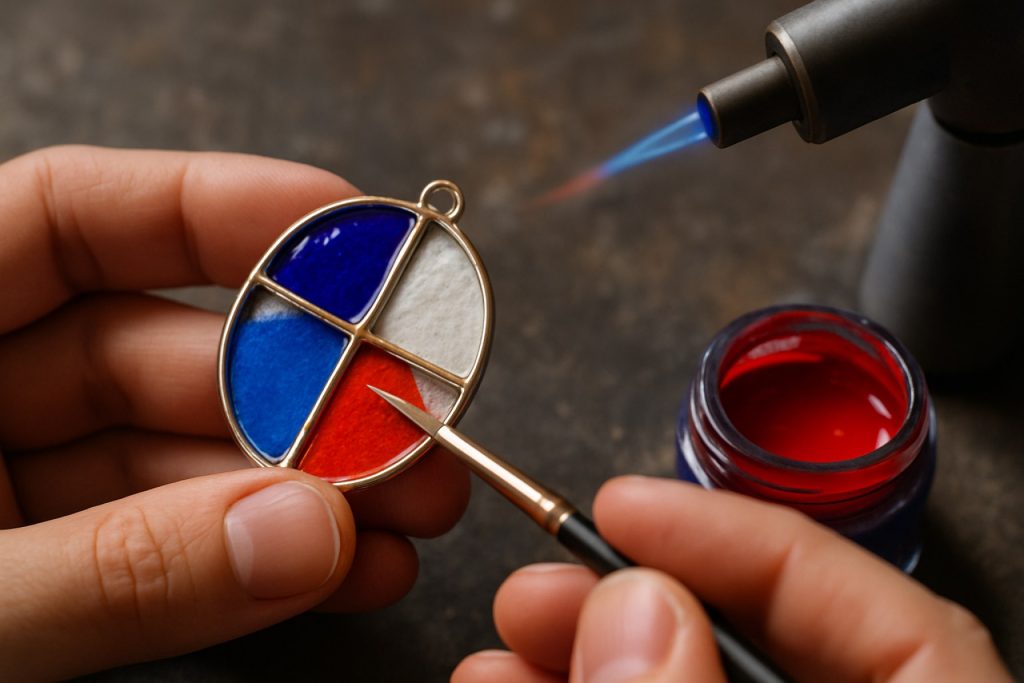
Jewelry Wire Enameling Technologies in 2025: Breakthroughs, Market Dynamics, and the Road Ahead. Discover how advanced processes and materials are redefining artistry and efficiency in the jewelry sector.
- Executive Summary: Key Trends and Market Outlook (2025–2029)
- Global Market Forecast: Growth Projections and Regional Hotspots
- Technological Innovations: Next-Gen Enameling Methods and Equipment
- Materials Evolution: Advances in Enamel Formulations and Wire Alloys
- Sustainability and Eco-Friendly Practices in Enameling
- Competitive Landscape: Leading Manufacturers and Emerging Players
- Applications: Fine Jewelry, Fashion, and Industrial Uses
- Regulatory Standards and Quality Assurance (Referencing jewelry.org, gia.edu)
- Challenges and Barriers: Technical, Economic, and Supply Chain Factors
- Future Outlook: Disruptive Technologies and Strategic Opportunities
- Sources & References
Executive Summary: Key Trends and Market Outlook (2025–2029)
The jewelry wire enameling sector is undergoing significant transformation as it enters 2025, driven by technological innovation, sustainability imperatives, and evolving consumer preferences. Enameling, the process of fusing colored glass to metal wire, remains a cornerstone of decorative jewelry, but recent years have seen a surge in advanced materials, automation, and eco-friendly practices shaping the industry’s trajectory.
A key trend is the adoption of high-performance enamel coatings that offer improved durability, color vibrancy, and resistance to tarnishing. Leading manufacturers such as Wieland and Schmalz are investing in research to develop lead-free and cadmium-free enamels, responding to tightening global regulations and consumer demand for safer, more sustainable products. These innovations are expected to become industry standards by 2027, particularly in Europe and North America, where regulatory scrutiny is highest.
