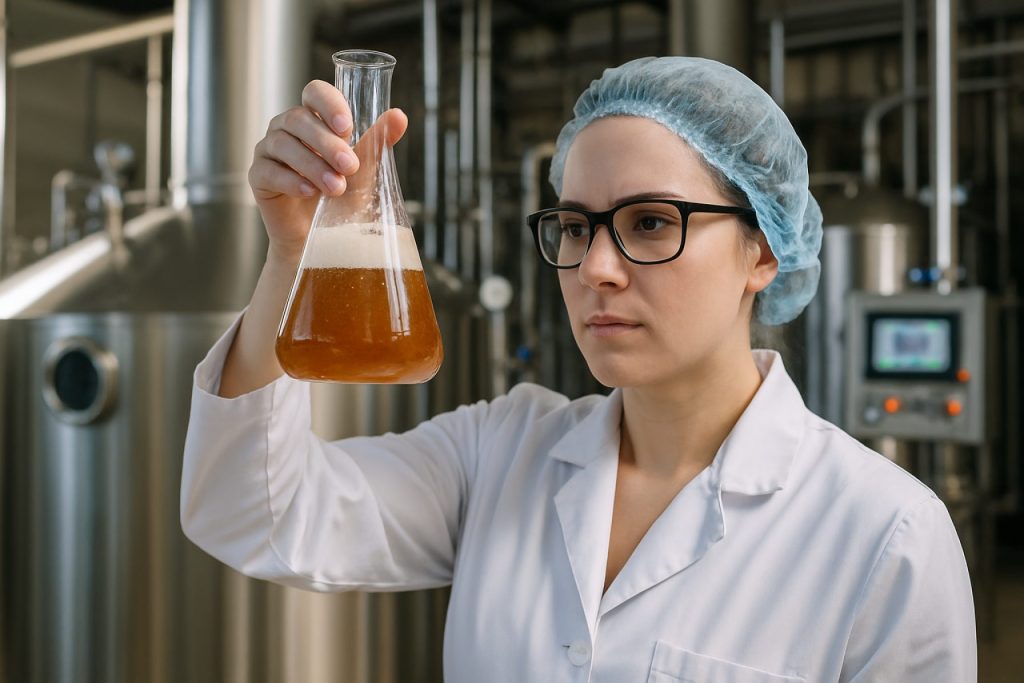
Revolutionizing Brewing Wort Filtration Biotechnologies in 2025: Innovations, Market Dynamics, and the Future of Efficient Brewing. Explore How Advanced Filtration Solutions Will Shape the Industry Over the Next Five Years.
- Executive Summary: Key Takeaways and 2025 Outlook
- Global Market Size, Growth Forecasts, and Regional Hotspots (2025–2030)
- Latest Filtration Technologies: Membrane, Crossflow, and Beyond
- Biotechnological Advances Driving Efficiency and Quality
- Leading Manufacturers and Innovators in Wort Filtration
- Sustainability Initiatives and Environmental Impact
- Cost-Benefit Analysis: CAPEX, OPEX, and ROI Trends
- Regulatory Landscape and Industry Standards (e.g., Brewers Association, EBC)
- Case Studies: Successful Adoption in Major Breweries
- Future Outlook: Emerging Trends, Disruptors, and Investment Opportunities
- Sources & References
Executive Summary: Key Takeaways and 2025 Outlook
The brewing industry is undergoing significant transformation in wort filtration biotechnologies as it moves into 2025, driven by efficiency demands, sustainability targets, and changing consumer expectations. Traditional methods such as kieselguhr (diatomaceous earth) filtration are being rapidly replaced or augmented by advanced alternatives, including crossflow membrane filtration, centrifugation, and novel enzymatic pre-treatments. These technological shifts are not only optimizing resource consumption but also addressing environmental and health concerns associated with older filtration media.
