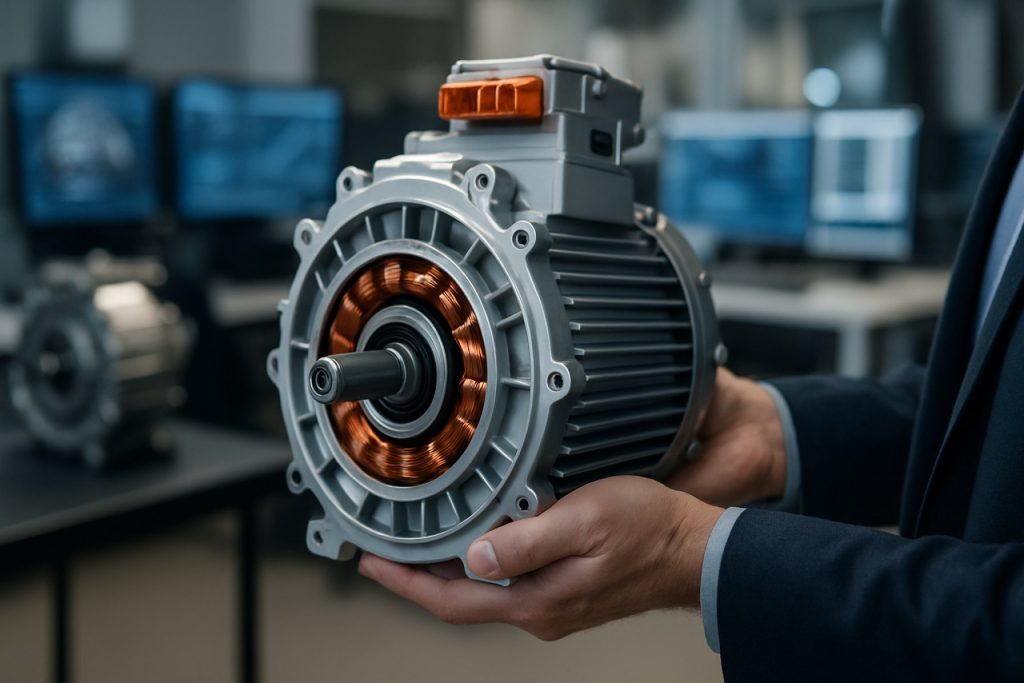
Electric Motor Innovation in 2025: How Breakthrough Technologies and Market Forces Are Accelerating a New Era of Efficiency. Discover What’s Powering the Industry’s Projected 8% Annual Growth Through 2030.
- Executive Summary: Key Trends and Market Drivers in 2025
- Global Market Forecast: 2025–2030 Growth Projections and Regional Hotspots
- Technological Breakthroughs: High-Efficiency Motors, Materials, and Digitalization
- Electrification of Transportation: Impact on Motor Design and Demand
- Industrial Automation and Robotics: Shaping the Next Generation of Motors
- Sustainability and Regulatory Pressures: Energy Standards and Eco-Design
- Competitive Landscape: Leading Innovators and Strategic Partnerships
- Supply Chain and Raw Materials: Risks, Opportunities, and Localization
- Emerging Applications: From Smart Grids to Medical Devices
- Future Outlook: Investment Priorities and Innovation Roadmap to 2030
- Sources & References
Executive Summary: Key Trends and Market Drivers in 2025
Electric motor innovation is poised to accelerate in 2025, driven by rapid advancements in materials, design, and manufacturing processes. The global push for electrification—particularly in automotive, industrial automation, and renewable energy sectors—is intensifying demand for high-efficiency, compact, and cost-effective electric motors. Key trends shaping the market include the adoption of rare-earth-free motor technologies, integration of digital control systems, and the scaling of production for next-generation electric vehicles (EVs).
Major automotive manufacturers are at the forefront of electric motor innovation. Tesla, Inc. continues to refine its permanent magnet synchronous reluctance motors, focusing on reducing rare earth material dependency and improving power density. Similarly, BMW Group is advancing its fifth-generation eDrive technology, which eliminates the need for rare earths entirely, supporting both sustainability and supply chain resilience. These developments are expected to influence broader industry standards and supply chains in 2025 and beyond.
