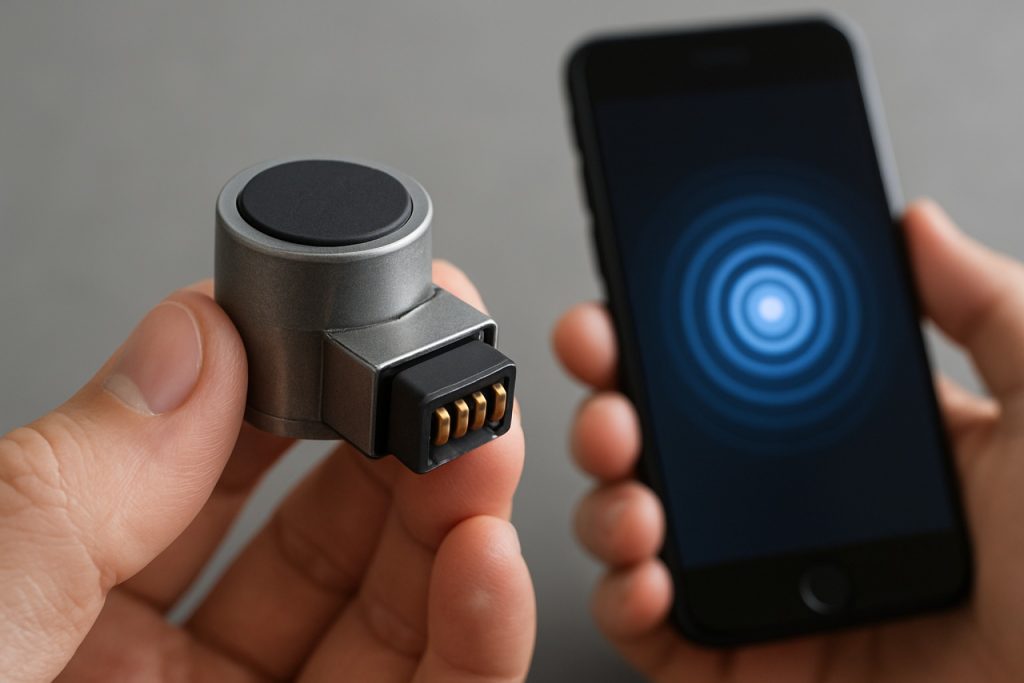
Table of Contents
- Executive Summary: Key 2025 Insights and Market Highlights
- Industry Overview: Evolution of Taktile Feedback Actuator Manufacturing
- Cutting-Edge Technologies: Latest Breakthroughs in Taktile Actuator Design
- Key Manufacturers and Industry Players (2025 Edition)
- Market Forecasts: 2025–2030 Growth Projections and Revenue Trends
- Emerging Applications: From Consumer Electronics to Automotive and Healthcare
- Supply Chain Dynamics and Strategic Sourcing
- Regional Analysis: Market Hotspots and Global Expansion Strategies
- Regulatory Landscape and Standards (Referencing ieee.org, asme.org)
- Future Outlook: Innovation Pipelines, Opportunities, and Competitive Threats
- Sources & References
Executive Summary: Key 2025 Insights and Market Highlights
The global tactile feedback actuator manufacturing sector is entering 2025 with robust momentum, driven by escalating demand for advanced haptic technologies across consumer electronics, automotive, and industrial applications. Tactile actuators—devices that simulate touch sensations—are critical in enabling immersive user experiences in smartphones, wearables, automotive interfaces, and emerging virtual/augmented reality devices.
Leading manufacturers such as TDK Corporation, Alps Alpine, Precision Microdrives, and Immersion Corporation are scaling up production capacities to meet surging OEM demand for next-generation actuators. In 2025, manufacturers are prioritizing miniaturization, power efficiency, and integration of smart feedback algorithms, addressing the needs of compact devices and sophisticated automotive human-machine interfaces.
The market is witnessing a technological shift from traditional eccentric rotating mass (ERM) and linear resonant actuator (LRA) designs to more advanced piezoelectric and electroactive polymer actuators. These new actuator types deliver faster response times, higher fidelity feedback, and improved durability, catering to increasingly discerning electronics and automotive markets. Companies like TDK Corporation are pioneering multi-layer piezo actuators, enabling thinner form factors and programmable tactile feedback profiles for flagship smartphones, wearables, and touch panels.
