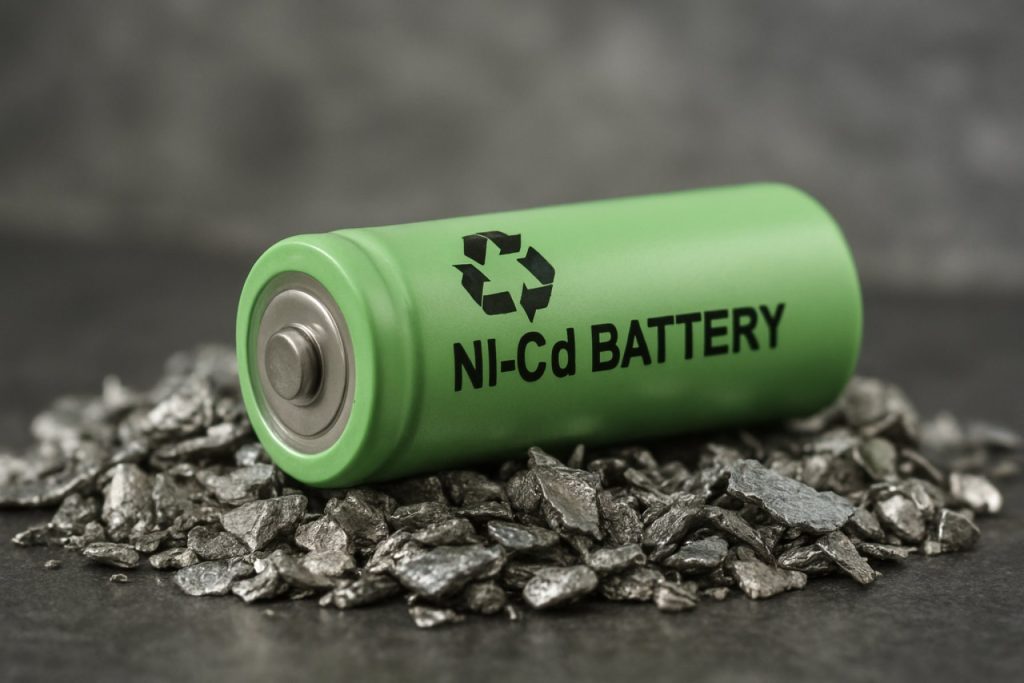
Unveiling the Future of Nickel-Cadmium Battery Recycling in 2025: How Next-Gen Technologies Are Revolutionizing Sustainability and Profitability. Get Ahead of the Curve with Exclusive Insights Into the Industry’s Most Disruptive Trends.
- Executive Summary: Key Trends and Market Drivers 2025–2030
- Global Market Size and Forecast: Growth Trajectories Through 2030
- Regulatory Landscape: International Policies and Standards
- Leading Recycling Technologies: Mechanical, Hydrometallurgical, and Pyrometallurgical Processes
- Emerging Innovations: Automation, AI, and Green Chemistry in Recycling
- Competitive Analysis: Profiles of Top Industry Players
- Supply Chain Dynamics: Collection, Logistics, and Material Flow
- Environmental and Economic Impact Assessment
- Strategic Partnerships and Industry Collaborations
- Future Outlook: Investment Opportunities and Technology Roadmap
- Sources & References
Executive Summary: Key Trends and Market Drivers 2025–2030
The period from 2025 through 2030 is expected to see significant transformation in nickel-cadmium (Ni-Cd) battery recycling technologies, driven by evolving environmental regulations, advances in process efficiency, and shifts in global supply chains. Governments in North America, the European Union, and Asia-Pacific are tightening restrictions on hazardous waste, with a focus on reducing cadmium pollution and increasing recovery rates of critical metals. In the EU, the Battery Directive continues to mandate high collection and recycling targets for industrial and portable Ni-Cd batteries, spurring investment in modernized recycling infrastructure and improved collection logistics.
