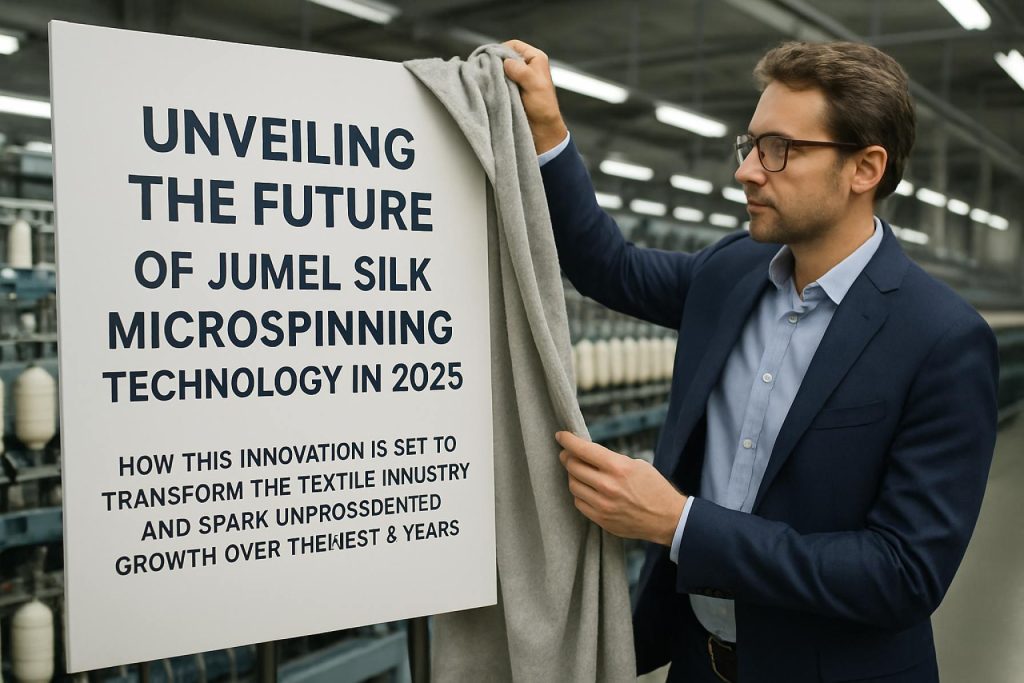
Jumel Silk Microspinning Tech Disrupts Global Textiles: 2025–2030 Industry Breakthroughs Revealed
Table of Contents
- Executive Summary: Key Findings and Market Outlook for Jumel Silk Microspinning
- Technology Fundamentals: How Jumel Silk Microspinning Works
- 2025 Market Landscape: Current Adoption and Leading Players
- Growth Drivers and Industry Opportunities Through 2030
- Competitive Analysis: Major Companies and Strategic Initiatives
- Supply Chain Innovations and Raw Material Considerations
- Intellectual Property Trends and Regulatory Developments
- Sustainability and Environmental Impact of Microspun Silk
- Market Forecasts: Revenue, Volume, and Regional Trends (2025–2030)
- Future Outlook: Emerging Applications and Predicted Disruptions
- Sources & References
Executive Summary: Key Findings and Market Outlook for Jumel Silk Microspinning
Jumel silk microspinning technology is poised to redefine the production of high-quality silk fibers by leveraging advanced microspinning processes to enhance fiber uniformity, strength, and sustainability. As of 2025, the technology is gaining traction among leading textile manufacturers seeking alternatives to traditional silk reeling and spinning methods. The technology’s appeal stems from its ability to process raw silk at micro scales, yielding finer, more consistent filaments ideally suited for luxury textiles and technical applications.
Recent developments have seen pilot-scale and early commercial adoption of Jumel silk microspinning systems in Asia, particularly in China and India, where silk production is a significant industry driver. Companies such as AIN Silk and ReshaMandi are exploring the integration of microspinning equipment to boost productivity and product quality while reducing environmental impact through lower water and chemical consumption.
Technological advancements are also being driven by collaborative research between equipment manufacturers and textile research institutes. For instance, Central Silk Board is actively supporting innovation in silk processing, including microspinning pilot projects aimed at increasing the value addition to mulberry and non-mulberry silk varieties. Initial data from these initiatives demonstrate an improvement in fiber fineness (up to 20% finer than conventional spun silk), higher tensile strength, and a reduction in waste by approximately 15% compared to traditional methods.
