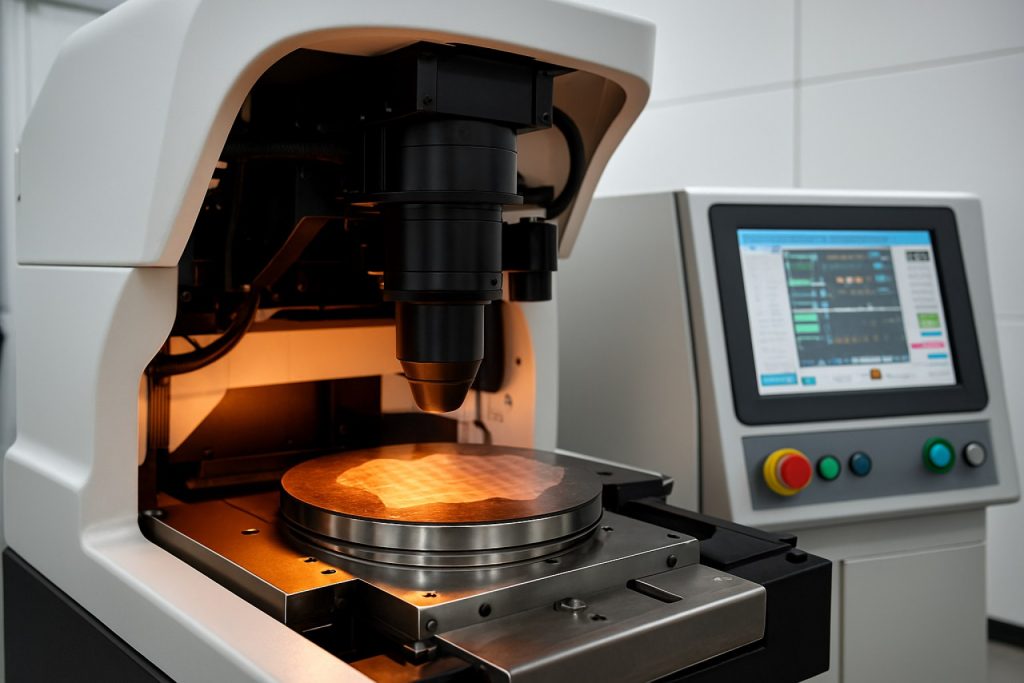
Table of Contents
- Executive Summary: Key Developments in Nonplanar Photolithography Equipment (2025–2030)
- Market Size and Growth Forecast: Revenue and Volume Projections
- Emerging Technologies: Innovations Shaping Nonplanar Photolithography
- Competitive Landscape: Major Manufacturers and New Entrants
- Key Applications: Semiconductors, MEMS, and Beyond
- Regional Analysis: Leading Markets and Expansion Hotspots
- Manufacturing Challenges: Technical Barriers and Solutions
- Supply Chain and Partnerships: Collaborations Across the Value Chain
- Regulatory and Standardization Updates: Compliance Trends
- Future Outlook: Opportunities, Risks, and Strategic Recommendations
- Sources & References
Executive Summary: Key Developments in Nonplanar Photolithography Equipment (2025–2030)
From 2025 onward, nonplanar photolithography equipment manufacturing is poised for significant progress, propelled by the expanding demand for advanced semiconductor devices and the rise of flexible, three-dimensional (3D) electronics. Traditional planar photolithography has reached its limits in addressing the complexities of next-generation device architectures—such as curved sensors, flexible displays, and biomedical implants—prompting leading equipment manufacturers to prioritize nonplanar solutions.
Key players, including ASML Holding, Canon Inc., and Nikon Corporation, have accelerated R&D efforts in adapting projection optics, stage mechanics, and resist coating systems for nonplanar substrates. In early 2025, ASML Holding announced collaborative pilot projects with major semiconductor foundries to develop prototype tools capable of patterning on curved wafers, leveraging advanced alignment and focus tracking technologies. Canon Inc. has similarly demonstrated new mask aligners optimized for non-flat surfaces, citing improved overlay accuracy and defect control as critical milestones for commercialization.
Meanwhile, Nikon Corporation reported successful integration of dynamic focus compensation in their step-and-repeat systems, enabling high-precision patterning on micro-lens arrays and other nonplanar substrates for imaging and sensing applications. Equipment modifications—such as multi-axis wafer stages and adaptive optics—are becoming increasingly standard in new product lines, reflecting the sector’s shift toward manufacturing flexibility and substrate diversity.
