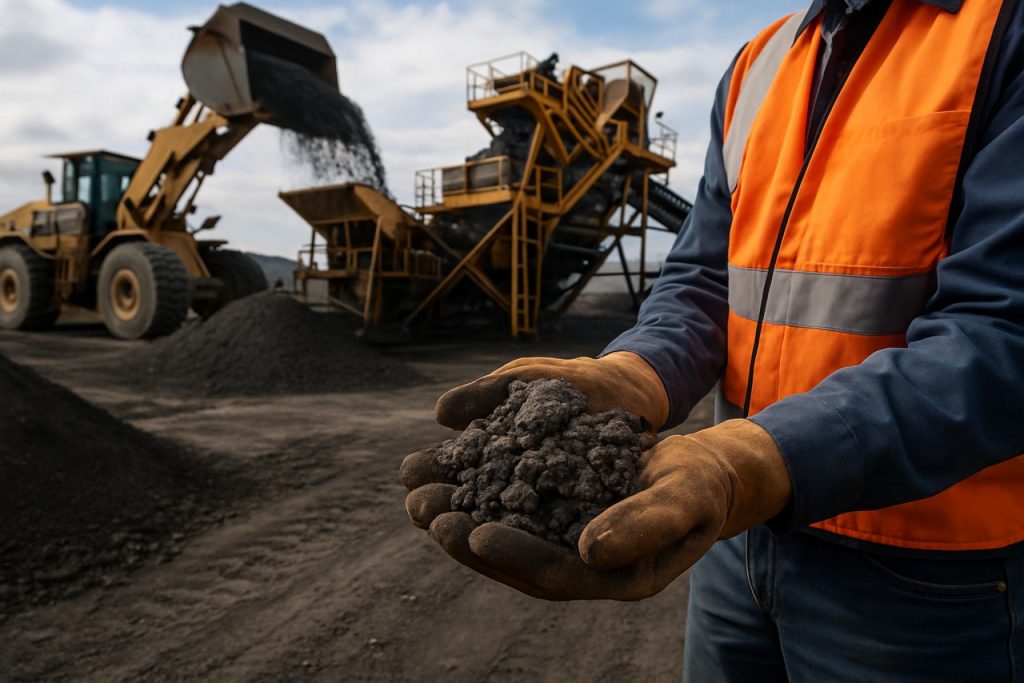
Rare Earth Mineral Processing in 2025: Navigating Disruption, Innovation, and Global Demand. How New Technologies and Geopolitics Are Shaping the Future of Critical Materials.
- Executive Summary: Key Trends and Market Outlook (2025–2029)
- Global Market Size, Growth Forecasts, and CAGR Analysis
- Technological Innovations in Rare Earth Mineral Processing
- Supply Chain Dynamics: From Mining to Refining
- Geopolitical Influences and Regulatory Landscape
- Major Players and Strategic Initiatives (e.g., lynascorp.com, mpmaterials.com, rareearth.org)
- Sustainability, Environmental Impact, and Circular Economy Approaches
- Emerging Applications: EVs, Wind Turbines, and Advanced Electronics
- Investment, M&A Activity, and New Project Pipelines
- Future Outlook: Opportunities, Risks, and Strategic Recommendations
- Sources & References
Executive Summary: Key Trends and Market Outlook (2025–2029)
The rare earth mineral processing sector is entering a pivotal phase between 2025 and 2029, shaped by intensifying global demand, evolving supply chains, and strategic policy interventions. Rare earth elements (REEs) are indispensable for advanced technologies, including electric vehicles, wind turbines, and defense systems. As the energy transition accelerates, the need for secure and sustainable rare earth supply chains is driving significant investments and technological innovation in mineral processing.
China remains the dominant force in rare earth processing, accounting for over 80% of global refined output. Leading Chinese companies such as Aluminum Corporation of China (Chinalco) and China Molybdenum Co., Ltd. (CMOC) continue to expand their processing capabilities, leveraging integrated supply chains and government support. However, geopolitical tensions and export controls are prompting major economies to diversify their supply sources and invest in domestic processing infrastructure.
