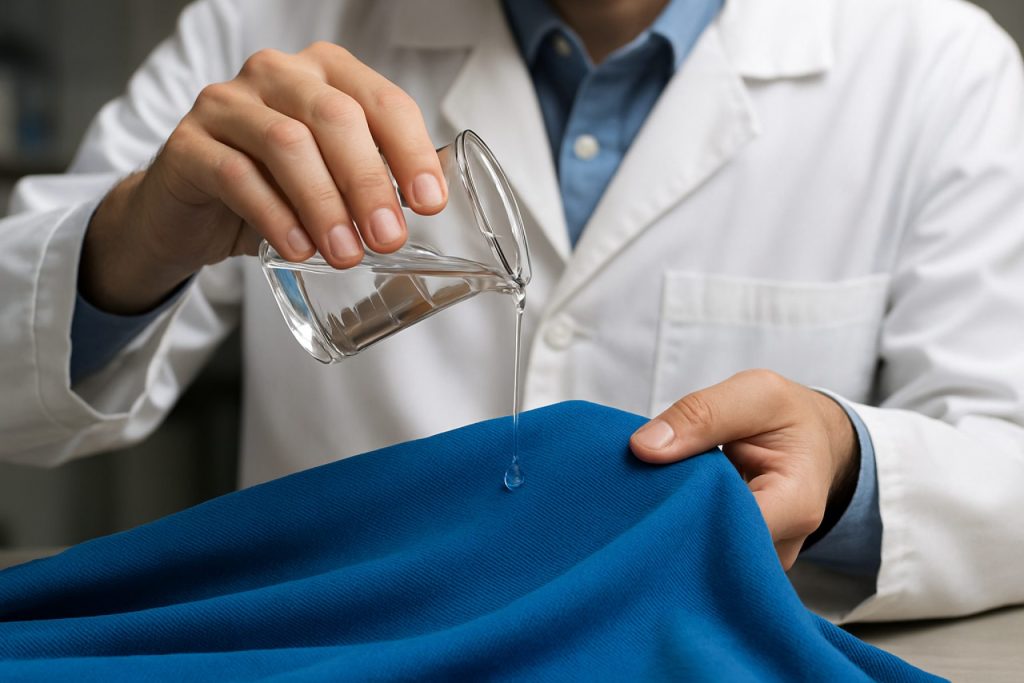
Unlocking the Science and Innovation Behind Textile Auxiliaries: How Modern Additives Are Transforming the Fabric Industry for Enhanced Quality and Sustainability
- Introduction to Textile Auxiliaries: Definitions and Historical Evolution
- Key Types of Textile Auxiliaries and Their Functions
- Role of Auxiliaries in Dyeing and Finishing Processes
- Innovations in Eco-Friendly and Sustainable Textile Auxiliaries
- Impact of Auxiliaries on Fabric Performance and Quality
- Regulatory Standards and Compliance in Textile Chemicals
- Market Trends and Leading Manufacturers of Textile Auxiliaries
- Challenges in Application and Compatibility with Modern Textiles
- Case Studies: Success Stories in Textile Auxiliary Implementation
- Future Outlook: Emerging Technologies and Opportunities in Textile Auxiliaries
- Sources & References
Introduction to Textile Auxiliaries: Definitions and Historical Evolution
Textile auxiliaries are a diverse group of chemical agents that play a crucial role in the processing and finishing of textiles. These substances are not intended to become part of the final textile product but are essential in facilitating various stages of textile manufacturing, such as pre-treatment, dyeing, printing, and finishing. Textile auxiliaries include surfactants, dispersing agents, wetting agents, softeners, leveling agents, and many others, each designed to impart specific properties or to enhance the efficiency of textile processing. Their primary function is to improve the quality, appearance, and performance of textile materials, ensuring that fabrics meet the desired standards for end-use applications.
The historical evolution of textile auxiliaries is closely linked to the development of the textile industry itself. In ancient times, textile processing relied on natural substances such as animal fats, plant extracts, and minerals to aid in cleaning, dyeing, and finishing fabrics. With the advent of the Industrial Revolution in the 18th and 19th centuries, the textile industry underwent significant mechanization and expansion, leading to increased demand for more efficient and specialized processing chemicals. The introduction of synthetic dyes in the mid-19th century further accelerated the need for new types of auxiliaries to ensure uniform dye uptake and colorfastness.
