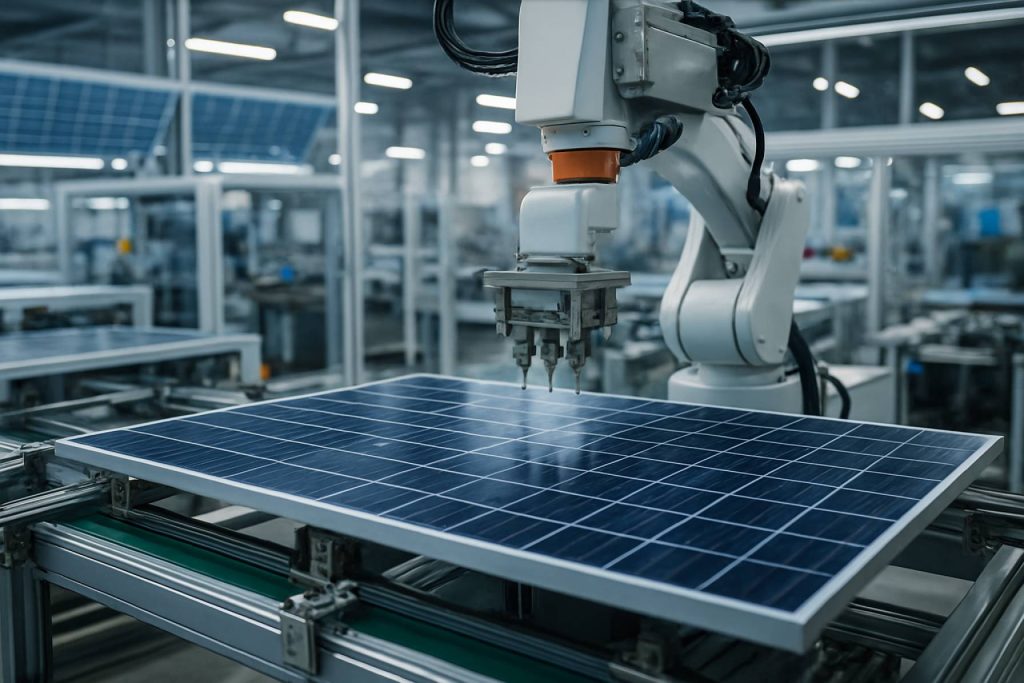
Solar Photovoltaic (PV) Panel Manufacturing in 2025: Navigating Explosive Market Growth and Technological Breakthroughs. Discover How Innovation and Policy Are Shaping the Next Five Years.
- Executive Summary: Key Trends and Market Drivers
- Global Market Size, Growth Rate, and 2025–2030 Forecasts
- Major Manufacturers and Industry Structure (e.g., First Solar, JinkoSolar, Trina Solar)
- Technological Innovations: High-Efficiency Cells, Bifacial Panels, and Tandem Structures
- Supply Chain Dynamics and Raw Material Sourcing
- Policy, Regulation, and Incentives: Impact on Manufacturing Expansion
- Sustainability and Circular Economy Initiatives in PV Manufacturing
- Regional Analysis: Asia-Pacific, Europe, North America, and Emerging Markets
- Competitive Landscape and Strategic Partnerships
- Future Outlook: Market Opportunities, Challenges, and Disruptive Technologies
- Sources & References
Executive Summary: Key Trends and Market Drivers
The solar photovoltaic (PV) panel manufacturing sector is experiencing robust growth in 2025, driven by accelerating global decarbonization efforts, technological innovation, and expanding policy support. The industry’s momentum is underscored by record-breaking new installations, with global solar PV capacity additions expected to surpass 400 GW in 2025, up from approximately 350 GW in 2023. This surge is fueled by ambitious renewable energy targets in major economies, declining module costs, and the rapid scaling of manufacturing capacity, particularly in Asia.
China remains the dominant force in PV manufacturing, accounting for over 80% of global module production. Leading Chinese manufacturers such as JinkoSolar, Trina Solar, and Canadian Solar (headquartered in Canada but with significant manufacturing in China) continue to expand their gigawatt-scale facilities, leveraging advanced automation and vertical integration to drive down costs and improve efficiency. These companies are at the forefront of adopting next-generation cell technologies, including TOPCon (Tunnel Oxide Passivated Contact) and HJT (Heterojunction Technology), which are expected to become mainstream by 2026 due to their higher conversion efficiencies and better performance in diverse climates.