Automotive applications are a notable growth driver in 2025, with leading Tier 1 suppliers integrating tactile actuators into infotainment systems, steering wheels, and cockpit controls. The electrification and digitization of vehicle interiors are pushing manufacturers such as Alps Alpine to develop robust haptic modules that meet stringent automotive reliability standards.
Regionally, Asia-Pacific remains the manufacturing epicenter, with Japanese and South Korean firms at the forefront, supported by expanding production bases in China and Southeast Asia. European and North American OEMs are increasingly collaborating with these suppliers to ensure a resilient tactile actuator supply chain and to localize advanced assembly operations.
Looking ahead, the tactile feedback actuator sector in 2025 and beyond will be shaped by further advances in materials science, the integration of AI-driven haptic tuning, and the proliferation of new end-use cases—ranging from medical devices to next-gen gaming peripherals. Strategic investments in R&D and manufacturing automation are poised to accelerate innovation cycles, positioning established and emerging manufacturers to capture market share in a rapidly evolving landscape.
Industry Overview: Evolution of Taktile Feedback Actuator Manufacturing
Tactile feedback actuator manufacturing has experienced rapid advancement in recent years, driven by the increasing demand for haptic technologies in smartphones, wearables, automotive touch interfaces, and virtual/augmented reality systems. As of 2025, the industry is witnessing a transition from traditional eccentric rotating mass (ERM) and linear resonant actuator (LRA) components to more sophisticated piezoelectric and electroactive polymer (EAP) actuators. These newer technologies offer finer control, lower power consumption, and thinner form factors—key requirements for next-generation consumer electronics and immersive interfaces.
Leading manufacturers such as Alps Alpine, TDK Corporation, and Immersion Corporation are investing in expanding production lines and developing proprietary actuator designs to address emerging applications. For example, Alps Alpine has announced advancements in compact actuators tailored for foldable displays and automotive controls, which require high durability and precise feedback. TDK Corporation is focusing on multilayer piezo actuators featuring improved response times, as well as compatibility with flexible substrates—a critical step for integration into flexible and wearable devices.
The shift towards mass customization is also notable, as manufacturers strive to meet the varying requirements of different device ecosystems. Automotive sector adoption is accelerating, with tactile actuators being integrated into touch-based dashboards and control panels to enhance driver safety and experience. Companies like Robert Bosch GmbH are pioneering the use of advanced actuators in haptic feedback for automotive human-machine interfaces, while Immersion Corporation continues licensing its haptic technologies to a broad array of device manufacturers.
Industry data for 2025 indicates robust growth, with investments targeting automation and quality control within manufacturing facilities. Smart manufacturing approaches, including AI-driven defect detection and process optimization, are being adopted to improve yield and reduce costs. This is particularly significant as global supply chain pressures and demand for sustainability push manufacturers to streamline operations and adopt eco-friendly materials and production methods.
Looking ahead to the next few years, the tactile feedback actuator sector is expected to benefit from the proliferation of XR devices, further miniaturization, and the continued rise of smart surfaces in both consumer and industrial domains. Collaboration between actuator makers and device OEMs is intensifying, with co-development initiatives aimed at achieving seamless integration. As innovation accelerates, tactile feedback actuator manufacturing is poised to remain a cornerstone technology for user interface evolution across industries.
Cutting-Edge Technologies: Latest Breakthroughs in Taktile Actuator Design
The manufacturing of tactile feedback actuators is experiencing rapid innovation in 2025, driven by escalating demand from sectors such as consumer electronics, automotive, medical devices, and virtual/augmented reality. Tactile feedback—often termed haptics—relies on miniature actuators (such as piezoelectric, electroactive polymer, and electromagnetic types) that can deliver nuanced physical sensations to users. Leading players in the field are advancing both the materials and processes involved in actuator production to achieve finer control, lower power consumption, and ultra-compact form factors.
Recent breakthroughs stem from the integration of advanced materials and microfabrication techniques. For instance, TDK Corporation has been at the forefront with its piezo haptic actuators, leveraging multilayer piezoelectric ceramics for high-definition feedback. Their latest product lines combine thinness (under 0.5 mm) with rapid response times, making them particularly suitable for smartphone touchscreens and wearables. Similarly, Alps Alpine is innovating on compact, low-profile actuators that utilize unique mechanical structures to magnify tactile sensations, specifically targeting automotive HMI (Human-Machine Interface) panels.
