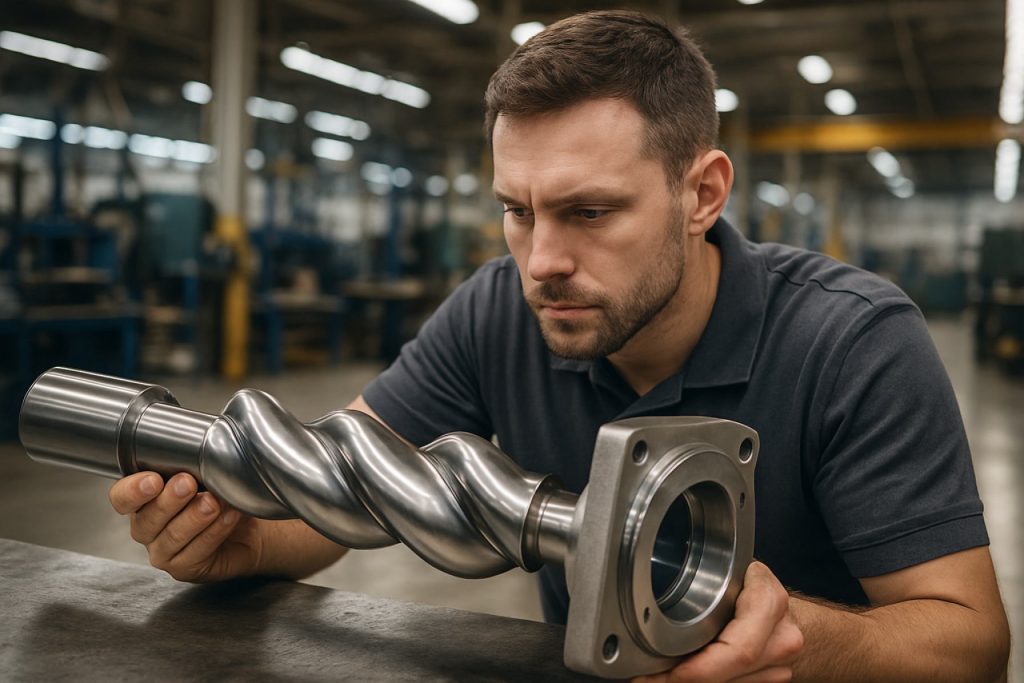
Table of Contents
- Executive Summary: Key 2025 Insights & Forecasts
- Global Market Outlook: Growth Projections to 2030
- Emerging Technologies Reshaping Helical Rotor Pump Design
- Sustainability Trends and Eco-Friendly Innovations
- Competitive Landscape: Manufacturer Profiles and Market Share
- Key End-Use Sectors: Oil & Gas, Water, Food, and More
- Regulatory & Compliance Developments Impacting the Sector
- Supply Chain Dynamics and Globalization Strategies
- Investment Hotspots: M&A, R&D, and Expansion Initiatives
- Future Outlook: Disruptive Trends and Strategic Recommendations
- Sources & References
Executive Summary: Key 2025 Insights & Forecasts
The global helical rotor pump manufacturing sector is positioned for steady growth in 2025, driven by robust demand from water and wastewater management, oil and gas, food processing, and chemical industries. Helical rotor pumps, also known as progressive cavity pumps, are favored for their ability to handle viscous, abrasive, and shear-sensitive fluids, making them indispensable across diverse industrial applications. As regulatory requirements for environmental compliance tighten and industries seek solutions for efficient fluid handling, manufacturers are scaling up innovation and production capacity to meet evolving needs.
Key manufacturers such as NETZSCH Pumpen & Systeme, SEEPEX, and Sulzer are investing in advanced materials, precision manufacturing, and digital monitoring technologies. The integration of Industrial Internet of Things (IIoT) capabilities is enabling predictive maintenance and real-time performance tracking, which are increasingly standard in new pump offerings. This digitalization trend is expected to enhance pump reliability, extend service life, and reduce total cost of ownership for end users.
