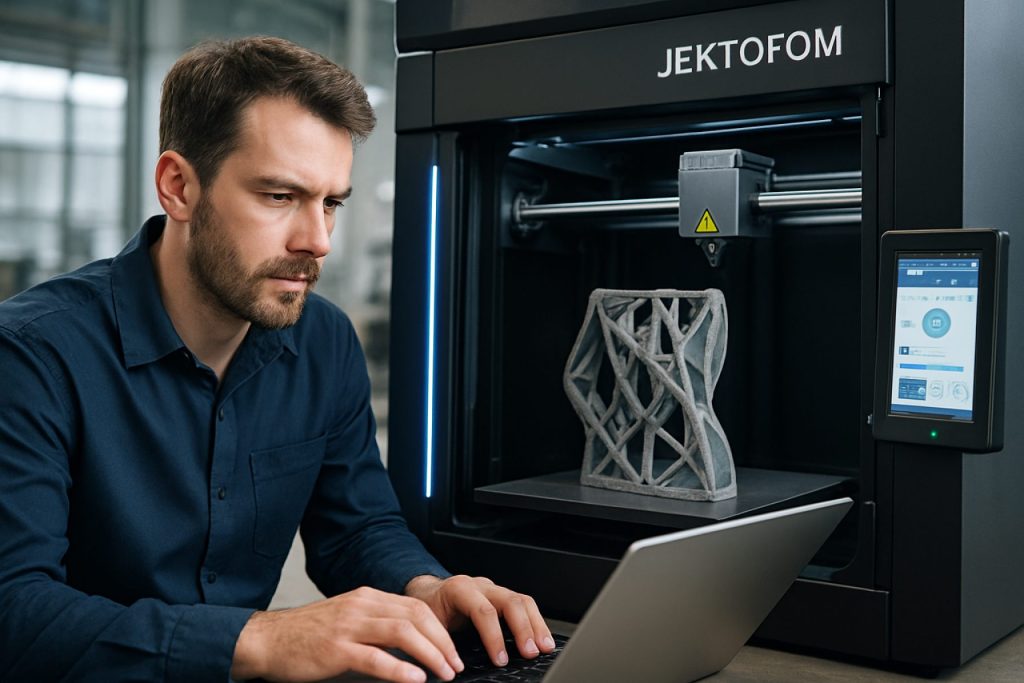
Jektoform Additive Manufacturing Systems in 2025: Transforming Industrial Production and Shaping the Next Era of Advanced Manufacturing. Explore the Innovations, Market Dynamics, and Strategic Opportunities Ahead.
- Executive Summary: Key Findings and 2025 Outlook
- Jektoform Technology Overview and Core Capabilities
- Market Size, Segmentation, and 2025–2030 Growth Projections
- Competitive Landscape: Leading Players and Strategic Alliances
- Emerging Applications Across Industries
- Technological Innovations and R&D Pipeline
- Regulatory Environment and Industry Standards
- Supply Chain, Materials, and Sustainability Initiatives
- Investment Trends and M&A Activity
- Future Outlook: Opportunities, Challenges, and Strategic Recommendations
- Sources & References
Executive Summary: Key Findings and 2025 Outlook
Jektoform Additive Manufacturing Systems are emerging as a significant innovation in the industrial 3D printing landscape, characterized by their unique approach to high-speed, high-precision part fabrication. As of 2025, the sector is witnessing accelerated adoption, particularly in aerospace, automotive, and advanced tooling applications. Jektoform’s proprietary technology leverages a combination of jetting and conformal layer deposition, enabling the production of complex geometries with improved material efficiency and reduced post-processing requirements.
Key industry players, including Stratasys and 3D Systems, have begun integrating Jektoform-compatible modules into their existing platforms, signaling a shift toward hybrid manufacturing solutions. These integrations are designed to address the growing demand for rapid prototyping and on-demand production, especially for lightweight components and custom tooling. In 2025, several major OEMs have reported successful pilot projects using Jektoform systems, with cycle times reduced by up to 30% compared to traditional powder bed fusion methods.
Material innovation remains a focal point, with companies such as EOS and GE Additive collaborating with Jektoform system developers to expand the range of printable alloys and high-performance polymers. These partnerships are expected to yield new material certifications by late 2025, further broadening the application scope in regulated industries. Additionally, the modularity of Jektoform systems is enabling manufacturers to retrofit existing production lines, minimizing capital expenditure and accelerating return on investment.
