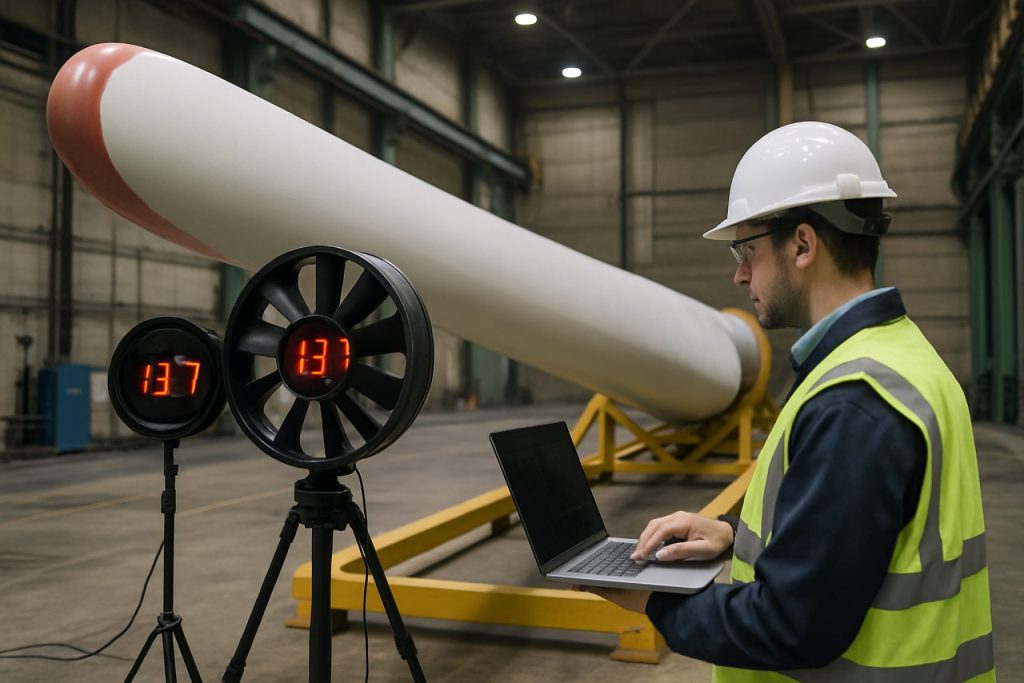
Table of Contents
- Executive Summary: Key Trends in Downscaled Blade Testing (2025–2030)
- Driving Forces: Why the Industry is Shifting to Downscaled Testing
- Core Technologies: Innovations in Downscaled Blade Testing Equipment
- Major Industry Players and Their 2025 R&D Initiatives
- Cost Savings and ROI: Comparative Analysis vs. Full-Scale Testing
- Market Forecast: Growth Projections Through 2030
- Challenges and Limitations: Accuracy, Scaling, and Regulatory Hurdles
- Case Studies: Real-World Applications from Leading Manufacturers
- Emerging Standards and Certification Pathways
- Future Outlook: Next-Gen Materials, AI Integration, and Global Expansion
- Sources & References
Executive Summary: Key Trends in Downscaled Blade Testing (2025–2030)
Downscaled wind turbine blade testing is set to play an increasingly pivotal role in the wind energy sector between 2025 and 2030. As the industry intensifies its drive toward larger, more efficient turbines, the necessity to validate new blade designs while managing costs and reducing development cycles is more pronounced than ever. Downscaled testing—using smaller, geometrically representative blade sections—offers a practical solution for early-stage validation of structural and aerodynamic performance.
Recent years have seen a surge in investment and collaboration focused on advanced downscaled testing methodologies. Major blade manufacturers and research institutes are expanding their capabilities, leveraging digital twins, high-fidelity simulation, and smart sensor integration to bridge the gap between small-scale and full-scale results. Companies such as Vestas and Siemens Gamesa Renewable Energy have emphasized the role of scaled testing in their R&D pipelines, particularly as blade lengths approach and exceed 100 meters. This approach accelerates design iteration while controlling costs compared to full-scale prototype fabrication and destructive testing.