In the industrial sector, companies like Siemens AG and ABB Ltd. are leveraging digitalization and smart manufacturing to enhance motor efficiency and predictive maintenance. The integration of Internet of Things (IoT) sensors and AI-driven analytics into electric motors is enabling real-time performance monitoring, reducing downtime, and optimizing energy consumption. This digital transformation is anticipated to be a key market driver, as industries seek to meet stricter energy efficiency regulations and lower operational costs.
Material innovation is another critical area. The development of advanced soft magnetic composites and high-performance ferrite magnets is enabling the production of lighter, more efficient motors. Nidec Corporation, a global leader in motor manufacturing, is investing heavily in research to commercialize these materials at scale, aiming to support the surging demand from the EV and home appliance markets.
Looking ahead, the outlook for electric motor innovation remains robust. The convergence of electrification trends, regulatory pressures for energy efficiency, and breakthroughs in digital and material technologies will continue to drive market growth. As manufacturers ramp up investments in R&D and scale up production capabilities, the next few years are expected to see a proliferation of high-performance, sustainable electric motor solutions across multiple industries.
Global Market Forecast: 2025–2030 Growth Projections and Regional Hotspots
The global electric motor market is poised for robust growth between 2025 and 2030, driven by accelerating electrification across industries, surging electric vehicle (EV) adoption, and ongoing innovation in motor efficiency and materials. Major manufacturers are scaling up production and investing in next-generation technologies to meet rising demand, particularly in automotive, industrial automation, and renewable energy sectors.
Asia-Pacific remains the dominant regional hotspot, led by China, Japan, and South Korea. China’s aggressive push for EVs and industrial modernization is fueling rapid expansion, with domestic giants such as Wolong Electric Group and Nidec Corporation investing heavily in high-efficiency and rare-earth-free motor designs. Nidec Corporation, a global leader in small precision motors and automotive drive systems, has announced plans to further expand its production capacity and R&D footprint in the region through 2030, targeting both EV and industrial applications.
Europe is emerging as a key innovation hub, propelled by stringent energy efficiency regulations and the continent’s ambitious decarbonization agenda. Companies like Siemens AG and Schneider Electric are advancing digitalized, smart motor systems for factories and infrastructure, while Robert Bosch GmbH and Continental AG are scaling up production of advanced traction motors for EVs. The European Union’s push for local battery and motor supply chains is expected to further stimulate regional investment and innovation.
In North America, the United States is witnessing renewed investment in electric motor manufacturing, spurred by federal incentives for clean energy and transportation. Regal Rexnord Corporation and ABB Ltd are expanding their portfolios with high-efficiency industrial motors and integrated drive solutions. The region is also seeing increased collaboration between automakers and motor specialists to localize EV powertrain production and reduce reliance on imported components.
Looking ahead, the global electric motor market is projected to grow at a compound annual growth rate (CAGR) in the high single digits through 2030, with total market value expected to surpass several hundred billion US dollars by the end of the decade. Key growth drivers include the proliferation of EVs, the rise of smart manufacturing, and the integration of advanced materials such as silicon carbide and ferrite alternatives. Regional hotspots will continue to shift as governments and industry leaders prioritize supply chain resilience, sustainability, and technological leadership in electric motor innovation.
Technological Breakthroughs: High-Efficiency Motors, Materials, and Digitalization
Electric motor innovation is accelerating rapidly in 2025, driven by the convergence of high-efficiency designs, advanced materials, and digitalization. These technological breakthroughs are reshaping the landscape for industries ranging from automotive to industrial automation and consumer appliances.
A major focus is on high-efficiency motors, particularly those meeting or exceeding the IE4 and IE5 efficiency classes. These ultra-premium efficiency motors are being adopted widely as regulatory standards tighten and energy costs rise. For example, ABB and Siemens have both expanded their portfolios of IE5 synchronous reluctance and permanent magnet motors, targeting applications in HVAC, pumps, and conveyors. These motors can deliver energy savings of up to 10% compared to previous generations, with payback periods often under two years in high-duty-cycle environments.