Automation and digitalization are also reshaping production. Companies like Fenice and Uhlmann are integrating robotics and precision control systems into enameling lines, enabling consistent quality and higher throughput. This shift is particularly pronounced among large-scale jewelry manufacturers seeking to meet rising demand for intricate, customized designs while maintaining cost efficiency. The use of computer-aided design (CAD) and computer-aided manufacturing (CAM) is expected to accelerate, allowing for rapid prototyping and mass customization of enameled wire jewelry.
Sustainability remains a central concern. The industry is moving toward closed-loop water and waste management systems, as well as the use of recycled metals and eco-friendly enamels. Argor-Heraeus, a major precious metals refiner, is collaborating with jewelry producers to ensure traceability and responsible sourcing throughout the enameling supply chain. These efforts align with broader ESG (Environmental, Social, and Governance) goals and are anticipated to influence purchasing decisions, especially among younger consumers.
Looking ahead to 2029, the market outlook for jewelry wire enameling technologies is robust. Demand is projected to grow steadily, fueled by the popularity of personalized and artisanal jewelry, as well as the expansion of online retail channels. Technological advancements, particularly in eco-friendly materials and automated production, are expected to lower costs and broaden design possibilities. As regulatory and consumer pressures mount, companies that prioritize innovation and sustainability are likely to capture greater market share and set new industry benchmarks.
Global Market Forecast: Growth Projections and Regional Hotspots
The global market for jewelry wire enameling technologies is poised for steady growth through 2025 and into the latter part of the decade, driven by rising demand for high-quality, durable, and aesthetically diverse jewelry products. Enameling, which involves fusing colored glass powder onto metal wires, is increasingly favored for its ability to deliver vibrant finishes and corrosion resistance, particularly in fine and fashion jewelry segments.
Key manufacturers such as Heraeus and Pfarr Stanztechnik are at the forefront of innovation, offering advanced enameling solutions and equipment tailored for the jewelry sector. Heraeus, a global materials technology leader, continues to expand its portfolio of precious metal wires and enameling materials, supporting both traditional and automated production lines. Meanwhile, Pfarr Stanztechnik specializes in precision machinery for wire processing, including enameling lines that enable consistent quality and high throughput.
Regionally, Asia-Pacific remains the dominant hotspot, with countries like China, India, and Thailand serving as major manufacturing and export hubs for jewelry and related technologies. The region benefits from a robust supply chain, skilled labor, and increasing investments in automation and quality control. European countries, particularly Italy and Germany, maintain their reputation for high-end jewelry production, leveraging advanced enameling techniques and machinery from established suppliers. North America, while smaller in production volume, is witnessing a surge in demand for custom and artisanal jewelry, prompting local manufacturers to adopt modern enameling technologies to enhance product differentiation.
Recent years have seen a shift toward eco-friendly and lead-free enameling materials, in line with tightening environmental regulations and consumer preferences for sustainable products. Companies such as Heraeus are actively developing and promoting environmentally responsible enamels and process innovations that reduce energy consumption and waste.
Looking ahead, the jewelry wire enameling technology market is expected to benefit from ongoing digitalization and automation trends. The integration of computer-controlled enameling lines, real-time quality monitoring, and data-driven process optimization is anticipated to improve efficiency and consistency, particularly in large-scale operations. As consumer tastes evolve and the global jewelry market expands, especially in emerging economies, demand for advanced enameling technologies is projected to remain robust through 2025 and beyond.
Technological Innovations: Next-Gen Enameling Methods and Equipment
The jewelry wire enameling sector is experiencing a wave of technological innovation in 2025, driven by the demand for higher precision, efficiency, and sustainability. Traditional torch and kiln enameling methods are being complemented—and in some cases replaced—by advanced techniques that leverage automation, digital controls, and new material science breakthroughs.
One of the most significant advancements is the integration of computer-controlled enameling equipment. These systems allow for precise temperature regulation and uniform application of enamel powders or liquid enamels onto fine jewelry wires, reducing human error and improving consistency. Leading manufacturers such as Rio Jeweler and Gesswein are expanding their portfolios to include programmable kilns and automated wire-coating lines, which are increasingly adopted by both artisanal and industrial jewelry producers.
Material innovation is also shaping the future of wire enameling. The development of lead-free and cadmium-free enamel formulations addresses both regulatory and consumer concerns about toxicity and environmental impact. Companies like Thompson Enamel are at the forefront, offering a wide range of eco-friendly enamels specifically engineered for compatibility with precious metal wires, including silver, gold, and copper alloys.