Outside China, the United States and Europe are intensifying efforts to localize PV manufacturing, spurred by supply chain resilience concerns and new policy incentives. The U.S. Inflation Reduction Act has catalyzed significant investment in domestic manufacturing, with companies like First Solar expanding their thin-film module production capacity. In Europe, initiatives to revive local manufacturing are underway, with firms such as Meyer Burger scaling up production of high-efficiency heterojunction modules. These regional developments aim to diversify the global supply chain and reduce dependency on Asian imports.
Key market drivers include the ongoing decline in PV module prices, which have reached historic lows in 2025, and the growing adoption of bifacial and high-wattage modules that enhance energy yield per unit area. Sustainability is also a rising priority, with manufacturers investing in low-carbon production processes and recycling initiatives to address lifecycle emissions and regulatory requirements.
Looking ahead, the solar PV manufacturing sector is poised for continued expansion, with global capacity projected to exceed 1,000 GW annually by 2027. The convergence of policy support, technological advancement, and market demand is expected to sustain double-digit growth rates, positioning solar PV as a cornerstone of the global energy transition.
Global Market Size, Growth Rate, and 2025–2030 Forecasts
The global solar photovoltaic (PV) panel manufacturing sector is experiencing robust growth, driven by accelerating renewable energy adoption, supportive government policies, and ongoing technological advancements. As of 2025, the worldwide annual PV module production capacity is estimated to exceed 1,200 GW, a significant increase from previous years, reflecting both new factory buildouts and capacity expansions by leading manufacturers. This surge is primarily led by China, which accounts for over 80% of global PV manufacturing capacity, with major players such as JinkoSolar, Trina Solar, Canadian Solar, and LONGi Green Energy Technology dominating the market.
In 2025, global PV panel shipments are projected to surpass 500 GW, up from approximately 350 GW in 2023. This growth is underpinned by strong demand in key markets including China, the United States, India, and the European Union. The U.S. is ramping up domestic manufacturing capacity, supported by incentives under the Inflation Reduction Act, with companies like First Solar and Q CELLS investing in new gigawatt-scale facilities. India is also expanding its manufacturing base, with firms such as Waaree Energies and Adani Green Energy increasing output to meet both domestic and export demand.
Technological innovation remains a key driver of market expansion. The industry is rapidly transitioning from PERC (Passivated Emitter and Rear Cell) to advanced cell architectures such as TOPCon (Tunnel Oxide Passivated Contact) and HJT (Heterojunction Technology), which offer higher efficiencies and better performance. Leading manufacturers including JinkoSolar and Trina Solar are scaling up production of these next-generation modules, aiming to capture premium market segments and support utility-scale projects.
Looking ahead to 2030, the global PV manufacturing market is forecast to maintain a compound annual growth rate (CAGR) of 8–10%, with annual module shipments potentially reaching 900 GW or more. This outlook is supported by ambitious national and corporate decarbonization targets, ongoing cost reductions, and the increasing competitiveness of solar PV compared to conventional energy sources. However, the sector faces challenges including supply chain constraints, trade policy uncertainties, and the need for further diversification of manufacturing outside China to enhance global energy security.
Major Manufacturers and Industry Structure (e.g., First Solar, JinkoSolar, Trina Solar)
The global solar photovoltaic (PV) panel manufacturing industry in 2025 is characterized by rapid expansion, technological innovation, and a highly competitive landscape dominated by a handful of major players, primarily headquartered in China, the United States, and Southeast Asia. The industry structure is shaped by both vertically integrated giants and specialized module producers, with a strong emphasis on scaling up capacity and improving efficiency to meet surging global demand.
Chinese manufacturers continue to dominate the global PV panel market, accounting for over 70% of worldwide module production capacity. JinkoSolar, Trina Solar, and Canadian Solar (despite its name, headquartered in China) are among the largest, each with annual module shipment volumes exceeding 50 GW as of 2024. These companies have aggressively expanded their manufacturing footprints, not only within China but also in Southeast Asia, India, and the United States, to mitigate trade barriers and serve regional markets more efficiently.
In the United States, First Solar stands out as the leading domestic PV panel manufacturer, specializing in thin-film cadmium telluride (CdTe) technology. First Solar has announced significant capacity expansions, with new factories coming online in Ohio and Alabama, aiming to reach over 10 GW of annual production capacity in North America by 2026. This positions the company as a key supplier for the U.S. market, especially in light of policy incentives favoring domestic content.
