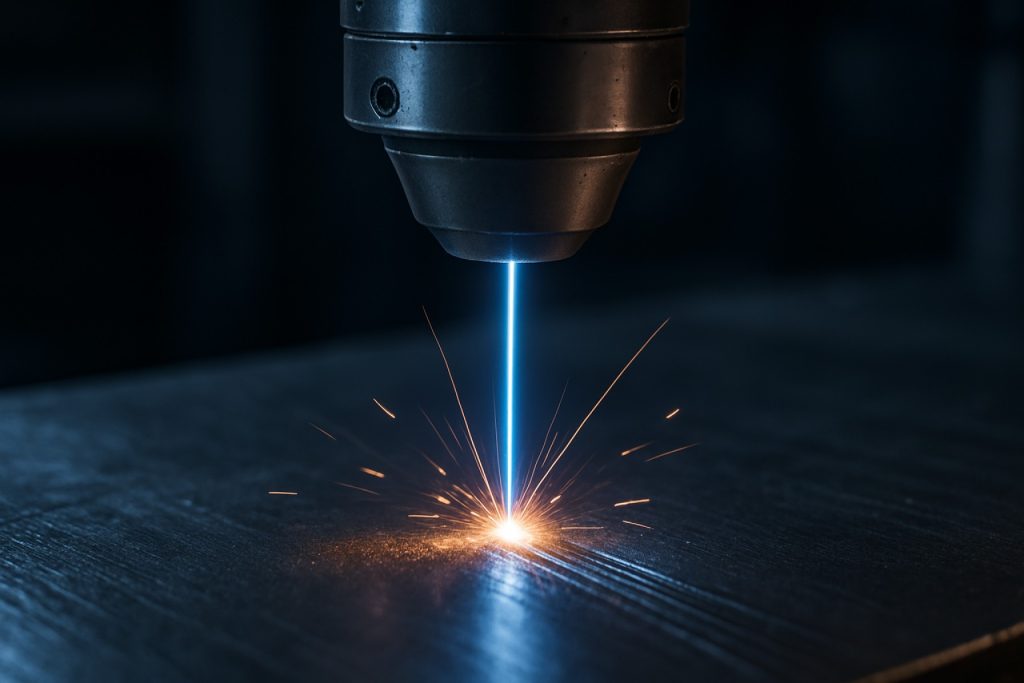
Femtosecond Laser Surface Engineering in 2025: Transforming Precision Manufacturing and Materials Science. Explore the Innovations, Market Dynamics, and Future Trajectory of Ultrafast Laser Technologies.
- Executive Summary & Key Findings
- Market Size, Growth Rate, and 2025–2029 Forecasts
- Core Technologies and Recent Innovations
- Leading Applications: Medical, Electronics, Aerospace, and Energy
- Competitive Landscape: Key Players and Strategic Initiatives
- Emerging Trends: Surface Functionalization and Micro/Nano-Structuring
- Regulatory Environment and Industry Standards
- Challenges: Technical Barriers and Scalability
- Investment, Funding, and M&A Activity
- Future Outlook: Opportunities and Strategic Recommendations
- Sources & References
Executive Summary & Key Findings
Femtosecond laser surface engineering (FLSE) has rapidly advanced into a pivotal technology for precision material processing, offering unparalleled control over surface morphology, chemistry, and function. As of 2025, the sector is witnessing robust growth, driven by increasing demand in microelectronics, medical devices, aerospace, and energy applications. The unique ability of femtosecond lasers to induce highly localized, non-thermal modifications enables the fabrication of micro- and nano-scale features with minimal collateral damage, setting new standards for quality and repeatability.
Key industry players such as TRUMPF, a global leader in industrial laser systems, and Amplitude Laser, specializing in ultrafast lasers, have expanded their femtosecond laser portfolios to address the growing need for high-throughput, high-precision surface structuring. TRUMPF has reported increased adoption of its femtosecond laser systems in semiconductor and medical device manufacturing, where surface texturing and functionalization are critical for product performance and regulatory compliance. Similarly, Amplitude Laser has introduced new femtosecond platforms tailored for industrial-scale surface engineering, emphasizing reliability and process scalability.