Testing centers, including facilities operated by organizations like National Renewable Energy Laboratory (NREL), continue to develop standardized protocols and share best practices, aiming to ensure that downscaled results are both reliable and translatable to commercial-scale blades. The use of advanced composite materials and novel blade architectures—such as segmented and recyclable blades—further underscores the importance of robust downscaled testing regimens.
Key trends for 2025–2030 include:
- Greater adoption of automated and digitalized test setups, reducing manual intervention and improving data accuracy.
- Integration of machine learning and predictive analytics to correlate downscaled test data with full-scale blade performance, expediting certification processes.
- Collaboration between OEMs, academic research centers, and standards bodies to harmonize test methods and validation protocols internationally.
- Expansion of modular test rigs and multi-axis loading platforms, allowing realistic simulation of complex in-service loads on downscaled blades.
- Continued focus on sustainability, using downscaled testing to rapidly vet new eco-friendly materials and recyclable blade designs before scale-up.
Looking forward, downscaled blade testing is expected to remain a mainstay of the innovation pipeline for wind turbine technology. As digital and physical test environments become more integrated and sophisticated, the sector will benefit from faster, more cost-effective development cycles—ultimately supporting the deployment of next-generation turbines and the global push for renewable energy expansion.
Driving Forces: Why the Industry is Shifting to Downscaled Testing
The wind energy sector is experiencing a dynamic transformation in testing methodologies, with downscaled wind turbine blade testing gaining significant traction as of 2025. This shift is directly influenced by several converging industry drivers, including escalating blade sizes, cost pressures, and the urgent need for accelerated innovation cycles.
Firstly, the dramatic increase in blade dimensions—some now exceeding 100 meters—has made full-scale physical testing increasingly complex and expensive. Full-scale static and fatigue tests demand vast infrastructure, specialized logistics, and extended lead times. As blade manufacturers strive to push aerodynamic and structural limits, these requirements have become a major bottleneck. Downscaled testing addresses these constraints by enabling the evaluation of new designs, materials, and manufacturing techniques on smaller, more manageable specimens, reducing both time and resource consumption.
Financial considerations are another powerful driver. The cost of full-scale blade prototypes, combined with the expense of building and operating large-scale test rigs, can represent a substantial portion of development budgets. Downscaled testing enables manufacturers to screen multiple design iterations and material combinations before committing to full-scale prototypes, substantially lowering overall R&D expenditures. This approach is increasingly embraced by leading sector players like Vestas and Siemens Gamesa Renewable Energy, who are both investing in advanced laboratory-scale test systems to optimize blade development pipelines.
Regulatory and certification pressures are also shaping the trend. As international standards evolve to accommodate the unique challenges of next-generation blades, certification bodies and industry groups recognize the value of validated downscaled models in de-risking full-scale certification. Institutions such as DNV and International Energy Agency (IEA) are increasingly collaborating with manufacturers to develop test protocols that bridge laboratory and field performance, expediting the route to market for novel designs.
Digitalization further amplifies the utility of downscaled testing. Advanced simulation tools, data analytics, and digital twins allow for the integration of downscaled empirical data with virtual models, enhancing predictive accuracy for full-scale performance. This symbiotic approach is expected to underpin the next wave of blade innovation, as companies leverage both physical and digital validation loops.
Looking ahead, the industry’s adoption of downscaled wind turbine blade testing is set to accelerate through 2025 and beyond. As blades continue to grow in size and complexity, and as the competitive and regulatory landscape intensifies, downscaled methodologies will be pivotal in enabling faster, more cost-effective, and reliable development of the wind turbine blades powering the energy transition.
Core Technologies: Innovations in Downscaled Blade Testing Equipment
Downscaled wind turbine blade testing has gained significant momentum in recent years, driven by the need to accelerate innovation, reduce prototyping costs, and enable rapid validation of advanced materials and aerodynamic concepts. As the industry moves into 2025, core technologies underpinning downscaled blade testing equipment are undergoing notable advancements, with a clear focus on precision, scalability, and digital integration.
A major innovation involves the use of advanced sensor arrays and data acquisition systems embedded within test rigs for small-scale blades. Leading manufacturers such as Siemens Gamesa and Vestas have developed proprietary sensor suites that enable real-time measurement of strain, vibration, and deflection on downscaled blade models. These sensors interface with cloud-based analytics platforms, providing engineers immediate feedback for iterative design improvements.