In the electroactive polymer (EAP) segment, Precision Microdrives Limited and Immersion Corporation are scaling up production of thin-film actuators and collaborating with device makers to embed haptic feedback in next-generation AR/VR controllers. Their focus is on manufacturability and consistent performance at scale, using roll-to-roll processing and automated assembly lines to ensure quality and throughput.
On the process innovation front, companies are increasingly adopting Industry 4.0 principles, integrating real-time quality monitoring and predictive maintenance into actuator production lines. Murata Manufacturing Co., Ltd. has reported investments in smart factory upgrades, employing AI-driven inspection systems to detect micro-defects in piezoelectric layers, directly improving yield and reliability. These approaches are expected to become the norm by 2026 as competition and quality demands intensify.
Looking forward, miniaturization and energy efficiency will continue as central themes. The industry outlook predicts rapid adoption of hybrid actuators—combining piezo and electromagnetic elements—for richer, more customizable tactile effects, especially in automotive and medical device interfaces. As manufacturing technologies mature, actuator costs are projected to decline, further accelerating integration into consumer products and industrial applications over the next few years.
Key Manufacturers and Industry Players (2025 Edition)
The global landscape for tactile feedback actuator manufacturing is evolving rapidly in 2025, with a mix of established multinationals and innovative startups driving advances in haptics technology. These players are meeting growing demand across consumer electronics, automotive, industrial, and medical sectors, as tactile interfaces become more central to user experience.
Leading the sector are several large-scale manufacturers with integrated R&D and production capabilities. TDK Corporation continues to be a dominant force, leveraging its expertise in piezoelectric and vibration actuator technologies. Their actuators are widely adopted in smartphones, automotive touchscreens, and wearable devices, benefitting from TDK’s global manufacturing footprint and vertical integration. Another major player, Alps Alpine Co., Ltd., supplies advanced tactile modules and actuators for both consumer and automotive applications. Their investments in miniaturization and energy efficiency have positioned them as a preferred supplier for next-generation infotainment and control systems.
In the precision haptics segment, Immersion Corporation plays a critical role, not as a manufacturer but as a licensor of haptic technologies and designs. Their intellectual property and software solutions are widely licensed by actuator manufacturers and OEMs worldwide, reflecting the importance of software-hardware integration in modern tactile feedback systems.
The Asian supply chain remains influential, with Joyson Electronics (Joyson Safety Systems) and Johnson Controls (for automotive haptic interfaces) expanding production to meet automotive OEM requirements for enhanced tactile feedback in vehicle interiors. Meanwhile, Precision Microdrives specializes in compact vibration motors and linear resonant actuators (LRAs), serving global demand for haptic-enabled consumer and wearable devices.
Emerging players are also making their mark in 2025. South Korea’s Samsung Electronics continues to innovate both in actuator integration for mobile devices and component manufacturing, leveraging its scale and technological capabilities. In Europe, Bosch is increasing investment in tactile feedback for automotive and industrial systems, capitalizing on its sensor and actuator expertise.
Looking ahead, the market is expected to see further consolidation among key players, increased collaboration on standards, and a shift toward more energy-efficient, miniaturized tactile actuators. The broadening application base—from AR/VR to medical devices—ensures that manufacturers such as TDK, Alps Alpine, and Samsung will continue to shape the industry’s direction through 2025 and beyond.
Market Forecasts: 2025–2030 Growth Projections and Revenue Trends
The tactile feedback actuator manufacturing sector is poised for robust growth between 2025 and 2030, driven by accelerating adoption in consumer electronics, automotive interfaces, and emerging spatial computing applications. As leading OEMs and component suppliers scale up production, the market is witnessing both capacity expansions and advances in actuator miniaturization and versatility.
Key industry players such as TDK Corporation, Alps Alpine, and Murata Manufacturing are expanding their portfolio of Linear Resonant Actuators (LRAs) and Piezoelectric Actuators to meet increasing demand for high-fidelity, low-latency haptic feedback in smartphones, game controllers, wearables, and AR/VR devices. Automotive manufacturers are also integrating advanced haptic systems into dashboards and touch interfaces, with suppliers like Immersion Corporation licensing tactile feedback technologies to Tier 1 automotive electronics makers.