Laser-based enameling is emerging as a next-generation method, enabling ultra-fine application of enamel to micro-wires and intricate filigree designs. This technology, still in early commercial deployment, promises to open new creative possibilities and further miniaturize jewelry components. Equipment suppliers such as Legor are investing in R&D to refine laser enameling systems for broader market adoption in the coming years.
Digital design and additive manufacturing are also influencing enameling workflows. CAD-driven patterning and 3D-printed wire forms allow for complex geometries that were previously difficult to enamel uniformly. This synergy between digital fabrication and enameling is expected to accelerate, with companies like H.S. Walsh providing integrated solutions for jewelers seeking to combine traditional craftsmanship with modern production techniques.
Looking ahead, the jewelry wire enameling industry is poised for further transformation as sustainability, automation, and digitalization converge. The next few years will likely see broader adoption of smart enameling equipment, increased use of environmentally responsible materials, and the emergence of new design paradigms enabled by advanced manufacturing technologies.
Materials Evolution: Advances in Enamel Formulations and Wire Alloys
The landscape of jewelry wire enameling technologies is undergoing significant transformation in 2025, driven by advances in both enamel formulations and wire alloy development. Traditionally, vitreous enameling—fusing powdered glass to metal at high temperatures—has been the standard. However, recent years have seen a surge in innovative materials and processes aimed at improving durability, color vibrancy, and environmental sustainability.
One of the most notable trends is the shift toward lead-free and cadmium-free enamel formulations. Regulatory pressures and consumer demand for safer, eco-friendly products have prompted manufacturers to develop new glass compositions that maintain the brilliance and adhesion of traditional enamels while eliminating hazardous substances. Companies such as Thompson Enamel have been at the forefront, offering a wide range of lead-free enamels specifically engineered for jewelry applications. These formulations are designed to be compatible with various wire alloys, ensuring strong bonding and resistance to chipping or fading.
Parallel to enamel innovation, wire alloy technology is also advancing. The industry is witnessing increased use of specialized alloys that enhance the performance of enameled jewelry. For example, fine silver and high-purity copper remain popular due to their excellent enamel adhesion and malleability. However, new silver-copper alloys and nickel-free alternatives are being introduced to address issues such as tarnish resistance, hypoallergenic properties, and improved mechanical strength. Hardwires, a recognized supplier, has expanded its portfolio to include advanced wire alloys tailored for enameling, focusing on consistent surface quality and precise dimensional tolerances.
Another area of progress is the development of pre-coated and pre-enameled wires, which streamline the manufacturing process and reduce labor costs. These wires, produced by companies like Wieland, are coated with uniform enamel layers in controlled environments, ensuring repeatable quality and minimizing defects. This technology is particularly attractive for large-scale jewelry producers seeking efficiency and scalability.
Looking ahead, the next few years are expected to bring further integration of digital technologies, such as laser-assisted enameling and automated quality control systems, enhancing precision and repeatability. The ongoing collaboration between enamel manufacturers, wire producers, and jewelry designers is likely to yield new material combinations and application techniques, expanding the creative possibilities for enameled jewelry. As sustainability and performance remain top priorities, the evolution of materials in jewelry wire enameling is set to continue at a rapid pace, shaping the industry’s outlook through 2025 and beyond.
Sustainability and Eco-Friendly Practices in Enameling
Sustainability and eco-friendly practices are increasingly shaping the landscape of jewelry wire enameling technologies in 2025 and are expected to remain a central focus in the coming years. The enameling process, which traditionally involves fusing powdered glass to metal at high temperatures, has historically raised environmental concerns due to energy consumption, use of heavy metals, and waste generation. However, the industry is actively responding with innovative solutions and greener alternatives.
A significant trend is the adoption of lead-free enamels. Major enamel suppliers such as Thompson Enamel have expanded their product lines to include lead-free options, reducing the environmental and health risks associated with traditional lead-based enamels. These formulations are now widely used by both large-scale manufacturers and independent artisans, reflecting a broader industry shift toward safer materials.
Energy efficiency is another area of focus. Modern kiln technologies are being developed to minimize energy consumption during the firing process. Companies like Paragon Industries, a leading kiln manufacturer, are introducing programmable, insulated kilns that optimize firing cycles and reduce heat loss. These advancements not only lower the carbon footprint of enameling operations but also contribute to cost savings for jewelry producers.