The 20th century marked a period of rapid innovation in textile chemistry, with the development of a wide range of synthetic auxiliaries tailored for specific fibers and processes. Advances in polymer science and surface chemistry enabled the creation of highly effective surfactants, dispersants, and finishing agents, transforming the capabilities of textile manufacturers. Today, the production and application of textile auxiliaries are governed by stringent quality and environmental standards, with leading organizations such as the International Organization for Standardization (ISO) and the Organisation for Economic Co-operation and Development (OECD) providing guidelines for safe and sustainable use.
Modern textile auxiliaries are designed not only for performance but also with a focus on environmental compatibility and human safety. The industry continues to innovate, developing biodegradable and non-toxic alternatives to traditional chemicals, in response to growing regulatory and consumer demands for sustainable textile production. As a result, textile auxiliaries remain a dynamic and essential component of the global textile value chain, supporting both technological advancement and environmental stewardship.
Key Types of Textile Auxiliaries and Their Functions
Textile auxiliaries are a diverse group of chemical agents essential to the textile manufacturing process. They are not part of the final textile product but play crucial roles in enhancing processing efficiency, imparting specific properties, and ensuring the quality of textiles. The main types of textile auxiliaries and their functions are outlined below:
- Pre-treatment Auxiliaries: These chemicals prepare raw fibers and fabrics for subsequent processing. They include wetting agents, detergents, sequestering agents, and anti-foaming agents. Wetting agents improve water penetration, detergents remove natural impurities, and sequestering agents bind metal ions that could interfere with dyeing or finishing. Pre-treatment is vital for achieving uniform dyeing and finishing results.
- Dyeing Auxiliaries: Used during the dyeing process, these auxiliaries ensure even dye uptake and color fastness. Dispersing agents help distribute dyes uniformly, leveling agents prevent uneven coloration, and fixing agents improve dye adherence to fibers. These chemicals are tailored to the specific dye and fiber type, optimizing color quality and process efficiency.
- Printing Auxiliaries: In textile printing, auxiliaries such as thickeners, binders, and emulsifiers are used to control the viscosity of print pastes, fix pigments, and stabilize emulsions. Thickeners ensure sharp print definition, while binders secure pigments to the fabric surface, enhancing wash and rub fastness.
- Finishing Auxiliaries: These are applied in the final stages to impart desired functional or aesthetic properties. Softeners improve fabric hand feel, anti-static agents reduce static buildup, and water-repellent agents provide hydrophobicity. Flame retardants, wrinkle-resist agents, and antimicrobial finishes are also common, adding value and performance to textiles.
- Specialty Auxiliaries: This category includes chemicals for specific technical or environmental needs, such as enzyme-based auxiliaries for bio-polishing, eco-friendly alternatives to conventional agents, and auxiliaries for technical textiles with unique performance requirements.
The development and application of textile auxiliaries are guided by both performance requirements and regulatory standards. Leading organizations such as the bluesign system and the OEKO-TEX Association set benchmarks for safety, environmental impact, and sustainability in textile chemical use. Major chemical manufacturers, including BASF and Archroma, are actively involved in innovating new auxiliaries that meet these evolving standards, supporting the textile industry’s shift toward safer and more sustainable production.
Role of Auxiliaries in Dyeing and Finishing Processes
Textile auxiliaries are a diverse group of chemical agents that play a crucial role in the dyeing and finishing processes of textile manufacturing. Their primary function is to facilitate and optimize the interaction between fibers, dyes, and finishing agents, ensuring that the desired color, texture, and performance characteristics are achieved efficiently and consistently. Without auxiliaries, many modern textile processes would be less effective, less sustainable, and more resource-intensive.
During the dyeing process, auxiliaries serve several essential purposes. Wetting agents, for example, reduce the surface tension of water, allowing dyes to penetrate fibers more uniformly. Dispersing agents help keep insoluble dyes evenly distributed in the dye bath, preventing aggregation and uneven coloration. Leveling agents promote uniform dye uptake, minimizing streaks or patches on the fabric. Additionally, sequestering agents are used to bind metal ions in water, which could otherwise interfere with dye-fiber interactions and cause color inconsistencies. These functions are critical for achieving high-quality, reproducible dyeing results across a wide range of fiber types and dye classes.
In the finishing stage, textile auxiliaries are equally indispensable. Softeners, for instance, are applied to improve the hand feel and drape of fabrics, while anti-static agents reduce static electricity buildup, especially in synthetic fibers. Other auxiliaries, such as flame retardants, water repellents, and antimicrobial agents, impart specific functional properties to textiles, enhancing their performance and end-use value. The application of these finishing auxiliaries is carefully controlled to ensure durability and compliance with safety and environmental standards.