In response, the United States, European Union, Australia, and Japan are accelerating rare earth processing projects. Lynas Rare Earths, headquartered in Australia, is the largest non-Chinese processor and is expanding its facilities in both Australia and Malaysia. The company is also developing a new processing plant in Texas, USA, in partnership with the U.S. Department of Defense, aiming to bolster domestic supply resilience. Similarly, MP Materials operates the Mountain Pass facility in California, the only integrated rare earth mining and processing site in North America, and is investing in advanced separation and magnet manufacturing capabilities.
The European Union is supporting projects such as Nordic Mining and Rare Earths Norway, which are focused on developing sustainable processing technologies and reducing environmental impacts. Japan’s Sojitz Corporation and Japan Oil, Gas and Metals National Corporation (JOGMEC) are also investing in rare earth processing partnerships and recycling initiatives.
Key trends for 2025–2029 include the adoption of cleaner, more efficient processing technologies, increased recycling of end-of-life products, and the establishment of regional processing hubs outside China. Governments are expected to provide further incentives and regulatory support to accelerate project development. Despite these efforts, supply chain bottlenecks and permitting challenges may persist, potentially constraining the pace of new capacity additions.
Overall, the outlook for rare earth mineral processing is characterized by robust investment, technological advancement, and a gradual rebalancing of global supply chains. The sector’s evolution will be critical to supporting the growth of clean energy and high-tech industries in the coming years.
Global Market Size, Growth Forecasts, and CAGR Analysis
The global rare earth mineral processing market is poised for significant growth in 2025 and the following years, driven by escalating demand for advanced electronics, renewable energy technologies, and electric vehicles (EVs). Rare earth elements (REEs) such as neodymium, praseodymium, dysprosium, and terbium are critical for manufacturing permanent magnets, batteries, and other high-tech components. The market’s expansion is underpinned by both supply chain diversification efforts and increased investment in processing capacity outside of China, which has historically dominated the sector.
As of 2024, China accounted for over 60% of global rare earth mineral production and an even higher share of processing capacity, with leading companies such as Aluminum Corporation of China (Chinalco) and China Molybdenum Co., Ltd. playing pivotal roles. However, geopolitical tensions and supply chain vulnerabilities have prompted major economies to accelerate domestic processing projects. For instance, Lynas Rare Earths, the largest non-Chinese rare earths producer, is expanding its processing facilities in Australia and Malaysia, with new capacity expected to come online in 2025. Similarly, MP Materials is ramping up its Mountain Pass facility in the United States, aiming to restore a fully integrated rare earth supply chain in North America.
Market size estimates for 2025 vary, but industry sources and company projections suggest the global rare earth mineral processing market will surpass USD 8 billion, with a compound annual growth rate (CAGR) of 8–10% through 2028. This growth is fueled by surging demand for neodymium-iron-boron (NdFeB) magnets used in EV motors and wind turbines, as well as government-backed initiatives to secure critical mineral supply chains. The European Union, United States, Japan, and Australia have all announced funding and policy support for new processing plants and recycling initiatives, aiming to reduce reliance on Chinese supply.
Looking ahead, the market outlook remains robust. New entrants and established players are investing in advanced separation technologies and environmentally sustainable processing methods. Companies such as The Chemours Company and Iluka Resources are exploring innovative extraction and refining techniques to improve efficiency and reduce environmental impact. As these projects come online, the global rare earth mineral processing market is expected to become more geographically diversified and resilient, supporting the rapid growth of clean energy and high-tech industries worldwide.
Technological Innovations in Rare Earth Mineral Processing
The rare earth mineral processing sector is undergoing significant technological transformation in 2025, driven by the urgent need for supply chain diversification, environmental sustainability, and efficiency improvements. As global demand for rare earth elements (REEs) continues to surge—particularly for use in electric vehicles, wind turbines, and advanced electronics—producers and technology developers are accelerating the adoption of innovative processing methods.
One of the most notable advancements is the shift toward solvent extraction alternatives. Traditional solvent extraction, while effective, is energy-intensive and generates substantial waste. In response, companies such as Lynas Rare Earths—the largest non-Chinese rare earths producer—are investing in new separation technologies that reduce chemical usage and improve recovery rates. Lynas is also expanding its processing capacity outside China, with new facilities in Australia and Malaysia, aiming to enhance supply chain resilience.
Another key innovation is the development of hydrometallurgical and ion-exchange processes. MP Materials, which operates the Mountain Pass mine in the United States, is implementing advanced hydrometallurgical techniques to optimize the extraction and purification of neodymium and praseodymium, critical for permanent magnets. These methods are designed to minimize environmental impact and lower operational costs, positioning MP Materials as a leader in sustainable rare earth processing.
