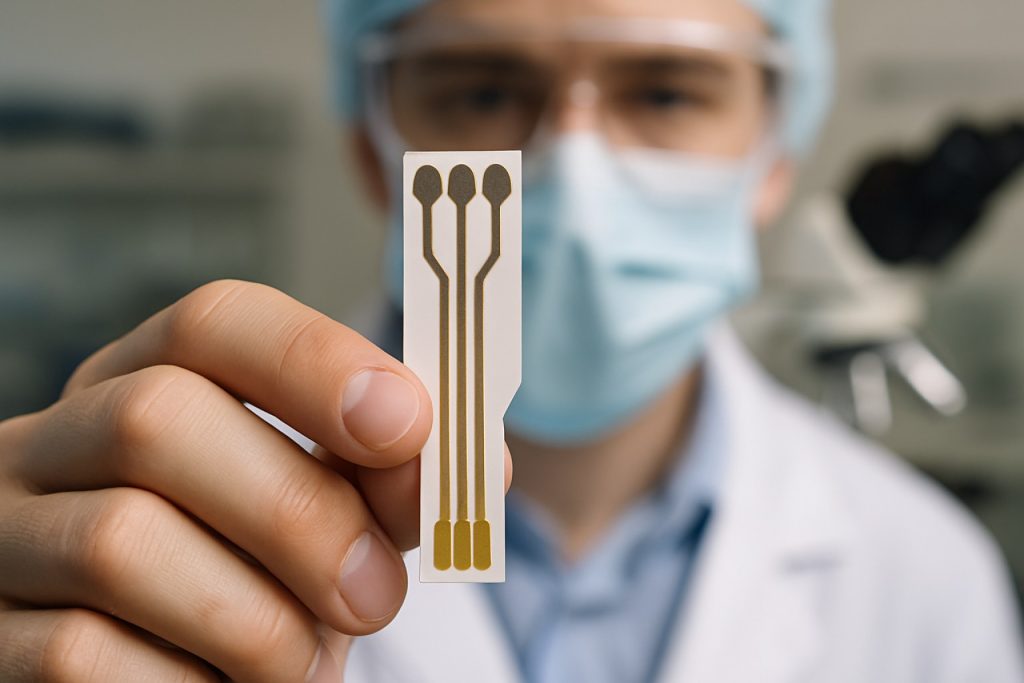
Table of Contents
- Executive Summary: Silkscreen Microelectrodes in 2025
- Current Market Size and 2025–2029 Growth Projections
- Key Players and Industry Collaborations (e.g., dropSens.com, metrohm.com, ieee.org)
- Latest Technological Advancements in Silkscreen Microelectrode Fabrication
- Emerging Applications: Healthcare, Environmental, and Wearable Tech
- Manufacturing Challenges and Solutions for Large-Scale Production
- Regulatory Trends and Industry Standards
- Competitive Landscape and Innovation Mapping
- Investment, M&A, and Funding Trends
- Future Outlook: Disruptive Opportunities and Strategic Recommendations
- Sources & References
Executive Summary: Silkscreen Microelectrodes in 2025
In 2025, the fabrication of silkscreen microelectrodes remains a cornerstone technology for the development of low-cost, scalable, and flexible electrochemical sensors. Silkscreen printing, also known as screen printing, enables the mass production of microelectrodes with customizable geometries and material compositions, supporting rapid innovation in sectors such as medical diagnostics, environmental monitoring, and wearable electronics. The technology’s appeal lies in its simplicity, compatibility with diverse substrates (including polymers, ceramics, and flexible films), and capacity for high-throughput manufacturing.
Recent advances are characterized by the integration of nanomaterials—such as graphene, carbon nanotubes, and metal nanoparticles—into silkscreen inks to enhance microelectrode sensitivity and selectivity. Leading material suppliers and printing equipment manufacturers, including DuPont and Fujifilm, have expanded their portfolios of conductive inks and pastes to meet demand for high-performance sensor components. These advancements support the fabrication of finer, more stable electrode features, pushing the boundaries of detection limits and extending device lifespans.
Adoption of automated screen printing platforms is accelerating, driven by the need for reproducibility and the capacity to scale up production. Companies such as ASYS Group and Meyer Burger Technology AG offer industrial-grade screen printing systems that enable precise control over electrode layer thickness and uniformity—key parameters for reliable sensor function. These systems are now equipped with real-time quality control and process monitoring, minimizing defects and supporting regulatory compliance in healthcare and environmental applications.