The development and use of textile auxiliaries are closely monitored and guided by industry organizations and regulatory bodies. For example, the bluesign® system sets stringent criteria for chemical inputs, promoting the use of safer and more sustainable auxiliaries throughout the textile supply chain. Similarly, the OEKO-TEX® Association provides certification for textiles tested for harmful substances, including auxiliaries, ensuring consumer safety and environmental protection. Leading chemical manufacturers, such as BASF and Dow, invest heavily in research and innovation to develop auxiliaries that meet evolving performance, safety, and sustainability requirements.
In summary, textile auxiliaries are indispensable to the dyeing and finishing processes, enabling the production of high-quality, functional, and sustainable textiles. Their careful selection and application are fundamental to meeting the technical, regulatory, and environmental demands of the modern textile industry.
Innovations in Eco-Friendly and Sustainable Textile Auxiliaries
The textile industry has traditionally relied on a wide range of chemical auxiliaries to facilitate processes such as dyeing, printing, finishing, and washing. However, growing environmental concerns and stricter regulations have driven significant innovation in the development of eco-friendly and sustainable textile auxiliaries. These advancements aim to reduce the ecological footprint of textile manufacturing while maintaining or enhancing product performance.
One major area of innovation is the replacement of hazardous chemicals with biodegradable and non-toxic alternatives. For example, surfactants derived from renewable plant-based sources are increasingly used instead of conventional petroleum-based compounds. Enzyme-based auxiliaries, such as those used for bio-polishing and bio-scouring, offer effective performance at lower temperatures and with reduced water and energy consumption. These enzymes, often produced through fermentation processes, help minimize the release of harmful effluents into the environment. Organizations like Novozymes are at the forefront of developing such bio-based solutions for the textile sector.
Another significant innovation is the development of waterless or low-water processing auxiliaries. Technologies such as digital printing and supercritical CO2 dyeing require specialized auxiliaries that function effectively without large volumes of water, thereby drastically reducing wastewater generation. Companies like Archroma and Huntsman are actively engaged in creating auxiliaries tailored for these advanced processes, supporting the industry’s shift toward water conservation.
Sustainable auxiliaries also focus on improving the recyclability and biodegradability of treated textiles. For instance, certain finishing agents are now designed to break down harmlessly at the end of a garment’s life cycle, facilitating easier recycling or composting. Additionally, the use of auxiliaries free from substances of very high concern (SVHCs), as defined by regulatory bodies such as the European Chemicals Agency (ECHA), is becoming standard practice among responsible manufacturers.
Industry-wide initiatives and certifications, such as the bluesign® system, further drive the adoption of sustainable textile auxiliaries by setting rigorous criteria for chemical safety, resource efficiency, and environmental impact. These frameworks encourage manufacturers to innovate and adopt greener alternatives, ensuring that the entire supply chain aligns with global sustainability goals.
In summary, innovations in eco-friendly and sustainable textile auxiliaries are transforming the textile industry. By leveraging biotechnology, green chemistry, and advanced processing techniques, manufacturers are reducing environmental impact while meeting the evolving demands of consumers and regulators for safer, more sustainable textiles.
Impact of Auxiliaries on Fabric Performance and Quality
Textile auxiliaries play a pivotal role in determining the performance and quality of fabrics throughout various stages of textile processing. These chemical agents, which include surfactants, softeners, wetting agents, leveling agents, and finishing chemicals, are essential for achieving desired fabric properties such as softness, color fastness, durability, and functional finishes. Their impact is evident from the initial pretreatment processes to the final finishing steps, directly influencing both the aesthetic and functional attributes of textiles.
During pretreatment, auxiliaries such as wetting agents and detergents facilitate the removal of natural impurities and processing residues from fibers, ensuring uniform absorption of dyes and chemicals in subsequent steps. This not only enhances the brightness and evenness of coloration but also improves the overall handle and appearance of the fabric. For example, the use of efficient scouring agents can significantly increase the hydrophilicity of cotton, making it more receptive to dyeing and finishing treatments.
In the dyeing process, auxiliaries like dispersing agents, leveling agents, and dye-fixing agents are crucial for achieving uniform color distribution and high color fastness. Leveling agents help prevent uneven dye uptake, while dispersing agents ensure that dyes remain evenly suspended in the dye bath. Dye-fixing agents, on the other hand, enhance the wash and light fastness of dyed fabrics, contributing to the longevity and quality of the final product. The importance of these auxiliaries is recognized by industry leaders such as Archroma and Huntsman Corporation, both of which develop specialized chemical solutions to optimize dyeing performance and fabric quality.
