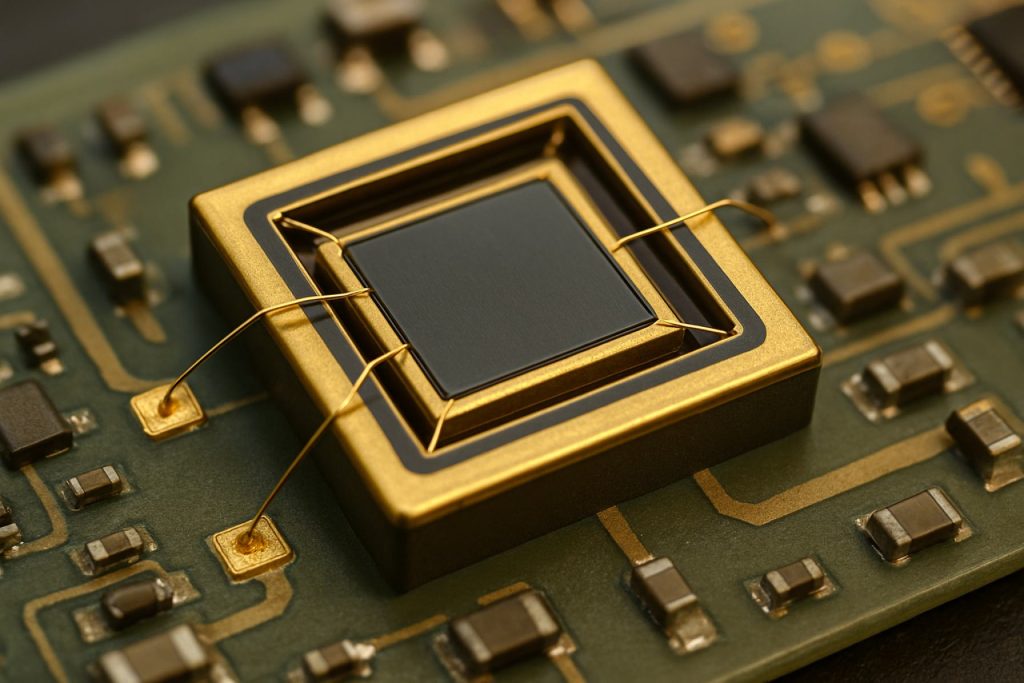
Why Gallium Arsenide Avalanche Photodiode Manufacturing in 2025 Is Set to Transform High-Speed Optoelectronics. Explore Market Surges, Next-Gen Tech, and Unmissable Trends Shaping the Future.
- Executive Summary: Key Insights for 2025–2030
- Gallium Arsenide APD Technology Overview & Innovations
- Market Size & Growth Forecasts Through 2030
- Key Players & Competitive Landscape (Official Company Profiles)
- Emerging Applications: Telecom, Lidar, and Beyond
- Supply Chain, Raw Materials, and Manufacturing Challenges
- Regulatory Environment & Industry Standards (IEEE, JEDEC)
- Regional Analysis: Asia-Pacific, North America, Europe
- R&D Hotspots: Patents, Partnerships, and Breakthroughs
- Future Outlook: Disruptive Trends & Strategic Opportunities
- Sources & References
Executive Summary: Key Insights for 2025–2030
Gallium arsenide (GaAs) avalanche photodiodes (APDs) remain at the forefront of high-speed and high-sensitivity photodetection, driven by their critical roles in optical communications, LiDAR, space instrumentation, and advanced medical imaging. As of 2025, rapid advances in manufacturing processes and rising market demand are shaping a dynamic outlook for the sector through 2030.
Leading manufacturers, including Hamamatsu Photonics K.K., Excelitas Technologies, and First Sensor AG (now part of TE Connectivity), are scaling production of GaAs APDs, focusing on enhanced device uniformity and reliability. These companies leverage proprietary wafer processing, advanced ion implantation, and precise passivation techniques to achieve low noise and high gain, meeting stringent requirements for next-generation optical modules and sensors.
