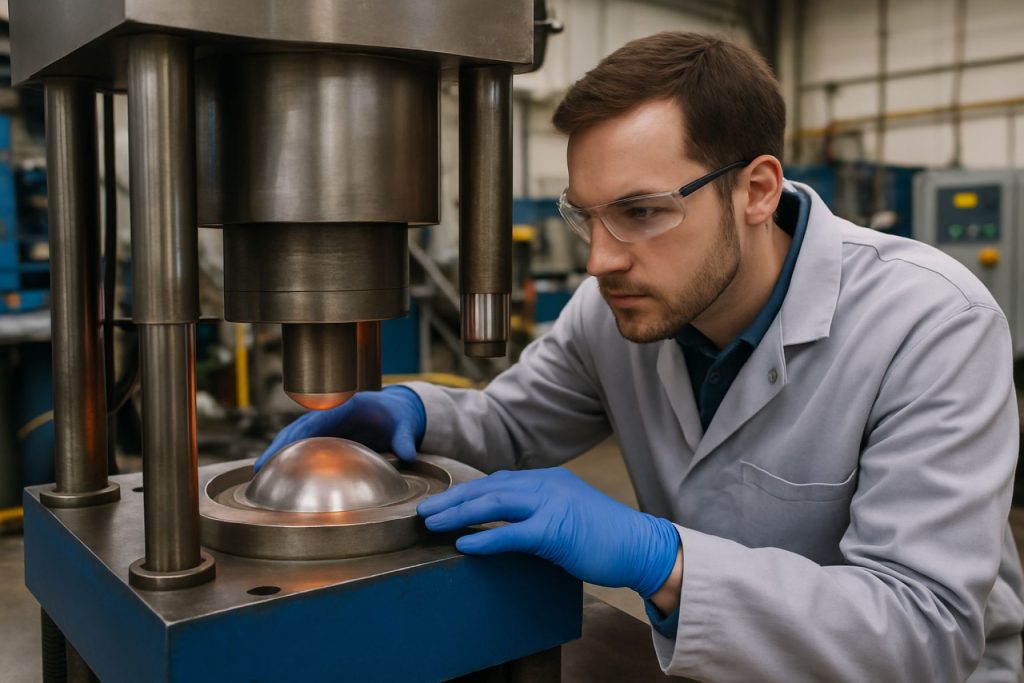
Table of Contents
- Executive Summary: 2025–2029 Market Outlook
- Key Technology Innovations in Superplastic Forming Platforms
- Major Industry Players and Strategic Initiatives
- Current Adoption Across Aerospace, Automotive, and Energy Sectors
- Emerging Research Hubs and Collaboration Platforms
- Regulatory Standards and Industry Guidelines (e.g., asme.org, sae.org)
- Forecast: Market Size, Growth Drivers, and Regional Trends
- Challenges: Material Science, Cost, and Scalability
- Future Outlook: Next-Gen Alloys and Digital Integration
- Case Studies: Pioneering Projects from Leading Manufacturers (e.g., boeing.com, airbus.com, honeywell.com)
- Sources & References
Executive Summary: 2025–2029 Market Outlook
Superplastic forming (SPF) research platforms are positioned at the forefront of advanced manufacturing innovation as the industry moves through 2025 and into the latter part of the decade. The current landscape is marked by a convergence of automotive, aerospace, and energy sector demand for lightweight, complex-shaped components, driving increased investment in both academic and industrial SPF research infrastructure. In particular, leading aerospace manufacturers and material suppliers are collaborating closely with research institutions to develop new alloys, process controls, and digital simulation tools aimed at further exploiting the superplasticity phenomenon for commercial applications.
A notable trend from 2024, continuing into 2025, is the proliferation of dedicated SPF research facilities and pilot lines in North America, Europe, and Asia. Companies such as GKN Aerospace and Airbus have made public investments in SPF technology, with the latter establishing partnerships to accelerate process development and component qualification for next-generation aircraft. In parallel, materials suppliers like TIMET and Kobe Steel are expanding their R&D capabilities, enabling rapid prototyping and testing of novel titanium and aluminum alloys optimized for superplastic forming.
