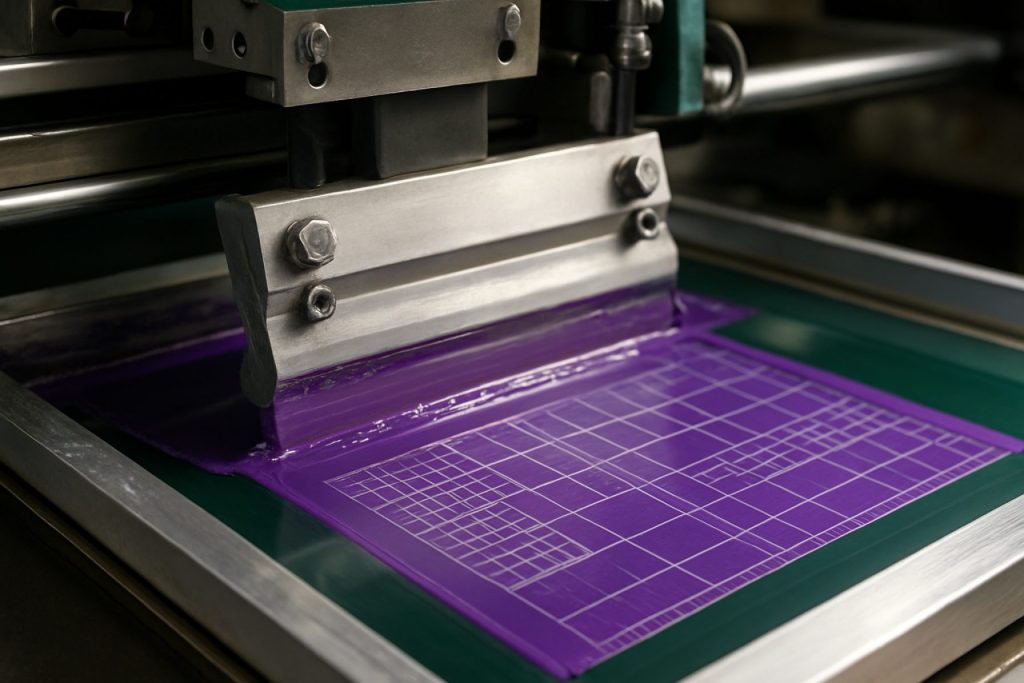
Table of Contents
- Executive Summary: Key Trends Shaping 2025–2030
- Market Forecast: Growth Projections and Regional Hotspots
- Technological Breakthroughs in Calibration Systems
- Automation and AI: The Next Wave in Equipment Calibration
- Leading Manufacturers & Strategic Partnerships (e.g., asml.com, screen.co.jp)
- Regulatory Standards and Quality Assurance Initiatives (e.g., sematech.org)
- Customization, Modularity, and Industry Demands
- Challenges: Downtime, Precision, and Workforce Training
- Sustainability and Energy Efficiency in Calibration Technology
- Future Outlook: What to Expect Through 2030
- Sources & References
Executive Summary: Key Trends Shaping 2025–2030
The silkscreen lithography sector is undergoing significant transformation in equipment calibration, driven by increasing demands for process precision, automation, and sustainability. As of 2025, manufacturers are rapidly advancing calibration methodologies to support shrinking device geometries and higher throughput in industries such as electronics, photovoltaics, and advanced packaging.
A core trend is the integration of smart sensors and closed-loop feedback systems in silkscreen lithography equipment. Companies like Katek SE and ASYS Group are implementing real-time monitoring within screen printers, allowing for automatic compensation of registration and print pressure deviations. This shift is reducing human error, minimizing downtime, and ensuring repeatable calibration across production runs.
Another key development is the adoption of Industry 4.0 principles, notably through remote calibration assistance and predictive maintenance. Equipment suppliers such as MPM Printing Solutions are offering IoT-enabled platforms that deliver data-driven calibration recommendations and alert operators to potential misalignments before they impact yield. This digitalization is projected to accelerate further through 2030, as more manufacturers seek to harness artificial intelligence and machine learning for adaptive calibration routines.
Environmental considerations are also shaping calibration priorities. Companies like SolarWorld in the photovoltaic sector are optimizing calibration for energy efficiency and reduced material waste. Calibration routines are being refined to use less consumable ink and enable tighter registration tolerances, which is particularly valuable for high-density circuit and solar cell manufacturing.
