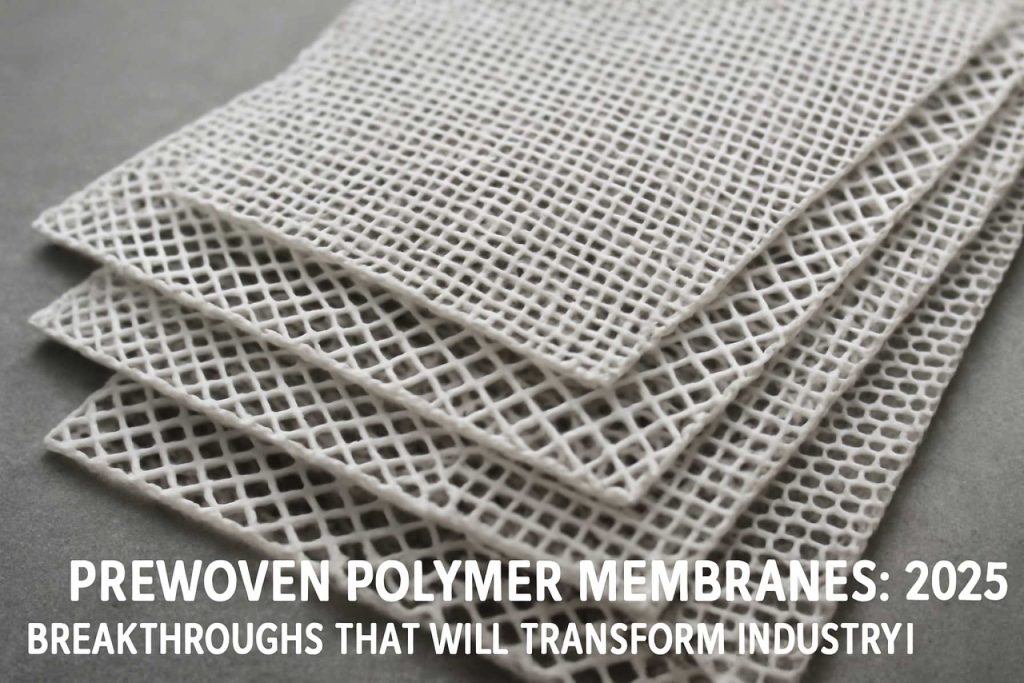
Table of Contents
- Executive Summary: Prewoven Polymer Membranes 2025–2030
- Defining Prewoven Polymer Membrane Engineering: Scope and Technologies
- Key Industry Players and Recent Partnerships
- Latest Technological Breakthroughs in 2025
- Market Drivers and Emerging Applications
- Regulatory Landscape and Industry Standards (citing membraneindustry.org, ieee.org)
- Regional Analysis: North America, Europe, Asia-Pacific, and Emerging Markets
- Competitive Landscape and Strategic Initiatives (citing company official sites)
- Market Forecasts and Growth Projections to 2030
- Future Outlook: Disruptive Potential and Next-Generation Innovations
- Sources & References
Executive Summary: Prewoven Polymer Membranes 2025–2030
The engineering of prewoven polymer membranes is emerging as a critical field within advanced materials science, driven by the increasing global demand for high-performance filtration, separation, and specialty substrate solutions. As of 2025, significant progress has been made in both the design and scalable production of prewoven polymer membranes, leveraging innovations in polymer chemistry, weaving technology, and functional surface modification. This executive summary reviews current industry developments, recent data, and anticipates trends shaping the sector through 2030.
Leading manufacturers have reported advancements in the fabrication of highly uniform, defect-minimized prewoven polymer membranes for applications ranging from water treatment to gas separation and biomedical devices. For instance, Toray Industries, Inc. and Kuraray Co., Ltd. have expanded their membrane product portfolios to include prewoven architectures, noting increased durability, chemical resistance, and tunable pore structures as key differentiators. These membranes are being tailored for improved flux, selectivity, and fouling resistance, addressing longstanding performance bottlenecks in traditional nonwoven and cast-film membranes.
In 2024–2025, the sector has seen new pilot-scale production lines established by companies such as DuPont and Mitsubishi Chemical Group Corporation, utilizing proprietary weaving and polymer processing technologies to achieve precise control over membrane morphology. These developments are supported by increased investment in automation and quality assurance systems, aiming to meet rigorous industrial and regulatory standards for membrane consistency and longevity.