Globally, leading brewing equipment manufacturers and biotechnology suppliers are at the forefront of these innovations. GEA Group and Alfa Laval have expanded their portfolios with high-efficiency crossflow membrane systems, which offer significant reductions in waste, lower energy usage, and improved consistency in wort clarity. Both companies have reported increased demand from breweries targeting improved sustainability and reduced operational costs. These systems have also proven adaptable to both large-scale and craft brewing segments, broadening their market impact by 2025.
Meanwhile, enzymatic solutions are being developed and commercialized to enhance filterability and throughput. Companies such as Novozymes have introduced enzyme blends that break down beta-glucans and other polysaccharides, which traditionally cause filtration bottlenecks. Such biotechnology applications are enabling breweries to process higher gravity worts and alternative raw materials—trends driven by consumer interest in unique beer profiles and local grains—while maintaining efficient filtration performance.
From a regulatory and sustainability perspective, the reduction of kieselguhr usage is a notable trend, with several brewers phasing out the material in response to occupational safety and waste disposal challenges. Major brewing groups are increasingly investing in closed-loop systems and filtration methods that minimize waste, supported by the broader adoption of circular economy principles within the sector. Equipment suppliers are responding with modular, scalable systems that allow incremental adoption and integration with existing brewhouse operations.
Looking ahead to the remainder of 2025 and beyond, the outlook for wort filtration biotechnologies is characterized by continued convergence of process automation, digital monitoring, and sustainability optimization. Partnerships between breweries, technology suppliers, and biotech firms are expected to accelerate the deployment of next-generation filtration solutions. As efficiency, flexibility, and environmental stewardship become central to brewing operations, wort filtration biotechnologies will remain a dynamic and strategically important field within the global brewing industry.
Global Market Size, Growth Forecasts, and Regional Hotspots (2025–2030)
The global market for brewing wort filtration biotechnologies is poised for robust expansion between 2025 and 2030, driven by the ongoing modernization of brewing operations, heightened focus on sustainability, and evolving consumer demands for craft and premium beers. Wort filtration, a critical step in brewing, involves the removal of solids and particulates after mashing to ensure clarity, prevent off-flavors, and optimize fermentation. The adoption of advanced filtration biotechnologies—ranging from crossflow membrane systems to novel enzymatic aids—is accelerating as breweries seek operational efficiency and quality consistency.
Market leaders such as GEA Group, renowned for its comprehensive portfolio of brewing process technologies, and Siemens, noted for process automation and digitalization solutions, are at the forefront of innovation in wort filtration. Pall Corporation and Eaton also play pivotal roles, supplying advanced filtration modules and consumables tailored for both macro- and microbreweries. Recent investments by these companies in R&D and manufacturing capacity underscore expectations of sustained market growth through the decade.
Regional analysis suggests that Europe will continue as a leading market, underpinned by a dense concentration of breweries and stringent quality standards. Germany, the United Kingdom, and Belgium remain critical hubs, while Eastern European countries are witnessing increasing adoption of modern filtration systems as local craft beer segments mature. In North America, the United States and Canada are demonstrating robust demand, buoyed by a vibrant craft brewing sector and a strong culture of process innovation. Notably, Bühler Group—a Swiss leader in process solutions—has forged partnerships with North American brewers to deploy modular, energy-efficient filtration systems.
Asia-Pacific represents the fastest-growing regional hotspot. China’s rapidly industrializing brewing industry and the expansion of premium and craft segments in Japan, South Korea, and Australia are propelling investments in automated and sustainable wort filtration solutions. Local and multinational suppliers are establishing production and service facilities to meet this surging demand.
From 2025 through 2030, the global wort filtration biotechnology market is expected to grow at a steady CAGR, with some projections (from company filings and public statements) suggesting annual growth rates of 6–8% in leading regions. Key growth drivers include the push for resource efficiency (especially water and energy savings), compliance with environmental regulations, and the need to ensure product safety and consistency at scale. The continued entry of new biotech solutions—from high-performance filter aids to enzyme blends—is anticipated to further transform the market landscape.
