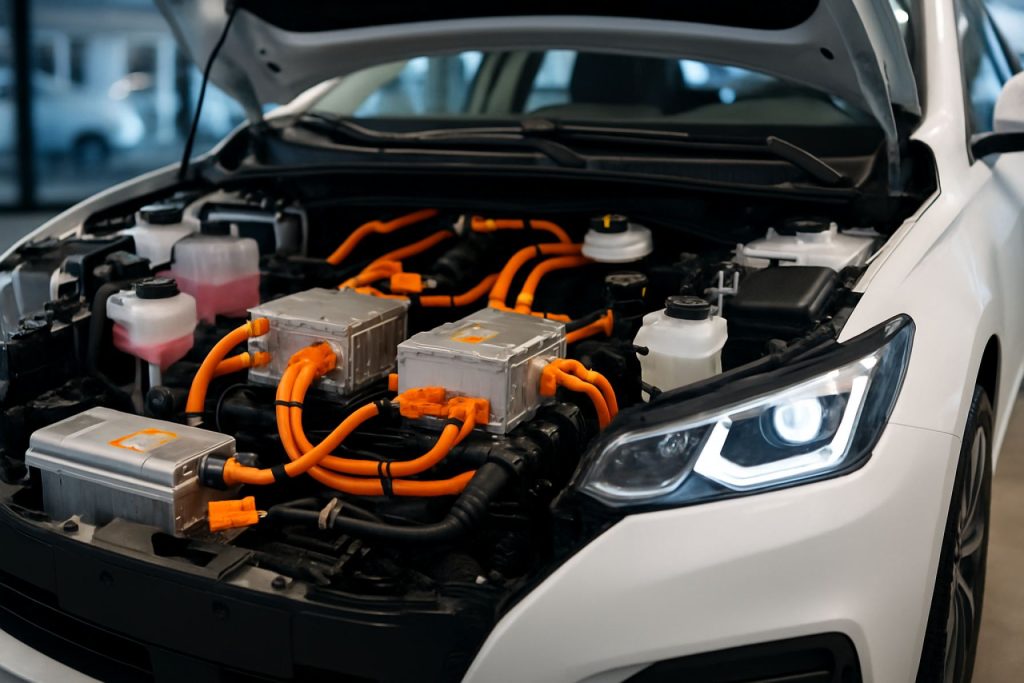
The Future of EV Powertrain & Drivetrain Systems in 2025: Unveiling Breakthrough Technologies, Market Dynamics, and Strategic Opportunities for the Next Five Years. Discover How Electrification is Redefining Mobility and Driving Unprecedented Growth.
- Executive Summary: Key Trends and Market Outlook (2025–2030)
- Global Market Size, Growth Rate, and Forecasts (2025–2030)
- Technological Innovations in EV Powertrain & Drivetrain Systems
- Competitive Landscape: Leading OEMs and Suppliers
- Battery Integration and Thermal Management Advances
- Emerging Architectures: e-Axles, In-Wheel Motors, and Modular Platforms
- Regulatory Drivers and Industry Standards (e.g., SAE, IEEE)
- Supply Chain Challenges and Opportunities
- Regional Analysis: North America, Europe, Asia-Pacific, and Rest of World
- Future Outlook: Strategic Roadmaps and Investment Priorities
- Sources & References
Executive Summary: Key Trends and Market Outlook (2025–2030)
The electric vehicle (EV) powertrain and drivetrain sector is entering a pivotal phase in 2025, marked by rapid technological evolution, intensified competition, and a clear trajectory toward higher efficiency and integration. As global EV adoption accelerates, automakers and suppliers are investing heavily in next-generation powertrain architectures, with a focus on cost reduction, performance, and sustainability.
A defining trend is the shift toward highly integrated drive units, combining electric motors, inverters, and reduction gears into compact, modular systems. Leading manufacturers such as Robert Bosch GmbH and ZF Friedrichshafen AG are commercializing advanced e-axle solutions that streamline assembly, reduce weight, and improve energy efficiency. For example, ZF’s latest e-drive platforms are designed for scalability across multiple vehicle segments, supporting both 400V and 800V architectures to enable faster charging and higher performance.
Permanent magnet synchronous motors (PMSMs) remain the dominant technology for EV traction, but there is growing momentum behind alternative motor designs that reduce or eliminate rare earth material dependence. Companies like Nidec Corporation and BorgWarner Inc. are advancing induction and switched reluctance motor technologies, aiming to address supply chain risks and cost volatility associated with rare earths.