Looking ahead, the outlook for silkscreen lithography equipment calibration includes broader standardization and interoperability efforts, as highlighted by industry groups such as SEMI. Collaborative initiatives are expected to define best practices for calibration processes and data exchange, supporting multisite consistency as global supply chains adapt to shifting market dynamics.
In summary, the 2025–2030 period will see silkscreen lithography equipment calibration become more automated, data-driven, and environmentally conscious. These trends are positioning manufacturers to meet the demands of next-generation electronics and energy applications while improving process reliability and sustainability.
Market Forecast: Growth Projections and Regional Hotspots
The market for silkscreen lithography equipment calibration is poised for notable growth in 2025 and the ensuing years, buoyed by the expanding applications of screen-printed electronics in sectors such as semiconductors, photovoltaics, and advanced displays. As manufacturers pursue finer pattern resolutions and higher process reliability, demand for precise calibration solutions—both hardware and software—continues to intensify.
Globally, the Asia-Pacific region is forecast to remain the dominant hotspot for silkscreen lithography calibration, propelled by robust investments in electronics manufacturing hubs across China, South Korea, Taiwan, and Japan. Leading equipment suppliers such as Tokyo Seimitsu and SCREEN Holdings have reported ongoing initiatives to enhance their calibration service portfolios and digitalize maintenance protocols, aiming to reduce downtime and improve repeatability in high-throughput screen printing lines. For instance, SCREEN Holdings has been expanding its support for automated calibration modules integrated with their precision printing equipment, targeting the smart manufacturing trend prevalent in East Asian factories.
Europe is also emerging as a significant market, driven by the continent’s leadership in printed electronics R&D and its push for sustainable manufacturing. German-based Meyer Burger Technology AG is investing in advanced calibration systems for its photovoltaic cell production lines, emphasizing traceability and data-driven optimization. Simultaneously, MESAGO Messe Frankfurt GmbH, organizer of major electronics manufacturing events, highlights the growing role of process calibration in ensuring consistent quality for automotive and medical device applications.
North America is witnessing steady demand, particularly from specialty electronics and research-focused institutions. Companies like DESCO Industries Inc. are expanding their calibration equipment offerings, responding to the needs of smaller-scale and prototype production environments that require flexibility and comprehensive traceability.
- Market growth is forecast to average 6–8% annually through 2028, underpinned by ongoing digital transformation and automation of calibration processes.
- Key drivers include the proliferation of IoT devices, demand for miniaturized circuitry, and stricter regulatory requirements for process validation and repeatability.
- Emerging regional hotspots include Southeast Asia, where new electronics manufacturing capacity is rapidly coming online, and India, where government initiatives support local production of advanced electronic components.
Looking ahead, the market outlook is characterized by a shift toward AI-powered calibration analytics, remote diagnostics, and cloud-based equipment monitoring, with leading manufacturers and service providers investing in next-generation calibration solutions to support evolving customer requirements worldwide.
Technological Breakthroughs in Calibration Systems
The calibration of silkscreen lithography equipment has entered a period of notable innovation, driven by the demand for higher precision and efficiency in electronics manufacturing processes. As of 2025, leading equipment manufacturers are deploying advanced calibration systems, integrating automation, real-time analytics, and AI-driven adjustment protocols to minimize human error and reduce downtime.
One significant breakthrough is the adoption of closed-loop calibration systems. These systems use integrated sensors and feedback mechanisms to continuously monitor and adjust crucial parameters such as screen alignment, tension, and squeegee pressure during operation. For instance, ASML—while primarily recognized for photolithography—has extended precision calibration protocols to hybrid screen-based equipment, emphasizing real-time overlay accuracy and process repeatability.
Equipment manufacturers such as Murakami Co., Ltd. and Sakurai Graphic Systems Corporation are integrating digital calibration modules within their silkscreen printers. These modules automatically measure screen stretch, frame warp, and off-contact distances, adjusting machine settings to meet tight tolerances required by the latest generation of printed electronics and displays. This shift toward digitalization is reducing manual interventions and is enabling predictive maintenance strategies.