The 2025–2029 period is also set to witness significant upgrades in process monitoring and digitalization within SPF research platforms. Integration of Industry 4.0 principles—such as real-time data acquisition, predictive modeling, and machine learning—is becoming standard practice in newly commissioned testbeds. This is exemplified by collaborations between research institutions and technology providers like Siemens, whose automation and simulation solutions are being embedded to enhance forming process precision and repeatability.
Looking forward, the market outlook for SPF research platforms is robust. There is strong momentum toward sustainable manufacturing, with SPF enabling material efficiency and reduced energy consumption compared to conventional forming. Additionally, the emergence of hybrid forming technologies—combining SPF with additive manufacturing or incremental sheet forming—will spur further research activity and platform development over the next five years. By 2029, the global network of SPF research hubs is expected to double, supporting expanded adoption in automotive lightweighting, aerospace structural parts, and high-value energy applications. As such, ongoing partnerships between OEMs, materials producers, and research organizations will remain central to the advancement and commercialization of superplastic forming technologies.
Key Technology Innovations in Superplastic Forming Platforms
Superplastic forming (SPF) research platforms are experiencing significant technological advancements as automotive, aerospace, and advanced manufacturing sectors seek lighter, high-performance materials. In 2025, leading research and industrial organizations are leveraging digitalization, automation, and advanced material science to transform SPF techniques and equipment.
A major trend is the integration of high-precision temperature and pressure control systems, which are critical for optimizing the superplastic state and achieving complex part geometries. Companies such as Aeromet International and GKN Aerospace are collaborating with research institutes to refine real-time monitoring and closed-loop feedback in forming presses, resulting in improved consistency and quality of formed titanium and aluminum components.
Research platforms are also adopting digital twins and simulation-driven process design. These virtual environments allow engineers to model superplastic deformation and predict formability limits before physical trials, significantly reducing development cycles. Airbus has reported ongoing collaborations with academic and industrial partners to deploy process simulation tools for optimizing the SPF process for complex aerospace structures.
Another notable innovation is the use of additive manufacturing (AM) to produce tailored dies and tooling for SPF applications. This approach, pursued by companies such as 3D Systems, enables rapid prototyping and iteration of tool designs, as well as the integration of conformal cooling channels to enhance temperature uniformity during forming.
Automation and robotics are increasingly incorporated into SPF research platforms to streamline material handling, reduce human error, and enable precise forming sequences. Fraunhofer Society institutes have demonstrated pilot lines where robots handle high-temperature blanks and finished components, improving both throughput and workplace safety.
In the coming years, SPF research platforms are expected to further expand their capabilities with machine learning algorithms for real-time process optimization and defect prediction. Partnerships between industrial giants and research centers are accelerating the translation of laboratory advances into scalable manufacturing solutions, particularly for lightweight, high-strength alloys used in electric vehicles and next-generation aircraft.
Overall, the convergence of digital technologies, advanced materials, and automation is setting a new standard for superplastic forming research platforms. These innovations not only enhance process reliability and efficiency but also open pathways for producing ever more complex and lightweight metal components at industrial scale.
Major Industry Players and Strategic Initiatives
Superplastic forming (SPF) research platforms are increasingly critical as industries such as aerospace, automotive, and energy seek lightweight, complex-shaped metal components with superior mechanical properties. As of 2025, major industry players are accelerating investments in advanced SPF research capabilities and strategic collaborations, positioning themselves for technological leadership in the next generation of forming processes.
Key aerospace manufacturers remain at the forefront of SPF research. Airbus continues to expand its internal research platforms, integrating SPF with hot forming and diffusion bonding to optimize titanium and aluminum structures for aircraft applications. Similarly, Boeing has ongoing partnerships with material suppliers and universities to refine SPF process modeling and in-line quality monitoring, aiming to reduce cycle times and improve reproducibility.
On the supplier and technology side, GKN Aerospace and Saab are investing in pilot SPF research platforms, focusing on digital simulation and rapid tooling development. Aeromet International is advancing its superplastic aluminum alloys in collaboration with major OEMs, leveraging pilot-scale SPF lines to accelerate qualification for next-generation aircraft components.
- Aramco is exploring SPF research for energy sector applications, particularly for complex, corrosion-resistant alloys used in piping and heat exchangers.
- Norsk Hydro has launched research initiatives integrating SPF and advanced aluminum alloys for automotive lightweighting, working with automotive OEMs on pilot trials.