Looking ahead, the market outlook for silkscreen microelectrode fabrication is robust. The technology is expected to maintain its relevance amid growing demand for point-of-care diagnostics and portable monitoring devices. Further miniaturization and integration with microfluidics are anticipated, with industry collaborations focusing on hybrid manufacturing approaches that combine silkscreen printing with additive manufacturing or photolithography for next-generation biosensors. Additionally, sustainability is emerging as a priority, with manufacturers exploring biodegradable substrates and eco-friendly inks—a trend supported by innovation leaders like Sun Chemical.
In summary, silkscreen microelectrode fabrication in 2025 is marked by material innovation, process automation, and expanding application domains. The sector is poised for continued growth, driven by end-user demands for cost-effective, reliable, and scalable sensor solutions, and underpinned by technological advances from leading stakeholders in materials and equipment manufacturing.
Current Market Size and 2025–2029 Growth Projections
The global market for silkscreen microelectrode fabrication is positioned for measured growth between 2025 and 2029, fueled by the integration of printed electronics into biosensor, environmental monitoring, and point-of-care diagnostic applications. The technique, known for its scalability and cost-effectiveness, leverages established printing technologies to produce reproducible and customizable microelectrode arrays. Leading industry participants—such as DuPont, Sun Chemical, and Agfa—continue to innovate in functional inks and printable pastes tailored for high-precision electrode patterns, driving adoption in both research and industrial settings.
As of 2025, the silkscreen microelectrode sector represents a substantial segment within the broader printed electronics market, which is estimated to exceed $50 billion globally. While precise segmentation for silkscreened microelectrodes is rarely reported independently, industry feedback and product launches from companies such as Zimmer & Peacock and Microsens indicate robust demand from medical diagnostics, food safety, and environmental sensing. These applications exploit the rapid prototyping and customization capabilities of silkscreen fabrication, which are difficult to achieve with traditional photolithographic processes.
From 2025 through 2029, the market is projected to grow at a compound annual growth rate (CAGR) in the high single digits, supported by continuous investments in materials development and the miniaturization of analytical devices. Emerging trends include the use of flexible substrates and the expansion of functional ink portfolios—such as carbon, gold, platinum, and silver/silver chloride systems—which enhance the performance and versatility of microelectrodes. Manufacturers like Gwent Group and DropSens (a subsidiary of Metrohm) are expanding their production capacities and portfolios, reflecting confidence in market expansion.
Looking ahead, the sector is expected to benefit from regulatory encouragement for decentralized diagnostics and environmental monitoring, as well as the proliferation of wearable and disposable sensor technologies. Collaborations between ink formulators, printing equipment manufacturers, and end users are anticipated to accelerate product innovation and application diversity. As a result, silkscreen microelectrode fabrication is poised to remain a key enabling technology in the evolving landscape of printed electronics from 2025 through the end of the decade.
Key Players and Industry Collaborations (e.g., dropSens.com, metrohm.com, ieee.org)
Silkscreen microelectrode fabrication has emerged as a pivotal technology in the evolution of electrochemical sensors, biosensors, and point-of-care diagnostic devices. As the market matures through 2025 and beyond, leading manufacturers and industry consortia are shaping standards and driving innovation through strategic collaborations.
Among the key players, Metrohm AG and its subsidiary DropSens S.L. continue to be at the forefront of screen-printed electrode (SPE) technology. DropSens, acquired by Metrohm in 2016, remains a primary supplier, offering a diverse catalog of carbon, gold, and platinum silkscreen microelectrodes. Their products are widely referenced in scientific literature and research projects, reflecting their strong presence in both academic and industrial R&D.
The sector also sees active participation from companies such as Zimmer & Peacock, which specializes in custom sensor design and contract manufacturing, and Pine Research Instrumentation, which provides ready-to-use silkscreen electrodes for educational and research applications. These firms are increasingly focusing on flexible substrates, miniaturization, and integration with microfluidic platforms to meet the growing demand for portable and wearable sensing devices.