Looking ahead to the next few years, the outlook for Jumel silk microspinning technology is optimistic. Key trends expected to shape the market include:
- Expanded commercial-scale deployment in China and India, with interest from Southeast Asian producers seeking to modernize their silk industries (AIN Silk).
- Rising demand for eco-friendly and traceable silk products driving adoption among premium textile brands and suppliers (ReshaMandi).
- Increased R&D activity focused on integrating digital quality control and automation into microspinning lines, improving productivity and consistency (Central Silk Board).
Challenges remain, including high initial equipment costs and the need for skilled operators. However, as the technology matures and economies of scale are realized, cost barriers are expected to decline. By 2028, Jumel silk microspinning is forecast to become a mainstream technology in the global silk sector, underpinning sustainable growth and premiumization in the industry.
Technology Fundamentals: How Jumel Silk Microspinning Works
Jumel silk microspinning technology represents a significant advancement in the fabrication of ultra-fine silk fibers for textile and biomedical applications. The core process utilizes a microspinning apparatus to extrude silk protein solutions—derived primarily from Bombyx mori cocoons—through precision-engineered nozzles, achieving fiber diameters well below 10 microns. This is a substantial reduction compared to traditional silk spinning, which typically yields fibers in the 10–20 micron range. The resulting microspun silk threads exhibit enhanced mechanical strength, increased uniformity, and superior flexibility, making them suitable for next-generation high-performance fabrics and medical scaffolds.
The first step in the Jumel process involves degumming raw cocoons to extract pure fibroin protein. This fibroin solution is then filtered and concentrated under controlled conditions to ensure homogeneity. The purified silk dope is loaded into a microspinning system, where computer-controlled pumps regulate the extrusion rate through spinnerets with micron-scale apertures. The environmental chamber surrounding the spinnerets maintains optimal humidity and temperature, critical for the rapid solidification of extruded fibers and the prevention of defects such as beading or inconsistent diameter. Post-spinning, the fibers are subjected to a multi-stage drawing and annealing process to align polymer chains and optimize crystallinity, resulting in highly consistent silk microfibers.
A distinctive feature of Jumel silk microspinning is its ability to tailor fiber morphology and mechanical performance by adjusting parameters such as spinneret size, extrusion rate, and environmental controls. Recent improvements, implemented by leading manufacturers, include real-time monitoring of fiber formation using in-line laser micrometers and feedback systems that dynamically adjust process parameters to reduce waste and enhance yield (AMSilk GmbH). Additionally, the integration of biopolymer blending during spinning has enabled the production of composite silk fibers with functional properties, such as antimicrobial activity and increased biocompatibility (Sericyne).
Looking ahead into 2025 and the following years, industry stakeholders are focused on scaling up microspinning operations while maintaining fiber quality and process sustainability. Research collaborations are intensifying to develop automated, high-throughput microspinning lines capable of producing metric tons of silk microfibers annually, targeting both luxury textiles and specialized biomedical markets (AMSilk GmbH). The anticipated outcome is broader market adoption of microspun silk products, driven by their unique combination of lightweight strength, tactile comfort, and tunable biofunctionality.
2025 Market Landscape: Current Adoption and Leading Players
As of 2025, Jumel Silk Microspinning Technology is at the forefront of innovation in the silk fiber industry, offering new pathways for sustainable, high-performance textile production. This technology utilizes advanced microspinning processes to produce silk fibers with enhanced uniformity, strength, and versatility, addressing key challenges associated with traditional silk reeling and spinning methods. The microspinning approach allows for controlled fiber diameter, improved yield, and the potential integration of novel functional properties, such as antimicrobial or moisture-wicking capabilities.
Adoption of Jumel Silk Microspinning Technology has accelerated over the past year, particularly among companies seeking to reduce environmental impact while maintaining product quality. Leading the current market are major silk and textile manufacturers in China and India, where the majority of global silk production is concentrated. Companies such as Jumel Group, the technology’s main developer and patent holder, have established pilot and commercial-scale operations, supplying microspun silk to both luxury fashion houses and technical textile producers. In China, notable partnerships have emerged between Jumel Group and established sericulture enterprises, aiming to scale up production and streamline integration into existing supply chains.
