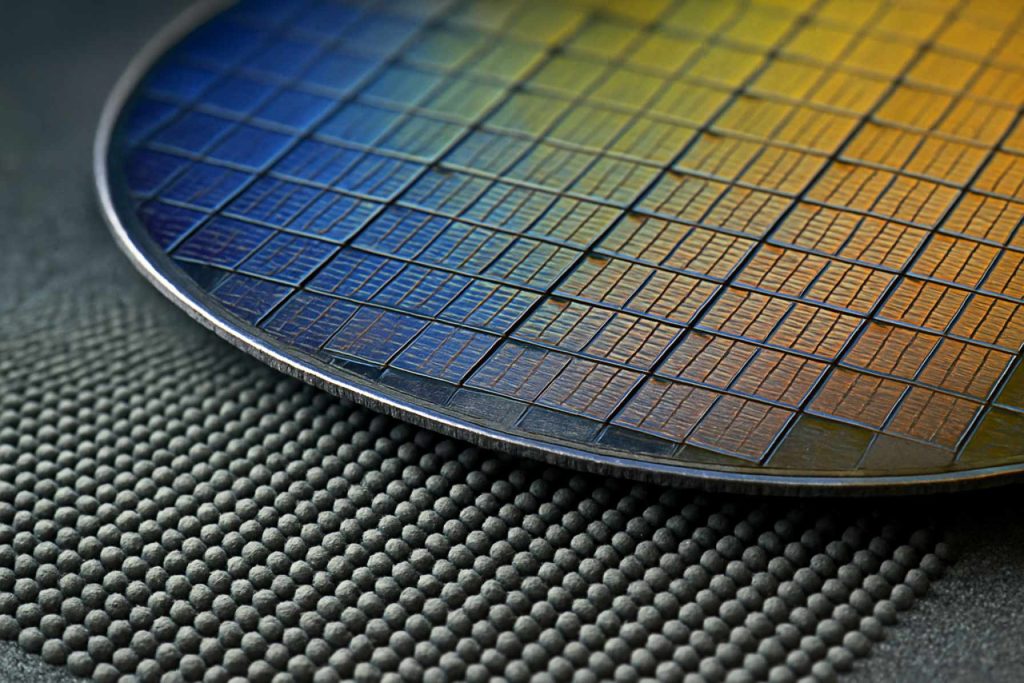
Table of Contents
- Executive Summary: Oxide Nanodot Technologies in 2025
- Market Size and Growth Forecasts Through 2030
- Key Applications: Electronics, Energy Storage, and Catalysis
- Emerging Fabrication Methods and Process Innovations
- Top Industry Players and Strategic Partnerships
- Regulatory and Standards Landscape (IEEE, ISO)
- Supply Chain Dynamics and Material Sourcing
- Investment Trends and Funding Activity
- Challenges: Scalability, Quality Control, and Environmental Impact
- Future Outlook: Disruptive Potential and Next-Gen Opportunities
- Sources & References
Executive Summary: Oxide Nanodot Technologies in 2025
The fabrication of oxide nanodots—nanoscale structures composed of metal oxides—has reached a pivotal stage in 2025, driven by advances in atomic-scale engineering and increasing demand from the semiconductor, memory, and sensor industries. These nanodots, typically ranging from 1 to 100 nanometers in diameter, exhibit unique electronic, optical, and catalytic properties, making their controlled synthesis a matter of strategic importance for next-generation devices.
The primary fabrication routes in use today include bottom-up methods such as atomic layer deposition (ALD), molecular beam epitaxy (MBE), and chemical vapor deposition (CVD), as well as top-down approaches like electron beam lithography (EBL) and nanoimprint lithography (NIL). In 2025, the emphasis has shifted towards scalable and cost-effective manufacturing, with industry leaders such as Oxford Instruments providing advanced ALD and MBE systems tailored for high-uniformity nanodot arrays. ALD, in particular, has gained traction for its atomic-level thickness control, enabling precise tuning of nanodot size and composition—a key requirement for memory and logic applications.
For high-throughput production, NIL has emerged as a strong contender. Companies like NIL Technology have introduced nanoimprint platforms capable of replicating patterns at sub-10 nm dimensions over wafer-scale areas, addressing the critical need for mass production compatibility. NIL’s ability to create highly ordered nanodot arrays is fostering its adoption in photonics and biosensing sectors, where pattern fidelity and throughput are paramount.
