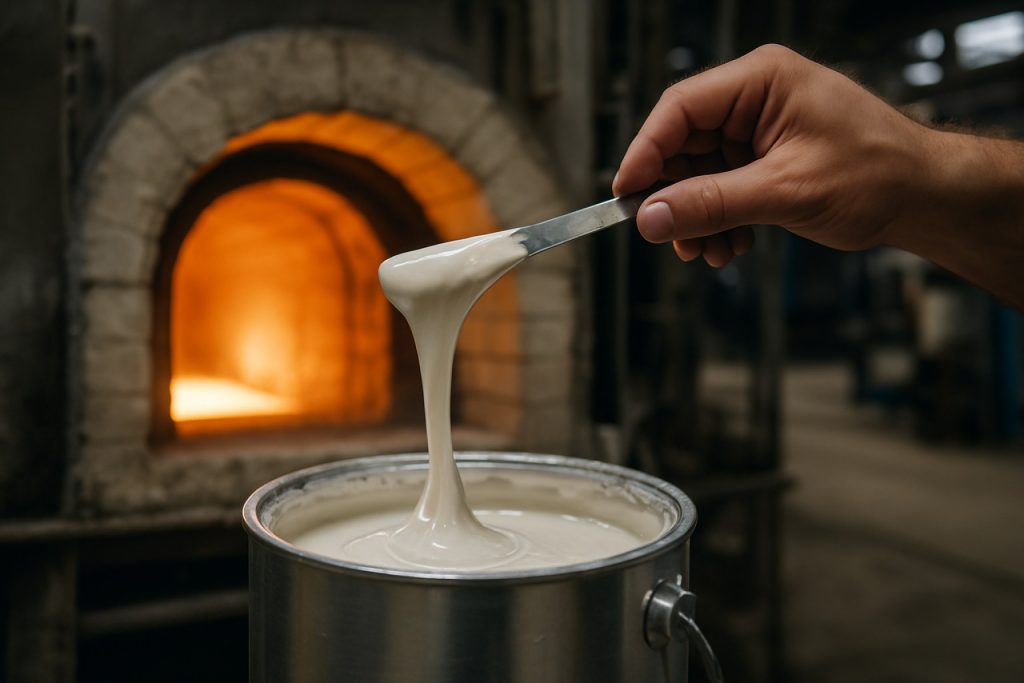
Table of Contents
- Executive Summary: Key Takeaways for 2025–2030
- Market Size & Forecast: Growth Projections to 2030
- Technological Innovations in Synthetic Thickeners
- Performance Benefits in High-Temperature Kiln Applications
- Leading Manufacturers & Industry Players (e.g., basf.com, dow.com, ashland.com)
- Regulatory & Environmental Considerations
- Competitive Landscape and Market Share Analysis
- Application Trends Across Industrial Sectors
- Challenges & Barriers to Adoption
- Future Outlook: Disruptive Trends and R&D Focus (2025–2030)
- Sources & References
https://youtube.com/watch?v=y1VVhwyww7w
Executive Summary: Key Takeaways for 2025–2030
Between 2025 and 2030, the use of synthetic thickeners in high-temperature kiln coatings is expected to accelerate, shaped by rising demands for operational efficiency and stricter environmental regulations in ceramics, refractories, and related industries. Synthetic thickeners—including acrylics, polyurethanes, and polyacrylates—are increasingly preferred for their superior rheological control, thermal stability, and consistency compared to traditional natural thickeners. This period will see incremental advances in formulation science, with manufacturers focusing on custom blends that optimize viscosity and application performance under the extreme heat conditions typical of kiln operations.
- Performance Requirements: The shift towards synthetic thickeners is driven by the need for coatings that maintain stability and viscosity above 1000°C, essential for protecting kiln linings and enhancing energy efficiency. Leading producers such as BASF and Dow are advancing product lines to address these high-specification requirements, incorporating additives that improve suspension, reduce sagging, and minimize defects in finished surfaces.
- Environmental and Regulatory Drivers: Regulatory pressures are growing, with increased scrutiny on VOC emissions and hazardous substances in industrial coatings. As a result, the market is pivoting toward waterborne, low-VOC synthetic thickener systems. Companies like AkzoNobel are investing in sustainable chemistry approaches that not only comply with evolving standards but also offer improved handling and worker safety.