From 2025 onward, the drive toward higher bandwidths (exceeding 25 Gbps) and increased integration within photonic integrated circuits (PICs) is accelerating innovation in GaAs APD design and fabrication. Hamamatsu Photonics K.K. continues to refine low-defect epitaxial growth and microfabrication, targeting automotive LiDAR and quantum communication markets. Meanwhile, Excelitas Technologies and First Sensor AG invest in automated wafer handling and advanced packaging, facilitating higher throughput and cost-effective mass production.
Strategic partnerships between device manufacturers and material suppliers are also gaining momentum. Collaborations aim to secure high-purity GaAs substrates and specialized epitaxial wafers, essential for yield improvement and performance consistency. The increasing prevalence of 6-inch and 8-inch GaAs wafers is expected to further streamline fabrication and reduce per-unit costs.
Looking to 2030, the GaAs APD manufacturing sector is poised for robust growth, catalyzed by the proliferation of 5G/6G optical networks, automotive autonomy, and satellite-based sensing. Key trends include the integration of on-chip electronics for signal processing, miniaturization for multi-channel detector arrays, and expanded use of digital twins and AI-based process control in wafer fabrication.
- Continued R&D in low-noise, high-speed GaAs APDs to meet telecom and LiDAR demands
- Adoption of larger wafer formats and automation to enhance economies of scale
- Growing role of integrated photonics, fueling demand for co-packaged GaAs APDs
- Strategic partnerships across the supply chain to ensure material quality and security
In summary, the period from 2025 to 2030 will see significant technological progress and market expansion in GaAs avalanche photodiode manufacturing, with established industry leaders and innovative newcomers shaping the competitive landscape.
Gallium Arsenide APD Technology Overview & Innovations
Gallium Arsenide (GaAs) avalanche photodiodes (APDs) represent a crucial technology for high-speed photodetection, particularly in optical communications, LIDAR, and sensing applications. As of 2025, advancements in GaAs APD manufacturing are marked by a blend of mature wafer processing techniques and ongoing innovation in device architecture and integration.
The manufacturing of GaAs APDs begins with high-purity single-crystal GaAs wafers, produced via methods such as the vertical gradient freeze (VGF) or liquid encapsulated Czochralski (LEC) processes. Industry leaders in GaAs wafer supply include Wafer World Inc. and Sumitomo Chemical, both providing substrates with low defect densities essential for maximizing APD performance. Epitaxial growth, typically by metal-organic chemical vapor deposition (MOCVD), is then used to create the layered heterostructures that define the absorption and multiplication regions of the device.
A key innovation in recent years has been the refinement of the Separate Absorption and Multiplication (SAM) structure, which leverages the superior electron mobility and higher breakdown field of GaAs to achieve lower noise and higher gain-bandwidth products. Companies such as Hamamatsu Photonics and ams OSRAM are notable for their advanced GaAs APD fabrication, often integrating proprietary passivation techniques and low-defect growth processes to enhance device reliability and uniformity.
Wafer-level processing steps—such as photolithography, plasma etching, and metallization—have been optimized to allow for high-throughput and high-yield production. For example, Coherent Corp. (formerly II-VI Incorporated) has expanded its vertically integrated manufacturing capacity, enabling scalable production of both discrete APDs and monolithic arrays for automotive and industrial sensing.
Looking ahead to the next few years, the outlook for GaAs APD manufacturing is shaped by a push towards higher pixel densities, wafer-scale integration, and hybridization with silicon readout circuits. Partnerships between GaAs foundries and integrated photonics companies are expected to accelerate, aiming at reducing cost per unit and enabling new system-level functionalities. Environmental and geopolitical considerations are also leading to regional diversification of supply chains, with new investments in facilities in Europe and North America reported by players like Samsung Electronics and Infineon Technologies.
In summary, GaAs APD manufacturing in 2025 is characterized by robust supply chains, ongoing device innovation, and a trend toward integration and scale, positioning the technology to meet the rising demands of high-speed and high-sensitivity optical applications globally.