- Kobe Steel and Mitsubishi Heavy Industries are developing high-throughput SPF research platforms in Japan, emphasizing automation, process monitoring, and integration with additive manufacturing.
Collaboration with academic institutions and government research centers remains a strategic priority. For example, the UK’s Catapult network and Germany’s Fraunhofer Institutes are supporting joint SPF research with multiple industrial partners, creating open-access testbeds for process validation and scale-up.
The outlook for 2025 and beyond is marked by convergence: digital twins, AI-driven process optimization, and hybrid manufacturing (combining SPF with laser or additive processes) are emerging as focal points for research platforms. As regulatory and sustainability pressures increase, major players are expected to accelerate the deployment of these advanced SPF research initiatives, reinforcing their competitive edge and enabling faster adoption across high-value manufacturing sectors.
Current Adoption Across Aerospace, Automotive, and Energy Sectors
Superplastic forming (SPF) research platforms have become central to innovation in manufacturing processes across the aerospace, automotive, and energy sectors. As of 2025, the adoption of SPF research infrastructure is accelerating, driven by increased demand for lightweight, high-strength components and efficiency gains in complex part production.
In the aerospace sector, leading manufacturers and suppliers are investing heavily in SPF research platforms. Companies such as Airbus and Boeing continue to collaborate with material suppliers and research institutes to optimize SPF for both titanium and aluminum alloys. For example, GKN Aerospace has expanded its SPF capabilities in Europe and North America, focusing on the development and qualification of large aircraft structures with enhanced geometrical complexity and reduced assembly requirements. These platforms use advanced digital monitoring and closed-loop control to refine process parameters, directly contributing to lighter and more fuel-efficient airframes.
The automotive industry is also ramping up the deployment of SPF research facilities. Major automakers such as Nissan Motor Corporation and BMW Group are integrating SPF platforms into their R&D centers to develop lightweight panels and structural components from aluminum and magnesium alloys. Recent data suggests that these research investments are enabling the prototyping of parts with up to 40% weight reduction compared to traditional stamping, while maintaining or improving crashworthiness. SPF research platforms are also being leveraged to investigate forming of next-generation battery enclosures and structural elements for electric vehicles.
- In 2025, collaborative research initiatives between automakers, universities, and material suppliers are fostering open innovation, with consortia such as the AutoForm and Superplastic Forming Industry Group advancing shared SPF process databases and simulation tools.
The energy sector, particularly in nuclear and renewable energy, is adopting SPF research platforms to form intricately-shaped heat exchangers and containment vessels from high-performance alloys. Companies like GE and Sandvik are investing in SPF pilot lines to validate new alloys and geometries capable of withstanding extreme operational environments. These research platforms are equipped with in-situ measurement technologies to monitor deformation mechanisms and optimize cycle times, critical for both performance and cost-efficiency.
Looking ahead, the next few years are expected to see further integration of artificial intelligence and digital twins into SPF research platforms, supporting predictive process control and rapid prototyping. The ongoing expansion across these sectors highlights SPF’s strategic role in meeting the evolving demands for lightweight, durable, and high-performance components.
Emerging Research Hubs and Collaboration Platforms
Superplastic forming (SPF) continues to gain traction as a transformative manufacturing process, particularly within the aerospace, automotive, and energy sectors. As of 2025, the acceleration of innovation in SPF is closely linked to the emergence of dedicated research hubs and collaborative platforms designed to foster cross-industry partnership, accelerate material advances, and optimize forming technologies. These research ecosystems are typically formed through alliances between academic institutions, industry leaders, and governmental bodies, enabling a synergistic approach to tackling current SPF challenges such as process efficiency, material cost, and manufacturability of complex geometries.
Europe remains a focal point for SPF research, with clusters such as the UK’s Midlands Advanced Manufacturing Hub and Germany’s Industrie 4.0 initiatives integrating SPF into broader digital manufacturing strategies. Notably, organizations like Airbus have been active in collaborating with universities and research institutes to enhance the superplastic forming capabilities for high-strength aluminum and titanium alloys, aiming at lighter and more resilient aerospace structures.