Emerging technologies are also targeting the recycling of rare earths from end-of-life products. Umicore, a global materials technology company, is scaling up its rare earth recycling capabilities, focusing on recovering REEs from spent magnets and batteries. This approach not only addresses resource scarcity but also aligns with circular economy principles, which are increasingly prioritized by manufacturers and policymakers.
Looking ahead, the next few years are expected to see further integration of artificial intelligence and automation in rare earth processing plants. These digital tools enable real-time monitoring and optimization of complex chemical processes, improving yield and reducing downtime. Additionally, collaborative research initiatives—often involving industry leaders and government agencies—are accelerating the commercialization of novel extraction methods, such as bioleaching and membrane-based separations.
Overall, the rare earth mineral processing industry in 2025 is characterized by rapid technological evolution, with major players like Lynas Rare Earths, MP Materials, and Umicore at the forefront. Their ongoing investments in innovation are expected to shape the sector’s outlook, making rare earth supply chains more sustainable, efficient, and resilient in the years ahead.
Supply Chain Dynamics: From Mining to Refining
The rare earth mineral processing sector is undergoing significant transformation in 2025, driven by geopolitical shifts, technological advancements, and the urgent need for diversified supply chains. Rare earth elements (REEs) are critical for high-tech industries, including electric vehicles, wind turbines, and defense systems. The supply chain, spanning from mining to refining, remains highly concentrated, with China historically dominating both extraction and processing capacities.
As of 2025, China Molybdenum Co., Ltd. and Aluminum Corporation of China Limited (CHINALCO) continue to be major players in the mining and initial processing of rare earths, controlling a significant share of global output. China’s dominance extends to the refining stage, where it accounts for over 80% of global rare earth separation and oxide production. This concentration has prompted other nations and companies to accelerate efforts to localize and secure their own supply chains.
In the United States, MP Materials operates the Mountain Pass mine, the only active rare earth mining and processing site in North America. In 2025, MP Materials is expanding its refining capabilities to produce separated rare earth oxides domestically, aiming to reduce reliance on Chinese processors. The company is also collaborating with downstream manufacturers to establish a vertically integrated supply chain for magnets and other high-value products.
Australia is another key player, with Lynas Rare Earths operating the Mount Weld mine and the advanced processing facility in Malaysia. Lynas is constructing a new processing plant in Western Australia, expected to be operational in the next few years, to further localize refining and reduce exposure to geopolitical risks. The company’s strategy includes partnerships with governments and end-users to ensure stable supply.
Emerging projects in Canada, such as those led by Noront Resources and other domestic firms, are in various stages of development, with a focus on environmentally responsible extraction and processing. These initiatives are supported by government incentives and strategic alliances with technology and automotive companies.
Looking ahead, the rare earth mineral processing landscape is expected to become more geographically diversified by the late 2020s. However, challenges remain, including the high capital costs of new processing facilities, environmental regulations, and the technical complexity of separating individual rare earth elements. Industry stakeholders are investing in research and development to improve processing efficiency and sustainability, with the goal of building resilient, transparent, and secure supply chains for the future.
Geopolitical Influences and Regulatory Landscape
The rare earth mineral processing sector in 2025 is profoundly shaped by geopolitical dynamics and evolving regulatory frameworks. As rare earth elements (REEs) are critical for advanced technologies—ranging from electric vehicles to defense systems—governments and industry stakeholders are intensifying efforts to secure supply chains and reduce strategic vulnerabilities.
China remains the dominant force in rare earth processing, accounting for over 80% of global refining capacity. The Chinese government, through state-owned enterprises such as Aluminum Corporation of China (Chinalco) and China Molybdenum Co., Ltd., continues to consolidate control over domestic production and export quotas. In 2024, China introduced stricter export licensing requirements for certain rare earth products, citing national security concerns. These measures are expected to persist into 2025, reinforcing China’s leverage in global supply chains.
In response, the United States, European Union, Australia, and Japan are accelerating policy initiatives to diversify supply and processing capabilities. The U.S. Department of Defense has expanded funding for domestic processing projects, supporting companies like MP Materials, which operates the Mountain Pass facility in California—the only large-scale rare earth processing site in North America. The U.S. government is also collaborating with allies to establish secure supply chains, as evidenced by joint ventures and memoranda of understanding with Australian producers such as Lynas Rare Earths, which is constructing a processing plant in Texas.