- Global Industrial Growth: Expansion in steel, cement, and ceramics manufacturing in Asia-Pacific, the Middle East, and North America is spurring demand for advanced kiln coatings. This trend is prompting global suppliers such as Evonik Industries to expand production capacity and to develop region-specific solutions tailored to local process conditions and raw material profiles.
- Technological Innovation: In the coming years, digitalization and in-line quality control are expected to influence product development. Producers are beginning to leverage smart sensors and data analytics to optimize thickener dosing and ensure coating uniformity, reducing waste and enhancing consistency in high-volume kiln operations.
In summary, the 2025–2030 outlook for synthetic thickeners in high-temperature kiln coatings is marked by technological progress, sustainability imperatives, and expanding industrial applications worldwide. Market leaders are positioned to capitalize on these drivers by introducing more robust, eco-friendly, and customizable thickener solutions tailored to the evolving demands of kiln-based industries.
Market Size & Forecast: Growth Projections to 2030
The global market for synthetic thickeners used in high-temperature kiln coatings is positioned for moderate yet steady growth through 2030, as industrial sectors seek advanced solutions to withstand increasingly demanding thermal environments. In 2025, the adoption of synthetic thickeners—such as polyacrylates, modified celluloses, and associative thickeners—in kiln coating formulations is being driven by advancements in ceramics, refractories, and heavy manufacturing. These materials improve the rheological properties, application performance, and thermal stability of coatings applied to kilns, furnaces, and related infrastructure.
Key industry players, including BASF, AkzoNobel, and Dow, are expanding their product portfolios to address the needs of high-temperature applications. Product innovations in associative and nonionic thickeners are particularly notable, with manufacturers emphasizing enhanced temperature resistance, chemical stability, and compatibility with a wide range of binders and pigments.
As of 2025, the market size for synthetic thickeners in kiln coatings is estimated to be in the low hundreds of millions USD globally, with incremental annual growth projected at 4–6% CAGR through 2030, based on capacity expansions and increased adoption in Asia-Pacific and Middle East regions. This growth is underpinned by the continued modernization of cement, glass, and ceramic production facilities, where higher process temperatures and more aggressive operating conditions demand upgraded coating technologies. Additionally, regulatory pressures to reduce emissions and energy consumption are pushing end-users to seek high-performance coatings, further fueling demand for advanced thickeners.
Market leaders such as BASF and AkzoNobel have reported ongoing investments in research and development, targeting synthetic polymers with high thermal and shear stability. Meanwhile, Dow continues to collaborate with kiln coating formulators to tailor thickener solutions for specific high-heat process requirements. This collaborative and innovation-focused atmosphere is expected to accelerate the development and commercial uptake of next-generation synthetic thickeners through the end of the decade.
Looking ahead, the outlook for synthetic thickeners in high-temperature kiln coatings remains robust, especially as global infrastructure and energy sectors undergo upgrades and expansion. Manufacturers are likely to focus on sustainability, performance enhancement, and cost efficiency to differentiate their offerings and capture emerging opportunities in both established and developing markets.
Technological Innovations in Synthetic Thickeners
In 2025, technological innovation in synthetic thickeners for high-temperature kiln coatings is accelerating, driven by the need for improved rheological performance, thermal stability, and environmental compliance. Synthetic thickeners, particularly those based on polyacrylate and modified cellulose chemistries, are increasingly favored over natural alternatives due to their superior consistency and stability at elevated temperatures found in kiln operations.
Key manufacturers in the sector are focusing on the molecular design of thickeners to address the challenges presented by aggressive kiln environments, including temperatures exceeding 1000°C and exposure to corrosive atmospheres. Companies such as BASF and Dow have introduced advanced synthetic thickener grades that maintain viscosity and dispersibility under thermal stress, enabling uniform coating application and reduced defect rates in ceramics and refractories. For example, next-generation polyacrylate-based thickeners feature engineered side chains and crosslinking patterns, enhancing their resistance to breakdown during both application and firing cycles.
Recent years have also seen the adoption of hybrid synthetic thickeners that combine organic and inorganic components, leveraging the strengths of both for increased tolerance to thermal shock and chemical attack. AkzoNobel and Lubrizol are among those developing such solutions, with products targeting coatings for kiln furniture, rollers, and high-performance tiles.