Geographically, Asia-Pacific remains the fastest-growing market, with significant investments in water infrastructure, especially in China and India, catalyzing demand for helical rotor pumps. Concurrently, North American and European manufacturers are emphasizing sustainable solutions, including pumps with higher energy efficiency and reduced environmental impact. Major players are also expanding their global production footprints to ensure proximity to customers and faster delivery times.
From a supply chain perspective, 2025 is expected to see a continued emphasis on securing high-quality raw materials and components, amid global economic uncertainties. Manufacturers are strengthening partnerships with local suppliers and investing in automation to mitigate labor shortages and production disruptions.
Looking ahead, the helical rotor pump market is forecast to maintain a positive growth trajectory through 2025 and beyond, with industry analysts anticipating notable gains in sectors such as renewable energy, mining, and pharmaceuticals. The convergence of sustainability imperatives, digital transformation, and increasing regulatory oversight is set to further shape manufacturing strategies. Leading companies like Nikkiso and ITT Inc. are expected to remain at the forefront of innovation, setting benchmarks for product performance and service excellence.
Global Market Outlook: Growth Projections to 2030
The global market for helical rotor pump manufacturing is set to experience robust growth through 2030, propelled by increasing demand in water and wastewater treatment, oil and gas, food processing, and chemical industries. As of 2025, industry players are responding to heightened requirements for efficient fluid handling and energy-saving technologies, which are key factors influencing purchasing decisions.
In recent years, the adoption of helical rotor pumps has expanded, largely due to their ability to handle viscous, abrasive, and shear-sensitive fluids. This versatility is driving their selection for challenging applications across municipal infrastructure upgrades and industrial process optimization. Leading manufacturers such as National Oilwell Varco, SPX FLOW, and SEW-EURODRIVE are continually investing in research and development to enhance pump efficiency, durability, and automation compatibility.
Market trends in 2025 reflect a shift towards digitalization, with smart monitoring systems and predictive maintenance solutions being integrated into new pump models. This advancement is particularly notable among major suppliers, as companies like ITT Inc. and Sulzer incorporate Industrial Internet of Things (IIoT) capabilities, enabling end-users to reduce downtime and operational costs.
Geographically, Asia-Pacific continues to be the fastest-growing region, led by infrastructure investments in China, India, and Southeast Asia. The region’s rapid urbanization and expanding industrial base are generating significant demand for reliable pumping solutions, with manufacturers scaling production capacity and distribution networks to meet this growth. European and North American markets, while mature, are seeing renewed activity driven by regulatory emphasis on energy efficiency and sustainability, prompting replacement of outdated equipment with advanced helical rotor pumps.
Looking ahead, the outlook for helical rotor pump manufacturing remains positive. Industry analysts and leading companies anticipate compound annual growth rates (CAGR) in the mid- to high-single digits through 2030, underpinned by ongoing investments in automation, environmental compliance, and product innovation. Strategic partnerships and acquisitions among manufacturers are expected to further consolidate the market, enabling broader technology adoption and expansion into emerging economies.
In summary, from 2025 and beyond, the sector’s growth trajectory is underpinned by technological advancements, expanding end-user sectors, and a strong focus on sustainability and operational efficiency, positioning helical rotor pumps as a critical component in modern fluid management systems.
Emerging Technologies Reshaping Helical Rotor Pump Design
In 2025, helical rotor pump manufacturing is experiencing significant transformation, driven by the adoption of emerging technologies aimed at improving efficiency, sustainability, and customization. One of the most noteworthy trends is the integration of advanced materials, such as reinforced polymers and corrosion-resistant alloys, which enhance pump durability in harsh environments and support longer operational lifespans. Manufacturers like Kosmek and Nordson Corporation are actively investing in materials research to address specific industry needs, including oil and gas, wastewater, and food processing.
Additive manufacturing (AM), or industrial 3D printing, is emerging as a disruptive force in pump component production. This technology enables rapid prototyping and on-demand manufacturing of complex rotor geometries previously impossible with traditional machining. Companies such as Grundfos have begun exploring 3D printing for producing bespoke components, thereby reducing lead times and waste, while enabling greater design flexibility for challenging pumping applications.
