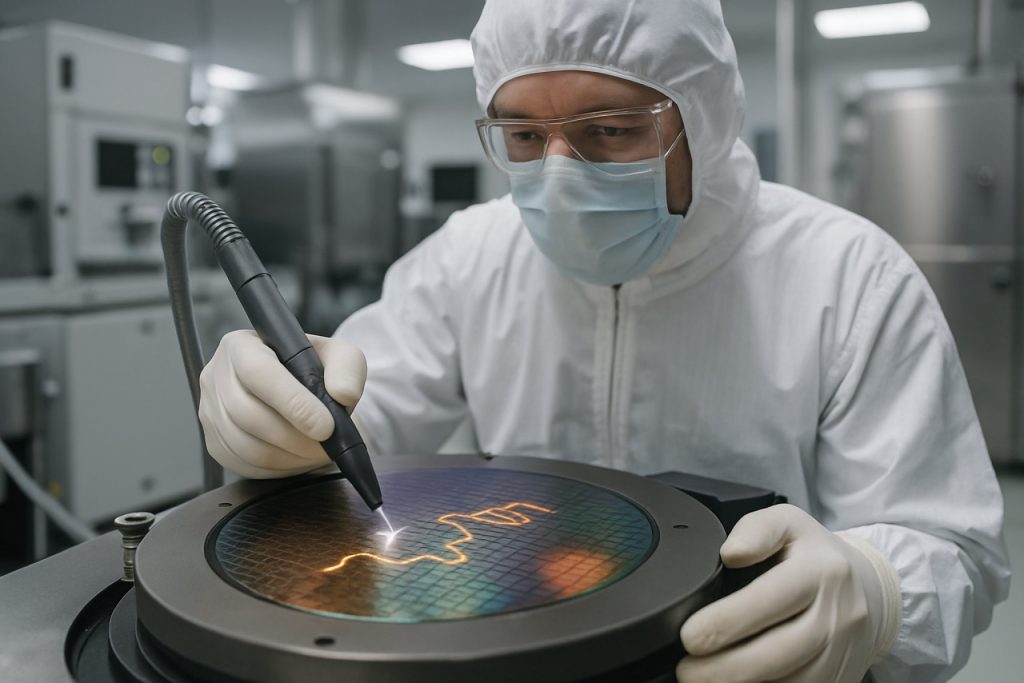
Table of Contents
- Executive Summary: The State of Polysilicon Etching in 2025
- Market Size and Forecast: 2025–2029 Growth Projections
- Key Drivers: Semiconductor Demand and Advanced Node Trends
- Emerging Etching Technologies: Plasma, Wet, and Hybrid Innovations
- Competitive Landscape: Leading Companies and Strategic Moves
- Sustainability and Environmental Impact of Etching Processes
- Challenges: Precision, Yield, and Cost Pressures
- Regional Analysis: Asia-Pacific, North America, Europe Overview
- Case Studies: Recent Deployments by Industry Leaders (e.g., Applied Materials, Lam Research, Tokyo Electron)
- Future Outlook: Roadmap for Polysilicon Etching to 2030 and Beyond
- Sources & References
Executive Summary: The State of Polysilicon Etching in 2025
In 2025, polysilicon layer etching technologies remain a cornerstone of semiconductor device fabrication, underpinning critical steps in transistor gate formation and advanced memory structures. As device scaling continues below the 5 nm node, the demand for highly selective, anisotropic, and damage-minimized etching processes has never been higher. The industry standard continues to be plasma-based dry etching, particularly variants of reactive ion etching (RIE) and high-density plasma (HDP) etching, favored for their precision and scalability. Leading equipment manufacturers such as Lam Research, Applied Materials, and Tokyo Electron have advanced process control, endpoint detection, and chamber designs to meet the increasingly stringent requirements of logic and memory fabs worldwide.
Technological advancements over the past year have focused on improving etch selectivity between polysilicon and underlying or adjacent materials, such as silicon dioxide and silicon nitride. Innovations in gas chemistries, pulsed plasma techniques, and atomic layer etching (ALE) have been pivotal, enabling sub-nanometer control over critical dimensions and reducing line edge roughness. For example, ALE, which alternates between surface modification and removal steps, is seeing pilot-scale adoption in high-volume manufacturing for its unparalleled precision. Both Lam Research and Applied Materials have reported progress in integrating such approaches into their toolsets to support the requirements of advanced nodes.