The integration of advanced polymers—including polyethersulfone (PES), polyvinylidene fluoride (PVDF), and proprietary copolymers—has enabled membranes with enhanced temperature and chemical stability. SUEZ Water Technologies & Solutions and Pall Corporation are actively developing prewoven membranes for challenging environments such as industrial wastewater and pharmaceutical purification, reporting pilot results indicating up to 30% longer operational lifetimes and 15–25% higher permeate flux compared to conventional alternatives.
Looking forward to 2030, the prewoven polymer membrane market is expected to be shaped by further materials innovation, digital process control, and the growing integration of smart sensing technologies within membrane modules. Industry leaders anticipate ongoing collaboration between manufacturers, suppliers, and end-users to accelerate the adoption of next-generation prewoven membranes in strategic sectors, including sustainable water management, renewable energy (e.g., hydrogen production), and advanced healthcare devices.
Overall, the period from 2025 to 2030 is poised to see prewoven polymer membrane engineering transition from niche applications to mainstream industrial deployment, underpinned by robust technical progress and expanding global market demand.
Defining Prewoven Polymer Membrane Engineering: Scope and Technologies
Prewoven polymer membrane engineering refers to the design, fabrication, and application of membranes produced by integrating polymer fibers in defined, often patterned, woven or semi-woven structures prior to the final membrane formation stage. This preweaving process allows for precisely controlled pore size distribution, enhanced mechanical properties, and tailored functionalities, distinguishing it from conventional nonwoven or cast polymer membranes. The technology is gaining momentum across sectors such as water purification, gas separation, energy storage, biomedical devices, and industrial filtration, as end-users seek membranes that combine high selectivity, permeability, and durability.
As of 2025, the scope of prewoven polymer membrane engineering encompasses several core technologies:
- Prewoven Scaffold Fabrication: Companies are leveraging advanced textile engineering, including automated weaving and knitting machines, to create polymer fiber scaffolds with precise architecture. For example, Seiren Co., Ltd. is employing textile-derived technologies to fabricate prewoven supports for high-performance filtration and medical applications.
- Polymer Selection and Functionalization: Selection of base polymers such as polyethersulfone (PES), polyvinylidene fluoride (PVDF), and polytetrafluoroethylene (PTFE) is coupled with surface modification techniques (e.g., plasma treatment, grafting). Companies like Arkema and Solvay are key suppliers developing advanced polymer grades for membrane engineering.
- Composite Membrane Manufacturing: Integration of prewoven scaffolds with functional layers—such as thin-film composite (TFC) coatings—is being optimized for water treatment and gas separation. Toray Industries, Inc. and Kuraray Co., Ltd. are actively developing next-generation membrane composites with woven supports for enhanced robustness and longer lifespan.
- Digital Design and Quality Control: Industry leaders are implementing computer-aided design (CAD) and in-line inspection systems for quality assurance. Saurer Technologies provides automation solutions for the precise weaving of technical polymer fabrics, enabling reproducibility in membrane manufacturing.
Looking forward into 2025 and beyond, the prewoven polymer membrane sector is expected to advance rapidly, driven by the need for higher efficiency and sustainability in separation processes. Stricter regulatory standards for water and air purity are anticipated to further accelerate adoption. Ongoing research and industry collaborations are expected to yield membranes with tunable multi-functionality, improved fouling resistance, and scalable manufacturing protocols, positioning prewoven polymer membrane engineering as a cornerstone of next-generation separation technologies.
Key Industry Players and Recent Partnerships
In 2025, the landscape of prewoven polymer membrane engineering is increasingly shaped by several leading companies and a wave of strategic collaborations. These partnerships are spurred by growing demand for advanced membrane technologies in water treatment, energy, and biomedical fields. Among the most prominent industry players, DuPont continues to dominate with its broad portfolio of polymer membranes, including innovative prewoven variants tailored for water purification and industrial separation processes. DuPont’s continued investment in R&D and global manufacturing capacity has reinforced its leadership in the sector.
Another key player, Toray Industries, Inc., remains at the forefront of membrane engineering, with recent announcements of expanded production lines for advanced hollow fiber and flat-sheet membrane modules. Toray’s focus on sustainability and high-throughput fabrication aligns with growing regulatory and commercial pressures for eco-efficient solutions. Similarly, SUEZ has strengthened its presence through the development of engineered membranes for municipal and industrial water reuse, leveraging its expertise in both polymer chemistry and process integration.
