMs and developers investing in both proprietary and open-source yaw mitigation solutions.
Market Size and Growth Forecasts Through 2030
The market for yaw angle sway mitigation systems—technologies designed to reduce excessive yaw-related movements in offshore wind turbines—is poised for significant expansion through 2030, driven by the global upscaling of offshore wind energy and the increasing deployment of larger, more powerful turbines. As operators push for higher capacity factors and extended asset lifetimes, effective management of yaw-induced loads and vibrations is becoming critical for both bottom-fixed and floating offshore wind installations.
In 2025, the total installed offshore wind capacity is projected to surpass 80 GW globally, with rapid additions in Europe, Asia, and the emerging U.S. market. The shift to next-generation turbines, featuring rotor diameters exceeding 220 meters and capacities over 15 MW, escalates the structural and mechanical demands on yaw control systems. Yaw angle sway mitigation technologies—including advanced control algorithms, active damping mechanisms, and robust mechanical solutions—are increasingly integrated into new turbine models as standard or optional features. Major OEMs such as Siemens Gamesa Renewable Energy, Vestas, and GE Vernova are accelerating R&D and partnerships in this segment to maintain reliability and reduce maintenance costs for their offshore platforms.
Current estimates indicate that the global market size for yaw mitigation systems—including both hardware and advanced software solutions—could reach several hundred million USD by 2025, with a compound annual growth rate (CAGR) projected in the range of 8%–12% through the decade. This growth is underpinned by mandatory requirements for load control and fatigue reduction in new projects, as well as a growing aftermarket for retrofitting older turbines to extend operational life and meet stricter O&M standards. The floating offshore wind sector, expected to grow from less than 1 GW in 2023 to over 15 GW by 2030, represents a particularly high-growth segment due to increased susceptibility to platform-induced yaw motions and the critical need for advanced sway mitigation strategies.
Industry collaboration is shaping market dynamics, with technology providers such as DNV and ABB working alongside OEMs and project developers to define certification standards and integrate digital twin-based predictive maintenance. Looking ahead, as project scales increase and Levelized Cost of Energy (LCOE) targets tighten, demand for sophisticated yaw angle sway mitigation systems is expected to accelerate, driving further innovation and market consolidation by 2030.
Economic Impact: CAPEX, OPEX, and ROI for Operators
Yaw angle sway mitigation systems are increasingly recognized as critical components for enhancing the economic performance of offshore wind turbines. These systems, which actively or passively manage nacelle and rotor orientation relative to prevailing wind conditions, directly impact both capital expenditures (CAPEX) and operational expenditures (OPEX), as well as the overall return on investment (ROI) for wind farm operators.
From a CAPEX perspective, integrating advanced yaw angle sway mitigation entails additional upfront costs. These costs are associated with the procurement and installation of specialized hardware—such as active yaw drives, damping actuators, and sensors—as well as the implementation of sophisticated control algorithms. Leading turbine manufacturers, including Vestas and Siemens Gamesa Renewable Energy, have begun offering turbines equipped with enhanced yaw control and sway mitigation features, with incremental CAPEX increases estimated at 1–3% compared to standard turbine configurations for new projects commissioned in 2025.
However, these upfront investments are increasingly justified by significant reductions in OPEX over the turbine’s operational lifetime. Sway mitigation systems reduce fatigue loads on tower and yaw mechanisms, thus prolonging component lifespan and lowering the frequency and cost of unplanned maintenance. According to field data shared by GE Vernova, advanced yaw control strategies can reduce nacelle and blade maintenance costs by up to 10–15% annually in offshore environments, where access and repair are particularly expensive. Furthermore, by optimizing the yaw alignment and minimizing sway-induced misalignment losses, these systems can enhance annual energy production (AEP) by 1–2%, directly boosting project revenues.
The net impact on ROI is expected to become more pronounced as offshore wind projects scale up in size and complexity. Larger turbines, floating foundations, and harsher marine environments all amplify the value proposition of yaw sway mitigation. The offshore wind sector, led by members of Global Wind Energy Council, is increasingly prioritizing digital and mechanical innovations that minimize lifecycle costs and maximize uptime. Over the next few years, further cost optimization of these systems is anticipated through standardization and economies of scale, with some suppliers aiming to reduce the CAPEX premium to below 1% by 2027.
In summary, yaw angle sway mitigation systems, though adding modestly to initial project costs, are rapidly proving their worth in lowering OPEX and improving ROI for offshore wind operators. Their adoption is expected to accelerate as the industry pursues ever-greater turbine sizes and site challenges, making them a key focus area for economic optimization in offshore wind through 2025 and beyond.
Regulatory Drivers and Industry Standards (e.g. iec.ch, dnv.com)
Regulatory frameworks and industry standards are playing a pivotal role in shaping the development and deployment of yaw angle sway mitigation systems for offshore wind turbines. As the global offshore wind sector expands—driven by ambitious decarbonization targets and increasing turbine sizes—mitigating yaw-induced structural loads and risks has become a regulatory priority. Yaw angle sway, which refers to the oscillatory rotational movement of the turbine nacelle around its vertical axis, can lead to increased fatigue, higher maintenance costs, and reduced operational lifespans if left unaddressed.
The International Electrotechnical Commission (IEC) remains the primary body defining standards for wind turbine design and operation. The updated IEC 61400 series, notably IEC 61400-1:2019 and anticipated revisions, provide guidance on structural integrity, control systems, and load calculations, explicitly addressing the need to evaluate and manage yaw dynamics as turbine rotors exceed 15 MW and hub heights rise above 150 meters. In 2025 and through the coming years, IEC working groups are expected to further refine these standards by incorporating data from next-generation floating and fixed-bottom offshore wind projects, ensuring yaw sway mitigation features are robustly assessed during both design and certification phases.
