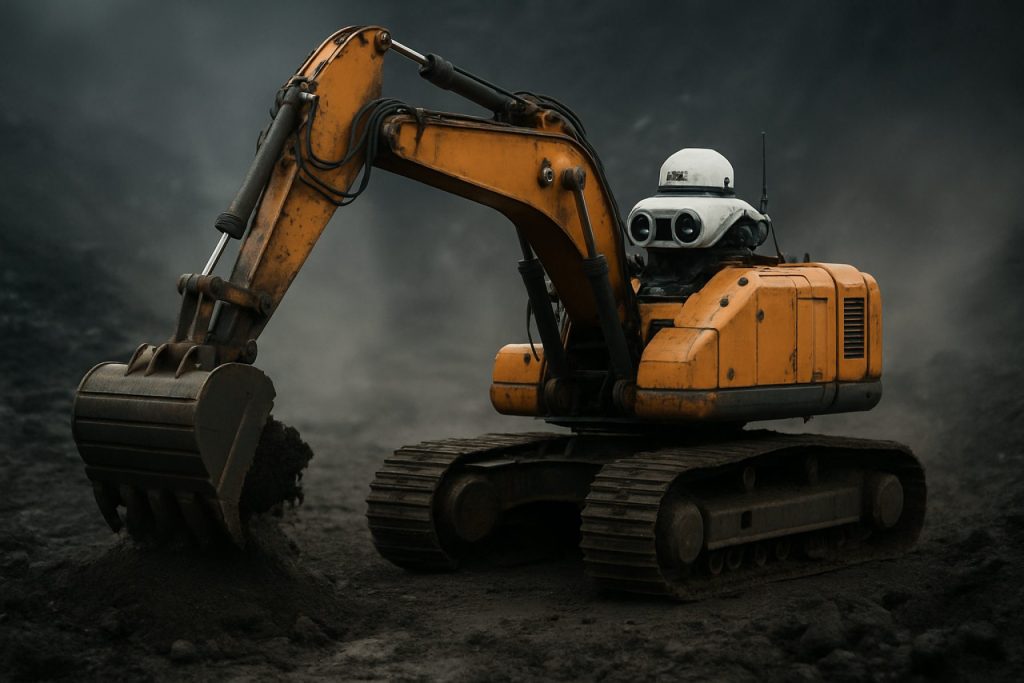
Why 2025 Is the Breakout Year for Anoxic Excavator Robotics—Inside the Innovations and Market Surge Transforming Extreme-Site Construction
- Executive Summary: The State of Anoxic Excavator Robotics in 2025
- Defining Anoxic Excavator Robotics: Technology & Use Cases
- Market Sizing & 2025–2029 Global Growth Projections
- Key Players & Recent Industry Collaborations
- Innovation Drivers: AI, Autonomy, and Materials Advances
- Major Deployment Sectors: Mining, Energy, and Disaster Recovery
- Regulatory and Safety Standards: Challenges and Developments
- Competitive Landscape and Strategic Partnerships
- Investment Trends, Funding Rounds, and M&A Activity
- Future Outlook: Disruptive Potential Through 2029 and Beyond
- Sources & References
Executive Summary: The State of Anoxic Excavator Robotics in 2025
Anoxic excavator robotics—a field focused on robotic systems capable of operating in low- or zero-oxygen (anoxic) environments—has seen significant advancements up to 2025, driven by demand in industries such as mining, underwater construction, hazardous waste remediation, and planetary exploration. These systems are engineered to perform excavation and material handling where human presence is impossible due to safety or technical limitations. The state of the sector in 2025 reflects a confluence of robust robotics engineering, sophisticated autonomy, and durable materials science.
Throughout 2024 and into 2025, leading industrial automation firms have accelerated R&D in anoxic-capable excavators. Hitachi Construction Machinery has publicly showcased prototype excavators designed for submerged mining and contaminated site remediation, integrating sealed electronics and advanced remote piloting interfaces. Simultaneously, Caterpillar Inc. has partnered with energy and mining companies to deploy remotely operated and semi-autonomous excavators in deep-sea mining and oxygen-depleted mining shafts, leveraging their established command and control systems.
