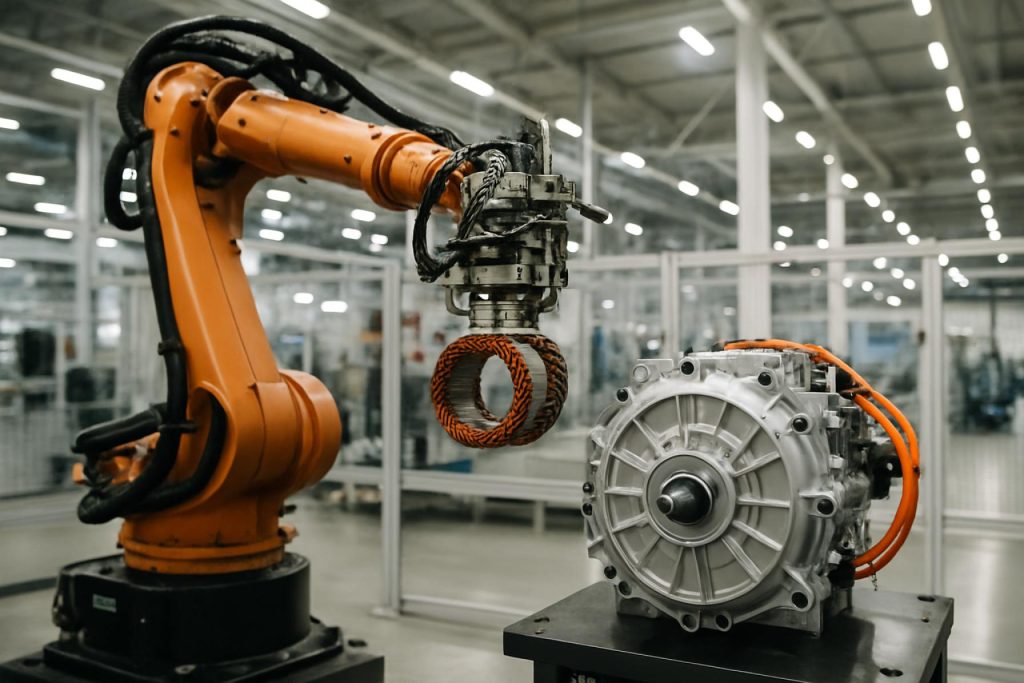
EV Motor Manufacturing in 2025: How Innovation, Supply Chains, and Global Policy Are Powering an 18% Annual Growth Surge. Explore the Technologies and Market Forces Shaping the Next Five Years.
- Executive Summary: Key Trends and Market Outlook (2025–2030)
- Market Size, Growth Rate, and Regional Breakdown
- Major Players and Competitive Landscape
- Technological Innovations in EV Motor Design and Materials
- Supply Chain Dynamics and Raw Material Sourcing
- Policy, Regulation, and Incentives Impacting EV Motor Manufacturing
- Sustainability Initiatives and Environmental Considerations
- Emerging Markets and Global Expansion Strategies
- Challenges: Cost, Scalability, and Talent Shortages
- Future Outlook: Forecasts, Opportunities, and Strategic Recommendations
- Sources & References
Executive Summary: Key Trends and Market Outlook (2025–2030)
The electric vehicle (EV) motor manufacturing sector is entering a pivotal phase in 2025, marked by rapid technological advancements, capacity expansions, and intensifying competition among global automakers and suppliers. As governments worldwide reinforce emissions regulations and incentivize electrification, the demand for high-efficiency, cost-effective electric motors is accelerating. Leading automotive manufacturers such as Tesla, Inc., Volkswagen AG, and Toyota Motor Corporation are scaling up in-house motor production and deepening collaborations with specialized suppliers to secure critical components and drive innovation.
A defining trend for 2025–2030 is the shift toward advanced motor technologies, including permanent magnet synchronous motors (PMSM), induction motors, and emerging axial flux designs. Companies like Nidec Corporation and Robert Bosch GmbH are investing heavily in R&D to enhance power density, efficiency, and manufacturability. For instance, Nidec Corporation has announced plans to expand its global production capacity to meet surging OEM demand, targeting over 10 million e-axle units annually by the late 2020s. Meanwhile, Robert Bosch GmbH continues to develop integrated drive modules, aiming to streamline assembly and reduce system costs for automakers.