Market data from 2024 into 2025 indicates robust investment in etch tool upgrades, particularly in leading-edge foundries and memory fabs ramping up production of DRAM, 3D NAND, and gate-all-around (GAA) transistors. Equipment suppliers are collaborating closely with major chipmakers to co-optimize etch steps with new device architectures. In parallel, environmental considerations are increasingly shaping process development, with companies like Lam Research and Tokyo Electron emphasizing reduced greenhouse gas emissions and improved abatement technologies in their latest product lines.
Looking ahead to 2026 and beyond, the polysilicon etching segment is expected to further embrace atomic-scale process controls, in situ metrology, and machine learning-driven process optimization. The convergence of these trends will support the continued evolution of semiconductor devices while addressing cost, yield, and sustainability challenges. With the ongoing commitment of leading suppliers and foundries, the state of polysilicon layer etching technology is poised for continued innovation and growth.
Market Size and Forecast: 2025–2029 Growth Projections
The market for polysilicon layer etching technologies is poised for significant growth from 2025 through 2029, closely following the expansion of both semiconductor device fabrication and advanced photovoltaic (PV) manufacturing. Polysilicon etching is a critical process step in the production of logic and memory chips, as well as in the fabrication of high-efficiency solar cells. As global demand for these end products accelerates, the market size for etching equipment, process gases, and related consumables is expected to expand accordingly.
By 2025, the transition to advanced technology nodes (such as 5nm and below) in semiconductor manufacturing is driving the need for highly precise, anisotropic etching solutions. Leading semiconductor equipment suppliers like Lam Research, Applied Materials, and Tokyo Electron continue to innovate in plasma etching systems, which account for the majority of new equipment installations for polysilicon etch applications. The integration of atomic layer etching (ALE) and high aspect ratio etch (HARC) techniques is expected to increase, improving both device performance and yield.
The solar industry similarly impacts polysilicon etching demand. The shift to passivated emitter and rear cell (PERC) and tunnel oxide passivated contact (TOPCon) solar technologies, both of which rely on precise polysilicon layer patterning, is driving investments in new etching lines. Equipment manufacturers such as SCREEN Holdings and SINGULUS TECHNOLOGIES report robust order books for wet and dry etching solutions tailored to PV applications, with expectations of continued growth through 2029 as solar cell efficiencies rise and production volumes increase.
From a regional perspective, Asia-Pacific—particularly China, South Korea, and Taiwan—remains the preeminent market for polysilicon etching technologies, driven by the concentration of leading foundries and solar cell manufacturers. Government incentives and ongoing capacity expansions in these regions are anticipated to sustain steady annual growth rates.
- By 2025, the total global market for polysilicon etching technologies (including equipment, process chemicals, and services) is projected to reach several billion USD, with compound annual growth rates (CAGR) in the mid- to high-single digits through 2029, supported by both semiconductor and PV sector demand.
- Key growth drivers include ongoing miniaturization in logic and memory manufacturing, increasing adoption of advanced solar cell architectures, and the proliferation of electric vehicles and renewable energy systems requiring high-performance chips and efficient PV modules.
- Challenges and potential constraints include supply chain volatility for specialty gases and materials, as well as the need for continued R&D investment to keep pace with device scaling and new substrate materials.
Overall, the outlook for polysilicon layer etching technologies between 2025 and 2029 is robust, with leading suppliers and manufacturers continuing to invest in advanced solutions to meet the evolving needs of the global electronics and renewable energy markets.
Key Drivers: Semiconductor Demand and Advanced Node Trends
The landscape for polysilicon layer etching technologies in 2025 is intrinsically linked to the surging demand for semiconductors and the ongoing shift toward advanced process nodes. As semiconductor manufacturers push further into sub-5nm and Gate-All-Around (GAA) transistor architectures, the complexity and precision required from etch processes—particularly for polysilicon gates—have increased dramatically. Key factors driving these advances include the proliferation of artificial intelligence (AI), 5G communications, and high-performance computing, all of which necessitate ever-smaller, more densely packed transistors.
Leading foundries and integrated device manufacturers (IDMs) are investing heavily in next-generation etch tools capable of delivering atomic-level selectivity and uniformity. For instance, Lam Research Corporation and Applied Materials, Inc. are both advancing high-aspect-ratio etch (HARC) solutions that address the stringent demands of modern logic and memory device fabrication. These tools utilize innovative plasma chemistries and advanced process controls to ensure precise pattern transfer, critical for the formation of ultra-thin gate structures and 3D architectures.