Latest Filtration Technologies: Membrane, Crossflow, and Beyond
The brewing industry is witnessing rapid advancements in wort filtration biotechnologies, with a strong focus on enhancing efficiency, sustainability, and product quality. In 2025, membrane and crossflow filtration systems remain at the forefront, driven by demands for reduced energy consumption, lower water usage, and consistent beer clarity. Traditional kieselguhr (diatomaceous earth) filtration, while still present, is increasingly being replaced or supplemented by these innovative technologies due to environmental and occupational safety concerns.
Membrane filtration—particularly ultrafiltration and microfiltration—has gained significant traction among large and craft brewers alike. These systems utilize semi-permeable membranes to separate solids from liquids at the molecular level, enabling precise control over turbidity and flavor stability. Manufacturers such as GEA Group and Pall Corporation are prominent providers of advanced membrane solutions tailored for brewing applications. Recent improvements in membrane durability and anti-fouling coatings have extended operational lifespans and reduced cleaning cycles, making membrane filtration a more cost-effective and reliable option for wort clarification.
Crossflow filtration, a subtype of membrane filtration, is particularly notable for its continuous operation and self-cleaning capabilities. Unlike dead-end filtration, crossflow systems maintain a tangential flow across the membrane surface, minimizing clogging and ensuring consistent performance. This technology is being widely adopted for its advantages in reducing manual intervention and waste generation. Bucher Unipektin and ANDRITZ AG are among the companies supplying scalable crossflow systems to breweries of various sizes, with modular designs that facilitate retrofitting into existing facilities.
In addition to membrane and crossflow methods, the industry is exploring next-generation biotechnologies such as enzymatic pretreatment and bio-based filter aids. Enzymatic processing, promoted by ingredient specialists like Novozymes, can break down haze-forming proteins and polysaccharides upstream, reducing the filtration load and enhancing throughput. Some breweries are piloting bio-derived filter media that offer biodegradability and reduced reliance on mined resources.
Looking ahead, the outlook for brewing wort filtration is shaped by tightening sustainability regulations, the need for flexible production lines, and the pursuit of zero-waste operations. Automation and digital monitoring—integrated by technology leaders such as Siemens AG—are expected to further optimize filtration processes, providing real-time insights into filter performance and predictive maintenance scheduling. As breweries continue to scale up and diversify their product portfolios, investments in advanced filtration biotechnologies will be central to maintaining quality and competitiveness in the global market.
Biotechnological Advances Driving Efficiency and Quality
The brewing industry’s ongoing quest for higher efficiency and product consistency has driven significant advances in wort filtration biotechnologies as of 2025. Traditional wort clarification relied heavily on lauter tuns and mash filters, but the past few years have seen a growing adoption of advanced filtration regimes, including crossflow membrane systems, centrifugation, and enzymatic aids to optimize both throughput and quality.
One of the most prominent trends is the increased integration of membrane filtration systems. Companies like GEA Group and Alfa Laval—both established global suppliers of brewery equipment—have actively promoted ceramic and polymeric crossflow membranes for wort clarification. These systems provide finer particle removal, improved turbidity reduction, and higher recovery rates compared to traditional methods, while reducing water and energy consumption. For example, GEA Group’s membrane-based solutions are designed to help brewers achieve consistent wort clarity with minimal oxygen pickup, addressing the industry’s increasing focus on shelf life and flavor stability.
Simultaneously, rapid developments in enzymatic biotechnologies are supplementing mechanical separation. Leading enzyme manufacturers, such as Novozymes</a), have expanded their portfolios with tailored enzyme blends that break down beta-glucans and arabinoxylans, allowing for faster wort runoff and reduced viscosity. These biotechnological aids also enable the use of alternative grains and adjuncts, supporting sustainability goals and recipe innovation. Enzyme-driven filtration accelerates lauter tun operations, and some estimates suggest brewers can achieve up to 20% higher throughput with optimized enzyme regimes.