Supply chain resilience and localization are also shaping the market outlook. In response to geopolitical uncertainties and critical material constraints—especially for rare earth magnets—manufacturers are diversifying sourcing strategies and exploring alternative motor topologies. Toyota Motor Corporation and Hyundai Motor Company are actively developing rare-earth-reduced and rare-earth-free motor technologies to mitigate supply risks and ensure long-term sustainability.
Looking ahead to 2030, the EV motor manufacturing landscape is expected to be characterized by further vertical integration, automation, and digitalization of production lines. Major players are investing in smart factories and advanced quality control systems to boost throughput and maintain competitiveness. The global EV market’s projected growth—driven by both passenger and commercial segments—will continue to fuel demand for innovative motor solutions, with Asia, Europe, and North America remaining key production hubs. As a result, the sector is poised for robust expansion, with leading companies leveraging scale, technology, and supply chain agility to capture emerging opportunities.
Market Size, Growth Rate, and Regional Breakdown
The global electric vehicle (EV) motor manufacturing sector is experiencing robust growth in 2025, driven by accelerating EV adoption, regulatory mandates, and technological advancements. As of 2025, the worldwide demand for EV motors is closely tied to the surging production of battery electric vehicles (BEVs) and plug-in hybrid electric vehicles (PHEVs), with major automakers scaling up their electrification strategies.
Asia-Pacific remains the dominant region in EV motor manufacturing, led by China, which accounts for the largest share of both EV production and motor supply. Chinese companies such as BYD Company Limited and Geely Automobile Holdings have vertically integrated operations, manufacturing both vehicles and key components, including traction motors. BYD in particular has expanded its in-house motor production capacity to support its rapidly growing EV lineup, while also supplying motors to other OEMs.
Japan and South Korea also play significant roles, with companies like Nidec Corporation and LG Corporation investing in new facilities and R&D to meet rising global demand. Nidec has announced plans to increase its annual production capacity for e-axle systems, which integrate motors, inverters, and gearboxes, targeting both domestic and international automakers.
Europe is witnessing rapid expansion in EV motor manufacturing, spurred by stringent emissions regulations and ambitious electrification targets. German automakers such as Volkswagen AG and BMW Group have invested heavily in localizing motor production. Volkswagen has established dedicated e-motor production lines at its Kassel plant, aiming to supply millions of units annually for its MEB platform vehicles. Similarly, BMW Group is ramping up in-house motor manufacturing to reduce reliance on external suppliers and enhance supply chain resilience.
In North America, the United States is scaling up domestic EV motor production, with companies like Tesla, Inc. and Ford Motor Company investing in new manufacturing lines and advanced motor technologies. Tesla continues to innovate with its proprietary motor designs, including the use of permanent magnet and induction motors across its vehicle lineup. Ford is expanding its EV manufacturing footprint, including motor assembly, to support its growing portfolio of electric models.
Looking ahead, the EV motor manufacturing market is projected to maintain double-digit annual growth rates through the late 2020s, underpinned by increasing EV penetration, ongoing investments in capacity expansion, and the emergence of new players. Regional supply chain localization, especially in Europe and North America, is expected to intensify as governments and OEMs seek to secure critical components and reduce geopolitical risks.
Major Players and Competitive Landscape
The global EV motor manufacturing sector in 2025 is characterized by intense competition among established automotive giants, specialized component suppliers, and emerging technology firms. The landscape is shaped by rapid technological advancements, increasing production capacities, and strategic partnerships aimed at securing supply chains and accelerating innovation.
Among the leading players, Tesla, Inc. continues to set benchmarks in EV motor efficiency and vertical integration. Tesla’s proprietary permanent magnet synchronous reluctance motors, used in its Model 3 and Model Y, are produced at its Gigafactories, with ongoing investments to scale output and reduce rare earth dependency. The company’s in-house approach to motor design and manufacturing provides a competitive edge in cost and performance.
Traditional automotive manufacturers are also expanding their EV motor capabilities. Volkswagen AG has ramped up production of its APP310 and APP550 electric drive units at its component plants, supporting the group’s ambitious electrification targets. Volkswagen’s strategy includes localizing motor production in key markets to mitigate supply chain risks and comply with regional content requirements.