Market Size & Growth Forecasts Through 2030
The global market for Gallium Arsenide (GaAs) Avalanche Photodiode (APD) manufacturing is poised for steady growth through 2030, underpinned by advances in high-speed optical communications, automotive LiDAR, and industrial sensing. As of 2025, the demand for GaAs APDs is being driven by the expansion of 5G networks, data center interconnects, and the proliferation of advanced driver-assistance systems (ADAS), all of which require high-sensitivity photodetectors for efficient signal processing.
Key manufacturers in this segment include Hamamatsu Photonics, a major supplier of photonic devices and APDs, and First Sensor (now part of TE Connectivity), both of which have reported increased activity in the photodiode segment. Hamamatsu Photonics in particular has noted growth in demand for APDs in their latest investor communications, attributing this to the expanding use of optical communication networks and medical imaging systems.
The Asia-Pacific region, led by China, Japan, and South Korea, continues to dominate GaAs APD manufacturing, supported by robust electronics and semiconductor ecosystems. Companies such as Sharp Corporation and Lumentum have made significant investments in photonics and optical component production, which includes GaAs-based APDs. In addition, China’s ongoing investment in domestic semiconductor capability is expected to further augment regional supply and technological advancement.
Looking toward 2030, the market is projected to experience mid-to-high single-digit compound annual growth, with the strongest gains anticipated in automotive and telecommunications sectors. The adoption of high-performance LiDAR systems for autonomous vehicles and increased deployment of high-speed optical networks are likely to sustain demand. Furthermore, ongoing R&D into GaAs integration with silicon-based electronics may open new avenues for cost-effective mass production, potentially reducing prices and expanding application scope.
- Continued investments from leading manufacturers such as Hamamatsu Photonics, TE Connectivity (First Sensor), Lumentum, and Sharp Corporation are expected to support capacity expansion and innovation.
- Demand volatility may occur due to shifts in global supply chains and semiconductor material availability; however, the long-term outlook remains positive given strategic prioritization of photonic technologies.
In summary, the GaAs APD manufacturing sector is on a growth trajectory supported by diversified end-use markets, ongoing technological innovation, and significant regional investments. With established industry players expanding their capabilities and new entrants leveraging advances in material science, the market is set to remain dynamic and competitive through 2030.
Key Players & Competitive Landscape (Official Company Profiles)
The Gallium Arsenide (GaAs) Avalanche Photodiode (APD) manufacturing sector in 2025 is marked by the activities of several specialized semiconductor companies with established expertise in III-V compound materials. GaAs APDs are essential for high-speed optical receivers, LIDAR, and advanced communication systems due to their superior performance in wavelength ranges where silicon devices are inefficient. The competitive landscape is characterized by vertically integrated manufacturers, niche suppliers, and a handful of new entrants investing in process innovation.
- Hamamatsu Photonics K.K.: Based in Japan, Hamamatsu is a dominant global player in the photonics sector, offering a broad portfolio of APDs, including GaAs-based devices for telecom, scientific, and industrial applications. The company leverages in-house epitaxial wafer growth, advanced device packaging, and strong R&D to maintain technological leadership. Hamamatsu’s continuous investment in production automation and quality control underscores its commitment to maintaining high device reliability and yield (Hamamatsu Photonics K.K.).
- Excelitas Technologies: Operating from North America and Europe, Excelitas is recognized for its specialty photonic components, including high-sensitivity GaAs APDs for LIDAR, medical imaging, and optical communication. The company emphasizes customization and close customer collaboration, often adapting device characteristics for emerging automotive and aerospace applications. Excelitas invests in both wafer fabrication and device assembly, ensuring supply chain resilience (Excelitas Technologies).
- First Sensor (a TE Connectivity company): Based in Germany and now under TE Connectivity, First Sensor is notable for its GaAs APD solutions tailored to industrial and automotive LIDAR, as well as medical diagnostics. The company’s vertical integration allows control over wafer processing and device packaging, supporting rapid product adaptation to evolving market needs (First Sensor).
- OSI Optoelectronics (OSI Systems, Inc.): This US-based manufacturer delivers a range of photodetector technologies, including GaAs APDs, targeting scientific instrumentation and defense sectors. OSI’s in-house wafer processing and commitment to high-reliability standards have positioned it as a trusted partner for OEMs requiring tailored solutions (OSI Optoelectronics).