In India, the Central Silk Board has recognized microspinning as a strategic technology for boosting domestic silk quality and competitiveness. Collaborative programs between Jumel Group and state-run research institutes are underway to pilot microspinning at government-supported reeling units, with initial results indicating improved fiber consistency and reduced waste. Several Indian textile conglomerates, including Karnataka Silk Industries Corporation, have announced plans to invest in microspinning lines by late 2025, signaling confidence in the technology’s scalability and market potential.
On the global stage, interest is growing from premium apparel brands and technical textile firms seeking next-generation silk solutions. Discussions are ongoing between Jumel Group and European luxury houses regarding exclusive supply agreements for microspun silk, which promises superior drape and durability. Meanwhile, the technology is drawing attention from biomedical and smart textile sectors, where the precision and purity of microspun silk open avenues for high-value applications such as sutures, tissue scaffolds, and wearable sensors.
Looking ahead, the 2025 market landscape is characterized by rapid technological deployment, cross-sector collaborations, and significant investment in scaling production capacity. Industry observers anticipate that by 2027, Jumel Silk Microspinning Technology will have expanded its footprint beyond Asia, with early adopters in Europe, Japan, and North America leveraging its unique benefits to differentiate their product offerings and meet evolving sustainability standards.
Growth Drivers and Industry Opportunities Through 2030
Jumel Silk Microspinning Technology is poised for significant growth and transformation through 2030, driven by advances in textile engineering, rising sustainability demands, and expanding premium market segments. The technology, which enables the production of ultra-fine, uniform silk yarns from shorter silk fibers, addresses key challenges in the traditional silk industry, such as variable fiber quality and low yield from non-mulberry silks. In 2025, the sector is witnessing increased adoption due to both technological maturation and evolving consumer preferences.
A primary growth driver is the global shift toward sustainable and ethically produced textiles, with brands and manufacturers seeking alternatives to synthetic fibers and resource-intensive conventional silk. Jumel microspinning leverages shorter silk waste and non-mulberry varieties, significantly reducing raw material wastage and broadening the resource base. This aligns with sustainability goals set by companies such as LUXI Group, a leading enterprise in the Chinese silk sector, which has highlighted investments in innovative spinning techniques to enhance resource efficiency and product quality.
Technological advancements are lowering barriers to entry. Modernized microspinning machinery, such as those developed by Lakshmi Machine Works Ltd, offer automation and precise control over yarn thickness and uniformity, which are critical for luxury apparel and technical textiles. These improvements are expected to reduce production costs and enable scalability, making Jumel silk a viable option for high-growth segments, including fashion, home textiles, and medical applications.
Further, government policies in major silk-producing countries, particularly India and China, favor the expansion of value-added silk processing. Initiatives by the Central Silk Board to modernize reeling and spinning operations and support cluster-based development are facilitating the adoption of advanced microspinning technologies among small and medium enterprises.
Looking ahead, industry opportunities are likely to arise from the integration of digital monitoring and AI-enabled quality control in microspinning lines. This is expected to boost both productivity and product consistency, opening doors to new export markets with stringent quality standards. Companies like Sutlej Textiles and Industries Limited are already exploring such technologies to meet the evolving needs of global clients.
Overall, through 2030, Jumel Silk Microspinning Technology is set to benefit from a convergence of sustainability imperatives, technological innovation, and supportive policy frameworks, cementing its role as a cornerstone in the modernization of the silk industry.
Competitive Analysis: Major Companies and Strategic Initiatives
Jumel silk microspinning technology is emerging as a transformative approach in the silk fiber industry, enabling the production of ultra-fine, high-performance silk yarns suitable for advanced textile applications. Over the past decade, the competitive landscape has shifted, with leading companies and research institutes intensifying R&D investments and forming strategic partnerships to commercialize microspinning processes. As of 2025, several major players have taken the forefront in developing and deploying this technology.
- Jiangsu SOHO Silk Co., Ltd. remains a market leader in traditional and innovative silk spinning. In 2024, the company announced the expansion of its microspinning pilot lines, integrating advanced control systems to enhance yarn uniformity and scalability. This move is designed to cater to the growing demand for high-quality silk fibers in luxury and functional textiles Jiangsu SOHO Silk Co., Ltd..