In 2025, actuator production volumes are expected to surge in response to new product cycles from major smartphone and XR headset brands, with Asian manufacturers in particular ramping up capacity. For example, TDK Corporation has announced investments in expanding its actuator production lines to support next-generation mobile devices. Similarly, Murata Manufacturing continues to advance its piezoelectric technologies, targeting wearables and medical devices with thinner, more power-efficient actuators.
Looking forward, the period through 2030 is likely to see further diversification in actuator types and form factors, including the adoption of new materials and hybrid electromechanical designs. Industry roadmaps indicate a sustained compound annual growth rate (CAGR) in the double digits, supported by the proliferation of touch-based interfaces across sectors and the evolution of spatial computing hardware. Market participants such as Alps Alpine and TDK Corporation are investing in R&D to push the boundaries of tactile realism and integration flexibility, broadening the addressable market.
- By 2027, high-volume smartphone shipments and the widespread rollout of XR devices are projected to be primary growth drivers for actuator manufacturers.
- Automotive haptics will grow rapidly as regulatory and consumer demands for safer, distraction-minimized controls intensify.
- Wearable and healthcare device integration will present new requirements for ultra-compact, energy-efficient actuators.
Overall, the tactile feedback actuator manufacturing market is set to benefit from both technology innovation and expanding use cases, with global supply chains adapting to meet surging and evolving demand through 2030.
Emerging Applications: From Consumer Electronics to Automotive and Healthcare
The manufacturing of tactile feedback actuators, also referred to as haptic actuators, is undergoing a significant evolution, driven by the expanding adoption of haptic technology across multiple sectors. In 2025 and the near future, the demand for advanced tactile feedback solutions is being shaped predominantly by three major industries: consumer electronics, automotive, and healthcare.
In consumer electronics, the proliferation of devices such as smartphones, wearables, and gaming controllers continues to fuel innovation in actuator design and production. Leading manufacturers are scaling up the integration of advanced haptic components to deliver more immersive user experiences. For example, Apple Inc. and Samsung Electronics employ custom linear resonant actuators (LRA) and eccentric rotating mass (ERM) motors in their flagship devices, focusing on miniaturization and energy efficiency to accommodate thinner device profiles and longer battery life. The ongoing transition towards flexible and foldable electronics is prompting actuator manufacturers to develop ultrathin, conformable solutions suitable for integration into novel form factors.
In the automotive sector, tactile feedback actuators are increasingly incorporated into touch-based controls, infotainment systems, and steering wheel interfaces. Major automotive suppliers such as Robert Bosch GmbH have invested in scalable actuator manufacturing, emphasizing robust performance under harsh environmental conditions and stringent automotive safety standards. The shift to electric vehicles and digital cockpits is further accelerating the adoption of haptics, with actuators enabling intuitive, eyes-free control for drivers—a critical aspect for enhancing safety and user comfort.
Healthcare represents another high-growth area for tactile feedback actuator manufacturing. Medical device manufacturers, including companies like Philips, are exploring haptics for surgical robotics, telemedicine interfaces, and rehabilitation devices. These applications demand actuators with precise force feedback and low latency, prompting manufacturers to invest in advanced materials and piezoelectric technologies. The push for remote and minimally invasive healthcare solutions is expected to drive further demand for miniature, reliable, and sterilizable actuators.
From a manufacturing standpoint, industry leaders such as TDK Corporation and Alps Alpine Co., Ltd. are ramping up research and development efforts to enhance actuator efficiency, durability, and manufacturability. Investments in automation and quality control are streamlining production processes, while collaborations between actuator manufacturers and end-device OEMs ensure that products meet the evolving needs of emerging applications. Looking ahead, the market for tactile feedback actuators is poised for sustained growth, with advances in materials science, MEMS technology, and mass customization likely to further expand their role across consumer electronics, automotive, and healthcare sectors.
Supply Chain Dynamics and Strategic Sourcing
The supply chain dynamics and strategic sourcing for tactile feedback actuator manufacturing are undergoing significant shifts in 2025, driven by increasing demand from sectors like consumer electronics, automotive, and medical devices. The proliferation of haptic technology in smartphones, gaming devices, automotive touchscreens, and AR/VR interfaces is placing new pressures on the global procurement and supply landscape.