Waste reduction and responsible sourcing are also gaining traction. Some manufacturers are implementing closed-loop water systems and improved filtration to capture and recycle particulates generated during wet enameling processes. Additionally, there is a growing emphasis on sourcing recycled metals for wire bases, aligning with broader jewelry industry initiatives for responsible material procurement. Organizations such as the Responsible Jewellery Council are setting standards and certifying companies that adhere to ethical and sustainable practices throughout the supply chain.
Looking ahead, the outlook for sustainable jewelry wire enameling is promising. Research into bio-based binders and alternative fluxes is underway, aiming to further reduce reliance on synthetic chemicals. Industry collaborations and knowledge-sharing platforms are fostering the adoption of best practices, while consumer demand for eco-friendly jewelry continues to drive innovation. As regulatory pressures mount and environmental awareness grows, it is expected that sustainability will remain a key driver of technological advancement in jewelry wire enameling through 2025 and beyond.
Competitive Landscape: Leading Manufacturers and Emerging Players
The competitive landscape for jewelry wire enameling technologies in 2025 is characterized by a blend of established global manufacturers and a dynamic cohort of emerging players, each contributing to technological innovation and market expansion. The sector is driven by increasing demand for high-quality, durable, and aesthetically versatile enameled wires, which are essential for both mass-market and artisanal jewelry production.
Among the leading manufacturers, ELANTAS stands out as a global leader in wire enamels, supplying advanced polymer-based coatings for fine and ultra-fine wires used in jewelry and decorative applications. The company’s ongoing investments in R&D have resulted in enamel formulations with enhanced flexibility, color stability, and environmental compliance, aligning with the jewelry industry’s shift toward sustainable materials. ELANTAS maintains a strong presence in Europe, North America, and Asia, serving both large-scale jewelry manufacturers and specialized wire producers.
Another significant player is ALTANA, the parent company of ELANTAS, which leverages its global chemical expertise to support innovation in wire enameling. ALTANA’s focus on eco-friendly and high-performance enamels is expected to shape industry standards in the coming years, particularly as regulatory pressures and consumer preferences increasingly favor non-toxic and recyclable materials.
In the Asia-Pacific region, Taiyo Holdings Co., Ltd. is recognized for its advanced enamel technologies, supplying both the electronics and jewelry sectors. The company’s expertise in precision coatings and color customization positions it as a key supplier for high-end jewelry wire applications, especially in markets such as Japan, South Korea, and China.
Emerging players are also making notable contributions, particularly in Europe and North America, where boutique manufacturers and startups are experimenting with novel enamel chemistries and application techniques. These companies often focus on niche markets, such as luxury or bespoke jewelry, and are agile in adopting digital manufacturing and sustainable practices. For example, several small-scale producers are exploring water-based and lead-free enamels, responding to both regulatory changes and consumer demand for ethical jewelry.
Looking ahead, the competitive landscape is expected to intensify as both established and emerging companies invest in automation, digital color matching, and environmentally friendly processes. Strategic collaborations between enamel suppliers, jewelry designers, and technology firms are likely to accelerate the adoption of next-generation enameling solutions, further diversifying the market and raising the bar for quality and sustainability.
Applications: Fine Jewelry, Fashion, and Industrial Uses
Jewelry wire enameling technologies are experiencing a dynamic phase in 2025, with applications expanding across fine jewelry, fashion accessories, and select industrial uses. The process of enameling—fusing colored glass powder onto metal wire—has evolved from traditional torch and kiln methods to include advanced, automated, and environmentally conscious techniques. This evolution is driven by both consumer demand for unique, durable designs and industry requirements for precision and scalability.
In the fine jewelry sector, leading manufacturers are leveraging high-purity precious metal wires (such as gold, silver, and platinum) with advanced enameling to create intricate, multicolored designs. Companies like Pandora and Tiffany & Co. have incorporated enameled wire elements into their collections, emphasizing both artisanal craftsmanship and repeatable quality. The use of lead-free, hypoallergenic enamels is now standard, reflecting stricter regulatory and consumer safety expectations. Automated micro-enameling systems, capable of applying ultra-thin, uniform coatings, are enabling mass production of detailed motifs previously only possible by hand.