Technological advancements are at the forefront of these changes. Hydrometallurgical processes—where batteries are shredded and valuable metals are leached and separated—are being refined for higher yields and lower energy consumption. Pyrometallurgical processing, which uses high temperatures to recover nickel and cadmium, remains prevalent but is increasingly supplemented by closed-loop systems to minimize emissions. Several industry leaders are investing in proprietary techniques to maximize recovery rates, with European recycling firms such as Umicore and Accurec Recycling GmbH enhancing their facilities to process larger volumes and meet stricter environmental standards. Umicore, for example, operates one of Europe’s largest battery recycling plants, employing both pyrometallurgical and hydrometallurgical routes to recover nickel, cadmium, and other metals for reuse in new battery production.
In Asia, China’s battery recycling sector is experiencing rapid consolidation, with licensed recyclers expanding their capacity to handle industrial-scale Ni-Cd waste. Chinese companies are also investing in automation and process optimization to improve material purity and reduce hazardous byproducts. In North America, firms such as Call2Recycle are leading collection and recycling initiatives, partnering with manufacturers and retailers to ensure compliance with regulatory standards and promote consumer participation in battery take-back programs.
Looking ahead, the global Ni-Cd battery recycling market will be shaped by several key drivers: the continued phase-out of Ni-Cd batteries in favor of lithium-ion chemistries, stricter export controls on hazardous waste, and the need for circular supply chains to secure critical materials. Although Ni-Cd battery demand is declining, legacy waste streams and industrial applications (such as emergency backup systems and aviation) will sustain recycling volumes through the late 2020s. The sector’s outlook is positive, with investments in research, automation, and environmentally responsible processes positioning major recyclers—such as Umicore, Accurec Recycling GmbH, and Call2Recycle—to meet new regulatory and market demands as the decade progresses.
Global Market Size and Forecast: Growth Trajectories Through 2030
The global market for nickel-cadmium (Ni-Cd) battery recycling technologies is poised for moderate yet steady growth through 2030, influenced by evolving environmental regulations, shifting battery usage patterns, and technological advancements. While nickel-cadmium batteries have been largely supplanted in many consumer applications by lithium-ion alternatives, they remain significant in industrial, emergency, aviation, and certain backup power sectors. This ongoing usage sustains a continuous stream of spent Ni-Cd batteries requiring environmentally compliant recycling solutions.
In 2025, the market is characterized by incremental capacity expansions and process improvements among established recyclers, particularly in Europe, North America, and East Asia. For example, SNAM (France) and Battery Solutions (USA) are among the leading companies operating dedicated Ni-Cd battery recycling facilities, employing hydrometallurgical and pyrometallurgical techniques to recover nickel, cadmium, and other valuable metals. Umicore (Belgium), a global materials technology group, also maintains significant recycling operations, integrating Ni-Cd battery processing into broader battery recycling streams.
Europe continues to account for a substantial share of global Ni-Cd battery recycling due to stringent directives—such as the EU Batteries Directive—that require safe collection and treatment of cadmium-containing batteries. Similar regulatory pressure is seen in North America, where the Rechargeable Battery Recycling Corporation (now Call2Recycle) coordinates collection and recycling initiatives in collaboration with manufacturers and retailers. In Asia, China’s growing industrial base and government-backed initiatives are driving the expansion of domestic Ni-Cd recycling infrastructure, with companies such as GEM Co., Ltd. emerging as important players.
Recent years have witnessed incremental improvements in process efficiency, energy consumption, and environmental safeguards across the sector. Hydrometallurgical processes, in particular, have gained momentum for their ability to selectively recover high-purity nickel and cadmium compounds, reducing hazardous emissions compared to traditional high-temperature methods. Companies are also investing in automation and digital tracking systems to improve traceability and material recovery rates.
Looking ahead to 2030, the overall market for Ni-Cd battery recycling technologies is expected to see only modest expansion in absolute volume, given the gradual decline in new Ni-Cd battery production. Nevertheless, regulatory mandates for closed-loop recycling, especially the safe handling of toxic cadmium, ensure that the recycling sector will remain an essential component of the battery supply chain. Market participants are likely to focus on further optimizing operational efficiency and environmental performance, with consolidation among recyclers and integration within broader battery recycling ecosystems anticipated as key trends.