Moreover, the transition to advanced nodes and three-dimensional device structures—such as FinFETs and GAA transistors—necessitates etch technologies that can handle complex topographies and minimize damage to underlying films. As a result, atomic layer etching (ALE) is gaining traction, enabling near-monolayer control over material removal. Both Lam Research Corporation and Tokyo Electron Limited have reported ongoing development and deployment of ALE-capable platforms, targeting not just feature scaling but also defect reduction and yield improvement.
In parallel, the semiconductor industry is experiencing robust capital expenditure cycles, with leading fabs in Asia, North America, and Europe expanding capacity to meet global chip demand. This expansion is further accelerating the adoption of state-of-the-art etch technologies. Companies such as Samsung Electronics and Taiwan Semiconductor Manufacturing Company are at the forefront of deploying advanced etch solutions to realize next-generation device performance and energy efficiency.
Looking ahead to the next few years, polysilicon etching will remain a focal point as the industry approaches 2nm and beyond. The push toward new materials, tighter process integration, and extreme miniaturization will likely drive further innovation in plasma source design, process chemistries, and real-time endpoint detection. Collaboration between toolmakers, chemical suppliers, and device manufacturers will be critical to overcoming the challenges posed by these advanced nodes and delivering the performance gains demanded by the market.
Emerging Etching Technologies: Plasma, Wet, and Hybrid Innovations
The ongoing evolution of polysilicon layer etching technologies is driven by the demand for advanced semiconductor devices and photovoltaics, requiring exceptional precision and scalability. As of 2025, significant innovation is occurring across plasma, wet, and hybrid etching techniques.
Plasma-based dry etching remains the primary method for patterning polysilicon in advanced logic and memory device fabrication. Leading equipment suppliers have reported improvements in plasma etch reactors, focusing on high aspect ratio structures and atomic-level control. For example, Lam Research and Applied Materials have introduced new platforms that enhance uniformity and selectivity, enabling the fabrication of sub-10 nm features and 3D architectures. These advancements are crucial as gate-all-around (GAA) FETs and 3D NAND structures become industry standards in the coming years.
Wet etching of polysilicon, while more limited in patterning capability, continues to see use in MEMS, solar cell manufacturing, and certain legacy nodes. Suppliers such as KOKUSAI ELECTRIC and Tokyo Seimitsu have optimized chemical formulations and process equipment to minimize surface roughness and reduce defects. In photovoltaics, wet chemical etching is being refined to improve texturing and passivation for high-efficiency solar cells, with the goal of increasing throughput and reducing chemical consumption.
- Hybrid Innovations: Hybrid etching technologies that combine plasma and wet steps are gaining traction for their ability to balance precision with process efficiency. These methods allow for selective removal of damaged layers post-plasma etch, or for the gentle release of MEMS structures. Companies like Tokyo Ohka Kogyo are investing in hybrid process development to address challenges in advanced packaging and 3D integration.
- Process Control and Sustainability: As feature sizes shrink, real-time process monitoring and end-point detection are crucial. Equipment suppliers are integrating AI-driven controls and advanced sensors to ensure repeatability and yield. There is also a marked industry focus on sustainability, with efforts to reduce greenhouse gas emissions and chemical waste through chamber design improvements and recycling strategies.
Looking ahead, the polysilicon etch landscape will increasingly emphasize atomic layer etching (ALE) for ultimate precision, particularly as device geometries move below 5 nm. Collaborative R&D between material suppliers, toolmakers, and device manufacturers is expected to accelerate, shaping the roadmap for the next generation of semiconductor and photovoltaic devices.
Competitive Landscape: Leading Companies and Strategic Moves
The competitive landscape for polysilicon layer etching technologies in 2025 is characterized by intense innovation, strategic collaborations, and geographical expansion among leading equipment manufacturers and technology providers. The drive for finer semiconductor nodes and advanced 3D device architectures is accelerating demand for highly selective, precise, and damage-minimizing etching solutions. This environment is pushing established players and emerging entrants to invest aggressively in both process technology and customer partnerships.
Industry Leaders and Technological Differentiation
Prominent contenders such as Lam Research Corporation, Applied Materials, Inc., and Tokyo Electron Limited (TEL) remain at the forefront, leveraging their expansive portfolios and global service networks. Each firm is focused on advancing dry (plasma-based) etching tools, with recent product generations emphasizing atomic-level precision, ultra-high selectivity, and low-defect processing to support sub-5nm and gate-all-around (GAA) transistor fabrication. For instance, Lam Research has highlighted its selective etch technologies for complex 3D architectures, while Applied Materials continues to integrate AI-driven process control and real-time metrology for higher throughput and yield.
