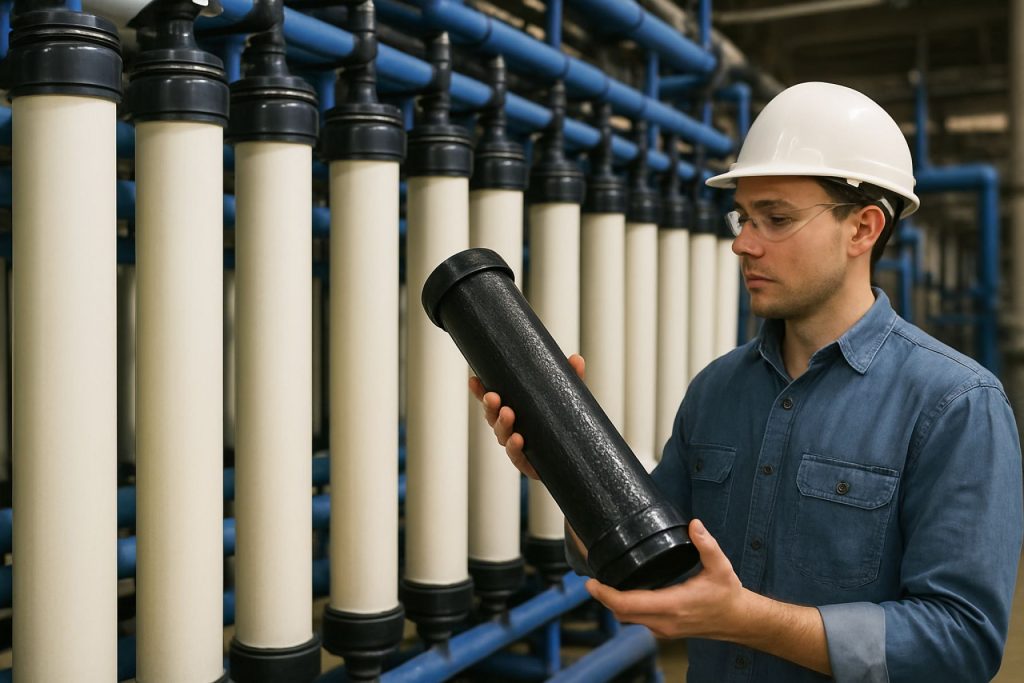
Slurry Ultrafiltration Membrane Technology in 2025: Transforming Industrial Filtration with Next-Gen Performance. Explore Market Growth, Innovations, and Strategic Shifts Shaping the Next Five Years.
- Executive Summary: 2025 Market Snapshot & Key Takeaways
- Technology Overview: Principles and Advances in Slurry Ultrafiltration Membranes
- Market Size & Growth Forecast (2025–2029): CAGR, Revenue, and Volume Projections
- Key Industry Players & Strategic Initiatives (e.g., pentair.com, ge.com, pall.com)
- Emerging Applications: Mining, Food Processing, Pharmaceuticals, and More
- Innovation Pipeline: Materials Science, Membrane Design, and Automation
- Regulatory Landscape & Industry Standards (e.g., water.org, epa.gov)
- Regional Analysis: North America, Europe, Asia-Pacific, and Rest of World
- Competitive Landscape: Mergers, Partnerships, and New Entrants
- Future Outlook: Disruptive Trends, Sustainability, and Investment Opportunities
- Sources & References
Executive Summary: 2025 Market Snapshot & Key Takeaways
The global slurry ultrafiltration membrane technology market in 2025 is characterized by robust growth, driven by increasing demand for efficient solid-liquid separation in industries such as pharmaceuticals, food and beverage, chemicals, and wastewater treatment. Ultrafiltration (UF) membranes are now a critical component in handling high-solid-content slurries, offering advantages in process efficiency, water reuse, and compliance with tightening environmental regulations.