Industry-wide collaboration is reinforced by the involvement of organizations like the Institute of Electrical and Electronics Engineers (IEEE), which supports the development of technical standards and organizes conferences such as the IEEE Sensors series, where advances in microfabrication—including silkscreen methods—are regularly showcased. Such gatherings foster cross-sector partnerships and the sharing of best practices, accelerating the transition from laboratory-scale fabrication to scalable industrial production.
Several leading firms are now entering joint ventures with academic institutions to push the boundaries of electrode material development, functionalization methods, and process automation. For instance, Metrohm and DropSens frequently participate in EU-funded consortia aimed at biosensor innovation, while Zimmer & Peacock collaborates with universities on rapid prototyping and customization for emerging applications.
Looking forward, the industry is expected to further emphasize sustainable production, cost efficiency, and rapid prototyping. Automation and digitalization of silkscreen processes, as well as the integration of Internet of Things (IoT) connectivity into electrode platforms, are likely to define the competitive landscape through 2025 and into the following years. These advancements are poised to lower barriers to entry and expand the range of applications for silkscreen microelectrodes across healthcare, environmental monitoring, and food safety sectors.
Latest Technological Advancements in Silkscreen Microelectrode Fabrication
Silkscreen microelectrode fabrication, a cornerstone technique for producing low-cost, scalable, and customizable electrochemical sensors, is witnessing rapid technological advancement in 2025. The method, which involves depositing conductive inks onto various substrates via screen-printing, continues to evolve in response to growing demand for point-of-care diagnostics, environmental monitoring, and wearable biosensors.
A significant trend in 2025 is the adoption of advanced conductive inks, particularly those based on nanomaterials such as graphene, carbon nanotubes, and metallic nanoparticles. These inks offer superior electrical performance and mechanical flexibility, enabling the production of highly sensitive electrodes with improved longevity. Leading manufacturers, such as Metrohm DropSens and Zimmer & Peacock, have introduced new lines of screen-printed electrodes (SPEs) incorporating these advanced materials. These innovations allow for enhanced signal-to-noise ratios and better compatibility with miniaturized, portable analyzers.
Automation and precision in silkscreen processes are also notable in 2025, with companies investing in next-generation, digitally controlled screen printers. These systems provide tighter control over ink deposition, feature size, and electrode geometry, leading to higher reproducibility and batch-to-batch consistency. For instance, SENSIT has expanded its automated production capabilities to address the increasing volume of custom microelectrode orders from the healthcare and environmental sectors.
Another advancement is the diversification of substrate materials. While traditional ceramic and plastic substrates remain popular, there is a growing adoption of flexible and even biodegradable substrates to meet sustainability goals and the requirements of wearable or disposable sensors. This shift is evidenced by collaborations between electrode manufacturers and specialty substrate providers, aiming to produce eco-friendly, high-performance sensor platforms.
Integration of silkscreen-fabricated microelectrodes with emerging electronics is also accelerating. Companies are developing hybrid platforms, embedding silkscreen electrodes directly onto flexible PCBs or microfluidic devices. This enables seamless integration with wireless modules for real-time data transmission, a feature increasingly valued in remote diagnostics and continuous monitoring applications.
Looking forward, the sector is expected to see further improvements in ink formulations (such as enzyme- or antibody-functionalized inks for direct biosensing) and the scaling up of production lines to meet the growing demand for affordable, high-performance microelectrodes. The ongoing partnerships between electrode manufacturers, ink producers, and device integrators will likely set the pace for commercialization and innovation in the next several years.
Emerging Applications: Healthcare, Environmental, and Wearable Tech
Silkscreen microelectrode fabrication is increasingly shaping the landscape of sensor technology, especially as demand grows for flexible, miniaturized, and cost-efficient devices across healthcare, environmental monitoring, and wearable technology sectors. In 2025, the convergence of advances in screen-printing, conductive inks, and substrate materials is driving new application frontiers for these microelectrodes.
In healthcare, silkscreen-printed microelectrodes are being rapidly adopted for point-of-care diagnostics and continuous health monitoring. Their compatibility with flexible substrates enables the creation of disposable biosensors for glucose, lactate, and other clinically relevant analytes. Companies like Merck KGaA and DuPont are supplying advanced conductive inks and pastes tailored for medical-grade screen-printing, supporting the mass production of wearable and implantable devices. The integration of silkscreen microelectrodes with microfluidic platforms is further enhancing diagnostic sensitivity and multiplexing capabilities, a trend expected to continue through 2027 as personalized medicine and telehealth expand.
