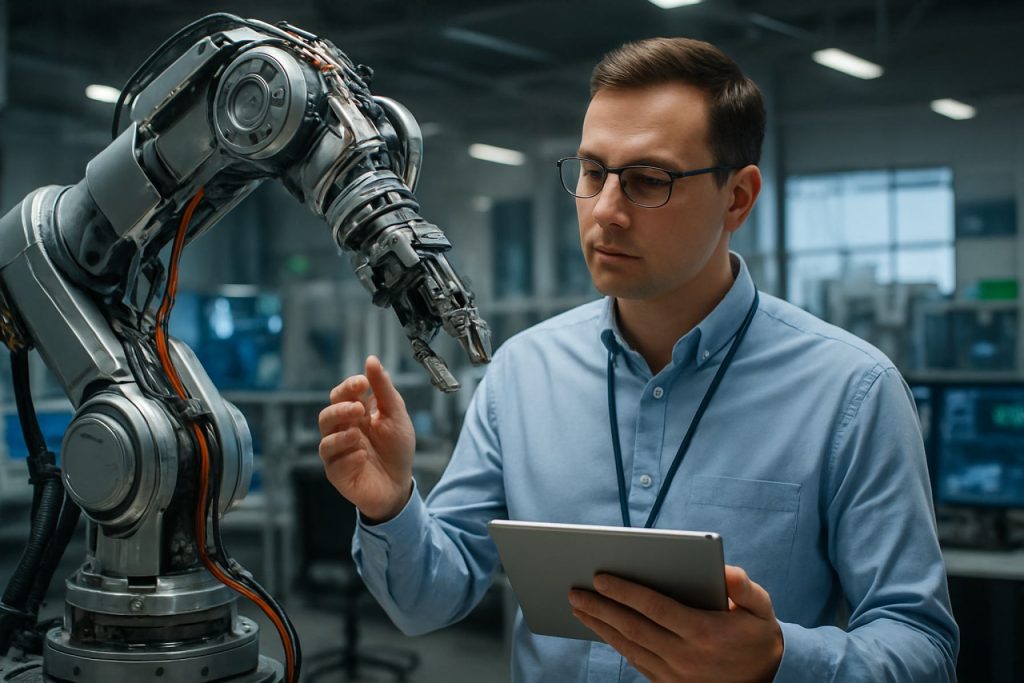
Table of Contents
- Executive Summary: Defining Workflow Kinematics Engineering in 2025
- Market Size & Growth Forecast: 2025–2030 Projections
- Key Industry Players and Strategic Alliances
- Emerging Technologies: AI, Robotics, and Digital Twins
- Sector Applications: Manufacturing, Healthcare, and Beyond
- Competitive Landscape and Barriers to Entry
- Regulatory Frameworks and Industry Standards
- Investment Trends and Funding Hotspots
- Challenges, Risks, and Resilience Strategies
- Vision 2030: Future Outlook and Game-Changing Innovations
- Sources & References
Executive Summary: Defining Workflow Kinematics Engineering in 2025
In 2025, Workflow Kinematics Engineering stands at the intersection of automation, robotics, artificial intelligence (AI), and process optimization, redefining how tasks and operations flow within industrial and enterprise environments. The discipline focuses on modeling, analyzing, and optimizing the dynamic movement of work elements—whether physical materials, digital information, or hybrid assets—across complex, interconnected systems. This approach aims to enhance productivity, minimize resource consumption, and deliver adaptive, resilient workflows that respond to real-time data and operational contingencies.
Recent advances in industrial automation and robotics are central to this evolution. Major manufacturers such as Siemens and FANUC have introduced next-generation controllers and intelligent robotics platforms, enabling finer-grained monitoring and adaptive orchestration of workflows on factory floors. These systems increasingly leverage edge computing and industrial IoT, allowing kinematic models of workflows to be updated dynamically as conditions change. Meanwhile, digital twin technologies—championed by companies like PTC—enable continuous simulation and optimization of workflow kinematics, reducing downtime and improving throughput across supply chains.