TEL, meanwhile, is expanding its regional footprint and local support structures in Asia, reinforcing its supply chain resiliency and proximity to leading foundries. The company has also invested in next-generation etch platforms capable of handling advanced materials stacks, including complex polysilicon and silicon-germanium layers, essential for logic and memory devices.
Strategic Partnerships and Ecosystem Collaboration
In response to increasing process complexity, leading tool vendors are deepening collaborations with device makers and materials suppliers. Co-development agreements and joint technology centers—particularly in Taiwan, South Korea, and the United States—are accelerating time-to-market for new etching chemistries and hardware modules. Lam Research and Applied Materials, Inc. have both announced new partnerships with major foundries and IDMs in 2024-2025, targeting the joint optimization of etch processes for next-generation gate structures and emerging memory devices.
Emerging players in Asia are also gaining attention by offering cost-competitive, locally adapted etch solutions, although scaling to the stringent demands of leading-edge production remains a challenge. Nevertheless, this dynamic is fostering a multi-tiered competitive environment, encouraging faster innovation cycles and more customized solutions.
Outlook
The polysilicon etch sector is expected to see sustained investment and incremental consolidation over the next few years, as both established leaders and regional challengers seek to balance process innovation with supply chain security. The competitive edge will likely hinge on the ability to deliver atomic-level control, integration with advanced metrology, and agile customer collaboration—all critical to the evolution of logic, memory, and power semiconductor devices.
Sustainability and Environmental Impact of Etching Processes
Polysilicon layer etching is a critical step in semiconductor manufacturing, particularly in the production of advanced logic and memory devices. The sustainability and environmental footprint of etching technologies are receiving heightened scrutiny in 2025 as the semiconductor industry aligns with global decarbonization and resource conservation initiatives. Traditionally, dry etching using plasma and fluorinated gases (such as SF6, CF4, and NF3) has dominated polysilicon etching due to its precision and scalability. However, these etchants are potent greenhouse gases and contribute significantly to the industry’s total emissions profile.
In response, leading equipment manufacturers and chipmakers are advancing new etching tool designs and process chemistries to reduce environmental impact. For instance, companies like Lam Research and Applied Materials are actively developing plasma etchers with lower process gas consumption and enhanced abatement systems. These upgrades aim to minimize emissions of perfluorinated compounds (PFCs) and other hazardous byproducts, aligning with the industry’s commitment to net-zero emissions within the next two decades.
Recent years have also seen a shift toward more selective chemistries and atomic layer etching (ALE) techniques, which offer potential environmental benefits. ALE, for example, can achieve high selectivity and material efficiency, reducing overall chemical usage and waste generation. Tokyo Ohka Kogyo Co., Ltd. and Entegris, Inc. are among the suppliers working on advanced chemistries and delivery systems that support such precision etching at reduced environmental cost.
Water and energy consumption remain key concerns. Polysilicon etch processes typically require ultra-pure water for chamber cleaning and cooling, and high electrical power for plasma generation. Semiconductor fabs, including those operated by Taiwan Semiconductor Manufacturing Company (TSMC) and Samsung Electronics, are investing in water recycling systems and energy-efficient tool platforms to address these challenges. Additionally, the transition to renewable energy sources at major fabs is expected to help offset the indirect carbon footprint of etching operations.
Looking ahead, regulatory pressures—particularly in the United States, Europe, and East Asia—are likely to accelerate the adoption of greener etching technologies. The next few years will see increased collaboration across the value chain to develop closed-loop chemical management, next-generation abatement, and process monitoring systems. These efforts are expected to drive measurable reductions in emissions and resource intensity for polysilicon etching, positioning the industry for long-term environmental compliance and sustainability leadership.
Challenges: Precision, Yield, and Cost Pressures
Polysilicon layer etching is a cornerstone process for advanced semiconductor manufacturing, underpinning the fabrication of transistors and memory devices. As the industry enters 2025, the challenges associated with etching these layers are intensifying due to the convergence of technical precision requirements, yield sensitivity, and persistent cost pressures. Device scaling below the 5nm node, 3D architectures, and the transition to gate-all-around (GAA) FETs all demand heightened etch selectivity, profile control, and material compatibility.