Meanwhile, advances in directed self-assembly (DSA) of block copolymers are being integrated with conventional lithographic techniques to achieve even smaller feature sizes and improved regularity. Equipment manufacturers such as ASML are actively developing DSA-capable platforms, anticipating that hybrid approaches will unlock new design possibilities in oxide nanodot patterning beyond the limitations of traditional photolithography.
Looking ahead, the next few years are expected to see further convergence between top-down and bottom-up fabrication methods, enabling the scalable production of complex oxide nanodot architectures with atomic precision. The integration of real-time process monitoring and AI-driven process control is also on the horizon, as highlighted by KLA Corporation’s newest inspection and metrology solutions, which are designed to ensure defect-free nanodot manufacturing at industrial scale.
As nanodot-based memory, logic, and sensing devices approach commercialization, the ecosystem of tool vendors, materials suppliers, and device manufacturers is poised for rapid growth and innovation, underscoring the vital role of advanced fabrication technologies in shaping the future of the oxide nanodot industry.
Market Size and Growth Forecasts Through 2030
The oxide nanodot fabrication technologies market is poised for significant expansion through 2030, underpinned by robust demand from electronics, optoelectronics, data storage, and sensing applications. As of 2025, technological innovation and increasing adoption across various sectors are driving market growth. Key drivers include the miniaturization trend in microelectronics and the emergence of advanced manufacturing processes.
Recent developments reveal a shift toward scalable and cost-effective fabrication techniques. For example, ASML Holding and Lam Research Corporation have been pioneering advanced lithography and atomic layer deposition (ALD) processes, enabling the controlled creation of oxide nanodots with high uniformity and reproducibility. Such advancements are critical for meeting the stringent demands of next-generation memory and logic devices.
In tandem, the materials segment is seeing dynamic activity. Companies such as Entegris, Inc. are supplying high-purity precursors and process chemicals tailored for ALD and chemical vapor deposition (CVD) of oxide nanostructures, ensuring consistent quality and performance. These contributions are essential for the reliable manufacturing of nanodots at commercial scale.
Industry experts anticipate the market to witness double-digit compound annual growth rates (CAGR) through 2030. This projection is supported by ongoing collaborations between fabrication equipment suppliers and leading semiconductor foundries, such as Taiwan Semiconductor Manufacturing Company (TSMC) and Intel Corporation, both of which are investing in next-generation oxide nanodot integration for advanced memory and logic nodes.
Looking ahead, the adoption of novel patterning methods—such as nanoimprint lithography and self-assembly—by innovators like Nanonex is expected to further reduce production costs and enable large-area fabrication, expanding the market’s reach to new applications, including non-volatile memories, photonic devices, and biosensors. Furthermore, the increasing alignment of fabrication standards driven by industry bodies like the Semiconductor Manufacturing Technology (SEMATECH) consortium will likely facilitate broader commercialization and interoperability across the ecosystem.
In summary, the oxide nanodot fabrication technologies market is on a strong growth trajectory through 2030, fueled by continuous process innovation, expanding end-use cases, and strategic partnerships among global industry leaders.
Key Applications: Electronics, Energy Storage, and Catalysis
The fabrication of oxide nanodots has emerged as a critical technology underpinning advancements in electronics, energy storage, and catalysis, with significant momentum continuing into 2025 and forecasts for progressive scaling in the near future. Several fabrication techniques are now routinely employed at industrial and research levels, each tailored to specific application requirements and material properties.
One of the most prominent approaches is atomic layer deposition (ALD), which enables precise control over nanodot size, composition, and spatial distribution. ALD has found extensive adoption in the semiconductor sector for gate oxides and charge-trapping layers, owing to its conformity and atomic-scale thickness control. For instance, Beneq and ALD NanoSolutions continue to enhance their ALD platforms, enabling scalable production of sub-10 nm oxide nanodots for advanced memory and logic devices anticipated in 2025 and beyond.
In parallel, template-assisted methods—such as nanosphere lithography and block copolymer patterning—are witnessing refinement for large-area, cost-effective nanodot array fabrication. EV Group supports these approaches with advanced nanoimprint lithography tools, allowing integration of oxide nanodot arrays in sensors and next-generation optoelectronic devices. These methods are increasingly being coupled with self-assembly techniques to achieve high throughput and uniformity.