Finishing auxiliaries impart additional properties to textiles, such as softness, water repellency, flame retardancy, and antimicrobial effects. Softeners, for instance, improve the tactile qualities of fabrics, making them more comfortable for end-users. Functional finishes, enabled by specific auxiliaries, can add value by providing wrinkle resistance, stain repellency, or UV protection. The development and application of these advanced auxiliaries are often guided by standards and research from organizations like the American Association of Textile Chemists and Colorists (AATCC), which sets benchmarks for textile performance and testing.
Ultimately, the judicious selection and application of textile auxiliaries are fundamental to achieving high-performance fabrics that meet consumer expectations and regulatory requirements. Their impact extends beyond mere appearance, influencing the durability, comfort, and functionality of textile products in diverse end-use applications.
Regulatory Standards and Compliance in Textile Chemicals
Textile auxiliaries, encompassing a broad range of chemicals used throughout textile processing—from pre-treatment and dyeing to finishing—are subject to stringent regulatory standards and compliance requirements. These regulations are designed to ensure not only the safety and quality of textile products but also to minimize environmental and human health risks associated with chemical use.
Globally, regulatory frameworks governing textile auxiliaries are shaped by both governmental agencies and international organizations. In the European Union, the European Chemicals Agency (ECHA) enforces the Registration, Evaluation, Authorisation and Restriction of Chemicals (REACH) regulation. REACH requires manufacturers and importers to register chemical substances, including textile auxiliaries, and to provide data on their properties, uses, and safe handling. Substances of Very High Concern (SVHCs) are subject to additional scrutiny, and their use in textiles may be restricted or banned.
In the United States, the U.S. Environmental Protection Agency (EPA) regulates chemicals under the Toxic Substances Control Act (TSCA). The EPA evaluates new and existing chemicals, including those used as textile auxiliaries, for potential risks to human health and the environment. Manufacturers must comply with reporting, recordkeeping, and testing requirements, and certain chemicals may be subject to restrictions or phase-outs.
Internationally, the International Organization for Standardization (ISO) develops voluntary standards that are widely adopted by the textile industry. ISO 14001, for example, provides a framework for environmental management systems, encouraging textile manufacturers to minimize the environmental impact of auxiliaries. Additionally, the Organisation for Economic Co-operation and Development (OECD) offers guidelines for the testing and assessment of chemicals, supporting harmonized safety standards across member countries.
Industry-driven initiatives also play a significant role in compliance. The Zero Discharge of Hazardous Chemicals (ZDHC) Foundation is a multi-stakeholder organization that sets guidelines for the elimination of hazardous chemicals in textile supply chains. Its Manufacturing Restricted Substances List (MRSL) specifies which auxiliaries are prohibited or restricted, promoting safer alternatives and transparency.
Compliance with these regulatory standards is essential for textile manufacturers and chemical suppliers. Non-compliance can result in product recalls, legal penalties, and reputational damage. As consumer awareness and regulatory scrutiny increase, the textile industry continues to innovate, developing eco-friendly and compliant auxiliaries to meet evolving standards and ensure sustainable production.
Market Trends and Leading Manufacturers of Textile Auxiliaries
The textile auxiliaries sector is experiencing significant transformation, driven by evolving consumer preferences, regulatory changes, and technological advancements. Textile auxiliaries—chemical agents used during various stages of textile processing such as pre-treatment, dyeing, printing, and finishing—are essential for enhancing fabric quality, performance, and appearance. The market is witnessing a shift towards sustainable and eco-friendly solutions, as environmental regulations tighten and end-users demand greener products.
One of the most prominent trends is the development and adoption of bio-based and low-impact auxiliaries. Manufacturers are investing in research to create products that reduce water and energy consumption, minimize effluent load, and comply with stringent global standards such as those set by the Organisation for Economic Co-operation and Development (OECD) and the International Labour Organization (ILO). These organizations play a pivotal role in shaping industry practices by promoting sustainable manufacturing and responsible chemical management.
Digitalization and automation are also influencing the textile auxiliaries market. Smart manufacturing processes, including automated dosing systems and real-time monitoring, are being integrated to optimize chemical usage and improve process efficiency. This not only reduces operational costs but also supports compliance with environmental and safety standards.