Key industry players, including SUEZ, Pall Corporation, Kubota Corporation, and Toray Industries, are actively expanding their ultrafiltration product portfolios and investing in R&D to address the challenges of fouling, membrane durability, and energy consumption. For example, SUEZ has continued to innovate in ceramic and polymeric UF modules, targeting high-turbidity and abrasive slurry streams, while Pall Corporation is focusing on modular, scalable systems for industrial and bioprocessing applications.
In 2025, the adoption of advanced membrane materials—such as polyethersulfone (PES), polyvinylidene fluoride (PVDF), and ceramic composites—has accelerated, enabling higher flux rates and longer operational lifespans. Companies like Toray Industries and Kubota Corporation are at the forefront of these developments, with Kubota’s submerged membrane systems gaining traction in municipal and industrial wastewater treatment plants globally.
Market data from industry sources indicate that the Asia-Pacific region, led by China and India, is the fastest-growing market for slurry ultrafiltration, propelled by rapid industrialization and stricter discharge standards. Europe and North America continue to invest in upgrading legacy systems, with a focus on circular economy initiatives and water reuse. The food and beverage sector, particularly dairy and starch processing, is a notable adopter, seeking to maximize product recovery and minimize waste.
Looking ahead, the slurry ultrafiltration membrane market is expected to maintain a strong growth trajectory through the late 2020s. Key trends include the integration of digital monitoring for predictive maintenance, the development of hybrid systems combining UF with other separation technologies, and increased collaboration between membrane manufacturers and end-users to tailor solutions for specific slurry characteristics. As regulatory pressures mount and sustainability goals intensify, ultrafiltration technology is poised to play an even more central role in industrial process optimization and environmental stewardship.
Technology Overview: Principles and Advances in Slurry Ultrafiltration Membranes
Slurry ultrafiltration membrane technology is a rapidly evolving field, driven by the need for efficient separation processes in industries such as pharmaceuticals, food and beverage, chemicals, and wastewater treatment. The core principle involves the use of semi-permeable membranes to separate suspended solids, colloids, and macromolecules from liquid slurries under pressure. Ultrafiltration membranes typically have pore sizes ranging from 1 to 100 nanometers, allowing for the selective retention of particles while permitting water and low-molecular-weight solutes to pass through.
Recent years have seen significant advances in membrane materials and module designs. Polymeric membranes, such as those made from polyethersulfone (PES), polyvinylidene fluoride (PVDF), and polysulfone (PS), remain widely used due to their chemical resistance and mechanical strength. However, the industry is witnessing a growing interest in ceramic membranes, which offer superior thermal and chemical stability, longer operational lifespans, and higher resistance to fouling. Companies like SUEZ and Veolia are actively developing and supplying both polymeric and ceramic ultrafiltration modules for slurry applications, targeting sectors with challenging feed streams.
A key technological trend in 2025 is the integration of advanced surface modification techniques to enhance membrane performance. Hydrophilic coatings, nanoparticle incorporation, and zwitterionic surface treatments are being employed to reduce fouling and improve flux recovery. For example, Pall Corporation and Kubota Corporation are investing in research and commercialization of membranes with anti-fouling properties, aiming to extend cleaning intervals and reduce operational costs.
Process intensification is another area of focus, with the adoption of high-shear modules and dynamic filtration systems that minimize cake layer formation on membrane surfaces. Companies such as GEA Group are offering crossflow ultrafiltration systems specifically designed for high-solids slurries, enabling higher throughput and more consistent product quality.
Digitalization and automation are also shaping the future of slurry ultrafiltration. Real-time monitoring of transmembrane pressure, flux, and fouling indicators, combined with predictive maintenance algorithms, are being implemented to optimize system performance and reduce downtime. Leading suppliers like Sartorius are integrating smart sensors and data analytics into their membrane systems, supporting the move toward Industry 4.0 in process industries.
