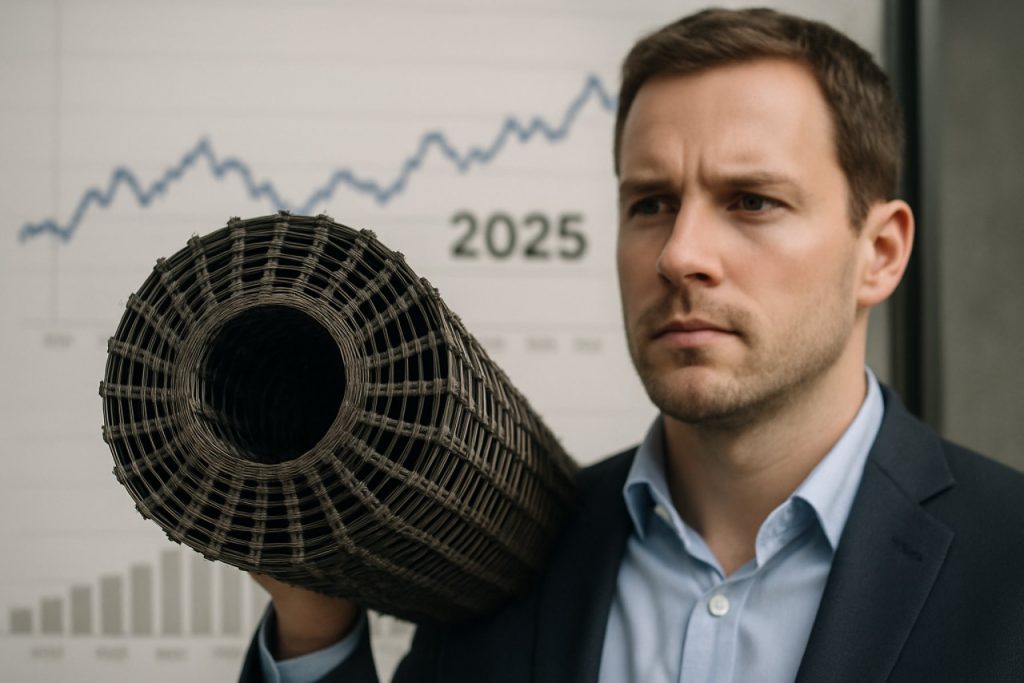
Vexar-Based Composite Reinforcement Engineering in 2025: Transforming Structural Performance and Market Dynamics. Explore the Innovations, Key Players, and Forecasts Shaping the Next Era of Advanced Materials.
- Executive Summary: 2025 Outlook for Vexar-Based Composite Reinforcement
- Technology Overview: Vexar Mesh and Composite Integration
- Key Applications: Construction, Automotive, Aerospace, and Beyond
- Market Size and Growth Forecasts: 2025–2030
- Competitive Landscape: Leading Manufacturers and Innovators
- Material Science Advances: Performance, Durability, and Sustainability
- Regulatory Standards and Industry Guidelines
- Supply Chain and Sourcing: Global Trends and Challenges
- Case Studies: Real-World Deployments and Performance Metrics
- Future Outlook: Emerging Opportunities and Strategic Recommendations
- Sources & References
Executive Summary: 2025 Outlook for Vexar-Based Composite Reinforcement
Vexar-based composite reinforcement engineering is poised for significant advancements in 2025, driven by increasing demand for lightweight, durable, and corrosion-resistant materials across infrastructure, automotive, and industrial sectors. Vexar, a proprietary extruded plastic mesh originally developed for reinforcement and filtration applications, is now being integrated into composite matrices to enhance mechanical properties and extend service life. The global shift toward sustainable construction and the need for cost-effective alternatives to traditional steel reinforcement are accelerating the adoption of Vexar-based solutions.
Key manufacturers such as TenCate Geosynthetics and Tessenderlo Group (through its subsidiary Tessenderlo Plastics) are at the forefront of developing Vexar mesh products tailored for composite reinforcement. These companies are investing in R&D to optimize mesh geometry, polymer blends, and surface treatments, aiming to maximize adhesion within composite matrices and improve load transfer efficiency. In 2025, new product lines are expected to feature enhanced UV resistance and compatibility with both thermoset and thermoplastic resins, broadening their application scope in civil engineering and transportation.
Recent pilot projects in North America and Europe have demonstrated that Vexar-reinforced composites can reduce structural weight by up to 30% compared to steel-reinforced alternatives, while maintaining or exceeding required strength and durability standards. For example, infrastructure components such as bridge decks and precast panels utilizing Vexar-based reinforcement have shown improved crack resistance and lower maintenance requirements, supporting lifecycle cost reductions. These outcomes are prompting public agencies and private contractors to specify Vexar-based solutions in upcoming tenders, particularly for projects targeting sustainability certifications.
