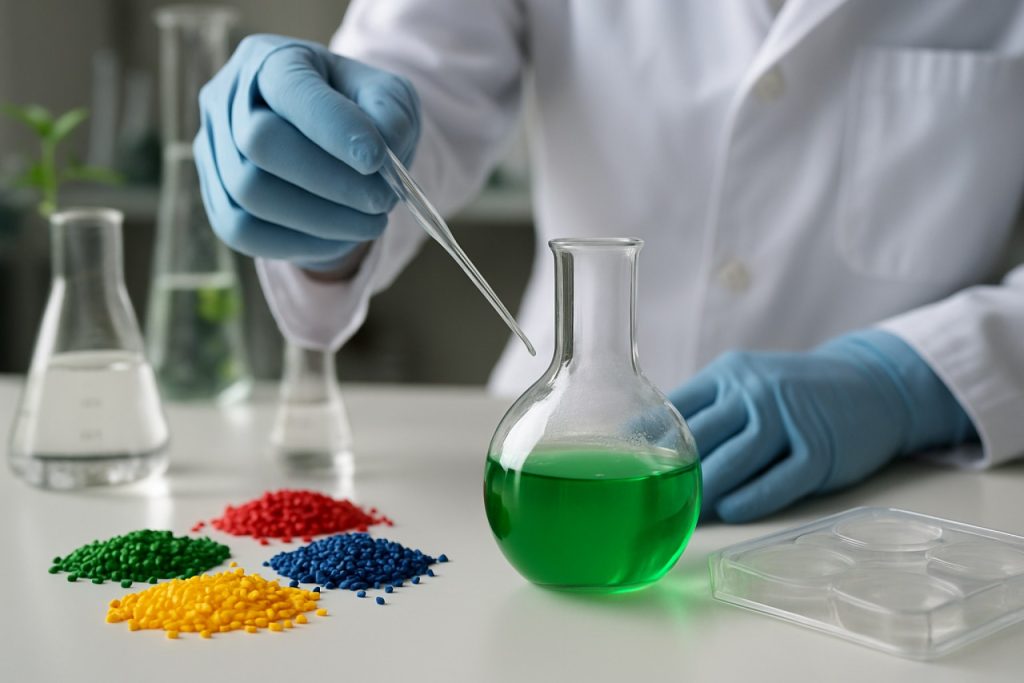
Enzyme-Catalyzed Polymer Synthesis in 2025: Pioneering Sustainable Materials and Accelerating Market Expansion. Explore How Biocatalysis is Transforming Polymer Manufacturing for a Greener Future.
- Executive Summary: Key Trends and Market Drivers in 2025
- Market Size, Segmentation, and 2025–2030 Growth Forecasts
- Technological Advances in Enzyme Engineering and Biocatalysis
- Competitive Landscape: Leading Companies and Strategic Initiatives
- Sustainability Impact: Environmental Benefits and Regulatory Drivers
- Emerging Applications: Bioplastics, Medical Devices, and Beyond
- Challenges: Scale-Up, Cost, and Enzyme Stability
- Regional Analysis: North America, Europe, Asia-Pacific, and Rest of World
- Investment, Partnerships, and M&A Activity
- Future Outlook: Innovation Roadmap and Market Opportunities Through 2030
- Sources & References
Executive Summary: Key Trends and Market Drivers in 2025
Enzyme-catalyzed polymer synthesis is poised for significant growth in 2025, driven by the convergence of sustainability imperatives, advances in enzyme engineering, and increasing industrial adoption. The global shift toward greener manufacturing processes is accelerating the replacement of traditional chemical catalysts with biocatalysts, particularly in the production of polyesters, polyamides, and specialty polymers. Enzymatic processes offer advantages such as mild reaction conditions, reduced energy consumption, and high selectivity, aligning with the environmental goals of major chemical producers and end-users.
Key industry players are scaling up investments in enzyme technology platforms. Novozymes, a global leader in industrial enzymes, continues to expand its portfolio of polymerization enzymes, targeting applications in biodegradable plastics and specialty materials. Similarly, BASF is integrating enzyme-catalyzed steps into its polymer production lines, aiming to reduce carbon footprint and enhance product performance. DSM is also advancing enzyme-enabled synthesis for high-performance materials, leveraging its expertise in both biotechnology and materials science.