Regulatory Landscape: International Policies and Standards
The regulatory landscape governing nickel-cadmium (Ni-Cd) battery recycling is evolving rapidly in 2025, driven by increasing environmental concerns and international commitments to hazardous waste management. Ni-Cd batteries, which contain toxic cadmium, are subject to stringent controls in many jurisdictions due to risks associated with improper disposal. The regulatory framework is largely shaped by international conventions, regional directives, and national policies, all emphasizing extended producer responsibility (EPR), collection targets, and best available recycling technologies.
At the global level, the Basel Convention continues to serve as the principal treaty controlling the transboundary movement and disposal of hazardous wastes, including spent Ni-Cd batteries. In 2025, signatory nations remain obligated to ensure that exports, imports, and recycling of Ni-Cd batteries adhere to strict environmental and safety standards set by the convention. The Convention’s Technical Guidelines on the Environmentally Sound Management of Waste Lead-acid and Ni-Cd Batteries have been updated to reflect advances in recycling technologies and material recovery processes.
In the European Union, the Battery Directive (Directive 2006/66/EC) remains the cornerstone of battery recycling regulation. The directive, as amended, imposes a ban on landfilling or incineration of industrial and automotive Ni-Cd batteries and requires producers to finance the collection, treatment, and recycling of spent batteries. The directive mandates a minimum recycling efficiency of 75% by average weight for Ni-Cd batteries. Ongoing discussions in 2025 about further revisions to the directive focus on tightening recycling targets and incorporating new reporting and traceability requirements to support a circular economy approach.
North America follows similar trends. In the United States, the Mercury-Containing and Rechargeable Battery Management Act guides the collection and recycling of Ni-Cd batteries, with additional state-level regulations in place. The Rechargeable Battery Recycling Corporation, now operating as Call2Recycle, continues to manage a national collection program in partnership with manufacturers, retailers, and municipalities. Canada enforces comparable stewardship programs under provincial regulations, emphasizing EPR and voluntary industry initiatives.
Asia-Pacific countries are also updating their frameworks. China, a major producer and consumer of Ni-Cd batteries, enforces strict hazardous waste management rules under its Solid Waste Pollution Prevention Law, obligating manufacturers to establish recycling systems for spent batteries. Japan maintains collection and recycling requirements under its Act on the Promotion of Effective Utilization of Resources, with industry groups like the Japan Portable Rechargeable Battery Recycling Center coordinating compliance and technology adoption.
Looking ahead, regulators globally are expected to further harmonize standards and reporting requirements, prioritizing closed-loop recycling and the phase-out of hazardous chemistries where feasible. As technological advances improve recovery rates and environmental performance, the regulatory focus is likely to shift toward higher collection targets, stricter monitoring, and incentives for innovation in recycling processes.
Leading Recycling Technologies: Mechanical, Hydrometallurgical, and Pyrometallurgical Processes
Nickel-cadmium (Ni-Cd) battery recycling remains a critical component in the sustainable management of hazardous materials and the recovery of valuable metals. As global regulations tighten and extended producer responsibility becomes more widespread, the battery recycling sector is experiencing a pronounced drive toward improved efficiency and environmental safety. In 2025 and the near future, three primary recycling technologies continue to dominate: mechanical, hydrometallurgical, and pyrometallurgical processes.
Mechanical Processes
Mechanical recycling typically serves as the first stage in Ni-Cd battery treatment. It involves dismantling batteries, followed by crushing and sorting to separate metallic, plastic, and other fractions. Renowned companies such as Umicore and Accurec Recycling GmbH employ advanced mechanical pre-processing lines to optimize material separation, improve safety, and limit environmental emissions. The latest innovations focus on higher automation, improved dust collection, and more precise sorting, paving the way for cleaner downstream processes.
Hydrometallurgical Processes
Hydrometallurgy is increasingly favored for its selectivity and lower energy requirements. After mechanical pre-treatment, the cadmium and nickel compounds are leached in aqueous solutions. Selective precipitation, solvent extraction, or ion exchange methods are then applied to recover cadmium, nickel, and sometimes cobalt. Companies like Saft (part of the TotalEnergies group) and Société Nationale des Métaux et Minéraux are investing in hydrometallurgical pilot plants to meet stricter environmental regulations and maximize metal yields. The 2025 outlook includes scaling up closed-loop systems, reducing reagent consumption, and integrating renewable energy sources into recycling operations.