Recent years have seen significant investments in R&D, with companies like Light Conversion and Spectra-Physics (a division of MKS Instruments) focusing on enhancing pulse energy, beam quality, and system integration. These advancements are enabling new applications, such as anti-icing surfaces for aerospace, antibacterial coatings for medical implants, and superhydrophobic textures for energy devices. The integration of femtosecond lasers with advanced motion control and real-time process monitoring is further improving throughput and consistency, addressing key industrial scalability challenges.
Looking ahead to the next few years, the FLSE market is expected to benefit from continued miniaturization trends and the push for sustainable manufacturing. The adoption of femtosecond laser systems is projected to accelerate, particularly in regions with strong electronics and medical sectors. Industry collaborations and standardization efforts, led by organizations such as Laser Institute of America, are anticipated to streamline technology transfer and workforce training, supporting broader commercialization.
- Femtosecond laser surface engineering is now a mainstream solution for high-value, precision-driven industries.
- Major manufacturers (TRUMPF, Amplitude Laser, Light Conversion, Spectra-Physics) are expanding capabilities and product lines.
- Key applications include microelectronics, medical devices, aerospace, and energy, with new use cases emerging.
- Ongoing R&D and industry partnerships are driving improvements in throughput, reliability, and process automation.
- Market outlook for 2025 and beyond is positive, with growth underpinned by technology maturation and expanding end-user adoption.
Market Size, Growth Rate, and 2025–2029 Forecasts
Femtosecond laser surface engineering, leveraging ultrashort laser pulses for precise material modification, is experiencing robust growth as industries seek advanced solutions for micro- and nano-scale surface structuring. As of 2025, the global market for femtosecond laser systems—integral to surface engineering applications—continues to expand, driven by demand in sectors such as electronics, medical devices, automotive, and aerospace.
Key industry players, including TRUMPF, Coherent, Light Conversion, and Spectra-Physics (a division of MKS Instruments), are investing in new product development and capacity expansion to meet rising demand. For example, TRUMPF has highlighted the increasing adoption of femtosecond lasers for high-precision micromachining and surface texturing, particularly in the semiconductor and medical technology industries. Coherent continues to expand its portfolio of ultrafast lasers, targeting applications in display manufacturing, bioengineering, and advanced materials processing.
In 2025, the femtosecond laser surface engineering market is estimated to be valued in the low single-digit billions (USD), with annual growth rates projected in the range of 7–10% through 2029. This growth is underpinned by several factors:
- Increasing miniaturization and complexity of electronic components, requiring advanced surface structuring for improved performance and reliability.
- Rising demand for biocompatible and functionalized surfaces in medical implants and devices, where femtosecond lasers enable precise, contamination-free processing.
- Automotive and aerospace sectors adopting laser texturing for friction reduction, wear resistance, and lightweighting strategies.
- Emergence of new applications in photonics, energy storage, and anti-counterfeiting, expanding the addressable market.
Geographically, Asia-Pacific is expected to maintain the largest share of the market, led by manufacturing investments in China, Japan, and South Korea. Europe and North America remain significant, with strong R&D and adoption in high-value manufacturing. Companies such as Light Conversion (Lithuania) and Spectra-Physics (USA) are notable for their innovation in high-power, high-repetition-rate femtosecond laser systems.
Looking ahead to 2029, the market outlook remains positive, with continued advances in laser source technology, process automation, and integration with digital manufacturing platforms. Strategic partnerships between laser manufacturers and end-users are expected to accelerate the commercialization of novel surface engineering applications, further driving market expansion.
Core Technologies and Recent Innovations
Femtosecond laser surface engineering has rapidly advanced in recent years, driven by the unique capabilities of ultrashort pulse lasers to precisely modify material surfaces at micro- and nanoscales. As of 2025, the technology is being adopted across a range of industries, including medical devices, aerospace, automotive, and electronics, due to its ability to create functionalized surfaces with minimal thermal damage and high reproducibility.
The core technology relies on femtosecond lasers—lasers emitting pulses with durations in the order of 10-15 seconds—which enable ablation, texturing, and structuring of surfaces with exceptional control. This results in features such as superhydrophobicity, enhanced adhesion, anti-reflective properties, and improved biocompatibility. Recent innovations have focused on increasing throughput, scalability, and integration with automated manufacturing systems.
