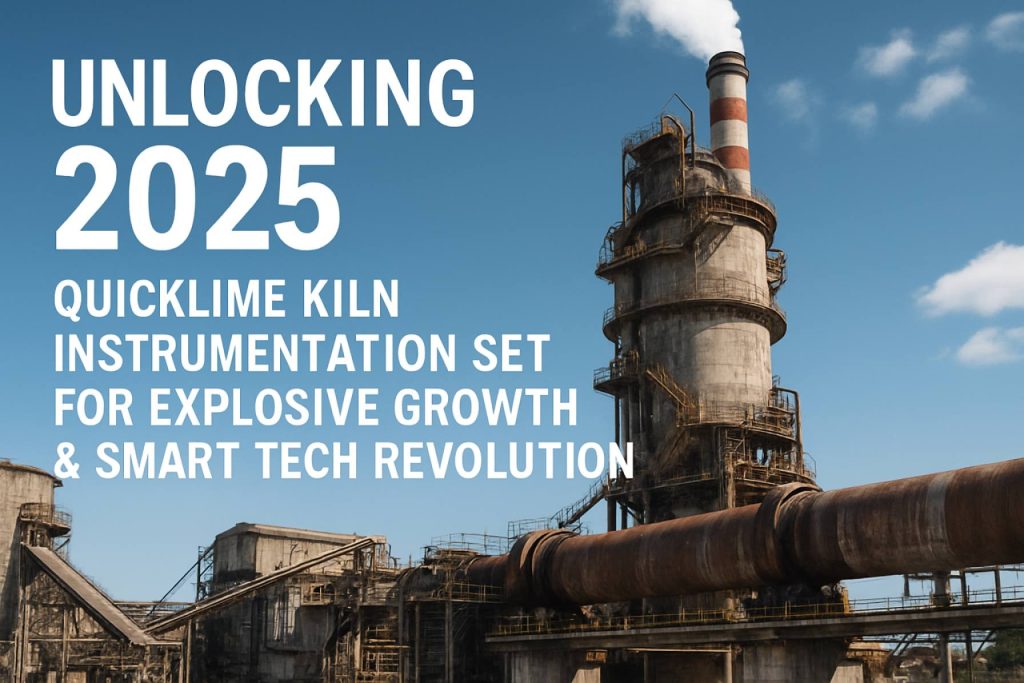
Table of Contents
- Executive Summary: 2025 Market Snapshot & Growth Projections
- Current State of Quiklime Kiln Instrumentation: Key Players and Solutions
- Emerging Technologies: Advanced Sensors, AI, and IoT Integration
- Market Drivers: Energy Efficiency, Sustainability, and Regulatory Pressures
- Competitive Landscape: Manufacturer Strategies and Innovation Initiatives
- Key End-User Segments and Application Trends
- Regional Analysis: Global Hotspots and Investment Opportunities
- Forecast 2025–2030: Market Size, Growth Rates, and Revenue Outlook
- Challenges and Risks: Supply Chain, Cybersecurity, and Skills Gap
- Future Outlook: Strategic Recommendations for Stakeholders
- Sources & References
Executive Summary: 2025 Market Snapshot & Growth Projections
The quicklime kiln instrumentation market in 2025 is poised for steady growth, driven by escalating demand for process optimization, energy efficiency, and emissions controls in the lime industry. Quicklime kilns—integral to sectors like steel, paper, and construction—are increasingly adopting advanced instrumentation solutions to meet stringent regulatory and operational requirements. Instrumentation encompasses temperature, pressure, emission, and gas analyzers, as well as automation systems that enable real-time process monitoring and control.
Leading kiln technology providers are reporting heightened interest in digitalized instrumentation. Companies such as FLSmidth have highlighted a marked shift toward integrated sensor networks and advanced process control (APC) systems in the quicklime sector, aiming for reduced fuel consumption and lower CO2 emissions. ANDRITZ and Siemens are also expanding their instrumentation portfolios to address sector-specific requirements, including high-temperature gas analytics and robust automation platforms.
