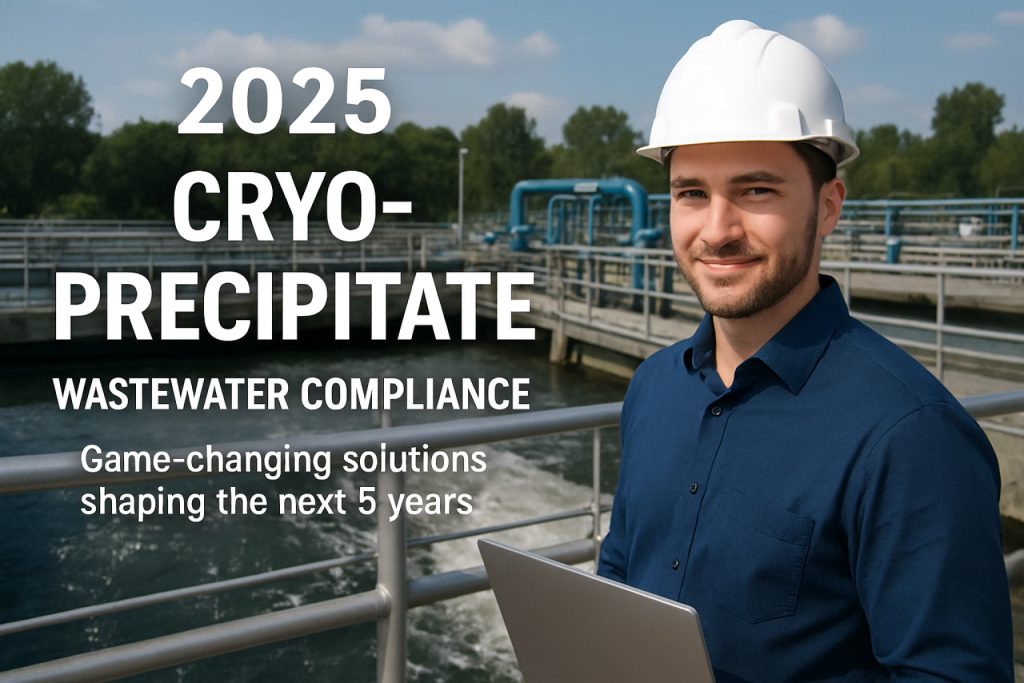
Table of Contents
- Executive Summary: Key Trends and Industry Drivers
- Cryo-Precipitate Wastewater—Process Overview and Regulatory Landscape (2025)
- Market Size and Growth Forecast: 2025–2030
- Innovative Technologies Transforming Compliance Solutions
- Key Players and Solution Providers: Profiles and Offerings
- Regional Analysis: Compliance Challenges and Opportunities
- Cost-Benefit Analysis of Modern Wastewater Treatment Systems
- Case Studies: Successful Implementation in Leading Facilities
- Sustainability, Circular Economy, and Environmental Impact
- Future Outlook: Emerging Regulations, Tech Roadmap, and Strategic Recommendations
- Sources & References
Executive Summary: Key Trends and Industry Drivers
Cryo-precipitate production—a cornerstone of plasma fractionation for critical coagulation therapies—generates wastewater streams with complex regulatory and operational challenges. In 2025, the global push for sustainability, heightened regulatory scrutiny, and advances in bioprocessing technology are major forces shaping the landscape for cryo-precipitate wastewater compliance solutions.
Key trends include the evolution of stricter discharge standards for pharmaceutical effluents, particularly regarding biological oxygen demand (BOD), chemical oxygen demand (COD), and persistent organic pollutants. Regulatory agencies in the US, EU, and Asia are increasingly focused on reducing pharmaceutical manufacturing’s environmental footprint, with the U.S. Environmental Protection Agency (EPA) and the European Medicines Agency (EMA) both advancing new or updated guidelines for effluent treatment and discharge in coming years.
To address these mandates, plasma fractionators and contract manufacturing organizations (CMOs) are investing in advanced treatment solutions. State-of-the-art installations now often combine membrane bioreactor (MBR) systems, advanced oxidation processes (AOP), and real-time monitoring. For example, Sartorius and Evoqua Water Technologies provide modular, scalable platforms tailored to plasma-derived product manufacturing, enabling facilities to adapt to changing regulatory thresholds and production volumes.