The adoption of silicon carbide (SiC) and gallium nitride (GaN) semiconductors in inverters is another key development, enabling higher power densities and improved thermal management. Infineon Technologies AG and STMicroelectronics N.V. are scaling up production of SiC-based power modules, which are increasingly specified by OEMs for their efficiency gains, particularly in 800V systems.
Looking ahead to 2030, the market outlook is shaped by regulatory pressures for lower emissions, consumer demand for longer range, and the need for cost-effective mass-market solutions. Automakers such as Tesla, Inc., Volkswagen AG, and Hyundai Motor Company are investing in in-house powertrain development to differentiate on performance and cost. Meanwhile, partnerships between OEMs and Tier 1 suppliers are expected to deepen, with joint ventures and technology-sharing agreements accelerating innovation cycles.
In summary, the 2025–2030 period will see EV powertrain and drivetrain systems become more efficient, modular, and sustainable, with a strong emphasis on vertical integration and supply chain resilience. The sector’s evolution will be critical to achieving broader EV adoption and meeting global decarbonization targets.
Global Market Size, Growth Rate, and Forecasts (2025–2030)
The global market for electric vehicle (EV) powertrain and drivetrain systems is poised for robust expansion in 2025 and the following years, driven by accelerating EV adoption, regulatory mandates, and rapid technological innovation. As of 2025, leading automakers and suppliers are scaling up production capacities and investing in next-generation powertrain architectures to meet surging demand and stricter emissions targets.
Major industry players such as Tesla, Inc., Volkswagen AG, BYD Company Ltd., and Hyundai Motor Company are expanding their EV portfolios, each integrating advanced powertrain systems that emphasize efficiency, modularity, and cost reduction. For example, Tesla, Inc. continues to refine its proprietary drive units and inverter technologies, while Volkswagen AG is rolling out its scalable MEB platform across multiple brands, supporting both rear- and all-wheel-drive configurations.
On the supplier side, companies like Robert Bosch GmbH, ZF Friedrichshafen AG, and BorgWarner Inc. are investing heavily in integrated e-axle systems, high-efficiency electric motors, and next-generation inverters. Robert Bosch GmbH has announced significant expansion of its e-mobility product lines, while ZF Friedrichshafen AG is scaling up production of its modular e-drive platforms to serve both passenger and commercial EV segments.
Market data from industry bodies and company disclosures indicate that the global EV powertrain and drivetrain market is expected to grow at a compound annual growth rate (CAGR) exceeding 20% between 2025 and 2030, with total market value projected to surpass $100 billion by the end of the decade. This growth is underpinned by rising EV penetration in key markets such as China, Europe, and North America, where government incentives and zero-emission vehicle mandates are accelerating the transition from internal combustion engines to electric drivetrains.
Looking ahead, the next few years will see further advancements in powertrain efficiency, the adoption of silicon carbide (SiC) and gallium nitride (GaN) semiconductors in inverters, and the proliferation of 800V architectures for faster charging and improved performance. Strategic partnerships between automakers and technology suppliers—such as those between Hyundai Motor Company and BorgWarner Inc.—are expected to accelerate innovation and cost reductions, solidifying the foundation for mass-market EV adoption through 2030.
Technological Innovations in EV Powertrain & Drivetrain Systems
The landscape of electric vehicle (EV) powertrain and drivetrain systems is undergoing rapid transformation in 2025, driven by advances in efficiency, integration, and materials. Automakers and suppliers are focusing on innovations that enhance range, performance, and cost-effectiveness, while also addressing sustainability and scalability for mass-market adoption.
A key trend is the shift toward highly integrated drive units, combining electric motors, inverters, and reduction gears into compact assemblies. This integration reduces weight, complexity, and manufacturing costs. For example, Robert Bosch GmbH has developed eAxle systems that consolidate these components, offering scalable solutions for various vehicle segments. Similarly, ZF Friedrichshafen AG has introduced its next-generation e-drives, which feature silicon carbide (SiC) power electronics for improved efficiency and thermal management.
Permanent magnet synchronous motors (PMSMs) remain the dominant architecture for EVs due to their high power density and efficiency. However, concerns over rare earth material supply have spurred research into alternative motor designs. Nidec Corporation is advancing induction and switched reluctance motors that reduce or eliminate rare earth usage, aiming to secure supply chains and lower costs.
