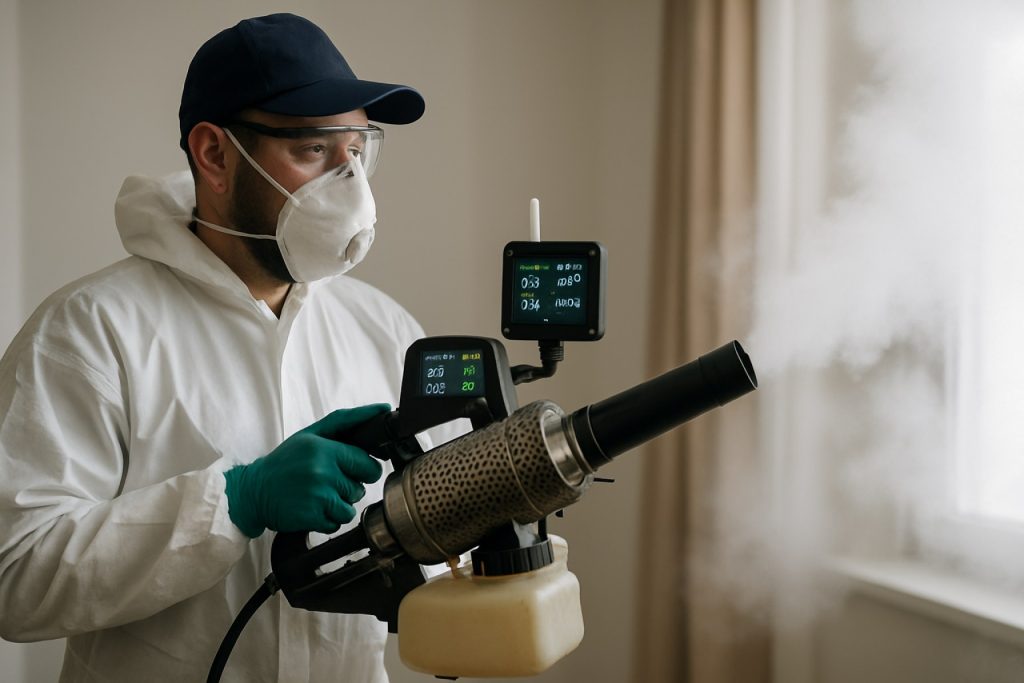
Table of Contents
- Executive Summary: Key Trends and Market Shifts in Fumigation Monitoring Sensors
- 2025 Market Size and Growth Forecast Through 2030
- Cutting-Edge Sensor Technologies: IoT, AI, and Real-Time Analytics
- Regulatory Drivers and Compliance Standards (EPA, ISO, etc.)
- Leading Manufacturers and Innovators (e.g., drager.com, honeywell.com)
- Deployment Challenges: Calibration, Integration, and Data Security
- Competitive Analysis: New Entrants vs. Established Brands
- End-User Insights: Agriculture, Warehousing, and Logistics Demand
- Sustainability and Environmental Impact: Next-Gen Solutions
- Future Outlook: Investment Hotspots and Anticipated Industry Disruptions
- Sources & References
Executive Summary: Key Trends and Market Shifts in Fumigation Monitoring Sensors
The development of fumigation monitoring sensors is experiencing rapid evolution in 2025, driven by stringent regulatory requirements, advancements in sensor technology, and the push for digital transformation in agriculture, logistics, and food safety. Growing concerns over efficacy, worker safety, and environmental impact are prompting stakeholders to adopt more accurate, real-time monitoring solutions. In response, major manufacturers and technology firms are expanding portfolios with sensors capable of detecting low concentrations of common fumigants such as phosphine, methyl bromide, and sulfuryl fluoride.
A notable trend in 2025 is the integration of wireless and IoT-enabled sensors, allowing for real-time data capture, remote monitoring, and automated compliance reporting. Companies like Drägerwerk AG & Co. KGaA and Honeywell International Inc. have introduced portable and fixed gas detection systems leveraging advanced electrochemical and photoionization technologies, designed for both indoor and outdoor fumigation scenarios. Their devices offer improved sensitivity and specificity, and are increasingly compatible with cloud-based dashboards for centralized control.