Recent data from industry consortia and company disclosures indicate a marked increase in pilot and demonstration-scale projects. For example, several European consortia, including members from Novozymes and BASF, are collaborating on the development of enzymatic routes to polylactic acid (PLA) and polyhydroxyalkanoates (PHA), with commercial-scale production targeted for the late 2020s. These efforts are supported by regulatory incentives and growing demand from packaging, automotive, and textile sectors for bio-based and compostable polymers.
Technological advances in enzyme engineering—such as directed evolution and computational design—are enabling the creation of robust biocatalysts with improved activity, stability, and substrate scope. Companies like Novozymes and BASF are investing in proprietary enzyme discovery platforms to accelerate the commercialization of new polymerization processes. The integration of digital tools and high-throughput screening is expected to further shorten development cycles and lower costs.
Looking ahead, the outlook for enzyme-catalyzed polymer synthesis in 2025 and beyond is highly positive. Market drivers include tightening environmental regulations, consumer demand for sustainable products, and the need for circular economy solutions. As enzyme technology matures and production scales increase, cost competitiveness with conventional processes is expected to improve, paving the way for broader adoption across multiple industries.
Market Size, Segmentation, and 2025–2030 Growth Forecasts
The market for enzyme-catalyzed polymer synthesis is poised for significant expansion between 2025 and 2030, driven by increasing demand for sustainable materials, regulatory pressures to reduce environmental impact, and ongoing advances in enzyme engineering. Enzyme-catalyzed processes are gaining traction as alternatives to traditional chemical polymerization, offering milder reaction conditions, higher selectivity, and the potential for biodegradable end-products.
Current estimates suggest that the global market for enzyme-catalyzed polymer synthesis, while still a niche within the broader biopolymers and specialty polymers sectors, is experiencing double-digit annual growth. This is particularly evident in applications such as biodegradable plastics, biomedical polymers, and specialty coatings. The market is segmented by polymer type (e.g., polyesters, polyamides, polysaccharides), end-use industry (packaging, medical, textiles, automotive), and geographic region.
Europe and North America are leading regions, supported by strong regulatory frameworks and established bioplastics industries. The European Union’s Green Deal and circular economy initiatives are accelerating the adoption of enzyme-catalyzed processes, especially in packaging and single-use plastics. In North America, the presence of major chemical and biotechnology companies, as well as a growing focus on sustainable manufacturing, is fostering market growth.
Key players in the enzyme-catalyzed polymer synthesis market include Novozymes, a global leader in industrial enzymes, which has developed tailored enzyme solutions for polymerization and depolymerization processes. BASF is actively investing in biopolymer research, including enzyme-enabled synthesis routes for specialty plastics. DuPont is also engaged in developing enzyme-catalyzed pathways for high-performance polymers, particularly for biomedical and packaging applications. In Asia, companies such as Toyobo are advancing enzyme-based technologies for specialty fibers and films.
Looking ahead to 2030, the market is expected to benefit from continued innovation in enzyme engineering, which will expand the range of accessible polymers and improve process economics. The integration of enzyme-catalyzed synthesis with biorefinery concepts and circular economy models is anticipated to open new market segments, particularly in upcycling plastic waste and producing high-value specialty materials. As enzyme costs decrease and process efficiencies improve, adoption is likely to accelerate across both established and emerging markets.
Overall, the enzyme-catalyzed polymer synthesis market is set for robust growth through 2025 and beyond, underpinned by sustainability imperatives, technological progress, and the strategic initiatives of leading chemical and biotechnology companies.
Technological Advances in Enzyme Engineering and Biocatalysis
Enzyme-catalyzed polymer synthesis is rapidly advancing as a sustainable alternative to traditional chemical polymerization, leveraging the specificity and mild reaction conditions of biocatalysts. In 2025, the field is witnessing significant technological progress, driven by innovations in enzyme engineering, process optimization, and industrial collaboration.
A key trend is the development of robust and highly selective enzymes, such as lipases, cutinases, and esterases, tailored for the synthesis of polyesters, polyamides, and other specialty polymers. Companies like Novozymes and BASF are at the forefront, investing in protein engineering to enhance enzyme stability, activity, and substrate scope. For example, Novozymes has expanded its enzyme portfolio to include biocatalysts optimized for polymerization under industrially relevant conditions, enabling the production of biodegradable plastics and specialty materials with reduced environmental impact.