In the software domain, platforms from firms such as SAP and Oracle are integrating AI-powered process mining and workflow automation with real-time data streams. This convergence allows organizations to precisely map, analyze, and optimize the “motion” of digital tasks as they traverse enterprise systems, identifying bottlenecks and inefficiencies previously hidden in static process diagrams.
Throughout 2025 and into the coming years, several trends are expected to shape the field. First, the deployment of collaborative robots (cobots) and autonomous mobile robots (AMRs) is expanding rapidly, driven by manufacturers like ABB and KUKA. These systems not only automate physical workflows but also generate rich kinematic data, feeding back into continuous improvement cycles. Second, the integration of AI-powered vision and sensor technologies is allowing for real-time adjustment of workflow kinematics in response to changing environments, a capability being advanced by OMRON Corporation and others.
Looking ahead, the outlook for Workflow Kinematics Engineering is marked by increasing convergence between physical and digital domains, underpinned by adaptive control systems and pervasive data analytics. Enterprises that harness these developments are likely to realize significant gains in operational agility, responsiveness, and efficiency, positioning Workflow Kinematics Engineering as a foundational pillar of next-generation industrial and business operations.
Market Size & Growth Forecast: 2025–2030 Projections
The market for Workflow Kinematics Engineering is poised for robust growth between 2025 and 2030, driven by rapid advancements in automation, robotics, and digital process optimization across manufacturing, logistics, and healthcare sectors. In 2025, global investments in workflow kinematics solutions—encompassing robotic arms, automated guided vehicles (AGVs), digital twin software, and motion planning systems—are expected to surpass $20 billion, fueled by rising demand for interconnected and adaptive factory floors.
Major industrial automation players such as Siemens, ABB, and FANUC are expanding their workflow kinematics portfolios, integrating sensor fusion, AI-driven motion control, and edge computing capabilities. These innovations are enabling manufacturers to achieve real-time process optimization, predictive maintenance, and safer human-robot collaboration. Similarly, logistics companies are adopting autonomous mobile robots (AMRs) and advanced conveyor kinematics to streamline handling and fulfillment operations—a trend strongly championed by KUKA and OMRON.
The outlook for 2025–2030 indicates a compound annual growth rate (CAGR) estimated at 10–14%, with Asia-Pacific and North America leading adoption due to strong manufacturing bases and digital infrastructure investments. Sectors such as automotive, electronics, and consumer goods are projected to remain the largest end-users, while healthcare and pharmaceuticals are expected to contribute significantly to demand growth, leveraging workflow kinematics for laboratory automation and precision logistics. Notably, Bosch Rexroth and Yaskawa Electric Corporation are actively innovating solutions for flexible assembly lines and adaptive kinematic configurations.
- Key market events (2025): Launch of new collaborative robot lines with enhanced force and motion sensing; expansion of cloud-based kinematics simulation platforms; and strategic partnerships between automation vendors and enterprise software providers.
- Data trends: Adoption rates of workflow kinematics engineering tools are highest in greenfield smart factories, where digital twins and real-time kinematics simulation are being integrated from the ground up.
- Outlook: By 2030, the market is expected to approach $40 billion, with convergence of AI, IoT, and advanced kinematics engineering driving hyperautomation and decentralized decision-making on factory floors.
Industry stakeholders are thus rapidly scaling investments to capture emerging opportunities, focusing on interoperability, ease of integration, and safety standards to enable the next generation of flexible, intelligent, and autonomous workflow systems.
Key Industry Players and Strategic Alliances
The landscape of workflow kinematics engineering in 2025 is shaped by both established automation leaders and emerging innovators, all vying to optimize motion, process control, and robotic integration across diverse industries. Key players such as Festo, Siemens, and ABB continue to advance modular kinematic solutions, leveraging their expertise in pneumatics, robotics, and digital automation. These organizations are focusing on adaptable, scalable systems designed to meet the evolving requirements of manufacturing, logistics, and healthcare operations.
Strategic alliances have become a central theme, with companies forming partnerships to accelerate innovation and interoperability. For instance, Rockwell Automation and FANUC maintain their longstanding collaboration to integrate intelligent robotic kinematics and edge analytics, targeting seamless workflow orchestration in smart factories. Additionally, ABB and Bosch Rexroth are advancing open industrial automation platforms that combine advanced motion control with AI-driven optimization, enhancing both the speed and precision of interconnected kinematic systems.
