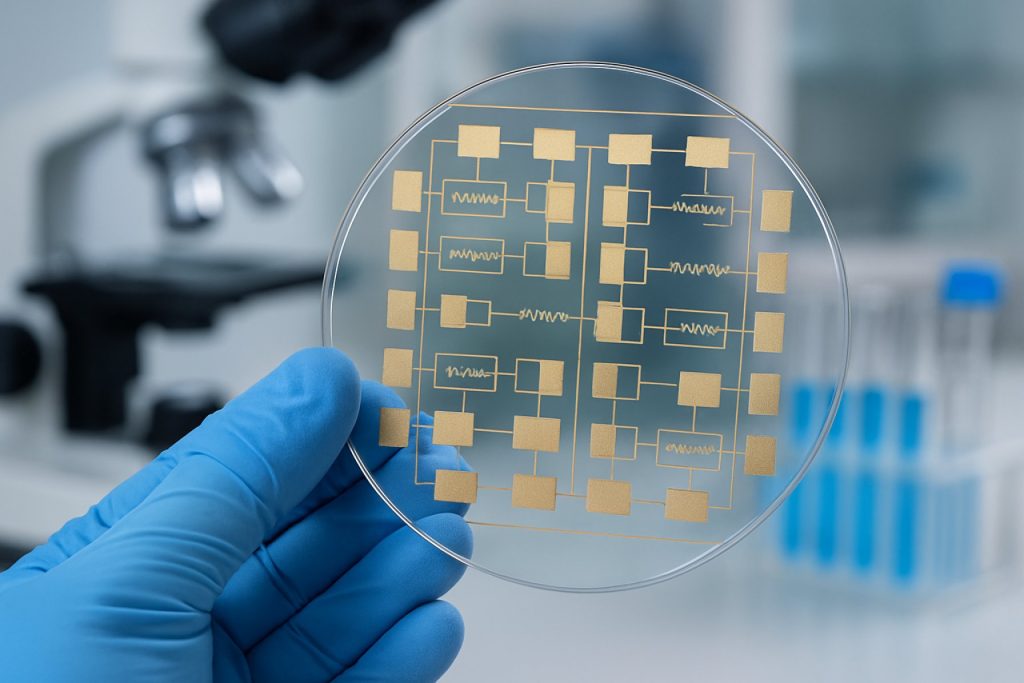
Nanowire Biosensor Fabrication in 2025: Unleashing the Next Wave of Ultra-Sensitive Diagnostics and Market Expansion. Explore How Advanced Manufacturing is Shaping the Future of Healthcare and Environmental Monitoring.
- Executive Summary: Key Trends and Market Drivers in 2025
- Technology Overview: Nanowire Biosensor Fabrication Methods
- Material Innovations: Advances in Nanowire Composition and Performance
- Current Market Landscape: Leading Players and Regional Hotspots
- Emerging Applications: Healthcare, Environmental, and Industrial Sectors
- Manufacturing Challenges and Solutions: Scalability, Cost, and Integration
- Regulatory Environment and Industry Standards (e.g., ieee.org, fda.gov)
- Competitive Analysis: Company Strategies and Partnerships (e.g., nanowiresolutions.com, nanowiresensor.com)
- Market Forecasts: Growth Projections Through 2030
- Future Outlook: Disruptive Trends and Next-Generation Nanowire Biosensors
- Sources & References
Executive Summary: Key Trends and Market Drivers in 2025
The nanowire biosensor fabrication sector is poised for significant advancements in 2025, driven by the convergence of materials innovation, scalable manufacturing, and expanding application domains. Nanowire-based biosensors, leveraging the unique electrical and surface properties of one-dimensional nanostructures, are increasingly recognized for their ultra-high sensitivity and rapid response times in detecting biomolecules. The market is witnessing a shift from laboratory-scale prototypes to scalable, reproducible manufacturing processes, with leading semiconductor and materials companies investing in next-generation fabrication techniques.
Key trends in 2025 include the adoption of bottom-up synthesis methods, such as vapor-liquid-solid (VLS) growth and template-assisted electrodeposition, which enable precise control over nanowire dimensions and composition. Companies like Intel Corporation and Samsung Electronics are leveraging their expertise in nanoscale semiconductor fabrication to explore silicon and III-V compound nanowires for biosensing platforms. These industry leaders are collaborating with academic and clinical partners to optimize device architectures for point-of-care diagnostics and environmental monitoring.