Current market dynamics are shaped by tightening environmental standards. The European Union’s Industrial Emissions Directive and similar frameworks globally are compelling lime producers to invest in continuous emissions monitoring systems (CEMS) and enhanced process analytics. For example, SICK AG has introduced advanced CEMS tailored for lime kilns, supporting regulatory compliance and operational transparency.
Data from leading equipment manufacturers indicate that automation and remote diagnostics are becoming baseline expectations. KHD Humboldt Wedag notes that predictive maintenance modules, powered by kiln instrumentation data, are reducing unplanned downtime and optimizing throughput for operators globally.
Looking ahead to 2026 and beyond, the market outlook points to further adoption of AI-driven analytics, cloud-based data integration, and tighter alignment with decarbonization initiatives. Industry participants are expected to prioritize instrumentation upgrades as part of broader digital transformation strategies, with North America, Europe, and Asia-Pacific as key growth regions. As kilns become more connected, the imperative for reliable, high-precision instrumentation will intensify, underpinned by sustained investment from both established lime producers and emerging players.
Current State of Quiklime Kiln Instrumentation: Key Players and Solutions
The current landscape of quicklime kiln instrumentation in 2025 is defined by increasing automation, digital integration, and a focus on process optimization for energy efficiency and emission reduction. Quicklime production, heavily reliant on rotary and shaft kilns, demands precise control of critical parameters including temperature, pressure, air flow, and gas composition to ensure product quality and regulatory compliance.
Key players dominating this segment include Siemens AG, Endress+Hauser, ABB Group, and Emerson Electric Co.. These companies offer a comprehensive suite of instrumentation solutions designed for the demanding environments of lime kilns.
- Temperature and Gas Analysis: Advanced optical pyrometers, thermocouples, and in-situ gas analyzers are widely deployed for continuous real-time monitoring of kiln temperatures and combustion gases (CO2, O2, SO2). For example, Siemens AG offers gas analysis systems with high resistance to dust and heat, specifically tailored for rotary kiln environments.
- Process Automation and Digitalization: Integration of kiln instrumentation with Distributed Control Systems (DCS) and Industrial Internet of Things (IIoT) platforms is accelerating, enabling predictive maintenance and advanced process control. ABB Group and Emerson Electric Co. supply DCS and smart sensor solutions that facilitate data-driven optimization, enhancing yield and reducing energy consumption.
- Emissions Monitoring: Compliance with tightening emission standards is driving adoption of Continuous Emissions Monitoring Systems (CEMS). Endress+Hauser and Siemens AG provide integrated CEMS platforms designed for the lime industry, capable of measuring a wide range of pollutants with high accuracy.
Looking ahead, kiln operators are expected to increasingly invest in smart instrumentation that supports remote monitoring, real-time optimization, and automated compliance reporting. The continued evolution of sensor miniaturization, wireless connectivity, and AI-driven analytics—offered by established players like ABB Group and Emerson Electric Co.—is poised to further enhance safety, efficiency, and sustainability in quicklime kiln operations through 2025 and beyond.
Emerging Technologies: Advanced Sensors, AI, and IoT Integration
The quicklime kiln sector is experiencing a significant technological transformation as advanced sensors, artificial intelligence (AI), and Internet of Things (IoT) solutions become increasingly integrated into kiln instrumentation. In 2025, operators are prioritizing these innovations to address energy efficiency, process stability, emissions reduction, and predictive maintenance.
A major focus has been the deployment of robust, high-temperature sensors capable of real-time monitoring of key parameters such as temperature, CO and O2 levels, and material flow. Manufacturers like Siemens AG have developed advanced process instrumentation specifically for harsh kiln environments, enabling precise data acquisition and control. These sensors are now commonly paired with centralized data platforms, which aggregate readings from multiple points in the kiln, allowing for holistic oversight and rapid anomaly detection.
AI-driven analytics are emerging as a game-changer in kiln operation. Companies such as ABB Ltd and Endress+Hauser are rolling out solutions that leverage machine learning to analyze sensor data in real time, optimize combustion conditions, and predict maintenance requirements. For example, ABB’s APC (Advanced Process Control) platforms use historical and live data to dynamically adjust fuel and air ratios, reducing energy consumption and stabilizing product quality.