Sustainability trends are influencing innovation as well. Manufacturers are integrating waterborne and low-VOC synthetic thickener systems to meet tightening environmental regulations in major markets. This is reflected in the product portfolios of companies like Celanese, which emphasizes both operational safety and reduced ecological footprint in its technical datasheets and press releases.
Looking ahead, R&D is expected to focus on smart thickeners with adaptive viscosity under dynamic temperature profiles, as well as further enhancements in compatibility with advanced binder and pigment systems. With kiln operators demanding coatings that extend maintenance cycles and improve yields, the synthetic thickener segment is poised for continued growth and sophistication through 2025 and beyond, underpinned by collaboration between chemical producers and end users.
Performance Benefits in High-Temperature Kiln Applications
In 2025, the adoption of synthetic thickeners in high-temperature kiln coatings continues to accelerate as manufacturers seek improved performance and process reliability. These thickeners, typically based on advanced acrylic or modified polyether chemistries, are engineered to withstand the extreme thermal and chemical stresses encountered in kiln environments, offering distinct advantages over traditional natural or semi-synthetic alternatives.
The primary performance benefit of synthetic thickeners in this context is their thermal stability. Unlike natural thickeners, which often degrade or lose viscosity when exposed to temperatures above 300°C, synthetic variants maintain their rheological properties even at temperatures exceeding 600°C. This enables more consistent coating application and film integrity throughout the firing process, reducing defects such as sagging or uneven coverage. According to BASF, one of the leading suppliers of specialty chemicals, their range of synthetic thickeners is specifically designed to deliver stable viscosity and controlled flow under high heat, which is crucial for optimal kiln coating performance.
Additionally, synthetic thickeners provide superior chemical resistance, tolerating the aggressive fluxes and gases present in kiln atmospheres. This resistance helps prevent premature breakdown or gelation, ensuring that the coating remains functional as a barrier and binder throughout the thermal cycle. Manufacturers such as Lubrizol and Ashland emphasize the role of their synthetic thickeners in enhancing the durability and lifespan of kiln coatings by maintaining structural integrity and minimizing contamination from binder residues.
Another significant advantage is formulation flexibility. Synthetic thickeners can be precisely engineered to deliver targeted viscosity profiles, thixotropy, and application properties, allowing kiln coating producers to tailor their products for specific substrates, application methods, and firing conditions. This customization supports the development of next-generation coatings for advanced ceramics, refractories, and functional components used in demanding sectors such as automotive, electronics, and energy.
Looking ahead to the next few years, ongoing R&D efforts are expected to yield thickeners with even higher thermal limits, lower emissions profiles, and improved environmental compatibility. Leading industry players, including BASF, are investing in novel polymer architectures and sustainable feedstocks to align with tightening regulatory standards and customer sustainability goals. As kiln operating temperatures and performance expectations continue to rise, the role of synthetic thickeners in ensuring reliable, high-performance coatings is likely to expand further.
Leading Manufacturers & Industry Players (e.g., basf.com, dow.com, ashland.com)
The global market for synthetic thickeners in high-temperature kiln coatings is experiencing notable activity in 2025, as key chemical manufacturers ramp up innovation and capacity to serve the demanding needs of refractory and ceramic applications. Industry focus remains on developing thickeners that deliver enhanced viscosity control, thermal stability, and compatibility with various binder systems under extreme kiln conditions.
Among the leading producers, BASF maintains a strong presence through its portfolio of rheology modifiers and synthetic polymers, which are engineered for advanced performance in industrial coatings. The company has emphasized continued investment in research and development, aimed at optimizing thickeners that withstand the high temperatures and aggressive environments typical of kiln operations. BASF’s solutions are widely adopted in ceramic and refractory coatings, benefiting from their proven ability to stabilize formulations and prevent sag or settling during application and firing.
Similarly, Dow remains a prominent supplier of synthetic thickeners, leveraging its expertise in acrylic and polyurethane chemistries. Dow’s recent efforts focus on improving the thermal endurance and rheological behavior of thickeners under kiln firing cycles, with particular attention to compatibility with waterborne and solventborne coatings. The company’s technical support and global supply capabilities have further solidified its role among kiln coating formulators seeking reliable and scalable thickener solutions.