Leading actuator manufacturers such as TDK Corporation and Alps Alpine have responded by expanding their supplier networks to secure critical materials, including piezoelectric ceramics and electromagnetic components. To mitigate supply chain risks—especially those exposed during the semiconductor shortages of recent years—these companies are increasingly adopting multi-sourcing strategies and diversifying procurement across regions in East Asia, North America, and Europe.
In 2025, the industry is seeing greater vertical integration, with firms like Johnson Electric investing in upstream materials sourcing and in-house fabrication of key actuator components. This move is aimed at reducing lead times and ensuring tighter quality control. Simultaneously, the push for sustainability and regulatory compliance (notably in the European Union) is influencing sourcing decisions, prompting manufacturers to prioritize suppliers with robust environmental certifications and to trace the origin of raw materials more carefully.
Another notable trend is the strategic collaboration between actuator suppliers and OEMs. Companies such as Precision Microdrives are working closely with customers from the design phase onward, allowing for highly customized sourcing of specialized components like linear resonant actuators (LRAs) and eccentric rotating mass (ERM) motors. This collaborative approach helps streamline inventory management and reduce the risk of component obsolescence.
Looking ahead, supply chain digitalization—leveraging real-time analytics and AI-driven demand forecasting—is set to further optimize sourcing processes. Several leading manufacturers are investing in digital platforms to enhance transparency and agility in procurement, especially as geopolitical factors and fluctuating raw material prices continue to pose challenges. The ongoing efforts toward regionalizing supply chains, particularly in response to lessons learned from global disruptions, are likely to persist over the next few years, enabling greater resilience and responsiveness in tactile feedback actuator manufacturing.
Regional Analysis: Market Hotspots and Global Expansion Strategies
The global landscape for tactile feedback actuator manufacturing is rapidly evolving, with several regional hotspots emerging as centers for innovation, production, and strategic expansion. As of 2025, East Asia—particularly China, South Korea, and Japan—continues to dominate in both volume and technological advancement. Companies such as Alps Alpine and TDK in Japan, and Samsung Electronics in South Korea, are leveraging deep expertise in piezoelectric and linear resonant actuator (LRA) technologies. Their proximity to major consumer electronics manufacturing hubs provides a significant advantage in supplying haptic components to leading smartphone, automotive, and wearable device brands.
China has intensified its investment in actuator manufacturing, with local giants expanding production capacities and integrating vertically with supply chains for smartphones and electric vehicles. The government’s continued support for advanced manufacturing and the presence of contract manufacturers such as Goertek and Sunwoda further consolidate the region’s dominance. Export data for 2024-2025 shows a clear uptick in actuator shipments destined for North American and European assembly plants, reflecting a concerted push for global market share.
In North America, the focus is on innovation and niche applications, particularly for medical devices, automotive haptics, and AR/VR platforms. Companies like Immersion Corporation are driving R&D efforts and forming licensing partnerships with hardware manufacturers worldwide. The United States also benefits from a robust intellectual property regime and close ties to Silicon Valley tech giants, supporting the domestic development and integration of novel haptic solutions.
Europe is asserting itself through specialization in automotive and industrial applications, with German and Scandinavian suppliers such as Bosch focusing on high-reliability actuators for advanced driver-assistance systems (ADAS) and human-machine interfaces (HMIs). With stringent EU regulations on device safety and environmental impact, European manufacturers are also at the forefront of developing sustainable actuator technologies and recycling programs.
Looking ahead, global expansion strategies are increasingly characterized by joint ventures, local assembly partnerships, and the establishment of regional R&D centers. Major Asian manufacturers are setting up production and customization facilities in North America and Europe to reduce lead times and comply with local regulatory requirements. Meanwhile, regional players in emerging markets—including India and Southeast Asia—are ramping up actuator production to support the growth of domestic electronics and automotive sectors. As 2025 unfolds and beyond, the tactile feedback actuator market is expected to become more geographically diversified, with collaborative innovation and supply chain resilience at the core of global expansion strategies.