IoT connectivity is further enhancing the value of these systems. By networking sensors, actuators, and control software, plant operators can remotely monitor kiln performance and receive predictive alerts for equipment wear or process deviations. ANDRITZ AG has introduced cloud-based platforms that give plant managers access to real-time and historical operational data from any location, supporting both immediate troubleshooting and long-term optimization.
Looking ahead, the next few years will see wider adoption of digital twins—virtual representations of kilns synchronized with live sensor input—for simulation, troubleshooting, and training purposes. As regulatory and cost pressures mount, the quicklime sector is expected to further embrace these digitalization trends, with instrumentation upgrades increasingly viewed as essential investments for competitive, sustainable operations.
Market Drivers: Energy Efficiency, Sustainability, and Regulatory Pressures
In 2025, the market for quicklime kiln instrumentation is being decisively shaped by the convergence of three major drivers: the imperative for energy efficiency, the intensifying focus on sustainability, and mounting regulatory pressures. Industrial lime producers are under increasing scrutiny to optimize their operations, reduce emissions, and ensure compliance with evolving standards worldwide.
Energy efficiency remains a pivotal concern for the lime industry, given that fuel costs can constitute up to 60% of total production expenses in calcination processes. Advanced kiln instrumentation—encompassing temperature, pressure, and gas analysis sensors—enables real-time process monitoring and precise control, directly impacting fuel usage and product quality. Companies such as Siemens AG and Endress+Hauser are actively supplying state-of-the-art process automation and sensor technology tailored for harsh kiln environments in the quicklime sector. Their solutions provide operators with granular process insights, facilitating immediate corrective actions and long-term efficiency gains.
Sustainability objectives are also accelerating instrumentation upgrades. Quicklime production is a significant source of CO2 emissions, and as decarbonization becomes a central tenet for industrial operations, lime producers are leveraging instrumentation to enable lower-carbon calcination. For instance, Thermo Fisher Scientific offers advanced gas analyzers that help optimize combustion, minimize excess air, and measure emissions in real time. These technologies are critical for both direct emission reductions and for enabling the adoption of alternative fuels or carbon capture strategies.
Regulatory pressures are intensifying, with the European Union’s Industrial Emissions Directive (IED) and similar frameworks in Asia and North America mandating stricter control and reporting of air pollutants from lime kilns. Automated monitoring and reporting systems, such as those provided by ABB, are now integral to compliance strategies, offering continuous emissions monitoring (CEM) and integration with plant control systems. This ensures that production facilities can demonstrate regulatory adherence and avoid costly penalties.
Looking ahead, the outlook for quicklime kiln instrumentation is one of robust growth and technical refinement. As digitalization expands and regulatory thresholds tighten further, demand for smart, networked sensor systems and advanced process analytics is expected to remain strong through the late 2020s. The industry’s trajectory is clear: kiln instrumentation is not only a lever for operational excellence but also a critical tool for meeting the dual challenges of sustainability and compliance in an increasingly regulated environment.
Competitive Landscape: Manufacturer Strategies and Innovation Initiatives
The competitive landscape of quicklime kiln instrumentation in 2025 is shaped by pronounced innovation, digital integration, and strategic collaborations among leading manufacturers. With increasingly strict environmental regulations and the push for operational efficiency, kiln operators are demanding advanced instrumentation systems that offer real-time monitoring, enhanced process control, and predictive maintenance capabilities.
Key industry players such as Siemens AG, Endress+Hauser Group, and Emerson Electric Co. are investing in next-generation sensor technologies and digital platforms. For instance, Siemens’ process instrumentation solutions for the cement and lime sector now feature integrated digital communication (PROFINET, HART), enabling seamless data flow between field devices and control systems. This digitalization allows operators to optimize combustion conditions and fuel usage in quicklime kilns, directly supporting sustainability and cost-reduction objectives.