Another driver is the integration of nanowire arrays onto flexible and transparent substrates, facilitating the development of wearable and implantable biosensors. DuPont and Corning Incorporated are actively developing advanced substrate materials and surface functionalization chemistries to enhance biocompatibility and sensor stability. The push towards roll-to-roll and large-area printing techniques is expected to lower production costs and accelerate commercialization, particularly for disposable biosensor formats.
In parallel, the sector is experiencing increased standardization efforts, with organizations such as the SEMI industry association working to establish guidelines for nanowire device fabrication, testing, and quality assurance. This is critical for ensuring device reproducibility and regulatory compliance, especially as nanowire biosensors move closer to clinical and industrial deployment.
Looking ahead, the outlook for nanowire biosensor fabrication is robust. The convergence of advanced materials, scalable manufacturing, and digital integration is expected to drive double-digit growth in the sector over the next few years. Strategic partnerships between technology giants, materials suppliers, and healthcare providers will be instrumental in overcoming technical and regulatory hurdles, paving the way for widespread adoption of nanowire biosensors in diagnostics, environmental monitoring, and personalized medicine.
Technology Overview: Nanowire Biosensor Fabrication Methods
Nanowire biosensor fabrication is a rapidly advancing field, with significant progress expected in 2025 and the following years. The core of these biosensors lies in the precise engineering of nanowires—typically silicon, zinc oxide, or other semiconducting materials—onto substrates to create highly sensitive detection platforms for biological molecules. The fabrication methods are evolving to meet the demands for scalability, reproducibility, and integration with existing semiconductor technologies.
The two principal approaches to nanowire fabrication are the “bottom-up” and “top-down” methods. Bottom-up techniques, such as vapor-liquid-solid (VLS) growth, allow for the synthesis of nanowires with controlled dimensions and doping profiles. Companies like Siltronic AG, a leading silicon wafer manufacturer, are actively involved in supplying high-purity substrates and exploring advanced nanowire growth processes. Meanwhile, Oxford Instruments provides equipment for chemical vapor deposition (CVD) and atomic layer deposition (ALD), both critical for bottom-up nanowire synthesis.
Top-down fabrication, on the other hand, leverages established semiconductor processing techniques such as photolithography and etching to carve nanowires from bulk materials. This approach is favored for its compatibility with large-scale manufacturing and integration with complementary metal-oxide-semiconductor (CMOS) technology. Lam Research and Applied Materials are prominent suppliers of etching and deposition equipment, supporting the transition of nanowire biosensors from laboratory prototypes to commercial products.
Recent years have seen the emergence of hybrid approaches, combining the precision of bottom-up growth with the scalability of top-down patterning. For example, directed self-assembly and nanoimprint lithography are being explored to align and position nanowires with high throughput. Nanoscribe GmbH specializes in high-resolution 3D printing and nanoimprint technologies, enabling the fabrication of complex nanowire architectures for biosensing applications.
Looking ahead to 2025 and beyond, the focus is on improving yield, uniformity, and device integration. Industry collaborations are intensifying, with semiconductor foundries and biosensor startups working together to develop standardized fabrication protocols. The integration of nanowire biosensors onto flexible and wearable substrates is also gaining momentum, driven by advances in materials science and roll-to-roll processing. As fabrication methods mature, the commercialization of nanowire biosensors for medical diagnostics, environmental monitoring, and food safety is expected to accelerate, supported by the robust supply chains and technical expertise of companies like Siltronic AG, Oxford Instruments, and Applied Materials.
Material Innovations: Advances in Nanowire Composition and Performance
The landscape of nanowire biosensor fabrication is undergoing rapid transformation in 2025, driven by material innovations that enhance sensitivity, selectivity, and scalability. Traditionally, silicon nanowires have dominated the field due to their compatibility with established semiconductor processes. However, recent years have seen a surge in the exploration and commercialization of alternative materials such as III-V semiconductors, metal oxides, and hybrid organic-inorganic structures.
One of the most significant trends is the integration of compound semiconductors like indium phosphide (InP) and gallium nitride (GaN) into nanowire biosensors. These materials offer superior electron mobility and chemical stability, which are critical for high-performance biosensing in complex biological environments. Companies such as ams-OSRAM AG and NXP Semiconductors are actively developing sensor platforms that leverage these advanced materials, aiming to deliver next-generation diagnostic tools with improved detection limits and multiplexing capabilities.