Regulatory Landscape and Standards (Referencing ieee.org, asme.org)
The regulatory landscape and standards for tactile feedback actuator manufacturing are evolving rapidly in response to increasing deployment across consumer electronics, automotive, medical devices, and industrial automation. In 2025, the sector is witnessing heightened attention to safety, interoperability, and performance benchmarks, driven by both industry demand and the need to ensure reliable user experiences.
Key regulatory bodies and standards organizations shaping this domain include the IEEE (Institute of Electrical and Electronics Engineers) and the ASME (American Society of Mechanical Engineers). The IEEE has established standards relevant to haptic interfaces and electromechanical actuator systems, such as those concerning human-system interaction (IEEE 2088) and tactile feedback protocols for wearable and embedded electronics. These standards provide guidance on interoperability, latency, signal fidelity, and user safety—factors critical to actuator design and manufacturing.
Meanwhile, the ASME contributes through mechanical and material standards, with a focus on the durability, fatigue resistance, and mechanical integration of actuators into complex assemblies. In 2025, collaboration between IEEE and ASME has intensified, leading to joint working groups that address cross-disciplinary issues such as standardizing performance metrics and lifecycle testing for tactile actuators intended for safety-critical applications, including surgical robotics and advanced driver-assistance systems.
Current regulatory trends also reflect an increased emphasis on global harmonization of standards. Manufacturers operating in the tactile feedback actuator space must now navigate compliance with both international (ISO/IEC) and regional directives—such as those from the European Union concerning RoHS (Restriction of Hazardous Substances) and CE marking, which influence material selection and process validation. The integration of feedback actuators into medical devices, for example, requires adherence not only to IEEE and ASME best practices but also to regulatory requirements like the FDA’s Quality System Regulation (QSR), further raising the bar for documentation and traceability.
Looking ahead to the next few years, the outlook is for more granular and sector-specific standards to emerge, especially as tactile feedback technology becomes embedded in critical infrastructure and personalized health solutions. Initiatives underway at IEEE and ASME signal a move toward certification schemes and reference architectures that streamline compliance, testing, and cross-border product launches, supporting both innovation and user safety in tactile actuator manufacturing.
Future Outlook: Innovation Pipelines, Opportunities, and Competitive Threats
The next several years promise significant transformation in the manufacturing of tactile feedback actuators, driven by the convergence of haptic innovation, miniaturization, and expanding application sectors. As of 2025, leading actuator manufacturers are accelerating R&D to address performance, cost, and scalability challenges, with a particular focus on high-fidelity touch response for consumer electronics, automotive interfaces, and emerging XR (extended reality) devices.
The innovation pipeline is robust. Major players such as TDK Corporation and Alps Alpine are investing heavily in next-generation piezoelectric and electromagnetic actuator technologies, aiming to deliver thinner, more energy-efficient, and precise haptic modules. TDK Corporation continues to expand its piezo actuator portfolio, with an emphasis on scalable MEMS-based solutions suitable for mass-market mobile devices and wearables. Meanwhile, Alps Alpine is leveraging its expertise in both automotive and consumer sectors to develop actuators meeting stringent reliability and miniaturization demands.
A key opportunity lies in the diversification of tactile feedback applications. Automotive manufacturers, including system suppliers such as Bosch, are collaborating with actuator specialists to integrate haptic feedback into in-vehicle infotainment and control panels, enhancing driver safety and engagement. Wearables and medical devices represent another growth frontier, with manufacturers like Precision Microdrives scaling up production of compact linear resonant actuators (LRAs) and eccentric rotating mass (ERM) motors for precise vibrotactile cues.
However, the sector faces competitive threats. Price pressures from commoditization, particularly in the smartphone and wearable market segments, are intensifying. Chinese and South Korean manufacturers are rapidly scaling capacity and improving actuator quality, narrowing the performance gap with incumbents in Japan, Europe, and the U.S. This global competition is likely to drive further investment in manufacturing automation, advanced materials, and integration of sensors and feedback loops, as evidenced by ongoing innovations at Johnson Electric and Nidec Corporation.
Looking ahead, the tactile feedback actuator industry is poised for steady growth through 2027 and beyond, propelled by increased demand for immersive user experiences and smart interfaces. Success will hinge on the ability to deliver differentiated actuator performance, cost-effective production, and rapid adaptation to evolving application requirements across industries.