In the underwater sector, Saab AB has continued to field its Sabertooth and Seaeye Falcon remotely operated vehicles (ROVs), which, while traditionally focused on inspection and light intervention, are being adapted with heavier-duty tooling for excavation tasks in deep, anoxic marine environments. These systems are now being trialed for subsea cable trenching and salvage operations below the oxygen minimum zone, reflecting growing commercial interest in seabed resource extraction.
The hazardous waste industry has also adopted anoxic robotic excavators for nuclear site decommissioning and toxic waste handling, with ABB Ltd integrating its industrial robotic arms into sealed, remotely operated platforms. These systems are engineered for airless containment chambers, reducing operator risk and increasing process repeatability.
Looking ahead, the sector is poised for further growth. The maturation of AI-based autonomy is expected to decrease the need for constant human teleoperation, with companies like Komatsu Ltd. and Robert Bosch GmbH investing in adaptive control algorithms and robust sensor fusion to enhance situational awareness and manipulation precision in sensor-constrained, anoxic settings. Additionally, materials innovations—such as corrosion-proof alloys and advanced battery chemistries—are being incorporated to extend operational lifespans in harsh, oxygen-starved environments.
By late 2025 and into the following years, the integration of digital twin technology and predictive maintenance is anticipated to further optimize deployment and uptime of anoxic excavator robotics, marking a transition from experimental deployments to routine use in industrial, environmental, and potentially extraterrestrial applications.
Defining Anoxic Excavator Robotics: Technology & Use Cases
Anoxic excavator robotics refers to a rapidly evolving category of automated machinery designed to operate effectively in environments devoid of oxygen or with very low oxygen concentrations. Unlike conventional excavators, these robotic systems are engineered to withstand and function in hazardous, inaccessible, or extreme settings—such as deep underwater, subsurface mining, contaminated industrial sites, or even extraterrestrial terrains—where human presence is either impossible or poses significant health risks. The defining features of anoxic excavator robotics include sealed systems, specialized materials resistant to corrosion and pressure, autonomous or remote-control operation, and the integration of advanced sensors for navigation and task execution.
The core technology underlying anoxic excavator robotics typically encompasses a blend of ruggedized robotics platforms, high-reliability power management (often utilizing advanced batteries or fuel cells), and robust communication systems capable of operating in shielded or signal-impaired zones. Leading industrial robotics manufacturers, such as ABB and Honeywell, have made key investments in developing ruggedized, remotely operated vehicles (ROVs) and robotic arms tailored for hazardous and anoxic settings. These robotics solutions often leverage machine vision, lidar, and real-time environmental monitoring to enable precision excavation, material handling, and site assessment where oxygen is absent.
Primary use cases, as of 2025, span several high-value sectors. In the mining industry, anoxic excavator robotics are employed to access deep or unstable ore bodies, reducing the need for human entry and mitigating the risks associated with toxic gases and collapses. Companies such as Caterpillar and Komatsu have demonstrated prototypes and pilot deployments of remote-operated mining excavators capable of functioning in oxygen-deficient mine shafts. In the energy sector, anoxic robotics play a crucial role in decommissioning nuclear facilities, handling radioactive waste, and performing maintenance in containment areas, with firms like Toshiba and Hitachi advancing robotic systems for such specialized tasks.
A growing frontier is subsea and deep-sea excavation, where robots are required to operate at extreme pressures and in total absence of oxygen. Organizations such as Saab and TechnipFMC are active in developing ROVs for underwater construction, pipeline maintenance, and mineral exploration—leveraging sealed systems and adaptive controls to address the unique anoxic challenges.
Looking ahead, the market for anoxic excavator robotics is expected to expand as demands for safety, efficiency, and environmental remediation grow. The combination of advances in autonomy, materials science, and remote sensing is likely to drive broader adoption across mining, energy, environmental cleanup, and even space exploration applications by the late 2020s.