Innovation initiatives in 2025 increasingly focus on the adoption of Industry 4.0 principles. Endress+Hauser has rolled out its IIoT platform, Netilion, which connects process instruments to cloud-based analytics, providing actionable insights for kiln health and efficiency. Their smart sensors offer self-diagnostics and remote calibration, reducing downtime and maintenance costs—key differentiators in a competitive market Endress+Hauser Group.
Meanwhile, Emerson emphasizes predictive analytics and automated process control in its Plantweb digital ecosystem, offering kiln instrumentation that integrates seamlessly with distributed control systems (DCS) and asset management platforms. This approach allows quicklime producers to anticipate equipment failures and optimize process variables in real time, a substantial operational advantage Emerson Electric Co..
Strategic partnerships are also reshaping the competitive environment. Siemens and Endress+Hauser have each announced collaborations with kiln OEMs and EPC contractors to co-develop bespoke instrumentation packages tailored to evolving environmental standards and customer needs Siemens AG. Such alliances are expected to proliferate through 2026 as demand grows for turnkey, digitally-enabled kiln solutions.
Looking ahead, the competitive focus will likely intensify around artificial intelligence (AI)-driven process optimization, carbon emissions monitoring, and holistic digital integration, as manufacturers vie to help lime producers meet tightening sustainability requirements and maximize profitability.
Key End-User Segments and Application Trends
The quicklime industry, a critical supplier to sectors such as steel, pulp and paper, environmental management, and construction, is experiencing notable shifts in kiln instrumentation trends as of 2025. Quicklime kiln operators are increasingly investing in advanced instrumentation solutions to enhance process control, product quality, energy efficiency, and regulatory compliance. These trends are driven by stricter environmental requirements, the rising cost of energy, and the need for operational automation in response to labor shortages and skills gaps.
Key end-user segments leveraging advanced kiln instrumentation include:
- Steel Manufacturing: Steel producers, among the largest consumers of quicklime, are rapidly adopting real-time process monitoring and emission control systems for their lime kilns. For example, companies like Tata Steel and ArcelorMittal are investing in technologies such as gas analyzers and temperature profiling to optimize lime quality and reduce fuel consumption.
- Pulp and Paper: In the pulp and paper sector, precise control of quicklime reactivity and purity is crucial for efficient causticizing. Kiln instrumentation—such as online analyzers and automated control valves—enables mills to maintain tight quality specifications and minimize downtime. Valmet has reported increasing deployment of lime kiln optimization systems in North American and European mills.
- Environmental and Flue Gas Treatment: Quicklime is essential for flue gas desulfurization (FGD) and water treatment. Power plants and waste incinerators are upgrading kiln instrumentation to ensure consistent product properties and compliance with emissions standards. Lhoist, a major lime producer, has highlighted investments in advanced process monitoring to meet these requirements.
- Construction Materials: With the ongoing demand for high-performance building materials, cement and autoclaved aerated concrete (AAC) manufacturers are refining lime kiln operations using modern instrumentation. Kiln Flame Systems Ltd offers burner management and temperature monitoring systems adopted by lime producers serving the construction industry.
Looking ahead, rapid integration of digitalization, such as IIoT connectivity and AI-driven analytics, is anticipated. Modular sensor platforms and cloud-based data visualization are expected to become mainstream among large and mid-sized lime producers. The outlook for 2025 and beyond suggests continued growth in demand for precise, robust, and interconnected kiln instrumentation, especially as decarbonization efforts accelerate across heavy industries.
Regional Analysis: Global Hotspots and Investment Opportunities
The global landscape for quicklime kiln instrumentation is evolving rapidly, with certain regions emerging as hotspots for investment and technological advancement. As of 2025, Asia-Pacific continues to dominate the market, driven by robust infrastructure development, environmental regulations, and the modernization of existing lime production facilities. China and India, in particular, are witnessing significant upgrades in kiln automation and process control systems to boost efficiency and comply with stricter emissions standards. Companies such as Siemens and ABB are actively deploying advanced instrumentation—including distributed control systems (DCS), temperature and gas analyzers, and process optimization solutions—across new and retrofitted plants in these countries.