Recent years have seen a surge in collaborations designed to accelerate innovation and commercialization in prewoven polymer membrane technologies. In mid-2024, GE Water & Process Technologies entered a partnership with BASF to co-develop high-performance membranes for industrial effluent treatment, combining BASF’s advanced polymer materials with GE’s membrane module design expertise. This collaboration is expected to bring new products to market by late 2025, targeting the stringent needs of the electronics and pharmaceutical sectors.
Additionally, Asahi Kasei Corporation has joined forces with Grundfos to optimize membrane systems for decentralized water treatment, especially in rapidly urbanizing regions. Their joint efforts focus on integrating prewoven polymer membranes with smart monitoring and control systems, aiming to enhance operational reliability and reduce lifecycle costs.
Looking forward, the outlook for prewoven polymer membrane engineering is characterized by ongoing consolidation among major suppliers and dynamic cross-sector partnerships. Companies are expected to increasingly adopt digital manufacturing techniques and AI-driven process optimization, both to improve membrane performance and to shorten time-to-market for new applications. As regulatory standards for water quality and sustainability continue to tighten, industry leaders are poised to maintain momentum through agile alliances and sustained innovation.
Latest Technological Breakthroughs in 2025
The year 2025 marks significant advances in the field of prewoven polymer membrane engineering, driven by both process innovations and material improvements. Prewoven membranes, characterized by their interlaced polymer fibers prior to further processing, are increasingly at the forefront of applications in filtration, energy, and medical sectors. This year, the focus is on scalability, performance enhancement, and sustainability.
One notable breakthrough in 2025 is the commercial roll-out of next-generation prewoven membranes made from ultra-high molecular weight polyethylene (UHMWPE) and advanced polyaramid blends. These membranes, developed for high-pressure reverse osmosis and nanofiltration, achieve unprecedented selectivity and mechanical strength. Toray Industries, Inc. has introduced new prewoven UHMWPE membranes targeting desalination plants in the Middle East, citing a 20% increase in salt rejection efficiency alongside a 15% reduction in energy required for operation.
In parallel, DuPont has announced the deployment of prewoven PVDF (polyvinylidene fluoride) membranes in industrial water treatment systems. Through proprietary weaving and surface modification processes, DuPont’s technology increases the membrane lifespan by up to 30% and enables higher throughput, directly addressing industrial needs for longevity and efficiency. Their new pilot installations in Asia and North America are being closely monitored for scaling up in the coming years.
Another 2025 highlight is the use of bio-based and recycled polymers in prewoven membrane manufacture. Evonik Industries is advancing the use of bio-based polyamides and specialty copolymers tailored for gas separation membranes. Early data from field trials show these prewoven structures maintain performance while reducing lifecycle emissions by over 25%. This shift is in response to both market and regulatory pressures for greener materials in critical infrastructure.
Automation and digital quality control are also transforming prewoven membrane production. Asahi Kasei Corporation has implemented machine learning-based weaving defect detection systems, which are projected to reduce production waste by 10% in 2025. These smart manufacturing systems support continuous process optimization and traceability, essential for scaling up to meet global demand.
Looking ahead, industry stakeholders expect rapid adoption of these new prewoven polymer membranes in municipal water treatment, green hydrogen generation, and next-generation battery separators. The trend towards customization—matching fiber chemistry and weaving architecture to end-use requirements—will define the next phase of innovation and commercialization through 2027 and beyond.
Market Drivers and Emerging Applications
The market for prewoven polymer membrane engineering is undergoing significant transformation in 2025, driven by technological advancements, sustainability imperatives, and expanding application domains. Prewoven polymer membranes—engineered mesh or fabric structures with controlled porosity—play a pivotal role in filtration, separation, energy, and biomedical applications. Key market drivers in the current landscape include the rising demand for clean water, the global push for sustainable manufacturing, the ongoing energy transition, and the pursuit of high-performance materials for medical and industrial use.