Environmental sensing is another high-growth area. Silkscreen microelectrodes are being deployed in compact, low-power devices for real-time detection of heavy metals, nitrates, and pesticides in water and soil. Manufacturers such as Metrohm AG and DropSens are commercializing screen-printed electrode solutions for field-deployable sensors, aiding in rapid, on-site environmental assessments. The ongoing development of novel functional inks, including those based on graphene or nanostructured metals, is expected to improve electrode selectivity and durability under harsh conditions.
Wearable technology is experiencing a surge in innovation, with silkscreen microelectrodes at the core of next-generation e-textiles and epidermal electronics. Flexible, printed electrodes are enabling continuous monitoring of biopotentials (ECG, EMG) and sweat biomarkers, powering a new class of unobtrusive health and fitness devices. DuPont and Sioen Industries are among the companies developing printable conductive materials and smart textile integration processes. Industry analysts predict that by 2027, the seamless incorporation of silkscreen microelectrodes into garments and patches will be pivotal for the mainstream adoption of personalized, real-time health monitoring solutions.
Looking forward, the sector is poised for continued growth as manufacturers refine fabrication processes to improve scalability, reduce costs, and enable mass customization. The synergy between material innovation and digital manufacturing is set to unlock broader adoption of silkscreen microelectrode-based devices, especially in decentralized diagnostics and environmental sustainability initiatives.
Manufacturing Challenges and Solutions for Large-Scale Production
Silkscreen printing has established itself as a pivotal technique for the mass manufacturing of microelectrodes, particularly for applications in biosensors, medical diagnostics, and environmental monitoring. As we enter 2025, the demand for high-throughput, cost-effective, and reproducible microelectrode fabrication continues to rise, driving both innovation and operational challenges in scaling up silkscreen-based processes.
A primary challenge in large-scale silkscreen microelectrode production is maintaining uniformity and reliability across vast batches. Variations in screen mesh size, ink viscosity, and substrate quality can lead to inconsistencies in electrode geometry and electrical performance. To address these issues, industry leaders have invested in advanced automated screen-printing systems capable of real-time process monitoring and closed-loop control. For example, companies such as Heraeus and DuPont have developed proprietary conductive inks and pastes specifically engineered for screen printing, offering improved rheological properties and enhanced adhesion to diverse substrates, which are critical for uniform layer deposition and high device yields.
Another notable challenge is the integration of microelectrodes onto flexible and unconventional substrates (such as PET or polyimide films) for next-generation wearable and point-of-care devices. This requires low-temperature curing inks and advanced substrate handling. DuPont and Sun Chemical have recently introduced silver and carbon-based inks that cure at lower temperatures, reducing thermal stress and broadening the range of compatible substrates.
Contamination control remains a critical concern in large-scale manufacturing. Particulate or ionic contaminants can compromise electrode performance, especially in biosensing applications. The adoption of cleanroom-compatible silkscreen lines and rigorous quality control protocols, such as in-line optical inspection and automated electrical testing, has become industry standard, as seen in the practices of Heraeus.
Looking ahead through 2025 and into the next few years, the outlook for large-scale silkscreen microelectrode fabrication is optimistic. The introduction of digital screen-printing technologies and hybrid additive manufacturing approaches promises further improvements in resolution, yield, and customization. Additionally, the growing availability of eco-friendly inks and recyclable substrates is expected to align the sector with global sustainability goals. As manufacturers continue to collaborate with material scientists and equipment suppliers, ongoing innovation is likely to further reduce costs and expand application domains for silkscreened microelectrodes.
Regulatory Trends and Industry Standards
Silkscreen microelectrode fabrication, a cornerstone technology in the development of electrochemical sensors and biosensors, is experiencing notable shifts in regulatory and standardization landscapes as of 2025. The increasing adoption of printed electronics across healthcare, environmental monitoring, and food safety sectors is prompting greater scrutiny of both the manufacturing processes and the end-use applications of silkscreen-printed microelectrodes.