- Lumentum Holdings Inc.: With a legacy in optical components for telecom and datacom, Lumentum is involved in GaAs-based photonic devices, including APDs for high-speed optical receivers. The company’s extensive manufacturing footprint and R&D resources enable large-scale production and rapid product iteration (Lumentum Holdings Inc.).
In 2025 and beyond, these companies are expected to strengthen their positions through investments in process automation, wafer-scale integration, and improved device reliability. The market remains moderately consolidated, with barriers to entry defined by the complexity of GaAs epitaxial growth and device fabrication, as well as stringent quality demands from automotive, aerospace, and telecom customers. New entrants may emerge from Asia, given ongoing regional investments in compound semiconductor manufacturing, but incumbents with established IP and process expertise are likely to retain competitive advantage.
Emerging Applications: Telecom, Lidar, and Beyond
Gallium arsenide (GaAs) avalanche photodiodes (APDs) are increasingly recognized for their superior performance in high-speed, low-noise photodetection, making them well-positioned for emerging applications across telecommunications, lidar, and other sectors in 2025 and the years ahead. The intrinsic properties of GaAs, such as high electron mobility and direct bandgap, allow for higher quantum efficiency and faster response times compared to traditional silicon-based APDs.
In telecommunications, the demand for increased bandwidth and faster data transmission is propelling the adoption of GaAs APDs, particularly in high-speed optical receivers for fiber-optic networks and coherent communication systems. Leading manufacturers such as Hamamatsu Photonics and Lumentum Holdings Inc. are advancing GaAs APD integration into optical transceivers, targeting 100G, 400G, and emerging 800G network infrastructure. These devices enable lower noise and higher sensitivity in dense wavelength division multiplexing (DWDM) systems, critical for the backbone of next-generation internet and data center connectivity.
Lidar (Light Detection and Ranging) is another domain witnessing robust adoption of GaAs APDs, driven by the rapid expansion of autonomous vehicles, robotics, and environmental mapping. GaAs-based APDs are preferred for their fast timing resolution and enhanced photon detection efficiency at wavelengths around 850–1060 nm, which are standard for automotive and industrial lidar. Companies such as First Sensor AG (now part of TE Connectivity) and Hamamatsu Photonics are developing GaAs APD arrays tailored for solid-state lidar modules, which are projected to become increasingly cost-competitive and reliable in mass-market applications throughout 2025 and beyond.
Beyond telecom and lidar, GaAs APDs are extending into quantum communications, spaceborne instrumentation, and biomedical imaging. The radiation hardness and high-speed capabilities of GaAs devices are attractive for satellite-based optical links and deep-space probes, areas where agencies such as the European Space Agency (ESA) and commercial satellite integrators are reportedly evaluating advanced photodiode arrays. In biomedical imaging, GaAs APDs facilitate time-correlated single photon counting (TCSPC) and fluorescence lifetime imaging, enabling new diagnostic modalities with greater precision.
Looking ahead, continued investment in GaAs APD manufacturing processes—including wafer-scale integration, improved passivation, and hybrid integration with silicon photonics—signals a positive outlook for broader adoption in new and existing applications. Collaboration among major photonics component suppliers and system integrators will further accelerate GaAs APD deployment, positioning the technology at the forefront of next-generation photonic sensing and communication systems.
Supply Chain, Raw Materials, and Manufacturing Challenges
The manufacturing of Gallium Arsenide (GaAs) avalanche photodiodes (APDs) in 2025 continues to be shaped by a complex supply chain, raw material sourcing challenges, and evolving production technologies. GaAs APDs are crucial components in high-speed optical communication, LIDAR, and sensing applications due to their superior sensitivity and fast response times. However, their production is vulnerable to fluctuations in raw material availability and geopolitical factors.
The primary raw materials for GaAs APD manufacturing are high-purity gallium and arsenic, both of which require stringent sourcing controls. Gallium is predominantly obtained as a byproduct of aluminum and zinc production. The supply is geographically concentrated, with leading producers such as 5N Plus and Umicore playing key roles in refining and supplying high-purity gallium for the optoelectronics industry. Arsenic, equally essential, is sourced under strict environmental and safety regulations, and its availability can be affected by mining restrictions and export controls.