Regulatory momentum is another key driver. With more jurisdictions mandating continuous atmospheric monitoring during fumigation, sensor developers are prioritizing reliability, traceability, and automated alerting features. For instance, RIKEN KEIKI Co., Ltd. and MSA Safety Incorporated are investing in multi-gas detection platforms, tailored for compliance with evolving health and safety standards in sectors like grain storage, quarantine, and shipping.
Recent years have also seen increased collaboration between sensor manufacturers and fumigation service providers, aiming to integrate sensors directly into fumigation control systems. This trend is expected to intensify through 2025 and beyond, further enhancing operational safety and efficiency. Moreover, the miniaturization of sensor components, driven by MEMS and nanotechnology, is enabling the development of lightweight, wearable detection badges, expanding sensor deployment to personal protection and mobile inspection units.
Looking ahead, the outlook for fumigation monitoring sensor development is robust. The sector is poised for further growth as digital agriculture and smart logistics demand more granular, automated, and interoperable environmental monitoring. Strategic investments from established leaders and emerging startups alike suggest ongoing innovation, with a focus on connectivity, data analytics, and sustainability. As the market matures, ongoing collaboration with regulatory bodies and end-users will be pivotal in shaping future product standards and accelerating adoption.
2025 Market Size and Growth Forecast Through 2030
The market for fumigation monitoring sensor development in 2025 is positioned at a pivotal point, driven by increasing regulatory pressures, technological innovations, and heightened emphasis on food safety across global supply chains. The adoption of advanced sensors is accelerating due to stricter residue limits and occupational safety standards for fumigant gases such as phosphine, methyl bromide, and sulfuryl fluoride. In particular, industries involved in grain storage, food processing, and shipping are investing in real-time monitoring systems to ensure compliance and reduce risks associated with under- or over-fumigation.
Several leading sensor and analytical technology providers are actively expanding their fumigation-specific portfolios. Companies such as SICK AG and Drägerwerk AG & Co. KGaA are introducing new gas sensing modules with improved detection limits, wireless connectivity, and compatibility with IoT-based facility management systems. These developments are enabling more precise, automated monitoring across distributed sites, supporting the growing trend toward data-driven pest control management.
In 2025, the global market size for fumigation monitoring sensors is estimated to reach several hundred million USD, with Asia-Pacific and North America as leading regions in terms of adoption. Expansion in these markets is fueled by government initiatives for food safety and export quality assurance, as well as by the modernization of agricultural infrastructure. For instance, regulatory frameworks in countries such as the United States and Australia increasingly mandate gas concentration logging and exposure limit verification during fumigation, propelling demand for robust sensor solutions.
The market is also witnessing an influx of compact, portable, and multi-gas detectors developed by firms like Honeywell International Inc. and MSA Safety Incorporated. These devices are designed for ease of use by non-specialist personnel, reducing operational barriers for smaller operators and emerging markets. Furthermore, the integration of cloud-based analytics and remote monitoring capabilities by manufacturers is expected to enhance scalability and centralize compliance tracking.
Looking ahead to 2030, the fumigation monitoring sensor market is projected to sustain a compound annual growth rate (CAGR) in the high single digits, with opportunities expanding due to increasing automation in post-harvest logistics and stricter international trade standards. As the industry embraces predictive analytics and AI-driven alerts, sensor manufacturers with advanced digital and regulatory compliance features are likely to capture a larger share of the evolving market landscape.
Cutting-Edge Sensor Technologies: IoT, AI, and Real-Time Analytics
The development of fumigation monitoring sensors has advanced rapidly, with a strong focus on integrating IoT connectivity, AI-driven analytics, and real-time data capabilities. As of 2025, several industry leaders are deploying sensor solutions capable of tracking critical fumigant concentrations—such as phosphine, sulfuryl fluoride, and methyl bromide—across grain storage, shipping containers, and food processing facilities. These sensors are designed to ensure worker safety, regulatory compliance, and maximized fumigation efficacy.
Key players in gas detection and environmental monitoring, including Honeywell, MSA Safety Incorporated, and Dräger, have released multi-gas and single-gas sensors with digital output and wireless communications. Their latest models feature integrated IoT modules, enabling remote monitoring and automated reporting. For instance, Honeywell’s portable detectors can now interface with cloud platforms, providing real-time alerts and compliance documentation accessible from any internet-connected device. MSA’s solutions employ Bluetooth and Wi-Fi modules for continuous environmental surveillance, critical for both operational transparency and emergency response.