Another major player, Ashland, continues to innovate in the field of specialty additives for high-temperature coatings. Ashland’s synthetic thickeners are designed for precise viscosity control and high suspension power, which are critical for uniform application on kiln-fired substrates. The company has made strategic enhancements to its product line to address the evolving needs of refractory and advanced ceramic manufacturers, including improved dispersibility and compatibility with a range of minerals and pigments.
Looking ahead, the competitive landscape is expected to intensify as demand for kiln coatings rises in sectors such as steel, cement, and advanced ceramics. Leading producers are poised to expand their offerings with thickeners that not only meet increasingly stringent performance requirements but also align with sustainability trends through reduced VOCs and improved lifecycle profiles. Strategic partnerships and technical collaborations are anticipated to accelerate product development, ensuring that synthetic thickeners remain at the forefront of high-temperature kiln coating innovation through 2025 and beyond.
Regulatory & Environmental Considerations
The regulatory and environmental landscape for synthetic thickeners used in high-temperature kiln coatings is evolving rapidly as governments and industry stakeholders intensify their focus on sustainability, workplace safety, and emissions control. As of 2025, synthetic thickeners—often based on modified polyacrylates, cellulose ethers, or polyurethanes—are subject to increasingly stringent regulations concerning their composition, handling, and end-of-life impact. Regulatory agencies in major markets such as the European Union, the United States, and East Asia are updating chemical registration frameworks and tightening permissible emission levels for volatile organic compounds (VOCs) and hazardous air pollutants (HAPs).
Within the European Union, the Registration, Evaluation, Authorisation and Restriction of Chemicals (REACH) regulation mandates comprehensive registration and risk assessment for synthetic polymeric additives, including thickeners, to ensure their safe use in industrial applications. Recent proposals under REACH and the European Green Deal are pushing manufacturers toward greater transparency regarding chemical ingredients and the development of thickeners with reduced environmental footprints. This has led major producers to increase investment in reformulation, eco-labeling, and life-cycle analysis of their product lines. For example, suppliers such as BASF and Dow have public sustainability commitments that directly influence their development and marketing of new thickener technologies for high-temperature applications.
In the United States, the Environmental Protection Agency (EPA) continues to review and update its Toxic Substances Control Act (TSCA) inventory, with a particular focus on polymers and additives used in industrial coatings. Manufacturers must provide detailed data on health and environmental impacts, which is leading to a preference for thickeners with lower toxicity and greater biodegradability. Industry organizations, such as the American Chemistry Council, are collaborating with regulators to facilitate compliance and promote best practices for the safe use and disposal of synthetic thickeners.
Furthermore, there is an increased push from both regulators and customers for kiln coating solutions that minimize energy use and emissions during application and curing. This is resulting in a market trend toward waterborne and low-VOC synthetic thickener systems, which are being adopted more widely as regulatory thresholds tighten. Companies like Celanese and Lubrizol have responded by expanding offerings that are tailored to these evolving requirements.
In summary, the regulatory environment in 2025 and beyond is expected to drive innovation in synthetic thickener chemistry, favoring formulations that are compliant with stricter health, safety, and environmental standards. This will likely accelerate the shift toward greener, safer alternatives while challenging manufacturers to balance performance with regulatory demands.
Competitive Landscape and Market Share Analysis
The competitive landscape for synthetic thickeners used in high-temperature kiln coatings is expected to remain dynamic through 2025 and into the following years, driven by ongoing advancements in materials science, changing regulatory requirements, and the growing adoption of energy-efficient kiln technologies. Key players in this specialized sector include global chemical manufacturers and specialty materials companies with established expertise in high-performance additives for industrial coatings.
Prominent multinationals such as BASF and Dow continue to maintain significant market positions, leveraging their broad product portfolios and R&D capabilities to supply synthetic rheology modifiers that perform under extreme thermal conditions. These companies have focused on developing tailor-made thickeners for refractory and kiln coating applications that require resistance to temperatures exceeding 1200°C, as seen in the ceramics, cement, and metals processing industries. Kuraray, recognized for its specialty polymers, and Ashland, known for its cellulosic and synthetic thickeners, are also prominent in this arena, offering products specifically engineered for high-temperature stability and consistent viscosity control.
