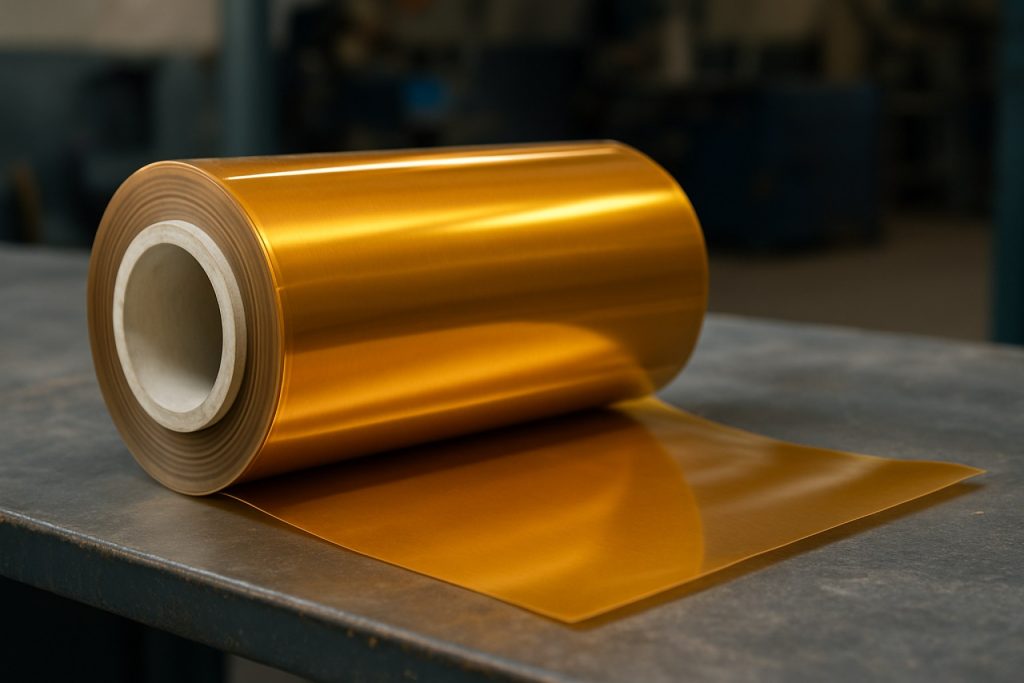
How Polyimide Membrane Sympolymerization Technologies Are Poised to Disrupt 2025 — Major Innovations, Market Shake-Ups, and What’s Next for High-Performance Applications
- Executive Summary: Key Trends and 2025 Outlook
- Polyimide Membrane Sympolymerization: Technology Primer & Evolution
- Cutting-Edge Breakthroughs: New Materials and Synthesis Techniques
- Leading Players: Company Innovations & Strategic Partnerships
- Core Applications: Electronics, Filtration, Energy, and Beyond
- Competitive Landscape: Global & Regional Market Dynamics
- Market Forecast 2025–2030: Growth Drivers, Challenges & Projections
- Regulatory Environment & Standards: Compliance and Impacts
- Future Outlook: Emerging Use Cases and Disruptive Possibilities
- Conclusion & Strategic Recommendations for Stakeholders
- Sources & References
Executive Summary: Key Trends and 2025 Outlook
Polyimide membrane sympolymerization technologies are expected to witness significant advancements and commercial momentum in 2025, driven by increasing demand for high-performance separation materials in sectors such as gas separation, water treatment, and electronics. Polyimide membranes, known for their superior thermal stability, chemical resistance, and mechanical strength, are increasingly being engineered through sympolymerization—a process leveraging the copolymerization of different diamines and dianhydrides to tailor membrane properties. This approach enables the fine-tuning of selectivity and permeability, essential for next-generation filtration and separation applications.
In 2025, global capacity expansions and technology upgrades are anticipated as major manufacturers invest in R&D and production facilities. For example, DuPont, a key innovator in advanced membrane materials, continues to enhance its product portfolio by integrating novel sympolymerization processes to improve flux and fouling resistance. Similarly, Toray Industries, Inc., a leader in polymer chemistry and membrane technology, has announced ongoing research into custom sympolymerization techniques designed to target gas separation markets, particularly for carbon capture and hydrogen recovery.