Pyrometallurgical Processes
Pyrometallurgical recycling, traditionally the dominant method, involves high-temperature smelting to recover metals. This method is robust and can handle mixed battery streams but requires substantial energy and careful management of emissions due to the hazardous nature of cadmium. Glencore, a global leader in non-ferrous metals recycling, continues to operate large-scale pyrometallurgical facilities, focusing on emission controls and recovery efficiency. Newer furnace designs and advanced off-gas treatment systems are enabling compliance with evolving environmental standards.
Outlook
Looking ahead, the recycling of Ni-Cd batteries is evolving toward hybridized processes—combining mechanical, hydro-, and pyrometallurgical steps for optimal recovery and minimal environmental impact. Regulatory pressures in the EU, US, and Asia-Pacific are expected to further accelerate the adoption of advanced recycling technologies. Companies with integrated recycling chains and strong R&D, such as Umicore and Glencore, are poised to lead the sector, while smaller specialized recyclers are increasingly adopting modular and scalable solutions.
Emerging Innovations: Automation, AI, and Green Chemistry in Recycling
Nickel-cadmium (Ni-Cd) battery recycling technologies are undergoing notable transformation in 2025, driven by stricter environmental regulations, sustainability goals, and the imperative to recover critical raw materials. The integration of automation, artificial intelligence (AI), and green chemistry is rapidly changing both the scale and sophistication of Ni-Cd battery recycling worldwide.
Automation is increasingly central to modern Ni-Cd recycling facilities. Robotics and advanced sorting systems are being deployed to efficiently dismantle batteries, separate components, and minimize human exposure to toxic cadmium dust. For instance, leading recycling firms such as Umicore and ECOBAT are investing in automated lines that increase throughput while ensuring compliance with EU and global safety standards. Adoption of real-time monitoring and automated process control systems further optimizes yield and reduces energy consumption.
AI is emerging as a vital enabler for quality control and process optimization in Ni-Cd recycling. Machine learning algorithms are being trained to identify battery chemistries, predict optimal disassembly methods, and monitor process variables for maximum material recovery. Accurec Recycling, one of Europe’s specialized battery recyclers, is piloting AI-driven diagnostic systems to sort and process batteries more efficiently while tracking cadmium emissions at every stage.
Green chemistry innovations are addressing the environmental footprint traditionally associated with Ni-Cd recycling. The industry is moving away from high-temperature pyrometallurgical methods toward hydrometallurgical and bioleaching techniques that use less energy and generate fewer hazardous byproducts. Companies like Umicore are exploring closed-loop systems that employ selective chemical leaching and advanced filtration to recover cadmium and nickel with minimal waste. These greener processes are projected to become more prevalent over the next few years as regulatory pressure and public scrutiny increase.
Globally, the outlook for Ni-Cd battery recycling in the near future is shaped by a transition to more sustainable battery chemistries, yet the volume of legacy Ni-Cd batteries entering recycling streams remains substantial. As markets such as Europe and Asia enforce stricter recycling quotas, advancements in automation, AI, and green chemistry will be critical for recyclers to remain compliant and competitive. Continuous innovation, supported by major players like ECOBAT and Umicore, is expected to further reduce costs and environmental impact, ensuring that Ni-Cd batteries are recycled efficiently and safely through the remainder of their lifecycle.
Competitive Analysis: Profiles of Top Industry Players
The nickel-cadmium (Ni-Cd) battery recycling sector in 2025 is characterized by a small but active group of established players, driven by regulatory mandates, mature collection systems, and the drive to recover toxic cadmium and valuable nickel. As Ni-Cd batteries become less common in consumer applications due to environmental restrictions, recycling activity increasingly focuses on industrial sources, such as emergency lighting, rail, and aviation. The competitive landscape is defined by a handful of specialized recyclers operating large-scale hydrometallurgical and pyrometallurgical facilities, often licensed or contracted by battery producers and compliance schemes.