Key industry players are pushing the boundaries of femtosecond laser systems. TRUMPF, a global leader in industrial laser technology, has expanded its portfolio of ultrashort pulse lasers, emphasizing high average power and beam quality for industrial-scale surface processing. Their TruMicro Series, for example, is designed for high-speed, high-precision applications, and is being integrated into production lines for electronics and medical device manufacturing. Similarly, Amplitude Laser specializes in high-energy femtosecond lasers, supporting both research and industrial applications, with a focus on reliability and pulse stability.
Another significant contributor, Light Conversion, has developed advanced femtosecond laser sources and beam delivery systems, enabling complex surface structuring for photonics and microfluidics. Their PHAROS and CARBIDE laser platforms are widely used in both R&D and industrial settings, offering flexibility in pulse duration and energy for diverse material processing tasks.
Recent years have also seen the emergence of turnkey femtosecond laser workstations, such as those from Laserline and Coherent, which integrate motion control, real-time monitoring, and user-friendly interfaces. These systems are designed to lower the barrier to entry for manufacturers seeking to adopt femtosecond laser surface engineering, supporting applications from anti-icing coatings in aerospace to antibacterial surfaces in healthcare.
Looking ahead, the outlook for femtosecond laser surface engineering is robust. Ongoing developments are expected to further improve processing speeds, reduce costs, and enable new functionalities, such as hierarchical surface structures and multi-material processing. As automation and AI-driven process optimization become more prevalent, femtosecond laser technology is poised to play a central role in next-generation manufacturing and surface functionalization.
Leading Applications: Medical, Electronics, Aerospace, and Energy
Femtosecond laser surface engineering is rapidly advancing as a transformative technology across several high-value sectors, notably medical devices, electronics, aerospace, and energy. The unique ability of femtosecond lasers to deliver ultrashort pulses—on the order of 10-15 seconds—enables precise material modification with minimal thermal damage, opening new frontiers for functional surface structuring and micro/nano-scale texturing.
In the medical sector, femtosecond laser processing is increasingly adopted for manufacturing advanced implants and surgical tools. The technology enables the creation of micro- and nano-patterned surfaces that enhance osseointegration and reduce bacterial adhesion, critical for orthopedic and dental implants. Companies such as TRUMPF and Amplitude Laser are actively supplying femtosecond laser systems tailored for medical device manufacturing, with ongoing collaborations with implant manufacturers to optimize surface functionalities for improved patient outcomes.
In electronics, the demand for miniaturization and high-density integration is driving the adoption of femtosecond laser micromachining for printed circuit boards (PCBs), flexible electronics, and semiconductor wafer processing. Femtosecond lasers enable high-precision drilling, cutting, and patterning of brittle materials such as glass and ceramics, which are increasingly used in next-generation electronic devices. Coherent and Lumentum are among the leading suppliers of ultrafast laser systems for electronics manufacturing, with recent product launches focused on high-throughput, automated solutions for industrial-scale production.
The aerospace industry is leveraging femtosecond laser surface engineering to enhance the performance and durability of critical components. Applications include the creation of superhydrophobic, anti-icing, and wear-resistant surfaces on turbine blades and airframe structures. These engineered surfaces contribute to improved fuel efficiency and reduced maintenance costs. TRUMPF and nLIGHT are actively engaged with aerospace OEMs to develop custom laser processing solutions, with several pilot projects expected to transition to full-scale production by 2025–2026.
In the energy sector, femtosecond laser texturing is being explored to boost the efficiency of photovoltaic cells and battery electrodes. By creating micro- and nano-scale surface features, laser processing can enhance light absorption and facilitate improved charge transfer. Companies such as Amplitude Laser and Coherent are collaborating with energy technology firms to scale up these processes for commercial deployment, with pilot lines anticipated in the next few years.
Looking ahead, the integration of femtosecond laser surface engineering into automated manufacturing lines, coupled with advances in beam delivery and process monitoring, is expected to accelerate adoption across these sectors. As system costs decrease and throughput increases, femtosecond laser technology is poised to become a standard tool for high-value surface functionalization by the late 2020s.
Competitive Landscape: Key Players and Strategic Initiatives
The competitive landscape of femtosecond laser surface engineering in 2025 is characterized by a dynamic interplay between established laser manufacturers, innovative startups, and strategic collaborations with end-user industries. The sector is driven by the demand for ultra-precise surface modification in applications ranging from medical devices and microelectronics to aerospace and energy. Key players are investing in both technological advancements and global expansion to capture emerging opportunities.