Recent data indicate that enzyme-catalyzed routes can achieve high molecular weight polymers with controlled architectures, rivaling conventional methods. BASF has reported successful pilot-scale production of polyesters using engineered lipases, demonstrating scalability and commercial viability. Meanwhile, DuPont is exploring enzymatic synthesis for high-performance polyamides, targeting applications in automotive and electronics sectors.
Collaborative efforts between enzyme producers and polymer manufacturers are accelerating technology transfer and market adoption. DSM and Evonik Industries are notable for their partnerships in developing bio-based monomers and polymers, integrating enzymatic steps into existing production lines. These collaborations are supported by industry bodies such as European Bioplastics, which advocate for biocatalytic processes as part of the circular economy.
Looking ahead, the outlook for enzyme-catalyzed polymer synthesis is promising. Advances in computational protein design and high-throughput screening are expected to yield next-generation enzymes with unprecedented efficiency and selectivity. The integration of digital tools and automation in enzyme engineering, as seen in initiatives by Novozymes and BASF, will further accelerate innovation. As regulatory and consumer pressures for sustainable materials intensify, enzyme-catalyzed processes are poised to capture a growing share of the polymer market, particularly in packaging, textiles, and biomedical applications.
Competitive Landscape: Leading Companies and Strategic Initiatives
The competitive landscape for enzyme-catalyzed polymer synthesis in 2025 is characterized by a dynamic interplay between established chemical giants, specialized biotechnology firms, and emerging startups. This sector is witnessing accelerated innovation, driven by the demand for sustainable materials and the unique advantages of enzymatic processes—such as mild reaction conditions, high selectivity, and reduced environmental impact.
Among the global leaders, BASF SE continues to invest in biocatalysis platforms, leveraging its extensive R&D infrastructure to develop enzyme-enabled routes for specialty polymers and biodegradable plastics. BASF’s collaborations with academic institutions and technology partners are focused on scaling up enzymatic polymerization processes, particularly for polyesters and polyamides, aiming to reduce reliance on fossil-based feedstocks.
Another major player, DSM, is advancing enzyme-catalyzed synthesis through its biotechnology division, with a focus on high-performance materials for automotive, electronics, and packaging applications. DSM’s strategic initiatives include partnerships with enzyme engineering firms and investments in pilot-scale production facilities to accelerate commercialization timelines.
In the enzyme supply and development segment, Novozymes stands out as a key innovator. The company is actively expanding its portfolio of polymerization enzymes, including lipases and cutinases, tailored for industrial-scale synthesis of polyesters and polyurethanes. Novozymes’ collaborations with polymer manufacturers are aimed at optimizing enzyme performance and process economics, with several demonstration projects underway in Europe and North America.
Emerging companies such as Carbios are gaining attention for their proprietary enzymatic recycling and synthesis technologies. Carbios has developed engineered enzymes capable of depolymerizing and repolymerizing PET, enabling closed-loop recycling and the production of high-quality recycled polymers. The company’s pilot plant operations and partnerships with major consumer brands signal a move toward broader industrial adoption in the coming years.
Strategic initiatives across the sector include joint ventures, licensing agreements, and open innovation platforms. Companies are increasingly engaging in cross-sector collaborations to address technical challenges such as enzyme stability, process scalability, and regulatory compliance. The outlook for 2025 and beyond suggests continued growth, with enzyme-catalyzed polymer synthesis poised to play a pivotal role in the transition to circular and bio-based economies.
Sustainability Impact: Environmental Benefits and Regulatory Drivers
Enzyme-catalyzed polymer synthesis is gaining significant momentum in 2025 as a sustainable alternative to traditional petrochemical-based polymerization processes. The environmental benefits of this approach are increasingly recognized by both industry and regulators, driving adoption and innovation in the sector.
One of the primary environmental advantages of enzyme-catalyzed polymer synthesis is its ability to operate under mild conditions—ambient temperature and pressure—thereby reducing energy consumption and associated greenhouse gas emissions. Enzymatic processes also typically avoid the use of toxic metal catalysts and hazardous solvents, resulting in safer manufacturing environments and less harmful waste streams. For example, the use of lipases and cutinases in the synthesis and recycling of polyesters, such as polylactic acid (PLA) and polyethylene terephthalate (PET), has demonstrated high selectivity and efficiency, enabling closed-loop recycling and upcycling of plastics.