One of the primary regulatory focuses is on materials safety and traceability. Regulatory agencies in the United States and European Union have intensified their oversight of inks, substrates, and additives used in silkscreen-printed electrodes, especially as these devices transition from laboratory to commercial medical diagnostics. For instance, the European Chemicals Agency (ECHA) continues to update its European Chemicals Agency guidelines regarding the use of silver, carbon, and nanomaterials in printed electronics, necessitating tighter supplier documentation and end-product safety validation.
At the same time, the International Electrotechnical Commission (IEC) and International Organization for Standardization (ISO) have expanded their collaborative efforts to develop standards specific to printed and flexible electronics, including microelectrode arrays. In 2024, the IEC published updates to IEC 62899, which addresses printed electronics general requirements. These evolving standards increasingly reference manufacturing reproducibility, electrical performance, and biocompatibility—factors critical for the regulatory approval of microelectrodes in medical and environmental settings (International Electrotechnical Commission).
From an industry perspective, leading manufacturers are proactively aligning with these regulatory expectations. Companies like SCREEN Holdings Co., Ltd., a global leader in silkscreen printing equipment, and Dropsens, a significant supplier of printed electrodes, have updated quality management systems to ensure compliance with ISO 13485 for medical devices and ISO 9001 for general quality assurance. Furthermore, traceability practices—including batch-level tracking and digital documentation—are becoming industry norms, driven by both regulatory and customer demands.
Looking forward, the next few years are expected to bring more harmonized international standards for printed microelectrodes, particularly as cross-border supply chains and collaborative research projects expand. The industry anticipates further guidance from regulatory bodies on environmental sustainability, recyclability of printed sensors, and lifecycle management. As the regulatory environment evolves, manufacturers and developers in the silkscreen microelectrode sector are likely to prioritize flexible production processes and robust compliance infrastructures to maintain market access and foster innovation.
Competitive Landscape and Innovation Mapping
The competitive landscape for silkscreen microelectrode fabrication is rapidly evolving in 2025, driven by surging interest in low-cost, scalable sensor platforms for biomedical, environmental, and industrial applications. The screen-printing (silkscreen) approach remains a cornerstone for mass-producing disposable electrochemical sensors due to its compatibility with a variety of substrates and its potential for automation. Leading manufacturers such as Metrohm, DropSens, and Pine Research Instrumentation continue to expand their portfolios, offering standardized and custom microelectrode arrays tailored for both academic research and commercial deployment.
Recent years have seen intensified R&D investment aimed at enhancing electrode sensitivity, reproducibility, and miniaturization. Metrohm and DropSens have launched novel screen-printed electrodes incorporating nanomaterials such as graphene, carbon nanotubes, and metal nanoparticles, further expanding the range of detectable analytes and improving signal-to-noise ratios. Furthermore, advances in multilayer printing and hybrid ink formulations are enabling more complex electrode architectures, facilitating the integration of on-chip reference and counter electrodes, as well as microfluidic features for sample handling.
Collaborations between industry and research institutions are also fostering innovation. Notably, partnerships with academic labs have accelerated the translation of lab-scale prototypes to commercial products. Companies such as Pine Research Instrumentation have started offering application-specific silkscreen microelectrode kits for rapid prototyping, supporting the trend towards customizable and modular sensor platforms.
Regional expansion is a key theme in 2025, with European and Asian manufacturers increasing production capacity to meet global demand, particularly for point-of-care diagnostics and environmental monitoring. The integration of silkscreen microelectrodes into emerging wearable and implantable devices is gaining momentum, attracting interest from companies in the broader electronics and medical device sectors. This trend is expected to intensify as regulatory pathways for electrochemical biosensors become more clearly defined.
Looking ahead, competitive differentiation will hinge on intellectual property around advanced ink formulations, electrode geometries, and scalable production methods. Automation and digitalization of the silkscreen process are likely to further reduce costs and improve batch-to-batch consistency. With continued cross-sector collaboration and robust end-user demand, the silkscreen microelectrode market is poised for sustained innovation and geographic diversification through 2025 and beyond.
Investment, M&A, and Funding Trends
In 2025, investment and M&A activity within the silkscreen microelectrode fabrication sector is showing signs of acceleration, driven by the growing demand for low-cost, scalable sensor technologies in healthcare, environmental monitoring, and industrial automation. The proliferation of wearable and point-of-care diagnostic devices—many of which rely on flexible, printed microelectrodes—continues to attract both strategic and venture capital funding. Companies specializing in printing technologies and advanced materials, such as Dycotec Materials and Cabot Corporation, have reported increased interest from investors seeking to capitalize on the expanding applications of printed electronics.