Material innovation is another key driver. The adoption of rare-earth-free magnet technologies and advanced soft magnetic composites is reducing reliance on critical raw materials while improving performance. Nidec Corporation, a global leader in motor manufacturing, has invested heavily in developing ferrite-based and amorphous core motors, which offer high efficiency without the supply chain risks associated with neodymium and dysprosium. Meanwhile, Tesla, Inc. continues to refine its use of silicon carbide inverters and copper rotor induction motors, pushing the boundaries of power density and thermal management in electric vehicle (EV) applications.
Digitalization is transforming both the design and operation of electric motors. Smart, connected motors equipped with embedded sensors and IoT capabilities are enabling predictive maintenance, real-time performance monitoring, and remote diagnostics. Schneider Electric and WEG are at the forefront, offering digital platforms that integrate motor data into broader energy management and automation systems. This not only reduces downtime but also optimizes energy consumption across entire facilities.
Looking ahead, the outlook for electric motor innovation remains robust. The push for electrification in transport, industry, and infrastructure is expected to drive further advances in efficiency, materials, and digital integration. Companies are investing in AI-driven design tools and additive manufacturing to accelerate prototyping and customization. As regulatory and market pressures intensify, the next few years will likely see even greater collaboration between motor manufacturers, material suppliers, and digital solution providers to deliver smarter, greener, and more resilient electric motor systems.
Electrification of Transportation: Impact on Motor Design and Demand
The electrification of transportation is driving a profound transformation in electric motor design and demand, with 2025 marking a pivotal year for innovation and scale. As automakers accelerate their shift toward electric vehicles (EVs), the requirements for electric motors are evolving rapidly, emphasizing higher efficiency, reduced weight, and lower reliance on critical materials such as rare earth elements.
Leading manufacturers are investing heavily in next-generation motor technologies. Tesla, Inc. continues to refine its permanent magnet synchronous reluctance motors, which offer improved efficiency and reduced cobalt and rare earth content. In 2025, Tesla’s focus remains on optimizing power density and manufacturability to support its expanding global EV lineup. Similarly, BMW Group is deploying its fifth-generation eDrive technology, which eliminates the need for rare earths entirely, addressing both cost and supply chain concerns.
The commercial vehicle sector is also seeing significant innovation. Daimler Truck AG is rolling out electric trucks and buses equipped with modular, scalable electric drive units, designed for durability and high torque. These advancements are crucial as regulatory pressures in Europe, North America, and Asia push for stricter emissions standards and zero-emission vehicle mandates by 2030.
Motor suppliers are responding with new architectures and materials. Nidec Corporation, a global leader in electric motor manufacturing, is expanding its production of e-axle systems, which integrate motor, inverter, and gearbox for compactness and efficiency. Nidec’s 2025 roadmap includes mass production of next-generation traction motors for both passenger and commercial EVs, targeting higher output and lower cost.
The demand for electric motors is set to surge. According to industry projections, global EV sales are expected to exceed 17 million units in 2025, up from around 10 million in 2023, directly increasing the need for advanced traction motors. This growth is prompting investments in new manufacturing facilities and supply chain localization, as seen in recent announcements from Robert Bosch GmbH and Siemens AG, both of which are scaling up their e-mobility divisions to meet rising OEM demand.
Looking ahead, the next few years will see further breakthroughs in motor efficiency, integration of power electronics, and adoption of alternative winding and cooling techniques. The electrification of transportation is not only reshaping the automotive landscape but also setting new benchmarks for electric motor innovation across industries.
Industrial Automation and Robotics: Shaping the Next Generation of Motors
Electric motor innovation is at the heart of the ongoing transformation in industrial automation and robotics, with 2025 marking a pivotal year for both technological advancement and market adoption. The demand for higher efficiency, precision, and adaptability in manufacturing environments is driving rapid evolution in motor design, control systems, and integration with digital platforms.
One of the most significant trends is the widespread adoption of high-efficiency permanent magnet synchronous motors (PMSMs) and brushless DC (BLDC) motors. These motors offer superior torque density, energy efficiency, and reliability compared to traditional induction motors, making them ideal for robotics and automated machinery. Leading manufacturers such as Siemens and ABB are investing heavily in next-generation motor platforms that incorporate advanced materials, such as rare-earth magnets and improved winding technologies, to further boost performance and reduce energy consumption.