Metal oxide nanowires, particularly those based on zinc oxide (ZnO) and tin oxide (SnO2), are also gaining traction due to their high surface-to-volume ratio and ease of functionalization. These properties facilitate the immobilization of biomolecules, enhancing the sensitivity of biosensors. Oxford Instruments and Nanowire Solutions are among the companies advancing scalable fabrication techniques such as vapor-liquid-solid (VLS) growth and template-assisted electrodeposition, which are crucial for commercial viability.
Hybrid nanowire systems, combining organic polymers with inorganic cores, are emerging as a promising avenue for flexible and wearable biosensors. These composites can be engineered to exhibit tailored electrical and mechanical properties, opening new possibilities for point-of-care diagnostics and continuous health monitoring. FlexEnable and Paragraf are notable for their work in integrating such materials into flexible electronics and sensor arrays.
Looking ahead, the focus is shifting toward large-scale, cost-effective manufacturing methods such as roll-to-roll processing and inkjet printing of nanowire inks. These approaches are expected to accelerate the deployment of nanowire biosensors in clinical, environmental, and food safety applications. Industry collaborations and partnerships with academic institutions are likely to intensify, fostering the translation of laboratory breakthroughs into robust commercial products. As material innovations continue to mature, the next few years will likely witness a proliferation of high-performance, application-specific nanowire biosensors, reshaping the diagnostics landscape.
Current Market Landscape: Leading Players and Regional Hotspots
The global landscape for nanowire biosensor fabrication in 2025 is characterized by a dynamic interplay of established technology leaders, emerging startups, and regionally concentrated innovation clusters. The sector is driven by the demand for highly sensitive, miniaturized, and rapid diagnostic solutions across healthcare, environmental monitoring, and food safety. Silicon, gold, and various metal oxide nanowires remain the primary materials, with fabrication methods such as vapor-liquid-solid (VLS) growth, template-assisted synthesis, and advanced lithography dominating commercial and pre-commercial production.
Among the leading players, Intel Corporation continues to leverage its expertise in semiconductor nanofabrication, exploring nanowire-based biosensor platforms for integration with CMOS technology. Thermo Fisher Scientific is actively developing nanowire sensor arrays for life sciences and diagnostics, capitalizing on its global manufacturing and distribution network. Oxford Instruments provides advanced deposition and etching equipment, enabling precise nanowire fabrication for both research and industrial clients.
In Asia, Samsung Electronics and Taiwan Semiconductor Manufacturing Company (TSMC) are investing in next-generation biosensor platforms, utilizing their advanced foundry capabilities to prototype and scale nanowire-based devices. These companies are collaborating with regional universities and medical centers to accelerate clinical validation and regulatory approval. Meanwhile, Hitachi and Panasonic in Japan are focusing on integrating nanowire biosensors into point-of-care diagnostic systems and wearable health monitors.
Europe remains a hotspot for nanowire biosensor innovation, with NXP Semiconductors and Infineon Technologies supporting the development of sensor platforms for medical and environmental applications. The region benefits from strong public-private partnerships and EU-funded initiatives aimed at scaling up nanofabrication infrastructure and fostering cross-border collaboration.
Startups and spin-offs are also shaping the market, particularly in North America and Europe. Companies such as Nanowire Solutions (if confirmed operational) and university-affiliated ventures are pushing the boundaries of label-free detection and multiplexed sensing. These firms often partner with established manufacturers for pilot production and market entry.
Looking ahead, the market is expected to see increased standardization of fabrication processes, greater integration with microfluidics and AI-driven analytics, and a shift toward scalable, cost-effective manufacturing. Regional clusters in the US (Silicon Valley, Boston), East Asia (South Korea, Taiwan, Japan), and Europe (Germany, the Netherlands) will likely remain at the forefront, supported by robust R&D ecosystems and proactive regulatory frameworks.
Emerging Applications: Healthcare, Environmental, and Industrial Sectors
Nanowire biosensor fabrication is rapidly advancing, with significant implications for healthcare, environmental monitoring, and industrial applications as of 2025 and looking ahead. The unique properties of nanowires—such as high surface-to-volume ratio, tunable electrical characteristics, and compatibility with various functionalization chemistries—make them ideal for sensitive, label-free detection of biomolecules and chemical species.
In healthcare, nanowire biosensors are being developed for early disease diagnostics, real-time monitoring, and personalized medicine. Companies like Nanowire Solutions are focusing on silicon and III-V compound nanowire platforms, enabling multiplexed detection of biomarkers for cancer, infectious diseases, and metabolic disorders. These sensors can be integrated into point-of-care devices, offering rapid and accurate results with minimal sample volumes. The trend toward miniaturization and integration with microfluidic systems is expected to accelerate, with several pilot projects aiming for regulatory approval and clinical deployment by 2026.