In the realm of software-driven workflow engineering, Siemens is pushing its Totally Integrated Automation (TIA) platform, which tightly couples kinematic modeling, simulation, and real-time control. This approach enables enterprises to virtually prototype workflows before physical deployment, reducing downtime and enabling rapid adaptation to changing production demands. Similarly, Festo is expanding its digital twin capabilities, allowing for predictive maintenance and continuous process improvement through real-time kinematic feedback loops.
Emerging players are also making waves by specializing in collaborative robotics (cobots) and flexible workflow modules. Companies like Universal Robots and KUKA are entering new strategic partnerships to integrate AI-based motion planning, fostering safer human-robot collaboration and adaptive process engineering. These alliances are expected to proliferate as more sectors—from electronics assembly to pharmaceuticals—require agile, networked kinematic solutions.
Looking ahead, the industry is poised for further consolidation and cross-sector alliances, particularly as Industry 4.0 standards mature and demand for interoperable kinematics surges. The next few years will likely see intensified collaboration among automation heavyweights, digital platform providers, and specialized robotics firms, driving greater standardization, plug-and-play integration, and workflow intelligence across global supply chains.
Emerging Technologies: AI, Robotics, and Digital Twins
Workflow Kinematics Engineering is undergoing rapid transformation in 2025, driven by the convergence of artificial intelligence (AI), robotics, and digital twin technologies. These advancements are reshaping the design, optimization, and automation of industrial workflows, from manufacturing assembly lines to logistics and supply chains.
A defining event in recent years has been the widespread deployment of AI-powered motion planning and real-time optimization in robotic systems. Companies such as FANUC and KUKA have integrated advanced machine learning algorithms in their industrial robots, enabling dynamic adaptation to changing workflow conditions. These robots now leverage sensor fusion and predictive analytics to adjust their kinematic paths in real time, improving both efficiency and safety on the factory floor.
Digital twin technology has also become central to workflow kinematics. Digital twins—virtual replicas of physical assets—are now used not only for visualization, but also for continuous optimization and predictive maintenance. Siemens and Schneider Electric have expanded their digital twin platforms, allowing engineers to simulate and tweak kinematic sequences before deploying changes to physical systems. This reduces downtime, improves throughput, and enables more agile responses to supply chain disruptions.
Data from 2024 and early 2025 indicates a measurable increase in the adoption of cloud-based collaborative engineering tools, further accelerating workflow optimization cycles. For example, ABB has launched cloud-enabled solutions that connect robots, controllers, and digital twins, allowing seamless monitoring and adjustment of workflow kinematics from remote locations.
Looking ahead, several trends are expected to shape the sector over the next few years. The integration of generative AI will enable automated workflow design, with algorithms proposing novel kinematic sequences that maximize efficiency and minimize energy consumption. Robotics platforms are anticipated to become increasingly modular and interoperable, supporting plug-and-play workflow reconfiguration. Digital twins will continue to evolve, incorporating richer real-time data streams and enhanced physics-based modeling.
The outlook for Workflow Kinematics Engineering is one of growing intelligence, adaptability, and resilience. As AI, robotics, and digital twins mature and converge, industries are poised to realize unprecedented gains in productivity and operational agility, setting new standards for the optimization and automation of complex workflows.
Sector Applications: Manufacturing, Healthcare, and Beyond
Workflow Kinematics Engineering, which involves the study and optimization of movement and process flows within complex systems, is rapidly reshaping sector applications across manufacturing, healthcare, and adjacent industries. The focus on intelligent motion and process orchestration is driven by increasing demands for productivity, safety, and adaptability amid evolving technological landscapes.
In manufacturing, Workflow Kinematics Engineering is at the core of digital transformation initiatives. Smart factories are adopting advanced robotics, collaborative automation, and digital twins to streamline both human and machine workflows. Companies such as Siemens and FANUC are leading the development of kinematically optimized systems that synchronize robots, AGVs, and human operators, minimizing idle time and reducing bottlenecks. By 2025, widespread integration of real-time motion analytics and adaptive scheduling is expected to enable dynamic adjustments to production lines, enhancing throughput and flexibility, particularly in automotive, electronics, and consumer goods sectors.
