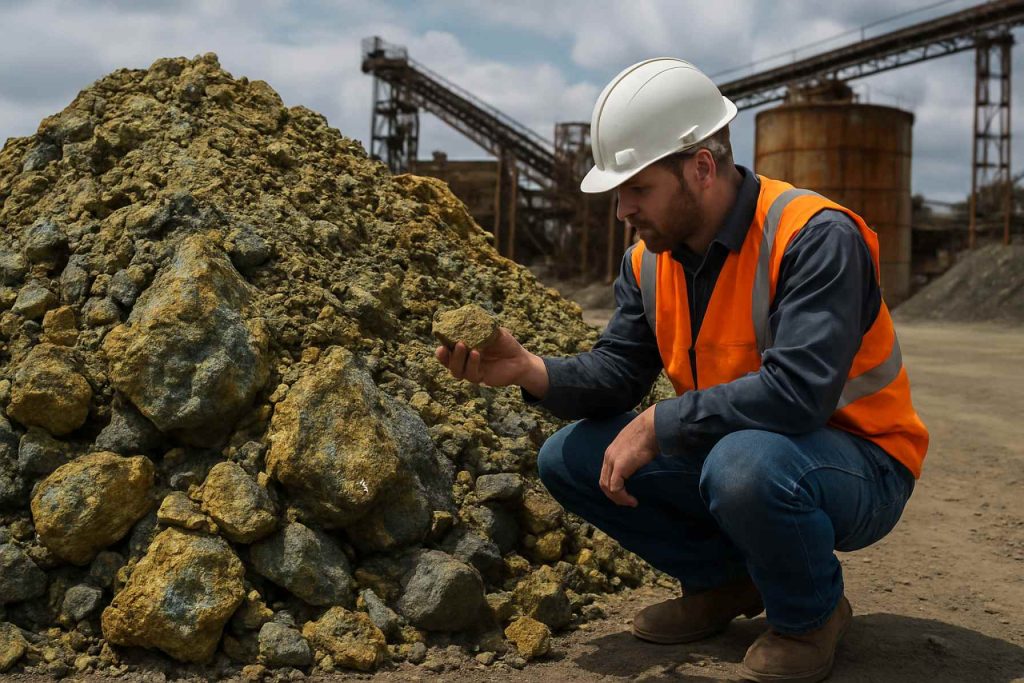
Table of Contents
- Executive Summary: The 2025 Millerite Ore Opportunity
- Market Size, Growth Forecasts, and Key Demand Drivers (2025–2030)
- Breakthrough Technologies in Millerite Ore Extraction and Refinement
- Sustainability and Environmental Impact: The New Industry Standard
- Leading Players and Strategic Partnerships (Sources: eramet.com, vale.com)
- Global Supply Chain Challenges and Solutions
- Government Policy, Incentives, and Regulatory Trends
- Investment Opportunities and Risk Analysis
- Emerging Applications: Batteries, Alloys, and Beyond
- Future Outlook: Strategic Roadmaps and Anticipated Disruptions
- Sources & References
Executive Summary: The 2025 Millerite Ore Opportunity
Millerite ore, a primary nickel sulfide mineral, is gaining renewed attention in 2025 as global demand for nickel intensifies, particularly in the battery and electric vehicle (EV) sectors. The reclamation and refinement of millerite ore are emerging as strategic priorities for mining companies aiming to diversify their nickel sources and reduce reliance on laterite and pentlandite ores. With the International Energy Agency forecasting substantial growth for nickel in EV batteries through 2030, the industry is compelled to optimize extraction and processing methods for less conventional ore bodies such as millerite.
Recent years have seen increased investment in the reclamation of historic mine tailings and the reprocessing of low-grade ore, as companies seek to capitalize on existing resources with advanced hydrometallurgical and bioleaching techniques. Leading nickel producers such as Vale and Norilsk Nickel have initiated pilot programs for the recovery of nickel from secondary sources, including millerite-rich residues, to support sustainability targets and secure long-term supply chains.
Key regions with known millerite occurrences, such as the Sudbury Basin in Canada and select sites in Russia and Australia, are witnessing renewed exploration and resource modeling. In Canada, Glencore and BHP are evaluating millerite-bearing tailings for economic recovery, leveraging existing concentrator infrastructure to minimize capital expenditure. These efforts align with government-backed initiatives to strengthen domestic critical minerals supply and reduce environmental liabilities associated with historic mining operations.