In North America, the Superplastic Forming Center at the University of Michigan, in partnership with major automotive suppliers and aerospace manufacturers, has expanded its research capacity with advanced forming presses and in-situ process monitoring equipment. Meanwhile, Lockheed Martin and Boeing maintain active SPF research and development programs, often working alongside government-funded research laboratories. These collaborations have yielded incremental advances in forming speeds and scale, with a strong emphasis on digital simulation and real-time process control.
Asia-Pacific research hubs are also accelerating SPF innovation. Japan’s government-industry-academia consortia, including members like Kobe Steel, are pushing the boundaries of SPF for both automotive and electronics applications, emphasizing new alloys and hybrid forming methods. China’s leading aerospace manufacturers, such as COMAC, have invested in SPF research platforms aimed at indigenizing advanced manufacturing technologies.
Looking ahead, the next few years are set to see a proliferation of open-innovation platforms and digital twins for SPF process optimization. Multi-partner consortia are expected to drive standardization in process parameters and lifecycle assessment, with organizations like the European Aluminium Association supporting shared research resources. The convergence of materials science, data analytics, and advanced forming equipment promises to further democratize access to SPF technologies, particularly for SMEs seeking to enter high-value manufacturing segments.
Regulatory Standards and Industry Guidelines (e.g., asme.org, sae.org)
Superplastic forming (SPF) is a pivotal manufacturing technology for complex, lightweight components—particularly in aerospace, automotive, and defense sectors. In 2025 and the coming years, regulatory standards and industry guidelines continue to shape the research platforms supporting SPF advancement, ensuring safety, quality, and interoperability across global markets.
Leading standards organizations, such as ASME (American Society of Mechanical Engineers) and SAE International, provide the foundational guidance for superplastic forming equipment, process parameters, and material properties. ASME’s Boiler and Pressure Vessel Code (BPVC) and related standards address the design and fabrication of pressure-containing components, with sections applicable to superplastically formed parts used in critical assemblies. Recent updates have referenced SPF-specific testing and qualification methods, reflecting the growing industrial application of these techniques.
Similarly, SAE International maintains several Aerospace Material Specifications (AMS) that detail requirements for superplastic alloys, including titanium and aluminum alloys frequently used in SPF research and production. The AMS 4911 specification, for example, is widely referenced for titanium alloy sheets in SPF/DB (superplastic forming/diffusion bonding) processes. In 2025, revision cycles are focusing on harmonizing SPF material and process standards with international counterparts, responding to increased cross-border collaboration and supply chain integration.
Research platforms—ranging from university laboratories to industry consortia—are increasingly aligning with these regulatory frameworks. Collaborative efforts, such as those led by Boeing and Airbus, emphasize the importance of standardized data collection and reporting for SPF process variables, ensuring comparability and reproducibility across research sites. Moreover, platforms supported by organizations like NASA and the National Institute of Standards and Technology (NIST) are integrating updated ASME and SAE guidance into their digital modeling and experimental validation protocols.
Looking ahead, regulatory bodies are expected to address emerging topics, such as digital twins for SPF process control, additive manufacturing integration, and environmental impact assessments. Industry guidelines will likely expand to cover sustainable practices and traceability, as global supply chains demand greater transparency and lifecycle management. The ongoing dialogue between standards organizations, manufacturers, and research entities ensures that SPF research platforms remain robust, compliant, and responsive to technological evolution through 2025 and beyond.
Forecast: Market Size, Growth Drivers, and Regional Trends
The global superplastic forming (SPF) research platform market is poised for robust growth in 2025 and the ensuing years, underpinned by increasing demand for lightweight, high-strength metal components in automotive, aerospace, and defense sectors. This process, which enables intricate forming of materials such as titanium and aluminum alloys at elevated temperatures, continues to attract substantial investment in research infrastructure and pilot production lines.
Recent initiatives spearheaded by leading aerospace manufacturers and material suppliers are setting the tone for market expansion. For example, Airbus has expanded its R&D facilities to focus on advanced SPF techniques, aiming to optimize component design and reduce material waste in future aircraft programs. Similarly, Boehlert GmbH, a European leader in metal forming, has announced upgrades to its research lines, integrating novel digital monitoring tools to refine process parameters and material flow.