Another significant innovation is the adoption of 800-volt architectures, which enable faster charging and higher power output. Hyundai Motor Company and Dr. Ing. h.c. F. Porsche AG have both commercialized 800V platforms, setting new benchmarks for charging speed and drivetrain efficiency. This trend is expected to proliferate across premium and eventually mainstream EV models in the coming years.
Thermal management is also a focal point, as efficient cooling of motors, inverters, and batteries is critical for sustained performance. LG Electronics Inc. and Schaeffler AG are developing advanced cooling solutions, including oil-cooled motors and integrated thermal modules, to support higher power densities and reliability.
Looking ahead, the next few years will see further adoption of modular, scalable powertrain platforms, enabling automakers to rapidly deploy new models with varying performance and range characteristics. The convergence of digital control, advanced materials, and integrated design is expected to yield EV drivetrains that are lighter, more efficient, and more affordable, accelerating the transition to electrified mobility worldwide.
Competitive Landscape: Leading OEMs and Suppliers
The competitive landscape for EV powertrain and drivetrain systems in 2025 is characterized by rapid innovation, strategic partnerships, and increasing vertical integration among leading OEMs and suppliers. As global EV adoption accelerates, automakers and tier-one suppliers are investing heavily in next-generation electric drive technologies to enhance efficiency, performance, and cost-effectiveness.
Among OEMs, Tesla, Inc. continues to set benchmarks in integrated powertrain design, leveraging in-house development of motors, inverters, and gearboxes. Tesla’s proprietary drive units, featuring permanent magnet synchronous motors and silicon carbide inverters, are widely recognized for their efficiency and scalability across its vehicle lineup. The company’s vertical integration strategy extends to battery and power electronics manufacturing, reinforcing its competitive edge.
European automakers are also advancing their EV powertrain capabilities. Volkswagen AG has rolled out its modular electric drive matrix (MEB) platform, enabling scalable production of rear- and all-wheel-drive EVs. The MEB platform’s standardized drivetrain modules are used across multiple brands within the group, including Audi, Skoda, and SEAT, supporting cost reduction and rapid model proliferation. Similarly, BMW Group is deploying its fifth-generation eDrive technology, which integrates the electric motor, transmission, and power electronics into a single housing, improving power density and manufacturing flexibility.
In Asia, Toyota Motor Corporation and Hyundai Motor Company are scaling up their EV portfolios with proprietary e-axle and integrated drive systems. Hyundai’s E-GMP platform, for example, features a compact powertrain layout and supports high-voltage architectures for faster charging and improved performance.
On the supplier side, Robert Bosch GmbH and ZF Friedrichshafen AG are leading providers of electric drive modules and e-axles, supplying both established and emerging automakers. Bosch’s eAxle integrates motor, power electronics, and transmission, while ZF’s modular e-drive systems are designed for flexible application across passenger and commercial vehicles. BorgWarner Inc. and Schaeffler AG are also expanding their portfolios with high-efficiency electric motors, reduction gears, and complete drivetrain solutions.
Looking ahead, the competitive landscape is expected to intensify as OEMs and suppliers race to deliver higher power densities, improved thermal management, and lower system costs. Strategic alliances, such as joint ventures for e-motor and inverter production, are likely to proliferate, while advances in silicon carbide semiconductors and integrated drive units will further differentiate market leaders.
Battery Integration and Thermal Management Advances
Battery integration and thermal management are pivotal to the evolution of EV powertrain and drivetrain systems, with 2025 marking a period of rapid innovation and deployment. As electric vehicles (EVs) become mainstream, automakers and suppliers are focusing on optimizing battery placement, improving energy density, and deploying advanced thermal management solutions to enhance performance, safety, and longevity.
A key trend is the shift toward cell-to-pack (CTP) and cell-to-chassis (CTC) integration, which eliminates traditional module structures to increase volumetric efficiency and reduce weight. Contemporary Amperex Technology Co., Limited (CATL), a global battery leader, has commercialized CTP technology, enabling higher energy density and simplified assembly. This approach is being adopted by major automakers, including Tesla, Inc., which has implemented structural battery packs in its latest platforms, integrating batteries directly into the vehicle chassis for improved rigidity and crash safety.
Thermal management is equally critical, especially as fast-charging and high-performance EVs proliferate. Liquid cooling systems are now standard in most new EVs, replacing earlier air-cooled designs. LG Energy Solution and Panasonic Corporation are advancing battery chemistries and pack designs that support more efficient heat dissipation. Meanwhile, Robert Bosch GmbH and Valeo are supplying integrated thermal management modules that combine battery, power electronics, and cabin climate control, optimizing energy use and extending battery life.