Among the global leaders, TRUMPF stands out for its extensive portfolio of ultrafast laser systems, including femtosecond sources tailored for industrial micromachining and surface structuring. The company has recently expanded its TruMicro series, focusing on higher pulse energies and improved beam quality to address the growing need for high-throughput, high-precision surface texturing in automotive and semiconductor manufacturing. Similarly, Coherent continues to innovate in the femtosecond domain, offering the Monaco and Astrella platforms, which are widely adopted for advanced surface engineering tasks such as functionalizing medical implants and creating anti-reflective or hydrophobic surfaces.
European firms such as Light Conversion and Amplitude Laser are also prominent, with a focus on high-repetition-rate femtosecond lasers and turnkey systems for industrial and research applications. These companies are increasingly collaborating with system integrators and research institutes to develop application-specific solutions, particularly in the fields of photonics and precision optics.
In Asia, IPG Photonics and Lumentum are expanding their presence, leveraging their expertise in fiber laser technology to deliver robust femtosecond sources for surface engineering. These companies are targeting the rapidly growing electronics and medical device manufacturing sectors in China, Japan, and South Korea, where demand for advanced surface functionalities is accelerating.
Strategic initiatives in 2025 include increased investment in R&D for higher average power and shorter pulse duration lasers, as well as the integration of AI-driven process monitoring and automation. Partnerships between laser manufacturers and end-users are fostering the development of tailored surface engineering solutions, such as anti-icing coatings for aerospace and biofunctional surfaces for implants. The outlook for the next few years points to continued consolidation, with leading players seeking to enhance their technological edge and global reach through acquisitions, joint ventures, and expanded service offerings.
Emerging Trends: Surface Functionalization and Micro/Nano-Structuring
Femtosecond laser surface engineering is rapidly advancing as a transformative technology for surface functionalization and micro/nano-structuring across diverse industries. In 2025, the field is characterized by a convergence of ultrafast laser innovation, precision control, and scalable manufacturing, enabling the creation of surfaces with tailored properties such as superhydrophobicity, anti-icing, antibacterial activity, and enhanced optical or tribological performance.
A key trend is the industrial adoption of femtosecond lasers for direct surface texturing, driven by their ability to ablate material with minimal heat-affected zones and sub-micron precision. Major laser manufacturers such as TRUMPF and Coherent have expanded their portfolios to include high-power, high-repetition-rate femtosecond systems specifically designed for surface structuring applications. These systems are now being integrated into production lines for sectors including automotive, aerospace, medical devices, and consumer electronics, where functionalized surfaces can deliver significant performance and durability benefits.
Recent developments focus on the scalability and repeatability of laser-induced periodic surface structures (LIPSS) and hierarchical micro/nano-patterns. Companies such as Light Conversion and Amplitude Laser are providing turnkey solutions that combine femtosecond sources with advanced beam delivery and real-time process monitoring, enabling high-throughput processing of metals, polymers, and ceramics. These advances are facilitating the mass production of surfaces with controlled wettability, friction, or optical properties, supporting applications from anti-fingerprint coatings to improved implant biocompatibility.
Another emerging direction is the integration of femtosecond laser texturing with additive manufacturing and hybrid processing. For example, TRUMPF is developing systems that combine laser powder bed fusion with in-situ surface structuring, allowing for the fabrication of components with engineered surface functionalities directly out of the printer. This approach is expected to accelerate the adoption of functionalized surfaces in high-value sectors such as medical implants and aerospace components.
Looking ahead, the outlook for femtosecond laser surface engineering is robust. Ongoing R&D by industry leaders and collaborations with research institutes are expected to yield further improvements in process speed, pattern complexity, and material compatibility. The next few years will likely see broader commercialization of laser-functionalized surfaces, particularly as regulatory and sustainability pressures drive demand for chemical-free, energy-efficient surface modification methods. As femtosecond laser technology matures, its role in enabling next-generation functional materials and devices is set to expand significantly.
Regulatory Environment and Industry Standards
The regulatory environment and industry standards for femtosecond laser surface engineering are evolving rapidly as the technology matures and its applications expand across sectors such as medical devices, aerospace, automotive, and microelectronics. In 2025, regulatory frameworks are increasingly focused on ensuring safety, process repeatability, and product quality, particularly as femtosecond laser systems are integrated into high-value manufacturing and critical component fabrication.