The electronics industry’s push for miniaturization and improved reliability is also fueling demand for ultra-thin, defect-free polyimide films and membranes. Kuraray Co., Ltd. and UBE Corporation are actively expanding their specialty polyimide lines to address these opportunities. These companies are focusing on fine-tuning molecular architectures via sympolymerization, aiming to achieve superior dielectric properties and thermal endurance for flexible printed circuits and chip packaging.
On the regulatory and sustainability front, sympolymerization technologies offer pathways to lower solvent use and reduced process emissions, aligning with tightening global environmental standards. Industry bodies such as American Chemistry Council are highlighting innovations in membrane fabrication that improve resource efficiency and lifecycle performance.
Looking ahead, 2025 is expected to mark a period of accelerated commercialization of sympolymerized polyimide membranes, with pilot projects transitioning to full-scale production. The focus will be on optimizing membrane architectures for specific end-uses, automation of sympolymerization processes, and integration with digital quality control systems. Strategic collaborations between material suppliers and end-users are likely to intensify, ensuring that the next generation of polyimide membrane technologies meets the evolving demands of clean energy, water purification, and advanced electronics markets.
Polyimide Membrane Sympolymerization: Technology Primer & Evolution
Polyimide membrane sympolymerization technologies are at the forefront of advanced separation and filtration solutions in 2025, evolving to meet the stringent demands of electronics, energy, and environmental sectors. Sympolymerization—also known as copolymerization—enables the fine-tuning of membrane properties such as selectivity, permeability, and thermal stability by incorporating two or more monomeric units into the polyimide backbone. This technological approach has become central to addressing the limitations of pristine polyimide membranes, particularly in high-performance gas separation, organic solvent nanofiltration, and pervaporation processes.
The last few years have witnessed a significant increase in the industrial scalability and customization potential of sympolymerized polyimide membranes. Major chemical manufacturers are leveraging their expertise in high-performance polymers to develop new monomer chemistries and process routes. For example, DuPont, a global leader in advanced materials, has expanded its polyimide membrane capabilities, focusing on copolymer systems that enhance solvent resistance and mechanical integrity for microelectronics and battery applications. Likewise, SABIC and Solvay are actively advancing membrane material platforms, integrating sympolymerization techniques to tailor molecular architecture for specific industrial separations.
The technology evolution is further propelled by the demand for membranes that can operate in aggressive chemical environments and at elevated temperatures. Sympolymerization allows for the introduction of functionalities such as ether, sulfone, or carboxyl groups, which improve processability and compatibility with other materials. Daikin Industries and Toray Industries—both recognized for their leadership in fluoropolymers and membrane science—have reported novel polyimide copolymer membranes with enhanced gas selectivity and anti-fouling properties, targeting hydrogen production and CO₂ capture markets.
Looking towards the next few years, the sector anticipates further breakthroughs in continuous and solvent-free sympolymerization processes, which promise reduced environmental impact and improved membrane uniformity. Automation, AI-driven process optimization, and modular production lines are enabling faster prototyping and scale-up. Partnerships between membrane specialists and end-users in semiconductors, pharmaceuticals, and sustainable energy are expected to accelerate commercialization of next-generation sympolymerized polyimide membranes. The intersection of advanced polymer chemistry, process engineering, and application-driven design will define the trajectory of polyimide membrane sympolymerization technologies through 2025 and beyond.
Cutting-Edge Breakthroughs: New Materials and Synthesis Techniques
Polyimide membranes have long been recognized for their outstanding thermal stability, mechanical strength, and chemical resistance, making them indispensable in high-performance separation processes. In 2025, the field is experiencing a surge in innovation driven by advancements in sympolymerization—where multiple monomers are polymerized simultaneously to fine-tune membrane properties at the molecular level. This technique is yielding membranes with unprecedented selectivity, permeability, and durability, targeting applications ranging from gas separation and pervaporation to energy storage and environmental remediation.
Recently, leading manufacturers such as DuPont and Toray Industries have unveiled next-generation polyimide membranes synthesized via controlled sympolymerization processes. These approaches allow for the incorporation of functionalized monomers and nanoparticles directly during synthesis, enabling the creation of membranes with tailored pore structures and enhanced antifouling characteristics. For instance, Toray Industries, a pioneer in advanced membrane materials, has reported success in developing sympolymerized polyimide membranes that exhibit both high gas selectivity and improved resistance to plasticization—a key limitation in conventional polyimides.