Japanese manufacturers remain influential, with Nidec Corporation emerging as a global leader in e-axle and traction motor supply. Nidec’s expansion of manufacturing facilities in Europe, China, and North America is aimed at meeting surging demand from both established automakers and new entrants. The company’s focus on modular, scalable motor platforms positions it as a preferred supplier for a wide range of EV models.
In China, BYD Company Limited and Geely Automobile Holdings Limited are notable for their vertically integrated EV production, including in-house motor manufacturing. BYD’s “Blade” motor technology and Geely’s investments in high-efficiency drive systems underscore China’s growing influence in the global EV supply chain.
Tier-1 suppliers such as Robert Bosch GmbH and ZF Friedrichshafen AG are also pivotal, supplying advanced electric drive modules and integrated e-axle systems to multiple OEMs. Bosch’s eAxle and ZF’s modular e-drive platforms are being adopted in a variety of passenger and commercial EVs, reflecting the trend toward standardized, scalable solutions.
Looking ahead, the competitive landscape is expected to intensify as new entrants, including technology firms and startups, leverage innovations in materials, manufacturing processes, and digitalization. Strategic alliances, joint ventures, and localization of production will remain key themes as companies strive to secure market share and respond to evolving regulatory and consumer demands.
Technological Innovations in EV Motor Design and Materials
The landscape of EV motor manufacturing in 2025 is characterized by rapid technological innovation, with a strong focus on efficiency, sustainability, and cost reduction. One of the most significant trends is the shift toward rare-earth-free and reduced-rare-earth motor designs. Traditional permanent magnet synchronous motors (PMSMs), which rely heavily on rare earth elements like neodymium and dysprosium, are being re-engineered to mitigate supply chain risks and environmental concerns. For example, Nissan Motor Corporation has developed a magnet-free induction motor for its latest EV models, aiming to reduce dependence on critical materials while maintaining performance.
Another major innovation is the adoption of hairpin winding technology, which enhances copper fill factor and thermal management in stators. This approach, increasingly implemented by manufacturers such as Robert Bosch GmbH, allows for higher power density and improved efficiency, directly contributing to longer vehicle range and reduced energy consumption. Bosch’s e-motor production lines in Europe and China are now equipped to mass-produce motors with this advanced winding technique.
Material science advancements are also shaping the future of EV motors. Companies like Tesla, Inc. are experimenting with silicon carbide (SiC) inverters and advanced lamination steels to minimize core losses and boost overall drivetrain efficiency. Tesla’s in-house motor manufacturing integrates these materials to achieve industry-leading performance metrics, as seen in their latest Model S and Model 3 platforms.
The integration of axial flux motor technology is gaining momentum, particularly for high-performance and space-constrained applications. Mercedes-Benz Group AG has announced plans to incorporate axial flux motors, which offer superior power-to-weight ratios, into select upcoming EV models. This technology, enabled by new manufacturing processes and materials, is expected to become more prevalent as production scalability improves.
Looking ahead, the next few years will likely see further automation and digitalization of EV motor manufacturing. Companies such as Siemens AG are deploying advanced robotics, AI-driven quality control, and digital twins to optimize production lines, reduce defects, and accelerate time-to-market. These innovations are essential for meeting the surging global demand for electric vehicles and for maintaining competitiveness in a rapidly evolving sector.
In summary, 2025 marks a pivotal year for EV motor manufacturing, with ongoing breakthroughs in design, materials, and production processes. The industry’s trajectory points toward motors that are more efficient, sustainable, and adaptable to diverse vehicle architectures, setting the stage for continued growth and innovation.
Supply Chain Dynamics and Raw Material Sourcing
The supply chain dynamics and raw material sourcing for EV motor manufacturing in 2025 are shaped by a combination of surging global demand, geopolitical factors, and technological innovation. Electric vehicle (EV) motors, particularly those using permanent magnets, rely heavily on critical raw materials such as neodymium, dysprosium, and praseodymium—rare earth elements (REEs) predominantly sourced from a limited number of countries. As of 2025, Tesla, Inc., BYD Company Limited, and Volkswagen AG are among the leading automakers investing in securing stable supplies of these materials, often through direct partnerships with mining companies or by supporting recycling initiatives.