Major chemical and biotechnology companies are actively investing in enzyme-based polymerization technologies. BASF, a global leader in chemicals, has ongoing research into biocatalytic processes for polymer production, focusing on reducing the carbon footprint of their materials portfolio. Novozymes, a world leader in industrial enzymes, is collaborating with polymer manufacturers to develop tailored enzyme solutions for both synthesis and depolymerization, supporting circular economy initiatives. DuPont is also advancing enzyme-enabled polymer technologies, particularly in the development of bio-based and biodegradable materials.
Regulatory drivers are accelerating the shift toward enzyme-catalyzed polymer synthesis. The European Union’s Green Deal and Circular Economy Action Plan, as well as the U.S. Environmental Protection Agency’s (EPA) focus on sustainable chemistry, are pushing manufacturers to adopt greener processes and materials. In 2025, new regulations on single-use plastics and extended producer responsibility (EPR) schemes are expected to further incentivize the adoption of enzymatic technologies for both polymer synthesis and recycling.
Looking ahead, the outlook for enzyme-catalyzed polymer synthesis is robust. Industry analysts anticipate increased commercialization of enzyme-enabled processes, particularly for biodegradable and bio-based polymers. Companies are expected to scale up pilot projects and form new partnerships to accelerate market entry. As enzyme engineering and process optimization continue to advance, the environmental benefits—lower emissions, reduced toxicity, and enhanced recyclability—will position enzyme-catalyzed polymer synthesis as a cornerstone of sustainable materials manufacturing in the coming years.
Emerging Applications: Bioplastics, Medical Devices, and Beyond
Enzyme-catalyzed polymer synthesis is rapidly advancing as a sustainable alternative to traditional chemical polymerization, with significant implications for bioplastics, medical devices, and other high-value applications. As of 2025, the field is witnessing a surge in both research activity and commercial interest, driven by the need for greener processes and the unique properties imparted by enzymatic catalysis.
In the bioplastics sector, enzyme-catalyzed synthesis is enabling the production of polyesters such as poly(lactic acid) (PLA) and polyhydroxyalkanoates (PHAs) under milder conditions, reducing energy consumption and minimizing toxic byproducts. Companies like Novozymes, a global leader in industrial enzymes, are actively developing tailored biocatalysts for polymerization processes. Their enzyme platforms are being integrated into pilot and commercial-scale bioplastic manufacturing, with a focus on improving yield, molecular weight control, and monomer selectivity. Similarly, BASF is investing in enzyme-enabled routes for biodegradable polymers, aiming to expand their ecoflex® and ecovio® product lines with more sustainable synthesis pathways.
Medical device manufacturing is another area where enzyme-catalyzed polymer synthesis is gaining traction. The precision and mild reaction conditions of enzymatic processes are particularly advantageous for producing biomedical-grade polymers with controlled architectures and minimal residual contaminants. Evonik Industries, a major supplier of specialty polymers for medical applications, is exploring enzymatic methods to synthesize polyesters and polyamides for use in resorbable implants and drug delivery systems. These efforts are expected to accelerate in the next few years as regulatory agencies increasingly favor greener manufacturing processes and as demand for advanced biomaterials grows.
Beyond bioplastics and medical devices, enzyme-catalyzed polymerization is being explored for specialty applications such as functional coatings, adhesives, and smart materials. The ability to fine-tune polymer microstructure and incorporate bio-based monomers is opening new avenues for high-performance, sustainable materials. Industry consortia and public-private partnerships are supporting scale-up initiatives, with organizations like Cargill leveraging their expertise in bio-based feedstocks to supply renewable monomers for enzymatic polymerization.
Looking ahead, the outlook for enzyme-catalyzed polymer synthesis is highly promising. Ongoing advances in enzyme engineering, process intensification, and feedstock diversification are expected to lower costs and expand the range of accessible polymers. As sustainability pressures mount and regulatory frameworks evolve, enzymatic processes are poised to play a central role in the next generation of bioplastics, medical devices, and beyond.
Challenges: Scale-Up, Cost, and Enzyme Stability
Enzyme-catalyzed polymer synthesis has emerged as a promising alternative to traditional chemical polymerization, offering advantages such as mild reaction conditions, high selectivity, and reduced environmental impact. However, as of 2025, several challenges continue to impede the widespread industrial adoption of these biocatalytic processes, particularly in the areas of scale-up, cost, and enzyme stability.