Test rigs themselves have become more modular and automated. Companies like GE Vernova are implementing robotic actuation systems capable of simulating complex, multi-axis loading scenarios on smaller blades. This allows for highly realistic fatigue and ultimate strength testing, mirroring full-scale operational conditions but at a fraction of the cost and time. Moreover, recent developments in additive manufacturing are enabling the rapid prototyping of intricate blade geometries that can be quickly mounted to these test platforms, further accelerating R&D cycles.
Digital twins, another transformative technology, are being tightly integrated into downscaled blade testing. By coupling physical tests with high-fidelity simulation environments, organizations such as DNV can validate computational models against physical results, continuously refining both the digital and physical prototypes. This approach is especially valuable for extrapolating test findings from scaled models to predict full-scale performance with higher confidence.
Looking ahead to the next few years, the outlook for downscaled blade testing equipment is shaped by increasing industry collaboration. Shared test facilities, such as those operated by Fraunhofer, are making advanced, standardized test platforms accessible to a wider range of innovators, including startups and universities. This democratization of high-precision testing is expected to foster a broader pipeline of blade design concepts, with faster paths to commercialization.
In sum, the convergence of embedded sensing, robotics, digital twin integration, and shared infrastructure is defining the next generation of downscaled wind turbine blade testing equipment in 2025 and beyond. These core innovations are poised to accelerate development cycles, enhance data quality, and lower the barriers for entry, ultimately supporting the advancement of more efficient and reliable wind turbine technologies.
Major Industry Players and Their 2025 R&D Initiatives
In 2025, the field of downscaled wind turbine blade testing is marked by significant research and development initiatives led by foremost wind energy manufacturers and technology providers. These efforts are driven by the imperative to accelerate prototype validation, reduce costs, and support the rapid iteration demanded by next-generation blade designs. Major players are leveraging small-scale and sub-component testing to complement or partially replace full-scale blade trials, which remain time-consuming and expensive.
A key initiative comes from Vestas Wind Systems, which continues to invest in advanced laboratory capabilities for downscaled blade testing. Vestas’ R&D focuses on combining physical testing of scaled blades with sophisticated digital twins and simulation environments, enabling rapid feedback for material innovations and structural enhancements. In 2025, Vestas is expanding its partnerships with academic institutions and materials suppliers to refine scaling laws and ensure laboratory results accurately predict full-scale performance.
Similarly, Siemens Gamesa Renewable Energy has announced the expansion of its blade test facilities to include comprehensive sub-component and downscaled blade test rigs. The company’s 2025 strategy emphasizes modular test setups that allow for quick configuration changes, facilitating faster validation of new aeroelastic concepts and manufacturing techniques. Siemens Gamesa is also integrating real-time sensor technologies and advanced data analytics to enhance the predictive value of scaled tests.
Leading blade manufacturer LM Wind Power, a GE Renewable Energy business, is directing 2025 R&D budgets toward automating downscaled test processes and improving the fidelity of correlation between scaled and full-scale results. LM Wind Power’s research teams are particularly focused on fatigue testing and damage progression monitoring, utilizing high-resolution imaging and non-destructive evaluation tools within their scaled test programs.
On the institutional front, organizations like the DNV and the National Renewable Energy Laboratory are expanding collaborative frameworks with industry for standardized protocols in downscaled blade testing. In 2025, these bodies are prioritizing the harmonization of test methods and data sharing to accelerate certification processes and support the commercialization of innovative blade designs.
Looking ahead, industry consensus suggests that R&D investments in downscaled blade testing will continue to grow through the next few years, driven by the push for larger, more efficient turbine designs and increasing pressure to shorten development cycles. The integration of digital tools, improved scaling methodologies, and collaborative industry-academic initiatives are expected to define the outlook for downscaled wind turbine blade testing across the sector.
Cost Savings and ROI: Comparative Analysis vs. Full-Scale Testing
Downscaled wind turbine blade testing is gaining significant traction in 2025 as a cost-effective alternative to traditional full-scale blade testing. The high capital investment, logistical complexity, and time requirements associated with full-scale testing have driven research institutions, manufacturers, and certification bodies to adopt downscaled approaches, particularly for early-stage design validation and material research. The comparative cost savings and return on investment (ROI) offered by downscaled testing are now well recognized within the industry.