In the medical device sector, femtosecond laser surface engineering is subject to stringent oversight by regulatory bodies such as the U.S. Food and Drug Administration (FDA) and the European Medicines Agency (EMA). These agencies require comprehensive validation of laser-processed surfaces, especially for implants and surgical tools, to ensure biocompatibility and long-term stability. Leading manufacturers like TRUMPF and Amplitude Laser are actively collaborating with regulatory authorities to develop standardized protocols for process validation and documentation, supporting the safe adoption of femtosecond laser technologies in regulated industries.
International standards organizations, including the International Organization for Standardization (ISO) and the International Electrotechnical Commission (IEC), are updating and expanding standards relevant to ultrafast laser processing. ISO 11137 and ISO 13485, for example, are being referenced for medical device manufacturing, while new work items are under discussion to address the unique aspects of femtosecond laser-material interactions, such as non-thermal ablation and sub-micron structuring. Industry leaders like Light Conversion and Spectra-Physics are participating in these standardization efforts, contributing technical expertise and supporting the harmonization of safety and performance benchmarks.
In the industrial sector, safety standards for laser equipment, such as IEC 60825, are being revised to account for the specific risks associated with ultrashort pulse lasers, including eye and skin exposure hazards. Companies such as Coherent and NKT Photonics are implementing advanced safety interlocks, real-time monitoring, and operator training programs to comply with these evolving requirements and to facilitate certification for global markets.
Looking ahead, the next few years will likely see the introduction of more application-specific standards, particularly for additive manufacturing, microfluidics, and surface texturing for tribological or antimicrobial properties. Industry consortia and public-private partnerships are expected to play a key role in shaping these standards, ensuring that femtosecond laser surface engineering continues to advance in a safe, reliable, and globally harmonized regulatory environment.
Challenges: Technical Barriers and Scalability
Femtosecond laser surface engineering (FLSE) has emerged as a transformative technology for precision micro- and nano-structuring of materials, but its broader industrial adoption faces several technical and scalability challenges as of 2025. One of the primary technical barriers remains the complexity of process control. Achieving consistent, reproducible surface features at high throughput requires precise management of laser parameters—pulse energy, repetition rate, scanning speed, and beam quality. Even minor fluctuations can lead to significant deviations in surface morphology, impacting functional performance in applications such as biomedical implants, microfluidics, and photonics.
Another significant challenge is the limited processing speed. While femtosecond lasers offer unparalleled precision, their ablation rates are generally lower than those of longer-pulse or continuous-wave lasers. This restricts their use in large-area or high-volume manufacturing. Efforts to scale up throughput, such as parallel processing with multi-beam setups or high-repetition-rate sources, are ongoing but introduce additional complexity in beam delivery and synchronization. Leading laser manufacturers like TRUMPF and Coherent are actively developing high-power femtosecond systems and advanced beam-shaping solutions to address these bottlenecks.
Material compatibility also poses a barrier. Not all substrates respond equally to femtosecond laser processing; for example, transparent materials or those with high thermal conductivity may require specialized approaches, such as burst-mode operation or tailored pulse sequences. Furthermore, the formation of debris and redeposition during ablation can degrade surface quality, necessitating post-processing steps that add to overall cost and complexity.
From a scalability perspective, integrating FLSE into existing industrial workflows is non-trivial. Automation, in-line monitoring, and real-time quality control are essential for mass production but remain underdeveloped for femtosecond laser systems. Companies like amcoss and LightMachinery are working on modular, automated platforms, yet widespread deployment is still in its early stages.
Looking ahead to the next few years, the outlook is cautiously optimistic. Advances in ultrafast laser sources, such as higher average powers and improved beam stability, are expected to enhance both throughput and reliability. Collaborative efforts between equipment manufacturers and end-users are likely to yield more robust, application-specific solutions. However, overcoming the current technical and scalability barriers will require continued innovation in laser hardware, process automation, and materials science, as well as standardization efforts led by industry bodies such as Laser Institute of America.
Investment, Funding, and M&A Activity
The femtosecond laser surface engineering sector is experiencing a notable surge in investment, funding, and merger and acquisition (M&A) activity as of 2025, driven by the expanding adoption of ultrafast laser technologies in manufacturing, medical devices, microelectronics, and energy applications. The demand for precision surface modification—enabled by femtosecond lasers—has attracted both established photonics companies and venture-backed startups, fueling competition and innovation.