One of the primary hurdles is the scale-up of enzymatic polymerization from laboratory to industrial production. Enzymes, while highly efficient in small-scale reactions, often exhibit reduced activity and stability under the rigorous conditions of large-scale reactors. Factors such as substrate inhibition, product inhibition, and mass transfer limitations become more pronounced at scale, leading to lower yields and inconsistent product quality. Companies like Novozymes and BASF, both active in industrial enzyme production, are investing in process engineering and reactor design to address these bottlenecks, but robust, scalable solutions remain under development.
Cost is another significant barrier. Enzymes, especially those tailored for specific polymerization reactions, can be expensive to produce and purify. The high cost of enzyme production is compounded by the need for frequent replenishment due to enzyme deactivation over time. While enzyme immobilization techniques—where enzymes are attached to solid supports to enhance reusability—have shown promise, they often introduce additional complexity and cost. DuPont and DSM are among the companies exploring enzyme engineering and immobilization strategies to improve cost-effectiveness, but the economic viability of these approaches at commercial scale is still being evaluated.
Enzyme stability under industrial conditions remains a persistent challenge. Many enzymes are sensitive to temperature, pH, and the presence of organic solvents commonly used in polymer synthesis. This sensitivity can lead to rapid loss of catalytic activity, necessitating frequent enzyme replacement and increasing operational costs. Efforts to engineer more robust enzymes through protein engineering and directed evolution are ongoing, with companies like Novozymes leveraging advanced biotechnology platforms to develop enzymes with enhanced stability profiles.
Looking ahead, the outlook for overcoming these challenges is cautiously optimistic. Advances in synthetic biology, enzyme engineering, and process intensification are expected to yield more robust and cost-effective biocatalysts within the next few years. Strategic collaborations between enzyme producers, polymer manufacturers, and academic institutions are likely to accelerate the translation of laboratory breakthroughs into scalable industrial processes. However, until these technical and economic barriers are fully addressed, enzyme-catalyzed polymer synthesis will likely remain a niche technology, primarily used for high-value specialty polymers rather than bulk commodity plastics.
Regional Analysis: North America, Europe, Asia-Pacific, and Rest of World
Enzyme-catalyzed polymer synthesis is gaining momentum globally, with distinct regional trends shaping its development and commercialization. As of 2025, North America, Europe, and Asia-Pacific are the primary hubs for innovation and industrial adoption, while the Rest of World (RoW) region is gradually increasing its participation, particularly in niche applications and through technology transfer.
North America remains a leader in enzyme-catalyzed polymer synthesis, driven by robust R&D infrastructure and a strong focus on sustainable materials. Major chemical and biotechnology companies, such as DSM (now part of dsm-firmenich), DuPont, and Novozymes (now part of Novonesis), are actively developing enzyme-based processes for bioplastics and specialty polymers. The region benefits from close collaboration between academia and industry, with universities and research institutes frequently partnering with private sector players to accelerate commercialization. The U.S. government’s continued support for green chemistry and bio-based manufacturing is expected to further stimulate market growth through 2025 and beyond.
Europe is at the forefront of regulatory and policy initiatives promoting sustainable polymer synthesis. The European Union’s Green Deal and Circular Economy Action Plan are catalyzing investments in enzyme-catalyzed processes, particularly for biodegradable and compostable plastics. Companies such as BASF, Novamont, and Clariant are scaling up production of enzyme-derived polymers, often in collaboration with regional biotech firms. The region’s emphasis on reducing plastic waste and carbon emissions is expected to drive further adoption, with several pilot and demonstration plants scheduled to come online by 2026.
Asia-Pacific is emerging as a dynamic growth center, propelled by increasing demand for sustainable materials in China, Japan, South Korea, and India. Local players such as Toyobo and Mitsui & Co. are investing in enzyme-catalyzed polymer technologies, often leveraging partnerships with global enzyme producers. The region’s large manufacturing base and government incentives for green technologies are expected to accelerate market penetration, particularly in packaging, textiles, and automotive sectors.
Rest of World (RoW) regions, including Latin America, the Middle East, and Africa, are at earlier stages of adoption. However, technology transfer initiatives and collaborations with multinational companies are enabling gradual uptake. For example, partnerships with global leaders such as Novonesis and BASF are facilitating pilot projects and capacity-building efforts in these regions.
Looking ahead, regional disparities in regulatory frameworks, feedstock availability, and R&D capabilities will continue to shape the pace and scale of enzyme-catalyzed polymer synthesis adoption. However, the global trend toward sustainability and circularity is expected to drive steady growth across all regions through the remainder of the decade.