Centrifugation, once reserved for large-scale operations, is now increasingly viable for small and mid-sized breweries due to new, modular designs. Alfa Laval and SPX FLOW have released compact, energy-efficient centrifuge solutions that reduce fine sediment content and improve wort clarity without excessive oxygen ingress. These technologies are helping craft and regional brewers meet stricter quality standards and reduce manual handling.
Looking forward, the next few years will likely see further integration of digital controls and real-time monitoring into filtration systems. Companies such as Siemens are working on sensor-driven automation platforms that continuously adjust filtration parameters for optimal yield and quality, minimizing losses and labor requirements.
In summary, the convergence of mechanical, enzymatic, and digital biotechnologies is reshaping wort filtration in breweries worldwide. This not only enhances process efficiency but also empowers brewers—large and small—to achieve unprecedented consistency, sustainability, and product quality in an increasingly competitive market.
Leading Manufacturers and Innovators in Wort Filtration
The global brewing industry is witnessing a rapid transformation in wort filtration technologies, driven by the dual imperatives of product quality and operational sustainability. As of 2025, a handful of leading manufacturers and innovative companies are shaping the future of wort filtration biotechnologies, leveraging decades of expertise, bioprocess engineering, and advanced materials science.
One of the most prominent players in this sector is GEA Group, a Germany-based multinational recognized for its cutting-edge brewery systems. GEA continues to advance its range of crossflow membrane filtration units and depth filtration solutions, prioritizing energy efficiency and reduced waste. Its systems, such as the GEA clearamic crossflow filter, are widely adopted for their low environmental impact and high wort clarity, serving both craft and large-scale breweries.
Another technological leader is Pall Corporation, part of Danaher Corporation, known for its robust filtration and separation solutions. Pall’s beer filtration systems utilize proprietary membrane and depth filter media, with products like the SUPRApak module specifically designed for rapid wort clarification and microbial stabilization. The company’s R&D focus is on extending filter lifetimes and reducing the need for diatomaceous earth and other consumables.
In the field of biotechnological filtration aids, Erbslöh Geisenheim AG, based in Germany, is notable for its development of natural, bio-based fining agents and filtration aids, which are increasingly favored for their sustainability and reduced allergenic potential. Erbslöh’s innovations cater to the growing demand for cleaner-label beers and efficient removal of haze-forming proteins and polyphenols.
Eaton is another global supplier offering a comprehensive range of brewing filtration solutions, including depth filters, sheet filters, and specialty filter media. Eaton’s BECO range is tailored to address the evolving needs of breweries seeking flexible, scalable, and regulatory-compliant filtration systems.
Looking ahead, the next few years are expected to see further integration of automation and digital monitoring into wort filtration, with companies like Bühler Group investing in smart filtration equipment capable of real-time process control. These advancements are aimed at maximizing yield, minimizing losses, and enabling data-driven quality assurance.
- GEA Group: Crossflow and membrane filtration; energy-efficient brewery solutions.
- Pall Corporation: Modular, high-clarity membrane systems; reduced use of traditional filter aids.
- Erbslöh Geisenheim AG: Natural, bio-based filtration aids; focus on sustainability and clean-label processing.
- Eaton: Depth and sheet filters; scalable and regulatory-compliant systems.
- Bühler Group: Automation and digitalization in filtration processes.
As sustainability mandates tighten and consumer preferences shift toward transparency and quality, these manufacturers are expected to further drive innovation in wort filtration biotechnologies, with an emphasis on resource efficiency, operational flexibility, and enhanced product safety.