Australia, leveraging its significant rare earth reserves, is positioning itself as a key non-Chinese supplier. Lynas Rare Earths remains the largest rare earths producer outside China, with ongoing expansion of its processing operations in Western Australia and Malaysia. The Australian government has introduced new critical minerals strategies, including streamlined permitting and financial incentives, to attract investment and accelerate project timelines.
The European Union, recognizing its dependence on imported rare earths, has enacted the Critical Raw Materials Act, which sets ambitious targets for domestic processing and recycling by 2030. The EU is supporting pilot projects and public-private partnerships to develop refining capacity within member states, with companies such as Eramet and Nornickel exploring rare earth processing initiatives.
Looking ahead, the regulatory landscape is expected to tighten, with increased scrutiny on environmental standards and supply chain transparency. Governments are likely to introduce further incentives for domestic processing, while also imposing stricter controls on exports and foreign investment in strategic assets. These trends will shape the competitive dynamics of rare earth mineral processing through the remainder of the decade.
Major Players and Strategic Initiatives (e.g., lynascorp.com, mpmaterials.com, rareearth.org)
The rare earth mineral processing sector in 2025 is characterized by intensified activity among a handful of major players, each pursuing strategic initiatives to secure supply chains, expand processing capacity, and reduce reliance on dominant producers. The global market remains highly concentrated, with China historically controlling the majority of both mining and processing capacity. However, recent years have seen significant investments and policy shifts aimed at diversifying the supply base and increasing processing capabilities outside China.
One of the most prominent non-Chinese companies is Lynas Rare Earths, headquartered in Australia. Lynas operates the Mount Weld mine, one of the world’s richest rare earth deposits, and processes concentrates at its advanced facility in Malaysia. In 2025, Lynas is advancing its U.S. expansion through a partnership with the U.S. Department of Defense to build a heavy rare earths separation facility in Texas, aiming to bolster North American supply chain resilience. The company is also investing in upstream and downstream integration to capture more value and ensure traceability throughout its supply chain.
In the United States, MP Materials is a key player, operating the Mountain Pass mine in California—the only large-scale rare earth mining and processing site in North America. MP Materials has made significant progress in restoring domestic processing capabilities, with its Stage II project targeting full separation and refining of rare earth oxides on-site by 2025. The company is also collaborating with major U.S. manufacturers to supply rare earth magnets, a critical component for electric vehicles and wind turbines, and is expanding into magnet production to further localize the supply chain.
On the industry association front, the Rare Earth Industry Association (REIA) plays a pivotal role in fostering collaboration, standardization, and responsible sourcing practices among global stakeholders. REIA’s initiatives in 2025 focus on promoting transparent supply chains, supporting research into environmentally sustainable processing technologies, and advocating for policy frameworks that encourage investment in new processing capacity outside China.
Other notable players include Iluka Resources, which is developing integrated rare earth processing at its Eneabba project in Australia, and Nornickel in Russia, which is exploring rare earth by-product recovery from its existing mining operations. These efforts are complemented by government-backed initiatives in the European Union and Japan to establish regional processing hubs and strategic stockpiles.
Looking ahead, the next few years are expected to see continued investment in rare earth processing infrastructure, with a focus on technological innovation, environmental stewardship, and supply chain security. The competitive landscape will likely evolve as new entrants emerge and established players deepen their integration across the value chain, reshaping the global rare earth mineral processing sector.
Sustainability, Environmental Impact, and Circular Economy Approaches
Rare earth mineral processing is under increasing scrutiny in 2025 due to its significant environmental footprint and the urgent need for sustainable practices. The extraction and separation of rare earth elements (REEs) typically involve energy-intensive processes and the use of hazardous chemicals, leading to concerns over waste management, water contamination, and greenhouse gas emissions. As global demand for REEs continues to rise—driven by their critical role in electric vehicles, wind turbines, and electronics—industry stakeholders are accelerating efforts to minimize environmental impact and embrace circular economy principles.