At the same time, SABIC and Evonik Industries are investing in scalable sympolymerization platforms that utilize green chemistry principles. These innovations prioritize solvent-free or low-toxicity synthesis pathways, aligning with global sustainability goals while maintaining high membrane performance. Evonik Industries, for example, is leveraging its expertise in specialty monomers to introduce new cross-linking agents during polyimide sympolymerization, resulting in membranes with finely tuned nanostructures and exceptional long-term stability under harsh industrial conditions.
Emerging collaborations with automation and process control specialists are also accelerating the commercialization of sympolymerization technologies. Companies such as DuPont are actively developing digitalized pilot lines that optimize reaction parameters in real time, improving reproducibility and scalability.
Looking ahead to the next few years, the outlook for polyimide membrane sympolymerization remains robust. Industry leaders anticipate further breakthroughs in monomer design and process intensification. The integration of advanced characterization tools and machine learning is expected to facilitate rapid screening of new sympolymerization recipes, expediting the path from discovery to industrial deployment. As regulations tighten on emissions and resource efficiency, demand for these high-performance membranes is projected to rise, with key players like Toray Industries and DuPont positioned at the forefront of innovation and supply.
Leading Players: Company Innovations & Strategic Partnerships
The landscape of polyimide membrane sympolymerization technologies in 2025 is shaped by a dynamic interplay among leading manufacturers, strategic alliances, and a wave of technological innovations. Polyimide membranes, prized for their exceptional thermal stability, chemical resistance, and selective permeability, are increasingly pivotal in advanced filtration, gas separation, and electronic applications. Recent advancements in sympolymerization—where multiple monomers are polymerized simultaneously to tailor membrane properties—have created new opportunities for performance improvements and market expansion.
Among the global leaders, DuPont continues to drive innovation, leveraging decades of expertise in polymer chemistry and membrane manufacturing. In 2024, DuPont announced enhancements to its polyimide membrane production lines, focusing on sympolymerization techniques to improve selectivity and mechanical strength for gas separation modules. The company’s ongoing collaborations with equipment suppliers and end-users in electronics and energy sectors aim to accelerate the adoption of next-generation polyimide membranes.
In Asia, Toray Industries maintains a prominent role, underpinned by robust R&D investments and strategic partnerships. Toray’s proprietary sympolymerization processes have resulted in membranes with superior durability and tunable molecular sieving capabilities, which are particularly sought after in hydrogen purification and carbon capture. The company’s joint ventures with local and international firms underscore a broader industry trend towards ecosystem-building, enabling faster scaling and technology transfer.
Another key player, Sumitomo Chemical, has focused on integrating sympolymerization with green chemistry principles. Their recent pilot programs, conducted in collaboration with academic institutions and component manufacturers, have demonstrated reduced solvent usage and lower energy consumption in membrane synthesis. These developments are not only environmentally significant but also respond to tightening global regulatory standards.
Strategic partnerships are central to accelerating market penetration and technology validation. For instance, DuPont and Toray Industries have both entered multi-year agreements with industrial gas producers and electronics manufacturers to co-develop custom membrane solutions. Such alliances are expected to intensify as demand for high-performance separation membranes grows, particularly in the semiconductor, specialty chemicals, and clean energy sectors.
Looking ahead, the next few years will likely witness further convergence between material innovation and digital process control. Companies are increasingly investing in AI-driven process optimization and real-time quality monitoring for sympolymerization reactors. As these capabilities mature, they are poised to deliver both enhanced membrane performance and greater manufacturing efficiency, solidifying the competitive positions of the sector’s leading players.
Core Applications: Electronics, Filtration, Energy, and Beyond
Polyimide membrane sympolymerization technologies are at the forefront of advanced materials innovation, underpinning critical progress in electronics, filtration, and energy sectors as of 2025 and looking ahead. Sympolymerization, involving the copolymerization of different diamines and dianhydrides, enables tailored membrane structures with enhanced mechanical, thermal, and chemical properties—traits pivotal for demanding modern applications.
In electronics, the demand for flexible, heat-resistant substrates is driving the adoption of advanced polyimide membranes. Companies such as DuPont and Kapton (DuPont) continue to expand their polyimide product lines, integrating sympolymerization to achieve finer control over film thickness, dielectric properties, and flexibility for use in flexible printed circuits, displays, and foldable devices. Industry leaders are investing in pilot lines and scaling up sympolymerization-based production to meet the needs of next-generation electronics, a trend expected to intensify through the late 2020s.