Market share has historically been concentrated among a handful of large suppliers with global manufacturing bases and technical support networks. However, recent years have seen a rise in regional and specialized manufacturers, particularly in Asia-Pacific, seeking to capture share by offering cost-effective alternatives and customized solutions for local kiln coating producers. This includes companies such as SNF Group, which has expanded its portfolio of specialty polymers and thickeners for industrial coatings.
Data from industry bodies and manufacturer disclosures indicate a gradual but persistent shift toward synthetic thickeners over traditional natural counterparts, driven by requirements for thermal consistency, low impurity content, and compatibility with advanced binder chemistries. Innovations in polyacrylate, polyurethane, and associative thickeners allow for finely tuned rheological properties, supporting the production of thinner, more uniform coatings with enhanced durability at high temperatures.
Looking ahead, the market is expected to become more competitive as end-users in cement, ceramics, and metallurgical sectors demand higher-performance kiln lining systems. Strategic partnerships, joint development agreements, and portfolio expansions are anticipated as companies compete to meet evolving technical specifications and sustainability standards. The entry of new players, particularly those focused on green chemistry and reduced VOC content, may further reshape market dynamics by 2027.
Application Trends Across Industrial Sectors
In 2025, the application of synthetic thickeners in high-temperature kiln coatings is witnessing significant evolution across diverse industrial sectors, notably ceramics, refractories, and metallurgy. As manufacturing processes demand greater thermal stability and performance, synthetic thickeners—primarily based on modified polyacrylamides, polyurethanes, and acrylate copolymers—are increasingly replacing traditional organic and mineral thickeners. Their superior rheological control, high-temperature resistance, and compatibility with advanced binder and pigment systems are driving this shift.
The ceramics industry, a major consumer of kiln coatings, is at the forefront of adopting these materials. Leading producers have reported increased utilization of synthetic thickeners to enhance application consistency, reduce sagging at elevated temperatures, and improve the overall durability of coatings on tiles, sanitaryware, and advanced ceramics. For instance, suppliers such as BASF and Dow offer specialized synthetic thickener formulations designed for use in high-temperature ceramic processes, with a focus on ensuring smooth application and optimal coating thickness.
In the refractory sector, synthetic thickeners are being specified for coatings applied to kiln linings and castables, where thermal cycling and chemical attack are frequent. The demand for precise rheology under extreme conditions is leading to the adoption of highly engineered thickeners that maintain viscosity even above 1000°C. Manufacturers such as Lubrizol are developing tailor-made thickener solutions that address these stringent requirements, enabling longer operational life and reduced maintenance for kilns.
The metallurgy industry, particularly in steel and non-ferrous metal production, is also experiencing a rise in synthetic thickener use. Kiln and furnace coatings formulated with advanced thickeners help control dust, enhance adhesion, and improve the protective qualities of coatings in aggressive, high-temperature atmospheres. Industry leaders are emphasizing the environmental and operational benefits of switching to low-VOC, highly efficient synthetic thickeners, aligning with broader sustainability goals.
Looking ahead to the next few years, the trend toward customization and functionalization of synthetic thickeners is expected to accelerate. Innovations targeting even higher heat resistance, pollutant reduction, and ease of application are forecast to expand their adoption across all sectors. Collaboration between chemical companies and end-users is intensifying to address specific kiln design and operational challenges, ensuring that synthetic thickeners remain central to the modernization of high-temperature coating technologies.
Challenges & Barriers to Adoption
The adoption of synthetic thickeners in high-temperature kiln coating formulations faces a complex set of challenges, especially as the ceramics, refractories, and cement industries seek to improve operational efficiency and environmental profiles in 2025 and the foreseeable future. One primary barrier is the thermal stability of synthetic thickeners under extreme kiln conditions, which often exceed 1500°C. While synthetic polymers such as polyacrylates and modified cellulose derivatives offer improved rheological control at ambient and elevated temperatures, their decomposition or volatilization at kiln firing temperatures can compromise coating integrity and performance. This limitation necessitates the development of advanced thickeners with enhanced heat resistance, a focus of ongoing research among leading chemical manufacturers such as BASF and Dow.