Looking ahead, the outlook for slurry ultrafiltration membrane technology is robust. Continued innovation in materials, module design, and process control is expected to drive wider adoption across industries facing increasingly stringent environmental and product quality regulations. The next few years will likely see further commercialization of hybrid systems, combining ultrafiltration with other separation technologies to address complex slurry streams and maximize resource recovery.
Market Size & Growth Forecast (2025–2029): CAGR, Revenue, and Volume Projections
The global market for slurry ultrafiltration membrane technology is poised for robust growth between 2025 and 2029, driven by increasing demand for efficient solid-liquid separation in industries such as pharmaceuticals, food and beverage, mining, and wastewater treatment. The market is expected to register a compound annual growth rate (CAGR) in the range of 7% to 9% during this period, reflecting both technological advancements and expanding application areas.
In 2025, the market size is projected to surpass USD 1.2 billion in revenue, with volume shipments of ultrafiltration modules and systems estimated at over 15,000 units globally. This growth is underpinned by stricter environmental regulations, particularly in Asia-Pacific and Europe, which are compelling industries to adopt advanced membrane-based separation solutions. The Asia-Pacific region, led by China and India, is anticipated to account for the largest share of new installations, owing to rapid industrialization and government initiatives targeting water reuse and zero liquid discharge.
Key industry players such as SUEZ, Pentair, Toray Industries, and Koch Separation Solutions are investing in R&D to enhance membrane durability, flux rates, and fouling resistance. These companies are also expanding their manufacturing capacities and global distribution networks to meet rising demand. For instance, Toray Industries has announced plans to scale up its ultrafiltration membrane production in response to growing orders from the industrial and municipal sectors.
The food and beverage industry is emerging as a significant growth driver, with ultrafiltration membranes increasingly used for clarification, protein concentration, and byproduct recovery. Similarly, the mining sector is adopting slurry ultrafiltration to improve tailings management and water recycling, further boosting market volumes. In wastewater treatment, the push for circular economy practices is accelerating the replacement of conventional filtration with membrane-based systems.
Looking ahead to 2029, the global slurry ultrafiltration membrane market is forecast to reach approximately USD 1.7 billion in annual revenue, with annual shipments exceeding 22,000 units. The market outlook remains positive, supported by ongoing innovation, regulatory momentum, and the growing need for sustainable industrial processes. Strategic partnerships and mergers among leading manufacturers are expected to further consolidate the market and drive technological progress.
Key Industry Players & Strategic Initiatives (e.g., pentair.com, ge.com, pall.com)
The slurry ultrafiltration membrane technology sector is witnessing significant activity in 2025, with established filtration and water technology companies driving innovation, capacity expansion, and strategic partnerships. The market is characterized by a focus on higher flux membranes, improved fouling resistance, and integration with digital monitoring systems to optimize performance in challenging slurry environments across industries such as mining, food & beverage, pharmaceuticals, and wastewater treatment.
- Pentair remains a prominent player, leveraging its expertise in advanced membrane modules and systems for industrial slurry applications. The company continues to invest in R&D for robust polymeric and ceramic ultrafiltration membranes, targeting enhanced durability and lower operational costs. Pentair’s global footprint and service network enable it to support large-scale deployments, particularly in Asia and North America, where demand for efficient slurry separation is rising (Pentair).
- Pall Corporation, a subsidiary of Danaher, is recognized for its high-performance ultrafiltration modules tailored for abrasive and high-solids slurries. In 2025, Pall is expanding its product line with membranes designed for higher chemical resistance and longer service life, addressing the needs of the mining and chemical processing sectors. The company is also advancing digital integration, offering remote monitoring and predictive maintenance solutions to maximize uptime (Pall Corporation).
- GE Vernova (formerly GE Water & Process Technologies) continues to play a strategic role, particularly in large-scale industrial and municipal projects. GE’s focus is on modular ultrafiltration systems that can be rapidly deployed and scaled, with ongoing collaborations to integrate AI-driven process optimization. Their membrane technologies are increasingly adopted in zero-liquid discharge (ZLD) and resource recovery applications, reflecting the sector’s sustainability priorities (GE Vernova).