Environmental monitoring is another area where nanowire biosensor fabrication is making strides. Organizations such as Sensirion are leveraging their expertise in sensor miniaturization to develop nanowire-based platforms for detecting pollutants, toxins, and pathogens in air and water. These sensors offer real-time, on-site analysis capabilities, which are crucial for rapid response to contamination events and for continuous monitoring in smart city infrastructures. The push for sustainability and stricter environmental regulations is expected to drive further adoption, with new sensor arrays capable of detecting multiple analytes simultaneously entering the market in the next few years.
In the industrial sector, nanowire biosensors are being integrated into process control systems for food safety, pharmaceutical manufacturing, and bioprocess monitoring. Companies like ams OSRAM are developing robust, scalable nanowire sensor platforms that can withstand harsh industrial environments while providing high sensitivity and selectivity. These sensors are being tailored for inline monitoring of contaminants, ensuring product quality and regulatory compliance. The ongoing trend toward Industry 4.0 and the Industrial Internet of Things (IIoT) is expected to further boost demand for such advanced sensing solutions.
Looking forward, the next few years will likely see continued innovation in nanowire biosensor fabrication techniques, including bottom-up and top-down approaches, as well as advances in surface functionalization and integration with digital platforms. Strategic collaborations between sensor manufacturers, healthcare providers, environmental agencies, and industrial partners are anticipated to accelerate commercialization and broaden the impact of nanowire biosensors across multiple sectors.
Manufacturing Challenges and Solutions: Scalability, Cost, and Integration
The fabrication of nanowire biosensors is at a pivotal stage in 2025, as the field transitions from laboratory-scale demonstrations to scalable, cost-effective manufacturing suitable for commercial deployment. The primary challenges remain scalability, cost control, and seamless integration with existing electronic platforms.
Scalability is a central concern, as traditional bottom-up synthesis methods—such as vapor-liquid-solid (VLS) growth—offer excellent control over nanowire properties but are difficult to adapt for high-throughput, wafer-scale production. Companies like Intel Corporation and Samsung Electronics, with their expertise in semiconductor nanofabrication, are exploring top-down approaches, including advanced lithography and etching, to pattern nanowires directly onto silicon wafers. These methods leverage existing CMOS infrastructure, enabling higher yields and better reproducibility, but often at the expense of increased process complexity and cost.
Cost remains a significant barrier, particularly for biosensors intended for point-of-care or disposable applications. The use of precious metals, complex surface functionalization, and stringent cleanroom requirements all contribute to elevated production expenses. To address this, manufacturers are investigating alternative materials such as silicon nanowires, which are compatible with established semiconductor processes, and scalable printing techniques like nanoimprint lithography. Applied Materials, Inc. is actively developing equipment and process solutions to reduce the cost per device by optimizing material utilization and automating key fabrication steps.
Integration with existing electronic systems is another critical hurdle. For nanowire biosensors to achieve widespread adoption, they must be reliably interfaced with readout electronics and data processing units. Companies such as Taiwan Semiconductor Manufacturing Company (TSMC) are working on monolithic integration strategies, embedding nanowire sensor arrays directly onto CMOS chips. This approach minimizes signal loss, reduces packaging complexity, and supports the miniaturization required for wearable and implantable devices.
Looking ahead, the next few years are expected to see further convergence between nanowire biosensor fabrication and mainstream semiconductor manufacturing. Collaborative efforts between biosensor startups and established foundries are likely to accelerate the translation of prototypes into mass-produced products. The adoption of Industry 4.0 principles—such as in-line metrology, AI-driven process control, and digital twins—will further enhance yield and consistency. As these solutions mature, the cost and scalability barriers are anticipated to diminish, paving the way for nanowire biosensors to enter diverse markets, from healthcare diagnostics to environmental monitoring.
Regulatory Environment and Industry Standards (e.g., ieee.org, fda.gov)
The regulatory environment and industry standards for nanowire biosensor fabrication are rapidly evolving as these devices transition from laboratory prototypes to commercial products. In 2025, the landscape is shaped by a combination of established frameworks for medical devices and emerging guidelines specific to nanomaterials and nanoscale fabrication processes.