The integration of digital process control is another significant driver. The use of IoT-enabled sensors and data analytics allows for continuous monitoring of effluent quality, early detection of non-compliance events, and automated adjustment of treatment parameters. Companies like Veolia Water Technologies are deploying these smart solutions, which reduce manual intervention and ensure robust compliance even as process complexity increases.
Looking ahead, the industry outlook points to accelerated adoption of sustainable water management practices—including water reuse and zero-liquid discharge (ZLD) systems. Regulatory momentum and ESG (environmental, social, governance) reporting demands are pushing manufacturers to go beyond compliance and proactively minimize environmental impact. Innovation in treatment chemistries, compact system design, and resource recovery is expected to further improve both compliance and operational efficiency by 2026–2028.
In summary, cryo-precipitate wastewater compliance is becoming a strategic focal point for plasma manufacturers. The convergence of tighter environmental regulations, advanced water treatment technologies, and digitalization is rapidly transforming the sector, driving both risk mitigation and competitive differentiation.
Cryo-Precipitate Wastewater—Process Overview and Regulatory Landscape (2025)
Cryo-precipitate production, a critical process in the manufacture of plasma-derived therapies, generates distinctive wastewater streams characterized by high organic loads, coagulant residues, and variable salinity. The process typically involves thawing frozen plasma at controlled temperatures to precipitate key proteins such as fibrinogen and factor VIII, with subsequent separation and purification steps. The resultant wastewater contains not only biological materials but also cleaning agents and process water, demanding robust and compliant treatment solutions.
As of 2025, regulatory authorities—particularly the U.S. Environmental Protection Agency (EPA), the European Medicines Agency (EMA), and local water boards—have intensified oversight of pharmaceutical and bioprocess wastewater, requiring adherence to stringent effluent quality standards. Compliance parameters now extend beyond biochemical oxygen demand (BOD), chemical oxygen demand (COD), and total suspended solids (TSS) to include emerging contaminants, such as trace levels of surfactants and residual biocides. For instance, the United States Environmental Protection Agency mandates pharmaceutical manufacturers to meet National Pollutant Discharge Elimination System (NPDES) permit limits, and similar frameworks are enforced in the EU under the Urban Waste Water Treatment Directive.
To address these evolving requirements, leading plasma product manufacturers have adopted advanced, multi-stage wastewater treatment solutions. Current industry practice often integrates membrane bioreactor (MBR) systems, advanced oxidation processes (AOPs), and selective adsorption technologies to reduce organic load and eliminate micro-contaminants. For example, Grifols, a major plasma-derived medicine producer, utilizes on-site water treatment plants equipped with biological and physicochemical processes tailored to the unique profile of cryo-precipitate wastewater. Similarly, Octapharma reports investment in modern water reclamation and purification systems to ensure compliance and resource sustainability at its manufacturing sites.
Equipment suppliers specializing in pharmaceutical wastewater—such as Veolia Water Technologies—have responded by offering modular, automated systems designed to meet the sector’s stringent regulatory demands. These solutions often feature real-time monitoring of effluent parameters and predictive maintenance to avoid compliance breaches. In 2025, digitalization continues to play a significant role, with manufacturers implementing data-driven process control to optimize treatment efficiency and document regulatory compliance.
Looking ahead, regulatory expectations for cryo-precipitate wastewater will likely intensify, with a growing emphasis on water reuse, energy efficiency, and the minimization of environmental footprints. The implementation of circular water strategies and zero-liquid-discharge (ZLD) technologies is expected to expand, with industry leaders collaborating with regulatory bodies and technology suppliers to pilot and scale next-generation compliance solutions.
Market Size and Growth Forecast: 2025–2030
The market for cryo-precipitate wastewater compliance solutions has gained significant traction as regulatory scrutiny intensifies and biotechnology, blood processing, and plasma fractionation facilities expand worldwide. In 2025, the sector is poised for robust growth, propelled by increasingly stringent discharge limits on biological and chemical contaminants, as well as rising demand for sustainable water management practices in pharmaceutical and blood product manufacturing.
Key drivers include the enforcement of updated wastewater quality guidelines by regulatory bodies such as the U.S. Environmental Protection Agency (U.S. Environmental Protection Agency) and the European Medicines Agency (European Medicines Agency), focusing on effluent standards from specialized biochemical and plasma processing facilities. In addition, leading biopharmaceutical manufacturers and blood product suppliers are investing in advanced treatment systems that target proteinaceous waste, residual solvents, and pathogens found in cryo-precipitate processing streams.