China remains the dominant player in rare earth processing, accounting for over 80% of global capacity. Major Chinese producers such as Aluminum Corporation of China (Chinalco) and China Molybdenum Co., Ltd. (CMOC) have announced investments in cleaner technologies, including closed-loop water systems and improved tailings management, to address regulatory and international pressure for greener supply chains. In 2024 and 2025, these companies have also begun pilot projects to recover REEs from industrial waste and end-of-life products, signaling a shift toward resource efficiency.
Outside China, companies in Australia and North America are advancing sustainability initiatives. Lynas Rare Earths, the largest non-Chinese REE producer, is expanding its processing operations in Australia and Malaysia with a focus on reducing radioactive waste and increasing recycling rates. The company is collaborating with local authorities to develop permanent disposal facilities and is investing in research to extract REEs from mine tailings and electronic scrap. In the United States, MP Materials is scaling up its Mountain Pass facility with a commitment to renewable energy use and closed-loop chemical recycling, aiming to set new benchmarks for environmental performance in the sector.
Industry organizations such as the Rare Earth Industry Association are promoting best practices and supporting the development of international standards for responsible sourcing and processing. In 2025, there is growing momentum for traceability systems and third-party certification schemes to ensure that rare earths are produced with minimal environmental harm.
Looking ahead, the next few years are expected to see increased investment in recycling technologies and urban mining, as well as the adoption of cleaner separation methods such as solvent extraction alternatives and bioleaching. These innovations, combined with stricter regulations and consumer demand for sustainable products, are likely to drive the rare earth sector toward a more circular and environmentally responsible future.
Emerging Applications: EVs, Wind Turbines, and Advanced Electronics
The processing of rare earth minerals is increasingly pivotal in supporting the rapid expansion of emerging applications such as electric vehicles (EVs), wind turbines, and advanced electronics. As of 2025, global demand for rare earth elements (REEs)—notably neodymium, praseodymium, dysprosium, and terbium—continues to surge, driven by their essential role in high-performance permanent magnets used in EV motors and wind turbine generators. The International Energy Agency projects that demand for these critical minerals could increase three- to seven-fold by 2040, with a significant portion of this growth materializing in the next few years.
China remains the dominant force in rare earth mineral processing, accounting for over 80% of global refined output. Major Chinese companies such as Aluminum Corporation of China (Chinalco) and China Molybdenum Co., Ltd. are central to the supply chain, operating large-scale separation and refining facilities. However, geopolitical concerns and supply chain vulnerabilities have prompted accelerated efforts in the United States, Europe, and Australia to develop independent processing capabilities.
In the United States, MP Materials operates the Mountain Pass facility, the only active rare earth mining and processing site in North America. The company is expanding its processing capacity to produce separated rare earth oxides domestically, with a particular focus on supplying the EV and wind energy sectors. Similarly, Lynas Rare Earths, headquartered in Australia, is ramping up its processing operations both in Australia and Malaysia, and is constructing a new facility in Texas in partnership with the U.S. Department of Defense to bolster domestic supply chains.
The European Union is also investing in rare earth processing infrastructure, with companies like Nordic Mining and Rare Earths Norway exploring new projects to support the continent’s green transition. These initiatives are designed to reduce reliance on imports and ensure a stable supply of critical materials for European manufacturers of EVs, wind turbines, and advanced electronics.
Looking ahead, the rare earth mineral processing sector is expected to see significant technological advancements aimed at improving efficiency and environmental sustainability. Companies are investing in new solvent extraction techniques, recycling of end-of-life magnets, and alternative processing methods to reduce waste and emissions. As demand for clean energy technologies accelerates, the ability to process rare earth minerals at scale and with minimal environmental impact will be a key differentiator for industry leaders.
Investment, M&A Activity, and New Project Pipelines
The rare earth mineral processing sector is experiencing a surge in investment, mergers and acquisitions (M&A), and the announcement of new project pipelines as global demand for critical minerals intensifies in 2025. This momentum is driven by the strategic importance of rare earth elements (REEs) in clean energy, electric vehicles, and advanced electronics, as well as efforts by governments and industry to diversify supply chains away from traditional dominant players.
In 2025, Lynas Rare Earths, the largest non-Chinese rare earths producer, continues to expand its processing capacity. The company is advancing its Kalgoorlie processing facility in Western Australia, which is expected to be fully operational this year, and is also progressing with its rare earths separation plant in Texas, USA, in partnership with the U.S. Department of Defense. These projects are part of a broader trend of Western investment in domestic processing capabilities to reduce reliance on Chinese supply chains.