A primary challenge in 2025 is achieving atomic-level precision without sacrificing throughput. The polysilicon etch process must deliver high anisotropy and selectivity to underlying films such as silicon dioxide or silicon nitride—essential for maintaining critical dimensions (CD) and preventing substrate damage. As device geometries shrink, even sub-nanometer deviations can result in electrical performance variability or outright device failure, putting immense pressure on etch uniformity and repeatability. Equipment manufacturers like Lam Research and Applied Materials continue to innovate in plasma etch chemistries and atomic layer etching (ALE) platforms to address these demands.
Yield management remains a persistent concern. With advanced nodes, the margin for process variability is minimal and defectivity must be stringently controlled. Unintended residues, micro-masking, or surface roughness introduced during polysilicon etch can propagate yield loss across entire wafer lots. To mitigate this, leading tool makers such as Tokyo Electron (TEL) are investing in integrated metrology and end-point detection systems, enabling in-situ monitoring and adaptive process control.
Cost pressures are equally acute. The increasing complexity of etch steps—often requiring multiple passes, advanced chemistries, or synergistic dry/wet cleans—drives up both capital and operational expenditures. Furthermore, as sustainability becomes a strategic priority, reducing the consumption of specialty gases and minimizing hazardous byproducts are now integral to cost and compliance strategies. Companies like Lam Research are focusing on eco-efficient platforms that lower energy and consumables usage without compromising process performance.
Looking ahead to the next few years, ongoing collaboration between equipment suppliers and device manufacturers is expected to yield further advances in etch selectivity, process stability, and cost efficiency. The adoption of AI-driven process optimization, real-time defect detection, and advanced chamber hardware will be essential for meeting the simultaneous demands of precision, yield, and cost containment in polysilicon layer etching.
Regional Analysis: Asia-Pacific, North America, Europe Overview
The global landscape for polysilicon layer etching technologies in 2025 is characterized by strong regional specialization, driven by semiconductor manufacturing hubs and advancements in process nodes. The Asia-Pacific region, North America, and Europe each play distinct roles in shaping the innovation and deployment of these critical etching technologies.
Asia-Pacific remains the powerhouse for semiconductor manufacturing, with countries such as China, South Korea, Taiwan, and Japan at the forefront. This region hosts major foundries and memory manufacturers that demand highly advanced and selective etching equipment for polysilicon layers, particularly as device geometries shrink to 5nm and below. Companies like Tokyo Seimitsu and Hitachi High-Tech Corporation are pivotal in supplying both etching tools and process metrology. Chinese equipment makers are also rapidly developing indigenous etch technologies to support the country’s push for semiconductor self-sufficiency, with increased domestic adoption projected into 2025 and beyond. The ongoing regional investments, such as new fab construction and government support in China, South Korea, and Taiwan, are expected to accelerate the deployment of next-generation plasma and atomic layer etching (ALE) tools.
North America continues to be a leader in etching tool innovation, with companies like Lam Research and Applied Materials driving process advancements needed by U.S.-based and global foundries. These companies are investing heavily in R&D to meet the requirements for extreme selectivity, profile control, and defect reduction in advanced nodes. North America’s role is further solidified by the ongoing construction and expansion of fabs in the U.S., supported by government incentives under initiatives such as the CHIPS Act. This creates a robust environment for the development and adoption of advanced polysilicon etch solutions, including high-aspect-ratio and atomic-level precision processes.
Europe maintains a niche yet highly influential position in the polysilicon etch ecosystem. European firms, such as ASM International, are known for their expertise in atomic layer etching and related process technologies. The region also benefits from strong collaboration between equipment manufacturers and leading research institutions. While Europe’s manufacturing capacity is smaller relative to Asia-Pacific and North America, its emphasis on specialty devices and R&D ensures continued demand for tailored etching solutions. European initiatives aimed at semiconductor sovereignty are expected to drive further investments in advanced etching capabilities over the next several years.
Looking forward, all three regions are poised to benefit from escalating demand for advanced chips in AI, automotive, and consumer electronics, ensuring ongoing investment in polysilicon layer etching innovation and capacity through and beyond 2025.
Case Studies: Recent Deployments by Industry Leaders (e.g., Applied Materials, Lam Research, Tokyo Electron)
Recent years have seen significant advancements in polysilicon layer etching technologies, driven by the demand for ever-smaller and more complex semiconductor devices. Industry leaders such as Applied Materials, Lam Research, and Tokyo Electron have each introduced new solutions, processes, and systems tailored to address the stringent requirements of advanced logic and memory manufacturing nodes.