Other notable players include LONGi Green Energy, the world’s largest manufacturer of monocrystalline silicon wafers and modules, and Talesun Solar, which has expanded its global reach through joint ventures and overseas manufacturing. These companies are investing heavily in next-generation technologies such as TOPCon (Tunnel Oxide Passivated Contact) and HJT (Heterojunction) cells, aiming to push module efficiencies beyond 24% in commercial production.
The industry is also witnessing increased vertical integration, with leading manufacturers controlling the supply chain from polysilicon production to finished modules. This integration helps manage costs, ensure quality, and secure supply amid ongoing geopolitical and trade uncertainties. Meanwhile, new entrants and regional players are emerging, particularly in India and Southeast Asia, supported by government incentives and rising local demand.
Looking ahead, the global PV manufacturing landscape is expected to remain highly dynamic through 2025 and beyond, with further consolidation among top players, continued capacity expansions, and a strong focus on technological differentiation. The race to scale up and innovate is driven by ambitious renewable energy targets worldwide and the imperative to reduce costs while improving module performance.
Technological Innovations: High-Efficiency Cells, Bifacial Panels, and Tandem Structures
The solar photovoltaic (PV) panel manufacturing sector is undergoing rapid technological transformation in 2025, with a strong focus on high-efficiency cells, bifacial panels, and tandem structures. These innovations are driven by the need to reduce the levelized cost of electricity (LCOE), maximize energy yield, and address land and resource constraints as global solar deployment accelerates.
High-efficiency cell technologies, particularly those based on passivated emitter and rear cell (PERC), tunnel oxide passivated contact (TOPCon), and heterojunction (HJT) architectures, are now mainstream in new manufacturing lines. Leading manufacturers such as JinkoSolar, Trina Solar, and Canadian Solar have announced mass production of TOPCon and HJT modules, with commercial module efficiencies exceeding 23% in 2025. These companies are investing heavily in R&D and expanding their production capacities to meet surging demand for high-performance modules.
Bifacial panel technology, which enables energy generation from both the front and rear sides of the module, continues to gain market share. Bifacial modules are now standard offerings from major manufacturers, including LONGi Green Energy and JA Solar. Field data and pilot projects demonstrate that bifacial modules can deliver 5–20% higher energy yields compared to monofacial panels, depending on installation conditions and albedo. This performance advantage is particularly attractive for utility-scale projects, where maximizing output per unit area is critical.
Tandem cell structures, especially those combining silicon with perovskite layers, are at the forefront of next-generation PV innovation. In 2025, several manufacturers and research consortia are piloting tandem modules with efficiencies approaching or surpassing 27%. Companies such as Meyer Burger are actively developing and scaling up perovskite-silicon tandem technologies, aiming for commercial production within the next few years. The promise of tandem structures lies in their potential to break through the single-junction efficiency limits of silicon, offering a pathway to even lower LCOE and broader application scenarios.
Looking ahead, the PV manufacturing landscape is expected to be shaped by continued advances in cell architectures, materials science, and automated production processes. The integration of high-efficiency, bifacial, and tandem technologies is anticipated to further drive down costs and accelerate the global transition to solar energy.
Supply Chain Dynamics and Raw Material Sourcing
The supply chain dynamics and raw material sourcing for solar photovoltaic (PV) panel manufacturing are undergoing significant transformation in 2025, shaped by global demand growth, geopolitical shifts, and technological advancements. The PV manufacturing process is highly dependent on a complex, international supply chain, with critical materials including polysilicon, silver, aluminum, glass, and specialty films. As of 2025, the global solar industry continues to experience robust expansion, with annual installations projected to surpass 400 GW, intensifying the need for reliable and resilient supply chains.
Polysilicon remains the foundational raw material for crystalline silicon PV cells, which account for over 90% of global module production. The majority of polysilicon production is concentrated in China, with leading manufacturers such as GCL-Poly Energy Holdings, Xinjiang Daqo New Energy, and Tongwei Group dominating the market. In 2025, these companies continue to expand capacity, but the industry faces ongoing scrutiny over supply chain transparency and calls for diversification, particularly from the United States and European Union, which are seeking to reduce reliance on a single region for critical materials.