Colloidal synthesis remains a preferred route for producing oxide nanodots for energy storage and catalysis applications, as it allows precise tuning of surface chemistry and crystallinity. Companies such as Sigma-Aldrich (MilliporeSigma) offer an expanding portfolio of metal oxide nanodots, supporting growing demand from supercapacitor and battery manufacturers seeking enhanced electrode materials.
In the coming years, hybrid fabrication strategies—combining top-down patterning with bottom-up deposition—are expected to gain traction, addressing challenges of scalability and cost while maintaining nanoscale precision. Notably, imec is actively involved in developing such combinatorial techniques, with pilot lines aimed at integrating oxide nanodot architectures into commercial memory and logic devices.
As oxide nanodot technologies mature, the emphasis is shifting toward integration into existing manufacturing ecosystems and scaling for commercial deployment. The next few years are projected to see increased collaboration between equipment providers, materials suppliers, and end-users to optimize process reliability and yield, meeting the stringent requirements of electronics, energy storage, and catalytic markets.
Emerging Fabrication Methods and Process Innovations
The fabrication of oxide nanodots—crucial for next-generation memory, sensing, and catalysis applications—has seen marked innovation entering 2025, driven by demands for ever-smaller, highly uniform nanostructures. Traditional techniques such as electron beam lithography (EBL) and nanoimprint lithography (NIL) remain foundational, but their scalability and cost have spurred the search for alternative methods. Recent advances focus on bottom-up approaches, atomic layer control, and hybrid patterning.
Atomic layer deposition (ALD) has emerged as a core technology for producing uniform oxide nanodots at wafer scale, offering atomic-level thickness control and conformal coatings on complex geometries. Leading ALD system providers, such as Beneq and Picosun (now part of Applied Materials), are integrating advanced precursor chemistries and in situ monitoring to enable sub-10 nm dot formation, especially for hafnium and titanium oxides. These developments allow for tighter pitch and higher device densities in memory and logic devices.
Self-assembly techniques, notably block copolymer (BCP) lithography, are gaining commercial viability. BCP-based patterning, championed by materials suppliers like Dow, enables the spontaneous formation of nanodot arrays with tunable diameters and spacing. In 2025, process integration efforts focus on combining BCP lithography with traditional pattern transfer steps, improving overlay accuracy, and reducing defectivity to meet semiconductor industry standards.
Direct-write approaches using focused ion beams or scanning probe methods continue to evolve, with companies such as Thermo Fisher Scientific enhancing beam stability and throughput. These methods, while slower, are valuable for prototyping, mask repair, and niche applications requiring custom nanodot patterns or ultra-high spatial resolution.
Furthermore, hybrid fabrication routes are being explored, merging top-down and bottom-up techniques. For example, Canon Inc. and ASML are investing in next-generation lithography platforms that incorporate novel resist materials and pattern multiplication schemes for oxide nanodot arrays.
Looking ahead, with the drive toward sub-5 nm features and 3D nanostructures, the industry anticipates a convergence of ALD, self-assembly, and advanced lithography. The push for greener manufacturing is also prompting the development of low-temperature, solution-based oxide nanodot fabrication, as seen in pilot lines by Merck KGaA. Collectively, these innovations in oxide nanodot fabrication are poised to support the surging demand for high-density, energy-efficient electronic and photonic devices over the next several years.
Top Industry Players and Strategic Partnerships
The landscape of oxide nanodot fabrication technologies is rapidly evolving, with major industry players and strategic partnerships shaping the field as we move into 2025 and beyond. Key global manufacturers are investing in advanced lithography, atomic layer deposition (ALD), and chemical vapor deposition (CVD) techniques to meet growing demand in electronics, optoelectronics, and energy storage applications.
Among the leaders, Applied Materials, Inc. continues to expand its portfolio of nanofabrication solutions, leveraging ALD and advanced etching systems to enable sub-10 nm oxide nanostructures. Their recent collaborations with semiconductor foundries signal a push towards higher-volume, cost-effective nanodot production for next-generation memory and logic devices.
Meanwhile, Lam Research Corporation has focused on plasma-enhanced ALD and atomic precision processing, key to achieving the uniformity and scalability required for oxide nanodot arrays in advanced DRAM and non-volatile memory components. Their technology partnerships with major chipmakers underscore the strategic importance of oxide nanodots in pushing Moore’s Law and heterogeneous integration.