Artificial intelligence is becoming integral to sensor operations. AI algorithms analyze collected data to distinguish between typical background fluctuations and genuine hazardous events, thus reducing false positives and optimizing alarm thresholds. This is particularly valuable in large-scale storage applications, where spatial and temporal variability in gas concentrations can complicate manual monitoring. Companies such as Siemens are leveraging AI-based pattern recognition to anticipate potential leaks or incomplete gas dispersal, enabling preemptive action and minimizing downtime.
The trend toward real-time analytics is also reshaping fumigation safety protocols. Cloud-based dashboards, developed by major sensor manufacturers, provide facility managers with up-to-the-minute visualizations of gas concentrations and environmental conditions. These dashboards support automated record-keeping and facilitate compliance with evolving regulatory standards, such as those outlined by the U.S. Environmental Protection Agency (EPA) and equivalent international bodies.
Looking ahead into the next few years, sensor miniaturization and multi-parameter integration are expected to accelerate. Several manufacturers are investing in next-generation MEMS-based detectors and advanced electrochemical sensors that can be embedded directly into cargo holds or packaging. This, combined with the ongoing expansion of 5G networks, will further reduce latency in data transmission and broaden the scope for remote and autonomous fumigation monitoring. As AI algorithms mature, predictive maintenance and anomaly detection will likely become standard features, continually raising the bar for fumigation safety and efficiency.
Regulatory Drivers and Compliance Standards (EPA, ISO, etc.)
The development of fumigation monitoring sensors in 2025 is strongly influenced by evolving regulatory drivers and compliance standards set by organizations such as the US Environmental Protection Agency (EPA), the International Organization for Standardization (ISO), and national authorities across major agricultural economies. As global concerns over chemical safety, occupational exposure, and environmental emissions intensify, sensor technologies are increasingly required to provide greater accuracy, real-time data, and integration capabilities to meet new and updated compliance mandates.
One of the key regulatory drivers has been the EPA’s ongoing refinement of air quality and worker safety standards related to fumigant use, particularly for substances such as methyl bromide and phosphine. The EPA’s Risk Mitigation Decision for Soil Fumigants has led to stringent requirements for continuous air monitoring at fumigation sites, pushing manufacturers to develop sensors capable of detecting low parts-per-million concentrations and transmitting data in real time to supervisory systems (US Environmental Protection Agency). In 2025, these requirements are further reinforced by the EPA’s expanded focus on digital record-keeping and remote inspection capabilities, necessitating sensor platforms that support secure data logging and wireless connectivity.
On the international stage, ISO standards—specifically ISO 16000 for indoor air quality and ISO 21899 for traceability and measurement of gaseous fumigants—are shaping the technical specifications for sensor calibration, response times, and reporting accuracy. Compliance with these standards is increasingly a prerequisite for global market access, motivating companies to certify their sensors accordingly (International Organization for Standardization). Additionally, the European Union’s REACH regulation and the Biocidal Products Regulation (BPR) are setting interoperability and safety requirements that affect sensor design, especially for manufacturers seeking CE marking for products sold across Europe.
In response, leading manufacturers such as Honeywell and MSI Sensors are updating their product lines with enhanced detection ranges, IoT-ready modules, and automated calibration features, explicitly referencing regulatory compliance in their technical documentation. Industry bodies, such as the Association of Equipment Manufacturers, are also publishing best practice guidelines to ensure member companies align with both EPA and ISO requirements.
Looking ahead, the regulatory landscape is expected to become even more rigorous as governments incorporate climate and sustainability targets into chemical management policy. Sensor developers will likely face new mandates for data transparency, cloud integration, and third-party certification, driving a wave of innovation in both hardware and software to ensure future-proof compliance.
Leading Manufacturers and Innovators (e.g., drager.com, honeywell.com)
The development of advanced fumigation monitoring sensors has accelerated in 2025 as regulatory bodies and industry clients increasingly demand higher accuracy, real-time data, and improved safety in pest control and commodity treatment environments. Key manufacturers and technology innovators continue to shape this sector, focusing on solutions that address both traditional fumigants such as phosphine and methyl bromide, as well as newer, less toxic alternatives.