Asia-Pacific remains the largest and fastest-growing region for textile auxiliaries, propelled by robust textile manufacturing hubs in China, India, Bangladesh, and Vietnam. These countries benefit from large-scale production capacities and increasing investments in modernizing textile processing infrastructure. Europe and North America, meanwhile, are focusing on high-value, specialty auxiliaries and sustainable solutions, reflecting stricter regulatory frameworks and consumer awareness.
Several leading manufacturers dominate the global textile auxiliaries landscape. BASF, a German multinational, is renowned for its comprehensive portfolio of textile chemicals, emphasizing innovation and sustainability. Archroma, headquartered in Switzerland, specializes in color and specialty chemicals, with a strong commitment to eco-friendly products. Huntsman Corporation, based in the United States, is another key player, offering advanced solutions for textile processing and finishing. Other notable companies include DyStar, recognized for its expertise in dyes and auxiliaries, and Clariant, which focuses on sustainable innovations in textile chemicals.
As the textile industry continues to evolve, the demand for high-performance, sustainable, and regulatory-compliant auxiliaries is expected to grow. Leading manufacturers are responding by expanding their product lines, investing in green chemistry, and collaborating with industry bodies to set new benchmarks for safety and environmental stewardship.
Challenges in Application and Compatibility with Modern Textiles
The application of textile auxiliaries—substances used to facilitate and enhance textile processing and end-use properties—faces several challenges, particularly as the textile industry evolves toward advanced fibers, sustainable practices, and multifunctional fabrics. One of the primary challenges is ensuring compatibility between auxiliaries and the increasingly diverse range of modern textile substrates, including synthetic fibers, blends, and high-performance materials. Traditional auxiliaries, often developed for natural fibers like cotton or wool, may not perform optimally with synthetic polymers such as polyester, nylon, or specialty fibers like aramids and elastanes. This can result in issues such as inadequate wetting, uneven dyeing, or impaired fabric hand and durability.
Another significant challenge is the environmental and regulatory pressure to reduce the ecological footprint of textile processing. Many conventional auxiliaries contain chemicals that are persistent, bioaccumulative, or toxic, leading to concerns about effluent treatment and worker safety. Regulatory frameworks such as the European Union’s REACH (Registration, Evaluation, Authorisation and Restriction of Chemicals) and the ZDHC (Zero Discharge of Hazardous Chemicals) initiative, which is supported by leading apparel and chemical companies, are driving the industry to reformulate auxiliaries for lower toxicity and improved biodegradability. This transition, however, is complex, as new formulations must maintain or enhance performance while meeting stringent safety and environmental standards (ZDHC Foundation).
The rise of functional and smart textiles—such as those with antimicrobial, water-repellent, or flame-retardant properties—introduces further compatibility challenges. Auxiliaries must not only impart the desired functionality but also avoid interfering with the base properties of the textile or with other finishing agents. For example, the use of certain softeners or antistatic agents can negatively impact the effectiveness of water-repellent finishes or dye uptake. Achieving synergistic effects without adverse interactions requires careful selection and optimization of auxiliary formulations, often necessitating close collaboration between chemical suppliers, textile manufacturers, and end-users (Archroma), a global leader in specialty chemicals for textiles.
Additionally, the increasing adoption of digital printing and low-liquor dyeing technologies demands auxiliaries that are effective at lower concentrations and compatible with novel application methods. This shift challenges chemical suppliers to innovate products that deliver consistent results under new processing conditions, while also supporting the industry’s goals for water and energy conservation (Huntsman Corporation), a major provider of textile chemicals, has highlighted the need for auxiliaries tailored to these emerging technologies.
In summary, the application and compatibility of textile auxiliaries with modern textiles are shaped by the interplay of fiber innovation, environmental regulation, functional performance demands, and evolving processing technologies. Addressing these challenges requires ongoing research, cross-sector collaboration, and a commitment to sustainable chemistry.
Case Studies: Success Stories in Textile Auxiliary Implementation
The implementation of textile auxiliaries has played a transformative role in modernizing textile manufacturing, enhancing product quality, and promoting sustainability. Several case studies from leading textile producers and chemical companies illustrate the tangible benefits and innovative approaches associated with the adoption of advanced textile auxiliaries.