Silver, essential for cell metallization, is another key input facing supply chain pressures. The solar sector now accounts for approximately 15% of global silver demand, and with rising module efficiencies, manufacturers are actively seeking to reduce silver content per cell. Companies like Trina Solar and JinkoSolar are investing in alternative metallization techniques and exploring copper-based solutions to mitigate cost and supply risks.
Glass and aluminum, used for module encapsulation and framing, are also subject to price volatility and logistical challenges. Leading glass suppliers such as Xinyi Glass Holdings and Flat Glass Group have ramped up production to meet surging demand, while module manufacturers are increasingly localizing supply chains to reduce transportation costs and carbon footprints.
In response to these dynamics, major PV manufacturers are pursuing vertical integration and strategic partnerships to secure raw material access. For example, LONGi Green Energy Technology and Canadian Solar have announced new investments in upstream polysilicon and wafer production, aiming to insulate themselves from market shocks and ensure long-term supply stability.
Looking ahead, the solar PV supply chain in 2025 and beyond is expected to become more diversified and resilient, with increased regional manufacturing initiatives in the U.S., Europe, and India. However, the sector will continue to face challenges related to raw material price fluctuations, trade policy uncertainties, and the need for sustainable sourcing practices as global solar deployment accelerates.
Policy, Regulation, and Incentives: Impact on Manufacturing Expansion
Policy frameworks, regulatory measures, and government incentives are playing a pivotal role in shaping the global landscape of solar photovoltaic (PV) panel manufacturing in 2025 and the coming years. As nations intensify their climate commitments and seek energy security, targeted interventions are accelerating both domestic manufacturing capacity and technological innovation.
In the United States, the Inflation Reduction Act (IRA) continues to be a transformative force, offering substantial tax credits and direct incentives for domestic PV manufacturing. The act’s provisions, including advanced manufacturing production credits, are spurring investments in new and expanded facilities. Major manufacturers such as First Solar and Q CELLS have announced multi-gigawatt factory expansions, citing the IRA’s incentives as a key driver. The U.S. Department of Energy is also supporting R&D and supply chain resilience, aiming to reduce reliance on imports and foster a vertically integrated domestic industry.
In the European Union, the Net-Zero Industry Act and the REPowerEU plan are central to the bloc’s strategy to boost local PV manufacturing. These policies prioritize permitting reform, financial support, and public procurement preferences for European-made panels. Companies such as Meyer Burger are scaling up production in Germany and other EU countries, leveraging these incentives to compete with Asian manufacturers. The European Solar PV Industry Alliance, backed by the European Commission, is coordinating efforts to reach at least 30 GW of annual manufacturing capacity by 2025.
China remains the world’s dominant PV manufacturing hub, supported by long-standing industrial policies, low-cost financing, and export incentives. Leading firms like JinkoSolar, Trina Solar, and Canadian Solar (despite its name, a major Chinese manufacturer) continue to expand capacity, invest in next-generation technologies, and benefit from robust domestic demand. However, new trade measures in the U.S. and EU—such as tariffs and local content requirements—are prompting some Chinese companies to consider overseas manufacturing investments to maintain market access.
Looking ahead, policy-driven incentives and regulatory frameworks are expected to remain decisive in shaping the competitive dynamics of PV manufacturing. Governments are increasingly linking incentives to sustainability criteria, supply chain transparency, and workforce development. As a result, the next few years will likely see a more geographically diversified manufacturing base, with policy and regulation as key levers for both expansion and innovation.
Sustainability and Circular Economy Initiatives in PV Manufacturing
Sustainability and circular economy initiatives are increasingly shaping the solar photovoltaic (PV) panel manufacturing sector in 2025, as the industry responds to both regulatory pressures and market demand for greener products. Major manufacturers are integrating eco-friendly practices across the value chain, from raw material sourcing to end-of-life management, to minimize environmental impact and enhance resource efficiency.
A key trend is the adoption of low-carbon manufacturing processes. Leading companies such as First Solar and Trina Solar have invested in energy-efficient production lines and are sourcing renewable electricity for their factories. First Solar, for example, emphasizes its use of closed-loop water systems and recycling of manufacturing scrap, while also publishing detailed sustainability reports outlining its carbon footprint reduction targets. Similarly, JinkoSolar has committed to using 100% renewable energy in its global operations by 2025, aligning with the RE100 initiative.