In the fashion jewelry segment, the focus is on vibrant color palettes, cost-effective base metals (such as copper and brass), and rapid design turnover. Companies like Swarovski and Chamilia (a Swarovski company) utilize enameling to add visual impact and surface protection to wire-based charms, bracelets, and earrings. The adoption of UV-curable enamels and digital color-matching systems is streamlining prototyping and short-run production, allowing brands to respond quickly to seasonal trends. Additionally, the integration of recycled metals and eco-friendly enamels is becoming a key differentiator in the market.
Beyond adornment, enameled wire technologies are finding niche industrial applications, particularly where electrical insulation and corrosion resistance are required alongside aesthetic appeal. For example, Elesa, a manufacturer of industrial components, employs enameled wires in decorative yet functional hardware for luxury interiors and equipment. The durability and color stability of modern enamels make them suitable for high-wear environments, expanding their use in sectors such as automotive interiors and consumer electronics.
Looking ahead, the outlook for jewelry wire enameling technologies is shaped by ongoing material innovations, digital manufacturing, and sustainability imperatives. The next few years are expected to see further integration of smart manufacturing (including AI-driven quality control and robotics), broader adoption of bio-based enamels, and increased customization options for both luxury and mass-market segments. As consumer preferences continue to evolve, the versatility and resilience of enameled wire will ensure its relevance across diverse applications.
Regulatory Standards and Quality Assurance (Referencing jewelry.org, gia.edu)
The regulatory landscape and quality assurance protocols for jewelry wire enameling technologies are evolving rapidly as the industry responds to increasing consumer demand for safety, traceability, and environmental responsibility. In 2025, regulatory standards are shaped by both international guidelines and national legislation, with a strong emphasis on the composition of enamels, the purity of base metals, and the processes used in wire enameling.
Organizations such as the Jewelers of America play a pivotal role in setting voluntary standards and best practices for the industry. These standards address the use of lead-free and cadmium-free enamels, which are now widely adopted to comply with regulations in the United States, European Union, and other major markets. The Gemological Institute of America (GIA) also provides educational resources and certification programs that emphasize the importance of material disclosure, process transparency, and quality control in jewelry manufacturing, including enameling techniques.
Quality assurance in wire enameling is increasingly reliant on advanced analytical methods. Techniques such as X-ray fluorescence (XRF) and energy-dispersive X-ray spectroscopy (EDX) are used to verify the elemental composition of both the wire substrate and the enamel coating, ensuring compliance with regulatory limits on hazardous substances. Manufacturers are also adopting ISO 9001 and ISO 14001 standards to formalize their quality management and environmental management systems, further supporting traceability and accountability throughout the supply chain.
In 2025, traceability is a key focus, with digital tracking systems and blockchain-based solutions being piloted to document the provenance of materials and the specifics of enameling processes. This is particularly relevant for luxury and bespoke jewelry, where consumers increasingly demand proof of ethical sourcing and environmentally responsible production. Industry bodies such as Jewelers of America are encouraging members to adopt these technologies to enhance consumer trust and meet evolving regulatory expectations.
Looking ahead, regulatory standards are expected to become more stringent, particularly regarding the use of nanomaterials in advanced enameling technologies and the management of waste and emissions from enameling processes. The industry is responding with ongoing research into safer, more sustainable enameling materials and closed-loop manufacturing systems. As a result, companies that proactively align with emerging standards and invest in robust quality assurance frameworks are likely to gain a competitive advantage in the global jewelry market.
Challenges and Barriers: Technical, Economic, and Supply Chain Factors
Jewelry wire enameling technologies, which involve the application of vitreous or synthetic enamel coatings to fine metal wires, face a range of challenges and barriers in 2025. These obstacles span technical, economic, and supply chain domains, influencing both established manufacturers and emerging players in the sector.
Technical Challenges remain significant. Achieving consistent enamel adhesion and uniformity on ultra-fine wires is a persistent issue, especially as jewelry designs demand ever-thinner gauges and more intricate color patterns. The compatibility of enamel formulations with various base metals—such as gold, silver, copper, and specialty alloys—requires ongoing research and process refinement. Leading suppliers like Wieland and HARD have invested in advanced enameling lines and proprietary enamel chemistries, but even these companies report that micro-cracking, color fading, and surface defects can occur, particularly when scaling up production or introducing new color palettes.