Market size projections indicate that the SPF research platform segment is expected to grow at a compound annual growth rate (CAGR) exceeding 7% from 2025 to 2028, driven by escalating requirements for reduced-emission vehicles and next-generation airframes. Asia-Pacific remains a particularly dynamic region, with new research centers emerging in China and Japan, supported by government-backed initiatives to localize advanced forming technologies. In North America, Lockheed Martin and GKN Aerospace are actively investing in SPF pilot plants and collaborative university research programs, aiming to secure intellectual property and supply chain resilience.
Key growth drivers include the rising adoption of high-performance alloys, the need for efficient prototyping platforms, and the integration of digital twins and simulation tools for process optimization. The automotive sector, particularly leading suppliers such as Magna International, is expected to increase SPF research spending to support electric vehicle (EV) lightweighting targets.
- Regional Trends: Europe and North America are likely to maintain leadership in SPF research platform deployment, while Asia-Pacific is forecast to accelerate its share through state-funded laboratory networks and industry-academia collaborations.
- Technology Outlook: The next few years will see a convergence of SPF with additive manufacturing and advanced simulation, further enhancing the value proposition of research platforms for rapid prototyping and low-volume production.
In summary, superplastic forming research platforms will see sustained global investment and innovation through 2025 and beyond, leveraging cross-sectoral demand for lighter, stronger, and more complex metal parts and benefiting from a vibrant ecosystem of industrial and academic stakeholders.
Challenges: Material Science, Cost, and Scalability
Superplastic forming (SPF) research platforms are at the forefront of innovation in advanced manufacturing, yet they continue to face significant challenges related to material science, cost, and scalability as the sector progresses into 2025 and beyond.
A central challenge remains the identification and development of alloys exhibiting reliable superplasticity at commercially viable strain rates. Traditional SPF materials—such as specific grades of aluminum, titanium, and magnesium alloys—require precise thermomechanical processing and control of microstructure, making large-scale, cost-effective production difficult. For instance, leading producers like Constellium and Tata Technologies have reported ongoing research to optimize alloy chemistries for enhanced elongation and lower forming temperatures, but widespread industrial adoption is slowed by the high costs and technical barriers of scaling laboratory breakthroughs to robust production lines.
Another major hurdle is the inherently slow forming rates and significant energy consumption associated with superplastic forming. Despite advances in press technology and process modeling, SPF’s cycle times remain substantially longer than conventional stamping or hydroforming, which is a critical bottleneck for automotive and aerospace applications that demand high throughput. Companies such as Aeromet International and Safran Group are investing in research platforms focused on process acceleration—experimenting with hybrid forming approaches and real-time control systems—but these solutions are still under evaluation for commercial readiness.
Cost is further compounded by the need for high-precision tooling and specialized furnaces capable of maintaining uniform temperatures and atmospheric control. This specialized infrastructure is expensive to commission and operate, placing SPF at a disadvantage compared to alternative methods. Furthermore, the limited availability of qualified suppliers capable of producing superplastically formed components at scale—particularly outside of aerospace—constrains market growth. The industry is seeing new investments in collaborative research centers and pilot lines, such as those supported by Airbus and GKN Aerospace, aimed at validating scalable SPF solutions for next-generation applications.
Looking ahead to the next few years, the outlook centers on breakthroughs in alloy development, digital process optimization, and modular forming platforms. These advances could reduce cycle times and lower costs, making SPF more accessible for sectors like automotive lightweighting and renewable energy. However, overcoming the entrenched challenges of material science and scalability remains a key research priority for all stakeholders in the SPF technology landscape.
Future Outlook: Next-Gen Alloys and Digital Integration
Superplastic forming (SPF) technologies are undergoing significant transformation, driven by concerted research efforts in advanced alloys and digital manufacturing integration. As we move through 2025 and into the latter half of the decade, global industry stakeholders are investing in research platforms that blend material science innovations with digitalization to unlock new frontiers in SPF applications.
A prominent trend is the focus on next-generation alloys—particularly high-strength aluminum, magnesium, and titanium systems—engineered for extreme formability at lower temperatures and faster cycle times. Leading aerospace suppliers and material producers such as Airbus and Boeing have ongoing collaborations with research institutions to tailor alloy microstructures for superplastic forming, aiming to reduce energy consumption and component weight in aircraft structures. Similarly, automotive leaders like Nissan Motor Corporation are piloting SPF platforms for lighter electric vehicle chassis, leveraging novel Al-Mg alloys to achieve intricate shapes and thinner gauges.