Drägerwerk AG & Co. KGaA, widely recognized for its expertise in gas detection technologies, remains at the forefront of fumigation sensor development. In 2025, Dräger is expanding its range of portable and fixed gas detection systems specifically tailored to the demands of agricultural and logistics applications. Their sensors now incorporate enhanced selectivity algorithms and wireless connectivity, enabling operators to receive real-time exposure data, which is critical for both occupational safety and regulatory compliance.
Similarly, Honeywell International Inc. continues to advance its sensor technology portfolio with an emphasis on miniaturization and cloud integration. Honeywell’s sensors are widely adopted for continuous monitoring of fumigant gases in storage silos, shipping containers, and food processing facilities. Their latest models offer multi-gas detection with digital calibration, supporting remote diagnostics and predictive maintenance—features that are increasingly standard as part of Industry 4.0 initiatives.
Another notable innovator, MSA Safety Incorporated, is leveraging its expertise in industrial safety solutions by delivering robust, easy-to-deploy fumigation sensors. MSA Safety’s devices are designed to withstand harsh chemical environments, and recent upgrades in sensor longevity and data logging are intended to support compliance with tightening international fumigation regulations.
In parallel, sensor manufacturers such as Industrial Scientific Corporation and RKI Instruments, Inc. are introducing smart sensors equipped with Bluetooth and IoT integration, enabling seamless data transfer and centralized monitoring. Both Industrial Scientific and RKI Instruments are actively collaborating with logistics providers and fumigation service companies to deploy networked sensor arrays, offering enhanced traceability and auditing capabilities.
Looking ahead, the outlook for fumigation monitoring sensor development remains robust. Manufacturers are expected to further integrate artificial intelligence and advanced analytics into their platforms, supporting predictive exposure assessment and automated reporting. As global standards for food safety and worker protection continue to evolve, the adoption of these next-generation sensors is set to become a baseline requirement for responsible fumigation operations.
Deployment Challenges: Calibration, Integration, and Data Security
The development and deployment of fumigation monitoring sensors in 2025 face a complex set of challenges related to calibration, integration, and data security. As the demand for precise, real-time environmental monitoring in fumigation processes grows, manufacturers are under increasing pressure to address these critical issues to ensure both regulatory compliance and operational efficiency.
Calibration remains a primary challenge, as sensor accuracy is paramount in detecting low-level concentrations of fumigants like phosphine and methyl bromide. Many leading sensor manufacturers, such as Sensirion and Honeywell, have rolled out advanced gas detection platforms with factory calibration and self-diagnostic features. However, real-world environments introduce variable humidity, temperature, and cross-sensitivity to other gases, often requiring frequent field recalibration. In 2025, there is a growing emphasis on automated or remote calibration routines to reduce downtime, with some companies integrating cloud-based calibration management to streamline compliance and minimize human error.
Integration with existing process control systems is another significant hurdle. Many fumigation facilities operate legacy infrastructure that is not natively compatible with modern IoT-based sensor platforms. Companies like Siemens and Emerson Electric are addressing this through the development of modular sensor systems with open communication protocols, such as OPC UA and Modbus TCP, which facilitate smoother integration into diverse automation environments. Additionally, there is a trend towards edge computing, where data from sensors is processed locally for immediate response, reducing dependence on centralized data centers and enhancing system reliability.
Data security concerns are intensifying as sensor networks become more interconnected. The risk of cyberattacks on industrial IoT devices has prompted sensor manufacturers and users to prioritize secure data transmission and storage. In 2025, best practices include end-to-end encryption, secure boot firmware, and regular security patching. Organizations such as Schneider Electric and ABB are incorporating cybersecurity frameworks aligned with international standards (e.g., IEC 62443) into their sensor solutions. The outlook for the next few years points towards increased regulatory scrutiny and mandatory certification for connected environmental sensors used in critical applications like fumigation.
As the sector advances, the successful deployment of fumigation monitoring sensors will hinge on continued progress in automated calibration, flexible integration with diverse operational platforms, and robust, standards-driven cybersecurity measures. These factors are set to shape the competitive landscape and adoption rate of sensor technologies in the fumigation industry through 2025 and beyond.
Competitive Analysis: New Entrants vs. Established Brands
The fumigation monitoring sensor landscape in 2025 is witnessing notable dynamism as both established brands and nimble new entrants compete to deliver reliable, precise, and regulatory-compliant solutions. Established leaders such as Honeywell and Siemens have long dominated the industrial gas detection and monitoring market, leveraging decades of R&D, robust global distribution, and integration with industrial automation platforms. Their fumigation sensor portfolios emphasize accuracy, robust calibration, and seamless connectivity with industrial control systems, addressing the needs of large-scale storage, logistics, and agricultural operations.