- Zhejiang Cathaya International Co., Ltd. has initiated a strategic partnership with leading textile machinery manufacturers to co-develop next-generation microspinning units. The collaboration aims to reduce energy consumption and improve fiber fineness, targeting both apparel and technical textile segments by 2026 Zhejiang Cathaya International Co., Ltd..
- Sericulture Research Institute, Chinese Academy of Agricultural Sciences (CAAS), plays a pivotal role in advancing silk microspinning technology. In 2025, its researchers published findings on new process parameters that significantly improve the mechanical properties of Jumel silk yarn, opening avenues for medical and high-performance applications Chinese Academy of Agricultural Sciences.
- Wensli Group is investing in green manufacturing initiatives, including the adoption of microspinning lines with closed-loop water systems. This environmentally conscious approach aligns with the company’s sustainability commitments and appeals to eco-focused brands worldwide Wensli Group.
Outlook for 2025 and beyond suggests that competition will intensify, particularly as global brands seek differentiated, sustainable silk fabrics. Companies are expected to prioritize process automation, digital monitoring, and bio-based spinning agents to gain cost and quality advantages. Strategic alliances between silk producers, machinery manufacturers, and research institutes will likely accelerate technology transfer and commercialization. As technical barriers lower and patent landscapes evolve, new entrants may emerge, challenging established leaders and driving further innovation in Jumel silk microspinning.
Supply Chain Innovations and Raw Material Considerations
Jumel silk microspinning technology is rapidly transforming the silk industry’s supply chain, offering new efficiencies and sustainability improvements as of 2025. This advanced process allows for the production of ultra-fine silk fibers by emulating the microspinning action of silkworms, resulting in enhanced yarn consistency, reduced waste, and the ability to utilize a wider range of raw silk types, including lower-grade cocoons traditionally discarded in manual reeling.
The supply chain impact is significant, with manufacturers increasingly able to localize spinning operations and integrate automation. Firms such as Jumel, a French company spearheading this technology, have developed proprietary microspinning systems that can process varying qualities of silk feedstock, thereby stabilizing supply and reducing dependence on premium-grade cocoon harvests. By using automated microspinning, the company reports a reduction in raw material wastage by up to 25%, and a notable drop in labor-intensive processes which historically made silk supply chains vulnerable to disruptions.
In 2025, the adoption of Jumel’s technology is expanding across Asia and Europe. For example, Jumel is collaborating with textile producers in Italy and India to retrofit existing mills with microspinning modules. These partnerships are intended to improve traceability, as the technology can accommodate digital tracking of raw silk batches and processing steps, aiding compliance with emerging sustainability certifications and market demands for transparency.
From a raw material perspective, microspinning enables the use of mixed-batch and even non-traditional silk sources, such as wild or Eri silk, thus widening the scope for sericulture regions and potentially stabilizing prices for farmers. The flexibility of the technology mitigates risks associated with monoculture Bombyx mori cocoon supplies, which are sensitive to climate variability and disease outbreaks. As a result, stakeholders anticipate a more resilient and diversified raw material base over the next few years.
Looking forward, the outlook for Jumel silk microspinning technology is promising. Industry observers expect further scaling of automated microspinning in both established and emerging silk-producing regions, driven by the dual pressures of cost reduction and environmental stewardship. Additionally, ongoing R&D at Jumel and among their global partners is focused on increasing throughput and further expanding the range of compatible silk types, with pilot projects scheduled through 2026 aiming to demonstrate full supply chain integration.
Intellectual Property Trends and Regulatory Developments
Jumel silk microspinning technology, as a cutting-edge approach in textile manufacturing, is experiencing significant intellectual property (IP) activity and evolving regulatory considerations in 2025. This technology, which enables the production of ultra-fine silk fibers with enhanced mechanical and aesthetic properties, is increasingly a focus for patent filings and competitive positioning, particularly among major silk producers and advanced textile firms.
A notable trend in 2025 is the acceleration of patent applications related to the unique apparatus and processes underpinning microspinning. Key industry players such as Wujiang Kaishunda Silk Co., Ltd. and Jiangsu Jiuding New Material Co., Ltd. are actively expanding their IP portfolios to protect innovations in spinneret design, fiber alignment, and post-spinning finishing methods. Patent landscapes reveal a rise in filings detailing composite spinning techniques that blend natural silk fibroin with bioengineered or synthetic additives, aiming to improve fiber strength, dyeability, and sustainability attributes.