Full-scale blade testing, mandated for certification and validation by standards such as those outlined by the DNV and IEC, involves substantial infrastructure—large test rigs, heavy lifting equipment, and specialized facilities. These requirements drive up costs significantly, often exceeding several million dollars for each prototype tested. Moreover, the increasing length and complexity of modern blades (with some exceeding 100 meters) further amplify these expenses, as highlighted by leading manufacturers such as Vestas and Siemens Gamesa Renewable Energy.
By contrast, downscaled blade testing enables multiple design iterations at a fraction of the cost. Recent years have seen test centers and research organizations, including collaborative efforts from companies like GE Renewable Energy and academic institutions, demonstrate that subscale models can accurately predict full-scale behavior when advanced similitude techniques and digital modeling are applied. The direct cost savings are estimated at 60–80% compared to full-scale test campaigns, particularly when factoring in reduced material usage, smaller test benches, and lower transport and handling costs. The ability to conduct parallel tests and rapidly iterate designs shortens development cycles, resulting in faster time-to-market and improved ROI.
Looking ahead, the outlook for downscaled blade testing remains positive. With the growing adoption of digital twins, enhanced simulation tools, and improved physical modeling, the reliability and acceptance of downscaled results continue to improve. Industry bodies, including IEC working groups, are actively evaluating frameworks for integrating downscaled testing into certification pathways, which would further increase its economic attractiveness. As turbine manufacturers face market pressures to innovate while maintaining profitability, downscaled testing is poised to play a central role in cost management and design optimization across the wind energy sector.
Market Forecast: Growth Projections Through 2030
The global market for downscaled wind turbine blade testing is poised for notable growth through 2030, driven by advancing wind turbine designs, the need for rapid prototyping, and the rising emphasis on cost-efficient validation processes. In 2025, key industry stakeholders are expected to increase investments in scaled testing facilities as the sector faces mounting pressure to accelerate product development cycles and ensure reliable blade performance.
Downscaled blade testing, which involves the use of smaller-scale models to replicate the structural and aerodynamic behavior of full-sized blades, is increasingly being adopted as a complement to full-scale testing. This approach offers significant cost and time savings while supporting the validation of novel materials and designs before scaling up to commercial prototypes. According to leading blade manufacturers such as GE Vernova and Siemens Gamesa Renewable Energy, the demand for more flexible and iterative testing methods is expected to intensify as blade lengths surpass 100 meters and offshore projects move into deeper waters.
By 2025, several new and upgraded downscaled blade testing facilities are anticipated to come online in Europe, North America, and Asia-Pacific. Organizations such as DNV and Fraunhofer are expanding their collaborative research and offering industry partners access to advanced scaled testing infrastructure. The proliferation of modular, digitally monitored rigs is enabling more precise data collection and simulation validation, accelerating feedback loops between design and testing teams.
Market forecasts indicate that the adoption of downscaled testing will accelerate particularly in regions where wind energy deployment targets are ambitious and local content requirements favor domestic blade development. For example, in China and the U.S., policy-driven expansion of both onshore and offshore wind installations is prompting local blade manufacturers to invest in scalable and rapid testing capabilities. The European Union’s focus on innovation and sustainability, as reflected in various Horizon Europe initiatives, further supports the integration of downscaled testing into standard industry practice.
Looking ahead to 2030, industry experts foresee downscaled wind turbine blade testing becoming a standard element of the blade certification process, with digitalization and automation enhancing its value proposition. As the global wind industry continues to scale up, the market for downscaled testing is projected to grow at a steady pace, supported by ongoing collaboration among OEMs, research institutes, and certification bodies such as DNV and TÜV SÜD. Overall, the next five years will likely see a shift from niche research applications to mainstream adoption, underpinning the next generation of wind turbine innovation.
Challenges and Limitations: Accuracy, Scaling, and Regulatory Hurdles
Downscaled wind turbine blade testing has emerged as a valuable approach for accelerating blade design validation and innovation, yet it faces notable challenges and limitations related to accuracy, physical scaling, and regulatory acceptance. As of 2025, the industry’s increased focus on larger, more complex rotors has intensified scrutiny on the reliability of results derived from sub-scale models, especially as these findings are used to support certification and commercial deployment.