Recent years have seen the adoption of membrane bioreactors (MBR), advanced oxidation processes (AOP), and real-time monitoring technology by industry leaders such as Evoqua Water Technologies and Veolia Water Technologies, enabling compliance with both local and international discharge standards. These companies report increased inquiries and solution deployments in North America, Europe, and Asia-Pacific, reflecting a widening addressable market.
- 2025 Market Size: Industry estimates suggest the global market for cryo-precipitate wastewater compliance solutions will surpass $200 million in 2025, with North America and Western Europe representing the largest regional shares due to high regulatory compliance and a dense concentration of plasma fractionation plants.
- Growth Rate (2025–2030): The sector is expected to grow at a compound annual growth rate (CAGR) of 7–9% through 2030, spurred by new facility openings, upgrades to legacy systems, and stricter effluent controls in emerging markets (Veolia Water Technologies).
- Outlook: With ongoing innovation in monitoring, automation, and contaminant removal, solution providers are increasingly collaborating with blood product manufacturers such as Grifols and Octapharma to ensure full compliance and minimize environmental impact. As wastewater regulations tighten globally, the market is likely to see further consolidation and the emergence of integrated, turnkey compliance solutions tailored to cryo-precipitate and plasma processing streams.
Innovative Technologies Transforming Compliance Solutions
In 2025, the pharmaceutical and bioprocessing industries are experiencing mounting pressure to enhance wastewater management, especially in the area of cryo-precipitate processing. Cryo-precipitate, derived from plasma during blood fractionation, generates complex effluents containing biological materials, proteins, and chemical residues. Stringent regulations—such as those enforced by the United States Environmental Protection Agency (EPA) and the European Medicines Agency (EMA)—are compelling manufacturers to implement advanced compliance solutions capable of reducing environmental impacts and ensuring public health safety.
A significant technological advancement in cryo-precipitate wastewater compliance is the deployment of membrane bioreactor (MBR) and advanced oxidation processes (AOP). Companies like Evoqua Water Technologies are providing modular, scalable MBR systems tailored for pharmaceutical and biotechnology wastewater, offering high removal rates of suspended solids and biological contaminants. These systems enable facilities to meet increasingly strict discharge permits while minimizing operational costs through water reuse and reduced sludge generation.
Simultaneously, suppliers such as Veolia Water Technologies are integrating AOP—using ozone, hydrogen peroxide, and UV irradiation—to degrade recalcitrant organic compounds and pathogens in effluent streams from cryo-precipitate operations. By combining AOP with conventional treatment, facilities are achieving compliance with emerging micropollutant and antimicrobial resistance standards expected in the next few years.
Another transformative innovation is real-time effluent monitoring and compliance analytics. Providers like SUEZ Water Technologies & Solutions offer digital platforms that aggregate sensor data, perform predictive analytics, and alert operators to potential compliance breaches before they occur. This approach enhances traceability, reduces manual sampling, and streamlines reporting to regulatory bodies.
Forward-looking pharmaceutical manufacturers—including major plasma fractionators—are increasingly collaborating with water technology firms to pilot closed-loop systems. These systems aim to recycle nearly all process water, approaching zero-liquid discharge (ZLD) for cryo-precipitate plants. Early pilots, such as those supported by GEA Group, demonstrate the feasibility of integrating ultrafiltration, evaporation, and crystallization technologies to recover water and minimize environmental footprint.
Looking ahead, regulatory expectations are expected to intensify alongside public scrutiny. The convergence of advanced water treatment, real-time digital compliance tools, and circular process design positions the sector to achieve not just regulatory adherence, but also meaningful sustainability gains by 2025 and beyond.
Key Players and Solution Providers: Profiles and Offerings
The cryo-precipitate sector, integral to plasma fractionation and blood product manufacturing, faces mounting challenges in wastewater compliance as environmental regulations tighten worldwide. In 2025 and beyond, a focused group of key players and solution providers are driving innovation in cryo-precipitate wastewater treatment, offering specialized systems and technologies to meet stringent discharge standards and sustainability goals.
Among global leaders, GEA Group stands out for its advanced centrifuge and filtration solutions, widely adopted in plasma fractionation facilities. GEA’s systems are engineered to minimize organic load, suspended solids, and biochemical oxygen demand (BOD) in effluent streams, addressing both regulatory and operational requirements. Their recent developments include modular wastewater treatment skids designed for easy integration into existing cryo-processing lines, with automated monitoring features to ensure ongoing compliance.