- Umicore: Headquartered in Belgium, Umicore is widely recognized as one of the global leaders in Ni-Cd battery recycling. The company operates a network of integrated recycling plants in Europe, notably in Belgium, and utilizes advanced hydrometallurgical processes to recover nickel, cadmium, and cobalt. In recent years, Umicore has emphasized closed-loop recycling and strict environmental controls, positioning itself as a preferred partner for European compliance schemes and OEMs. The company’s capacity and technical expertise enable it to process both consumer and industrial Ni-Cd streams.
- BatterieIngenieure GmbH: Germany-based BatterieIngenieure GmbH has developed specialized diagnostic and recycling services for Ni-Cd batteries, particularly in industrial and transportation sectors. Their approach combines diagnostics, disassembly, and materials recovery, ensuring that valuable metals are efficiently extracted and hazardous waste is minimized. Their partnerships with German and European waste collection bodies have facilitated streamlined logistics for end-of-life Ni-Cd batteries.
- Recylex S.A.: French company Recylex S.A. manages a significant share of Europe’s Ni-Cd recycling, operating both pyrometallurgical and hydrometallurgical lines. Recylex is notable for its extensive network for battery collection and its ability to process mixed battery chemistries. Their operations are aligned with EU directives, and the company is investing in process upgrades to improve cadmium recovery rates and reduce emissions.
- Retriev Technologies: North American recycler Retriev Technologies (formerly Toxco) is one of the region’s few large-scale Ni-Cd recyclers. With facilities in the US and Canada, Retriev processes a substantial proportion of industrial Ni-Cd batteries, using both mechanical and thermal separation techniques. The company collaborates with manufacturers, compliance organizations, and government agencies to ensure regulatory compliance and maximize material recovery.
Looking ahead, Ni-Cd recycling capacity is expected to remain stable or decline slightly, reflecting reduced battery demand, but regulatory pressure for safe cadmium disposal ensures continued activity. Leading companies are investing in process efficiency, emissions control, and automation. Collaborations with battery stewardship programs and OEMs are key for feedstock security. The competitive landscape remains concentrated, with high technical barriers limiting new entrants.
Supply Chain Dynamics: Collection, Logistics, and Material Flow
Nickel-cadmium (Ni-Cd) batteries, once prevalent in portable electronics and industrial applications, remain a significant focus for recycling due to their hazardous cadmium content and valuable nickel. In 2025, supply chain dynamics for Ni-Cd battery recycling are shaped by tightening environmental regulations, advancements in collection and logistics, and evolving material flow strategies to maximize resource recovery and minimize environmental risks.
Collection networks in the Ni-Cd battery recycling sector have become increasingly structured, driven by extended producer responsibility (EPR) policies and stricter enforcement across regions such as the European Union and North America. Organizations like Accurec Recycling in Germany and Umicore in Belgium operate extensive collection programs, partnering with manufacturers, retailers, and municipal collection points to aggregate post-consumer and industrial batteries. These networks are complemented by mobile collection events and reverse logistics strategies, ensuring even small quantities from distributed sources are efficiently gathered. In the United States, Call2Recycle acts as a central stewardship organization, coordinating collection from over 16,000 public drop-off sites and facilitating logistics between stakeholders.
Logistics for Ni-Cd battery transport in 2025 are increasingly sophisticated, as regulatory frameworks—such as the EU Battery Regulation—demand traceability and safety in handling hazardous materials. Specialized containers, secure labeling, and digital tracking systems are standard practice, minimizing the risk of leakage, fire, or environmental release during transit. Leading recyclers such as Ecobat and Battery Solutions have adopted advanced inventory and tracking software, integrating data across their supply chains to enhance transparency and regulatory compliance. Moreover, cross-border shipments of Ni-Cd batteries are subject to the Basel Convention controls, requiring detailed documentation and pre-notification procedures.
Material flow within recycling facilities has evolved to prioritize both safety and recovery rates. Upon arrival, batteries are sorted by chemistry, with Ni-Cd units separated for dedicated processing lines. Leading facilities, such as those operated by Umicore, utilize hydrometallurgical and pyrometallurgical techniques to extract nickel and cadmium. These processes are continuously optimized to improve yield, reduce emissions, and enable closed-loop recycling, where recovered metals re-enter battery manufacturing or other industrial uses.