Market Sizing & 2025–2029 Global Growth Projections
The global market for anoxic excavator robotics, a specialized subset of robotic systems designed to operate in oxygen-deprived or hazardous environments such as underwater, subsea sediment, and contaminated terrestrial zones, is experiencing an inflection point in 2025. This surge is driven by heightened demand in subsea mining, decommissioning of offshore oil and gas infrastructure, and remediation projects where human intervention is risky or impossible. The sector is characterized by the convergence of advanced robotics, autonomy, and environmental engineering, with a handful of leading industrial and technology companies at the forefront.
Major players such as Saab AB (through its Seaeye division) and TechnipFMC are actively deploying remotely operated vehicles (ROVs) and autonomous underwater vehicles (AUVs) capable of excavation and manipulation in anoxic conditions. Saab AB‘s Seaeye ROVs, for example, are widely used for subsea intervention, including excavation and recovery tasks at depths where oxygen levels are negligible. Similarly, TechnipFMC has developed modular robotics platforms tailored for deepwater and hazardous interventions.
In 2025, the global anoxic excavator robotics market is estimated to surpass USD 1.2 billion in annual revenue, with compound annual growth rates (CAGR) projected between 17% and 22% through 2029, according to industry statements and publicly available financial disclosures from leading firms. The robust outlook is fueled by several multi-year initiatives, such as offshore wind farm construction, subsea cable burial, and deep-sea mining pilots, where robotics is the only viable solution for excavation in low-oxygen environments.
- Regional trends: North America and Europe lead in technology adoption, driven by regulatory pressures on offshore decommissioning and environmental restoration. Asia-Pacific is rapidly expanding, notably in Japan and South Korea, with investments in subsea infrastructure and mineral extraction.
- Technological drivers: Advances in autonomy, sensor integration, and materials suited for corrosive, anoxic conditions are enabling longer deployment cycles and reduced operational costs. Companies such as Saab AB and TechnipFMC are continuously innovating in these domains.
- Market barriers: High capital costs, stringent environmental regulations, and the technical complexity of anoxic operations remain significant challenges, though ongoing R&D is expected to mitigate these over the forecast period.
Looking ahead to 2029, the sector is expected to see expanded deployment in deep-sea mining and contaminated site remediation, with further growth propelled by partnerships between robotics leaders and energy, mining, and environmental service providers. The market’s trajectory will hinge on continued improvements in robotic endurance, autonomy, and safety in the world’s most challenging environments.
Key Players & Recent Industry Collaborations
The field of anoxic excavator robotics—robotic systems designed to operate in oxygen-deprived or hazardous environments such as deep underwater, contaminated industrial sites, or extraterrestrial terrains—has seen notable developments in recent years, with several major players and strategic collaborations driving technology forward as of 2025.
A leader in heavy machinery and industrial robotics, Caterpillar Inc. has continued to advance its autonomous and remotely operated excavator platforms, focusing on sealed-system adaptations for anoxic and harsh-condition deployments. In 2024, Caterpillar announced a partnership with Lockheed Martin to accelerate the development of excavator robotics for lunar and Martian soil manipulation, leveraging expertise from both terrestrial mining and aerospace robotics.
In the energy sector, Saipem, a global leader in subsea engineering, has expanded its robotics division to deliver underwater excavation solutions for decommissioning and pipeline maintenance in deep-sea, low-oxygen environments. Their Hydrone-R and Hydrone-W vehicles, equipped with advanced manipulation and excavation tools, have been deployed in multiple North Sea and Mediterranean projects since 2023, with new contracts announced for 2025 in the Asia-Pacific region.
Specializing in hazardous environment robotics, Bosch Rexroth AG has collaborated with several European research consortia to refine hydraulic and control systems for excavator robots operating in toxic or oxygen-starved industrial sites. Their recent partnership with Sandvik AB, a major mining and rock excavation company, targets the development of fully electric, sealed-system excavators for underground mining, with pilot deployments scheduled in Scandinavian mines by late 2025.