Wafer fabrication for GaAs devices is capital-intensive and requires advanced epitaxial growth techniques such as Metal-Organic Chemical Vapor Deposition (MOCVD). Leading wafer suppliers like Wafer Technology Ltd. and ATEC Group provide GaAs substrates, but the market remains sensitive to capacity constraints and lead times. In 2025, the demand for high-quality GaAs wafers is expected to rise, driven by the expansion of 5G telecom infrastructure and automotive LIDAR. This puts additional pressure on upstream suppliers to scale production and maintain stringent quality standards.
The downstream manufacturing process of GaAs APDs involves complex photolithography, doping, and precise fabrication steps. Companies such as Hamamatsu Photonics, a global leader in photonic devices, and Lumentum Holdings, known for their optical components and modules, invest heavily in yield improvement and process automation to address scaling challenges. Hamamatsu Photonics particularly emphasizes in-house raw material purification and proprietary wafer processing to secure supply chain stability.
Despite ongoing investments, the GaAs APD sector faces persistent challenges in 2025. Geopolitical tensions—including export regulations affecting gallium—have led to increased interest in diversifying supply sources and recycling initiatives. Environmental compliance and traceability requirements are also tightening, compelling manufacturers to enhance sustainability practices. Looking ahead, the sector is expected to focus on vertical integration, localization of supply chains, and adoption of circular economy principles to mitigate raw material risks and ensure resilient GaAs APD manufacturing.
Regulatory Environment & Industry Standards (IEEE, JEDEC)
The regulatory environment and industry standards for Gallium Arsenide (GaAs) Avalanche Photodiode (APD) manufacturing are shaped by a combination of international standards, regional regulations, and the policies of key industry bodies. As of 2025, compliance with these frameworks is critical for manufacturers aiming to ensure device reliability, interoperability, and market acceptance, particularly in high-performance sectors such as optical communications, LIDAR, and medical imaging.
A primary standard-setting body is the Institute of Electrical and Electronics Engineers (IEEE), whose standards for photonic devices—including IEEE 1597 and IEEE 802.3 (relevant for optical transceiver performance)—guide the development and testing of APDs. These standards define metrics for responsivity, noise factors, breakdown voltage, and bandwidth, which are integral to device qualification. IEEE’s continued updates, expected through 2025, will address increasing demand for higher data rates and stricter reliability metrics in communications networks.
The JEDEC Solid State Technology Association is another influential organization, especially in defining reliability and quality assurance methodologies. JEDEC’s JESD22 series provides standardized procedures for environmental stress testing, thermal cycling, and failure analysis applicable to GaAs APDs. Adherence to these protocols is essential for meeting the qualification requirements of major telecommunications operators and defense contractors.
Environmental and safety regulations are also central to GaAs APD manufacturing. The use of arsenic-containing compounds is tightly regulated under the European Union’s REACH Directive and the RoHS Directive, which restrict hazardous substances in electronics. Global manufacturers such as Hamamatsu Photonics and Coherent Corp. (formerly II-VI Incorporated) have implemented robust compliance programs to ensure their products meet these requirements, which are expected to become even more stringent in the coming years.
Industry forums and trade associations, including the SEMI International, facilitate consensus on process standards, cleanroom protocols, and supply chain traceability. In 2025 and beyond, increased emphasis is being placed on traceability from wafer fabrication to final device packaging, driven by both industry self-regulation and customer requirements in the aerospace and defense sectors.
Looking forward, the regulatory landscape is anticipated to evolve with the proliferation of quantum communication and automotive LIDAR, both of which will demand tighter standards on device sensitivity, timing jitter, and reliability. Active engagement with standards bodies and proactive compliance will remain vital for manufacturers seeking to lead in the GaAs APD market.