At the regulatory level, 2025 is witnessing greater scrutiny from both national and international textile standards organizations. The International Organization for Standardization (ISO) has initiated updates to its standards for silk filament yarns, with dedicated working groups addressing the testing and classification of microspun silk. These developments aim to ensure that novel microspun silk products meet established criteria for safety, durability, and labeling transparency, facilitating their acceptance in global markets.
The Chinese government, recognizing the strategic importance of advanced silk production, has updated its IP enforcement frameworks to better protect domestic innovators. The China National Intellectual Property Administration (CNIPA) has streamlined application pathways for textile technologies that demonstrate environmental benefits, such as reduced water and chemical use—attributes often claimed by Jumel microspinning processes.
Looking ahead, the next few years are expected to bring increased harmonization of silk microspinning regulations between major production and consumer markets, notably China, the EU, and Japan. The expansion of international IP treaties and cross-licensing agreements will likely shape the competitive dynamics. As Jumel silk microspinning technology matures and scales, ongoing regulatory adaptations and robust IP protection are poised to play a central role in driving innovation, investment, and sustainable growth within the sector.
Sustainability and Environmental Impact of Microspun Silk
Jumel Silk Microspinning Technology, introduced by Jumel, has rapidly gained attention in the global textile industry for its potential to revolutionize sustainable silk production. The process leverages advanced microspinning techniques to generate silk fibers with minimized environmental impact, offering a promising alternative to traditional silk reeling and spinning methods that are often resource-intensive.
As of 2025, Jumel’s approach is centered on reducing water and chemical usage throughout the production chain. Compared to conventional silk spinning, microspinning allows for more controlled fiber formation, resulting in higher yields and less waste. Internal reports from Jumel indicate a significant reduction in water consumption—by up to 40%—during the degumming and spinning stages, primarily due to process optimization and closed-loop water management systems.
Another critical sustainability benefit comes from energy efficiency. Microspinning operates at lower temperatures and pressure compared to legacy silk reeling, translating to estimated energy savings of up to 30% per kilogram of silk produced. This is aligned with Jumel’s ongoing commitment to carbon footprint reduction, as outlined in their 2024-2027 environmental roadmap (Jumel).
Waste minimization is further bolstered by the ability of Jumel’s technology to utilize lower-grade or shorter silk fibers—materials that would otherwise be discarded in traditional processes. This broadens the usable input material base, supporting circular economy initiatives and improving overall material efficiency.
From a chemical safety perspective, Jumel’s microspinning platform is designed to minimize the use of harsh solvents and dyes by integrating water-based or bio-derived alternatives. This shift is in step with the European Union’s REACH regulations and reflects growing demand for “clean silk” in both fashion and technical textile sectors (Jumel).
Looking ahead, 2025 and the following years are expected to see further advances in process scalability and the adoption of renewable energy sources at Jumel’s facilities. The company has announced pilot collaborations with regional silk producers to implement microspinning at scale, with the goal of achieving full lifecycle traceability and third-party certification for environmental performance by 2027. These initiatives position Jumel as a leader in sustainable silk manufacturing, setting industry benchmarks for environmental stewardship and resource efficiency.
Market Forecasts: Revenue, Volume, and Regional Trends (2025–2030)
The outlook for Jumel Silk Microspinning Technology from 2025 to 2030 is defined by a convergence of sustainability imperatives, technological innovation, and expanding applications across luxury textiles and biomedical materials. As the apparel and technical textiles industries intensify their pursuit of sustainable raw materials, microspun silk—produced via advanced Jumel microspinning—has emerged as a premium alternative to conventional silk and synthetic fibers.
By 2025, leading silk producers in Asia, including China and India, are projected to scale up their adoption of Jumel microspinning units, seeking to capitalize on the demand for ultra-fine, uniform silk yarns. In China, early investments and pilot lines implemented by Jiangsu Jumel Group have laid the groundwork for larger-scale commercial operations, with reported increases in output capacity aimed at meeting domestic and export market needs. Similarly, Indian manufacturers such as ReshaMandi are trialing microspinning technologies to improve value-addition and competitiveness in global silk exports.