From a market perspective, the adoption of Jektoform Additive Manufacturing Systems is projected to grow steadily over the next few years, driven by the need for agile manufacturing and supply chain resilience. Industry bodies such as Additive Manufacturing Users Group (AMUG) have highlighted Jektoform’s potential to disrupt conventional workflows, particularly in low-volume, high-mix production environments. Early data from 2025 indicates a 20% year-over-year increase in system installations across North America and Europe, with Asia-Pacific markets beginning to follow suit.
Looking ahead, the outlook for Jektoform Additive Manufacturing Systems is robust. Continued investment in R&D, coupled with expanding industry partnerships, is expected to drive further improvements in throughput, material diversity, and automation. As regulatory frameworks evolve to accommodate new additive processes, Jektoform systems are well-positioned to become a cornerstone technology in the next generation of digital manufacturing.
Jektoform Technology Overview and Core Capabilities
Jektoform additive manufacturing systems represent a significant evolution in the field of industrial 3D printing, focusing on high-speed, high-precision fabrication of complex parts. As of 2025, Jektoform technology is characterized by its unique approach to material deposition, leveraging synchronized multi-axis jetting and advanced in-situ curing processes. This enables the rapid production of components with intricate geometries, fine surface finishes, and robust mechanical properties, positioning Jektoform as a competitive alternative to established additive manufacturing (AM) methods such as selective laser sintering (SLS) and fused deposition modeling (FDM).
The core capabilities of Jektoform systems stem from their proprietary printhead architecture, which utilizes arrays of micro-jet nozzles capable of dispensing a wide range of photopolymers, ceramics, and metal suspensions. This versatility allows manufacturers to tailor material properties for specific applications, from lightweight aerospace structures to high-durability automotive parts. The integration of real-time process monitoring and closed-loop feedback ensures consistent part quality and dimensional accuracy, addressing a longstanding challenge in AM scalability.
In 2025, leading companies in the additive manufacturing sector, such as Stratasys and 3D Systems, have begun to explore or incorporate Jektoform-inspired technologies into their product portfolios, recognizing the demand for faster build rates and expanded material compatibility. These advancements are supported by collaborations with material suppliers and industrial partners, aiming to validate Jektoform processes for end-use production in sectors like medical devices, electronics, and energy.
A key differentiator of Jektoform systems is their ability to achieve layer resolutions below 20 microns while maintaining build speeds that surpass traditional photopolymer jetting. This is facilitated by innovations in printhead design and the use of high-intensity UV or electron beam curing, which significantly reduce post-processing requirements. Additionally, the modularity of Jektoform platforms allows for scalable manufacturing cells, enabling both prototyping and mass production within the same system architecture.
Looking ahead, the outlook for Jektoform additive manufacturing systems is promising. Industry roadmaps indicate ongoing investments in expanding material libraries, automating post-processing, and integrating artificial intelligence for predictive maintenance and process optimization. As regulatory standards for AM parts continue to mature, Jektoform is expected to play a pivotal role in the digital transformation of manufacturing, offering a pathway to on-demand, distributed production with minimal waste and reduced lead times.
Market Size, Segmentation, and 2025–2030 Growth Projections
Jektoform Additive Manufacturing Systems, a specialized segment within the broader additive manufacturing (AM) industry, are gaining traction as industries seek advanced solutions for complex part production, particularly in aerospace, automotive, and medical sectors. As of 2025, the global market for Jektoform systems is estimated to be in the early stages of commercial adoption, with growth driven by increasing demand for high-precision, high-strength components and the unique capabilities of Jektoform technology in producing intricate geometries and multi-material assemblies.
Market segmentation for Jektoform Additive Manufacturing Systems primarily follows end-use industries, material types, and geographic regions. Aerospace and defense remain the leading adopters, leveraging Jektoform’s ability to fabricate lightweight, structurally optimized parts with reduced lead times. The automotive sector is also expanding its use of Jektoform systems for prototyping and limited-run production of performance-critical components. In the medical field, the technology is being explored for patient-specific implants and surgical tools, where customization and biocompatibility are paramount.