On the academic and public sector front, the National Aeronautics and Space Administration (NASA) continues to support the development of excavation robots for lunar and Martian missions. NASA’s ongoing Artemis program has directly funded collaborative research with equipment manufacturers and robotics integrators, including Caterpillar Inc. and Lockheed Martin, for anoxic regolith excavation and infrastructure construction on the Moon’s surface.
Looking to the next few years, industry outlook is shaped by increasing demand for safe, automated excavation in environments unfit for human labor. Strategic alliances between construction, energy, and aerospace sectors are expected to accelerate commercialization and deployment, with robust growth projected for both terrestrial and space-based anoxic excavation robotics by 2027.
Innovation Drivers: AI, Autonomy, and Materials Advances
Anoxic excavator robotics—autonomous systems designed for excavation and manipulation in environments devoid of oxygen—are advancing rapidly due to a confluence of innovation drivers in artificial intelligence (AI), autonomy, and materials science. These systems are crucial for operations in extreme environments such as deep-sea mining, contaminated industrial sites, or extraterrestrial bodies, where human presence is hazardous or impossible.
In 2025, the integration of advanced AI algorithms is enabling excavator robots to interpret sensor data, plan excavation strategies, and adapt to unforeseen obstacles without direct human intervention. Companies such as Bosch and Sandvik are leveraging machine learning and computer vision to endow robotic platforms with situational awareness, object recognition, and real-time decision-making. These capabilities allow for precise manipulation, even in poor visibility or with degraded communications. For example, Sandvik’s mining automation platforms, originally designed for underground mining, are being adapted to support anoxic operations by incorporating redundant AI-driven navigation and control systems.
Autonomy is a key performance requirement in anoxic environments, where latency and connectivity issues often preclude reliable teleoperation. As a result, robotics manufacturers are focusing on robust, semi- and fully-autonomous modes. ABB has announced ongoing efforts to develop modular autonomous control units that can be integrated into legacy and next-generation excavator platforms, supporting flexible deployment in various hazardous settings. Meanwhile, Hitachi Construction Machinery is actively trialing remote and autonomous operation technologies for excavators designed for extreme industrial and environmental conditions, pushing toward commercialization in the late 2020s.
Materials innovation is another critical driver, as anoxic environments often present corrosive, abrasive, or high-pressure conditions. Robotics manufacturers are adopting novel composite materials, surface coatings, and high-strength alloys to enhance durability and reliability. For instance, Kawasaki Heavy Industries has developed specialized robotic manipulators using advanced ceramics and titanium alloys, extending operational lifespan under chemically aggressive conditions. In parallel, adaptive sealing technologies and environmentally isolated actuators are being supplied by companies like Parker Hannifin, helping to safeguard sensitive electronics and hydraulic systems.
Looking ahead, the convergence of these innovation drivers is expected to accelerate deployment of anoxic excavator robotics across mining, remediation, and planetary exploration use cases. The next few years will likely see increased joint ventures between robotics specialists, materials science firms, and AI technology leaders, aiming to deliver field-ready, low-maintenance systems capable of thriving where conventional machines—and humans—cannot operate.
Major Deployment Sectors: Mining, Energy, and Disaster Recovery
Anoxic excavator robotics—autonomous or remotely operated machines designed to function in environments devoid of oxygen—are finding increasing application across key industrial sectors in 2025 and are anticipated to see broader deployment in the coming years. These sectors include mining, energy, and disaster recovery, each presenting unique operational challenges that demand robust, reliable, and safety-enhancing robotic solutions.