Digital integration is a parallel pillar shaping SPF research platforms. The deployment of Industry 4.0 technologies—real-time process monitoring, predictive modeling, and closed-loop control—enables precise tuning of forming parameters and accelerates alloy qualification. Partnerships between machine manufacturers such as Quintus Technologies and software providers are producing integrated simulation and control suites for SPF presses, enhancing process repeatability and reducing development lead times. In 2025, pilot lines equipped with cloud-based analytics are generating high-fidelity datasets that fuel machine learning algorithms, further optimizing the forming process for complex aerospace and automotive components.
Sector-specific research platforms are also expanding through international consortia and public-private partnerships. Initiatives in Europe and Asia, often involving organizations such as Airbus and JFE Steel Corporation, are creating shared SPF testbeds for alloy development and process validation under real-world manufacturing conditions. These collaborative efforts are expected to accelerate the transfer of superplastic forming from laboratory to full-scale production, especially for next-gen alloy systems.
Looking ahead, the outlook for SPF research platforms is marked by a convergence of material innovation and digital intelligence. By 2027, industry analysts anticipate that integrated research platforms will deliver not only faster alloy development cycles and expanded forming capabilities, but also enable adaptive, data-driven SPF lines. This will position superplastic forming as a cornerstone of lightweighting strategies across transportation, energy, and consumer sectors, supporting broader sustainability goals and manufacturing agility.
Case Studies: Pioneering Projects from Leading Manufacturers (e.g., boeing.com, airbus.com, honeywell.com)
Superplastic forming (SPF) continues to underpin innovation in aerospace and automotive manufacturing, with leading manufacturers launching dedicated research platforms to refine and scale this advanced process. As of 2025, companies such as Boeing, Airbus, and Honeywell are at the forefront, leveraging SPF research platforms to address challenges of lightweighting, design flexibility, and cost reduction.
A notable case study is Boeing’s ongoing investment in SPF research at its dedicated manufacturing centers. The company’s SPF platforms focus on optimizing titanium and aluminum alloy forming for large, complex aerostructures. In 2024, Boeing expanded its St. Louis facility’s SPF research capabilities, integrating real-time process analytics and automation to accelerate development cycles and improve repeatability for components in next-generation commercial and defense aircraft. This platform is expected to deliver new process data and tooling strategies, enhancing both structural performance and production efficiency over the next several years.
Meanwhile, Airbus has intensified its commitment to SPF research through collaborative platforms involving academia and suppliers. The company’s Bremen site, a hub for materials innovation, has recently initiated multi-partner SPF projects aimed at scaling up the use of ultrafine-grained titanium alloys in fuselage and wing applications. These efforts combine advanced forming simulations with in-situ monitoring, enabling rapid validation of new alloy systems. Airbus’s SPF research platform is scheduled to deliver its first production-ready demonstrator parts by 2026, with the outlook of supporting future single-aisle and widebody aircraft programs.
On the systems and equipment front, Honeywell has leveraged its SPF research platform to develop integrated forming and heat treatment solutions for aerospace and energy sector customers. In 2025, Honeywell’s research centers are piloting smart SPF cells equipped with IoT sensors, allowing for closed-loop feedback and predictive maintenance. Data from these platforms is already informing the design of next-generation turbine engine components, with anticipated efficiency and durability gains expected to be validated in operational environments by 2027.
The outlook for superplastic forming research platforms is robust. As digitalization and materials science converge, these industry-led initiatives are set to lower barriers for adopting SPF in both established and emerging sectors. The next few years will likely see greater integration of AI-driven process control, eco-friendly forming gases, and expanded use of advanced alloys, positioning SPF as a cornerstone of sustainable, high-performance manufacturing.
Sources & References
- GKN Aerospace
- Airbus
- TIMET
- Kobe Steel
- Siemens
- Aeromet International
- 3D Systems
- Fraunhofer Society
- Boeing
- Saab
- Norsk Hydro
- Mitsubishi Heavy Industries
- Nissan Motor Corporation
- GE
- Sandvik
- Lockheed Martin
- ASME
- NASA
- National Institute of Standards and Technology
- Magna International
- Constellium
- Tata Technologies
- Quintus Technologies
- JFE Steel Corporation
- Honeywell