Material circularity is another focal point. Manufacturers are increasingly designing panels for recyclability and reusability. First Solar operates dedicated recycling facilities capable of recovering up to 90% of semiconductor material and glass from decommissioned modules. European manufacturers, under the guidance of organizations like SolarPower Europe, are collaborating to standardize recycling protocols and improve collection rates for end-of-life PV modules. The European Union’s Waste Electrical and Electronic Equipment (WEEE) Directive continues to drive compliance and innovation in recycling infrastructure.
Supply chain transparency and responsible sourcing are also gaining prominence. Companies such as Canadian Solar and LONGi Green Energy Technology are publishing supplier codes of conduct and conducting third-party audits to ensure ethical sourcing of polysilicon and other critical materials. This is partly in response to growing scrutiny over labor and environmental practices in the upstream supply chain.
Looking ahead, the outlook for sustainability in PV manufacturing is robust. Industry bodies like Solar Energy Industries Association and SolarPower Europe are setting ambitious targets for lifecycle emissions reductions and circularity. Innovations in panel design—such as bifacial modules and lead-free soldering—are expected to further reduce environmental impacts. As global solar deployment accelerates, the integration of circular economy principles will be critical to ensuring the long-term sustainability and social license of the PV industry.
Regional Analysis: Asia-Pacific, Europe, North America, and Emerging Markets
The global landscape of solar photovoltaic (PV) panel manufacturing in 2025 is characterized by dynamic regional shifts, technological advancements, and evolving policy frameworks. The Asia-Pacific region continues to dominate both production capacity and technological innovation, while Europe and North America are intensifying efforts to localize manufacturing and reduce supply chain dependencies. Emerging markets are also ramping up investments, aiming to capture a share of the rapidly expanding global solar market.
Asia-Pacific remains the epicenter of PV panel manufacturing, with China accounting for over 80% of global production capacity. Leading Chinese manufacturers such as JinkoSolar, Trina Solar, and Canadian Solar (headquartered in Canada but with major manufacturing in China) are expanding their gigawatt-scale facilities and investing in next-generation technologies, including TOPCon and heterojunction cells. In 2025, these companies are expected to further increase their market share, driven by strong domestic demand and aggressive export strategies. Southeast Asian countries, notably Vietnam and Malaysia, are also significant players, hosting manufacturing plants for global firms seeking to diversify supply chains and mitigate trade risks.
Europe is witnessing a resurgence in PV manufacturing, propelled by the European Union’s Green Deal and the REPowerEU initiative, which aim to strengthen energy security and accelerate the energy transition. Companies such as Meyer Burger in Germany and Switzerland are scaling up production of high-efficiency modules, leveraging advanced cell technologies and automated manufacturing. The EU’s policy support, including funding for local gigafactories and incentives for domestic content, is expected to boost regional capacity, with several new plants scheduled to come online by 2026.
North America is rapidly expanding its PV manufacturing footprint, spurred by the U.S. Inflation Reduction Act and related incentives for domestic solar production. First Solar, the largest U.S.-based manufacturer, is investing billions in new facilities in Ohio, Alabama, and Louisiana, focusing on thin-film cadmium telluride technology. Other companies, such as Qcells (a subsidiary of Hanwha Solutions, South Korea), are also building large-scale factories in Georgia, aiming to supply both modules and upstream components like wafers and cells.
Emerging markets in Latin America, the Middle East, and Africa are increasingly investing in local PV manufacturing to meet growing demand and reduce import reliance. Governments in India, for example, are supporting domestic manufacturers such as Waaree Energies and Adani Solar through production-linked incentives and import duties. These efforts are expected to gradually increase regional self-sufficiency and foster technology transfer in the coming years.
Overall, the outlook for 2025 and beyond points to continued growth in global PV manufacturing, with regional diversification and technological innovation shaping the competitive landscape.
Competitive Landscape and Strategic Partnerships
The competitive landscape of solar photovoltaic (PV) panel manufacturing in 2025 is characterized by intense rivalry among established global players, rapid technological innovation, and a growing emphasis on strategic partnerships to secure supply chains and accelerate market expansion. The industry is led by a handful of dominant manufacturers, primarily headquartered in China, with significant contributions from companies in the United States, Europe, and emerging markets.