- Veolia Water Technologies is another key global supplier, offering a broad portfolio of ultrafiltration solutions for slurry treatment. Veolia’s recent initiatives include pilot projects for circular economy applications, such as recovery of valuable metals from industrial slurries and closed-loop water reuse in manufacturing (Veolia Water Technologies).
- Koch Separation Solutions is advancing ceramic and polymeric ultrafiltration membranes, focusing on high-turbidity and high-temperature slurry streams. The company’s strategic partnerships with OEMs and end-users are aimed at co-developing customized solutions for complex process streams in food, biotech, and mining (Koch Separation Solutions).
Looking ahead, the slurry ultrafiltration membrane technology market is expected to see further consolidation, with leading players investing in automation, digitalization, and sustainability-driven innovations. Strategic alliances, pilot projects, and regional manufacturing expansions are likely to shape the competitive landscape through 2025 and beyond.
Emerging Applications: Mining, Food Processing, Pharmaceuticals, and More
Slurry ultrafiltration membrane technology is rapidly gaining traction across several industries, with 2025 marking a pivotal year for its adoption in emerging applications such as mining, food processing, and pharmaceuticals. This technology, which utilizes semi-permeable membranes to separate fine particles and dissolved substances from liquid slurries, is being recognized for its ability to enhance process efficiency, reduce waste, and recover valuable resources.
In the mining sector, ultrafiltration membranes are increasingly deployed for the treatment and recycling of process water, as well as for the recovery of metals from tailings and effluents. Companies like SUEZ and Veolia are at the forefront, offering advanced membrane systems designed to handle the high solids content and aggressive chemistries typical of mining slurries. These solutions are helping mining operations meet stricter environmental regulations and reduce freshwater consumption, a trend expected to intensify through 2025 and beyond as sustainability pressures mount.
In food processing, ultrafiltration is being adopted for the clarification, concentration, and fractionation of products such as dairy, juices, and plant-based beverages. Leading membrane manufacturers like Pall Corporation and GEA Group are supplying systems that enable processors to improve product quality, increase yield, and minimize by-product waste. For example, ultrafiltration is used to concentrate proteins in dairy streams and to clarify fruit juices without the need for traditional fining agents, aligning with the industry’s move toward cleaner-label products and more sustainable processing.
The pharmaceutical industry is also embracing slurry ultrafiltration for applications such as the purification of antibiotics, vaccines, and other biologics. Companies like Merck KGaA (operating as MilliporeSigma in North America) are providing membrane solutions that meet stringent regulatory requirements for purity and process validation. The technology’s ability to efficiently separate biomolecules from complex fermentation broths or cell culture media is driving its adoption in both large-scale manufacturing and emerging biopharmaceutical production platforms.
Looking ahead, the outlook for slurry ultrafiltration membrane technology is robust. Ongoing advancements in membrane materials—such as ceramic and composite membranes—are expanding the range of treatable slurries and improving resistance to fouling and chemical attack. As industries continue to prioritize resource efficiency, regulatory compliance, and product quality, the deployment of ultrafiltration systems is expected to accelerate, with key players like SUEZ, Veolia, Pall Corporation, GEA Group, and Merck KGaA driving innovation and market growth through 2025 and the following years.
Innovation Pipeline: Materials Science, Membrane Design, and Automation
The slurry ultrafiltration membrane technology sector is experiencing a dynamic phase of innovation, driven by advances in materials science, membrane design, and automation. As of 2025, the industry focus is on enhancing membrane selectivity, durability, and fouling resistance to meet the demands of increasingly complex industrial slurries in sectors such as mining, chemicals, and food processing.