In the filtration segment, sympolymerized polyimide membranes are enabling higher selectivity and improved fouling resistance, crucial for both industrial gas separation and high-performance water purification. Toray Industries and UBE Corporation have demonstrated polyimide membrane modules with advanced copolymer compositions, targeting CO2 capture and solvent-resistant nanofiltration. Recent deployments in petrochemical and environmental sectors underscore the growing commercial viability of these technologies. Ongoing research focuses on refining monomer selection and reaction conditions to further expand operational lifespans and permeability profiles.
Energy storage and conversion applications are also leveraging sympolymerized polyimide membranes for their ionic conductivity, thermal stability, and mechanical strength. In lithium-ion batteries and emerging solid-state systems, companies like SK hynix are exploring polyimide separators to enhance safety and capacity retention. Meanwhile, research alliances involving manufacturers and academic labs are advancing sympolymerized polyimides for fuel cell and flow battery membranes, aiming for commercialization within the next three to five years.
Looking beyond 2025, continued collaboration between material suppliers, device manufacturers, and end-users is anticipated to accelerate the adoption of sympolymerization-based polyimide membranes. Advanced process control, digitalization in membrane fabrication, and the push for sustainability (including recycling and greener monomer sources) are expected to further differentiate industry leaders. As market requirements evolve, especially in flexible electronics and sustainable filtration, sympolymerization will remain a keystone technology shaping the next generation of high-performance polyimide membranes.
Competitive Landscape: Global & Regional Market Dynamics
The competitive landscape for polyimide membrane sympolymerization technologies is evolving rapidly in 2025, as global demand for advanced separation solutions in sectors such as electronics, water treatment, and gas separation accelerates. Polyimide membranes are prized for their exceptional thermal and chemical stability, and sympolymerization techniques—where two or more monomers are polymerized together—have enabled the creation of membranes with tailored properties for high-performance applications.
Asia-Pacific continues to dominate both production and innovation, with leading manufacturers in China, Japan, and South Korea scaling up capacities and investing in next-generation sympolymerization technologies. Major players such as Toray Industries and UBE Corporation in Japan have integrated advanced sympolymerization processes in their polyimide membrane product lines, targeting electronics, display, and energy sectors. Toray Industries has reported ongoing investment in R&D related to high-selectivity gas separation membranes and ultrathin film composites, leveraging sympolymerization to enhance permeability and selectivity.
In China, enterprises like Suzhou Huibo New Material and Shenzhen Best New Materials are scaling up commercial production of polyimide membranes for filtration and microelectronic applications. These companies are also collaborating with domestic research institutions to refine sympolymerization techniques for improved membrane uniformity and scalability.
In the United States, DuPont remains a prominent innovator, focusing on high-performance separation membranes for industrial and environmental markets. The company is investing in membrane chemistries that exploit sympolymerization to balance permeability, selectivity, and durability, particularly for applications in water purification and clean energy.
European firms, notably Evonik Industries in Germany, are also active, emphasizing the sustainable and energy-efficient attributes of their polyimide membrane portfolios. Investments by Evonik Industries in advanced copolymerization and hybrid sympolymerization processes are expected to yield membranes with enhanced resistance to fouling and degradation, aligning with strict EU environmental standards.
Looking ahead, competition will intensify as established players and emerging specialists strive to achieve cost-effective, scalable sympolymerization processes. The next few years will likely see increased collaboration between industrial manufacturers and academic research groups, as well as the introduction of automated, digitally controlled sympolymerization reactors to boost reproducibility and throughput. As the market matures, intellectual property and proprietary sympolymerization recipes are poised to become key differentiators, particularly as end-users seek custom solutions for challenging separation tasks.
Market Forecast 2025–2030: Growth Drivers, Challenges & Projections
The polyimide membrane sympolymerization technologies sector is projected to experience notable growth between 2025 and 2030, driven by rising demand in advanced filtration, gas separation, and flexible electronics applications. The sympolymerization approach, which involves the co-polymerization of dianhydrides and diamines to tailor membrane properties, is gaining recognition for enabling high thermal stability and chemical resistance, critical for next-generation membrane systems.
Growth is expected to be propelled by the increasing deployment of polyimide membranes in hydrogen purification, carbon capture, and organic solvent nanofiltration. Leading manufacturers such as DuPont and Evonik Industries have ongoing R&D and commercialization efforts centered on high-performance polyimide membranes, signaling market confidence. These companies are optimizing sympolymerization processes to enhance selectivity, permeability, and mechanical robustness, aligning with the requirements of the energy and semiconductor industries.