Revenue forecasts for the sector anticipate a compound annual growth rate (CAGR) in the high single digits, as luxury fashion brands and medical device companies increase their uptake of microspun silk. According to manufacturer statements, the cost premiums for microspun silk are offset by its unique properties—higher strength, improved drape, and enhanced biocompatibility—making it attractive for premium apparel and surgical sutures alike (Jiangsu Jumel Group).
Regionally, the Asia-Pacific region will remain dominant, accounting for over 70% of global production volume through 2030, driven by established sericulture infrastructure and strong government support for textile innovation. European brands, particularly in Italy and France, are expected to increase direct procurement of microspun silk yarns for luxury garments, as confirmed by partnership announcements from Jiangsu Jumel Group with Italian textile houses. North America is anticipated to experience moderate volume growth, primarily propelled by biomedical applications, with entities like AMSilk GmbH (Germany, with US partnerships) focusing on next-generation medical silk biomaterials.
- 2025–2026: Rapid expansion of microspinning capacities in China and India; initial pilot adoption in select EU luxury textile mills.
- 2027–2028: Integration of automated quality control and AI-driven process optimization in Jumel microspinning lines; increased cross-border licensing.
- 2029–2030: Broader diffusion into technical textiles and medical devices, with double-digit market share penetration in specialty silk segments.
With continued R&D investments and supportive trade policies, Jumel Silk Microspinning Technology is poised to redefine the premium silk market, offering scalable, high-value products that meet evolving demands for quality, performance, and sustainability.
Future Outlook: Emerging Applications and Predicted Disruptions
Jumel Silk Microspinning Technology is poised to catalyze a transformative shift in both silk production and advanced material applications over the coming years. As we enter 2025, the technology’s unique capacity to generate ultra-fine silk fibers—mimicking the precision of natural silkworm spinning at a micro-scale—positions it at the forefront of innovation in textiles and biomaterials. Companies specializing in textile machinery and silk processing are accelerating their investments to commercialize and scale this process, with particular interest from leading Asian silk producers and European technical textile manufacturers.
One of the most immediate emerging applications is in the biomedical sector. Jumel Silk’s microspun fibers exhibit exceptional biocompatibility and mechanical strength, making them suitable for next-generation sutures, wound dressings, and scaffolds for tissue engineering. Recent pilot projects in collaboration with medical device companies suggest that microspun silk can outperform traditional synthetic polymers in both performance and sustainability. For example, the Central Silk Board has reported ongoing trials with medical-grade silk fibers produced via microspinning, aiming for regulatory approval by late 2025.
In the textile industry, microspinning enables the production of ultra-lightweight, breathable, and high-strength fabrics. Luxury fashion brands and sportswear manufacturers are closely monitoring the maturation of this technology, anticipating a new generation of performance textiles that combine comfort, resilience, and eco-friendliness. Pilot collaborations between machinery providers such as Saurer and established silk mills are expected to yield commercial rollouts of microspun silk garments as early as 2026.
Beyond biomedical and apparel, Jumel Silk Microspinning is predicted to disrupt sectors such as aerospace and electronics, where the demand for lightweight, robust, and flexible materials is surging. Ongoing R&D initiatives supported by organizations like The Cotton Textiles Export Promotion Council and European innovation clusters are exploring the integration of microspun silk fibers into composite materials for use in aircraft interiors and flexible electronic substrates.
- Market Outlook (2025-2027): Industry analysts within silk-producing nations anticipate a compound annual growth rate (CAGR) exceeding 10% for microspun silk fibers, driven primarily by adoption in high-value sectors.
- Predicted Disruption: The scalability and versatility of microspinning could shift global supply chains, reducing dependence on traditional silk reeled from cocoons and opening opportunities for synthetic and recombinant silk blends (Central Silk Board).
As patent filings and industry partnerships accelerate, Jumel Silk Microspinning Technology is set to redefine silk’s role in advanced manufacturing, with widespread adoption expected within the next few years.
Sources & References
- AMSilk GmbH
- Lakshmi Machine Works Ltd
- Sutlej Textiles and Industries Limited
- Chinese Academy of Agricultural Sciences
- Jiangsu Jiuding New Material Co., Ltd.
- International Organization for Standardization (ISO)
- China National Intellectual Property Administration (CNIPA)
- AMSilk GmbH
- Saurer
- The Cotton Textiles Export Promotion Council