Technological advancements in ore beneficiation and hydrometallurgical refinement are central to the 2025 millerite opportunity. Modern pressure oxidation and solvent extraction techniques are enabling higher nickel yields from complex ores, while also addressing impurities that have historically limited millerite processing. Companies are also exploring partnerships with equipment manufacturers to deploy modular, scalable processing plants at remote or legacy sites, supporting rapid project deployment and reducing logistical bottlenecks.
Looking ahead, the outlook for millerite ore reclamation and refinement is robust, underpinned by the growing imperative for supply chain resilience and environmental stewardship in the nickel sector. As demand for battery-grade nickel accelerates, efficient recovery and processing of millerite ore are poised to play a pivotal role in the global raw materials landscape, offering both economic and sustainability benefits for industry stakeholders.
Market Size, Growth Forecasts, and Key Demand Drivers (2025–2030)
The global market for millerite ore reclamation and refinement is poised for notable growth between 2025 and 2030, fueled primarily by the accelerating demand for battery-grade nickel and the ongoing transition to electric vehicles (EVs). Millerite (NiS), a nickel sulfide mineral, is increasingly recognized as a valuable secondary source for nickel extraction, especially as high-grade primary nickel sulfide deposits become scarcer and environmental regulations tighten around traditional mining.
As of 2025, nickel demand is projected to surpass 3.5 million tonnes, with the battery sector accounting for nearly 40% of this consumption. The reclamation of nickel from millerite-bearing ores and tailings is thus an increasingly attractive strategy to augment supply and reduce reliance on newly mined materials. Major mining and metal companies, such as Rio Tinto and Vale S.A., have begun to invest in advanced hydrometallurgical and bioleaching technologies to improve nickel yields from lower-grade ores and historic tailings, including those containing millerite. These moves are in response to both resource constraints and stricter sustainability criteria imposed by downstream industries.
Between 2025 and 2030, the market for millerite ore processing is expected to grow at a compound annual growth rate (CAGR) of 6–8%, aligning with the broader nickel market expansion. This growth is underpinned by several demand drivers:
- Strong policy support for EV manufacturing and battery recycling across North America, Europe, and East Asia.
- Corporate ESG (Environmental, Social, Governance) commitments demanding transparent, low-carbon nickel supply chains.
- Technological advancements in selective leaching and solvent extraction, which enable higher nickel recovery rates from complex ore bodies and waste streams.
- Strategic investments by companies such as Glencore and Nornickel in expanding processing capacity for nickel sulfide ores, including those with significant millerite content.
Looking ahead, the outlook for millerite ore reclamation and refinement remains positive. Industry leaders are targeting circular economy models that incorporate closed-loop recycling of nickel from mining wastes and end-of-life batteries, further bolstering demand for efficient millerite processing techniques. As regulatory frameworks evolve and technology matures, the sector is anticipated to play a crucial role in meeting the world’s nickel needs for clean energy and sustainable mobility.
Breakthrough Technologies in Millerite Ore Extraction and Refinement
The rapid evolution of nickel demand, fueled by the electric vehicle and renewable energy sectors, has driven significant advancements in millerite (NiS) ore reclamation and refinement technologies as of 2025. Millerite, a key nickel sulfide mineral, is increasingly targeted for recovery not only from primary mines but also from legacy tailings and low-grade ores. In the past year, several mining and metallurgical companies have accelerated research and deployment of breakthrough technologies to enhance both the efficiency and environmental sustainability of millerite ore processing.
A notable trend is the integration of bioleaching methods, which utilize specialized microorganisms to selectively extract nickel from millerite ores. Companies such as Vale S.A. and Rio Tinto are piloting bioleaching in both primary mining operations and tailings reclamation projects. Early results from these initiatives indicate that bioleaching can reduce energy consumption by up to 30% compared to traditional pyrometallurgical processes, while also minimizing sulfur dioxide emissions—a persistent challenge in nickel sulfide ore processing.