Integration of smart sensors and connectivity is another key innovation area. Motors equipped with embedded sensors can monitor parameters like temperature, vibration, and load in real time, enabling predictive maintenance and minimizing unplanned downtime. Schneider Electric and Rockwell Automation are at the forefront of developing intelligent motor management systems that leverage Industrial Internet of Things (IIoT) platforms for seamless data exchange and remote diagnostics.
The push for sustainability is also shaping motor innovation. Regulatory frameworks, such as the European Union’s Ecodesign Directive, are setting stricter efficiency standards for industrial motors, prompting manufacturers to accelerate the development of IE4 and IE5 ultra-premium efficiency motors. Companies like Nidec Corporation are expanding their portfolios to include motors that not only meet but exceed these requirements, supporting global decarbonization goals.
Looking ahead, the convergence of artificial intelligence and motor control is expected to unlock new levels of autonomy and adaptability in robotics. AI-driven algorithms can optimize motor performance in real time, adjusting speed, torque, and energy use based on dynamic operational conditions. This is particularly relevant for collaborative robots (cobots) and flexible manufacturing systems, where agility and safety are paramount.
In summary, 2025 and the following years will see electric motor innovation driven by efficiency, intelligence, and sustainability imperatives. The combined efforts of industry leaders and regulatory bodies are setting the stage for smarter, greener, and more responsive motors that will define the next generation of industrial automation and robotics.
Sustainability and Regulatory Pressures: Energy Standards and Eco-Design
In 2025, the electric motor industry is experiencing significant transformation driven by tightening sustainability requirements and evolving regulatory frameworks. Governments and regulatory bodies worldwide are enforcing stricter energy efficiency standards, compelling manufacturers to innovate in both design and production processes. The European Union’s Ecodesign Directive, for example, has mandated that as of July 2023, all new electric motors placed on the market must meet the IE3 or higher efficiency class, with further tightening expected in the coming years. This regulatory push is accelerating the adoption of advanced materials, improved winding techniques, and integrated electronics to minimize energy losses and environmental impact.
Major industry players are responding proactively. Siemens AG has expanded its portfolio of high-efficiency motors, integrating digitalization and smart monitoring to optimize energy use throughout the motor’s lifecycle. Similarly, ABB Ltd is investing in synchronous reluctance and permanent magnet technologies, which offer higher efficiency and lower carbon footprints compared to traditional induction motors. These innovations are not only in response to regulatory mandates but also to growing customer demand for sustainable solutions in sectors such as manufacturing, HVAC, and transportation.
In North America, the U.S. Department of Energy’s updated energy conservation standards for electric motors, effective from 2025, are expected to save nearly 7 quadrillion BTUs of energy over 30 years, according to official projections. This is prompting manufacturers to accelerate the development of IE4 and IE5 “Super Premium” and “Ultra Premium” efficiency motors. Companies like Regal Rexnord Corporation are introducing new product lines that exceed current minimum efficiency requirements, leveraging advanced design software and eco-friendly manufacturing processes.
Sustainability is also influencing supply chain decisions. There is a marked shift toward recyclable materials and reduced use of rare earth elements, as seen in the efforts of Nidec Corporation, which is developing ferrite-based motors to decrease reliance on critical minerals. Additionally, digital twin technology and lifecycle analysis tools are being adopted to ensure compliance and optimize environmental performance from design to end-of-life.
Looking ahead, the convergence of regulatory pressure, corporate sustainability goals, and technological innovation is expected to drive rapid adoption of next-generation electric motors. The industry outlook for 2025 and beyond points to continued investment in eco-design, with a focus on circularity, resource efficiency, and digital integration, positioning electric motors as a cornerstone of global decarbonization efforts.
Competitive Landscape: Leading Innovators and Strategic Partnerships
The competitive landscape for electric motor innovation in 2025 is characterized by rapid technological advancements, strategic alliances, and a focus on sustainability and efficiency. Major industry players are investing heavily in research and development to address the growing demand for high-performance electric motors across automotive, industrial, and consumer applications.