Recent years have seen a notable uptick in funding rounds for startups and scale-ups offering silkscreen-compatible conductive inks, substrates, and automated printing solutions. Several players have secured multi-million-dollar investments aimed at boosting production capabilities and expanding R&D in microelectrode design. For example, DuPont, a longstanding leader in conductive inks, has recently announced new capital allocations to accelerate product development and strategic collaborations targeting next-generation biosensors and microelectronic components.
Mergers and acquisitions are also becoming increasingly prevalent, with established electronics manufacturers seeking to vertically integrate silkscreen microelectrode fabrication into their portfolios. In early 2025, industry observers noted a trend of acquisitions targeting niche firms with expertise in high-throughput silkscreen processes, particularly those offering turnkey solutions for medical device and environmental sensor markets. Companies such as SCREEN Holdings Co., Ltd. and Agfa-Gevaert Group have been identified as active participants in expanding their capabilities through strategic partnerships and targeted M&A, leveraging their global reach and technical infrastructure.
Looking forward, the sector is poised for continued growth as governments and private investors prioritize healthcare innovation, sustainability, and the development of smart infrastructure. The ability of silkscreen microelectrode fabrication to enable mass production of reliable, miniaturized, and cost-effective sensors positions it as a critical technology in the ongoing evolution of the Internet of Things (IoT) and digital healthcare. As a result, further rounds of funding, increased cross-sector partnerships, and consolidation among key players are anticipated in the coming years, particularly as new regulatory standards and end-user requirements drive demand for advanced, scalable solutions.
Future Outlook: Disruptive Opportunities and Strategic Recommendations
The silkscreen microelectrode fabrication sector is poised for significant transformation in 2025 and the ensuing years, driven by rapid advancements in materials science, automation, and integration with digital manufacturing techniques. Silkscreen printing, established as a scalable and cost-effective method for producing microelectrodes, is increasingly being adopted beyond traditional academic and R&D environments, with commercial and industrial players intensifying their focus on high-throughput, reproducible production.
One of the most disruptive opportunities lies in the convergence of silkscreen printing with emerging nanomaterial inks, including graphene, carbon nanotubes, and metal nanoparticle composites. Companies such as Merck KGaA and DuPont are actively developing advanced conductive pastes and inks specifically tailored for printed electronics and biosensor applications. This trend is expected to accelerate the transition from traditional metal-based electrodes to novel hybrid materials, offering enhanced sensitivity, flexibility, and miniaturization. As a result, the next generation of microelectrodes will likely enable more sophisticated point-of-care diagnostics, wearable sensors, and environmental monitoring devices with improved performance and reduced costs.
Automation and digitalization of the silkscreen process are also anticipated to reshape the competitive landscape. Leading manufacturers such as MicroChemicals GmbH and SCREEN Holdings Co., Ltd. are investing in automated printing platforms capable of micron-scale resolution and real-time quality monitoring. Integration with machine learning and computer vision is expected to further reduce defects and boost yields, making customized electrode patterns more accessible for specialized applications in medical diagnostics, food safety, and industrial analytics.
Strategically, stakeholders are encouraged to forge collaborations across the value chain—from specialty chemical companies to medical device OEMs—to accelerate time-to-market for innovative sensor products. Regulatory compliance, especially for medical and environmental devices, will remain a critical consideration, with proactive engagement with industry bodies such as the Semiconductor Industry Association recommended to align with evolving standards and ensure global interoperability.
- Invest in R&D for multifunctional, biocompatible printing inks to address emerging application niches.
- Adopt automated, digitally controlled silkscreen production lines to improve scale, consistency, and traceability.
- Pursue cross-sector partnerships to leverage expertise in materials, microfabrication, and regulatory affairs.
- Monitor advances in machine learning for process optimization and predictive maintenance of fabrication equipment.
In summary, silkscreen microelectrode fabrication is on the cusp of disruptive change in 2025, propelled by materials innovation, smart automation, and collaborative business models. Companies agile enough to embrace these trends stand to capture significant value as demand for high-performance, cost-effective microelectrodes rapidly expands across diverse sectors.