Materials science breakthroughs are at the core of this innovation pipeline. Leading manufacturers are investing in novel polymer blends, ceramic composites, and hybrid materials to improve membrane performance. For example, SUEZ and Pall Corporation are actively developing next-generation polymeric and ceramic membranes with enhanced chemical and thermal stability, targeting applications where aggressive slurries have previously limited membrane lifespans. These materials are engineered to resist abrasion and chemical attack, extending operational cycles and reducing downtime.
Membrane design is also evolving rapidly. Companies such as Koch Separation Solutions are introducing modular ultrafiltration systems that allow for easy scaling and maintenance. Innovations include asymmetric pore structures and surface modifications that minimize fouling and enable higher flux rates, even with high-solids-content slurries. The integration of nanomaterials and surface coatings is another trend, with the aim of imparting anti-fouling and self-cleaning properties to membranes, thus reducing the frequency of chemical cleaning and prolonging service life.
Automation and digitalization are transforming slurry ultrafiltration operations. Real-time monitoring and process control systems, such as those developed by Veolia Water Technologies, are being integrated into membrane plants to optimize performance and predict maintenance needs. These systems leverage sensors, data analytics, and machine learning to adjust operating parameters dynamically, ensuring consistent product quality and energy efficiency. The adoption of Industry 4.0 principles is expected to accelerate, with remote diagnostics and predictive maintenance becoming standard features in new installations.
Looking ahead to the next few years, the innovation pipeline is expected to deliver membranes with even greater selectivity and robustness, tailored for specific slurry compositions. Collaborative R&D efforts between membrane manufacturers, end-users, and academic institutions are likely to yield breakthroughs in both materials and process integration. As regulatory pressures on water reuse and waste minimization intensify, the demand for advanced slurry ultrafiltration solutions is set to grow, positioning the sector for continued technological advancement and market expansion.
Regulatory Landscape & Industry Standards (e.g., water.org, epa.gov)
The regulatory landscape for slurry ultrafiltration membrane technology is evolving rapidly as global attention intensifies on water quality, industrial wastewater management, and resource recovery. In 2025, regulatory agencies and industry bodies are increasingly emphasizing stricter discharge limits, water reuse, and the adoption of advanced treatment technologies, including ultrafiltration (UF) membranes, to address environmental and public health concerns.
In the United States, the U.S. Environmental Protection Agency (EPA) continues to update effluent guidelines for industries generating high-strength slurries, such as food processing, pharmaceuticals, and chemical manufacturing. The EPA’s National Pollutant Discharge Elimination System (NPDES) permits are pushing facilities to adopt membrane-based solutions to meet lower total suspended solids (TSS) and chemical oxygen demand (COD) thresholds. The EPA also encourages water reuse initiatives, where ultrafiltration membranes play a critical role in producing high-quality effluent suitable for non-potable applications.
Globally, organizations like Water.org advocate for the adoption of advanced water treatment technologies in developing regions, supporting regulatory frameworks that incentivize the use of ultrafiltration for both municipal and industrial applications. The European Union’s Water Framework Directive and Urban Waste Water Treatment Directive are also driving the adoption of membrane technologies, with member states updating national standards to reflect the latest best available techniques (BAT) for slurry and wastewater treatment.
Industry standards are being shaped by technical committees and industry consortia. The International Organization for Standardization (ISO) and the ASTM International are actively developing and revising standards for membrane performance, testing protocols, and material safety. For example, ISO 14034 on environmental technology verification and ASTM D6908 for membrane filtration performance are increasingly referenced in procurement and regulatory compliance.
Major membrane manufacturers, such as SUEZ and Toray Industries, are collaborating with regulatory bodies to ensure their slurry ultrafiltration products meet or exceed evolving standards. These companies are also participating in pilot projects and demonstration plants to validate compliance with new regulations and to support the development of future standards.