The global transition towards clean energy is a major catalyst, with polyimide membranes increasingly adopted in fuel cell systems and hydrogen production facilities. For instance, Sekisui Chemical is expanding its membrane portfolio to address hydrogen value chain demands, leveraging its expertise in high-performance polymers. Similarly, Toray Industries is deploying sympolymerization-derived membranes for both gas separation and water treatment, targeting improved efficiency and cost-effectiveness.
Another important growth driver is the electronics sector, where flexible displays and advanced integrated circuits require ultra-thin, high-purity polyimide films. Companies like Kuraray Co., Ltd. and Sumitomo Chemical are scaling up production of customizable polyimide membranes to meet surging demand from OLED and microelectronics manufacturers.
Despite these positive trends, the industry faces challenges such as volatile raw material prices, complex synthesis routes, and stringent regulatory frameworks related to chemical manufacturing. Innovations in green chemistry and process intensification are expected to mitigate some of these concerns, with industry consortia and standards bodies collaborating to streamline regulatory compliance and promote safer production practices.
Forecasts for 2025–2030 suggest a compound annual growth rate (CAGR) in the high single digits for sympolymerization-based polyimide membranes, with Asia-Pacific poised to lead global expansion. Strategic investments in capacity, technology partnerships, and vertical integration are likely to define the competitive landscape, as established players and new entrants alike target innovations in both membrane performance and manufacturing sustainability.
Regulatory Environment & Standards: Compliance and Impacts
As polyimide membrane sympolymerization technologies advance, the regulatory environment in 2025 is increasingly shaped by both global and regional standards that address environmental impact, material safety, and manufacturing consistency. Regulatory scrutiny is particularly pronounced due to the widespread application of polyimide membranes in sensitive sectors such as electronics, energy storage, and medical devices. Governments and industry bodies are tightening requirements for chemical synthesis routes, solvent usage, and end-product emissions, impacting how manufacturers approach sympolymerization processes.
In the European Union, the European Chemicals Agency (ECHA) oversees REACH compliance, which mandates thorough registration and evaluation of chemicals used in polyimide manufacture. For sympolymerization, this translates to stricter monitoring of monomer purity, byproduct minimization, and process waste management. Recent updates in 2024/2025 are pushing manufacturers toward solvent recovery and closed-loop systems to mitigate environmental impact, a trend mirrored by Asian regulatory authorities.
In the United States, the Environmental Protection Agency (EPA) continues to refine its oversight of hazardous air pollutants and waste streams arising from aromatic diamines and dianhydrides used in polyimide sympolymerization. The agency’s National Emission Standards for Hazardous Air Pollutants (NESHAP) have been updated to include lower permissible limits for specific solvent and monomer emissions, directly impacting plant operations and process design.
Japan, home to several leading polyimide membrane producers, maintains rigorous industrial standards through the Ministry of Economy, Trade and Industry (METI), which requires manufacturers to demonstrate both product safety and environmental stewardship. Japanese producers such as DuPont (operating Kapton™ polyimide), Toray Industries, Inc., and UBE Corporation are actively aligning with both domestic and international standards, often exceeding baseline requirements to maintain market access and brand reputation.
Industry-wide, compliance with International Organization for Standardization (ISO) standards—particularly ISO 9001 (quality management) and ISO 14001 (environmental management)—remains a prerequisite for global supply chain integration. Additionally, new efforts in 2025 are underway to standardize testing for membrane performance and chemical resistance, driven by manufacturers and industry consortia.
Looking ahead, compliance costs and product qualification cycles are expected to rise, but these regulations are also catalyzing innovation in green chemistry and process efficiency. Companies investing in advanced sympolymerization technologies that reduce solvent use, improve yield, and offer cleaner waste profiles are likely to gain competitive advantages. The regulatory trend is clear: sustainability and compliance will be integral to the continued growth of the polyimide membrane sector worldwide.
Future Outlook: Emerging Use Cases and Disruptive Possibilities
Polyimide membrane sympolymerization technologies are poised for significant advances in 2025 and the near future, enabling disruptive new applications and performance gains across multiple sectors. Sympolymerization, which involves the copolymerization of different monomers to tune membrane properties, is increasingly central to the development of next-generation polyimide membranes. This approach enables precise control over pore structure, chemical resistance, and mechanical strength, which are critical for advanced separations, electronics, energy storage, and filtration technologies.