Alongside bioleaching, hydrometallurgical advancements are reshaping millerite refinement. High-pressure acid leaching (HPAL) and pressure oxidation (POX) techniques are being refined to boost nickel recovery rates from complex sulfide matrices. Nornickel has reported increased yields through the adoption of modified POX circuits that allow for selective precipitation of nickel, improving both purity and throughput. These processes also facilitate the recovery of byproducts such as cobalt, adding further value and promoting circular resource management.
- Automation and digitalization are also transforming millerite reclamation. Real-time ore characterization using X-ray fluorescence (XRF) sensors and advanced process control systems are being deployed at mine sites owned by BHP and Anglo American. This allows for dynamic adjustment of grinding, flotation, and leaching parameters, maximizing nickel recovery from heterogenous ore bodies and historic tailings.
- Water and waste management innovations are increasingly integral to new projects. Closed-loop water recycling, as implemented by Glencore, and dry-stack tailings technologies are reducing both water consumption and environmental risk, in line with stricter global regulatory standards.
Looking forward, the sector is expected to see expanded deployment of these technologies, especially as the economic feasibility of extracting nickel from lower-grade millerite deposits improves. Collaborative research programs among major producers and equipment suppliers are likely to yield further breakthroughs in selective leaching agents, process intensification, and secondary metal recovery. These advances position millerite ore reclamation as a pivotal part of the nickel supply chain transformation through the latter half of the 2020s.
Sustainability and Environmental Impact: The New Industry Standard
As the demand for nickel rises in the transition to electric vehicles and renewable energy systems, the sustainability and environmental impact of millerite ore reclamation and refinement have become central concerns for the nickel industry in 2025. Millerite (NiS), a primary nickel sulfide mineral, is increasingly targeted for its comparatively high nickel content and the relative energy efficiency of its processing compared to laterite ores.
Recent years have seen leading nickel mining and refining companies implement new reclamation strategies and cleaner technologies to address environmental challenges. A prominent example includes the integration of closed-loop water management systems and advanced tailings treatment, minimizing the release of heavy metals and sulfide compounds into local ecosystems. Companies such as Vale and Nornickel have publicly committed to improving their water recycling rates and reducing tailings dam construction, aligning with global best practices for sustainable mineral processing.
In the realm of ore refinement, the adoption of hydrometallurgical techniques—such as high-pressure acid leaching (HPAL) and bioleaching—has gained traction as an alternative to traditional pyrometallurgical smelting. These methods, now piloted by industry leaders, allow for the extraction of nickel from lower-grade millerite ore with less energy input and reduced atmospheric emissions. For instance, Glencore has expanded pilot operations for bioleaching, which uses microbial action to separate nickel from sulfide ores, resulting in lower greenhouse gas emissions and less hazardous byproducts.
Furthermore, there is a growing emphasis on the reclamation of legacy millerite mine sites. Companies are increasingly required to present detailed closure and rehabilitation plans prior to project approval. This includes re-vegetation, restoration of natural watercourses, and long-term monitoring of reclaimed areas. FPX Nickel, for example, has outlined comprehensive reclamation protocols designed to return mined land to a stable, productive state, with measurable targets for biodiversity restoration and community benefit.
Looking forward, regulatory pressures and evolving market expectations are set to drive further innovation in sustainable millerite ore processing. The industry standard is rapidly shifting towards full lifecycle stewardship, with environmental, social, and governance (ESG) metrics playing a decisive role in project financing and customer procurement decisions. As major automakers and battery producers tighten sourcing requirements, millerite-derived nickel that meets robust sustainability criteria is expected to command a premium, reinforcing the impetus for continued environmental improvements across the supply chain.
Leading Players and Strategic Partnerships (Sources: eramet.com, vale.com)
The landscape of millerite ore reclamation and refinement in 2025 is shaped by the activities and alliances of several leading players, with a growing emphasis on sustainability and supply chain security. Two industry giants, Eramet and Vale, are at the forefront, leveraging their expertise and global reach to advance the reclamation and processing of nickel from millerite deposits.
Eramet, a French mining and metallurgical group, has intensified its investment in nickel ore beneficiation, particularly focusing on the extraction and processing of millerite ores found within its global portfolio. The company is actively deploying advanced hydrometallurgical and pyrometallurgical technologies to boost recovery rates and reduce environmental impact. In 2024, Eramet announced the expansion of its nickel operations in Indonesia, centered around sustainable ore reclamation methods, with full-scale production ramp-up expected in 2025. Strategic partnerships with local governments and technology providers are integral to Eramet’s approach, aiming to secure long-term access to high-grade millerite resources and to streamline the refinement process for battery-grade nickel products (Eramet).