One of the foremost challenges is the accuracy of downscaled tests in representing the true structural and aerodynamic behavior of full-scale blades. Physical scaling laws, such as those described by similitude theory, dictate that geometric, kinematic, and dynamic similarities must be maintained between the model and prototype. However, perfectly replicating material properties, load distributions, and failure modes at a reduced scale is often infeasible. For example, material anisotropy and manufacturing defects may have disproportionate effects on smaller specimens, potentially leading to non-representative failure mechanisms. These discrepancies are being actively studied by blade manufacturers and research organizations, but solutions remain limited and are often case-specific.
Another significant limitation is the challenge of simulating real-world environmental conditions—such as temperature fluctuations, moisture ingress, and complex loading sequences—on downscaled blades. Full-scale test facilities, such as those operated by Vestas and GE Vernova, can subject prototype blades to multi-axial static and fatigue loads that closely mirror operational stresses. In contrast, downscaled tests may be constrained by the capabilities of laboratory equipment and the simplified assumptions inherent in their designs, sometimes resulting in testing protocols that lack the fidelity required for rigorous certification.
The regulatory landscape introduces additional hurdles. Certification agencies, including those referenced by DNV, have historically required full-scale testing to demonstrate compliance with international standards (such as IEC 61400-23). While there is growing recognition of the role of downscaled testing in early-stage R&D and as a supplement to digital models, current certification pathways rarely accept downscaled physical tests as a substitute for full-scale validation. This regulatory conservatism stems from concerns over scaling-induced inaccuracies and the lack of standardized methodologies for extrapolating sub-scale results to commercial turbines.
Looking to the next few years, industry stakeholders are working to address these gaps through collaborative research, improved scaling techniques, and the integration of advanced digital twins. However, until consensus is reached among OEMs, research institutions, and certifying bodies, downscaled wind turbine blade testing will remain primarily a research and development tool, rather than a direct enabler of commercial certification.
Case Studies: Real-World Applications from Leading Manufacturers
In 2025, downscaled wind turbine blade testing is increasingly recognized by leading manufacturers as an essential step in accelerating innovation and reducing costs within the wind energy sector. This approach involves constructing and testing scaled-down replicas of full-size blades to simulate mechanical, aerodynamic, and material behaviors under controlled laboratory conditions. By leveraging these methods, manufacturers can generate rapid data feedback, refine digital models, and validate new concepts before committing to the expense and complexity of full-scale prototyping.
A prominent case is Vestas, which continues to integrate downscaled blade testing in its innovation pipeline. In recent years, the company has used subscale blade sections to validate new composite materials and aerodynamic features, directly influencing the development of their next-generation turbine platforms. The iterative testing of scaled prototypes has enabled Vestas engineers to identify structural optimizations that translate into lighter, more resilient full-scale blades, supporting their push toward longer rotors and higher capacity factors.
Similarly, Siemens Gamesa Renewable Energy has deployed downscaled blade testing as part of its advanced research and development. In 2024, the company revealed that smaller blade models were instrumental in the design of its latest offshore turbines, particularly for validating load response and fatigue performance of new blade geometries. By integrating lessons learned from these scaled tests, Siemens Gamesa accelerated the certification process for its large-format blades while minimizing risk and prototype costs.
Academic and industry collaborations are also on the rise, exemplified by partnerships between companies such as GE Vernova and leading technical universities. GE Vernova has supported multi-year research projects with institutions like DTU Wind Energy, utilizing downscaled blade testing to investigate advanced sensor integration and digital twin validation. These collaborations are feeding into GE’s ongoing efforts to deploy ever-larger blades, with the subscale approach proving vital for de-risking bold design choices in the pre-commercial phase.
Looking ahead, the adoption of downscaled blade testing is expected to deepen as the wind industry pursues efficiency and sustainability. Automation, improved scaling laws, and advanced material characterization will further enhance the fidelity of these tests. Manufacturers are likely to expand their use of hybrid physical-digital testing environments, combining subscale experiments with high-resolution simulation. This trend positions downscaled blade testing as a cornerstone of the sector’s innovation toolkit for the remainder of the decade and beyond.