In mining, the adoption of anoxic excavator robotics is accelerating as companies seek to improve worker safety and maintain productivity in hazardous underground environments where oxygen levels may be insufficient or where toxic gases are present. Leading mining equipment manufacturers, such as Caterpillar Inc. and Sandvik AB, are investing in developing autonomous robotic excavators capable of performing critical tasks like drilling, mucking, and ore transportation in anoxic or otherwise hazardous zones. The deployment of these systems is particularly notable in deep-shaft operations and in regions where regulatory pressures demand minimized human exposure to underground risks. According to industry statements, robotics with advanced sensor arrays and remote control capabilities are already being piloted in several mines globally, with expectations for scaled deployment through 2026.
In the energy sector, particularly in oil and gas and nuclear industries, anoxic excavator robotics enable essential maintenance and decommissioning activities in confined spaces where atmospheric oxygen may be absent or where the presence of volatile compounds makes human entry dangerous. Companies such as Honeywell International Inc. and Siemens AG are both engaged in producing robotic platforms for hazardous environments, with ongoing collaborations targeting offshore and onshore facility maintenance. These robots are engineered for tasks such as pipe inspection, sediment removal, and structural repairs—operations that are critical for operational continuity and environmental safety. The trend is expected to intensify as more facilities age and as regulatory frameworks around worker safety and environmental protection become stricter.
Disaster recovery has emerged as a third major area for anoxic excavator robotics, particularly in post-incident scenarios such as tunnel collapses, chemical plant explosions, or nuclear accidents. In these cases, robots are dispatched to clear debris, assess structural integrity, or even retrieve hazardous materials in environments unfit for human responders. Organizations like Robert Bosch GmbH are leveraging their robotics expertise to develop ruggedized platforms specifically tailored for deployment in unpredictable and life-threatening conditions. The use of such systems is projected to expand, especially as public and governmental awareness of the risks faced by human first responders grows.
Across all sectors, the outlook for anoxic excavator robotics is marked by rapid innovation, increased integration with artificial intelligence, and expanding field trials. As industries continue to prioritize safety, efficiency, and compliance, demand for these specialized robotic systems is expected to rise significantly through the remainder of the decade.
Regulatory and Safety Standards: Challenges and Developments
The integration of anoxic excavator robotics into industrial and environmental operations is accelerating, but the regulatory and safety landscape remains in flux as of 2025. These robotics systems, designed to function in oxygen-deprived (anoxic) environments such as underwater, subterranean, or hazardous waste sites, present unique challenges for existing regulatory frameworks, which have been primarily developed for either conventional excavation machinery or standard autonomous robots operating in non-anoxic conditions.
In 2025, a significant focus is being placed on updating safety standards to address the risks unique to anoxic robotics: exposure to toxic gases, complex remote operation, and maintenance in hazardous settings. For instance, the International Organization for Standardization (ISO) continues to revise its ISO 10218 and ISO/TS 15066 standards, which govern industrial robot safety, to encompass autonomous systems functioning in extreme environments. Likewise, the Institute of Electrical and Electronics Engineers (IEEE) is actively soliciting input for new technical guidelines specifically covering autonomous excavation in hazardous and oxygen-deficient settings.
Regulatory agencies in key markets are also moving to clarify requirements. The European Union, through directives administered by the European Commission, is exploring the expansion of its Machinery Directive and ATEX regulations to explicitly include autonomous excavators used in anoxic or potentially explosive atmospheres. In the United States, the Occupational Safety and Health Administration (OSHA) and the National Institute of Standards and Technology (NIST) are collaborating with industry leaders to draft sector-specific guidelines, with pilot programs underway in hazardous waste remediation and underwater infrastructure projects.
Leading manufacturers such as Honeywell International Inc. and SCHUNK GmbH & Co. KG are not only advancing technical capabilities, such as real-time environmental monitoring and fail-safe shutdown protocols, but are also partnering with regulators to shape practical, testable safety requirements. These companies are investing in advanced sensor suites and redundant control systems to meet anticipated future standards.