China continues to dominate the global supply of rare earths, accounting for over 60% of global production and refining capacity. This concentration has prompted manufacturers to diversify their sourcing strategies and invest in alternative supply chains. For example, General Motors Company has announced plans to source rare earth materials from North America and Australia, aiming to reduce reliance on single-region suppliers and enhance supply chain resilience. Similarly, LG Energy Solution and Samsung SDI Co., Ltd. are exploring partnerships with non-Chinese suppliers to secure long-term access to critical minerals.
In response to supply chain vulnerabilities, several automakers and motor manufacturers are accelerating the development of magnet-free motor technologies, such as induction and switched reluctance motors, which reduce or eliminate the need for rare earths. Tesla, Inc. has already implemented induction motors in some of its models, and is actively researching next-generation motor designs to further decrease raw material dependency.
Recycling and circular economy initiatives are gaining traction as well. Companies like Robert Bosch GmbH and Nidec Corporation are investing in processes to recover rare earths and copper from end-of-life motors, aiming to create closed-loop supply chains and reduce environmental impact. These efforts are supported by industry bodies such as the European Automobile Manufacturers’ Association, which advocates for sustainable sourcing and recycling standards across the sector.
Looking ahead, the outlook for EV motor manufacturing supply chains in the next few years is characterized by ongoing efforts to localize raw material sourcing, diversify suppliers, and innovate in motor design. While challenges remain—particularly regarding rare earth availability and price volatility—industry leaders are proactively adapting their strategies to ensure stable, sustainable, and scalable production as global EV adoption accelerates.
Policy, Regulation, and Incentives Impacting EV Motor Manufacturing
Policy, regulation, and government incentives are playing a pivotal role in shaping the landscape of EV motor manufacturing in 2025 and the coming years. As nations intensify their commitments to decarbonization and clean mobility, regulatory frameworks are directly influencing the pace and direction of investment in electric vehicle (EV) motor production, supply chain localization, and technology innovation.
In the United States, the Inflation Reduction Act (IRA) continues to be a major driver for domestic EV motor manufacturing. The IRA provides substantial tax credits and incentives for automakers and component suppliers that source critical materials and manufacture EV components, including motors, within North America. This has led to a surge in announcements of new or expanded motor production facilities by companies such as General Motors and Ford Motor Company, both of which are investing in vertically integrated EV supply chains to meet eligibility requirements for federal incentives.
The European Union is also advancing its regulatory agenda with the Fit for 55 package and the proposed Euro 7 emissions standards, which are accelerating the transition to electric mobility. These policies are compelling automakers and suppliers to ramp up local EV motor manufacturing to comply with stricter emissions targets and to benefit from incentives for European-made components. Companies like Volkswagen AG and Stellantis N.V. are investing in new motor production lines and gigafactories across the continent, aiming to secure supply chain resilience and regulatory compliance.
In China, the world’s largest EV market, the government continues to support domestic EV motor manufacturing through a combination of purchase subsidies, tax exemptions, and industrial policy. The “Made in China 2025” initiative and ongoing New Energy Vehicle (NEV) policies are fostering rapid expansion of local motor production by leading firms such as BYD Company Limited and Geely Auto Group. These companies are not only scaling up to meet domestic demand but are also positioning themselves as global suppliers of advanced EV motors.
Looking ahead, the interplay of policy, regulation, and incentives is expected to further accelerate investment in advanced motor technologies, such as rare-earth-free designs and high-efficiency architectures. Governments are increasingly linking incentives to sustainability criteria, including local content requirements and environmental standards, which will shape the competitive dynamics of EV motor manufacturing through 2025 and beyond.
Sustainability Initiatives and Environmental Considerations
Sustainability is a central focus in EV motor manufacturing as the industry enters 2025, with leading companies implementing initiatives to reduce environmental impact across the supply chain. The shift toward electrification is inherently aimed at lowering greenhouse gas emissions, but manufacturers are increasingly scrutinizing the full lifecycle of electric vehicle (EV) motors—from raw material sourcing to end-of-life recycling.