Emerging technologies in 2025 include the use of phase change materials (PCMs) and advanced heat pumps. Nissan Motor Corporation and Hyundai Motor Company are deploying heat pump systems in their latest EVs, which recover waste heat from the drivetrain to warm the cabin and battery, reducing energy consumption in cold climates. Additionally, battery suppliers are experimenting with immersion cooling, where cells are directly bathed in dielectric fluids for superior thermal control—a technology being piloted by SAIC Motor Corporation in select models.
Looking ahead, the next few years will see further integration of battery and drivetrain systems, with a focus on modular, scalable architectures and smart thermal management. These advances are expected to support longer range, faster charging, and improved safety, accelerating the global transition to electric mobility.
Emerging Architectures: e-Axles, In-Wheel Motors, and Modular Platforms
The evolution of electric vehicle (EV) powertrain and drivetrain systems is accelerating in 2025, with a strong industry focus on emerging architectures such as e-axles, in-wheel motors, and modular platforms. These innovations are reshaping how automakers design, manufacture, and scale EVs, aiming for higher efficiency, flexibility, and cost-effectiveness.
E-axle systems, which integrate electric motors, power electronics, and transmission into a single compact unit, are becoming the preferred solution for both passenger and commercial EVs. Major suppliers like Robert Bosch GmbH, ZF Friedrichshafen AG, and BorgWarner Inc. have launched next-generation e-axle platforms, offering scalable solutions from small cars to heavy-duty trucks. For example, ZF Friedrichshafen AG’s e-axle systems are now featured in several 2025 model-year vehicles, providing up to 800V architectures and supporting fast charging and high power density. These integrated systems reduce weight, improve packaging, and streamline assembly, contributing to lower total cost of ownership and enhanced vehicle performance.
In-wheel motor technology, while still in the early stages of mass adoption, is gaining traction for specific applications. Companies such as Nidec Corporation and Protean Electric are advancing in-wheel motor solutions that offer direct drive to each wheel, enabling advanced torque vectoring and unprecedented design flexibility. In 2025, pilot programs and limited production runs are underway, particularly in urban mobility vehicles and light commercial fleets, where the benefits of compactness and maneuverability are most pronounced.
Modular EV platforms, often referred to as skateboard architectures, are now the foundation for most new EV launches. Automakers such as Volkswagen AG (with its MEB platform), Hyundai Motor Company (E-GMP), and Toyota Motor Corporation (e-TNGA) are leveraging these platforms to rapidly expand their EV portfolios. These architectures allow for flexible battery and drivetrain configurations, supporting a wide range of vehicle types and sizes while optimizing manufacturing efficiency and reducing development time.
Looking ahead, the convergence of e-axle, in-wheel motor, and modular platform technologies is expected to further accelerate EV adoption. As these systems mature, industry stakeholders anticipate improvements in range, performance, and affordability, positioning EVs for mainstream acceptance across global markets in the coming years.
Regulatory Drivers and Industry Standards (e.g., SAE, IEEE)
The regulatory landscape and industry standards for EV powertrain and drivetrain systems are rapidly evolving as governments and industry bodies push for higher efficiency, safety, and interoperability in electric vehicles. In 2025, regulatory drivers are primarily shaped by increasingly stringent emissions targets, safety requirements, and harmonization efforts across major automotive markets.
The United States, European Union, and China continue to lead with aggressive electrification mandates. The European Union’s CO2 fleet targets for 2025 and 2030 are compelling automakers to accelerate the adoption of advanced electric powertrains, including multi-speed transmissions and high-efficiency inverters. The U.S. Environmental Protection Agency’s updated vehicle emissions standards, effective from model year 2027, are already influencing 2025 product planning, pushing OEMs to invest in next-generation drivetrain architectures and battery integration (U.S. Environmental Protection Agency).
Industry standards are critical for ensuring safety, performance, and interoperability. The Society of Automotive Engineers (SAE International) continues to update its J-standard series, which cover everything from high-voltage wiring (J3068) to electric drive system safety (J2980). In 2025, SAE’s focus includes harmonizing standards for high-voltage connectors and communication protocols between powertrain components, supporting modular and scalable drivetrain designs.