Looking ahead, the regulatory trend is toward more stringent effluent limits, mandatory water reuse targets, and lifecycle assessments of membrane systems. This is expected to drive further innovation in slurry ultrafiltration membrane technology, with a focus on higher selectivity, fouling resistance, and energy efficiency. Industry stakeholders anticipate that harmonized global standards and certification schemes will emerge, facilitating wider adoption and cross-border technology transfer in the next few years.
Regional Analysis: North America, Europe, Asia-Pacific, and Rest of World
The global landscape for slurry ultrafiltration membrane technology is evolving rapidly, with distinct regional trends shaping market dynamics and adoption rates. As of 2025, North America, Europe, Asia-Pacific, and the Rest of World (RoW) regions each present unique drivers, challenges, and opportunities for this advanced separation technology.
North America remains a significant hub for innovation and deployment of slurry ultrafiltration membranes, particularly in the United States and Canada. The region’s strong focus on industrial wastewater treatment, driven by stringent environmental regulations and sustainability goals, is fostering demand for high-performance membrane systems. Leading manufacturers such as GE (through its water technologies division) and DuPont are actively developing and supplying ultrafiltration solutions tailored for complex slurry applications in sectors like food processing, mining, and oil & gas. The presence of established infrastructure and investment in R&D is expected to sustain North America’s leadership in both technology development and adoption through the next several years.
Europe is characterized by robust regulatory frameworks and a strong emphasis on circular economy principles, which are accelerating the uptake of slurry ultrafiltration membranes. Countries such as Germany, France, and the Netherlands are at the forefront, leveraging these technologies for resource recovery and water reuse in municipal and industrial settings. Companies like SUEZ and Veolia are prominent players, offering integrated membrane solutions and investing in pilot projects to demonstrate the viability of ultrafiltration for challenging slurry streams. The European Union’s Green Deal and related funding mechanisms are expected to further stimulate market growth and innovation in the region through 2025 and beyond.
Asia-Pacific is witnessing the fastest growth in slurry ultrafiltration membrane adoption, propelled by rapid industrialization, urbanization, and increasing environmental awareness. China, Japan, and South Korea are leading the charge, with significant investments in upgrading water treatment infrastructure and addressing industrial effluent challenges. Major regional suppliers such as Toray Industries and Mitsubishi Chemical Group are expanding their membrane portfolios and production capacities to meet surging demand. Government initiatives targeting water pollution control and resource efficiency are expected to drive continued expansion in the Asia-Pacific market over the next few years.
Rest of World (RoW) regions, including Latin America, the Middle East, and Africa, are gradually increasing their adoption of slurry ultrafiltration membranes, primarily in response to water scarcity and the need for efficient industrial wastewater management. While market penetration remains lower compared to other regions, international technology providers and local integrators are collaborating to introduce cost-effective solutions tailored to regional needs. As infrastructure investments and regulatory frameworks mature, these markets are anticipated to offer new growth opportunities for membrane technology suppliers through 2025 and beyond.
Competitive Landscape: Mergers, Partnerships, and New Entrants
The competitive landscape for slurry ultrafiltration membrane technology in 2025 is characterized by a dynamic mix of established players, strategic mergers, technology-driven partnerships, and the emergence of innovative new entrants. As industries such as pharmaceuticals, food and beverage, mining, and wastewater treatment increasingly demand efficient solid-liquid separation, companies are intensifying efforts to expand their portfolios and global reach.
Major membrane manufacturers, including SUEZ and Pall Corporation, continue to consolidate their positions through targeted acquisitions and collaborations. SUEZ, for example, has been actively integrating advanced ultrafiltration modules into its water and process solutions, leveraging its global footprint to serve both municipal and industrial clients. Pall Corporation, a subsidiary of Danaher, remains a leader in crossflow and tangential flow filtration systems, with ongoing investments in R&D to enhance membrane durability and fouling resistance.