In healthcare, Workflow Kinematics Engineering is enabling new models of care delivery and process optimization. Hospitals and clinics are deploying autonomous mobile robots for supply chain logistics, disinfection, and patient transport, with companies like OMRON and ABB providing kinematically advanced solutions. In surgical settings, the precise kinematics of robotic-assisted systems, such as those developed by Intuitive Surgical, are being integrated with workflow automation platforms to optimize procedure sequencing, instrument tracking, and staff coordination. This not only improves operational efficiency but also elevates patient safety and care quality.
Beyond manufacturing and healthcare, Workflow Kinematics Engineering is finding applications in logistics, warehousing, and even entertainment. Major logistics providers are investing in intelligent robotic picking and sorting systems that leverage kinematic modeling for faster, more accurate material handling. Companies like KUKA are deploying these solutions in large distribution centers to meet the surging demand for e-commerce fulfillment. In theme parks and live events, advanced mechatronic systems are choreographing complex motion sequences for rides and stage performances, ensuring both safety and creative flexibility.
Looking ahead to the next few years, continued advancements in sensors, AI-driven motion planning, and interoperability standards are set to expand the scope and impact of Workflow Kinematics Engineering. The growing adoption of open-source kinematic libraries and cross-sector collaboration will enable broader accessibility and innovation. Organizations that effectively harness these developments will be well-positioned to achieve significant gains in productivity, resilience, and user experience across diverse domains.
Competitive Landscape and Barriers to Entry
The competitive landscape of Workflow Kinematics Engineering in 2025 is characterized by a convergence of automation, robotics, and advanced software platforms, with a handful of established players and nimble emerging firms shaping market dynamics. This sector underpins the optimization of movement, sequencing, and orchestration in automated workflows, particularly within manufacturing, logistics, and smart facilities.
Major industrial automation and robotics companies continue to hold significant influence, leveraging deep expertise in mechatronics, motion control, and integration. Entities such as Siemens, ABB, and FANUC have expanded their workflow kinematics offerings with new digital twin environments, AI-powered motion planning, and modular systems compatible with Industry 4.0 standards. These incumbents benefit from extensive R&D resources, global service networks, and longstanding relationships with large industrial clients.
In parallel, software-centric companies are intensifying competition by focusing on interoperability, simulation, and cloud-based orchestration—key differentiators in workflow kinematics. For example, Rockwell Automation and Schneider Electric are integrating workflow kinematics modules into their industrial automation suites, enabling real-time optimization and predictive maintenance. The trend toward open standards and API-driven architectures has lowered some integration barriers, but proprietary protocols and legacy systems remain obstacles for new entrants.
Barriers to entry in this field remain substantial despite the increasing modularity of components and platforms. Key hurdles include:
- Technological Complexity: Mastery of both physical kinematics and digital orchestration requires multidisciplinary expertise, high upfront investment, and access to advanced testing environments.
- Intellectual Property: Leading companies hold extensive patents on kinematic algorithms, motion control hardware, and workflow simulation tools.
- Certification and Compliance: Adherence to international safety, interoperability, and cybersecurity standards—such as those maintained by ISO—is mandatory and often resource-intensive.
- Customer Entrenchment: Industrial clients typically favor proven, scalable solutions with established vendor support, making it challenging for new players to displace incumbents.
Looking forward, the market is expected to see increased collaboration between hardware and software specialists, further blurring traditional boundaries. Startups focusing on AI-driven kinematic optimization and cloud-native workflow engines may carve out niche opportunities, but they will likely need to partner with or be acquired by established firms to scale effectively. As automation deepens across sectors, competitive intensity will rise alongside the demand for secure, interoperable, and highly adaptive workflow kinematics solutions.
Regulatory Frameworks and Industry Standards
As Workflow Kinematics Engineering becomes increasingly integral to the automation and optimization of industrial and manufacturing processes, the regulatory frameworks and industry standards governing this sector are evolving rapidly in 2025. Regulatory efforts are focusing on safety, interoperability, data integrity, and cybersecurity, which are essential to ensure reliable and scalable deployment of kinematic systems in diverse workflows.