The next few years are expected to see a substantial rollout of AI-enhanced calibration services. For example, Koh Young Technology, a leader in inspection and process control, is developing AI-powered solutions that analyze real-time printing data to predict calibration drift and recommend or execute adjustments automatically. Such advances are critical as feature sizes shrink and uniformity demands become more stringent in sectors like flexible displays and micro-LED fabrication.
Industry organizations including the SEMI (Semiconductor Equipment and Materials International) are also establishing new calibration standards and interoperability protocols. These standards are designed to ensure that equipment from different manufacturers can communicate calibration data, facilitating more integrated and automated production environments.
Looking ahead, the convergence of IoT connectivity, advanced sensors, and machine learning will likely reshape silkscreen lithography calibration. Manufacturers are expected to invest heavily in remote diagnostics and cloud-based calibration management, promoting factory-wide optimization and faster product changeovers. The industry focus is clear: to achieve consistently high yields and throughput by making calibration more intelligent, autonomous, and interconnected across the silkscreen lithography workflow.
Automation and AI: The Next Wave in Equipment Calibration
The calibration of silkscreen lithography equipment is experiencing a significant transformation in 2025, driven by advanced automation and the integration of artificial intelligence (AI) technologies. Historically, calibration processes relied heavily on manual intervention, which was not only time-consuming but also prone to human error. However, recent industry developments indicate a rapid shift toward automated and AI-enabled calibration solutions, reshaping operational efficiency and precision standards across the sector.
Equipment manufacturers are embedding sophisticated sensor arrays and machine learning algorithms into their latest silkscreen lithography platforms, enabling real-time monitoring and dynamic adjustment of critical parameters such as screen alignment, registration accuracy, and ink deposition. For instance, leading firms such as ASML and SCREEN Holdings are incorporating proprietary AI-driven modules that continuously analyze equipment performance, detect drift or deviations, and autonomously execute fine-tuning routines without halting production. This not only minimizes downtime but also ensures consistent product quality, a crucial factor in industries like microelectronics and printed circuit board (PCB) manufacturing.
In parallel, automation providers such as KUKA are collaborating with lithography system manufacturers to deliver robotic solutions that automate the physical aspects of calibration—such as screen replacement, cleaning, and test pattern analysis. This synergy is resulting in “lights-out” calibration environments, where human intervention is limited to supervisory roles, further enhancing throughput and repeatability.
Data from 2025 indicates that facilities adopting AI-based calibration solutions are achieving up to 40% reductions in calibration cycle times and a corresponding drop in calibration-related defects, according to technology deployment updates from SÜSS MicroTec. These improvements are especially pertinent as the industry prepares for the increasing complexity of next-generation substrates and finer feature resolutions in silkscreen lithography.
Looking ahead over the next few years, the outlook is characterized by the proliferation of self-learning calibration systems, capable of adapting to new materials and process recipes autonomously. Industry consortia such as SEMI are actively developing standards for interoperable AI modules, suggesting that cross-platform calibration protocols will soon become mainstream. As a result, manufacturers can expect further reductions in operational costs, improved equipment uptime, and a scalable path toward highly flexible, automated lithography lines.
Leading Manufacturers & Strategic Partnerships (e.g., asml.com, screen.co.jp)
As silkscreen lithography continues to evolve as a critical process in semiconductor and advanced electronics manufacturing, leading equipment manufacturers and their strategic partnerships are shaping the landscape of calibration standards, automation, and digital integration. In 2025, companies such as SCREEN Holdings Co., Ltd. and ASML remain at the forefront, leveraging their global presence and technical expertise to drive innovations in calibration solutions for silkscreen lithography equipment.
SCREEN Holdings, a pioneer in screen printing and imaging technology, has focused on enhancing the precision and repeatability of its lithography systems through advanced calibration modules and software upgrades. Their latest silkscreen printers, widely adopted in the flat panel display and semiconductor sectors, feature automated calibration routines that reduce human intervention and minimize downtime. Strategic collaborations with major semiconductor foundries and display manufacturers have accelerated the rollout of AI-based diagnostics and remote calibration services, addressing the industry’s demand for higher throughput and process stability in 2025 and beyond (SCREEN Holdings Co., Ltd.).