Sustainability Initiatives and Environmental Impact
The brewing industry’s focus on sustainability in wort filtration has intensified in 2025, with leading breweries and equipment suppliers adopting advanced biotechnologies to reduce environmental impact. Traditional filtration methods, often reliant on diatomaceous earth (DE) or kieselguhr, have raised sustainability concerns due to resource extraction, waste generation, and disposal challenges. In response, the sector is transitioning towards eco-friendlier alternatives, such as crossflow membrane filtration, regenerative filter aids, and circular economy strategies.
Major brewing technology providers are at the forefront of these innovations. GEA Group, a global leader in process technology, has expanded its portfolio of membrane-based filtration systems that minimize waste and energy consumption. Their systems are increasingly implemented by large-scale brewers aiming to reduce water usage and lower their carbon footprint. These membrane technologies eliminate the need for mineral filter aids, significantly decreasing solid waste output and supporting breweries in meeting tightening environmental regulations.
Similarly, Krones AG has prioritized sustainability in its brewing equipment solutions, introducing wort filtration modules that offer high efficiency and reduced environmental impact. Their systems focus on reducing water and energy consumption during filtration, a critical component in sustainability roadmaps for breweries worldwide. Krones’ commitment is evident in collaborations with leading breweries to pilot and scale up regenerative filtration and waste minimization practices.
On the supplier side, Eaton, known for its filtration technologies, has developed sustainable filter media that are biodegradable and sourced from renewable materials. These innovations lower the environmental burden of spent filter disposal and help brewers align with circular economy principles. Eaton also supports breweries with process optimization to further reduce resource input and waste generation.
Industry organizations, such as the Brewers Association, have stepped up guidance on best practices for sustainable wort filtration, including the adoption of life cycle assessment (LCA) tools and benchmarking emissions from filtration processes. These initiatives promote transparency and help breweries set actionable sustainability targets.
Looking ahead, the integration of digital monitoring and automation is expected to further enhance the environmental performance of wort filtration systems by enabling real-time optimization of resource use and early detection of inefficiencies. As regulatory pressures mount and consumer demand for sustainable production grows, the adoption of biotechnological solutions in wort filtration is poised to accelerate, shaping a greener future for the brewing industry.
Cost-Benefit Analysis: CAPEX, OPEX, and ROI Trends
The cost-benefit analysis of brewing wort filtration biotechnologies in 2025 is shaped by continued advancements in filtration systems, growing sustainability demands, and the evolving economics of brewery operations. Capital expenditures (CAPEX) for modern wort filtration technologies, such as crossflow membrane filtration and advanced mash filter presses, remain significant, but operational expenditures (OPEX) are increasingly being optimized through energy-efficient designs, automation, and extended equipment lifespans.
In terms of CAPEX, leading suppliers such as GEA Group and Pentair offer state-of-the-art mash filter systems and crossflow filtration units. Initial investments for large-scale breweries can exceed several hundred thousand euros, particularly when integrating fully automated systems. Nonetheless, mid-sized and craft brewers are gaining access to modular, scalable solutions, lowering upfront barriers and allowing incremental upgrades as production scales. GEA Group emphasizes modularity and flexible configurations in its filtration technologies, allowing breweries to align CAPEX with current and future production needs.
OPEX considerations revolve around maintenance, membrane replacement (for membrane systems), energy consumption, and consumables (such as filter aids for traditional systems). Crossflow membrane filtration—offered by both GEA Group and Pall Corporation—typically reduces OPEX by minimizing filter aid usage, lowering water consumption for cleaning, and enabling higher wort recovery rates. For instance, mash filters can increase extract yields by up to 2% compared to conventional lauter tuns, directly translating to raw material cost savings. Automated cleaning-in-place (CIP) systems further reduce labor and downtime, contributing to operational efficiency.
Return on investment (ROI) calculations increasingly incorporate not only direct cost savings but also sustainability-related benefits. Breweries adopting advanced wort filtration technologies report shorter payback periods—often 2 to 4 years—due to improved wort clarity, higher extract yields, energy savings, and reduced waste. Pentair and Krones AG highlight the role of their systems in supporting sustainability and compliance initiatives, which are becoming critical as breweries respond to stricter environmental regulations and consumer demand for greener production.