A significant development is the harmonization of safety protocols for robotic motion and collaborative automation systems. Regulatory bodies such as the International Organization for Standardization (ISO) and the International Electrotechnical Commission (IEC) are updating standards like ISO 10218 (Robots and robotic devices – Safety requirements for industrial robots) and IEC 61508 (Functional safety of electrical/electronic/programmable electronic safety-related systems) to address the growing complexity of kinematics within integrated workflow platforms. These standards are being revised to reflect the latest advances in sensor fusion, machine learning-based motion planning, and human-robot collaboration, with anticipated ratification of new amendments by late 2025.
Interoperability has emerged as a critical regulatory priority. Organizations such as the OPC Foundation are leading efforts to standardize communication protocols for workflow kinematics components, enabling seamless integration of robots, automated guided vehicles (AGVs), and other motion-centric automation devices from different vendors. The OPC UA (Unified Architecture) protocol is being extended to encapsulate richer kinematic data models, facilitating standardized exchange of motion parameters and status information between diverse platforms.
Data security and traceability within workflow kinematic systems are also under increased regulatory scrutiny. Industry groups like ODVA are updating the EtherNet/IP protocol specifications to include enhanced security features and authenticated motion command sequences, complying with new cyber-resilience directives being rolled out in the European Union and North America. These updates are expected to become de facto requirements for manufacturers seeking to deploy kinematic solutions in critical infrastructure and high-reliability sectors over the next few years.
Looking ahead, the convergence of artificial intelligence with workflow kinematics is prompting preemptive regulatory action. Committees at ISO and IEC are forming new working groups to address ethical, safety, and transparency guidelines for AI-driven motion control in workflows. Industry consensus is that by 2027, a new generation of standards will emerge, directly addressing the lifecycle management, auditability, and explainability of autonomous kinematic systems, ensuring both compliance and public trust in these transformative technologies.
Investment Trends and Funding Hotspots
Investment in Workflow Kinematics Engineering—the discipline at the intersection of process automation, robotics, and motion systems—is accelerating in 2025, with capital flowing into both established players and innovative startups. This surge is driven by the demand for seamless integration of robotics, AI, and digital workflow solutions across manufacturing, logistics, and healthcare sectors.
A clear hotspot is the industrial automation sector, where companies are leveraging workflow kinematics to optimize production lines and reduce downtime. Siemens has announced expanded investment in its Digital Industries division, focusing on advanced kinematic simulation tools and adaptive motion control for smart factories. Similarly, FANUC Corporation continues to allocate substantial R&D budgets toward enhancing robot kinematics for high-precision, collaborative tasks.
Startups specializing in workflow kinematics software and sensor integration are attracting significant venture capital. Investment groups have shown a strong preference for companies developing digital twin platforms and AI-driven motion planning, reflecting the need for flexible and resilient workflows. Notably, ABB Ltd has launched a venture fund aimed at early-stage companies innovating in adaptive robotics and cloud-based workflow orchestration.
Geographically, the United States, Germany, China, and Japan remain leading funding hotspots. In 2025, Europe is witnessing increased public-private partnerships to bolster workflow kinematics research, especially around the EU’s Industry 5.0 vision. German automation clusters, anchored by companies like KUKA, are receiving substantial government and industry co-investment to accelerate the adoption of modular, reconfigurable kinematic systems in both automotive and electronics manufacturing.
- In Asia, the Chinese government is channeling investment into next-generation manufacturing, with companies such as Estun Automation scaling up research in multi-axis motion control and digital workflow integration.
- Japan’s robotics leaders, including Yaskawa Electric Corporation, report increased funding for collaborative robot arms and AI-enhanced kinematics aimed at logistics and healthcare automation.
The outlook for the next several years suggests continued strong investment as industries pursue higher efficiency and adaptability. With global supply chain pressures and workforce shortages, workflow kinematics engineering is positioned as a key enabler for automation and operational resilience, driving further capital inflows and public funding initiatives worldwide.