ASML, best known for its photolithography systems, has also expanded its collaborative efforts to encompass hybrid lithography strategies—integrating silkscreen technologies in advanced packaging and compound semiconductor fabrication. Through partnerships with leading materials suppliers and precision equipment firms, ASML is developing calibration protocols that ensure process compatibility and traceability across multi-step lithographic processes. Their commitment to open innovation is reflected in joint development agreements with equipment calibration specialists, focusing on real-time sensor integration, machine learning for drift correction, and cross-platform calibration standardization (ASML).
- Strategic Alliances: In 2025, cross-industry partnerships are intensifying. For example, SCREEN Holdings and Tokyo Ohka Kogyo Co., Ltd. are collaborating on photoresist and screen printing materials, optimizing calibration parameters for emerging applications in flexible and mini-LED displays.
- Automated Calibration Ecosystems: Equipment manufacturers are partnering with automation leaders such as Yaskawa Electric Corporation to deliver robotic calibration and in-line metrology solutions, further reducing process variability and enabling predictive maintenance capabilities.
Looking ahead, continued investment in calibration automation, machine learning integration, and open-standards development is expected to further enhance equipment reliability and process yield. Strategic partnerships among leading manufacturers, materials suppliers, and automation specialists will be pivotal in meeting the stringent requirements of next-generation semiconductor and display manufacturing through 2025 and into the late 2020s.
Regulatory Standards and Quality Assurance Initiatives (e.g., sematech.org)
In 2025, the calibration of silkscreen lithography equipment is increasingly governed by stringent regulatory standards and quality assurance initiatives, reflecting the elevated demand for precision and repeatability in semiconductor and electronics manufacturing. Regulatory bodies and industry consortia have intensified their focus on harmonizing calibration protocols to minimize variability and ensure compatibility across global supply chains.
One of the most prominent efforts comes from SEMI (Semiconductor Equipment and Materials International), which, in collaboration with industry stakeholders, continues to update its SEMI Standards for lithography and screen printing equipment. The SEMI E10 and E79 standards specify requirements for equipment reliability, maintainability, and calibration, directly impacting silkscreen lithography operations. In 2025, SEMI has initiated working groups to address emerging challenges in the calibration of hybrid lithography systems—combining screen printing with photolithographic processes—ensuring that equipment adheres to more rigorous metrological benchmarks.
At the manufacturer level, companies like ASML and SCREEN Holdings Co., Ltd. have bolstered their quality assurance frameworks by integrating advanced diagnostic modules and automated calibration routines in their latest silkscreen lithography equipment. These initiatives are designed to comply with both SEMI standards and region-specific requirements, such as the European Union’s CE marking and the U.S. FDA’s 21 CFR Part 11 for traceability in medical and microelectronic device production.
Suppliers of calibration instruments, such as Keysight Technologies, are also responding to regulatory pressures by releasing toolkits specifically tailored for lithography process control. In 2025, these toolkits feature enhanced traceability, digital certification, and remote validation capabilities, aligning with ISO/IEC 17025 accreditation requirements commonly mandated by OEMs and contract manufacturers.
Looking ahead to the next few years, industry-wide adoption of digital twin technology and AI-driven predictive maintenance is expected to further embed calibration processes within holistic quality management systems. Regulatory agencies and standards bodies are anticipated to mandate real-time calibration verification and data logging, ensuring continuous compliance and rapid response to process deviations. Initiatives such as SEMI’s Smart Manufacturing efforts and the collaborative “International Roadmap for Devices and Systems” are likely to define the next generation of calibration protocols, reinforcing the role of quality assurance as a cornerstone of silkscreen lithography equipment performance and reliability.
Customization, Modularity, and Industry Demands
The silkscreen lithography sector in 2025 is marked by a rapidly evolving landscape of customization and modularity in equipment calibration, driven by escalating industry demands for precision, throughput, and adaptability. As printed electronics, advanced displays, and microfabrication industries continue to diversify their product offerings, calibration solutions are expected to become increasingly tailored to specific production workflows and substrate requirements.
Leading equipment manufacturers are responding to this trend by offering modular calibration systems that allow users to adapt silkscreen lithography machines for different applications and print resolutions. For instance, ASYS Group and SMT Maschinen- und Vertriebs GmbH & Co. KG have integrated software-driven calibration modules into their platforms, enabling real-time adjustment and compensation for environmental factors such as temperature or humidity. This modularity ensures consistent print quality, reduces downtime for recalibration, and supports faster changeovers between product lines.