In the United States, the U.S. Food and Drug Administration (FDA) remains the primary regulatory authority overseeing the approval and monitoring of biosensors intended for clinical use. The FDA’s Center for Devices and Radiological Health (CDRH) applies the existing medical device classification system to nanowire biosensors, typically categorizing them as Class II or Class III devices depending on their intended use and risk profile. In recent years, the FDA has issued guidance documents addressing the unique considerations of nanotechnology in medical devices, emphasizing the need for detailed characterization of nanomaterials, biocompatibility assessments, and robust manufacturing controls. The agency encourages early engagement through its Q-Submission Program to clarify regulatory expectations for novel nanowire-based diagnostics.
Globally, harmonization efforts are underway to align standards for nanowire biosensor fabrication. The International Organization for Standardization (ISO) and the IEEE Standards Association are both active in developing technical standards relevant to nanoscale sensors. ISO/TC 229 focuses on nanotechnologies, including terminology, measurement, and risk management, while the IEEE has established working groups for standards in nanoelectronics and biosensor interoperability. These standards address critical aspects such as reproducibility of nanowire synthesis, surface functionalization protocols, and electrical characterization methods.
Industry consortia and alliances, such as the SEMI (Semiconductor Equipment and Materials International), are also contributing to best practices for nanowire device fabrication, particularly in the context of semiconductor manufacturing and quality assurance. SEMI’s standards for contamination control, cleanroom environments, and process monitoring are increasingly relevant as nanowire biosensor production scales up.
Looking ahead, regulatory agencies are expected to refine their approaches to address the unique challenges posed by nanowire biosensors, including potential environmental and occupational health risks associated with nanomaterial handling. The next few years will likely see the introduction of more specific guidance documents and possibly new regulatory pathways tailored to nanoscale biosensors. Industry stakeholders are advised to closely monitor updates from the FDA, ISO, IEEE, and SEMI, and to participate in public consultations to help shape the evolving standards landscape for nanowire biosensor fabrication.
Competitive Analysis: Company Strategies and Partnerships (e.g., nanowiresolutions.com, nanowiresensor.com)
The competitive landscape for nanowire biosensor fabrication in 2025 is characterized by a dynamic interplay of technological innovation, strategic partnerships, and vertical integration. Companies are leveraging proprietary fabrication techniques, expanding their intellectual property portfolios, and forming alliances to accelerate commercialization and address the growing demand for sensitive, miniaturized biosensing platforms.
Key players such as Nanowire Solutions and Nanowire Sensor are at the forefront, each employing distinct strategies to gain market share. Nanowire Solutions focuses on scalable silicon nanowire fabrication, offering both custom sensor development and foundry services. Their approach emphasizes compatibility with existing semiconductor manufacturing infrastructure, enabling cost-effective mass production and integration into lab-on-chip devices. In 2024–2025, the company has announced collaborations with medical device manufacturers and academic research centers to co-develop application-specific biosensors, particularly for point-of-care diagnostics and environmental monitoring.
Nanowire Sensor, meanwhile, differentiates itself through proprietary surface functionalization chemistries and multiplexed sensor arrays. Their partnerships with biotechnology firms and clinical laboratories are aimed at validating sensor performance in real-world diagnostic workflows. In early 2025, the company expanded its R&D alliances to include pharmaceutical companies, targeting drug discovery and biomarker screening applications. This move is expected to accelerate the translation of nanowire biosensor technology from research to regulated clinical and industrial settings.
Beyond these specialized firms, established semiconductor and materials companies are entering the nanowire biosensor space. For example, STMicroelectronics and imec are leveraging their expertise in nanoscale fabrication and microelectronics to develop integrated biosensor platforms. These organizations are forming consortia with startups and research institutes to address challenges in reproducibility, scalability, and regulatory compliance. Their involvement is expected to drive standardization and facilitate the adoption of nanowire biosensors in high-volume applications.
Looking ahead, the competitive environment is likely to intensify as companies pursue vertical integration—combining nanowire synthesis, device fabrication, and data analytics under one roof. Strategic partnerships will remain crucial, particularly for navigating regulatory pathways and accessing specialized markets such as personalized medicine and food safety. The next few years will see increased investment in pilot manufacturing lines, joint ventures for clinical validation, and cross-sector collaborations, positioning nanowire biosensor fabrication as a key enabler of next-generation diagnostics and environmental sensing.
Market Forecasts: Growth Projections Through 2030
The global market for nanowire biosensor fabrication is poised for robust growth through 2030, driven by accelerating demand for rapid, sensitive, and miniaturized diagnostic platforms across healthcare, environmental monitoring, and food safety sectors. As of 2025, the sector is witnessing increased investment in both research and commercial-scale manufacturing, with several key players expanding their production capabilities and forging strategic partnerships to address the growing need for advanced biosensing technologies.