Meanwhile, MP Materials, operator of the Mountain Pass mine in California, is investing heavily in downstream processing infrastructure. In 2025, the company is ramping up its Stage II and Stage III projects, which will enable the full separation and refining of rare earth oxides, including neodymium-praseodymium (NdPr), within the United States. MP Materials has also entered into strategic partnerships with major automakers to supply rare earth magnets for electric vehicle motors, further solidifying its role in the North American supply chain.
In Europe, Nordic Mining and other regional players are advancing feasibility studies and pilot projects for rare earth processing, supported by European Union initiatives aimed at securing critical raw materials. The EU’s Critical Raw Materials Act, implemented in 2024, is catalyzing new investments and joint ventures across the continent, with several projects expected to reach final investment decisions by 2026.
China remains the world’s largest processor of rare earths, with state-owned enterprises such as Chinalco and China Molybdenum Co., Ltd. continuing to consolidate domestic resources and invest in advanced processing technologies. However, recent export controls and geopolitical tensions are prompting international companies to accelerate alternative supply chain development.
Looking ahead, the rare earth processing sector is expected to see continued M&A activity as established players seek to secure feedstock and expand processing capabilities. New entrants, particularly in North America, Australia, and Europe, are likely to benefit from government incentives and strategic partnerships. The next few years will be critical in determining the global balance of rare earth processing capacity, with significant implications for technology and energy transition industries worldwide.
Future Outlook: Opportunities, Risks, and Strategic Recommendations
The future of rare earth mineral processing is poised at a critical juncture in 2025, shaped by intensifying global demand, evolving supply chain strategies, and mounting environmental scrutiny. Rare earth elements (REEs) are indispensable for advanced technologies, including electric vehicles, wind turbines, and defense systems. As the world accelerates its energy transition, the need for secure, sustainable, and diversified rare earth supply chains is more urgent than ever.
China remains the dominant force in rare earth processing, accounting for over 85% of global refined output. However, geopolitical tensions and export controls have prompted major economies to invest in alternative processing capabilities. The United States, through initiatives such as the Department of Defense-backed projects, is supporting domestic processing at facilities like MP Materials’ Mountain Pass, the only integrated rare earth mining and processing site in North America. MP Materials is expanding its separation and refining capacity, aiming to supply both domestic and international markets with critical REEs.
Australia is also emerging as a key player, with Lynas Rare Earths operating the world’s largest non-Chinese rare earth processing plant in Malaysia and developing a new facility in Western Australia. Lynas is scaling up production of neodymium-praseodymium (NdPr), vital for permanent magnets, and is collaborating with governments to establish processing in the United States. Meanwhile, Iluka Resources is constructing a rare earth refinery at Eneabba, supported by the Australian government, to further diversify global supply.
Europe is accelerating its rare earth strategy, with companies like Nordic Mining and Neo Performance Materials investing in processing and recycling projects. The European Union’s Critical Raw Materials Act, effective from 2025, sets ambitious targets for domestic processing and recycling, aiming to reduce reliance on imports and enhance supply chain resilience.
Despite these opportunities, significant risks persist. Environmental concerns over radioactive waste and water usage in processing remain a challenge, prompting stricter regulations and community opposition. The high capital and technical barriers to entry, coupled with volatile REE prices, may deter new entrants and slow project timelines. Furthermore, China’s continued dominance in downstream magnet manufacturing could limit the impact of upstream diversification unless matched by investments in value-added processing.
Strategic recommendations for stakeholders include: accelerating investment in environmentally responsible processing technologies; fostering international partnerships to share expertise and mitigate supply risks; and supporting end-to-end supply chain development, from mining to magnet manufacturing. Governments and industry must also prioritize research into recycling and alternative materials to ensure long-term sustainability and security in the rare earth sector.
Sources & References
- Aluminum Corporation of China (Chinalco)
- China Molybdenum Co., Ltd. (CMOC)
- Lynas Rare Earths
- MP Materials
- Nordic Mining
- Japan Oil, Gas and Metals National Corporation (JOGMEC)
- Umicore
- Lynas Rare Earths
- Eramet
- Nornickel
- MP Materials
- Lynas Rare Earths
- Nordic Mining
- Neo Performance Materials