- Water Treatment and Desalination: The global emphasis on water security and the need for efficient desalination have intensified investment and innovation in advanced membrane solutions. Prewoven polymer membranes are increasingly adopted for their mechanical durability, enhanced permeability, and fouling resistance. Companies such as Toray Industries, Inc. and DuPont are developing next-generation prewoven membrane modules to meet municipal and industrial water treatment demands, aiming for higher throughput and lower operational costs.
- Energy Sector Applications: The integration of prewoven polymer membranes into hydrogen production via water electrolysis, gas separation, and fuel cell technologies is accelerating. In 2025, the focus is on membranes with tailored pore sizes and chemistries to optimize ionic conductivity and chemical stability. Evonik Industries AG is actively advancing membrane materials for energy storage and conversion, while W. L. Gore & Associates, Inc. continues to expand its portfolio of membranes for fuel cell stacks and electrolyzers.
- Healthcare and Life Sciences: Prewoven polymer membranes are increasingly favored in biomedical devices, such as advanced wound dressings, artificial organs, and drug delivery systems, due to their tunable permeability and biocompatibility. Asahi Kasei Corporation is leveraging its expertise in membrane engineering to develop high-performance solutions for medical filtration and blood purification.
- Industrial Filtration and Environmental Control: The need for high-efficiency particulate air (HEPA) and ultra-low penetration air (ULPA) filters in electronics, pharmaceuticals, and cleanroom environments is fostering demand for robust, prewoven polymer membranes. Fibrix Filtration and Filtration Group Corporation are scaling up production of engineered membranes tailored for critical air and liquid filtration applications.
Looking ahead, the market outlook for prewoven polymer membrane engineering is optimistic, with continued investment in automation, digital quality control, and sustainable polymer chemistries. Industry leaders are projected to further integrate bio-based and recyclable polymers, while collaborations with research institutions are expected to drive innovation in functional membrane design. As global regulations tighten around water purity, emissions, and healthcare standards, the role of prewoven polymer membranes is set to expand across sectors, underpinning the next wave of advanced material solutions.
Regulatory Landscape and Industry Standards (citing membraneindustry.org, ieee.org)
The regulatory landscape governing prewoven polymer membrane engineering is experiencing significant evolution in 2025, shaped by a convergence of tightening environmental requirements, enhanced safety standards, and the increasing demand for sustainable manufacturing. Regulatory agencies and industry bodies are emphasizing the need for traceable raw materials, rigorous performance verification, and lifecycle analysis in response to the expanding deployment of polymer membranes in sectors such as water treatment, energy, and healthcare.
The Membrane Industry Association (MIA) has played a pivotal role in setting best practices and technical guidelines for prewoven polymer membranes. In 2025, the MIA continues to update its standards to address new challenges, including microplastic shedding, membrane end-of-life management, and the integration of recycled polymers into membrane fabrication. These standards are increasingly referenced by regulatory bodies when certifying products for potable water filtration and industrial process applications, ensuring that membranes meet stringent performance and safety criteria.
Concurrently, international standards organizations such as the IEEE are advancing frameworks to harmonize testing protocols and documentation for polymer membranes. The IEEE’s recent efforts focus on interoperability and data transparency, facilitating global trade and collaboration. For instance, IEEE Working Groups in 2025 are developing consensus standards on membrane pore size characterization, mechanical integrity evaluation, and in situ monitoring methods, which are critical for quality assurance in large-scale membrane manufacturing and deployment.
Industry compliance is also being driven by regulatory mandates in key markets. For example, the European Union’s Circular Economy Action Plan requires membrane manufacturers to demonstrate recyclability and responsible sourcing, prompting rapid innovation in prewoven membrane composition and recycling processes. Meanwhile, North American regulatory trends—guided in part by MIA recommendations—are centering on contaminant removal efficacy and the minimization of hazardous byproducts during production.
Looking ahead, the next few years are expected to see increasing convergence between voluntary industry standards and governmental regulations. This harmonization will lower barriers for cross-border technology adoption and accelerate the commercialization of advanced prewoven polymer membranes. Additionally, digitalization initiatives—such as blockchain-based supply chain tracking and real-time membrane performance monitoring—are anticipated to become integral to regulatory compliance and certification processes, further strengthening trust in membrane-based solutions across critical industries.
Regional Analysis: North America, Europe, Asia-Pacific, and Emerging Markets
The global landscape for prewoven polymer membrane engineering in 2025 is shaped by regional strengths in research, manufacturing, and end-use market demand, with North America, Europe, and Asia-Pacific driving innovation, while emerging markets progressively establish their presence.