On the materials side, partnerships between equipment manufacturers and specialty resist suppliers (e.g., Tokyo Ohka Kogyo and JSR Corporation) are accelerating the development of conformal coatings and tailored chemistries for robust, uniform pattern transfer on 3D topographies. Progress in this area is expected to support mass production readiness for advanced medical devices, advanced packaging, and next-generation optoelectronics by 2027.
Looking ahead to 2030, industry forecasts suggest that the adoption rate of nonplanar photolithography equipment will rise sharply, particularly in sectors requiring high-value, complex geometries. Equipment manufacturers are expected to scale up production capacity and introduce modular toolsets, reducing customization costs and supporting faster time-to-market for innovative device designs. Industry consortia and standardization efforts, such as those led by SEMI, are anticipated to play a pivotal role in establishing interoperability and process guidelines, further accelerating commercialization across the supply chain.
Market Size and Growth Forecast: Revenue and Volume Projections
The global market for nonplanar photolithography equipment is poised for significant expansion in 2025 and the ensuing years, driven by rapid advancements in semiconductor device architectures, displays, and flexible electronics. As the demand for three-dimensional (3D), curved, and flexible substrates rises, traditional planar lithography tools encounter limitations, opening opportunities for novel equipment specifically engineered for nonplanar surfaces.
Leading semiconductor equipment manufacturers are ramping up research and development efforts to commercialize nonplanar photolithography solutions. ASML Holding NV, the world’s largest lithography equipment supplier, has highlighted ongoing work in next-generation systems that address complex substrate topographies, though its primary focus remains on extreme ultraviolet (EUV) technology for planar wafers. Meanwhile, companies such as Canon Inc. and Nikon Corporation—both established in advanced lithography—are exploring adaptations of mask aligners and steppers for nonplanar applications, targeting new markets in flexible and wearable electronics.
While precise revenue figures dedicated solely to nonplanar photolithography are not yet publicly disclosed due to the nascent state of the segment, several indicators point to robust growth. The flexible electronics industry, a primary end-user, is forecast to surpass $50 billion globally by 2025, with a compound annual growth rate (CAGR) exceeding 10% over the next few years, according to projections from suppliers such as Kateeva, Inc., a leader in inkjet-based deposition and patterning for flexible OLED displays. As device makers accelerate adoption, demand for specialized lithography tools will follow.
- Volume Projections: Equipment shipments are expected to transition from low-volume, custom-built systems toward scalable, production-ready platforms by 2025–2027. Industry leaders anticipate initial annual unit volumes in the hundreds, with the potential to reach several thousand units as adoption in consumer electronics, automotive, and healthcare gathers pace.
- Revenue Outlook: The aggregate market value for nonplanar photolithography equipment is projected to reach several hundred million dollars by 2027, fueled by investments from both established manufacturers and emerging innovators. SÜSS MicroTec SE, a supplier of mask aligners and photolithography tools, has announced expansion in its product portfolio to address 3D integration and advanced packaging applications, signaling anticipated revenue streams from nonplanar solutions.
In summary, the sector is in an early commercialization phase, with strong growth drivers stemming from end-market innovation. The next few years will likely see accelerated investment, rising shipment volumes, and a transition from niche to mainstream manufacturing applications.
Emerging Technologies: Innovations Shaping Nonplanar Photolithography
The landscape of nonplanar photolithography equipment manufacturing is rapidly evolving, driven by the increasing demand for advanced packaging, flexible electronics, and three-dimensional microfabrication. As of 2025, leading semiconductor equipment manufacturers are intensifying research and development in this sector, aiming to overcome the limitations of traditional planar lithography and address the complexities of patterning on curved, flexible, or irregular surfaces.
One significant technological innovation is the adaptation of maskless lithography and direct-write laser systems for nonplanar substrates. Companies such as Nanoscribe GmbH are advancing two-photon polymerization techniques, enabling high-resolution, three-dimensional structuring on diverse surfaces. These systems are increasingly being integrated into prototyping and production environments, particularly for micro-optics and biomedical device applications.
Major lithography equipment suppliers, including ASML Holding, are exploring the extension of their existing optical lithography platforms to accommodate nonplanar applications, leveraging advanced alignment and focus systems. While mainstream immersion and EUV lithography remain tailored for planar wafers, the push towards heterogeneous integration and wafer-level packaging is prompting collaborations between toolmakers and material scientists to develop adaptable photolithography modules that maintain nanoscale precision on variable topographies.