Chinese manufacturers continue to hold a commanding share of global PV module production. JinkoSolar Holding Co., Ltd., Trina Solar Co., Ltd., and Canadian Solar Inc. (despite its name, headquartered in China) are among the top producers, each with multi-gigawatt annual manufacturing capacities and vertically integrated operations. These companies have invested heavily in next-generation cell technologies, such as TOPCon and heterojunction, to maintain cost leadership and improve module efficiency. JA Solar Technology Co., Ltd. and LONGi Green Energy Technology Co., Ltd. are also major players, with LONGi particularly recognized for its leadership in monocrystalline silicon wafer production.
Outside China, First Solar, Inc. remains a key competitor, specializing in thin-film cadmium telluride (CdTe) technology and expanding its manufacturing footprint in the United States, India, and Europe. First Solar’s strategic investments in new gigawatt-scale factories are designed to meet surging demand and address supply chain resilience, especially in light of policy incentives such as the U.S. Inflation Reduction Act. European manufacturers, including Meyer Burger Technology AG, are focusing on high-efficiency heterojunction and perovskite tandem technologies, leveraging regional support for domestic manufacturing.
Strategic partnerships and joint ventures are increasingly central to the industry’s evolution. Manufacturers are collaborating with polysilicon suppliers, equipment makers, and downstream project developers to secure raw materials, accelerate technology transfer, and ensure market access. For example, Trina Solar and LONGi have entered into long-term supply agreements with polysilicon producers to mitigate price volatility and supply risks. Additionally, cross-border alliances are emerging, with Asian manufacturers partnering with local firms in the U.S., India, and Europe to establish localized production and comply with trade regulations.
Looking ahead, the competitive landscape is expected to remain dynamic, with further consolidation likely as companies seek scale and technological differentiation. Strategic partnerships—spanning R&D, supply chain integration, and market development—will be critical for manufacturers aiming to capture growth in both mature and emerging solar markets.
Future Outlook: Market Opportunities, Challenges, and Disruptive Technologies
The solar photovoltaic (PV) panel manufacturing sector is poised for significant transformation in 2025 and the years immediately following, driven by a convergence of market opportunities, emerging challenges, and disruptive technologies. Global demand for solar PV continues to surge, with annual installations expected to surpass 400 GW in 2025, propelled by ambitious decarbonization targets and supportive policy frameworks in major economies. Leading manufacturers such as JinkoSolar, Trina Solar, and Canadian Solar are expanding production capacities and investing in next-generation cell technologies to maintain competitiveness.
A key market opportunity lies in the rapid adoption of high-efficiency cell architectures, notably TOPCon (Tunnel Oxide Passivated Contact) and HJT (Heterojunction Technology), which are expected to become mainstream by 2025. These technologies offer higher conversion efficiencies and improved temperature coefficients compared to traditional PERC (Passivated Emitter and Rear Cell) modules. Companies like LONGi Green Energy and JA Solar are scaling up TOPCon and HJT production lines, aiming to deliver modules with efficiencies exceeding 24%. The commercialization of tandem perovskite-silicon cells, while still in early stages, is also being actively pursued by industry leaders and could disrupt the market by 2027 with potential efficiencies above 28%.
However, the sector faces notable challenges. Supply chain volatility, particularly for polysilicon and critical minerals, remains a concern, with price fluctuations impacting manufacturing costs. Trade tensions and evolving regulatory requirements in the US, EU, and India are prompting manufacturers to diversify supply chains and localize production. For instance, First Solar is expanding its manufacturing footprint in the United States to mitigate geopolitical risks and comply with domestic content incentives.
Disruptive technologies are reshaping the competitive landscape. Automation and digitalization of manufacturing processes are being accelerated to enhance yield, reduce labor costs, and improve quality control. The integration of AI-driven quality inspection and advanced robotics is becoming standard among tier-1 manufacturers. Additionally, sustainability is emerging as a differentiator, with companies like REC Group and Hanwha Q CELLS investing in low-carbon manufacturing and circularity initiatives to address environmental concerns and meet evolving customer expectations.
Looking ahead, the solar PV manufacturing industry is expected to remain highly dynamic, with continued innovation in cell and module technologies, supply chain realignment, and a growing emphasis on sustainability. These trends will shape the sector’s trajectory through 2025 and beyond, positioning it as a cornerstone of the global energy transition.
Sources & References
- JinkoSolar
- Trina Solar
- First Solar
- Meyer Burger
- LONGi Green Energy Technology
- Q CELLS
- Talesun Solar
- JA Solar
- Tongwei Group
- Xinyi Glass Holdings
- Flat Glass Group
- SolarPower Europe
- REC Group