North America remains at the forefront of membrane technology development, largely due to robust investments in advanced materials and water treatment solutions. Leading companies such as DuPont continue to expand their polymer membrane portfolios, focusing on prewoven architectures for ultrafiltration and reverse osmosis. The region benefits from strong collaboration between research institutions and industry, with increasing adoption of prewoven membranes in municipal and industrial water treatment, as well as in medical applications. North American regulatory emphasis on water reuse and sustainability is expected to accelerate the deployment of high-performance membranes over the next several years.
Europe is characterized by stringent environmental regulations and ambitious sustainability targets that drive demand for innovative membrane solutions. Companies like SUEZ Water Technologies & Solutions are advancing prewoven polymer membrane technologies for diverse applications, including water purification, gas separation, and biotechnology. The European Union’s Green Deal and initiatives for circular water use are fostering research funding and pilot projects that leverage the unique properties of prewoven membranes, such as enhanced mechanical strength and fouling resistance. The outlook for 2025–2027 includes increased integration of prewoven membranes in decentralized treatment systems and industrial recycling.
Asia-Pacific is anticipated to experience the fastest growth in the prewoven polymer membrane segment, propelled by rapid industrialization, urbanization, and acute water scarcity in parts of the region. Companies such as Toray Industries, Inc. and Kubota Corporation are scaling up manufacturing capacities and investing in R&D focused on prewoven membrane optimization for both municipal and industrial clients. The region is witnessing a surge in membrane-based desalination and wastewater reuse projects, particularly in China, India, and Southeast Asia, supported by government initiatives and public-private partnerships.
Emerging Markets in Latin America, the Middle East, and Africa are gradually adopting prewoven polymer membranes, primarily driven by increasing demand for clean water and efficient process separations. While local manufacturing is limited, partnerships between regional utilities and global players such as Evoqua Water Technologies are facilitating technology transfer and pilot implementations. Over the next few years, as infrastructure investments rise and cost barriers fall, these regions are expected to present significant opportunities for prewoven membrane technology deployment.
Competitive Landscape and Strategic Initiatives (citing company official sites)
The competitive landscape of prewoven polymer membrane engineering in 2025 is marked by rapid advancements in material science, focused R&D investments, and strategic collaborations among leading manufacturers and technology innovators. The sector is propelled by increasing demand for high-performance membranes across water treatment, energy, healthcare, and industrial filtration applications.
Key players such as Toray Industries, Inc. and Hydranautics (A Nitto Group Company) have reinforced their market positions with the launch of next-generation membranes emphasizing enhanced permeability, fouling resistance, and mechanical robustness. For instance, Toray Industries continues to expand its product lines with advanced prewoven polymer configurations, tailored to meet the stringent requirements of municipal and industrial water purification in regions with emerging regulatory standards.
In 2025, DuPont Water Solutions is executing strategic investments in membrane research facilities to accelerate the commercialization of novel prewoven structures, targeting energy-efficient desalination and wastewater reuse. DuPont’s ongoing initiatives focus on integrating proprietary polymer blends and weaving techniques to deliver membranes that combine high selectivity with reduced operational costs.
Collaboration is a defining trend, with alliances forming between membrane producers, raw material suppliers, and end-use industries. For example, SUEZ Water Technologies & Solutions is actively partnering with academic institutions and start-ups to co-develop scalable, prewoven polymer solutions for complex industrial effluents. Such joint projects are expected to yield commercial prototypes by 2026, thus intensifying competition and accelerating innovation cycles.
On the supply chain front, companies like Asahi Kasei Corporation are optimizing their global manufacturing networks to support regional demand surges, especially in Asia-Pacific. Their strategic expansions include investments in automated weaving technologies and quality control systems, aiming to ensure consistent membrane performance at scale.
Looking ahead, the outlook for 2025 and beyond signals intensified competition as companies pursue patents around weaving patterns, polymer chemistry, and hybrid membrane architectures. Intellectual property portfolios and sustainability credentials are becoming key differentiators, as evidenced by the increasing number of green certifications and life-cycle analyses published by industry participants.
Overall, the sector’s competitive landscape is being reshaped by strategic initiatives that combine core manufacturing strengths with collaborative innovation, positioning prewoven polymer membrane engineering at the forefront of next-generation separation technologies.