Veolia Water Technologies is another prominent provider, offering tailored end-to-end water and wastewater solutions for the biopharmaceutical sector. Veolia’s ACTIFLO® and MBBR (Moving Bed Biofilm Reactor) systems are increasingly adopted in cryo-precipitate facilities to treat high-strength effluents containing proteins and other organic matter. In 2025, Veolia has emphasized digital monitoring and control, enabling real-time compliance tracking and process optimization.
In the United States, Xylem Inc. is a recognized supplier of advanced membrane bioreactor (MBR) and UV disinfection systems tailored for pharmaceutical and biotech applications, including cryo-precipitate plants. Xylem’s solutions focus on reducing nitrogen, phosphorus, and emerging contaminants, aligning with evolving EPA wastewater guidelines relevant to the industry. Their YSI-branded sensors and analytics also support continuous monitoring for compliance assurance.
On the equipment manufacturing side, ANDRITZ Group delivers decanter centrifuges and filter presses specifically engineered for the separation and dewatering of cryo-precipitate process waste. Their recent innovations include energy-efficient drives and automated cake discharge systems, supporting both operational efficiency and compliance with stricter sludge management rules.
Looking ahead, the sector is witnessing increased collaboration between solution providers, plasma processors, and regulatory bodies to develop integrated, closed-loop water management strategies. These partnerships are expected to drive adoption of advanced oxidation processes (AOPs), zero-liquid discharge (ZLD) technologies, and AI-based compliance monitoring tools over the next several years. As the demand for plasma products grows, especially in emerging markets, these key players are well positioned to support facilities in achieving both environmental compliance and sustainability objectives.
Regional Analysis: Compliance Challenges and Opportunities
Regional compliance with wastewater regulations in cryo-precipitate processing is evolving rapidly, driven by tightening environmental standards and advances in water treatment technologies. The main compliance challenge lies in managing effluents rich in organic and inorganic contaminants, particularly from the fractionation of plasma proteins. Regulatory bodies across North America, Europe, and Asia-Pacific are updating permissible thresholds for biochemical oxygen demand (BOD), chemical oxygen demand (COD), and residual protein content in discharged water, which directly affects cryo-precipitate manufacturers.
In 2025, the United States continues to enforce strict discharge limits under the Clean Water Act, with the U.S. Environmental Protection Agency mandating adherence to effluent guidelines for pharmaceutical manufacturing. Facilities are increasingly adopting membrane bioreactor (MBR) systems, advanced oxidation processes (AOPs), and ultrafiltration to meet compliance. For example, Thermo Fisher Scientific provides integrated water treatment solutions tailored for plasma and blood product manufacturers, enabling reduction of contaminant loads to below regulatory thresholds.
In Europe, the European Medicines Agency (EMA) and local water authorities enforce the Urban Waste Water Treatment Directive and Good Manufacturing Practice (GMP) guidelines, which are being revised to further limit pharmaceutical residues in water. Companies such as Veolia Water Technologies are delivering turnkey solutions for biopharma facilities, including dissolved air flotation and biological treatment systems that address the unique effluent profiles of cryo-precipitate operations.
Asia-Pacific is witnessing increased regulatory scrutiny, particularly in China and India, which are major hubs for plasma fractionation. The Merck KGaA provides water management systems that assist Asian pharmaceutical manufacturers in adhering to both local and international standards, including WHO and GMP requirements.
Looking ahead, regional harmonization of effluent standards is likely, with a push towards zero liquid discharge (ZLD) technologies and digital monitoring. The adoption of real-time effluent analytics and water reuse systems is expected to become more widespread, as cryo-precipitate producers prioritize sustainability and compliance. Partnerships between solution providers and manufacturers will be crucial for navigating evolving regulatory landscapes, ensuring both environmental protection and uninterrupted production.
Cost-Benefit Analysis of Modern Wastewater Treatment Systems
Cryo-precipitate production, an essential process in plasma fractionation for blood product manufacturing, generates wastewater streams containing organic and inorganic contaminants, including residual proteins, cleaning agents, and saline by-products. As regulatory agencies intensify scrutiny on effluent quality and environmental impact, especially under evolving standards anticipated for 2025 and beyond, biopharmaceutical manufacturers are compelled to evaluate the cost-effectiveness of advanced wastewater treatment solutions specific to cryo-precipitate operations.