Among the global leaders, Siemens AG continues to set benchmarks in electric motor technology, leveraging its expertise in digitalization and automation. Siemens has recently expanded its portfolio with high-efficiency, low-carbon motors designed for both industrial and mobility sectors, and is actively collaborating with automotive OEMs to integrate next-generation drive systems. Similarly, ABB Ltd. is pushing the boundaries with its IE5 ultra-premium efficiency motors, which are designed to reduce energy consumption and carbon emissions. ABB’s strategic partnerships with manufacturers in the automotive and process industries are accelerating the adoption of smart, connected motor solutions.
In the automotive sector, Tesla, Inc. remains at the forefront of electric motor innovation, with its proprietary permanent magnet synchronous reluctance motors powering the latest vehicle models. Tesla’s vertical integration strategy and in-house motor development have enabled rapid iteration and performance improvements, setting industry standards for efficiency and power density. Meanwhile, Nidec Corporation, a Japanese multinational, is aggressively expanding its global footprint, supplying advanced traction motors for electric vehicles (EVs) and investing in new production facilities in Europe and North America to meet surging demand.
Strategic partnerships are a defining feature of the current landscape. For example, Robert Bosch GmbH has entered into joint ventures with automakers and technology firms to co-develop next-generation e-axle systems, integrating electric motors, power electronics, and transmissions into compact units. Schneider Electric SE is collaborating with industrial automation partners to deliver smart motor management solutions, leveraging IoT and AI for predictive maintenance and energy optimization.
Looking ahead, the competitive environment is expected to intensify as new entrants and established players race to commercialize innovations such as axial flux motors, solid-state drives, and integrated power electronics. The focus on sustainability, regulatory compliance, and digital integration will continue to drive strategic alliances and investments, shaping the evolution of electric motor technology through 2025 and beyond.
Supply Chain and Raw Materials: Risks, Opportunities, and Localization
The supply chain for electric motor innovation in 2025 is characterized by both significant risks and emerging opportunities, particularly as the industry navigates raw material constraints and increasing localization efforts. Electric motors, especially those used in electric vehicles (EVs) and industrial automation, rely heavily on materials such as copper, rare earth elements (notably neodymium and dysprosium for permanent magnets), and advanced steel alloys. The global demand for these materials is projected to rise sharply, driven by the accelerating adoption of EVs and renewable energy systems.
One of the primary risks in the supply chain is the concentration of rare earth element production. As of 2025, China remains the dominant supplier, accounting for over 60% of global rare earth mining and an even larger share of processing capacity. This concentration exposes manufacturers to geopolitical risks and potential supply disruptions. Companies such as Tesla, Inc. and General Motors Company have responded by seeking alternative motor designs that reduce or eliminate rare earth dependence, such as induction motors or ferrite-based magnet technologies.
Copper, another critical input, faces its own set of challenges. Global copper demand is expected to outpace supply in the near term, with the International Energy Agency warning of potential shortages as electrification accelerates. Major motor manufacturers like Siemens AG and Nidec Corporation are investing in recycling initiatives and exploring alternative winding materials to mitigate these risks.
Opportunities are emerging through supply chain localization and vertical integration. In North America and Europe, governments and industry leaders are incentivizing domestic production of key materials and components. For example, Robert Bosch GmbH has expanded its electric motor manufacturing footprint in Europe, while BorgWarner Inc. is investing in U.S.-based facilities to reduce reliance on overseas suppliers. These moves aim to enhance supply chain resilience and reduce lead times.
Looking ahead, the outlook for electric motor supply chains involves a delicate balance between securing raw materials and advancing sustainable practices. Companies are increasingly forming strategic partnerships with mining firms and material processors, as well as investing in closed-loop recycling systems. The push for localization is expected to intensify, with new regional supply hubs emerging by 2027. As innovation continues, the industry’s ability to adapt its supply chain strategies will be crucial in supporting the next generation of electric motor technologies.
Emerging Applications: From Smart Grids to Medical Devices
Electric motor innovation is rapidly expanding the scope of applications across diverse sectors, with 2025 marking a pivotal year for integration into smart grids, medical devices, and beyond. The convergence of advanced materials, digital control, and connectivity is enabling electric motors to play a central role in the next generation of intelligent systems.