In the semiconductor and electronics industries, polyimide membranes produced via sympolymerization are set to play a crucial role in flexible printed circuits, organic photovoltaics, and advanced display technologies. Leading materials manufacturers such as DuPont and Toray Industries are actively developing new polyimide grades that combine high thermal resistance with ultra-thin, defect-free profiles essential for miniaturized and flexible devices. These innovations are expected to support the scaling of next-generation chip packaging and wearable electronics through 2025 and beyond.
Another rapidly emerging application area is advanced gas separation and filtration. Sympolymerized polyimide membranes are being optimized for selective permeability, enabling highly efficient separation of gases such as CO2, H2, and N2. Companies like UBE Corporation are investing in new membrane formulations and scalable production methods to address growing demand from energy, environmental, and industrial sectors, particularly in carbon capture and hydrogen purification systems. The ability to tailor membrane performance through sympolymerization could make polyimide membranes a preferred choice for these critical applications within the next few years.
In lithium-ion battery manufacturing, sympolymerized polyimide membranes offer high thermal stability and robust chemical resistance, making them increasingly attractive as battery separators. Companies such as ENF Technology and Sumitomo Chemical are reported to be scaling up research and pilot production for these separators, aiming to support the accelerating global shift to electric vehicles and renewable energy storage.
Looking ahead, the outlook for polyimide membrane sympolymerization technologies is one of rapid innovation and expanding adoption. Continued advances in monomer chemistry, process engineering, and hybrid material integration are expected to unlock new use cases in areas such as water desalination, medical devices, and membrane-based chemical synthesis. As leading players intensify their R&D efforts and production capabilities, polyimide sympolymerization is set to become a cornerstone of advanced membrane technologies, driving disruptive possibilities across several high-growth industries through 2025 and beyond.
Conclusion & Strategic Recommendations for Stakeholders
The polyimide membrane sympolymerization sector is poised for significant advancement through 2025 and the following years, driven by mounting demand for high-performance separation materials in gas purification, water treatment, and electronics. Stakeholders across the value chain—membrane fabricators, chemical suppliers, end-users, and strategic investors—must navigate a landscape marked by rapid innovation, shifting regulatory frameworks, and intensifying competition from both established and emerging players.
Key industry leaders such as DuPont, UBE Corporation, and Toray Industries continue to invest in R&D to refine sympolymerization processes, focusing on scalability, reproducibility, and cost efficiency. Recent advancements emphasize copolymerization techniques that enable tunable pore size distributions and improved chemical resistance, directly addressing the needs of hydrogen purification and carbon capture applications. The industry’s shift toward greener, less toxic solvent systems and energy-efficient synthesis aligns with global sustainability goals and regulatory drivers, particularly in the EU, North America, and East Asia.
For membrane producers, strategic partnerships with downstream users—such as hydrogen producers, semiconductor manufacturers, and water treatment firms—are recommended to secure early market access and co-develop application-specific materials. Suppliers of polyimide monomers and precursors should prioritize backward integration to ensure material availability and price stability, given the expected volatility in feedstock markets. Collaboration with equipment manufacturers and process automation firms will be crucial to scaling up sympolymerization technologies from lab to industrial scale, reducing unit costs and enhancing quality assurance.
Strategic investors should closely monitor regulatory signals regarding PFAS, VOC emissions, and other environmental concerns, as compliance requirements are likely to influence technology adoption and capital allocation. Supporting startups and academic-industry consortia engaged in next-generation membrane sympolymerization—such as those exploring bio-based monomers or hybrid inorganic-organic structures—could offer early-mover advantages as new performance benchmarks are set.
In conclusion, the next few years will be critical for stakeholders to establish leadership positions in the polyimide membrane sympolymerization domain. Adopting a proactive stance on sustainable manufacturing, value chain integration, and cross-sectoral collaboration will be essential to capitalize on emerging market opportunities and to mitigate risks associated with technological and regulatory disruption. Engaging with global leaders such as DuPont, UBE Corporation, and Toray Industries—either as partners or benchmarks—will remain a prudent strategic move as the industry evolves.
Sources & References
- DuPont
- Kuraray Co., Ltd.
- UBE Corporation
- American Chemistry Council
- Daikin Industries
- Evonik Industries
- Sekisui Chemical
- Sumitomo Chemical
- European Chemicals Agency
- UBE Corporation