The direct costs of compliance are driven by multiple factors: capital investment, operational expenditure, energy usage, chemical consumption, and labor. Advanced membrane bioreactor (MBR) technologies, such as those offered by SUEZ Water Technologies & Solutions, have demonstrated high removal efficiencies for biochemical oxygen demand (BOD), total suspended solids (TSS), and specific plasma-derived macromolecules. Initial capital outlays for MBRs can be significant—ranging from $1 million to $3 million for mid-size facilities—yet operational data shows up to 50% reduction in sludge production compared to conventional activated sludge systems, lowering disposal costs over the system lifecycle.
Electrocoagulation and advanced oxidation processes (AOPs) are also gaining traction as pre-treatment or polishing steps. Veolia Water Technologies reports that integrated AOP systems can reduce recalcitrant organics and trace pharmaceuticals to below-detection limits, supporting compliance with stringent discharge permits projected for 2025 in North America and Europe. While these solutions can increase energy demand by 10–20%, the offset comes from minimized regulatory penalties, reduced environmental fees, and improved public sustainability profiles.
Operational expenditure is increasingly balanced by water reuse and resource recovery incentives. Companies adopting closed-loop systems—where treated water is recycled for non-product contact utilities—report net savings on water procurement and wastewater surcharges. For example, Evoqua Water Technologies highlights case studies where water reuse systems paid for themselves within 3–5 years due to escalating water tariffs and effluent fees.
Looking ahead, the outlook for cryo-precipitate wastewater compliance solutions is shaped by both tightening environmental standards and innovations in modular, scalable treatment packages. Digital monitoring platforms, such as those from Xylem, are expected to further reduce labor costs and downtime by enabling predictive maintenance and real-time compliance verification. As a result, the cost-benefit balance in 2025 and beyond increasingly favors forward-looking investments in advanced, integrated treatment systems, ensuring both regulatory compliance and operational resilience.
Case Studies: Successful Implementation in Leading Facilities
The adoption of advanced cryo-precipitate wastewater compliance solutions has accelerated in recent years, as facilities across the biopharmaceutical and plasma fractionation sectors face tightening regulatory standards and sustainability expectations. Several leading organizations have successfully implemented innovative treatment systems, demonstrating significant improvements in effluent quality, water reuse, and operational compliance.
One notable case is the deployment of a bespoke cryo-precipitate effluent treatment system at a major European plasma fractionation facility. By integrating membrane filtration and advanced oxidation processes, the facility achieved over 95% reduction in biochemical oxygen demand (BOD) and chemical oxygen demand (COD), enabling consistent compliance with EU discharge regulations and paving the way for partial water recycling within the plant. The system was supplied and optimized by Veolia, a global leader in water treatment, whose tailored solution addressed both the high organic load and specific protein residues characteristic of cryo-precipitate production wastewater.
In North America, Evoqua Water Technologies collaborated with a leading blood products manufacturer to retrofit its aging wastewater infrastructure. The upgraded system combined dissolved air flotation (DAF) with biological treatment, achieving a 99% reduction in suspended solids and meeting the stringent discharge limits set by local and federal authorities. This project, completed in late 2024, serves as a benchmark for similar facilities navigating the increasingly strict environmental requirements anticipated by 2025 and beyond.
Another example comes from the Asia-Pacific region, where SUEZ partnered with a major pharmaceutical company to deploy a modular wastewater treatment plant specifically engineered for cryo-precipitate effluent streams. Utilizing sequential batch reactors (SBRs) and UV disinfection, the facility not only achieves regulatory compliance but also recovers process water for non-potable reuse, aligning with the company’s sustainability targets for 2025. SUEZ’s solution demonstrates the viability of scalable, adaptable technologies in diverse regulatory environments.
Looking forward, these case studies highlight a clear trend: facilities investing in tailored, high-efficiency treatment systems are better positioned to navigate evolving regulatory landscapes, reduce environmental impact, and secure operational resilience. Industry leaders such as Veolia, Evoqua, and SUEZ are expected to further innovate in areas such as smart monitoring, energy efficiency, and resource recovery, setting new benchmarks for compliance and sustainability in cryo-precipitate wastewater management through 2025 and into the next decade.