Digitalization is another key driver, with leading manufacturers integrating Industrial Internet of Things (IIoT) solutions into both the manufacturing process and the pumps themselves. Embedded sensors and remote monitoring capabilities allow for real-time performance tracking, predictive maintenance, and process optimization. Sulzer, for example, offers digitally connected pump solutions that provide continuous diagnostics and data analytics, helping operators reduce downtime and energy consumption.
Automation and robotics are increasingly utilized on the factory floor to streamline assembly, inspection, and quality assurance processes. These technologies minimize human error, improve repeatability, and support higher production throughput. At the same time, computer-aided engineering (CAE) tools, such as advanced computational fluid dynamics (CFD) modelling, are being leveraged to simulate and optimize rotor profiles for maximum hydraulic efficiency and minimal pulsation.
Looking ahead, the next several years are expected to bring further advancements in smart manufacturing, including the use of artificial intelligence for process optimization and the adoption of digital twins for real-time simulation and lifecycle management of pumps. Sustainability will remain a central focus, with ongoing efforts to minimize energy consumption and environmental impact throughout the pump’s lifecycle. These technological shifts are set to redefine competitive advantage and accelerate innovation in the global helical rotor pump sector.
Sustainability Trends and Eco-Friendly Innovations
In 2025, sustainability trends and eco-friendly innovations are shaping the helical rotor pump manufacturing sector, as global pressure mounts for resource-efficient industrial equipment. Manufacturers are responding to tightening environmental regulations and increasing customer demand for energy-efficient and low-emission solutions. A central trend is the integration of advanced materials, such as composite polymers and corrosion-resistant alloys, which extend pump lifespan, reduce maintenance, and minimize resource consumption during the manufacturing process. Companies like NOV Inc. and Sulzer are investing in R&D to develop pump components with lower environmental footprints, focusing on recyclability and reduced use of hazardous substances.
Another significant development is the adoption of high-efficiency motors and optimized rotor-stator geometries. By refining these designs, manufacturers have been able to significantly reduce energy consumption during pump operation—an essential factor as more end-users seek to lower their carbon emissions and operational costs. For example, ABB supplies motors and drives that are increasingly used to enhance efficiency in progressive cavity and helical rotor pumps. These technological improvements support compliance with international energy efficiency standards, such as IE4 and IE5, which are becoming more widely adopted.
Digitalization also plays a key role in sustainability efforts. The implementation of smart monitoring systems enables predictive maintenance, reducing unplanned downtime and extending equipment lifecycles. Remote diagnostics and IoT-based controls, offered by manufacturers like SEW-EURODRIVE, minimize site visits and help optimize pump performance, further reducing environmental impact.
Water conservation and resource management are additional priorities. Manufacturers are engineering helical rotor pumps to handle a wider range of fluids—including abrasive and high-viscosity waste streams—thereby supporting water reuse and recycling initiatives in industries such as wastewater treatment, mining, and food processing. Companies such as NETZSCH are at the forefront of delivering pumps that facilitate efficient slurry and sludge handling, aiding customers’ sustainability targets.
Looking ahead beyond 2025, the sector is expected to see greater collaboration between manufacturers, material suppliers, and end-users to accelerate the adoption of circular economy principles. This will likely include programs for take-back, refurbishment, and remanufacturing of pumps, as well as further advances in biodegradable and recycled materials for pump components, aligning with global sustainability goals.
Competitive Landscape: Manufacturer Profiles and Market Share
The competitive landscape of helical rotor pump manufacturing in 2025 is defined by a mix of established global manufacturers, regional players, and emerging innovators. The market is shaped by ongoing investments in advanced materials, digital monitoring technologies, and energy-efficient designs, as the oil & gas, wastewater, and food processing sectors continue to drive demand for robust and reliable pumping solutions.
Leading manufacturers such as NOV Inc. (National Oilwell Varco), Colfax Corporation, and Sulzer Ltd. maintain significant market shares worldwide, leveraging diversified product lines and global service networks. NOV Inc. remains a dominant force, especially in upstream oil & gas applications, where its Moyno and Mono branded pumps are widely utilized for challenging fluid transport and artificial lift systems. Sulzer Ltd., with its broad industrial pump portfolio, has enhanced its presence in the water and wastewater sector through continual product innovation and strategic acquisitions.