On the materials side, Entegris, Inc. is supplying high-purity precursors and process chemistries tailored for oxide nanodot deposition, forging close relationships with tool suppliers and device manufacturers. Their 2024-2025 initiatives include joint development programs targeting improved yield and defect control for high-k dielectric nanodots.
In Europe, ASM International N.V. has expanded its ALD tool offerings, emphasizing low-temperature processes compatible with flexible substrates and 3D nanodot architectures. Strategic alliances with research institutes and integrated device manufacturers (IDMs) are enabling transfer of lab-scale nanodot processes to high-throughput industrial platforms.
Additionally, Tokyo Ohka Kogyo Co., Ltd. (TOK) is pioneering advanced photoresists and patterning materials optimized for oxide nanodot formation through extreme ultraviolet (EUV) lithography and nanoimprint technologies. Their partnerships with leading semiconductor fabs and toolmakers are crucial to advancing high-resolution nanodot patterning.
Looking ahead, the industry is witnessing increased cross-border collaborations, such as joint ventures between equipment suppliers and material providers to co-develop integrated nanodot fabrication ecosystems. These strategic partnerships are aimed at accelerating the commercialization of oxide nanodot-enabled devices in emerging markets such as quantum computing, neuromorphic circuits, and next-generation sensors.
Regulatory and Standards Landscape (IEEE, ISO)
The regulatory and standards landscape for oxide nanodot fabrication technologies is evolving rapidly as the field matures and transitions from laboratory-scale innovation to commercial-scale manufacturing. In 2025 and looking ahead, both international and industry-specific bodies are actively shaping the guidelines that will govern the safe, reproducible, and scalable production of oxide nanodots for electronics, photonics, and biomedical applications.
The International Organization for Standardization (ISO) has been instrumental in setting foundational standards for nanomaterials, including those relevant to oxide-based nanostructures. ISO Technical Committee 229 (Nanotechnologies) continues to refine standards such as ISO/TS 80004-1:2015, which provides vocabulary for nanomaterials, and ISO/TR 16197:2014, which addresses the physicochemical characterization of engineered nanoparticulate materials, including oxides. In 2025, ISO is working toward new guidance documents that specifically address the unique challenges of oxide nanodot size uniformity, purity, and surface functionalization, with draft standards expected for public comment in the next two years.
On the electronics standards front, the Institute of Electrical and Electronics Engineers (IEEE) is a key driver. The IEEE Nanotechnology Council is leading initiatives to establish performance benchmarks and interoperability metrics for oxide nanodot arrays used in advanced memory and sensor devices. The anticipated release of updated guidelines under the IEEE P1650 project will incorporate reliability testing protocols and environmental safety considerations for nanofabrication processes, reflecting the growing industrial interest in oxide nanodot-enabled technologies.
In parallel, industry consortia such as the SEMI (Semiconductor Equipment and Materials International) and the Semiconductor Industry Association are collaborating with regulatory agencies and academic partners to align fabrication standards with existing semiconductor manufacturing practices. Their focus for 2025 includes harmonizing quality control methodologies and developing best practices for the integration of oxide nanodot processes into established cleanroom environments.
Looking ahead, the regulatory environment is expected to become more stringent as applications of oxide nanodots in critical sectors—such as medical diagnostics and quantum computing—advance toward commercialization. Ongoing engagement between standards bodies, manufacturers, and regulators will be essential to ensure that compliance frameworks keep pace with technological innovation, providing both safety assurances and fostering global interoperability for oxide nanodot fabrication.
Supply Chain Dynamics and Material Sourcing
The supply chain dynamics and material sourcing for oxide nanodot fabrication technologies in 2025 are shaped by increasing demand for advanced electronic, energy, and sensing applications. Recent years have seen major semiconductor and materials manufacturers invest in the development of scalable, high-purity oxide nanodot production lines to support next-generation devices.
A significant trend is the vertical integration of supply chains by leading foundries and specialty material suppliers. Companies such as TSMC and Samsung Electronics have expanded their in-house capabilities for atomic layer deposition (ALD) and molecular beam epitaxy (MBE)—key techniques for producing uniform oxide nanodots at sub-10 nm scales. This internalization reduces reliance on external suppliers for critical oxide precursors and substrate materials, enhancing supply chain resilience amid geopolitical and logistical uncertainties.