Looking ahead, the next few years are expected to see continued downward pressure on OPEX through predictive maintenance, digitalization, and improved membrane chemistries. As wort filtration solutions become more cost-competitive and scalable, their adoption will likely broaden across brewery sizes, further shifting the cost-benefit balance in favor of advanced biotechnologies.
Regulatory Landscape and Industry Standards (e.g., Brewers Association, EBC)
The regulatory landscape and industry standards for brewing wort filtration biotechnologies are experiencing dynamic evolution in 2025, driven by a convergence of sustainability mandates, product quality requirements, and technological advancements. Internationally, organizations such as the Brewers Association and the European Brewery Convention (EBC) are instrumental in shaping the frameworks that govern wort filtration processes. Their guidelines set benchmarks for clarity, microbiological stability, and the minimization of undesirable compounds—criteria that are increasingly being embedded into national and international regulatory codes.
A significant development in the past year has been the harmonization of definitions and test protocols for filtration efficiency and filter-aid residues. The Brewers Association updated its Best Practices for Wort Production to reflect new filtration media, such as crossflow membrane and kieselguhr-free systems, in response to environmental concerns over traditional filter aids. Meanwhile, the EBC has continued to publish standardized methods for evaluating filter performance, haze measurement, and the impact of filtration on sensory attributes, with the latest revisions emphasizing resource efficiency and waste reduction.
Global regulatory authorities are also raising expectations. In the European Union, brewing operations are now subject to stricter limits on the disposal of spent filtration materials and effluents, aligning with the EU Green Deal objectives. This has pushed many European brewers to accelerate the adoption of closed-loop and regenerative filtration technologies that comply with both EBC standards and environmental regulations. In the United States, the Brewers Association continues to lobby for harmonized FDA and TTB (Alcohol and Tobacco Tax and Trade Bureau) recognition of modern filtration aids and biotechnologies, ensuring regulatory clarity for innovative solutions.
Looking ahead, the next few years will likely see industry standards incorporate digital traceability of filtration media, in line with broader food safety trends. Traceable biotechnological filter products and automated process monitoring are expected to become prerequisites for compliance, particularly among large-scale brewers and those exporting internationally. Companies at the forefront of biotech filter development, such as GEA Group—a leading supplier of brewery process equipment—are already aligning their solutions to meet evolving standards and sustainability reporting requirements.
As regulatory bodies and industry associations continue to refine wort filtration guidelines, breweries will need to remain agile, investing in technology and best practices that ensure compliance while driving operational efficiency and product quality.
Case Studies: Successful Adoption in Major Breweries
In recent years, leading breweries worldwide have accelerated the adoption of advanced wort filtration biotechnologies to enhance process efficiency, sustainability, and product quality. As of 2025, several high-profile case studies illustrate how major industry players are leveraging these innovations.
One notable example is Anheuser-Busch InBev, the world’s largest brewer, which has integrated crossflow membrane filtration systems into multiple facilities across Europe and the Americas. By replacing traditional kieselguhr (diatomaceous earth) filtration with automated membrane-based systems, AB InBev has reported significant reductions in water and energy consumption, aligning with its ambitious 2025 sustainability goals. The transition has also improved operational safety by eliminating hazardous filter aids and has enabled quicker product changeovers, supporting a broader range of beer styles and increasing overall flexibility.
Similarly, Carlsberg Group has deployed next-generation rotary vacuum drum filters and ceramic membrane modules at its flagship breweries in Denmark and Eastern Europe. Carlsberg’s implementation, in collaboration with filtration technology leaders, focuses on maximizing wort clarity and yield while minimizing waste streams. The company emphasizes the role of these systems in reducing the environmental footprint of brewing operations, particularly by lowering solid waste and improving the recovery of valuable byproducts for animal feed or energy generation.