European manufacturers such as NETZSCH Group and Pumpenfabrik Wangen GmbH also command strong positions, particularly in food processing, chemical, and environmental markets, owing to their focus on hygienic design, modularity, and compliance with international standards. NETZSCH Group continues to expand its footprint via investments in digital pump monitoring and predictive maintenance platforms.
In Asia-Pacific, regional growth is spearheaded by companies like Kirloskar Brothers Limited and CNP (Nanfang Pump Industry), who capitalize on burgeoning infrastructure, water management, and industrial expansion. These companies are increasingly integrating helical rotor technologies into broader pump solutions to address both efficiency and lifecycle cost concerns.
Market share distribution in 2025 remains concentrated among these global leaders, but the landscape is evolving as smaller specialized manufacturers adopt additive manufacturing, advanced coatings, and IoT-enabled diagnostics to carve out niche segments. Over the next few years, consolidation is expected to continue, driven by strategic mergers and acquisitions as companies seek to expand geographic reach and technological capabilities.
- Key drivers: Energy efficiency, remote monitoring, compliance with environmental regulations.
- Outlook: Intensifying competition among global leaders and regional players, with increasing emphasis on digital transformation and sustainability.
- Major players (2025): NOV Inc., Sulzer Ltd., Colfax Corporation, NETZSCH Group, Pumpenfabrik Wangen GmbH, Kirloskar Brothers Limited, CNP.
Key End-Use Sectors: Oil & Gas, Water, Food, and More
In 2025, helical rotor pump manufacturing continues to align closely with key end-use sectors, notably oil & gas, water and wastewater management, and food processing. The robust demand from these industries is driving both production volume and technological innovation among leading pump manufacturers worldwide.
The oil & gas sector remains a pivotal market, especially for upstream applications such as crude oil transfer, multiphase pumping, and enhanced oil recovery. The helical rotor pump’s ability to handle viscous fluids and multiphase mixtures with minimal shear makes it indispensable in these operations. Global companies, including Sulzer and NOV Inc., have reported sustained demand for helical rotor solutions as operators focus on maximizing efficiency and reducing downtime in mature oilfields.
Within water and wastewater treatment, helical rotor pumps are favored for their reliability in handling sludge, slurries, and abrasive materials. Municipal and industrial water management agencies are increasingly specifying these pumps for both new installations and retrofits, in response to tightening regulations and sustainability objectives. Firms such as Ziehl-Abegg and SEW-EURODRIVE are notable suppliers, delivering customized rotor pump systems for diverse water sector applications.
The food and beverage industry is another major end-user, leveraging the gentle pumping action of helical rotor pumps to preserve product integrity in processes involving dairy, fruit juices, and viscous foodstuffs. Hygienic design, ease of cleaning, and compliance with international food safety standards are critical considerations driving innovation. Companies such as WANGEN PUMPEN and NETZSCH are actively introducing advanced sanitary rotor pumps to meet the stringent requirements of global food manufacturers.
Looking ahead, the outlook for helical rotor pump manufacturing is shaped by ongoing digitalization, a push for energy efficiency, and continued expansion into emerging markets. Manufacturers are investing in smart pump technologies and remote monitoring solutions to support predictive maintenance and optimize lifecycle performance, particularly in sectors where operational uptime is critical. As sustainability and resource optimization gain further prominence, demand is also expected to grow in biogas, mining, and chemical processing sectors, reinforcing the strategic importance of helical rotor pumps across the industrial landscape.
Regulatory & Compliance Developments Impacting the Sector
The regulatory landscape for helical rotor pump manufacturing is evolving rapidly as global and regional authorities tighten environmental, safety, and efficiency standards. In 2025, several significant regulatory and compliance developments are shaping the sector, influencing both production processes and product design.