Regional Analysis: Asia-Pacific, North America, Europe
The global landscape for Gallium Arsenide (GaAs) Avalanche Photodiode (APD) manufacturing is notably concentrated across three primary regions: Asia-Pacific, North America, and Europe. Each region brings unique strengths and strategic directions as of 2025, shaped by ongoing technological advances and regional industrial policies.
Asia-Pacific continues to dominate GaAs APD manufacturing, underpinned by robust semiconductor ecosystems in countries such as China, Japan, South Korea, and Taiwan. In China, state-backed initiatives and investments drive capacity expansions and technology upgrades. Leading Chinese firms such as GigaDevice Semiconductor and Huawei Technologies are exploring GaAs-based solutions for high-speed optical communications and LiDAR. Japan maintains a stronghold through established players like Hamamatsu Photonics, recognized for advanced photonic device fabrication, and Mitsubishi Electric, which integrates GaAs APDs into optical transceivers for datacom and sensing. South Korea’s vertically integrated semiconductor giants, such as Samsung Electronics, are reported to be investing in compound semiconductor R&D, though their commercial focus remains primarily on Si and InP photonics as of 2025. In Taiwan, the supply chain supports both foundry and fabless models, aiding smaller firms and international customers.
North America remains a center for high-performance and specialized APDs, driven by defense, aerospace, and data center applications. Companies like Lumentum Holdings and Coherent Corp. (formerly II-VI Incorporated) are key innovators, leveraging proprietary processes for low-noise, high-gain GaAs APDs. The U.S. benefits from a strong R&D base, with collaboration between industry, national laboratories, and universities pushing advancements in device reliability and integration. Additionally, defense-sector demand for secure and high-speed optical systems secures funding for GaAs APD advances through government procurement and research contracts.
Europe is distinguished by its focus on quality and niche applications, particularly in scientific instrumentation, automotive LiDAR, and quantum technologies. Excelitas Technologies (with significant operations in Germany and the UK) leads in specialty APD modules. France’s Thales Group and Germany’s OSRAM are active in integrating GaAs APDs into sensing and security systems. The European Union’s emphasis on semiconductor sovereignty and funding through initiatives such as IPCEI (Important Projects of Common European Interest) further supports GaAs photonic device manufacturing in the region.
Looking ahead, the Asia-Pacific region is expected to retain manufacturing leadership, particularly as domestic supply chains mature and export restrictions influence global sourcing. North American and European players will likely focus on high-value, differentiated GaAs APD products and system integration, targeting segments where performance, security, and regulatory compliance are paramount.
R&D Hotspots: Patents, Partnerships, and Breakthroughs
The landscape of gallium arsenide (GaAs) avalanche photodiode (APD) manufacturing in 2025 is marked by rapid R&D activity, with leading players investing in advanced process integration, novel device structures, and strategic partnerships. GaAs APDs are critical for applications demanding high-speed and high-sensitivity detection, including optical communications, LiDAR, and quantum photonics. The sector’s innovation hotspots reflect a convergence of patent filings, collaborative research, and technology transfers, driven by performance demands and evolving application requirements.
Patent activity remains robust in 2025, as established manufacturers and emerging innovators alike protect intellectual property related to epitaxial growth, wafer bonding, device passivation, and low-noise circuit integration. Hamamatsu Photonics, a global leader in photonic devices, continues to secure intellectual property around high-gain, low-noise GaAs APD structures, aiming to expand their performance envelope for next-generation optical links and sensing. Similarly, Lumentum Holdings, known for its photonic components in telecom, has strengthened its patent portfolio around monolithic integration and wafer-scale manufacturing techniques for GaAs-based detectors. Several Asian manufacturers, including Ricoh Company and KODENSHI, have filed patents on surface passivation and anti-reflective coatings that enhance device lifetime and quantum efficiency.
Partnerships and consortia are central to accelerating breakthroughs. Cross-industry alliances, such as university-industry collaborations, are facilitating technology transfer from research labs to commercial fabs. In Japan, Hamamatsu Photonics has reported ongoing joint research projects with university photonics departments, focusing on ultra-fast GaAs APD arrays for automotive LiDAR and quantum communication. Meanwhile, companies such as Lumentum Holdings are partnering with foundries specializing in compound semiconductors to scale up manufacturing while maintaining device uniformity and reliability.