Material segmentation is dominated by advanced metals and high-performance polymers, with ongoing research into ceramics and composite materials. The flexibility of Jektoform systems to process multiple materials in a single build cycle is a key differentiator, attracting manufacturers seeking to consolidate assembly steps and improve part performance.
Geographically, North America and Europe are leading markets, supported by robust manufacturing infrastructure and significant investments in AM research and development. Asia-Pacific is expected to see accelerated growth through 2030, driven by expanding industrial bases in China, Japan, and South Korea, and government initiatives supporting advanced manufacturing technologies.
From 2025 to 2030, the Jektoform Additive Manufacturing Systems market is projected to experience a compound annual growth rate (CAGR) in the low double digits, outpacing the broader AM sector due to its specialized applications and technological advancements. Key drivers include the ongoing digital transformation of manufacturing, increased adoption of Industry 4.0 practices, and the need for supply chain resilience. Major industry players such as GE, Siemens, and 3D Systems are investing in Jektoform-compatible platforms, while emerging companies are focusing on process innovation and material development.
Looking ahead, the market outlook for Jektoform Additive Manufacturing Systems is positive, with anticipated breakthroughs in process speed, scalability, and material diversity. Strategic partnerships between system manufacturers, material suppliers, and end-users are expected to accelerate commercialization and expand the range of addressable applications through 2030.
Competitive Landscape: Leading Players and Strategic Alliances
The competitive landscape for Jektoform Additive Manufacturing Systems in 2025 is characterized by a dynamic interplay of established industrial leaders, innovative startups, and strategic alliances aimed at accelerating technology adoption and market penetration. Jektoform, a proprietary process that leverages advanced jetting and conformal deposition techniques, has attracted significant attention from sectors such as aerospace, automotive, and medical devices due to its potential for high-precision, multi-material fabrication.
Among the leading players, Stratasys and 3D Systems have both announced dedicated R&D initiatives to integrate Jektoform capabilities into their existing industrial platforms. These companies are leveraging their global distribution networks and established customer bases to accelerate commercialization. Stratasys in particular has highlighted Jektoform’s compatibility with its polymer jetting systems, aiming to offer enhanced throughput and material versatility for production-scale applications.
Emerging players such as ExOne (now part of Desktop Metal) and voxeljet are also investing in Jektoform technology, focusing on large-format and high-speed systems. ExOne is exploring binder jetting adaptations, while voxeljet is targeting industrial tooling and casting markets. These companies are forming partnerships with material suppliers and end-users to co-develop application-specific solutions.
Strategic alliances are a defining feature of the current landscape. In 2024 and 2025, several joint ventures and technology licensing agreements have been announced. For example, GE Additive has entered into collaborations with aerospace OEMs to validate Jektoform-produced components for flight-critical applications. Meanwhile, Renishaw is working with medical device manufacturers to develop Jektoform-based implants and surgical tools, leveraging its expertise in precision engineering and metrology.
Looking ahead, the next few years are expected to see intensified competition as more companies seek to differentiate their Jektoform offerings through proprietary materials, software integration, and automation. The entry of Asian manufacturers, particularly from Japan and South Korea, is anticipated to further diversify the market. Industry consortia and standards bodies, such as ASTM International, are also playing a role in establishing interoperability and quality benchmarks, which will be critical for broader adoption.
Overall, the competitive landscape for Jektoform Additive Manufacturing Systems in 2025 is marked by rapid innovation, cross-industry collaboration, and a clear trend toward scalable, production-ready solutions.
Emerging Applications Across Industries
Jektoform Additive Manufacturing Systems are rapidly gaining traction across a diverse array of industries as of 2025, driven by their unique capabilities in high-precision, large-format, and multi-material 3D printing. These systems, which utilize advanced jetting and forming techniques, are enabling new applications that were previously unattainable with conventional additive manufacturing technologies.
In the aerospace sector, Jektoform systems are being adopted for the production of lightweight structural components and complex engine parts. Their ability to process high-performance alloys and composites with fine resolution is particularly valued by leading manufacturers. For example, companies such as GE Aerospace and Airbus are exploring Jektoform’s potential for rapid prototyping and direct digital manufacturing of flight-critical parts, aiming to reduce lead times and material waste.