Emerging Standards and Certification Pathways
Downscaled wind turbine blade testing is gaining prominence as the wind energy sector pursues faster, more cost-effective innovation cycles. As of 2025, the emergence of new standards and certification pathways is closely tied to the increased use of scaled-down prototypes for both academic research and industrial pre-certification procedures. Key industry players and standards organizations are focusing on aligning testing protocols for downscaled models with those used in full-scale blade certification, ensuring that results are both reliable and transferable.
The DNV certification body has been instrumental in revising guidelines and technical references to incorporate methodologies for downscaled blade testing, especially in the context of design validation and material qualification. DNV’s updates reflect ongoing industry feedback and the necessity to accommodate rapid design iteration, particularly as next-generation blades incorporate novel materials and advanced aerodynamic profiles.
Meanwhile, the International Energy Agency (IEA) Wind Technology Collaboration Programme continues to serve as a platform for multinational cooperation, where working groups are actively discussing harmonized test procedures for downscaled blades. These efforts are expected to culminate in updated recommendations and best practices by 2026, focusing on areas such as similitude requirements, geometric scaling, and load application methods to ensure that test data remains predictive of full-scale performance. The IEA Wind TCP’s task groups are also considering digital twin integration for scaled testing, which is likely to become a certification requirement in the near future.
Blade manufacturers such as GE Vernova and Siemens Gamesa Renewable Energy are increasingly collaborating with accredited test facilities to implement downscaled testing early in the R&D cycle. These companies are not only validating structural integrity and fatigue performance of new blade designs but are also working with standards organizations to ensure that emerging guidelines reflect practical manufacturing and operational realities.
Looking ahead, the sector anticipates that, by 2027, formalized certification pathways for downscaled blade testing will be referenced in procurement specifications and regulatory submissions. This transition will further legitimize scaled testing as a mainstream part of the wind turbine development process, reduce lead times to certification, and support the rapid deployment of innovative blade technologies. The continued evolution of standards, driven by collaboration among manufacturers, certifiers, and research bodies, will be critical to maintaining safety and performance as turbines grow in size and complexity.
Future Outlook: Next-Gen Materials, AI Integration, and Global Expansion
The future of downscaled wind turbine blade testing is being shaped by a combination of advanced materials research, integration of artificial intelligence (AI), and the broadening of global test infrastructure. Looking into 2025 and the immediate years ahead, these trends are expected to drive significant innovations and efficiency gains in both design validation and commercialization cycles for wind turbine blades.
One of the most notable developments is the increasing adoption of next-generation composite materials in blade prototypes, such as carbon fiber-reinforced polymers and hybrid laminates. These materials not only promise higher strength-to-weight ratios but also introduce new failure modes and complex behaviors that must be characterized at scale. Downscaled testing facilities are therefore evolving to accommodate these advanced materials, allowing for rapid iteration before full-scale manufacturing. Major turbine manufacturers and blade suppliers, including Siemens Gamesa Renewable Energy and Vestas Wind Systems, have signaled ongoing investments in material R&D and small-scale validation as part of their strategy to deliver larger, lighter, and more durable blades.
Simultaneously, AI and machine learning tools are being integrated into downscaled testing environments to accelerate data analysis, predictive modeling, and anomaly detection. These technologies enable real-time monitoring of stress, fatigue, and vibration in test blades, and are expected to significantly reduce the time from prototype to certification. Organizations such as National Renewable Energy Laboratory (NREL) are pioneering digital twin approaches, which rely on AI-enhanced simulations validated by physical downscaled tests. This convergence of digital and physical methodologies is projected to become industry standard by the late 2020s, streamlining the optimization of blade designs prior to full-scale trials.
On the global stage, the expansion of dedicated test centers and collaborative research hubs is fostering broader access to downscaled blade testing. Emerging markets in Asia and Latin America are ramping up investment in such infrastructure to support local wind energy growth and reduce reliance on overseas certification. For example, Xinjiang Goldwind Science & Technology in China and GE Renewable Energy are actively developing new testing capabilities aligned with international standards, enabling more rapid regional deployment of innovative blade technologies.
Altogether, the near future for downscaled wind turbine blade testing is defined by the intersection of advanced materials science, digital intelligence, and global collaboration. These factors are poised to reduce development costs, enhance reliability, and accelerate the scaling of next-generation wind power worldwide.