In the realm of smart grids, electric motors are increasingly embedded in distributed energy resources and demand response systems. High-efficiency motors, often equipped with variable speed drives and IoT connectivity, are being deployed in grid-interactive buildings and industrial facilities. These motors enable real-time load balancing and energy optimization, supporting the transition to renewable energy sources. Companies such as Siemens AG and Schneider Electric are at the forefront, integrating smart motor solutions into their energy management platforms to enhance grid flexibility and resilience.
In medical technology, miniaturized and precision-controlled electric motors are revolutionizing devices ranging from surgical robots to implantable pumps. The ongoing development of brushless DC and stepper motors with advanced feedback systems is enabling higher accuracy and reliability in minimally invasive procedures. maxon Group, a leader in high-precision drive systems, continues to innovate with motors designed for critical medical applications, including artificial hearts and drug delivery systems. Similarly, Portescap is advancing ultra-compact motors for portable medical devices, supporting trends toward home-based and wearable healthcare solutions.
Emerging applications also include robotics, where electric motor innovation is central to the development of collaborative robots (cobots) and autonomous mobile platforms. Enhanced torque density, energy efficiency, and integrated sensing are enabling safer and more adaptive robotic systems for manufacturing, logistics, and service industries. ABB Ltd and Yaskawa Electric Corporation are notable for their ongoing investments in smart motor technologies tailored for robotics and automation.
Looking ahead, the outlook for electric motor innovation in these emerging applications is robust. The proliferation of digital twins, AI-driven predictive maintenance, and further miniaturization are expected to accelerate adoption across sectors. As regulatory standards for efficiency and connectivity tighten, manufacturers are poised to deliver motors that are not only smarter and more efficient but also integral to the digital transformation of energy, healthcare, and automation systems.
Future Outlook: Investment Priorities and Innovation Roadmap to 2030
The electric motor sector is poised for significant transformation through 2025 and into the latter part of the decade, driven by surging demand in electric vehicles (EVs), industrial automation, and renewable energy integration. Investment priorities are increasingly focused on efficiency, sustainability, and digitalization, with leading manufacturers and technology developers outlining ambitious innovation roadmaps to 2030.
A central trend is the acceleration of research and deployment of next-generation motor technologies, such as axial flux motors, high-efficiency permanent magnet synchronous motors (PMSMs), and rare-earth-free alternatives. Companies like Nidec Corporation, a global leader in motor manufacturing, have announced substantial capital expenditure plans through 2025 to expand production capacity for EV traction motors and to develop advanced e-axle systems. Similarly, Siemens AG is investing in digital twin and simulation technologies to optimize motor design and predictive maintenance, aiming to reduce lifecycle costs and improve reliability across industrial and mobility applications.
Sustainability is a key investment driver, with manufacturers prioritizing the reduction of rare earth material dependency and the adoption of recyclable materials. Robert Bosch GmbH is actively developing magnet-free and reduced-rare-earth motor designs, targeting both automotive and industrial markets. The company’s roadmap includes scaling up production of these sustainable motors by 2027, aligning with broader industry goals for carbon neutrality.
Digitalization and smart manufacturing are also shaping the innovation landscape. ABB Ltd is integrating IoT sensors and cloud-based analytics into its motor platforms, enabling real-time performance monitoring and predictive diagnostics. This approach is expected to become standard across the industry by 2030, supporting both operational efficiency and new service-based business models.
Looking ahead, the sector anticipates robust growth, with global electric motor demand projected to rise sharply as electrification expands in transport, HVAC, and industrial automation. Strategic investments are being channeled into R&D for ultra-high-efficiency motors, advanced power electronics, and integrated drive systems. Collaborative initiatives between OEMs, material suppliers, and research institutions are expected to accelerate commercialization of breakthrough technologies, particularly in the context of tightening energy efficiency regulations and sustainability targets.
By 2030, the electric motor industry is expected to be characterized by widespread adoption of digitalized, sustainable, and high-performance motor solutions, underpinned by ongoing investment from major players such as Nidec Corporation, Siemens AG, Robert Bosch GmbH, and ABB Ltd.
Sources & References
- Siemens AG
- Wolong Electric Group
- Robert Bosch GmbH
- Daimler Truck AG
- Rockwell Automation
- BorgWarner Inc.
- maxon Group
- Yaskawa Electric Corporation