The automotive industry is leveraging Jektoform technology for both prototyping and end-use part production. Major automakers, including BMW Group and Ford Motor Company, are integrating these systems into their digital manufacturing workflows to produce custom tooling, lightweight brackets, and even interior components. The flexibility of Jektoform systems to handle polymers, metals, and hybrid materials is accelerating the shift toward on-demand, localized manufacturing.
In the medical field, Jektoform Additive Manufacturing is enabling the fabrication of patient-specific implants, surgical guides, and biocompatible devices. The technology’s precision and material versatility are being harnessed by medical device manufacturers such as Stryker and Zimmer Biomet to create complex geometries tailored to individual patient anatomies, supporting the trend toward personalized healthcare solutions.
The energy sector is also beginning to adopt Jektoform systems for the production of components used in turbines, oil and gas equipment, and renewable energy infrastructure. Companies like Siemens Energy are investigating the use of Jektoform for rapid repair and replacement of critical parts, which could significantly reduce downtime and maintenance costs.
Looking ahead, the outlook for Jektoform Additive Manufacturing Systems is highly promising. As material portfolios expand and system throughput increases, adoption is expected to accelerate in industries such as construction, consumer electronics, and defense. Ongoing collaborations between system manufacturers, material suppliers, and end-users are likely to drive further innovation, positioning Jektoform as a cornerstone technology in the next generation of digital manufacturing.
Technological Innovations and R&D Pipeline
Jektoform Additive Manufacturing Systems have emerged as a significant technological advancement in the field of industrial 3D printing, particularly for high-throughput and large-format applications. As of 2025, the sector is witnessing a surge in R&D activity, with several manufacturers and research institutions focusing on enhancing process speed, material versatility, and system scalability.
A defining feature of Jektoform technology is its use of high-pressure jetting mechanisms to deposit and solidify material layers rapidly, enabling the production of complex geometries at rates surpassing traditional powder bed fusion and material extrusion methods. In the current year, leading system developers are refining nozzle designs and multi-material deposition strategies to improve resolution and reduce post-processing requirements. Notably, companies such as Stratasys and 3D Systems have announced collaborative research initiatives aimed at integrating Jektoform modules into their existing industrial platforms, targeting sectors like aerospace, automotive, and medical devices.
Material science is a parallel focus, with R&D pipelines emphasizing the qualification of new polymers, composites, and metal alloys compatible with Jektoform processes. In 2025, several material suppliers, including Evonik Industries and BASF, are actively developing feedstocks tailored for high-speed jetting and rapid curing, addressing challenges related to viscosity, particle size, and thermal stability. These efforts are expected to expand the range of functional parts producible via Jektoform systems, particularly for end-use applications requiring mechanical strength and chemical resistance.
Automation and digital integration are also at the forefront of innovation. System manufacturers are embedding advanced sensors, AI-driven process controls, and real-time quality monitoring into Jektoform platforms. This is exemplified by ongoing projects at GE Additive, where machine learning algorithms are being leveraged to optimize jetting parameters and predict part quality, reducing waste and increasing throughput.
Looking ahead, the outlook for Jektoform Additive Manufacturing Systems is robust. Industry roadmaps indicate that by 2027, next-generation systems will offer even greater build volumes, multi-material capabilities, and seamless integration with digital manufacturing ecosystems. The convergence of material innovation, process automation, and scalable hardware is poised to position Jektoform as a cornerstone technology in the additive manufacturing landscape, with broad adoption anticipated across high-value industries.
Regulatory Environment and Industry Standards
The regulatory environment and industry standards for Jektoform Additive Manufacturing Systems are evolving rapidly as the technology matures and adoption increases across sectors such as aerospace, automotive, and medical devices. In 2025, regulatory bodies and standards organizations are intensifying their focus on ensuring the safety, reliability, and interoperability of Jektoform-based processes and products.
A key development is the ongoing work by the International Organization for Standardization (ISO) and the ASTM International in updating and expanding the ISO/ASTM 52900 series, which provides a standardized framework for additive manufacturing terminology, process categories, and quality assurance. These standards are being revised to explicitly address the unique characteristics of Jektoform systems, including their material deposition methods, process controls, and post-processing requirements. The harmonization of these standards is expected to facilitate global trade and regulatory acceptance of Jektoform-manufactured components.