Major semiconductor and nanotechnology companies are at the forefront of this expansion. Intel Corporation and Taiwan Semiconductor Manufacturing Company (TSMC) have both announced initiatives to adapt their advanced fabrication processes for biosensor applications, leveraging their expertise in nanoscale manufacturing to enable high-throughput, cost-effective production of silicon nanowire arrays. These efforts are complemented by specialized firms such as Nanowire Solutions, which focuses on custom nanowire synthesis and integration for biosensor developers, and Oxford Instruments, a supplier of precision nanofabrication equipment widely used in the sector.
Recent data from industry sources indicate that the nanowire biosensor market is expected to achieve a compound annual growth rate (CAGR) exceeding 20% through 2030, with the Asia-Pacific region projected to lead in both manufacturing and adoption due to strong government support and a burgeoning biotechnology ecosystem. The United States and Europe are also anticipated to see significant growth, propelled by investments in point-of-care diagnostics and personalized medicine.
Key trends shaping the market outlook include the integration of nanowire biosensors with microfluidic and lab-on-chip platforms, enabling multiplexed detection and real-time analysis. Companies such as Thermo Fisher Scientific and Abbott Laboratories are exploring partnerships and in-house development of nanowire-based diagnostic devices, aiming to bring next-generation biosensors to clinical and field settings.
Looking ahead, the market is expected to benefit from ongoing advances in scalable nanowire synthesis, surface functionalization, and device packaging. As regulatory pathways for nanomaterial-based diagnostics become clearer, commercialization timelines are likely to accelerate, further fueling market expansion. By 2030, nanowire biosensor fabrication is set to become a cornerstone technology in the global biosensing landscape, with broad implications for public health, environmental stewardship, and food safety.
Future Outlook: Disruptive Trends and Next-Generation Nanowire Biosensors
The landscape of nanowire biosensor fabrication is poised for significant transformation in 2025 and the coming years, driven by advances in materials science, scalable manufacturing, and integration with digital health platforms. The push toward next-generation biosensors is characterized by a shift from laboratory-scale, proof-of-concept devices to robust, reproducible, and cost-effective fabrication methods suitable for mass production and real-world deployment.
One of the most disruptive trends is the adoption of bottom-up synthesis techniques, such as vapor-liquid-solid (VLS) growth and template-assisted electrodeposition, which enable precise control over nanowire dimensions and composition. Companies like Oxford Instruments are at the forefront, providing advanced deposition and etching systems that support the fabrication of high-quality semiconductor nanowires with tailored properties. These methods are increasingly being optimized for compatibility with standard semiconductor processing, paving the way for integration into existing microelectronics manufacturing lines.
Another key development is the move toward wafer-scale fabrication. Industry leaders such as Lam Research and Applied Materials are investing in equipment and process solutions that enable the parallel production of nanowire arrays on large substrates. This scalability is essential for reducing costs and ensuring the uniformity required for clinical and commercial biosensor applications.
Material innovation is also accelerating. The use of novel materials—such as silicon-germanium alloys, III-V semiconductors, and even 2D materials like graphene—offers enhanced sensitivity, selectivity, and biocompatibility. Companies like Novellus Systems (now part of Lam Research) have contributed to the development of atomic layer deposition (ALD) and chemical vapor deposition (CVD) tools that facilitate the integration of these advanced materials into nanowire structures.
Looking ahead, the convergence of nanowire biosensor fabrication with microfluidics and wireless electronics is expected to yield fully integrated, point-of-care diagnostic platforms. The emergence of flexible and wearable biosensors, enabled by advances in nanowire transfer printing and substrate engineering, is likely to disrupt traditional healthcare monitoring. Companies such as Flex are exploring these frontiers, leveraging their expertise in flexible electronics manufacturing.
In summary, the next few years will see nanowire biosensor fabrication transition from specialized research to scalable, industry-ready processes. This evolution will be underpinned by innovations in synthesis, materials, and integration, positioning nanowire biosensors as a cornerstone of future diagnostic and health monitoring technologies.
Sources & References
- DuPont
- Siltronic AG
- Oxford Instruments
- Nanoscribe GmbH
- ams-OSRAM AG
- NXP Semiconductors
- FlexEnable
- Paragraf
- Thermo Fisher Scientific
- Hitachi
- Infineon Technologies
- Sensirion
- ams OSRAM
- International Organization for Standardization
- IEEE
- STMicroelectronics
- imec
- Oxford Instruments
- Flex