Meanwhile, ULVAC, Inc. and EV Group (EVG) are investing in equipment that facilitates conformal coating, imprint lithography, and photomask projection on 3D and flexible substrates. EVG, for example, has recently introduced platforms designed for nanoimprint lithography (NIL) that can pattern complex 3D shapes and curved surfaces, supporting next-generation sensor and microfluidic device manufacturing.
The outlook for the next few years suggests a transition from niche R&D applications toward broader adoption in industrial production. The proliferation of flexible displays, wearable electronics, and advanced sensor arrays is expected to catalyze demand for nonplanar photolithography tools. Equipment manufacturers are responding by developing modular systems with real-time surface mapping, adaptive optics, and advanced process control to ensure uniformity and repeatability across nonplanar substrates.
Collaborative initiatives between equipment vendors and end-users—such as those seen in consortia like SEMI—are likely to accelerate the standardization and commercialization of nonplanar photolithography processes. As the sector matures, ongoing innovation in light sources, resist chemistries, and automation will be central to unlocking new capabilities and scaling production for the coming decade.
Competitive Landscape: Major Manufacturers and New Entrants
The competitive landscape for nonplanar photolithography equipment manufacturing in 2025 is characterized by a mix of established semiconductor equipment giants and emerging technology-focused entrants. The demand for advanced lithography solutions capable of handling curved, flexible, or otherwise nonplanar substrates is accelerating, driven by innovations in flexible electronics, biomedical devices, and advanced packaging.
Among the major incumbents, ASML Holding N.V. continues to exert significant influence on the photolithography equipment market. While their flagship extreme ultraviolet (EUV) systems are primarily designed for planar silicon wafers, ASML has initiated research collaborations aimed at adapting projection optics and stage technology for nonplanar and heterogeneous substrates, particularly for advanced packaging and 3D integration.
Canon Inc. and Nikon Corporation, both pioneers in mask aligner and stepper systems, are leveraging their expertise in precision optics and alignment to develop lithography platforms suitable for non-flat substrates. Canon’s industrial equipment division has reported ongoing R&D into maskless and conformal photolithography tools targeting micro-LED displays and biomedical sensor applications. Similarly, Nikon’s Advanced Lithography Division has announced pilot lines in Japan for flexible display and sensor manufacturing using modified projection aligners.
New entrants and specialized manufacturers are increasingly shaping the nonplanar segment. KARL SUSS America, Inc. (part of SÜSS MicroTec Group), known for its mask aligners and bonders for MEMS and advanced packaging, has introduced mask aligner models with substrate conformal imprinting capabilities, specifically designed for curved and 3D substrates. Meanwhile, EV Group (EVG) has expanded its nanoimprint lithography (NIL) portfolio to include systems for nonplanar and roll-to-roll processing, targeting flexible electronics and biomedical chips.
The competitive barrier remains high due to the technical complexity of maintaining precise pattern transfer and alignment on nonplanar surfaces. However, several academic spin-offs and startups are entering the field, often through partnerships with established tool vendors. These new entrants typically focus on proprietary conformal optics, adaptive exposure systems, or hybrid additive/subtractive approaches—sometimes in collaboration with device manufacturers and research consortia.
Looking ahead, the landscape is expected to see further collaboration between leading equipment manufacturers and specialist startups, with a focus on tool modularity and process flexibility. As device architectures become increasingly three-dimensional and application-specific, the ability to deliver reliable, scalable nonplanar lithography equipment will be central to competitive positioning in this evolving market.
Key Applications: Semiconductors, MEMS, and Beyond
Nonplanar photolithography equipment manufacturing is rapidly gaining traction across a diverse set of key applications, most notably in the fields of semiconductors and microelectromechanical systems (MEMS), as well as in emerging sectors such as advanced packaging, biomedical devices, and flexible electronics. As of 2025, the demand for innovative lithography solutions is driven by the growing complexity of device architectures and the need for patterning on non-flat substrates.
- Semiconductors: The semiconductor industry is undergoing a paradigm shift as device geometries shrink and architectures become more three-dimensional. Nonplanar photolithography equipment is increasingly essential for producing advanced logic and memory devices with features such as FinFETs and gate-all-around (GAA) transistors. Leading manufacturers like ASML continue to push the boundaries with extreme ultraviolet (EUV) lithography and are actively exploring solutions for patterning over topographies and nonplanar surfaces. These technologies are crucial for meeting the demands of next-generation chip designs, especially as the industry moves toward sub-2nm process nodes.