In Europe, sustainability imperatives and the European Green Deal are accelerating investment in digitalization and energy management within the lime industry. Leading kiln technology suppliers, such as Maerz Ofenbau AG and Lhoist, are focusing on integrating real-time data acquisition, predictive maintenance, and emission monitoring systems to optimize kiln performance and reduce the sector’s carbon footprint. The anticipated tightening of EU industrial emissions directives by 2026 is expected to fuel further adoption of sophisticated instrumentation in quicklime kilns, particularly in Germany, France, and Poland.
North America is seeing renewed investment in quicklime production, mainly due to the resurgence of construction and steel industries. The United States, home to major lime producers such as Graymont and Carmeuse, is investing in advanced process control and emission reduction solutions. These companies are collaborating with automation partners to implement smart sensors and integrated control platforms, aiming for improved energy efficiency and compliance with tightening EPA regulations.
In Latin America and the Middle East, investment is focused on both greenfield lime projects and modernization of older kilns. The adoption of advanced instrumentation is growing, albeit at a slower pace, often driven by multinational cement and mining companies seeking to standardize operations across global assets. For example, FLSmidth continues to supply digital kiln monitoring and process automation solutions to new projects in Brazil and Saudi Arabia.
Looking ahead, regional demand for quicklime kiln instrumentation will be shaped by government policies, the pace of industrial expansion, and the push for decarbonization. Asia-Pacific and Europe are expected to remain at the forefront of investment and technological adoption, while emerging markets will increasingly prioritize instrumentation as they scale up production and environmental compliance.
Forecast 2025–2030: Market Size, Growth Rates, and Revenue Outlook
The quicklime kiln instrumentation market is poised for significant transformation between 2025 and 2030, driven by advances in process automation, digitalization, and stringent environmental regulations. As quicklime producers prioritize operational efficiency and emissions reduction, demand for sophisticated instrumentation—spanning temperature, pressure, gas analysis, and process control—continues to rise.
In 2025, leading kiln instrumentation providers report strong order books, particularly in regions with rapid industrialization and environmental compliance mandates. Siemens and Endress+Hauser have highlighted increased deployment of integrated sensor networks and advanced analyzers within lime kiln operations, facilitating real-time process optimization and predictive maintenance. Additionally, ABB has introduced digital twins and cloud-based diagnostics for rotary kiln systems, offering actionable insights that translate into reduced fuel consumption and minimized unplanned downtime.
From 2025 onwards, the industry anticipates a compound annual growth rate (CAGR) in the high single digits for kiln instrumentation, outpacing general industrial automation due to the sector’s unique need for rugged, high-accuracy instruments capable of withstanding harsh kiln environments. The Asia-Pacific region is set to lead growth, buoyed by expanding steel, construction, and chemical sectors that are major consumers of quicklime. European markets, meanwhile, are investing in upgrades to meet decarbonization targets, often retrofitting existing kilns with state-of-the-art monitoring and control solutions.
Revenue for kiln instrumentation is expected to surpass previous forecasts, with market leaders such as Siemens, Endress+Hauser, and ABB continuing to expand their portfolios. For example, Endress+Hauser has reported a year-on-year increase in demand for its gas analysis and emission monitoring systems, reflecting both regulatory and operational drivers. Additionally, new entrants focusing on niche sensors and IoT-enabled solutions are expected to intensify competition, fostering innovation and price competitiveness.
Looking towards 2030, the quicklime kiln instrumentation market will likely see heightened integration of artificial intelligence, advanced data analytics, and remote services. These capabilities promise not only further efficiency gains but also enhanced regulatory compliance and sustainability for quicklime producers worldwide.
Challenges and Risks: Supply Chain, Cybersecurity, and Skills Gap
The quicklime kiln instrumentation sector faces a complex landscape of challenges and risks in 2025 and the immediate future, particularly in the areas of supply chain reliability, cybersecurity, and workforce skills. These issues are shaping investment decisions and operational priorities for kiln operators and instrumentation suppliers worldwide.