Customization is also increasingly prevalent in automated diagnostic and alignment features. Manufacturers like Meyer Burger Technology AG are embedding smart sensors and closed-loop feedback systems into silkscreen lithography equipment. These enhancements facilitate automatic registration and stencil alignment, allowing for precise layer stacking and defect minimization—an essential requirement for sectors like photovoltaics and microelectronics, where tolerances are exceptionally tight.
Industry associations, such as SEMI, are actively collaborating with equipment suppliers to standardize calibration protocols and data exchange formats. This initiative is expected to accelerate interoperability between modular components and streamline qualification processes across global manufacturing sites.
Looking ahead, the outlook for silkscreen lithography equipment calibration is strongly influenced by digital transformation and the adoption of Industry 4.0 principles. Adaptive calibration routines powered by machine learning and artificial intelligence are being developed to predict calibration drift and schedule proactive maintenance. Companies like EKRA Automatisierungssysteme GmbH are investing in cloud-based monitoring platforms that provide remote diagnostics and calibration analytics, catering to the growing demand for predictive maintenance and operational transparency.
In summary, the silkscreen lithography market in 2025 and the near future is characterized by heightened modularity and customization in calibration systems. This evolution is intimately tied to rising industry demands for flexibility, accuracy, and data-driven manufacturing, positioning the sector for continued innovation and responsiveness to emerging application needs.
Challenges: Downtime, Precision, and Workforce Training
Silkscreen lithography remains a cornerstone in printed electronics and advanced manufacturing, but the calibration of its equipment faces persistent and evolving challenges as of 2025. The sector is under pressure to optimize uptime, enhance precision, and address a growing skills gap, all while adapting to rapid technological change.
One of the foremost issues is downtime linked to calibration routines. As screen printing systems become more automated and integrated with Industry 4.0 protocols, unexpected calibration drift can lead to significant production halts. This is particularly critical in automotive and display applications, where even minor misalignments can trigger batch-wide defects. Manufacturers such as MINO Group and SPS Technoscreen have responded by embedding predictive maintenance features and auto-calibration systems into their high-end presses, aiming to reduce mean time to repair (MTTR) and pre-empt unplanned stoppages.
The challenge of maintaining precision at micron-scale tolerances is intensifying with the demand for finer features in touch panels, PCBs, and biosensors. Calibration must now accommodate advanced substrate materials and variable ink rheologies, which can shift due to environmental factors. Equipment suppliers like ASYS Group have introduced closed-loop feedback and vision-based alignment modules to improve repeatability, but in-line process verification remains complex. Ensuring traceable calibration standards across global manufacturing sites is an ongoing concern, particularly as OEMs push for zero-defect initiatives.
Workforce training emerges as a parallel challenge. The sophistication of modern silkscreen lithography systems requires technicians with hybrid skills in mechatronics, automation, and quality control. However, the industry faces an aging workforce and a shortage of new entrants familiar with both legacy and digital calibration protocols. Equipment makers, such as MINO Group, are expanding technical training programs and remote support services, but uptake varies by region and market segment. The lack of highly trained staff can exacerbate calibration errors and prolong downtime, impacting overall throughput.
Looking ahead, leading manufacturers are pursuing further automation, AI-driven diagnostics, and digital twins to manage calibration complexity. Over the next few years, the focus will be on minimizing human intervention, enhancing traceability, and supporting real-time calibration analytics. However, these advances will require coordinated investment in both technology and workforce development to realize their full potential across the silkscreen lithography value chain.
Sustainability and Energy Efficiency in Calibration Technology
As the semiconductor and advanced electronics sectors move towards heightened sustainability goals in 2025, silkscreen lithography equipment calibration is undergoing significant evolution. New regulations and corporate ambitions for net-zero manufacturing are directly impacting the calibration process, pushing for both energy efficiency and reduced environmental impact. Key industry players are embedding advanced technologies—such as automated calibration systems and AI-driven analytics—into their silkscreen lithography lines to minimize waste and energy consumption.