Key industry players such as TRUMPF, a global leader in industrial lasers, and Coherent, known for its broad ultrafast laser portfolio, have continued to invest heavily in R&D and production capacity for femtosecond laser systems. TRUMPF has announced multi-million-euro expansions of its laser manufacturing facilities in Europe and North America, aiming to meet the growing demand for high-precision surface texturing and microstructuring solutions. Similarly, Coherent has increased its capital expenditure in 2024–2025, focusing on scaling up its ultrafast laser production lines and expanding its application development centers.
In the startup ecosystem, companies specializing in femtosecond laser-based surface engineering—such as those developing anti-icing, antibacterial, or superhydrophobic surfaces—have attracted significant venture capital. For example, several European and North American startups have secured Series A and B funding rounds in the $10–30 million range, with participation from both strategic investors and dedicated photonics venture funds. These investments are often aimed at accelerating commercialization of proprietary surface engineering processes for sectors like aerospace, automotive, and medical implants.
M&A activity has also intensified. In late 2024 and early 2025, there have been several high-profile acquisitions of niche femtosecond laser technology firms by larger photonics and materials processing companies. amcoss, a specialist in advanced surface processing equipment, has expanded its portfolio through the acquisition of a femtosecond laser microstructuring startup, aiming to integrate laser-based solutions into its existing product lines. Meanwhile, Light Conversion, a leading manufacturer of femtosecond laser sources, has entered strategic partnerships with surface engineering solution providers to co-develop turnkey systems for industrial clients.
Looking ahead, the sector is expected to see continued consolidation as larger players seek to acquire innovative startups and intellectual property, while public and private funding is likely to remain robust given the broadening industrial relevance of femtosecond laser surface engineering. The next few years will likely witness further cross-border investments and joint ventures, particularly in Asia and North America, as companies position themselves to capture emerging opportunities in advanced manufacturing and functional surface design.
Future Outlook: Opportunities and Strategic Recommendations
Femtosecond laser surface engineering is poised for significant advancements and broader adoption in 2025 and the coming years, driven by ongoing innovations in ultrafast laser technology, increasing industrial demand for precision surface modification, and the push for sustainable manufacturing. The unique ability of femtosecond lasers to induce highly controlled, non-thermal material modifications at micro- and nano-scales continues to unlock new applications across sectors such as medical devices, aerospace, automotive, and electronics.
Key industry players, including TRUMPF, Amplitude, and Light Conversion, are investing in the development of higher-power, more compact, and energy-efficient femtosecond laser systems. These advancements are expected to lower the barriers to entry for small and medium-sized enterprises, enabling wider deployment beyond traditional research and high-end manufacturing environments. For example, TRUMPF has recently introduced new femtosecond laser platforms designed for industrial-scale surface texturing and functionalization, targeting applications such as friction reduction, hydrophobicity, and improved adhesion.
In the medical sector, femtosecond laser surface engineering is anticipated to play a pivotal role in the fabrication of next-generation implants and surgical tools with enhanced biocompatibility and antibacterial properties. Companies like Amplitude are collaborating with medical device manufacturers to develop tailored surface structures that promote cell integration and reduce infection risks. Similarly, the electronics industry is leveraging femtosecond laser processing for the creation of micro- and nano-patterned surfaces to improve device performance and reliability.
Looking ahead, the integration of femtosecond laser systems with advanced automation, machine vision, and AI-driven process control is expected to further enhance throughput, repeatability, and customization. This trend is supported by ongoing partnerships between laser manufacturers and automation specialists, aiming to deliver turnkey solutions for high-volume production lines. Additionally, the growing emphasis on green manufacturing is likely to accelerate the adoption of femtosecond laser techniques, as they offer minimal material waste, reduced chemical usage, and lower energy consumption compared to conventional surface treatment methods.
Strategically, stakeholders are encouraged to invest in workforce training, cross-sector collaborations, and the development of application-specific process libraries to maximize the value of femtosecond laser surface engineering. As the technology matures, standardization efforts led by industry bodies and consortia will be crucial in ensuring process reliability and facilitating regulatory approvals, particularly in safety-critical fields such as healthcare and aerospace.