Automation and digital process control are being adopted to improve quality and repeatability, but the high initial investment and the need for skilled operators remain barriers for smaller workshops. Furthermore, environmental regulations on heavy metals and volatile organic compounds (VOCs) in enamel formulations are tightening, especially in the EU and North America, requiring reformulation and new compliance protocols. Companies such as Schoeller Wires are actively developing lead-free and cadmium-free enamels, but these alternatives can present new technical hurdles, such as reduced color brilliance or altered firing temperatures.
Economic Barriers are also pronounced. The cost of precious metal wire substrates has remained volatile, with gold and silver prices experiencing fluctuations due to global economic uncertainty. This volatility impacts both raw material procurement and end-product pricing. Additionally, the capital expenditure required for state-of-the-art enameling equipment, such as continuous furnaces and precision winding systems, can be prohibitive for new entrants. Established players like Metallwarenfabrik and Cookson-CLAL have the scale to absorb these costs, but smaller manufacturers often struggle to compete on price and quality.
Supply Chain Factors further complicate the landscape. Sourcing high-purity enamels and specialty metal wires is increasingly challenging due to geopolitical tensions and logistical disruptions. The sector relies on a limited number of global suppliers for both raw enamels and precision-drawn wires, making it vulnerable to bottlenecks. For example, disruptions in European or East Asian supply chains can delay production schedules and increase costs. Companies like Wieland and HARD have responded by diversifying suppliers and investing in local production capabilities, but the risk of shortages and delays remains a concern for the industry as a whole.
Looking ahead, overcoming these challenges will require continued investment in R&D, greater collaboration across the supply chain, and adaptation to evolving regulatory and market demands. The sector’s ability to innovate in enamel chemistry, process automation, and sustainable sourcing will be critical to its resilience and growth in the coming years.
Future Outlook: Disruptive Technologies and Strategic Opportunities
The jewelry wire enameling sector is poised for significant transformation in 2025 and the coming years, driven by advances in materials science, automation, and digital integration. Enameling, the process of fusing colored glass to metal wires, is a critical step in producing high-value jewelry components, and recent technological innovations are set to disrupt traditional manufacturing paradigms.
One of the most notable trends is the adoption of advanced enameling furnaces and precision-controlled kilns, which enable more consistent temperature management and improved color uniformity. Leading equipment manufacturers such as Barton Smith and Uhlmann are investing in next-generation enameling lines that incorporate real-time process monitoring and automated quality control. These systems reduce human error, minimize material waste, and allow for the production of increasingly intricate wire designs.
Material innovation is another key driver. The development of lead-free and cadmium-free enamels, in response to tightening environmental and safety regulations, is accelerating. Companies like Thompson Enamel are at the forefront, offering a broad palette of eco-friendly enamels that meet global compliance standards. This shift not only addresses regulatory requirements but also appeals to a growing segment of environmentally conscious consumers.
Digitalization is reshaping the design-to-production workflow. Computer-aided design (CAD) and computer-aided manufacturing (CAM) tools are being integrated with enameling processes, enabling rapid prototyping and mass customization. Industry leaders such as Rio Grande are expanding their digital service offerings, providing jewelers with access to virtual design environments and automated order fulfillment. This digital shift is expected to lower entry barriers for small-scale designers and foster greater innovation in wire enameling artistry.
Looking ahead, the convergence of additive manufacturing (3D printing) with enameling technologies presents a disruptive opportunity. While still in early stages, research collaborations between equipment suppliers and academic institutions are exploring the direct application of enamel powders onto 3D-printed metal wires, potentially enabling unprecedented design complexity and production efficiency.
Strategically, companies that invest in automation, sustainable materials, and digital platforms are likely to capture emerging market opportunities. As consumer demand for personalized and ethically produced jewelry grows, the ability to offer bespoke, eco-friendly enameled wire products will become a key differentiator. The next few years will likely see increased collaboration between technology providers, material suppliers, and jewelry brands, accelerating the pace of innovation and setting new industry standards.
Sources & References
- Schmalz
- Fenice
- Argor-Heraeus
- Heraeus
- Pfarr Stanztechnik
- Rio Jeweler
- Thompson Enamel
- Legor
- H.S. Walsh
- Paragon Industries
- Responsible Jewellery Council
- ELANTAS
- ALTANA
- Pandora
- Elesa
- Jewelers of America
- Metallwarenfabrik
- Cookson-CLAL