Looking forward, the outlook for Ni-Cd battery recycling supply chains in the next few years is marked by increasing automation, more granular tracking, and broader international harmonization of standards. Companies are investing in digital twin technology and artificial intelligence to optimize collection routes and material flow. Meanwhile, the anticipated phase-down of Ni-Cd batteries in new products—due to regulatory restrictions—shifts supply chain focus toward legacy waste streams, emphasizing the importance of robust logistics and efficient recycling technologies to responsibly manage the remaining inventory and recover critical materials.
Environmental and Economic Impact Assessment
Nickel-Cadmium (Ni-Cd) battery recycling technologies are undergoing significant transformation as environmental regulations tighten and resource recovery becomes increasingly vital. In 2025, the environmental and economic impacts of these technologies are shaped by evolving recycling processes, corporate investments, and global efforts to mitigate the adverse effects of hazardous cadmium waste.
Ni-Cd batteries, classified as hazardous waste due to their cadmium content, pose substantial risks to soil and water if not properly managed. As a result, the European Union and other regions have enforced strict recycling mandates, leading to advancements in hydrometallurgical and pyrometallurgical recycling processes. Hydrometallurgical methods, which use aqueous chemistry to separate metals, are favored for their lower environmental impact compared to traditional pyrometallurgical (high-temperature) approaches. These processes enable the recovery of both nickel and cadmium, reducing landfill burden and minimizing toxic emissions.
In 2025, major industry players such as Umicore and Accurec Recycling GmbH are at the forefront of Ni-Cd battery recycling in Europe. Umicore operates integrated facilities capable of processing industrial-scale battery waste, employing advanced hydrometallurgical techniques to recover metals with high efficiency. Accurec Recycling GmbH, another specialized recycler, emphasizes closed-loop recycling systems that minimize energy consumption and environmental pollution. Both companies contribute not only to resource conservation but also to the reduction of CO2 emissions associated with primary metal production.
Economically, the recovery of nickel and cadmium from spent batteries provides a significant secondary raw material stream. This is increasingly important amidst volatile global metal prices and supply chain disruptions. The refined metals are reintroduced into the manufacturing cycle, supporting the circular economy and reducing dependence on primary mining operations. Moreover, complying with recycling regulations helps manufacturers and importers avoid penalties, further incentivizing investment in efficient recycling infrastructure.
Looking ahead, the next few years are expected to bring further improvements in recycling yields and automation, driven by ongoing research and the adoption of digital monitoring systems. The regulatory landscape is likely to tighten further, especially in Asia and North America, spurring additional capacity investments and technology upgrades among leading recyclers. As the market for portable electronics and industrial applications continues to transition to alternative chemistries, legacy Ni-Cd waste streams will persist, ensuring continued relevance for specialized recycling technologies.
Overall, Ni-Cd battery recycling technologies in 2025 represent a critical nexus of environmental stewardship and economic opportunity, with industry leaders like Umicore and Accurec Recycling GmbH setting benchmarks for sustainable resource management in the sector.
Strategic Partnerships and Industry Collaborations
Strategic partnerships and industry collaborations are increasingly shaping the landscape of nickel-cadmium (Ni-Cd) battery recycling technologies as the sector adapts to evolving environmental regulations and sustainability targets in 2025 and the coming years. The collaborative approach stems from the need to address the technical challenges of Ni-Cd battery recycling—specifically, the safe handling of toxic cadmium and efficient recovery of nickel for reuse in new batteries or other applications.
Among the leading forces in this space is Umicore, a global materials technology and recycling group headquartered in Belgium. Umicore operates advanced battery recycling facilities in Europe, focusing on recovering valuable metals from end-of-life batteries, including Ni-Cd chemistries. The company actively forges partnerships with battery manufacturers, electronics producers, and waste management firms to ensure a steady supply of spent batteries and to optimize collection logistics. In recent years, Umicore has expanded its collaboration network to include automakers and industrial equipment suppliers, aiming to streamline the flow of industrial Ni-Cd waste into their recycling system.