However, the past 12–24 months have seen a surge of smaller companies and start-ups focusing on advanced sensor technologies tailored specifically to fumigation applications. These new entrants, such as Sensirion and Amphenol, are leveraging miniaturized MEMS, real-time wireless networking, and IoT-enabled data analytics to address emerging market requirements. They are capitalizing on growing regulatory scrutiny that demands more granular, real-time monitoring, as well as customer demand for user-friendly, mobile-enabled platforms.
Key events driving competition include the acceleration of digital transformation initiatives and stricter fumigant exposure regulations in North America, Europe, and Asia-Pacific. Established firms are scaling up with cloud-based data services and AI-powered analytics—Honeywell, for instance, has enhanced its ecosystem to provide predictive maintenance and compliance reporting for fumigant gas monitoring. Meanwhile, new entrants are rolling out compact, battery-powered multi-gas sensors that can be rapidly deployed in smaller facilities or remote locations, and often at a lower cost point.
Data suggests that while established brands retain a stronghold in sectors requiring system-wide integration, new entrants are gaining traction in specialized applications—such as portable monitoring for shipping containers or rapid on-site detection for pest control operators. Industry alliances and technology licensing deals are also on the rise, with major players seeking partnerships with start-ups to accelerate innovation cycles and address gaps in their product lines.
Looking ahead to the next few years, the competitive landscape is expected to intensify. Integration with cloud platforms, AI-driven analytics, and edge computing for real-time alerts will be pivotal differentiators. Regulatory harmonization and sustainability pressures may further favor agile, innovation-driven firms that can swiftly adapt to evolving standards. However, established brands are likely to maintain their lead in large-scale and highly regulated projects, provided they continue to innovate and form strategic partnerships.
End-User Insights: Agriculture, Warehousing, and Logistics Demand
The demand for advanced fumigation monitoring sensors is intensifying within the agriculture, warehousing, and logistics sectors, driven by regulatory requirements, food safety imperatives, and supply chain modernization. In 2025, end-users are increasingly prioritizing real-time, precise detection of fumigants such as phosphine, methyl bromide, and sulfuryl fluoride to ensure both compliance and operational efficacy.
Within agriculture, post-harvest grain protection is a critical use case. Farmers and grain storage operators seek sensors capable of providing continuous, in-situ measurements to avoid under- or over-fumigation, which can lead to pest survival or product contamination respectively. Companies such as Micro Sensor Co., Ltd. and Sensirion AG are responding with miniaturized, robust gas sensors designed for harsh environments typically found in grain silos and storage bins. These sensors enable remote monitoring, reducing the need for manual sampling and exposure risks for workers.
In warehousing and food processing facilities, quality control managers emphasize the role of fumigation sensors in maintaining residue levels below regulatory thresholds. Automated, network-connected sensor solutions are being integrated with facility management systems, a trend supported by global automation providers like Siemens AG, which offers industrial measurement and control technologies suitable for hazardous gas monitoring. The adoption of smart sensors helps warehouses comply with increasingly strict food safety standards while minimizing downtime during fumigation cycles.
The logistics sector, particularly companies involved in containerized shipping and cross-border transport, faces mounting pressure to document the absence of residual fumigants before customs clearance. Portable, fast-response sensors are now a requirement for logistics providers, who must track and certify air quality in real time. Solutions from firms such as Honeywell International Inc. and Drägerwerk AG & Co. KGaA are being deployed for rapid spot-checking during container inspections, and adoption is projected to accelerate as international regulations evolve.
Looking forward, end-users are expected to demand even greater integration between fumigation monitoring sensors and digital traceability platforms. Cloud-enabled data sharing, predictive analytics, and automated compliance reporting are key areas of interest for 2025 and beyond. As these sectors continue to digitize their operations, sensor manufacturers will face strong expectations for interoperability and cybersecurity, alongside core performance metrics such as sensitivity, selectivity, and robustness.