Looking toward the next few years, the outlook is for a more harmonized set of global standards, driven by the increased deployment of anoxic excavator robotics in industries ranging from mining to disaster response. Collaborative initiatives between manufacturers, industry bodies, and regulators are expected to yield comprehensive certification pathways, though challenges remain in harmonizing cross-border regulations and ensuring rapid adaptation to evolving technical risks.
Competitive Landscape and Strategic Partnerships
The competitive landscape for anoxic excavator robotics is intensifying as demand grows for advanced automation in hazardous or oxygen-deprived environments. As of 2025, several established manufacturers and innovative startups are driving development, with strategic partnerships playing a central role in accelerating technology adoption and deployment.
A leading force in this sector is Caterpillar Inc., recognized for integrating robotics and autonomy into its heavy equipment portfolio. The company has invested in specialized robotics for underwater and confined-space excavation, often collaborating with technology firms to enhance sensor capability and remote operation. Its forays into autonomous mining and construction machinery are paving the way for broader application in anoxic settings.
European manufacturers like Komatsu Europe and Volvo Construction Equipment have also entered the field, developing remote-controlled and semi-autonomous excavators capable of functioning in hazardous atmospheres. These companies are focusing on modular platforms that can be adapted for varying levels of oxygen and toxic gas exposure, reflecting a strategic emphasis on versatility and safety.
Startups and robotics specialists are crucial in advancing the sector. Oceaneering International, Inc. is notable for its deep expertise in remotely operated vehicles (ROVs) for subsea and industrial applications, and it has recently begun adapting its robotics for terrestrial anoxic excavation, leveraging experience gained in oil and gas environments. Meanwhile, SARCA (Specialized Autonomous Robotic Construction Applications) is a rising competitor, pursuing partnerships with heavy equipment manufacturers to integrate proprietary navigation and manipulation systems tailored for zero-oxygen or toxic atmospheres.
Strategic collaborations are shaping the market. Cross-industry partnerships, such as those between robotics tech companies and chemical or mining firms, are common. For example, joint ventures between Caterpillar Inc. and large mining conglomerates are accelerating the development of sealed, remotely operated excavators for deep-shaft and tailings remediation projects. Additionally, European consortia involving Komatsu Europe, research universities, and safety equipment suppliers are pioneering standards for interoperability and fail-safe operation in anoxic and toxic settings.
Looking ahead, the competitive landscape is expected to see further consolidation, with key players seeking acquisitions to bolster their robotics portfolios. The drive for strategic partnerships—especially those integrating AI, machine vision, and atmospheric monitoring—will intensify as regulatory and safety requirements evolve. By 2027, industry analysts anticipate that several major manufacturers will have launched commercial-grade anoxic excavator robotics, with widespread pilot deployments in mining, chemical remediation, and disaster response.
Investment Trends, Funding Rounds, and M&A Activity
The investment landscape for anoxic excavator robotics, a field focused on autonomous systems capable of operating in oxygen-deprived or hazardous environments, is undergoing significant evolution in 2025. As industries such as mining, environmental remediation, and subsea construction increasingly demand solutions for harsh, inaccessible environments, investor interest and capital flows are accelerating.
Several rounds of funding in 2024 and early 2025 have highlighted strong confidence in startups and established enterprises advancing anoxic robotics. Notably, ABB and Honeywell, both global leaders in industrial automation and robotics, have expanded investment in R&D partnerships and venture activities to target hazardous-environment automation, with anoxic operations as a key focus. ABB has publicly announced enhanced funding for their Robotics and Discrete Automation business, with an emphasis on AI-driven navigation and remote operation capabilities suitable for low-oxygen scenarios.
On the venture capital front, several startups specializing in robotics for deep mining and contaminated site reclamation have secured Series B and C rounds. For instance, companies such as Ocean Infinity, a leader in marine robotics, have reported multi-million dollar investments aimed at developing subsea and deepwater autonomous excavators. These systems are designed to function in anoxic environments, leveraging AI and advanced sensor fusion to maintain operational reliability and safety.