The Institute of Electrical and Electronics Engineers (IEEE) is also active, with standards such as IEEE 2030.1.1 addressing interoperability and safety for electric vehicle powertrains and charging systems. These standards are increasingly referenced in regulatory frameworks and procurement specifications, especially for commercial and fleet vehicles.
China’s GB/T standards, managed by the Standardization Administration of China (Standardization Administration of China), are being updated to align more closely with international norms, particularly in areas like battery safety and drivetrain communication protocols. This harmonization is crucial for global OEMs and suppliers seeking to streamline development and certification processes across regions.
Looking ahead, regulatory and standards bodies are expected to focus on cybersecurity for drivetrain control systems, functional safety (ISO 26262), and lifecycle sustainability metrics. The convergence of standards will facilitate cross-border manufacturing and accelerate the deployment of advanced EV powertrain technologies, such as silicon carbide inverters and integrated e-axle systems, which are being commercialized by leading suppliers like Robert Bosch GmbH and ZF Friedrichshafen AG.
Supply Chain Challenges and Opportunities
The supply chain for EV powertrain and drivetrain systems is undergoing significant transformation as automakers and suppliers respond to surging demand, regulatory pressures, and technological innovation in 2025 and the coming years. The shift from internal combustion engine (ICE) to electric vehicle (EV) architectures has created both challenges and opportunities across the value chain, particularly in sourcing critical components such as electric motors, inverters, reduction gears, and high-voltage wiring.
A primary challenge is the procurement and processing of raw materials for key drivetrain components, especially rare earth elements for permanent magnet motors and copper for wiring. Leading automakers like Tesla, Inc. and Volkswagen AG have responded by vertically integrating parts of their supply chains and securing long-term contracts with mining and refining partners. For example, Tesla, Inc. has invested in direct sourcing of lithium, nickel, and rare earths to mitigate price volatility and supply disruptions.
Another challenge is the global distribution of manufacturing capacity for powertrain components. While Asia—particularly China—remains dominant in battery and motor production, European and North American automakers are accelerating local investments to reduce dependency and improve supply chain resilience. Robert Bosch GmbH, a major supplier of e-axles and inverters, has expanded its manufacturing footprint in Europe and North America to support regional OEMs and comply with local content requirements.
Opportunities are emerging for suppliers that can deliver next-generation drivetrain technologies, such as silicon carbide (SiC) inverters and integrated e-axle systems. Companies like BorgWarner Inc. and ZF Friedrichshafen AG are investing in R&D and new production lines to meet automaker demand for higher efficiency, reduced weight, and modularity. These innovations are expected to help OEMs achieve stricter efficiency and emissions targets, while also lowering total system costs.
Looking ahead, the EV powertrain supply chain is expected to become more regionalized and collaborative. Automakers are forming joint ventures with suppliers and even competitors to share risk and accelerate technology deployment. For instance, Hyundai Motor Company and LG Corporation have established joint ventures for battery and drivetrain component production. As the market matures, digitalization and supply chain transparency will be critical for managing risks and ensuring the timely delivery of high-quality components.
In summary, while the EV powertrain and drivetrain supply chain faces ongoing challenges in raw material sourcing, capacity distribution, and technology integration, it also presents significant opportunities for innovation, regional investment, and strategic partnerships in 2025 and beyond.
Regional Analysis: North America, Europe, Asia-Pacific, and Rest of World
The global landscape for EV powertrain and drivetrain systems is rapidly evolving, with distinct regional trends shaping technology adoption, manufacturing, and supply chain strategies through 2025 and beyond. North America, Europe, and Asia-Pacific remain the primary hubs for innovation and production, while the Rest of World is gradually increasing its participation, often through partnerships and localized assembly.
- North America: The United States and Canada are witnessing significant investments in EV powertrain manufacturing, driven by both established automakers and new entrants. General Motors is scaling up its Ultium platform, which features modular drive units and integrated power electronics, aiming for broad deployment across its EV lineup. Ford Motor Company is expanding its EV production capacity, with a focus on in-house e-motor and transmission development. The region is also seeing increased localization of battery and drivetrain component supply, supported by government incentives and the Inflation Reduction Act, which encourages domestic sourcing and assembly.
- Europe: European automakers are accelerating the shift to electrified powertrains, with a strong emphasis on efficiency and sustainability. Volkswagen Group is rolling out its MEB and SSP platforms, featuring scalable electric drive modules and advanced thermal management. Stellantis is investing in multiple gigafactories and e-axle production, while BMW Group is introducing fifth-generation eDrive technology with integrated motors, inverters, and transmissions. The European Union’s regulatory push for zero-emission vehicles by 2035 is accelerating R&D and supply chain localization for powertrain components.