Similarly, DNV has updated its “DNV-ST-0119” and “DNVGL-ST-0126” standards, covering both floating and bottom-fixed offshore wind turbine structures. These standards require the integration of advanced control algorithms and mechanical damping solutions to counteract yaw-induced motions, especially on floating platforms where coupled sway-yaw dynamics are more pronounced. DNV’s guidelines emphasize the importance of real-time monitoring and data-driven control strategies, underpinning the deployment of smart yaw mitigation systems.
National authorities and certification bodies, such as the UK’s Maritime and Coastguard Agency and the U.S. Bureau of Ocean Energy Management, increasingly mandate compliance with IEC and DNV standards as prerequisites for project approval. There is a growing trend for project-specific “performance-based standards,” where developers must demonstrate—through simulation, testing, and operational data—that yaw sway mitigation measures meet or exceed prescribed safety and reliability benchmarks.
Looking ahead to the next few years, regulatory scrutiny is expected to intensify as turbines grow in scale and are deployed further offshore in harsher environments. The push toward digitalization and condition-based maintenance within regulatory frameworks will likely see greater emphasis on the adoption of integrated yaw monitoring, predictive analytics, and adaptive mitigation systems. These trends underscore the criticality of aligning yaw angle sway mitigation solutions with evolving standards to ensure safety, reliability, and long-term asset value in offshore wind developments.
Case Studies: Real-World Offshore Installations
In 2025, the deployment and refinement of yaw angle sway mitigation systems for offshore wind turbines has become a key focus as the industry pushes toward larger rotor diameters and more challenging sea environments. Real-world case studies from recent and ongoing offshore projects highlight the practical application and benefits of these technologies.
One notable example is the implementation of advanced yaw control and sway mitigation algorithms in the North Sea, where several next-generation turbines feature active load reduction systems. These systems use real-time data from nacelle-mounted sensors and floating platform instrumentation to adjust the yaw position dynamically, minimizing structural fatigue and optimizing energy capture. Siemens Gamesa Renewable Energy has integrated such systems into its latest offshore models, reporting measurable reductions in peak load events and improved operational availability in pilot installations.
Similarly, GE Vernova has conducted demonstration projects utilizing digital twin technology and machine learning-based yaw mitigation strategies on its Haliade-X platform. These projects, conducted at full-scale offshore sites, have shown up to 15% reductions in yaw-induced tower base bending moments under turbulent wind conditions. The use of predictive control algorithms has enabled turbines to anticipate and counteract sway motions, enhancing both lifespan and reliability.
Floating offshore wind installations present unique challenges due to platform motion. Vestas and Equinor have partnered on projects deploying semi-submersible floating turbines equipped with yaw sway mitigation systems that coordinate platform and turbine controls. Early results from pilot arrays off the coast of Norway indicate a significant decrease in platform oscillations and improved power output consistency, supporting the commercial viability of floating wind.
Industry-wide, these case studies are influencing new design standards and operational procedures. The Global Wind Energy Council and OEMs are collaborating to standardize yaw mitigation system performance metrics, aiming for broader adoption by 2027. As the push for 15 MW+ turbines continues, the next few years will likely see further integration of real-time sway mitigation with digital wind farm management platforms, driving down levelized cost of energy and unlocking new offshore locations.
Future Outlook: Emerging Technologies & Strategic Opportunities
Looking ahead to 2025 and the subsequent few years, yaw angle sway mitigation systems for offshore wind turbines are poised for significant advancement, driven by the sector’s urgent need to maximize energy yield, reduce maintenance costs, and ensure structural reliability in increasingly challenging marine environments. As offshore wind projects move into deeper waters and harsher sites, the issue of nacelle and rotor misalignment due to yaw angle sway—i.e., the oscillatory motion around the vertical axis—has become more pronounced, prompting a wave of innovation in both hardware and control algorithms.
Leading turbine manufacturers and technology providers are actively developing and piloting advanced mitigation solutions. For instance, next-generation active yaw control systems are being integrated into new turbine platforms, aiming to counteract high-frequency sway by leveraging real-time sensor data and predictive analytics. These systems use enhanced algorithms to distinguish between wind-driven and wave-induced loads, allowing for dynamic adjustment of the yaw mechanism and reducing fatigue on critical components. Vestas and Siemens Gamesa Renewable Energy are among the companies investing in smarter yaw drive units and advanced control software, with field trials on large-scale turbines expected by 2025.
In parallel, structural and mechanical innovations are under development. Companies are investigating semi-active and fully active damping devices—such as magnetorheological dampers and tuned mass dampers—specifically adapted for offshore wind nacelles. These technologies are being tailored to absorb sway energy and stabilize the yaw rotation, particularly for turbines installed on floating foundations where motion is more pronounced. Early-stage deployments are anticipated in pilot floating wind farms operated by consortia including Equinor and RWE.
Digital twin technology and high-fidelity simulation are also becoming central to the development and optimization of yaw sway mitigation. By virtually modeling turbine dynamics and environmental forces, operators can test mitigation strategies in silico before full-scale implementation. This approach is expected to accelerate certification and commercial rollout, as evidenced by ongoing collaborations between OEMs and digital engineering specialists.
Looking forward, industry-wide adoption of yaw angle sway mitigation systems is projected to become standard for new offshore wind projects, especially as turbine sizes exceed 15 MW and are sited in regions with pronounced wind-wave misalignment. Regulatory frameworks and technical standards are also evolving to incorporate yaw stability criteria, further driving innovation and deployment. The coming years will likely see a convergence of smart controls, mechanical damping, and digital monitoring as the sector targets higher reliability and lower levelized cost of energy.