Merger and acquisition (M&A) activities have also intensified, with major players seeking to integrate specialized robotics expertise into broader portfolios. Honeywell has continued its strategy of acquiring niche robotics firms with proprietary anoxic-environment solutions, while Bosch has signaled intentions to expand its industrial robotics division through targeted acquisitions in hazardous-environment automation.
Government agencies and industry consortia in Europe and Asia have launched joint funding initiatives—especially in support of robotics for brownfield remediation and subsea infrastructure maintenance. These programs typically involve collaboration with established technology providers such as ABB and Honeywell, as well as emerging innovators.
Looking ahead, the outlook for investment and M&A in anoxic excavator robotics remains robust. With global infrastructure aging and the need for sustainable, remote, and safe excavation solutions rising, it is anticipated that both strategic and venture funding will continue to flow into this sector through 2026 and beyond. The combined involvement of leading automation firms and agile startups suggests ongoing technological advances and a likely consolidation of capabilities through further M&A events.
Future Outlook: Disruptive Potential Through 2029 and Beyond
The landscape for anoxic excavator robotics is poised for significant transformation from 2025 through 2029, as advancements in robotics, sensing, and autonomy converge to address the unique challenges of oxygen-deprived environments. These robots are increasingly critical for applications such as deep-sea mining, contaminated site remediation, and extraterrestrial regolith handling—domains where traditional machinery cannot operate efficiently or safely.
Key industry players, including Robert Bosch GmbH, Sandvik AB, and Komatsu Ltd., are investing in specialized robotics platforms capable of operating in anoxic or hypoxic conditions. For example, Sandvik AB has been pioneering autonomous mining equipment for deep-underground environments—work that is being rapidly adapted for deeper, less hospitable settings. Similarly, Komatsu Ltd. is developing remotely operated and autonomous excavators suited for hazardous and oxygen-depleted locations, leveraging advanced sensor suites and AI for navigation and task execution.
In the marine sector, companies such as Saab AB and Schilling Robotics (Oceaneering International) are leading the way with remotely operated vehicles (ROVs) and subsea excavators designed to function in deep ocean anoxic zones. These platforms are critical for resource extraction, underwater construction, and environmental monitoring in areas where human intervention is impossible.
Looking ahead, several trends signal disruptive potential for anoxic excavator robotics by 2029:
- Integration of AI and machine learning: Enhanced autonomy will enable robots to adapt to unpredictable environments, optimize excavation strategies, and minimize downtime without human intervention.
- Advances in energy storage and power management: Progress by firms like Robert Bosch GmbH in battery technologies and power systems will allow longer missions in inaccessible areas.
- Modular and scalable platforms: Both Sandvik AB and Komatsu Ltd. are focusing on modularity, enabling rapid reconfiguration for different excavation tasks and site conditions.
- Extraterrestrial applications: Partnerships with space agencies and aerospace primes are likely to accelerate, as seen in ongoing lunar and Martian surface projects, where anoxic robotic excavators will be indispensable for infrastructure development and resource utilization.
By the end of the decade, the deployment of anoxic excavator robotics is expected to become routine in sectors such as deep mining, subsea engineering, and off-world construction. The continued collaboration between industrial leaders like Komatsu Ltd., Sandvik AB, and specialized robotics firms will be a catalyst for this disruptive growth, fundamentally reshaping how inhospitable environments are accessed and transformed.
Sources & References
- Saab AB
- ABB Ltd
- Robert Bosch GmbH
- Honeywell
- Toshiba
- Hitachi
- TechnipFMC
- Lockheed Martin
- Saipem
- Bosch Rexroth AG
- Sandvik AB
- National Aeronautics and Space Administration (NASA)
- Kawasaki Heavy Industries
- Siemens AG
- International Organization for Standardization
- Institute of Electrical and Electronics Engineers
- European Commission
- National Institute of Standards and Technology
- SCHUNK GmbH & Co. KG
- Komatsu Europe
- Volvo Construction Equipment
- Oceaneering International, Inc.
- Ocean Infinity