Challenges, Risks, and Resilience Strategies
Workflow kinematics engineering, which focuses on the systematic optimization and automation of process flows across industrial and enterprise environments, faces a dynamic landscape of challenges and risks as it moves into 2025 and the years ahead. The increasing complexity of interconnected systems, coupled with the rapid adoption of digitalization and smart automation, shapes the core of these challenges.
A prominent risk is the integration of legacy systems with advanced automation platforms. Many enterprises continue to operate with a mix of outdated machinery and cutting-edge digital solutions, resulting in interoperability gaps. This can lead to inefficiencies, increased downtime, and security vulnerabilities. For instance, organizations implementing advanced robotic process automation (RPA) must ensure seamless communication between old and new systems, a challenge recognized by automation leaders such as Siemens and ABB.
Cybersecurity is another major concern as workflow kinematics engineering increasingly relies on connected devices and cloud-based platforms. The expanded attack surface exposes workflows to potential breaches, data leaks, and operational disruptions. In response, industry bodies like the International Organization for Standardization are strengthening standards for secure industrial communications and process integrity.
Supply chain volatility—exacerbated by geopolitical tensions and ongoing global disruptions—presents further risks. The reliability of hardware components, software updates, and skilled labor can all impact workflow continuity. Companies such as Rockwell Automation are addressing these vulnerabilities by emphasizing resilient system architectures and promoting predictive maintenance strategies to anticipate and mitigate failures before they disrupt operations.
To build resilience, organizations are investing in digital twins, simulation platforms, and AI-driven analytics. These technologies allow for real-time monitoring, scenario planning, and proactive response to disruptions. Digital twin platforms, exemplified by solutions from Siemens, enable continuous optimization and risk assessment of physical workflows without halting production.
Looking forward, the focus for workflow kinematics engineering will be on adaptive systems capable of self-healing, self-optimization, and cyber-physical convergence. Strategic collaboration with technology providers, adherence to evolving international standards, and ongoing workforce upskilling will be critical to managing current and emerging risks. The industry outlook anticipates increased investment in modular, scalable architectures that can flexibly respond to unforeseen challenges while sustaining productivity and security.
Vision 2030: Future Outlook and Game-Changing Innovations
As industries increasingly seek to optimize productivity and flexibility, the field of Workflow Kinematics Engineering is undergoing transformative change. By 2025, the convergence of advanced robotics, real-time data analytics, and AI-driven automation is shaping a new era for manufacturing, logistics, and service sectors. The vision for 2030 centers on the integration of intelligent kinematic systems that adapt dynamically to changing workflow demands, with innovations already taking root in several sectors.
A leading trend is the proliferation of collaborative robots (cobots) and autonomous mobile robots (AMRs) designed for adaptive workflow orchestration. Companies such as KUKA and FANUC are deploying kinematic systems that can reconfigure motion paths and task sequences in real time, responding to shifts in production requirements or supply chain disruptions. These developments are enabled by advances in sensor technology, machine learning algorithms, and high-speed wireless connectivity, allowing robots to function as integral, flexible components of human-machine teams.
Looking ahead, the next few years will see the maturation of digital twin technology as a central pillar of workflow kinematics. Digital twins—virtual replicas of physical processes—are increasingly being adopted for simulation, optimization, and predictive maintenance. Organizations like Siemens are at the forefront, leveraging digital twins to synchronize kinematic workflows across distributed manufacturing sites, enhancing both efficiency and resilience.
Meanwhile, the integration of edge computing and Industrial Internet of Things (IIoT) architectures is poised to further elevate workflow kinematics. Real-time data collected from sensors embedded in machines, conveyors, and robotic arms enable granular monitoring and rapid decision-making. Companies such as ABB are advancing IIoT-enabled platforms that provide insights into motion control, downtime analysis, and energy optimization.
By 2030, experts anticipate a paradigm shift toward fully autonomous, self-optimizing workflows, underpinned by AI-powered orchestration engines. These systems will not only automate routine motion sequences but also learn from historical performance data to redesign and optimize kinematic chains with minimal human intervention. The adoption of open standards and interoperable protocols will be crucial in enabling cross-vendor integration and scaling these innovations across global supply networks. As such, the outlook is one of rapid acceleration, with Workflow Kinematics Engineering set to become a cornerstone of next-generation industrial competitiveness and agility.