Sustainability and Environmental Impact: Next-Gen Solutions
The evolution of fumigation monitoring sensor technology is reshaping approaches to sustainability and environmental compliance in post-harvest and structural pest management. As regulations tighten on fumigant emissions and worker exposure, the industry is accelerating the deployment of advanced sensing solutions that enable real-time, in-situ measurement of key fumigants such as phosphine, sulfuryl fluoride, and methyl bromide alternatives. Recent years have seen a transition from traditional manual sampling to fully integrated sensor networks, with expectations for significant commercialization and adoption through 2025 and beyond.
Leading sensor manufacturers are focusing on enhancing detection sensitivity, selectivity, and connectivity. For example, Drägerwerk AG & Co. KGaA has continued development of portable and stationary gas detection systems tailored for fumigation environments, emphasizing rapid response times and high specificity to hazardous fumigants. Similarly, Honeywell International Inc. and MSA Safety Incorporated are expanding their range of wireless and IoT-enabled detectors, aiming to support continuous monitoring and integration with digital compliance platforms.
A notable trend in 2025 is the integration of low-power, miniaturized sensors—often based on electrochemical, photoionization, or spectroscopy techniques—into smart logistics and warehouse management systems. These sensors provide granular data on gas concentration dynamics, supporting both immediate safety measures and long-term emission reduction strategies. For instance, Sensirion AG is advancing compact gas sensors designed for precise measurement of trace-level fumigants, facilitating both mobile and fixed monitoring solutions.
The push toward sustainability is also driving the adoption of cloud-connected platforms, enabling centralized oversight, automated alerts, and regulatory reporting. This digital transformation is expected to intensify over the next few years, as supply chain actors face increasing demands for transparency and proof of compliance with environmental standards. Sensor manufacturers are responding by incorporating AI-driven analytics and predictive maintenance features to reduce false alarms and optimize sensor lifespan.
Looking ahead, the sector anticipates that next-generation sensors will not only meet stricter occupational exposure limits and emission caps, but also support the transition to alternative, lower-impact fumigants and non-chemical treatments. The collaboration between technology developers, regulatory authorities, and major industry users is likely to expand, fostering continued innovation. As a result, monitoring sensor development will remain a cornerstone of sustainable fumigation practices through 2025 and the years immediately following.
Future Outlook: Investment Hotspots and Anticipated Industry Disruptions
The global push for improved food safety, stricter environmental regulations, and the digital transformation of agriculture is accelerating innovation in fumigation monitoring sensor development. As of 2025, investment is flowing into technologies that promise to make fumigation processes more transparent, efficient, and sustainable. Several key trends and anticipated disruptions are shaping this sector.
One prominent investment hotspot is the integration of Internet of Things (IoT) technologies with sensor platforms. Companies are leveraging miniaturized, low-power gas sensors that can be deployed across storage facilities and shipping containers to provide real-time, remote measurement of fumigant concentrations. For example, Honeywell and Siemens are expanding their industrial sensor portfolios to include specialized gas detection solutions tailored for agricultural storage and logistics, where real-time monitoring is critical for compliance and safety.
Another focus area is the development of multi-gas sensors capable of detecting a range of fumigants—such as phosphine, methyl bromide, and sulfuryl fluoride—simultaneously. This is driven by regulatory bodies increasingly mandating the documentation and limitation of exposure during fumigation processes. Sensor developers like Drägerwerk AG are enhancing their offerings with advanced electrochemical and photoionization detectors that deliver higher sensitivity and selectivity.
Artificial intelligence (AI) and machine learning are emerging as disruptors in this space, supporting predictive maintenance and advanced analytics for fumigation operations. By analyzing sensor data in real time, these systems can optimize fumigant dosing and ventilation protocols, reducing chemical use and minimizing environmental impact. Companies such as Bosch are actively researching AI-powered monitoring solutions for industrial applications, including agricultural supply chains.
Looking ahead, the next few years are expected to see increased collaboration between sensor manufacturers, fumigation service providers, and regulatory agencies to develop standardized, interoperable monitoring systems. Efforts to create wireless, battery-operated, and intrinsically safe sensors will remain a priority, especially for use in remote or hazardous environments. Additionally, there is growing interest in integrating blockchain technology for secure traceability of fumigation data, particularly in cross-border grain and produce shipments.
In summary, the convergence of IoT, AI, and advanced sensor technology is poised to transform fumigation monitoring. The most significant investment opportunities will likely be in platforms that combine real-time multi-gas detection, predictive analytics, and robust data integration, setting new industry benchmarks for safety and regulatory compliance.