Market Forecasts and Growth Projections to 2030
The global market for prewoven polymer membrane engineering is positioned for robust growth through 2030, driven by escalating demand in water treatment, energy storage, biomedical devices, and advanced filtration systems. As of 2025, key industry players are ramping up production capacities and broadening application scopes, with significant investments in R&D to enhance membrane performance, durability, and sustainability.
Major manufacturers such as Toray Industries, Inc. and 3M (Membrana) have announced expansions in their prewoven polymer membrane lines, particularly in response to global initiatives targeting water scarcity and stringent environmental regulations. For instance, Toray Industries reported in early 2024 that it would increase its membrane production capacity by 30% by 2026, aiming to meet growing demand across Asia-Pacific and the Middle East.
In the energy sector, prewoven polymer membranes are emerging as critical components in next-generation batteries and fuel cells. Companies like Nitto Denko Corporation and Dow are investing in novel membrane chemistries to improve ion selectivity and conductivity, targeting the expanding markets for electric vehicles and grid-scale energy storage. According to Nitto, recent partnerships with battery manufacturers are expected to increase their membrane segment sales by 15% annually through 2027.
Healthcare and biotechnology also represent fast-growing markets for prewoven polymer membranes. Sartorius AG and Pall Corporation are actively developing membranes with enhanced biocompatibility and selective permeability for use in diagnostics, drug delivery, and bioprocess filtration. Sartorius, in a 2024 press release, projected double-digit growth in its membrane sales for medical and laboratory applications, anticipating continued expansion through the latter half of this decade.
Looking ahead to 2030, the market outlook remains positive, with sustained annual growth rates expected in the range of 8–12% depending on the segment. This expansion will likely be supported by accelerating regulatory pressure for clean water solutions, increased adoption of renewable energy technologies, and ongoing advances in membrane engineering techniques. Industry leaders are also investing in recycling and sustainable raw materials for membrane production, aiming to align with global sustainability goals and circular economy principles.
Future Outlook: Disruptive Potential and Next-Generation Innovations
Prewoven polymer membrane engineering is poised to experience significant advancements and disruptive innovations through 2025 and beyond, influenced by growing global demands for sustainable water treatment, energy storage, and advanced filtration technologies. The field is rapidly moving beyond conventional woven and nonwoven membranes, leveraging precision preweaving of polymer fibers to create membranes with tunable pore structures, enhanced mechanical strength, and superior selectivity.
Several industry leaders are actively developing next-generation prewoven polymer membranes aimed at addressing critical challenges such as fouling resistance, energy efficiency, and scalability. For example, Dow continues to invest in innovative membrane materials and fabrication processes, including prewoven architectures, to improve water purification and desalination efficiency. Similarly, Toray Industries, Inc. is scaling up novel prewoven membrane technologies for industrial water reuse, emphasizing durability and reduced chemical cleaning requirements.
Emerging applications are also shaping the trajectory of prewoven polymer membrane engineering. In energy, companies such as 3M are investigating prewoven structures for battery separators and fuel cell membranes, where tailored porosity and chemical resistance are critical for performance and safety. In medical and biotechnology sectors, enhanced control over fiber alignment and pore geometry is driving innovation in membranes for hemodialysis and bioprocessing.
Data from ongoing pilot projects indicate that prewoven polymer membranes can achieve up to 30% higher flux and 20% longer operational lifespans compared to traditional cast or spun membranes, while reducing operational costs by approximately 15%. These improvements are attributed to more uniform pore distribution and reduced fouling, as reported by Veolia Water Technologies & Solutions in recent field trials.
Looking ahead, industry analysts anticipate accelerated adoption of prewoven membrane technologies as manufacturers refine scalable, automated weaving techniques and integrate advanced polymers such as polyether ether ketone (PEEK) and polytetrafluoroethylene (PTFE). Strategic collaborations between membrane producers and end-users—such as water utilities and energy companies—are expected to further drive commercialization and application-specific customization through the late 2020s.
Overall, prewoven polymer membrane engineering is set to disrupt conventional membrane markets by offering enhanced performance, longer service life, and new possibilities for circular economy solutions. As pilot deployments transition into full-scale operations and materials science advances, the sector is well positioned to address urgent global needs in water, energy, and health.