One notable example is the collaboration between Archroma, a global leader in specialty chemicals, and textile mills in South Asia. By introducing their “ONE WAY” sustainability service, Archroma enabled mills to optimize the use of auxiliaries such as wetting agents, dispersants, and softeners. This resulted in a significant reduction in water and energy consumption during dyeing and finishing processes, while maintaining or improving fabric quality. The project demonstrated that carefully selected auxiliaries could reduce the environmental footprint of textile production without compromising performance.
Another success story comes from Huntsman Corporation, which partnered with apparel manufacturers to implement their AVITERA SE reactive dyes and associated auxiliaries. These products allowed for lower-temperature dyeing and shorter processing times, leading to up to 50% water and energy savings. The auxiliaries used in this system also improved dye fixation and wash-off, resulting in brighter colors and enhanced fastness properties. This case highlights how innovative auxiliaries can address both economic and ecological challenges in textile processing.
In the realm of functional textiles, DyStar has worked with sportswear brands to incorporate advanced finishing auxiliaries that impart moisture management, antimicrobial, and UV-protection properties. By leveraging their expertise in chemical synthesis and application technology, DyStar enabled brands to differentiate their products in a competitive market while ensuring compliance with stringent safety and environmental standards.
Furthermore, the adoption of enzymatic auxiliaries, as promoted by organizations like Novozymes, has revolutionized processes such as bio-polishing and denim finishing. Enzyme-based auxiliaries offer a biodegradable alternative to traditional chemicals, reducing effluent load and improving fabric hand feel. Textile mills implementing these solutions have reported not only environmental benefits but also operational efficiencies and cost savings.
These case studies collectively underscore the pivotal role of textile auxiliaries in driving innovation, sustainability, and competitiveness within the textile industry. The ongoing collaboration between chemical companies, textile manufacturers, and global organizations continues to set new benchmarks for responsible and high-performance textile production.
Future Outlook: Emerging Technologies and Opportunities in Textile Auxiliaries
The future of textile auxiliaries is being shaped by rapid technological advancements, evolving regulatory landscapes, and increasing demand for sustainable solutions. As the textile industry faces mounting pressure to reduce its environmental footprint, the development and adoption of innovative auxiliary chemicals are becoming central to achieving both performance and sustainability goals.
One of the most significant trends is the shift toward bio-based and biodegradable auxiliaries. Researchers and manufacturers are exploring natural polymers, enzymes, and plant-derived surfactants as alternatives to conventional petrochemical-based products. These bio-based auxiliaries not only reduce reliance on fossil resources but also minimize the release of persistent chemicals into the environment. For example, enzymatic desizing and scouring agents are gaining traction for their ability to lower water and energy consumption during textile processing, while also reducing effluent load.
Digitalization and smart process control are also transforming the application of textile auxiliaries. The integration of sensors, data analytics, and automation in dyeing and finishing processes enables precise dosing and real-time monitoring of chemical usage. This leads to optimized resource utilization, improved product quality, and reduced waste. Such advancements align with the broader goals of Industry 4.0, which is being actively promoted by organizations like the International Labour Organization and International Organization for Standardization through the development of standards and best practices for sustainable manufacturing.
Another promising area is the development of multifunctional auxiliaries that impart additional properties to textiles, such as antimicrobial, UV-protective, or water-repellent finishes. Innovations in nanotechnology and advanced materials science are enabling the creation of auxiliaries that deliver these functionalities with lower chemical loads and improved durability. For instance, the use of silver nanoparticles or bio-based antimicrobial agents is being explored to meet the growing demand for hygienic and protective textiles in healthcare and consumer markets.
Regulatory frameworks are also influencing the future of textile auxiliaries. Stricter environmental and safety regulations, such as those set by the U.S. Environmental Protection Agency and the European Chemicals Agency, are driving the phase-out of hazardous substances and encouraging the adoption of greener alternatives. Compliance with global standards, including those developed by the International Organization for Standardization, is becoming a prerequisite for market access and brand reputation.
In summary, the future of textile auxiliaries lies in the convergence of green chemistry, digital innovation, and regulatory compliance. Companies that invest in research and development of sustainable, high-performance auxiliaries will be well-positioned to capitalize on emerging opportunities and address the evolving needs of the global textile industry.
Sources & References
- International Organization for Standardization
- OEKO-TEX Association
- BASF
- Archroma
- European Chemicals Agency (ECHA)
- American Association of Textile Chemists and Colorists (AATCC)
- European Chemicals Agency (ECHA)
- Zero Discharge of Hazardous Chemicals (ZDHC) Foundation
- DyStar
- Clariant
- ZDHC Foundation