A key area of attention is the reduction of rare earth element usage in permanent magnet motors. Companies such as Tesla, Inc. have announced plans to eliminate rare earths from future motor designs, citing both environmental and supply chain concerns. This move is expected to influence industry standards, as rare earth mining is associated with significant ecological disruption and geopolitical risk. Similarly, BMW Group has developed fifth-generation eDrive motors that do not require rare earths, demonstrating a commitment to sustainable innovation.
Energy efficiency in manufacturing processes is another priority. Volkswagen AG has invested in green electricity for its EV component plants, aiming to achieve carbon-neutral production. The company’s Salzgitter facility, for example, is powered by renewable energy and incorporates closed-loop systems for aluminum and copper recycling. Nidec Corporation, a major global supplier of EV motors, has also set targets to reduce CO2 emissions intensity in its operations and is increasing the use of recycled materials in motor components.
Battery and motor recycling is gaining momentum as EV adoption accelerates. Stellantis N.V. has launched pilot programs for recovering and reusing critical materials from end-of-life motors, while Renault Group operates dedicated facilities for dismantling and recycling electric powertrains. These efforts are expected to scale in the coming years, supported by evolving regulations in the European Union and other regions mandating higher recycling rates and extended producer responsibility.
Looking ahead, the outlook for sustainability in EV motor manufacturing is shaped by both regulatory pressure and consumer demand for greener vehicles. The industry is likely to see increased adoption of closed-loop material systems, further reductions in hazardous substances, and greater transparency in supply chains. As manufacturers like Hyundai Motor Company and Honda Motor Co., Ltd. expand their EV portfolios, sustainability initiatives will remain a competitive differentiator and a core component of long-term strategy.
Emerging Markets and Global Expansion Strategies
The global landscape for EV motor manufacturing is undergoing rapid transformation in 2025, driven by surging demand for electric vehicles (EVs) and strategic expansion into emerging markets. Major manufacturers are intensifying efforts to localize production, secure supply chains, and tap into new consumer bases, particularly in Asia, Latin America, and Africa.
China remains the epicenter of EV motor manufacturing, with companies such as BYD Company Limited and Geely Automobile Holdings expanding both domestic capacity and overseas operations. In 2025, BYD continues to scale up its global footprint, with new plants and joint ventures in Southeast Asia and Europe, aiming to reduce logistics costs and adapt to local market requirements. Geely, meanwhile, is leveraging its international brands and partnerships to establish assembly and component facilities in regions like Eastern Europe and South America.
India is emerging as a significant player, with government incentives and a growing domestic market attracting investments from both local and international manufacturers. Tata Motors Limited and Ashok Leyland are ramping up EV motor production, while global suppliers such as Robert Bosch GmbH are expanding their Indian operations to serve both domestic and export markets. The Indian government’s Production Linked Incentive (PLI) scheme is expected to further accelerate localization of advanced motor technologies through 2026.
In Southeast Asia, Thailand and Indonesia are positioning themselves as regional EV manufacturing hubs. PTT Public Company Limited in Thailand and PT Astra International Tbk in Indonesia are investing in new facilities and partnerships to produce motors and related components, targeting both local assembly and export opportunities.
European automakers are also adapting their global strategies. Volkswagen AG and Renault Group are localizing EV motor production in Eastern Europe and North Africa to mitigate supply chain risks and comply with regional content requirements. These moves are complemented by partnerships with local suppliers and technology transfer initiatives.
Looking ahead, the next few years will see intensified competition for market share in emerging economies, with manufacturers focusing on cost optimization, local sourcing, and flexible production models. The expansion of EV motor manufacturing into new geographies is expected to drive innovation, lower costs, and accelerate the global transition to electric mobility.
Challenges: Cost, Scalability, and Talent Shortages
The rapid expansion of electric vehicle (EV) motor manufacturing in 2025 is accompanied by significant challenges, particularly in the areas of cost control, scalability, and talent acquisition. As automakers and suppliers race to meet surging global demand, these obstacles are shaping the competitive landscape and influencing strategic decisions across the industry.