Material sourcing for oxide nanodot fabrication is increasingly focused on purity and traceability. Oxide targets (e.g., hafnium oxide, zinc oxide, titanium dioxide) used in physical vapor deposition and ALD are now sourced from specialized chemical suppliers such as Alfa Laval and Merck KGaA, which have ramped up investments in purification and quality assurance systems. These suppliers work closely with device manufacturers to customize material properties for specific electrical and optical functionalities, reflecting a shift toward collaborative, just-in-time supply models.
Emerging regulations on critical minerals, particularly concerning indium and rare earth dopants, are prompting manufacturers to diversify sourcing and invest in recycling initiatives. For example, Umicore has expanded its recycling operations to recover indium oxide and other valuable compounds from electronic waste, bolstering supply chain sustainability and reducing exposure to raw material volatility.
Looking ahead to the next few years, industry outlook is cautiously optimistic. The maturation of digital inventory management and blockchain-enabled traceability is expected to further streamline oxide nanodot material flows. However, securing consistent supplies of ultra-high-purity precursors remains a challenge, particularly as demand surges from quantum computing and advanced memory sectors. Leading industry bodies such as SEMI are coordinating efforts to standardize material specifications and promote greater supply chain transparency, aiming to support the robust and sustainable growth of oxide nanodot fabrication technologies through the late 2020s.
Investment Trends and Funding Activity
The investment landscape for oxide nanodot fabrication technologies in 2025 is characterized by a combination of strategic corporate funding, government-backed initiatives, and growing venture capital interest. As oxide nanodots become increasingly critical to next-generation electronics, sensors, and energy devices, the sector is witnessing a shift from purely academic research to commercialization-focused investment.
Major semiconductor manufacturers have announced dedicated funding to advance oxide nanodot fabrication. In 2024, Taiwan Semiconductor Manufacturing Company (TSMC) revealed an expansion of its R&D budget, with a portion allocated to novel nanofabrication techniques that include oxide-based nanodots for advanced memory and logic devices. Similarly, Intel Corporation has outlined further investments in atomic-layer deposition (ALD) and related nanoscale patterning methods—key for oxide nanodot formation—within its roadmap for sub-2nm technology nodes.
Government funding programs in the US, Europe, and Asia have prioritized oxide nanomaterials. In the United States, the Department of Energy continues to support research consortia targeting scalable oxide nanodot synthesis for energy-efficient electronics and quantum applications, with several new grants awarded for 2025-2026. The European Commission’s Horizon Europe program has earmarked funding for collaborative projects focusing on oxide nanodot-enabled devices, including sensors and neuromorphic components, building on initiatives such as the NANO-ARCH project.
On the venture capital front, startups specializing in advanced nanofabrication have secured Series A and B rounds, driven by demand from the semiconductor, photonics, and biomedical industries. For instance, Imperial College London spinout Nanofabrication Ltd. announced a £5M funding round aimed at scaling up production of oxide nanodot arrays through proprietary lithography and deposition techniques. In Asia, Samsung Electronics is reportedly increasing investment in research alliances focused on oxide nanodots for memory and neuromorphic hardware.
Looking ahead to 2025 and beyond, the trend is toward larger funding allocations for pilot production lines and scale-up infrastructure. Collaborative investment models—linking industry leaders, national labs, and academic institutions—are expected to accelerate translation from lab-scale demonstrations to manufacturable processes. The sector’s robust funding activity underscores a broad recognition of oxide nanodots as foundational to the next wave of microelectronic and quantum technologies.
Challenges: Scalability, Quality Control, and Environmental Impact
The rapid advancement of oxide nanodot fabrication technologies has brought forth significant opportunities, particularly in electronics, photonics, and catalysis. However, as the industry approaches 2025 and anticipates further expansion in the following years, several challenges must be addressed to ensure sustainable and reliable scale-up. The principal concerns revolve around scalability, quality control, and environmental impact.
Scalability remains a core challenge as the transition from laboratory-scale fabrication to industrial-scale production of oxide nanodots is still fraught with complexity. Techniques such as atomic layer deposition (ALD) and nanoimprint lithography are increasingly being refined for high-throughput applications. For example, Applied Materials has been developing advanced ALD systems capable of producing uniform oxide layers over large substrates, but maintaining precise nanodot size and distribution at wafer-scale volumes is an ongoing challenge due to process variability and equipment limitations. Furthermore, companies like Veeco Instruments Inc. are pushing for improvements in process repeatability and material utilization, yet the high cost and technical requirements for uniformity currently limit widespread adoption.