- MEMS: MEMS devices, which often feature complex three-dimensional structures, require specialized lithography techniques to accurately define patterns on curved or irregular surfaces. Equipment manufacturers such as SÜSS MicroTec are developing mask aligners and projection systems tailored for nonplanar MEMS fabrication, enabling higher performance in sensors, actuators, and RF components. These capabilities are vital for the continued miniaturization and integration of MEMS in applications ranging from automotive to consumer electronics.
- Advanced Packaging: The trend toward heterogeneous integration and 3D stacking in advanced packaging necessitates precise photolithography on stepped and nonplanar surfaces. Companies like Tokyo Ohka Kogyo Co., Ltd. are offering materials and equipment solutions that support high-resolution patterning for fan-out wafer-level packaging (FOWLP) and chiplet integration. The adoption of such technologies is expected to accelerate through 2025 and beyond, driven by the need for higher bandwidth and lower latency in high-performance computing and AI chips.
- Flexible and Biomedical Devices: The rise of flexible electronics and implantable biomedical devices has created new demand for photolithography equipment capable of handling substrates that are nonplanar, stretchable, or biocompatible. Companies like Kloe are developing direct-write and maskless lithography systems that can accommodate these unconventional form factors, enabling innovation in wearable sensors, smart textiles, and lab-on-chip devices.
Looking ahead, the outlook for nonplanar photolithography equipment manufacturing remains robust. The convergence of semiconductor scaling, MEMS complexity, and new frontiers in flexible and biomedical electronics ensures continued investment and technological advancement. As equipment vendors and materials suppliers expand their portfolios to address these evolving requirements, the next few years will likely see further breakthroughs in resolution, throughput, and process adaptability, cementing nonplanar photolithography as a cornerstone of future microfabrication.
Regional Analysis: Leading Markets and Expansion Hotspots
In 2025, the regional landscape for nonplanar photolithography equipment manufacturing is shaped by rapid technological adoption, increased investment, and strategic expansions across key markets. Asia-Pacific continues to dominate as the leading market, driven largely by aggressive semiconductor manufacturing growth in countries such as South Korea, Taiwan, Japan, and increasingly, China. ASML, the preeminent photolithography equipment supplier, maintains significant operational and customer footprints in Taiwan and South Korea, supporting the advanced packaging and 3D device manufacturing needs of semiconductor giants like TSMC and Samsung Electronics. These regions are investing heavily in next-generation lithography, including nonplanar and heterogeneous integration processes, to retain technological leadership.
China is rapidly closing the technology gap through substantial state-backed investments and the emergence of domestic equipment manufacturers. SMIC and local toolmakers are accelerating R&D in nonplanar lithography as part of national efforts to localize semiconductor production and reduce reliance on foreign equipment. In early 2025, multiple new fabrication facilities dedicated to advanced packaging and 3D integration have been announced in key Chinese tech hubs, signaling a likely uptick in demand for nonplanar lithography solutions over the next several years.
In the United States, the CHIPS Act and related incentives are catalyzing onshore semiconductor manufacturing, with a focus on advanced node capabilities and heterogeneously integrated devices. Major toolmakers such as Lam Research and Applied Materials are expanding their U.S. manufacturing capacity and R&D for next-generation lithography, including nonplanar applications. The Southwest and Pacific regions—especially Arizona and California—are emerging as hotspots for both domestic and foreign investment in new fabs incorporating these advanced tools.
Europe remains a vital player, anchored by the Netherlands-based ASML, whose global leadership in lithography equipment is central to the region’s role in the supply chain. European R&D consortia are also targeting nonplanar photolithography for specialized applications in automotive and industrial semiconductors, leveraging support from the European Chips Act.
Looking ahead, the overall outlook points to sustained regional competition and targeted expansion. Asian markets, especially China, are poised for the fastest growth in nonplanar photolithography equipment demand, while the U.S. and Europe focus on technology leadership and supply chain resilience. Strategic partnerships between tool manufacturers, foundries, and regional governments are expected to intensify, shaping the competitive landscape for nonplanar photolithography through the late 2020s.
Manufacturing Challenges: Technical Barriers and Solutions
Nonplanar photolithography equipment manufacturing faces unique technical barriers, particularly as semiconductor and microfabrication industries demand solutions for patterning on curved, flexible, or irregular surfaces. As of 2025, the primary challenges involve precise alignment and focus control, mask deformation, and ensuring uniform exposure across non-flat substrates. Addressing these issues is critical for applications ranging from flexible displays to biomedical devices.