Another significant challenge is the compatibility of synthetic thickeners with diverse coating matrices and raw materials. Coatings applied to kiln furniture, bricks, and refractories often incorporate a variety of inorganic binders and fillers, and the interaction with synthetic thickeners can influence viscosity, workability, and setting times. Achieving stable, homogeneous dispersions without negative side effects—such as foaming, sedimentation, or adverse chemical reactions—remains a technical hurdle. Manufacturers like Ashland are working to tailor thickener chemistries to address these compatibility issues, but the diversity of end-use environments slows the pace of standardization.
Cost factors also play a prominent role in hindering broader adoption. Synthetic thickeners are generally more expensive than traditional natural alternatives (such as bentonite or guar gum), and their use must be justified by clear performance gains or process efficiencies. The volatility in raw material prices and energy costs, coupled with supply chain uncertainties noted in recent years, further complicates procurement and long-term adoption planning for kiln coating manufacturers. Cost-sensitive sectors, particularly in emerging markets, may be hesitant to switch from tried-and-true natural thickeners unless compelling economic or regulatory drivers emerge.
Regulatory and sustainability considerations are increasingly influential. Growing scrutiny over the environmental impact of synthetic additives—including concerns about microplastic generation and end-of-life disposal—has prompted kiln coating formulators to weigh the life-cycle impacts of synthetic thickeners. Companies such as Brenntag are investing in more sustainable synthetic chemistries, but widespread adoption may be slowed by evolving standards and lack of unified certification protocols for high-temperature applications.
In summary, while synthetic thickeners hold considerable promise for optimizing kiln coating performance, their adoption in 2025 and beyond will be shaped by continued advances in thermal stability, formulation compatibility, cost-effectiveness, and compliance with evolving environmental regulations.
Future Outlook: Disruptive Trends and R&D Focus (2025–2030)
Looking ahead to 2025 and the subsequent years, the synthetic thickener segment for high-temperature kiln coatings is poised for notable transformation driven by both technological advancements and shifts in end-user demands. The ceramics, refractories, and industrial coatings sectors are intensifying their focus on kiln coatings that maintain performance under increasingly severe thermal and chemical environments, prompting rapid innovation in thickener chemistry.
One key disruptive trend expected to accelerate is the development and adoption of high-performance, temperature-stable synthetic thickeners. Traditional thickening agents, such as natural gums and cellulose derivatives, often degrade or lose rheological control at elevated kiln temperatures. In contrast, novel synthetic polymers—especially hydrophobically-modified alkali-swellable emulsions (HASE), polyacrylates, and polyurethanes—are being engineered for enhanced stability and tailored viscosity profiles BASF. These materials can be fine-tuned to resist breakdown at temperatures exceeding 1000°C, while maintaining application properties such as brushability and sag resistance.
Another major R&D thrust is the move towards sustainable and low-emission synthetic thickeners. Responding to tightening environmental regulations and sustainability mandates, manufacturers are prioritizing waterborne formulations and thickeners with lower volatile organic compound (VOC) content. Leading chemical companies are investing in “green chemistry” approaches to synthesize thickeners using renewable feedstocks, and to design polymers that are easier to remove or recycle at end of life Dow.
Digitalization and data-driven formulation are also shaping the future landscape. Advanced rheology modeling—leveraging machine learning and big data—enables R&D teams to predict thickener performance more accurately under high-temperature kiln conditions, thus shortening development cycles and reducing the need for trial-and-error in the lab Lubrizol.
From 2025 onwards, the kiln coatings market is expected to see:
- Greater adoption of bespoke synthetic thickeners designed for specific refractories and ceramic coating systems.
- Expansion of supplier collaboration with OEMs to co-develop next-generation kiln coating solutions.
- Increased commercialization of thickeners that balance high-temperature durability, cost-effectiveness, and environmental compliance.
Given these trends, the competitive landscape will likely be dominated by chemical majors and specialized additives firms with robust R&D pipelines and close integration with kiln coating manufacturers. The period to 2030 is forecasted to yield both incremental improvements in thickener chemistry and potential breakthroughs—such as smart thickeners with self-adjusting properties—fueling further performance gains in high-temperature kiln environments.