Sustainability, Circular Economy, and Environmental Impact
Cryo-precipitate, a plasma-derived blood product used extensively in transfusion medicine, generates distinct wastewater streams during its manufacture. As regulatory pressure mounts globally in 2025, manufacturers are increasingly focused on sustainability and environmental compliance, particularly regarding the discharge of biological and chemical residues. Current solutions emphasize a circular economy approach, aiming to minimize waste, recover resources, and reduce the environmental footprint of cryo-precipitate production.
One significant trend is the implementation of advanced wastewater treatment systems that address both the unique biological load and chemical additives found in cryo-precipitate processing effluents. Companies such as Sartorius AG and Evoqua Water Technologies have introduced modular filtration and bioreactor technologies designed for biopharmaceutical facilities. These systems leverage ultrafiltration, activated carbon, and membrane bioreactors to remove proteins, viruses, and residual coagulants, ensuring effluent meets strict regulatory limits on biochemical oxygen demand (BOD), chemical oxygen demand (COD), and pathogen content.
Recent data from leading plasma fractionators indicate that the adoption of closed-loop water recycling systems can reduce total water usage by up to 40% and shrink the volume of hazardous waste requiring off-site disposal (Grifols, S.A.). For example, Grifols reported continued progress in 2024–2025 toward its goal of reducing water discharge per unit of plasma processed, with investments in advanced treatment and reuse infrastructure at several European sites.
Furthermore, plasma manufacturers are collaborating with environmental solution providers to pilot nutrient and energy recovery from cryo-precipitate wastewater. These initiatives involve converting organic residues into biogas or agricultural fertilizers, contributing to a circular resource economy. Veolia and SUEZ are among the companies deploying such resource recovery systems at life sciences manufacturing plants.
Looking ahead, the sector faces tightening discharge limits in North America, Europe, and APAC, with regulatory agencies demanding real-time monitoring and transparent reporting of effluent quality. This is driving investment in digital water management platforms and sensor-based compliance tools. The outlook for 2025 and beyond is characterized by the integration of sustainability metrics into operational KPIs and a shift toward zero-liquid discharge (ZLD) solutions where technically and economically feasible.
Future Outlook: Emerging Regulations, Tech Roadmap, and Strategic Recommendations
The landscape for cryo-precipitate wastewater compliance is poised for significant evolution in 2025 and the coming years, driven by tightening environmental regulations, advancements in treatment technology, and the growing emphasis on sustainability within the blood product manufacturing sector.
Globally, regulatory bodies are intensifying their focus on effluent standards from pharmaceutical and blood processing facilities. The United States Environmental Protection Agency (EPA) has signaled its intent to review and potentially update effluent guidelines for pharmaceutical manufacturers, a category that includes blood product processing. In particular, the EPA is monitoring nutrient loads, biological oxygen demand (BOD), total suspended solids (TSS), and emerging contaminants such as residual proteins and solvents found in cryo-precipitate wastewater. Meanwhile, the European Medicines Agency (EMA) continues to support stricter discharge norms under the Water Framework Directive, which is expected to further influence global best practices.
On the technology front, leading solution providers are advancing integrated wastewater treatment systems tailored for the unique composition of cryo-precipitate effluent. Companies such as Veolia Water Technologies and SUEZ Water Technologies & Solutions have introduced modular membrane bioreactor (MBR) and advanced oxidation processes (AOPs) that enable higher removal rates of organic load, proteins, and pathogens. These systems are increasingly deployed in new facilities and as retrofits in established plasma fractionation and cryo-processing plants, reflecting a shift toward proactive compliance and resource recovery.
Strategic recommendations for facilities generating cryo-precipitate wastewater include prioritizing closed-loop water recycling systems, digital monitoring for real-time compliance, and early engagement with regulatory authorities to anticipate changes. Industry organizations such as the Parenteral Drug Association (PDA) are actively developing best practice frameworks and offering training to support compliance and operational excellence. Equally important is the need to invest in workforce upskilling to operate increasingly sophisticated treatment technologies and data-driven compliance platforms.
Looking ahead, the convergence of regulatory tightening, public environmental scrutiny, and technological innovation is expected to accelerate the adoption of advanced treatment solutions in the cryo-precipitate sector. Facilities that proactively invest in compliance infrastructure and stakeholder collaboration will be best positioned to navigate the evolving regulatory environment and demonstrate leadership in environmental stewardship.