Vale, headquartered in Brazil, remains one of the world’s largest nickel producers and a pivotal force in the evolution of millerite ore refinement. The company has implemented significant process optimizations at its operations in Canada and Indonesia, targeting higher recovery of nickel from sulfide sources, including millerite. Vale’s 2025 strategy emphasizes closed-loop water systems, reduced carbon emissions, and enhanced tailings management—key for environmental compliance and long-term operational viability. In recent years, Vale has entered into strategic agreements with battery manufacturers and automotive OEMs, seeking to ensure a transparent and traceable supply of refined nickel tailored for electric vehicle (EV) batteries (Vale).
Looking ahead, the next few years are likely to see deeper collaboration between major nickel producers, technology innovators, and downstream consumers. Joint ventures targeting millerite ore reclamation are expected to proliferate, especially in regions like Indonesia and Canada, where resource potential and supportive regulatory frameworks align. The shared goal is to accelerate the production of high-purity nickel, critical for the fast-growing EV and energy storage sectors. As stakeholder expectations rise around ESG performance, these partnerships are positioned not just for operational efficiency, but also for leadership in responsible resource stewardship.
Global Supply Chain Challenges and Solutions
The global supply chain for millerite (nickel sulfide) ore reclamation and refinement is poised for significant transformation in 2025 and the coming years, driven by mounting demand for nickel in battery manufacturing and stainless steel production. The resurgence of interest in millerite as a nickel source is largely due to the shift toward electric vehicles (EVs) and energy storage, sectors that require high-purity nickel and have placed unprecedented pressure on traditional nickel supply chains. However, the millerite supply chain faces a series of challenges, including ore accessibility, processing complexity, geopolitical constraints, and environmental regulations.
One of the primary supply chain challenges is the declining grade and increasing depth of accessible nickel sulfide ores, including millerite. Many established nickel mining regions, such as Canada and Australia, are now encountering deeper deposits and more complex mineralogy, increasing operational costs and complicating extraction and beneficiation processes. Companies like Vale S.A. and BHP Group have reported ongoing investments in ore sorting, improved flotation, and hydrometallurgical techniques to enhance the recovery of millerite and other nickel-bearing minerals. These efforts aim to offset declining ore grades and increase the yield from existing operations.
Another significant constraint is the environmental and regulatory landscape. The reclamation and refinement of millerite entails the management of sulfur emissions and tailings, both of which are subject to increasingly stringent global regulations. To address these challenges, industry leaders are investing in closed-loop water systems, improved tailings management, and sulfur recovery technologies. For example, Nornickel has accelerated its environmental modernization projects, including the implementation of advanced sulfur capture systems in its nickel processing facilities.
Geopolitical disruptions and trade tensions continue to impact nickel supply chains, with resource nationalism and export restrictions in key mining countries adding volatility to raw material flows. In response, downstream manufacturers and refiners are seeking to diversify sources and invest in local refining capacity. Notably, there is a trend toward vertical integration, as seen with battery manufacturers establishing partnerships or direct investments in mining and refining operations to secure long-term supply.
Looking ahead, the outlook for the millerite ore supply chain in 2025 and beyond is cautiously optimistic. Technological advancements in ore processing, recycling, and digital supply chain management are expected to mitigate some of the current challenges. Collaborative initiatives among miners, refiners, and end-users aim to ensure stable supply while adhering to sustainability targets. Strategic investments and environmental stewardship will be pivotal as the sector strives to meet the surging demand for nickel in the global transition to low-carbon technologies.
Government Policy, Incentives, and Regulatory Trends
Government policy and regulatory frameworks are playing an increasingly pivotal role in shaping the reclamation and refinement of millerite ore, a key nickel sulfide mineral. As global demand for nickel—especially battery-grade nickel—continues to surge due to the electric vehicle (EV) and renewable energy sectors, countries with significant nickel resources are enacting policies to ensure efficient resource management and promote sustainable practices.