In 2024 and 2025, the sector has witnessed a notable uptick in partnerships between membrane technology providers and process engineering firms. Kubota Corporation, renowned for its submerged membrane bioreactor (MBR) systems, has entered into joint ventures with regional engineering companies to localize production and tailor solutions for high-solids applications, particularly in Asia-Pacific markets. Similarly, Toray Industries has expanded its collaboration with chemical and mining companies to develop next-generation ultrafiltration membranes capable of handling abrasive and high-viscosity slurries.
New entrants are also making their mark, often focusing on niche applications or leveraging novel materials. Startups specializing in ceramic and hybrid polymer-ceramic membranes are attracting attention for their ability to withstand aggressive cleaning regimes and extend operational lifespans. These companies are frequently supported by partnerships with established players, who seek to integrate disruptive technologies into their existing product lines.
The competitive environment is further shaped by the entry of companies from adjacent sectors, such as specialty chemicals and advanced materials. For instance, Evonik Industries has begun to commercialize proprietary membrane materials designed for challenging slurry environments, signaling a trend toward vertical integration and material innovation.
Looking ahead, the slurry ultrafiltration membrane market is expected to see continued consolidation, with leading companies acquiring innovative startups and forming alliances to address evolving regulatory and sustainability requirements. The focus on energy efficiency, membrane longevity, and process integration will likely drive further collaboration between technology developers and end-users, ensuring a competitive and rapidly evolving landscape through the remainder of the decade.
Future Outlook: Disruptive Trends, Sustainability, and Investment Opportunities
The future of slurry ultrafiltration membrane technology is poised for significant transformation as industries intensify their focus on sustainability, process efficiency, and regulatory compliance. As of 2025, several disruptive trends are shaping the sector, with leading manufacturers and technology providers investing in advanced materials, digitalization, and circular economy solutions.
A key trend is the development of next-generation membranes with enhanced fouling resistance and higher selectivity, driven by the need to process increasingly complex industrial slurries. Companies such as SUEZ and Pall Corporation are at the forefront, introducing polymeric and ceramic membranes engineered for longer lifespans and reduced cleaning frequency. These innovations are particularly relevant for sectors like mining, food and beverage, and pharmaceuticals, where slurry composition can be highly variable and challenging.
Digitalization is another disruptive force, with membrane systems now integrating real-time monitoring and predictive maintenance. Veolia and Kubota Corporation are deploying smart sensors and data analytics to optimize membrane performance, reduce downtime, and extend operational life. This shift not only improves process reliability but also aligns with broader Industry 4.0 initiatives across manufacturing and water treatment.
Sustainability is a central driver, as regulatory pressures and corporate ESG commitments push for lower energy consumption and waste generation. Membrane manufacturers are responding by developing modules that operate at lower pressures and enable higher recovery rates, thus minimizing both energy use and concentrate disposal. Toray Industries and Membranium are notable for their efforts in producing energy-efficient ultrafiltration modules and promoting closed-loop water reuse in industrial settings.
Investment opportunities are expanding, particularly in regions with stringent environmental regulations and water scarcity concerns. The Asia-Pacific market, led by China and India, is witnessing rapid adoption of ultrafiltration technologies for industrial wastewater treatment and resource recovery. Strategic partnerships and joint ventures are expected to accelerate, as seen in recent collaborations between global membrane suppliers and local engineering firms.
Looking ahead, the slurry ultrafiltration membrane sector is likely to see continued growth through 2030, underpinned by advances in material science, digital integration, and circular economy business models. Companies that can deliver robust, sustainable, and digitally enabled solutions are well-positioned to capture emerging opportunities and address the evolving needs of industrial clients worldwide.
Sources & References
- SUEZ
- Pall Corporation
- Kubota Corporation
- Veolia
- GEA Group
- Sartorius
- Pentair
- GE Vernova
- Koch Separation Solutions
- Water.org
- International Organization for Standardization
- ASTM International
- DuPont
- Evonik Industries
- Membranium