Heineken N.V., another global brewing giant, has adopted high-capacity tangential flow filtration technologies in several of its production sites. This move has enabled greater throughput and consistent wort quality, essential for large-scale operations supplying diverse markets. Heineken highlights real-time monitoring and process automation as key advantages, ensuring consistent product standards and robust traceability throughout the filtration stage.
Many of these technological transitions have been facilitated by partnerships with filtration system specialists such as GEA Group and Pall Corporation, both recognized for their modular, scalable solutions tailored for brewing applications. These providers have worked closely with breweries to integrate data-driven process control, remote diagnostics, and predictive maintenance—critical for minimizing downtime and maximizing return on investment in capital-intensive systems.
Looking ahead, the ongoing adoption of biotechnologies in wort filtration is expected to intensify, driven by tightening sustainability regulations and the competitive imperative for operational efficiency. As digitalization deepens and filtration materials advance, major breweries will likely continue to set benchmarks for the industry, demonstrating the tangible benefits of modern wort filtration biotechnologies on a global scale.
Future Outlook: Emerging Trends, Disruptors, and Investment Opportunities
As 2025 approaches, the brewing industry’s approach to wort filtration is undergoing marked transformation, shaped by advances in biotechnology, sustainability imperatives, and digitalization. Traditional filtration media such as kieselguhr (diatomaceous earth) are being progressively replaced by novel, more sustainable solutions. Key players are accelerating the adoption of crossflow membrane filtration and centrifuge-based systems that offer higher efficiency, lower waste, and reduced environmental impact.
Leading equipment manufacturers and technology suppliers are pivotal in this shift. GEA Group AG has pioneered modular filtration units that integrate seamlessly into both new and existing brewhouses, promising reduced energy and water use. Alfa Laval AB is advancing centrifugal separation technologies that minimize oxygen pickup, enhance protein removal, and ensure consistent wort quality—crucial for both craft and industrial-scale operations. Meanwhile, Pall Corporation is expanding its high-selectivity membrane portfolios, enabling brewers to tailor wort clarity and composition without reliance on consumable filter aids.
In 2025, two major disruptors are poised to reshape investment priorities: digitization of process control and the rise of bio-based filtration aids. Smart sensors, real-time analytics, and automated process feedback are enabling brewers to optimize filtration cycles and throughput dynamically, thus reducing losses and ensuring quality. Companies such as Siemens AG are integrating industrial IoT solutions into brewing lines, providing actionable insights from filtration data and predictive maintenance alerts.
Another significant trend is the commercialization of biotechnological filtration aids, such as enzymatic pre-treatments and biodegradable filter media derived from renewable resources. These innovations aim to further decrease environmental footprint and align with global sustainability regulations. Industry consortia and organizations like Brewers Association are actively supporting research initiatives and pilot programs to validate these new technologies at scale.
Investment opportunities in 2025 and beyond are likely to concentrate on startups and partnerships that combine bioengineering expertise with process automation. With consumer and regulatory pressure mounting, breweries are seeking technologies that deliver not only operational efficiency, but also compliance with stricter waste management and carbon reduction targets. Strategic alliances among equipment suppliers, biotech firms, and brewing conglomerates are expected to drive the sector’s next wave of innovation, with the Asia-Pacific and North American markets leading in adoption rates.
In sum, the outlook for brewing wort filtration biotechnologies is defined by a convergence of sustainability, digitalization, and bio-innovation—offering substantial growth and transformation opportunities for forward-thinking stakeholders.
Sources & References
- GEA Group
- Alfa Laval
- Siemens
- Pall Corporation
- Eaton
- Bühler Group
- Bucher Unipektin
- ANDRITZ AG
- GEA Group
- Alfa Laval
- SPX FLOW
- Siemens
- Erbslöh Geisenheim AG
- Krones AG
- Pentair
- Anheuser-Busch InBev
- Carlsberg Group
- Heineken N.V.