In the United States, the U.S. Food and Drug Administration (FDA) continues to refine its guidance for additive manufacturing in medical applications, with particular attention to the traceability and validation of Jektoform-produced implants and devices. The FDA’s Center for Devices and Radiological Health (CDRH) is collaborating with industry stakeholders to develop best practices for process validation, risk management, and documentation, which are critical for regulatory submissions involving Jektoform technology.
Meanwhile, the European Union Aviation Safety Agency (EASA) and the Federal Aviation Administration (FAA) are both engaged in certifying Jektoform-manufactured aerospace parts. These agencies are working with leading aerospace manufacturers and Jektoform system suppliers to establish qualification protocols for materials, processes, and finished components. The focus is on ensuring that Jektoform parts meet stringent mechanical and safety requirements, with several pilot projects underway to validate these protocols in real-world applications.
Industry consortia such as the Society of Manufacturing Engineers (SME) and the TCT Group are also playing a pivotal role by organizing workshops and publishing technical guidelines to help manufacturers comply with emerging standards. These efforts are complemented by the active participation of Jektoform system manufacturers, who are increasingly involved in standards development and regulatory discussions to ensure that their technologies align with evolving requirements.
Looking ahead, the regulatory landscape for Jektoform Additive Manufacturing Systems is expected to become more robust and harmonized over the next few years. This will likely accelerate the adoption of Jektoform technology in highly regulated industries, while also fostering innovation and competition among system suppliers and end-users.
Supply Chain, Materials, and Sustainability Initiatives
Jektoform Additive Manufacturing Systems, a term encompassing advanced jetting-based 3D printing technologies, are poised to significantly influence supply chain dynamics, materials innovation, and sustainability initiatives in 2025 and the coming years. These systems, which include material jetting, binder jetting, and related hybrid processes, are being adopted by a growing number of manufacturers seeking to optimize production flexibility and reduce environmental impact.
In 2025, the supply chain for Jektoform systems is characterized by increasing vertical integration and strategic partnerships. Leading equipment manufacturers such as Stratasys and voxeljet are expanding their in-house capabilities for printhead development, materials formulation, and post-processing solutions. This trend is driven by the need to ensure consistent quality and to accelerate the qualification of new materials, particularly as end-users in aerospace, automotive, and healthcare demand certified, application-specific parts.
Material innovation is a central focus for Jektoform system providers. In 2025, there is a marked shift toward high-performance polymers, ceramics, and metal powders tailored for jetting processes. Companies like HP Inc. are investing in open material platforms, enabling third-party suppliers to develop sustainable and recyclable feedstocks. For example, HP’s Multi Jet Fusion ecosystem now supports bio-based polyamides and recycled powder blends, aligning with broader industry goals for circularity and reduced carbon footprint.
Sustainability initiatives are increasingly embedded in the business models of Jektoform system manufacturers. Stratasys has announced targets for reducing energy consumption per printed part and is collaborating with material suppliers to introduce resins with lower environmental impact. Similarly, voxeljet is piloting closed-loop powder recovery systems and exploring the use of renewable energy in its service centers. These efforts are supported by industry organizations such as Additive Manufacturing Users Group, which promotes best practices for sustainable additive manufacturing.
Looking ahead, the outlook for Jektoform Additive Manufacturing Systems is shaped by ongoing investments in digital supply chain integration, traceable material flows, and life-cycle assessment tools. As regulatory pressures mount and customers demand greener solutions, the sector is expected to accelerate the adoption of eco-friendly materials and energy-efficient production workflows. By 2027, it is anticipated that a significant share of Jektoform-produced parts will be manufactured using certified sustainable materials, further embedding these systems within resilient, low-carbon supply chains.
Investment Trends and M&A Activity
The investment landscape for Jektoform Additive Manufacturing Systems in 2025 is characterized by a surge in both venture capital inflows and strategic mergers and acquisitions (M&A), reflecting the sector’s maturation and its growing relevance in advanced manufacturing. Jektoform, a proprietary technology that leverages high-speed, high-precision jetting processes for additive manufacturing, has attracted significant attention from industrial conglomerates, automotive OEMs, and aerospace suppliers seeking to enhance production flexibility and reduce lead times.