Another key player is SNAM, based in France, which specializes in the recycling of various battery types, with a significant focus on Ni-Cd batteries from industrial and portable sources. SNAM partners with original equipment manufacturers (OEMs) and compliance schemes across Europe to facilitate the take-back and processing of spent batteries, ensuring compliance with the EU Battery Directive and fostering circular economy practices. Their ongoing collaboration with logistics companies and hazardous waste handlers supports the safe and efficient transport of Ni-Cd batteries to recycling facilities.
In North America, Call2Recycle operates the continent’s largest battery collection and recycling program, collaborating with manufacturers, retailers, municipalities, and recyclers to manage consumer and industrial Ni-Cd battery waste. Strategic partnerships with retail chains and electronics distributors are central to expanding collection points and raising public awareness about proper disposal and recycling options. Call2Recycle’s alliances with certified downstream recycling partners ensure that recovered nickel and cadmium are processed in compliance with stringent environmental standards.
Looking ahead, the sector anticipates further consolidation and cross-border collaboration, particularly as new EU and North American regulatory frameworks tighten recycling efficiency targets for Ni-Cd batteries. Joint ventures between recyclers, automotive OEMs, and raw materials suppliers are expected to intensify, with an emphasis on technology sharing and co-investment in advanced hydrometallurgical and pyrometallurgical recycling processes. These alliances will be pivotal to scaling up capacity, enhancing metal recovery rates, and minimizing the environmental footprint of Ni-Cd battery recycling throughout 2025 and beyond.
Future Outlook: Investment Opportunities and Technology Roadmap
Nickel-cadmium (Ni-Cd) battery recycling technologies are entering a critical phase in 2025, as regulatory pressures, sustainability goals, and market dynamics converge to accelerate innovation and investment. The European Union’s Battery Regulation, which mandates strict recycling efficiencies and cadmium recovery targets, is a major driver shaping the sector. Globally, the Ni-Cd battery market is relatively mature and shrinking in consumer segments due to environmental concerns, but industrial and backup power applications keep volumes significant, ensuring a continued need for advanced recycling infrastructure.
Leading players in the recycling domain, such as Umicore, Snam, and Battery Solutions, are making strategic investments to upgrade processing facilities and implement more efficient hydrometallurgical and pyrometallurgical processes. Umicore, for instance, leverages high-temperature smelting technology to recover cadmium and nickel with minimal emissions, aligning with EU environmental compliance. Meanwhile, Snam is expanding its footprint in Europe, focusing on closed-loop recycling systems that enable the reintroduction of recovered metals into battery manufacturing, thus supporting circular economy objectives.
Technological advancements in the next few years are expected to address challenges associated with cadmium toxicity and process safety. Investments are being funneled into automation, real-time monitoring, and improved separation and purification methods to increase recovery rates and reduce operational risks. Industry consortia and battery stewardship programs, such as those spearheaded by Call2Recycle in North America and the European Battery Alliance, are fostering public-private partnerships to streamline collection logistics and raise consumer awareness.
Looking ahead, the investment outlook remains cautiously optimistic. While lithium-ion battery recycling attracts the lion’s share of venture capital, Ni-Cd recycling technologies are poised for incremental growth, underpinned by regulatory mandates and the residual need for cadmium management. Companies with demonstrated technological expertise and robust compliance track records—such as Umicore and Snam—are likely to capture the largest share of new investment, particularly as governments introduce extended producer responsibility (EPR) schemes and green procurement policies.
- By 2025–2027, the focus will be on scaling up existing technologies and integrating digitalization for traceability and efficiency.
- Emerging partnerships between recyclers and battery manufacturers are expected to enhance material circularity.
- Regulatory harmonization across regions will further drive technology standardization and cross-border investment opportunities.
Overall, the next few years will see a steady modernization of Ni-Cd battery recycling, driven by compliance obligations, environmental stewardship, and the pursuit of greater resource efficiency.
Sources & References
- Umicore
- SNAM
- GEM Co., Ltd.
- Accurec Recycling GmbH
- TotalEnergies
- ECOBAT
- BatterieIngenieure GmbH
- Recylex S.A.
- Retriev Technologies
- Ecobat