- Asia-Pacific: The region, led by China, is the world’s largest EV market and a powerhouse in drivetrain innovation. BYD Company and Geely Auto Group are vertically integrating e-motor, inverter, and transmission production, while Toyota Motor Corporation and Nissan Motor Corporation are advancing hybrid and full-electric powertrain systems. China’s government policies continue to support domestic manufacturing and technology leadership, with a focus on high-efficiency, cost-effective drive units and next-generation silicon carbide (SiC) inverters.
- Rest of World: While adoption is slower, countries in South America, the Middle East, and Africa are beginning to assemble EVs and powertrain components, often through joint ventures with global OEMs. Local assembly of imported drivetrain kits is becoming more common, and governments are starting to introduce incentives to attract investment in EV supply chains.
Looking ahead to the next few years, regional competition and collaboration are expected to intensify, with a focus on cost reduction, supply chain resilience, and the integration of advanced materials and digital controls in EV powertrain and drivetrain systems. The interplay between local policy, global technology standards, and consumer demand will continue to shape the evolution of this critical sector.
Future Outlook: Strategic Roadmaps and Investment Priorities
The evolution of electric vehicle (EV) powertrain and drivetrain systems is set to accelerate through 2025 and beyond, as automakers and suppliers intensify investments in next-generation architectures, efficiency improvements, and vertical integration. The strategic focus is shifting from first-generation electrification to scalable, modular platforms that can underpin a wide range of models, reduce costs, and enable rapid deployment of new technologies.
Major OEMs are prioritizing the development of integrated drive units (IDUs), which combine electric motors, power electronics, and transmission into a single compact assembly. This approach, championed by companies such as Volkswagen AG and Tesla, Inc., is expected to deliver significant gains in efficiency, manufacturability, and performance. For example, Volkswagen’s MEB and SSP platforms are designed to support a broad portfolio of EVs, leveraging standardized powertrain modules to streamline production and reduce complexity. Tesla continues to push the envelope with its proprietary drive units and silicon carbide inverter technology, aiming for higher range and lower energy losses.
Suppliers are also playing a critical role in shaping the future landscape. Robert Bosch GmbH and ZF Friedrichshafen AG are investing heavily in next-generation e-axles and modular electric drive systems, targeting both passenger and commercial vehicle segments. ZF’s latest e-drive platforms, for instance, integrate advanced cooling, lightweight materials, and high-voltage architectures to support higher power densities and faster charging capabilities.
Looking ahead, the industry is expected to see a rapid adoption of 800V architectures, which enable faster charging and improved efficiency. Companies like Hyundai Motor Company and Dr. Ing. h.c. F. Porsche AG have already commercialized 800V systems, and this trend is likely to become mainstream as battery and power electronics technologies mature. Additionally, the integration of silicon carbide (SiC) semiconductors in inverters and power modules is projected to further enhance drivetrain efficiency and reduce thermal losses.
- By 2025, most leading automakers plan to localize key powertrain components, including motors and inverters, to secure supply chains and reduce costs.
- Strategic partnerships between OEMs and Tier 1 suppliers are intensifying, with joint ventures and co-development agreements focused on next-gen e-mobility platforms.
- Investment priorities are shifting toward software-defined drivetrains, enabling over-the-air updates and advanced energy management features.
In summary, the next few years will see a convergence of modularity, efficiency, and digitalization in EV powertrain and drivetrain systems, underpinned by robust investment from both automakers and suppliers. This strategic roadmap is expected to drive down costs, accelerate mass-market adoption, and set new benchmarks for performance and sustainability in the EV sector.
Sources & References
- Robert Bosch GmbH
- ZF Friedrichshafen AG
- BorgWarner Inc.
- Infineon Technologies AG
- STMicroelectronics N.V.
- Volkswagen AG
- Hyundai Motor Company
- BYD Company Ltd.
- Dr. Ing. h.c. F. Porsche AG
- LG Electronics Inc.
- Schaeffler AG
- Toyota Motor Corporation
- Contemporary Amperex Technology Co., Limited (CATL)
- Valeo
- Nissan Motor Corporation
- Protean Electric
- IEEE
- General Motors
- Stellantis
- Geely Auto Group