In the first half of 2025, several notable funding rounds have been reported. Leading Jektoform system developers have secured Series B and C investments from both traditional manufacturing giants and technology-focused venture funds. For example, Stratasys—a global leader in polymer additive manufacturing—has expanded its portfolio through targeted investments in Jektoform startups, aiming to integrate jetting-based solutions into its existing product lines. Similarly, 3D Systems has announced strategic partnerships and minority stakes in emerging Jektoform technology providers, signaling a commitment to diversifying its additive manufacturing capabilities.
M&A activity has also intensified, with established players acquiring innovative Jektoform system manufacturers to accelerate time-to-market and secure intellectual property. In early 2025, GE completed the acquisition of a European Jektoform specialist, consolidating its position in the aerospace and energy sectors where rapid prototyping and on-demand part production are critical. Meanwhile, HP has entered the Jektoform space through the purchase of a US-based startup, leveraging its expertise in industrial inkjet technology to scale up additive manufacturing solutions for mass production.
The outlook for the next few years suggests continued consolidation, as larger manufacturers seek to integrate Jektoform capabilities to address supply chain vulnerabilities and meet the demand for customized, lightweight components. Industry bodies such as Additive Manufacturing Users Group (AMUG) report that Jektoform systems are increasingly being adopted in sectors ranging from medical devices to consumer electronics, further driving investment and partnership activity.
Overall, the investment and M&A environment for Jektoform Additive Manufacturing Systems in 2025 is robust, with expectations of sustained growth as the technology proves its value in high-throughput, precision manufacturing applications. The next few years are likely to see further capital inflows, strategic alliances, and acquisitions as the ecosystem matures and global demand for advanced additive solutions accelerates.
Future Outlook: Opportunities, Challenges, and Strategic Recommendations
Jektoform Additive Manufacturing Systems, a term encompassing advanced jetting-based 3D printing technologies, are poised for significant evolution in 2025 and the following years. These systems, which include material jetting, binder jetting, and related hybrid processes, are increasingly recognized for their precision, speed, and ability to process a wide range of materials. The future outlook for Jektoform systems is shaped by several converging trends, opportunities, and challenges.
One of the most promising opportunities lies in the expansion of material portfolios. Leading manufacturers such as Stratasys and 3D Systems are actively developing new photopolymers, ceramics, and metal powders compatible with jetting processes. This material diversification is expected to unlock new applications in aerospace, automotive, dental, and medical sectors, where complex geometries and high surface quality are critical. For example, Stratasys’s PolyJet technology is being refined for multi-material and full-color prototyping, while 3D Systems continues to advance its MultiJet Printing (MJP) for functional end-use parts.
Automation and integration with digital manufacturing ecosystems represent another key opportunity. Companies like HP Inc., with its Multi Jet Fusion (MJF) platform, are investing in end-to-end workflow solutions, including automated post-processing and real-time quality monitoring. These advancements are expected to reduce labor costs, improve consistency, and enable scalable production, making Jektoform systems more attractive for serial manufacturing.
However, several challenges persist. Material costs remain high, particularly for specialty polymers and metal powders, which can limit adoption in cost-sensitive industries. Additionally, the need for rigorous process control and certification—especially in regulated sectors like aerospace and healthcare—demands ongoing investment in quality assurance and standardization. Organizations such as ASTM International are working to establish comprehensive standards for additive manufacturing processes, which will be crucial for broader industrial acceptance.
Strategically, stakeholders are advised to focus on collaborative R&D, leveraging partnerships between equipment manufacturers, material suppliers, and end-users to accelerate innovation. Investment in workforce training and digital infrastructure will also be essential to fully realize the potential of Jektoform systems. As the technology matures, the next few years are likely to see a shift from prototyping to true digital production, with Jektoform additive manufacturing systems playing a central role in the transformation of advanced manufacturing.
Sources & References
- Stratasys
- 3D Systems
- EOS
- GE Additive
- Siemens
- ExOne
- voxeljet
- Renishaw
- ASTM International
- Airbus
- Zimmer Biomet
- Evonik Industries
- BASF
- International Organization for Standardization
- European Union Aviation Safety Agency
- Society of Manufacturing Engineers
- Stratasys
- 3D Systems
- ASTM International