Cost remains a central concern. The production of advanced EV motors—especially permanent magnet synchronous motors (PMSMs) and induction motors—relies heavily on critical materials such as rare earth elements and copper. Volatility in the prices of neodymium, dysprosium, and copper has led to unpredictable input costs, pressuring manufacturers’ margins. Companies like Tesla, Inc. and BYD Company Limited have responded by investing in supply chain integration and exploring alternative motor designs that reduce or eliminate rare earth dependency. For example, Tesla, Inc. has announced plans to develop next-generation motors that minimize rare earth usage, aiming to stabilize costs and reduce environmental impact.
Scalability is another pressing issue. The transition from pilot lines to mass production requires substantial capital investment in advanced manufacturing equipment, automation, and quality control systems. Leading suppliers such as Nidec Corporation and Robert Bosch GmbH are expanding their global manufacturing footprints, with new plants and capacity upgrades scheduled through 2026. However, scaling up production is complicated by the need to maintain tight tolerances and high efficiency in motor assembly, as well as by ongoing supply chain disruptions for key components.
Talent shortages further exacerbate these challenges. The EV motor sector requires a specialized workforce skilled in electrical engineering, advanced manufacturing, and automation. Companies report difficulties in recruiting and retaining talent, particularly in regions where the EV industry is expanding rapidly. Robert Bosch GmbH and Nidec Corporation have launched training and apprenticeship programs to address these gaps, but the pace of workforce development often lags behind industry growth.
Looking ahead, the industry is expected to continue grappling with these challenges through the remainder of the decade. Strategic investments in supply chain resilience, automation, and workforce development will be critical for manufacturers seeking to maintain competitiveness and meet the ambitious production targets set by automakers worldwide.
Future Outlook: Forecasts, Opportunities, and Strategic Recommendations
The outlook for EV motor manufacturing in 2025 and the following years is shaped by accelerating electrification, evolving supply chains, and intensifying competition among global automakers and component suppliers. As governments worldwide tighten emissions regulations and set ambitious electrification targets, demand for electric vehicles (EVs) and, consequently, for advanced electric motors is expected to surge. Major automakers such as Toyota Motor Corporation, Volkswagen AG, and Ford Motor Company have announced multi-billion-dollar investments in EV production capacity, with a significant portion allocated to in-house motor development and manufacturing.
In 2025, the industry is witnessing a shift toward more efficient and compact motor technologies, such as permanent magnet synchronous motors (PMSM) and induction motors, with a growing focus on reducing reliance on rare earth materials. Companies like Tesla, Inc. are pioneering the use of innovative motor architectures, including the carbon-wrapped rotor in their Plaid models, which enhances performance and efficiency. Meanwhile, suppliers such as Robert Bosch GmbH and Nidec Corporation are scaling up production of next-generation e-axle systems and integrated drive units, aiming to supply both established automakers and emerging EV startups.
Strategically, vertical integration is becoming a key trend. Automakers are increasingly bringing motor manufacturing in-house to secure supply, optimize performance, and protect intellectual property. For example, Hyundai Motor Company has expanded its EV motor production lines, while BYD Company Limited continues to leverage its vertically integrated model, producing motors, batteries, and power electronics internally. This approach is expected to enhance supply chain resilience amid ongoing geopolitical uncertainties and raw material price volatility.
Looking ahead, opportunities abound in the development of rare-earth-free motor technologies, digital manufacturing, and recycling of motor components. The adoption of advanced manufacturing techniques, such as automation and AI-driven quality control, is anticipated to improve efficiency and reduce costs. Strategic recommendations for industry players include investing in R&D for alternative motor designs, forging partnerships with material suppliers, and expanding global manufacturing footprints to meet regional demand and regulatory requirements.
In summary, the EV motor manufacturing sector in 2025 is poised for robust growth, driven by technological innovation, strategic investments, and the global push toward sustainable mobility. Companies that prioritize agility, vertical integration, and continuous innovation are likely to secure a competitive edge in the evolving landscape.
Sources & References
- Volkswagen AG
- Toyota Motor Corporation
- Robert Bosch GmbH
- Hyundai Motor Company
- BYD Company Limited
- Geely Automobile Holdings
- LG Corporation
- ZF Friedrichshafen AG
- Nissan Motor Corporation
- Siemens AG
- European Automobile Manufacturers’ Association
- General Motors
- Stellantis N.V.
- Volkswagen AG
- Renault Group
- Ashok Leyland
- PT Astra International Tbk