Quality control is another significant hurdle, particularly given the critical dependence of device performance on nanodot uniformity, composition, and defect density. Inline metrology and process monitoring tools are being integrated into fabrication lines to address these issues. Organizations such as KLA Corporation are deploying advanced inspection and measurement systems tailored to nanometer-scale features, aiming to identify defects and ensure consistency. However, as nanodots decrease in size and increase in array complexity, the need for highly sensitive, non-destructive quality assessment tools becomes even more pressing.
Environmental impact is also coming under increasing scrutiny, especially in light of global sustainability mandates and the semiconductor industry’s pledge to reduce carbon emissions. Many oxide nanodot fabrication processes rely on precursors or etchants that pose environmental and health risks. Leading manufacturers, including Lam Research, are investing in greener chemistries and waste minimization protocols, such as closed-loop recycling of process gases and the adoption of low global warming potential (GWP) chemicals. Life cycle assessments are being integrated into process design to anticipate and mitigate environmental footprints.
Looking forward, overcoming these challenges will require continued collaboration between equipment manufacturers, material suppliers, and end-users. The next few years are likely to see further advancements in scalable, environmentally responsible fabrication methods and robust quality control systems, paving the way for the broader commercialization of oxide nanodot technologies.
Future Outlook: Disruptive Potential and Next-Gen Opportunities
As the semiconductor and nanotechnology sectors advance toward sub-5 nm device architectures, oxide nanodot fabrication technologies are gaining significant momentum. The period from 2025 onward will likely witness a confluence of innovations, with scalable, high-throughput, and cost-effective methods at the forefront. Atomic Layer Deposition (ALD), Electron Beam Lithography (EBL), and self-assembly techniques are expected to be pivotal in enabling next-generation oxide nanodots for applications spanning memory, quantum computing, catalysis, and sensing.
In 2025, leading suppliers of ALD systems, such as Picosun and Beneq, are scaling up their equipment to meet demand for ultra-thin, highly uniform oxide nanodot arrays. Their recent product roadmaps emphasize sub-nanometer thickness control and compatibility with a broad range of oxide chemistries, facilitating integration into advanced CMOS and neuromorphic device platforms. Similarly, Oxford Instruments is developing next-gen plasma-enhanced ALD reactors designed for high-volume manufacturing, supporting both traditional silicon and emerging compound semiconductor substrates.
On the lithography front, JEOL and Nion are refining EBL systems for direct writing of oxide nanodots with sub-10 nm precision. The push toward maskless, high-resolution patterning is expected to lower the barrier for prototyping and accelerate the transfer of novel oxide materials from the lab to pilot production. In parallel, directed self-assembly approaches—leveraging block copolymer templates and surface functionalization—are being advanced by equipment makers such as EV Group, enabling scalable patterning over large wafers.
Looking forward, the integration of oxide nanodot fabrication with 3D architectures is projected to unlock disruptive potential in artificial intelligence accelerators and quantum information processors. Equipment providers are aligning their R&D with industry roadmaps such as those set by SEMI, emphasizing defect control, throughput, and yield improvement. There is also a growing focus on sustainability, with manufacturers introducing low-temperature and low-waste deposition processes to minimize environmental impact.
The next few years will likely see oxide nanodot fabrication technologies become foundational to emerging device paradigms, with substantial investments in tool automation, process monitoring, and materials innovation. The collective efforts of leading equipment manufacturers and industry bodies are expected to sustain rapid progress, positioning oxide nanodots as critical enablers for the semiconductor industry’s evolution beyond Moore’s Law.
Sources & References
- Oxford Instruments
- ASML
- KLA Corporation
- Entegris, Inc.
- Nanonex
- Beneq
- EV Group
- imec
- Thermo Fisher Scientific
- Canon Inc.
- ASM International N.V.
- Tokyo Ohka Kogyo Co., Ltd.
- International Organization for Standardization (ISO)
- Alfa Laval
- Umicore
- NANO-ARCH
- Imperial College London spinout Nanofabrication Ltd.
- Veeco Instruments Inc.
- JEOL