In 2024, Applied Materials announced the expansion of its Centura platform with new etch chambers specifically optimized for ultra-thin polysilicon gate etching in 3 nm and below logic devices. Their advancements focus on atomic-level precision, selective removal, and defect minimization, reflecting the industry shift toward gate-all-around (GAA) transistor architectures and high aspect ratio features. Field deployments with several leading foundries have demonstrated improved critical dimension (CD) control and reduced line edge roughness, both essential for scaling logic transistors to sub-3 nm nodes.
Lam Research has also reported key deployments of its VECTOR and Kiyo etch systems at major memory and logic fabs globally. In 2023–2025, these systems have been increasingly adopted for advanced DRAM and 3D NAND production, where precision polysilicon etching is crucial for gate stack and wordline formation. Lam’s innovations emphasize high selectivity, plasma uniformity, and chamber-to-chamber reproducibility, which are critical for maintaining yield as device structures become more vertical and intricate. Recent customer collaborations have highlighted the impact of Lam’s proprietary pulsed plasma technology in achieving superior etch profiles and lower defectivity.
Tokyo Electron continues to deploy its high-throughput polysilicon etch solutions, particularly the Tactras series, at leading foundries and IDMs. In the current market, Tokyo Electron’s focus has been on integrating advanced endpoint detection and real-time process control, which enhance both uniformity and repeatability in complex multi-patterning and GAA processes. The company has reported successful integration of its systems into high-volume manufacturing lines for sub-5 nm logic and advanced memory applications, noting measurable improvements in etch rate stability and process window flexibility.
Looking ahead to 2025 and beyond, these industry leaders are expected to further refine atomic layer etching (ALE) and other next-generation techniques, aligning with the rising adoption of 2 nm and GAA transistor technologies. Collaboration with device makers is set to intensify, focusing on co-optimization of etch chemistries, hardware, and process flows to enable the next wave of semiconductor scaling and performance improvements.
Future Outlook: Roadmap for Polysilicon Etching to 2030 and Beyond
The future of polysilicon layer etching technologies is shaped by the rapid evolution of semiconductor device architectures and the ongoing push for miniaturization and performance improvements. As of 2025, leading-edge logic and memory devices increasingly demand sub-5 nm features, placing new requirements on both selectivity and anisotropy in etching processes. Conventional dry etching, particularly reactive ion etching (RIE), remains a workhorse for polysilicon patterning, but advancements are being driven by a need for atomic-level precision and reduced process variability.
Key industry players such as Lam Research and Applied Materials are actively developing next-generation plasma etching platforms that leverage advanced process control, AI-driven endpoint detection, and novel chemistries to address these challenges. In 2024 and 2025, these companies have highlighted selective etching techniques that enable more precise removal of polysilicon while protecting underlying or adjacent layers, which is crucial for complex gate-all-around (GAA) and 3D NAND structures.
The integration of remote plasma and atomic layer etching (ALE) is becoming more prevalent, allowing for the removal of individual atomic layers and thus delivering unprecedented control for advanced nodes. For example, Lam Research has announced ALE platforms designed for critical polysilicon etch steps in sub-3 nm logic and next-generation memory. This approach not only improves edge placement accuracy but also minimizes defects, a key requirement as device pitches shrink below 20 nm.
Furthermore, sustainability concerns are driving the adoption of greener chemistries and abatement solutions for etching byproducts, with major suppliers reporting investment in eco-friendly process gases and waste management systems. As a result, equipment manufacturers are collaborating with semiconductor fabs to meet both performance and environmental targets over the next few years.
From 2025 and onwards, the roadmap for polysilicon etching will increasingly emphasize:
- Integration of AI and advanced sensors for real-time process optimization and yield enhancement.
- Expansion of ALE and highly selective plasma etching for complex 3D architectures.
- Development of environmentally sustainable etching chemistries and abatement technologies.
- Collaboration between equipment suppliers and device makers to tailor etch solutions for new device structures and materials.
These trends suggest that by 2030, polysilicon etching technologies will deliver greater precision, flexibility, and sustainability, underpinning the continued scaling of semiconductor devices. Industry leaders like Applied Materials, Lam Research, and Tokyo Electron are expected to remain at the forefront, driving innovation in both equipment and process integration to meet the evolving demands of the semiconductor marketplace.