Among the noteworthy developments, companies like ASML and SCREEN Holdings have announced investments in smart calibration routines. These innovations enable equipment to self-monitor and adjust calibration parameters in real time, reducing the need for repeated manual intervention and therefore cutting down on both material waste and energy use. For instance, SCREEN Holdings’ latest silkscreen printers feature closed-loop calibration mechanisms that optimize ink deposition and curing energy use, contributing to both process stability and sustainability targets.
Integration of digital twins and IoT connectivity in calibration technology is gaining traction. SEMI (the global industry association serving the electronics manufacturing supply chain) highlights that digital twins can simulate the calibration process, allowing for predictive maintenance and more accurate alignment while minimizing line downtime and associated resource consumption. This digital-first approach is projected to reduce energy usage during calibration by up to 15% over traditional methods by 2027, according to ongoing industry trials.
Another focus is the use of eco-friendly calibration consumables. Leading suppliers are transitioning to non-toxic, recyclable calibration inks and substrates, lowering the lifecycle environmental footprint of the calibration process. TOKYO OHKA KOGYO has introduced water-based calibration solutions that are both effective and compliant with stringent emissions regulations, addressing the dual challenge of performance and sustainability.
Looking forward, the industry outlook indicates further integration of renewable energy sources to power calibration equipment and the adoption of circular economy principles in equipment lifecycle management. Equipment manufacturers are collaborating with semiconductor fabs and environmental bodies to set new benchmarks for sustainable calibration practices by 2030, aiming to align with global sustainability frameworks such as those set by the Science Based Targets initiative. The ongoing advancements suggest that silkscreen lithography calibration will continue to be a lever for both operational excellence and environmental stewardship in the coming years.
Future Outlook: What to Expect Through 2030
Looking ahead to 2030, the calibration of silkscreen lithography equipment is poised for significant advancements, driven by the demand for higher throughput, tighter tolerances, and the ongoing miniaturization of electronic components. As the electronics and semiconductor industries strive for enhanced yield and reliability, equipment calibration will remain a crucial focus, with new technologies and standards shaping future practices.
In 2025, leading equipment manufacturers are already integrating advanced automation and AI-driven calibration routines into their silkscreen lithography systems. For example, ASMPT and Mycronic have begun implementing self-diagnostic features and predictive maintenance algorithms that continuously monitor and adjust the alignment, pressure, and screen wear of their printers. This transition from manual to automated calibration is expected to accelerate, reducing human error and downtime while improving repeatability.
Another key development through 2030 will be the adoption of Industry 4.0 principles. Equipment from manufacturers such as Speedline Technologies is increasingly designed for connectivity, allowing calibration data to be collected, analyzed, and acted upon in real time across entire production lines. This connectivity enhances traceability, enables remote diagnostics, and supports faster responses to process drift or deviations, thus maintaining high-quality output and compliance with industry standards.
The proliferation of new materials—such as flexible substrates and advanced solder pastes—will necessitate more sophisticated calibration protocols. As product geometries grow ever finer, calibration systems must deliver micron-level precision. Companies like DEK (a division of ASMPT) are developing closed-loop feedback systems that automatically compensate for substrate warpage, environmental fluctuations, and tool wear, ensuring consistent print quality even on challenging assemblies.
By 2030, it is anticipated that calibration processes will be increasingly predictive and adaptive, utilizing machine learning algorithms trained on large datasets gathered from global equipment fleets. This will empower manufacturers to anticipate maintenance needs, optimize process parameters dynamically, and extend equipment lifespan. Standardization efforts led by organizations such as SEMI are also likely to yield new guidelines for calibration intervals, documentation, and verification, further enhancing best practices and interoperability.
In summary, the next five years will see silkscreen lithography equipment calibration become more intelligent, automated, and integrated—forming a foundation for the high-yield, high-mix manufacturing environments expected by 2030.
Sources & References
- ASYS Group
- SCREEN Holdings
- Meyer Burger Technology AG
- MESAGO Messe Frankfurt GmbH
- DESCO Industries Inc.
- ASML
- Murakami Co., Ltd.
- Sakurai Graphic Systems Corporation
- Koh Young Technology
- KUKA
- SÜSS MicroTec
- Tokyo Ohka Kogyo Co., Ltd.
- Yaskawa Electric Corporation
- EKRA Automatisierungssysteme GmbH
- SPS Technoscreen
- SEMI
- ASMPT
- Mycronic