A primary driver is the increasing stringency of emissions and energy efficiency regulations, particularly in key markets such as the European Union and North America. The EU’s Ecodesign Directive and related regulations are pushing manufacturers to design pumps with higher energy efficiency and lower lifecycle environmental impact. These rules are expected to tighten further in the next few years, prompting manufacturers like Kirloskar Brothers Limited and Sulzer to invest in R&D for improved rotor geometries, materials, and variable speed drive integration.
Similarly, the U.S. Department of Energy (DOE) continues to update minimum efficiency standards for pump systems, affecting domestic and imported helical rotor pumps. Compliance with these standards is mandatory for market access, and the ongoing review process suggests possible further tightening by 2026. Major manufacturers including Nikkiso and Grundfos have responded by certifying products under recognized efficiency schemes and providing detailed performance data to customers.
On the materials and safety front, the adoption of REACH (Registration, Evaluation, Authorisation and Restriction of Chemicals) in Europe and similar chemical safety directives elsewhere are affecting the selection of alloys, coatings, and seals in pump construction. Manufacturers must document and sometimes reformulate product components to avoid restricted substances and ensure worker and environmental safety. This compliance process is particularly relevant for exporters serving multiple jurisdictions, as seen with global suppliers like ITT Inc..
Additionally, increasing scrutiny over wastewater and hazardous fluid handling—especially in oil & gas, chemical, and wastewater treatment sectors—has led to stricter certification requirements for helical rotor pumps. Standards from bodies such as the American Petroleum Institute (API) and the International Organization for Standardization (ISO) are being updated, with anticipated new editions in the coming years that further address leakage control, durability, and remote monitoring capabilities.
Looking forward, manufacturers must balance innovation with compliance, given the likelihood of continued regulatory tightening through 2027. Those investing proactively in sustainable manufacturing, digital traceability, and modular design are expected to maintain competitive market access and meet client expectations for transparency and reliability.
Supply Chain Dynamics and Globalization Strategies
The helical rotor pump manufacturing sector in 2025 is marked by complex supply chain dynamics and rapidly evolving globalization strategies. As key industries such as oil & gas, wastewater management, and food processing continue to demand high-performance pumping solutions, manufacturers are adapting to a landscape shaped by geopolitical shifts, technological advancements, and sustainability imperatives.
A primary supply chain challenge in 2025 is the volatility in sourcing critical raw materials, notably high-grade stainless steel and specialized elastomers essential for rotor and stator production. Manufacturers like NOV Inc. and Sulzer have responded by intensifying supplier vetting and diversifying procurement across multiple continents to mitigate disruptions. This includes forming strategic alliances with regional suppliers and investing in local material processing facilities, especially in Asia-Pacific and Eastern Europe, to buffer against potential trade restrictions and logistical bottlenecks.
Another significant trend is the integration of digital supply chain management tools. Companies such as SEW-EURODRIVE are leveraging real-time inventory tracking, predictive analytics for demand forecasting, and automated procurement systems. These initiatives aim to enhance transparency and responsiveness, reducing lead times and minimizing the impact of unexpected market fluctuations or transportation delays.
Globalization strategies for helical rotor pump manufacturers are increasingly focused on regionalization—the establishment of manufacturing and assembly hubs closer to end-user markets. This approach, adopted by firms like NETZSCH, enables quicker customization to local regulatory standards and customer preferences while reducing environmental footprints from shipping. Additionally, regional service centers facilitate rapid maintenance and spare part availability, a critical advantage in industries where downtime carries high costs.
Sustainability considerations are also reshaping global supply networks. Manufacturers are seeking to lower carbon emissions by sourcing recycled metals and adopting green logistics practices. For example, Sulzer has publicly committed to expanding its use of sustainable materials and optimizing transportation routes to minimize environmental impact.
Looking ahead, the ongoing digital transformation and decentralization of production are expected to further strengthen supply chain resilience. Strategic investments in automation, 3D printing for prototyping, and collaborative platforms for supplier management are likely to become standard across leading helical rotor pump manufacturers. As these trends mature, the sector is anticipated to deliver greater reliability, shorter delivery cycles, and enhanced adaptability to shifting global market conditions.