Supply Chain Constraints
The sourcing of specialized sensors, control systems, and automation components for quicklime kilns remains vulnerable to ongoing global supply chain disruptions. Key manufacturers, such as Siemens and Endress+Hauser, report persistent delays for specific electronic modules and chips, a situation exacerbated by geopolitical tensions and the lingering aftereffects of the COVID-19 pandemic. These delays can extend lead times for critical kiln instrumentation upgrades or replacements, impacting both greenfield installations and retrofits. In response, companies are increasing inventory buffers and seeking alternative suppliers, but the risk of bottlenecks remains high through at least 2026.
Cybersecurity Threats
As quicklime kilns become more digitally integrated—leveraging remote monitoring, predictive analytics, and Industrial Internet of Things (IIoT) connectivity—the threat landscape for cyberattacks is expanding rapidly. Companies such as ABB and Rockwell Automation have highlighted the rising frequency of targeted attacks on operational technology (OT) assets in process industries, including lime production. Vulnerabilities in legacy control systems, combined with the increased adoption of cloud-based data platforms, require kiln operators to invest in robust cybersecurity measures such as network segmentation, regular patching, and comprehensive threat monitoring. Regulatory pressure, particularly in Europe and North America, is expected to intensify, mandating higher standards for OT security compliance within the next few years.
Skills Gap and Workforce Challenges
A significant risk for the sector is the ongoing shortage of skilled personnel capable of designing, operating, and maintaining advanced kiln instrumentation systems. According to Siemens and ABB, the rapid pace of technological innovation is outstripping the rate at which the workforce can be trained. This challenge is particularly acute in regions with aging technical staff and limited access to specialized training. Industry stakeholders are responding with expanded apprenticeship programs, remote support solutions, and the integration of augmented reality (AR) tools for on-site maintenance and troubleshooting. However, bridging the skills gap will remain a critical risk through the late 2020s.
Looking ahead, the quicklime kiln instrumentation sector must navigate these intertwined risks through diversification of supply chains, proactive cybersecurity strategies, and sustained investment in workforce development to ensure reliable, safe, and efficient kiln operations.
Future Outlook: Strategic Recommendations for Stakeholders
The future outlook for quicklime kiln instrumentation is shaped by mounting pressures for improved efficiency, sustainability, and regulatory compliance across the lime production sector. As of 2025, stakeholders are witnessing a rapid evolution in sensor technologies, data analytics, and process automation, all converging to redefine best practices for kiln operation and maintenance.
A primary recommendation for kiln operators and plant managers is the proactive adoption of advanced process instrumentation, such as tunable diode laser spectrometers and infrared temperature sensors. For instance, the integration of in-situ gas analyzers enables real-time monitoring of critical parameters like O2, CO, and CO2 concentrations inside the kiln, directly supporting fuel optimization and emissions reduction efforts. Companies like Siemens and Endress+Hauser have recently expanded their process gas analytics portfolios, offering robust solutions that meet the demanding conditions of quicklime kilns.
Digitalization is expected to accelerate, with distributed control systems (DCS) and cloud-based platforms enabling predictive maintenance and performance benchmarking. Stakeholders should invest in retrofitting legacy instrumentation with smart sensors and wireless networks, thus enhancing data accessibility and reliability. Emerson has highlighted the value of integrating digital valve monitoring and advanced process controls to minimize unplanned downtime and optimize lime quality.
Environmental compliance is a critical driver for instrumentation upgrades. With tightening emission standards anticipated through 2027, especially in the European Union and North America, stakeholders must prioritize instrumentation capable of supporting continuous emissions monitoring (CEM). Solutions from ABB and Siemens are now widely used for CEM applications in lime kilns, providing the data necessary for regulatory reporting and internal sustainability targets.
Finally, workforce training on new instrumentation and digital tools remains essential. Stakeholders are encouraged to partner with instrument manufacturers for technical support and skill development programs, ensuring smooth implementation and long-term return on investment. As these technologies mature, early adopters will likely benefit from enhanced operational resilience, lower energy costs, and stronger compliance records—positioning them competitively in a rapidly modernizing lime industry.