Investment, Partnerships, and M&A Activity
Investment, partnerships, and M&A activity in enzyme-catalyzed polymer synthesis have accelerated in 2025, reflecting the sector’s growing strategic importance for sustainable materials and green chemistry. The field is attracting capital from both established chemical manufacturers and specialized biotechnology firms, as well as from venture capital and corporate venture arms seeking exposure to bio-based innovation.
Major chemical companies are deepening their commitment to enzyme-catalyzed processes. BASF, a global leader in chemicals, has continued to expand its R&D and partnership portfolio in biocatalysis, with a focus on developing enzyme-enabled routes for specialty polymers and biodegradable plastics. Similarly, DSM has maintained its investment in enzyme technology platforms, leveraging its expertise in both life sciences and materials to create new bio-based polymers and intermediates.
On the biotechnology side, Novozymes—the world’s largest industrial enzyme producer—has announced new collaborations with polymer manufacturers to scale up enzymatic polymerization processes, particularly for polyesters and polyamides. These partnerships are aimed at both improving process efficiency and reducing the environmental footprint of polymer production. DuPont has also been active, building on its long-standing work in bio-based materials and enzymes to form joint ventures and licensing agreements targeting high-performance, renewable polymers.
Startups and scale-ups are increasingly targets for strategic investment and acquisition. Companies such as Carbios, which specializes in enzymatic recycling and synthesis of plastics, have secured additional funding rounds and entered into joint development agreements with major packaging and consumer goods firms. These deals are often structured to accelerate commercialization and secure supply agreements for bio-based or recycled polymers.
Venture capital interest remains robust, with dedicated funds and corporate investors backing early-stage companies developing novel enzyme platforms for polymer synthesis. The trend is reinforced by growing regulatory and consumer pressure for sustainable materials, as well as by advances in enzyme engineering and process scale-up.
Looking ahead, the next few years are expected to see further consolidation as large chemical and materials companies seek to acquire or partner with innovative enzyme technology providers. The competitive landscape is likely to be shaped by the ability to deliver cost-effective, scalable, and high-performance bio-based polymers, with strategic alliances and M&A activity playing a central role in technology deployment and market expansion.
Future Outlook: Innovation Roadmap and Market Opportunities Through 2030
Enzyme-catalyzed polymer synthesis is poised for significant growth and innovation through 2030, driven by the convergence of green chemistry, biotechnology, and the increasing demand for sustainable materials. As of 2025, the sector is witnessing a transition from laboratory-scale demonstrations to early-stage industrial adoption, with several key players and collaborative initiatives shaping the innovation roadmap.
Major chemical and biotechnology companies are investing in enzyme engineering to improve the efficiency, selectivity, and scalability of polymerization processes. For example, BASF and DSM have both announced R&D programs focused on biocatalysis for specialty polymers, targeting applications in packaging, automotive, and medical devices. These efforts are complemented by partnerships with enzyme specialists such as Novozymes, which is leveraging its expertise in industrial enzymes to develop tailored biocatalysts for polymer synthesis.
The market outlook is underpinned by growing regulatory and consumer pressure to reduce the environmental footprint of plastics. Enzyme-catalyzed routes offer advantages such as milder reaction conditions, reduced energy consumption, and the ability to use renewable feedstocks. In 2025, pilot-scale production of polyesters and polyamides using lipase and cutinase enzymes is underway, with companies like DuPont and Arkema exploring commercial-scale implementation for high-value applications.
Looking ahead, the next few years are expected to see:
- Expansion of enzyme libraries through protein engineering and directed evolution, enabling the synthesis of novel polymers with tunable properties.
- Integration of enzyme-catalyzed steps into existing polymer manufacturing lines, reducing transition costs and accelerating adoption.
- Emergence of start-ups and spin-offs, particularly in Europe and North America, focused on biodegradable and bio-based polymers for packaging and textiles.
- Collaborative consortia involving industry, academia, and government agencies to address scale-up challenges and standardize performance metrics.
By 2030, enzyme-catalyzed polymer synthesis is projected to capture a growing share of the specialty and performance polymer markets, especially where sustainability and regulatory compliance are critical. The sector’s trajectory will depend on continued advances in enzyme technology, cost competitiveness, and the ability to demonstrate clear environmental benefits at scale. Companies with strong biocatalysis capabilities and established supply chains, such as BASF, Novozymes, and DSM, are well positioned to lead this transformation.