Investment Hotspots: M&A, R&D, and Expansion Initiatives
The global helical rotor pump manufacturing sector is currently experiencing an active period of investment, with a focus on mergers and acquisitions (M&A), research and development (R&D), and geographic expansion. As demand for efficient fluid handling grows across wastewater, oil & gas, food & beverage, and industrial applications, leading manufacturers are strategically positioning themselves to capture emerging market opportunities through both organic and inorganic growth.
In 2025, M&A activity remains robust as companies seek to consolidate their market positions and broaden their product portfolios. Notably, established players such as SEEPEX and NOV Inc. continue to integrate smaller firms specializing in niche pump technologies or regional market access. These moves are driven by the need to address evolving customer requirements, particularly in sectors demanding tailored and energy-efficient solutions.
R&D investments are also intensifying, as manufacturers respond to stricter environmental regulations and growing emphasis on lifecycle cost reduction. Companies like Sulzer and NETZSCH are channeling funds toward the development of advanced materials, digital monitoring capabilities, and pumps capable of handling challenging fluids with minimal maintenance. For instance, recent R&D initiatives center on improving rotor-stator geometries for higher efficiency and extended operational life, as well as integration with IoT platforms for predictive maintenance and remote monitoring.
Geographic expansion is another prominent trend, with manufacturers targeting high-growth regions in Asia-Pacific, the Middle East, and South America. Companies such as Grundfos and Kirloskar Brothers Limited are investing in new manufacturing facilities and service hubs to better serve local markets and reduce lead times. This localized approach is seen as critical for meeting the customization needs of diverse industries and addressing regional regulatory requirements.
Looking ahead, the outlook for investment in the helical rotor pump manufacturing sector remains positive. Industry participants are expected to continue leveraging M&A to acquire innovative technologies and expand their global footprint, while R&D spending is likely to focus on sustainability, digitalization, and enhanced performance. As end-user industries increasingly prioritize energy efficiency and reliability, manufacturers that invest in next-generation pump technologies and flexible production capabilities are poised to capture a greater share of the market over the next few years.
Future Outlook: Disruptive Trends and Strategic Recommendations
The helical rotor pump manufacturing sector is poised for notable transformation in 2025 and the following years, driven by disruptive trends in materials technology, digitalization, sustainability, and global supply chain strategies. Demand is anticipated to rise across industries such as wastewater management, oil and gas, food processing, and chemical manufacturing, with an increased focus on energy-efficient and low-maintenance solutions.
One of the most significant trends is the adoption of advanced materials and coatings to enhance pump durability, corrosion resistance, and performance under challenging conditions. Leading manufacturers are investing in research and development to optimize rotor and stator compositions, as seen in the product innovations of NORD Drivesystems and Sulzer. These advancements aim to extend service intervals and minimize downtime, which is critical for industries with continuous operation cycles.
Digitalization is another disruptive force reshaping manufacturing and lifecycle management. The integration of IoT-enabled sensors, predictive analytics, and remote monitoring platforms is becoming standard practice among major players like Kirloskar Brothers Limited and Grundfos. Such smart pumps enable real-time visibility into performance metrics, facilitating proactive maintenance and efficiency optimizations, which are especially valued as labor shortages and operational costs rise globally.
Sustainability considerations are influencing both product design and manufacturing processes. Companies are increasingly adopting energy-efficient motors and recyclable materials to align with stricter environmental regulations and customer expectations. For example, Voirtech and NOV have been spotlighted for developing pumps that minimize environmental impact, supporting broader goals in water conservation and reduced carbon emissions.
From a strategic perspective, manufacturers are urged to diversify their supplier base and invest in localized production capabilities to mitigate risks posed by geopolitical tensions and logistics disruptions. Partnerships and collaborations, such as those between equipment makers and digital solution providers, will be crucial for maintaining technological edge and market relevance.
In summary, the future outlook for helical rotor pump manufacturing suggests accelerated innovation in smart, efficient, and sustainable technologies. Companies that proactively invest in advanced materials, digital integration, and robust supply chains will be best positioned to capture growth and navigate disruptions in the coming years.