In 2025, several nation-states are advancing environmental standards and economic incentive programs aimed at responsible millerite ore processing. For instance, Vale S.A., a major nickel producer with operations in Brazil and Canada, is actively collaborating with local governments to implement stricter tailings management and reclamation requirements. This follows recent regulatory tightening in Canada, where amendments to the Metal and Diamond Mining Effluent Regulations (MDMER) have mandated more robust water quality monitoring and post-mining land restoration for nickel operations, including those processing millerite ores.
Indonesia, another leading nickel producer, has maintained its ban on the export of unprocessed nickel ores, including millerite, to stimulate domestic value-added industries. The Indonesian government continues to offer tax holidays, investment allowances, and expedited permitting for companies establishing local refining capacities, as confirmed by partnerships with PT Aneka Tambang Tbk (ANTAM). The government’s goal is to foster a vertically integrated nickel supply chain, incentivizing modern hydrometallurgical facilities that can efficiently process lower-grade sulfide ores, including millerite, while complying with strict environmental standards.
- In the European Union, the Critical Raw Materials Act (2023/2024) continues to shape regional policy through financial support for circular economy projects, recycling initiatives, and funding for research into low-impact ore processing technologies. This includes backing for pilot projects that apply advanced bioleaching and solvent extraction techniques to millerite-containing tailings, with the aim of maximizing nickel recovery while minimizing environmental disruption.
- Australia’s government, through the Department of Industry, Science and Resources, is expanding grants and co-investment programs for companies demonstrating best-in-class reclamation and refining processes for nickel ores. Compliance with the updated Mine Rehabilitation Fund and new requirements for progressive mine closure plans is a prerequisite for project approval, as exemplified by operations run by BHP and First Quantum Minerals.
Looking ahead to the next few years, the outlook is for continued regulatory convergence on environmental stewardship, with governments leveraging financial incentives and stricter permitting to drive innovation in millerite ore reclamation and refinement. The trend is toward more transparent supply chains, mandatory ESG disclosures, and the prioritization of projects that can demonstrate reduced carbon and ecological footprints, positioning responsible millerite ore operations as central to the future of the global nickel industry.
Investment Opportunities and Risk Analysis
Investment in millerite ore reclamation and refinement is gaining momentum as the global demand for nickel intensifies, particularly for use in battery technologies and stainless steel. Millerite (NiS), a nickel sulfide mineral, has historically been less favored compared to pentlandite ores due to its lower nickel content and metallurgical challenges. However, advancements in extraction technologies and the evolving economics of nickel supply are altering its investment profile through 2025 and beyond.
A key driver is the strategic focus on resource diversification and supply security, especially in regions actively seeking to establish domestic nickel supply chains. Companies such as Vale and Glencore, major global nickel producers, have begun evaluating and, in some cases, piloting reclamation of lower-grade sulfide ores, including millerite, from legacy mine tailings and previously uneconomical deposits. This approach not only addresses environmental liabilities but also recovers valuable metals as nickel prices remain robust.
Technological advancements are central to the millerite opportunity. Hydrometallurgical processes—such as bioleaching and pressure oxidation—have demonstrated improved recoveries and cost efficiencies for millerite-hosted ores in pilot plants and early commercial operations. Such technologies reduce energy input and greenhouse gas emissions compared to traditional pyrometallurgical routes, aligning with the low-carbon objectives of companies like Rio Tinto and BHP, both of which are invested in innovation for ore processing.
Despite these opportunities, several risks must be carefully considered. First, the variability in millerite ore bodies and their often complex mineralogy can complicate processing, potentially impacting recovery rates and operating costs. Second, regulatory scrutiny around tailings reclamation and environmental permitting can impose delays or require significant upfront investment. Third, nickel price volatility—driven by fluctuations in stainless steel production and battery sector demand—may affect project economics and investor returns.
Looking ahead, the investment outlook for millerite ore reclamation and refinement will depend on the pace of technological adoption, supportive policy frameworks, and sustained nickel demand growth. Companies with established expertise, operational scale, and robust environmental management are well-positioned to capitalize on these trends through 2025 and into the late 2020s, while new entrants may face steeper barriers to entry but could benefit from strategic partnerships and technology licensing.