Breakthroughs in 2025 are anticipated in areas like defect reduction during molecular beam epitaxy (MBE) and metal-organic chemical vapor deposition (MOCVD), both crucial for GaAs APD yield and performance. There is also momentum in developing monolithic integration technologies, enabling GaAs APDs to be fabricated alongside signal processing electronics for lower system cost and improved miniaturization. Hamamatsu Photonics and Lumentum Holdings are both actively publishing and patenting innovations in these domains, with several prototypes expected to reach pilot production by late 2025 or 2026.
Looking ahead, the global GaAs APD sector is poised for further breakthroughs through continued patenting, cross-disciplinary partnerships, and process innovations, reinforcing its strategic importance in the photonics ecosystem.
Future Outlook: Disruptive Trends & Strategic Opportunities
Looking ahead to 2025 and beyond, the manufacturing landscape for Gallium Arsenide (GaAs) avalanche photodiodes (APDs) is poised for notable transformation, shaped by emerging disruptive trends and strategic opportunities across the optoelectronics sector. The convergence of rising demand for high-performance photonic devices in applications such as next-generation LiDAR, 3D sensing, quantum communications, and high-speed optical networks is driving significant investments and innovation in GaAs APD manufacturing.
A key trend is the acceleration of hybrid integration and monolithic photonic integration, where GaAs APDs are combined with other compound semiconductor components—such as lasers and modulators—on a single chip. This approach enables improved performance, miniaturization, and cost-efficiency, particularly for automotive and consumer electronics markets. Leading manufacturers such as Hamamatsu Photonics and Coherent Corp. (formerly II-VI Incorporated) are advancing integration techniques and expanding manufacturing capacity to meet anticipated surges in demand for solid-state LiDAR and optical communication modules.
Another disruptive opportunity lies in the development of wafer-scale, high-yield manufacturing processes. Innovations in metal-organic chemical vapor deposition (MOCVD) and molecular beam epitaxy (MBE) are expected to increase throughput and reduce defect rates for GaAs wafers. Companies such as Advanced Ion Technologies Group and ams-OSRAM AG are investing in advanced epitaxial growth systems and in-line inspection solutions to address quality and scalability challenges, supporting broader adoption in telecommunications and medical imaging.
Sustainability and supply chain resilience are also gaining prominence. With growing geopolitical uncertainties and raw material constraints, manufacturers are exploring closed-loop recycling processes and secure sourcing strategies for gallium and arsenic. Organizations like Semiconductor Industry Association are facilitating industry-wide efforts to create robust supply chains and promote responsible sourcing, which are critical for long-term manufacturing stability.
Looking toward the late 2020s, the convergence of AI-driven quality control, automation in wafer handling, and real-time process monitoring will further improve yields and cost structures. These advancements are expected to lower barriers for new entrants and enable smaller foundries to participate in the GaAs APD value chain, potentially spurring increased regional diversification and innovation.
- Hybrid and monolithic integration to drive miniaturization and performance gains
- Wafer-scale process innovation to boost yields and scalability
- Supply chain security and sustainability as strategic imperatives
- Automation and AI adoption as enablers for cost reduction and quality assurance
In summary, GaAs avalanche photodiode manufacturing is entering a dynamic period, with disruptive trends creating new avenues for growth, collaboration, and technological leadership across the global optoelectronics industry.
Sources & References
- Hamamatsu Photonics K.K.
- First Sensor AG
- Wafer World Inc.
- Sumitomo Chemical
- ams OSRAM
- Samsung Electronics
- Infineon Technologies
- Lumentum
- OSI Optoelectronics
- European Space Agency (ESA)
- 5N Plus
- Umicore
- ATEC Group
- Institute of Electrical and Electronics Engineers (IEEE)
- JEDEC Solid State Technology Association
- GigaDevice Semiconductor
- Huawei Technologies
- Mitsubishi Electric
- Thales Group
- OSRAM
- Ricoh Company
- KODENSHI
- Advanced Ion Technologies Group
- Semiconductor Industry Association