A significant technical barrier remains the development of advanced optical systems capable of dynamic focus adjustment and distortion correction. Conventional photolithography tools, designed for flat wafers, struggle to maintain image fidelity over three-dimensional surfaces. Companies such as Nikon Corporation and Canon Inc. are actively investing in adaptive optics and variable projection systems to overcome these hurdles. For example, adaptive lens elements and real-time feedback mechanisms are being integrated to correct for curvature-induced aberrations during exposure.
Another persistent challenge is the fabrication and handling of conformable masks or reticles. Nonplanar substrates can require flexible or stretchable photomasks that maintain pattern accuracy despite bending or stretching. As of 2025, suppliers like MicroChemicals GmbH are developing novel materials and processes for flexible photomask production, including polymer-based masks and direct-write techniques to bypass traditional mask requirements.
Uniform photoresist coating on non-flat surfaces is another manufacturing bottleneck. Traditional spin coating struggles with inconsistent thickness on nonplanar substrates. In response, equipment manufacturers such as SÜSS MicroTec SE have introduced spray coating and meniscus coating systems that deliver more uniform resist layers over complex geometries. These advances are supported by closed-loop process controls and in-situ metrology.
The outlook for the next few years includes accelerated collaboration between equipment vendors and end-users in fields like flexible electronics and medical sensors. Industry initiatives, such as those led by SEMI, are driving standardization efforts for nonplanar lithography processes. It is anticipated that by the late 2020s, hybrid lithographic platforms—combining projection, direct-write, and maskless strategies—will become increasingly viable for commercial production.
Despite these advancements, cost, yield, and throughput remain concerns. The integration of machine learning for process optimization and adaptive control is expected to further mitigate technical barriers, positioning nonplanar photolithography equipment as a critical enabler for next-generation microfabrication.
Supply Chain and Partnerships: Collaborations Across the Value Chain
The landscape of nonplanar photolithography equipment manufacturing in 2025 is defined by a complex and evolving web of supply chain relationships and strategic partnerships. As semiconductor device architectures grow increasingly three-dimensional and intricate—driven by advanced memory, logic, and packaging demands—the need for robust collaboration across the value chain has become paramount.
Leading equipment providers such as ASML and Canon Inc. have intensified their cooperation with specialty optics suppliers and materials companies to address the unique challenges in processing non-flat surfaces. For example, ASML’s ongoing supply agreements with precision optics manufacturers are crucial for the development of next-generation projection systems capable of conformal patterning. Canon, which has long invested in maskless lithography and nanoimprint technologies, announced in late 2024 expanded partnerships with resist material suppliers to ensure reliable pattern transfer on complex topographies.
Upstream, suppliers of UV light sources, advanced photoresists, and nanoimprint materials—such as Tokyo Ohka Kogyo Co., Ltd. and Dow—are aligning their R&D with equipment manufacturers’ roadmaps. These collaborations aim to optimize material formulations for better adhesion, resolution, and defect control in nonplanar contexts. In early 2025, several suppliers reported joint pilot lines with toolmakers, accelerating feedback cycles and reducing time-to-market for new processes.
At the system integration level, partnerships between equipment vendors and semiconductor foundries, such as TSMC and Samsung Electronics, have deepened. Foundries are increasingly co-developing process flows and tool specifications with lithography equipment manufacturers to enable faster qualification of nonplanar processes for high-volume manufacturing. For instance, in Q1 2025, TSMC confirmed expanded technical exchanges with multiple equipment suppliers to address overlay accuracy and defectivity in 3D device fabrication.
Looking ahead, the next few years are expected to bring further integration of supply chain partners through joint development agreements, shared pilot facilities, and cross-licensing of technology. International consortia and industry groups—such as SEMI—are facilitating pre-competitive collaboration to standardize metrology and process control for nonplanar lithography. Such initiatives are critical for mitigating supply chain risks and ensuring interoperability as nonplanar device architectures become mainstream.
Overall, the competitive and technical challenges of nonplanar photolithography are forging closer, more agile partnerships across the value chain, with 2025 marking a period of intensified collaboration and ecosystem maturity.