Emerging Applications: Batteries, Alloys, and Beyond
The reclamation and refinement of millerite ore—a nickel sulfide mineral (NiS)—are increasingly integral to emerging applications such as advanced battery chemistries, specialty alloys, and catalytic processes. As global demand for nickel accelerates, especially in the context of electrification and green technologies, millerite’s high nickel content and relatively low iron impurities make it an attractive feedstock for next-generation applications. In 2025 and the coming years, the industry is witnessing notable developments in both the technological and commercial spheres related to millerite ore processing.
Recent advancements focus on improving the efficiency and sustainability of millerite ore reclamation. Traditional methods, including flotation and pyrometallurgical smelting, are being complemented by hydrometallurgical processes such as high-pressure acid leaching (HPAL) and bioleaching, which can yield higher nickel recovery rates and minimize environmental impact. Leading nickel producers are piloting these advanced processes to extract nickel from complex sulfide ores, including millerite. For instance, Vale and Nornickel are investing in plant upgrades and new pilot facilities to optimize nickel recovery from diverse mineralogical sources, with millerite being a target due to its favorable characteristics.
The battery sector, particularly producers of nickel-rich cathode materials for lithium-ion batteries, is driving much of the renewed interest in millerite. Major battery manufacturers and their supply chain partners are seeking secure, high-grade nickel sources to support the surge in electric vehicle (EV) production. Companies such as Umicore and BASF are closely monitoring developments in nickel supply and have expressed interest in refined nickel products derived from millerite as part of their efforts to ensure feedstock flexibility and supply chain resilience.
Beyond batteries, millerite-derived nickel is also being utilized in specialty alloys for aerospace, electronics, and chemical engineering, where purity and specific alloying characteristics are critical. Demand for such alloys is forecasted to grow steadily through 2025 and beyond, underpinned by trends in lightweighting and high-performance materials.
Looking ahead, the outlook for millerite ore reclamation and refinement is shaped by ongoing investments in process innovation, tightening environmental regulations, and the strategic imperative to diversify nickel supply chains. Industry participants are expected to further scale up both primary and secondary recovery of millerite, leveraging digitalization and process automation for greater efficiency and traceability. As the market evolves, the role of millerite as a key nickel source is set to expand, particularly in high-value applications critical to the energy transition and advanced manufacturing sectors.
Future Outlook: Strategic Roadmaps and Anticipated Disruptions
The future of millerite ore reclamation and refinement is set against the backdrop of accelerating demand for nickel, driven by the proliferation of electric vehicles, renewable energy storage, and advanced manufacturing. As the nickel supply chain faces pressure to deliver higher volumes of battery-grade material, millerite—an important nickel sulfide mineral—has become increasingly significant, particularly given its potential for efficient extraction and lower impurity profiles compared to laterite ores.
In 2025 and beyond, strategic roadmaps across the nickel sector prioritize the integration of advanced hydrometallurgical and bioleaching technologies to optimize millerite processing. Companies such as MMC Norilsk Nickel and Vale S.A. are actively investing in R&D to enhance recovery rates from low-grade and complex ores, including millerite, while minimizing environmental impact and energy consumption. These efforts are underpinned by ongoing pilot projects and plant upgrades aimed at reducing the carbon footprint of nickel production, in line with global sustainability targets.
The reclamation of millerite-bearing tailings and historic mine waste is also anticipated to gain traction, as industry leaders seek to maximize resource utilization and address legacy environmental liabilities. Initiatives led by Rio Tinto and Glencore are exploring the application of innovative separation and refining techniques to previously uneconomical deposits, with the dual goal of supplying critical nickel units and remediating impacted sites.
Disruptive factors on the horizon include the scaling of direct nickel extraction from millerite ores using solvent extraction and electrowinning, which promise to streamline the production of high-purity nickel intermediates suitable for battery precursor manufacturing. Moreover, the adoption of digital process control, real-time ore characterization, and AI-driven optimization is expected to further boost operational efficiency and traceability throughout the value chain.
Looking forward, the anticipated surge in downstream demand, coupled with regulatory pressures for sustainable sourcing, will likely accelerate the deployment of closed-loop systems and circular economy approaches. Strategic partnerships between mining companies, battery producers, and automakers are poised to emerge as a defining trend, fostering innovation in millerite ore reclamation and refinement technologies and setting new industry benchmarks for environmental stewardship and supply security.