Regulatory and Standardization Updates: Compliance Trends
The regulatory landscape for nonplanar photolithography equipment manufacturing is evolving rapidly, driven by the increasing complexity of advanced packaging and heterogeneous integration. As of 2025, regulatory bodies and industry consortia are refining standards to address new challenges in three-dimensional (3D) and curved-surface device fabrication. The International Electrotechnical Commission (IEC) and the Semiconductor Equipment and Materials International (SEMI) continue to play pivotal roles in standardization, updating technical standards to include criteria for alignment, cleanliness, and defect inspection unique to nonplanar surfaces.
SEMI has advanced several standards applicable to nonplanar photolithography, such as SEMI S2 for equipment safety and SEMI E10 on equipment reliability. These standards are being reviewed to ensure they address emerging concerns, including particle contamination and process uniformity on non-flat substrates. The SEMI Advanced Packaging Committee is also examining new guidelines for mask alignment and overlay accuracy for 3D surfaces, with draft revisions expected by late 2025 (SEMI).
On the international front, the IEC Technical Committee 47 (TC 47), focused on semiconductor devices, has initiated working groups to establish test and measurement protocols specific to nonplanar lithography systems. The aim is to harmonize inspection and validation procedures across regions, which is particularly important as supply chains become more globalized (International Electrotechnical Commission).
Environmental and safety compliance remains a top priority. With new photolithography chemistries and exposure sources being introduced for nonplanar processing, manufacturers must comply with evolving regulations on hazardous material handling and emissions. For example, equipment manufacturers such as ASML and Canon Inc. are adapting their processes and documentation to ensure compliance with the European Union’s RoHS (Restriction of Hazardous Substances) and REACH (Registration, Evaluation, Authorization and Restriction of Chemicals) directives as applied to advanced semiconductor equipment.
Looking ahead, regulatory focus is expected to intensify around data integrity (e.g., traceability of process conditions on complex substrates) and cybersecurity, as nonplanar photolithography equipment becomes increasingly networked and integrated with factory automation systems. The SEMI Cybersecurity Initiative is developing best practices that will likely become de facto requirements for equipment suppliers entering the mid-to-late 2020s (SEMI).
As the sector grows, ongoing engagement with standards bodies and proactive compliance strategies will be crucial for equipment manufacturers to ensure market access and operational resilience in the face of tightening global regulations.
Future Outlook: Opportunities, Risks, and Strategic Recommendations
The future outlook for nonplanar photolithography equipment manufacturing in 2025 and the coming years is shaped by rapid technological advancements, evolving applications, and strategic industry shifts. As the demand for complex, three-dimensional microstructures in sectors such as semiconductor packaging, MEMS, optics, and flexible electronics intensifies, manufacturers are increasingly investing in next-generation equipment capable of patterning on non-flat, heterogeneous substrates.
Key players in lithography equipment—such as ASML Holding NV and Canon Inc.—are exploring extensions of their existing planar systems for advanced packaging and heterogeneous integration, recognizing the commercial need for tools that can address nonplanar geometries. Nikon Corporation has also showcased research into 3D patterning technologies, positioning itself to compete in this emerging segment. Meanwhile, specialized firms such as SÜSS MicroTec SE and EV Group are actively developing mask aligners, imprint, and nanoimprint lithography systems, with product lines that explicitly target nonplanar and flexible substrates.
Opportunities abound in the convergence of advanced packaging, where chiplets and multi-die structures require ultra-precise alignment and patterning on uneven surfaces. The expansion of micro-optics and biomedical devices—where curved and flexible substrates are common—further widens the addressable market. The 2025–2027 period is expected to see pilot lines and commercial rollouts for nonplanar photolithography, particularly as semiconductor manufacturers such as Taiwan Semiconductor Manufacturing Company Limited (TSMC) and Intel Corporation explore new device architectures demanding novel lithography solutions.
However, risks persist. The technical complexity of achieving uniform exposure, focus, and resist coating on non-flat surfaces presents significant engineering challenges. Equipment costs are anticipated to be high, potentially limiting adoption to high-value applications in the near term. IP risks and supply chain vulnerabilities, particularly concerning specialized optics and precision motion systems, could also impact timelines and costs.
Strategically, equipment manufacturers should prioritize partnerships with substrate suppliers and device makers to co-develop compatible processes and accelerate technology validation. Investment in modular architectures and software-driven alignment systems will be critical to address diverse substrate topologies and minimize time-to-market. Industry groups such as SEMI and collaborative initiatives involving leading research institutes are expected to play a pivotal role in setting standards and fostering ecosystem development. Overall, while the path to mass adoption remains challenging, near-term demand from niche, high-value applications will drive innovation and incremental revenue in nonplanar photolithography equipment manufacturing.