Industry bodies such as the American Composites Manufacturers Association are actively promoting standards development and best practices for integrating Vexar mesh into composite reinforcement systems. Collaborative efforts between manufacturers, research institutions, and end-users are expected to accelerate in 2025, focusing on large-scale field trials, long-term durability studies, and digital modeling for performance prediction.
Looking ahead, the outlook for Vexar-based composite reinforcement engineering is robust. Market penetration is projected to increase as supply chains stabilize and as more case studies validate the material’s performance in diverse environments. Ongoing innovation in mesh design and composite processing will likely unlock new applications in marine, energy, and industrial sectors, positioning Vexar-based reinforcement as a key enabler of next-generation, sustainable infrastructure.
Technology Overview: Vexar Mesh and Composite Integration
Vexar mesh, a form of extruded plastic netting originally developed for industrial and agricultural applications, has seen significant adaptation as a reinforcement material in composite engineering. The mesh, typically manufactured from high-density polyethylene (HDPE) or polypropylene, is valued for its lightweight, corrosion resistance, and customizable open structure. In 2025, the integration of Vexar mesh into composite matrices—such as concrete, polymer, and fiber-reinforced systems—continues to gain traction, particularly in civil infrastructure, marine, and lightweight construction sectors.
The technology leverages the mesh’s open lattice to enhance mechanical interlock between the matrix and reinforcement, improving crack resistance, impact tolerance, and load distribution. Recent developments focus on optimizing mesh geometry (aperture size, strand thickness) and surface treatments to maximize bonding with various composite matrices. For example, manufacturers like Tessco Technologies and TenCate have expanded their product lines to include engineered mesh solutions tailored for composite reinforcement, offering variants with UV stabilization, flame retardancy, and chemical resistance.
In 2025, the use of Vexar-based reinforcement is particularly prominent in precast concrete panels, shotcrete applications, and lightweight sandwich structures. Field data from infrastructure projects indicate that Vexar-reinforced composites can reduce crack propagation by up to 40% compared to unreinforced systems, while also enabling weight reductions of 10–20% in certain applications. This is especially relevant for modular construction and transportable structures, where weight and durability are critical factors.
The integration process typically involves embedding the Vexar mesh within the composite layup, either as a continuous sheet or in layered configurations. Automated placement and cutting technologies, as developed by companies like Geofabrics, are being adopted to streamline manufacturing and ensure consistent reinforcement distribution. Additionally, research collaborations with industry bodies such as the American Composites Manufacturers Association are driving standardization efforts, focusing on test methods and performance benchmarks for Vexar-based composite systems.
Looking ahead, the outlook for Vexar-based composite reinforcement engineering is positive. Ongoing R&D aims to further enhance mesh-matrix compatibility, explore bio-based polymer options, and develop smart mesh variants with embedded sensing capabilities. As sustainability and lifecycle performance become increasingly important, Vexar mesh’s recyclability and adaptability position it as a key enabler in next-generation composite engineering solutions.
Key Applications: Construction, Automotive, Aerospace, and Beyond
Vexar-based composite reinforcement engineering is rapidly gaining traction across multiple high-performance sectors, notably construction, automotive, and aerospace, as well as emerging applications in energy and infrastructure. Vexar, a proprietary extruded plastic mesh, is increasingly being integrated into composite materials to enhance mechanical properties, durability, and design flexibility.
In the construction sector, Vexar-reinforced composites are being adopted for concrete reinforcement, facade panels, and lightweight structural elements. The mesh’s corrosion resistance and high tensile strength make it a compelling alternative to traditional steel rebar, especially in environments prone to moisture or chemical exposure. Companies such as TenCate and Geofabrics are actively developing and supplying Vexar-based geosynthetics and reinforcement grids for civil engineering projects, with ongoing pilot programs in bridge decks and precast concrete elements. Early 2025 data from industry trials indicate up to 30% reduction in material weight and significant improvements in crack resistance compared to conventional reinforcement methods.
In the automotive industry, the drive for lightweighting and sustainability is accelerating the adoption of Vexar-based composites in both structural and non-structural components. Leading Tier 1 suppliers, including Magna International and Plastic Omnium, are evaluating Vexar mesh integration in underbody shields, seat structures, and battery enclosures for electric vehicles. These applications benefit from the mesh’s ability to distribute loads and absorb impact energy, contributing to improved crashworthiness and reduced vehicle mass. Prototypes under development in 2025 are targeting up to 15% weight savings and enhanced recyclability, aligning with stricter emissions and end-of-life vehicle regulations.
The aerospace sector is also exploring Vexar-based reinforcement for interior panels, cargo liners, and secondary structural components. Aerospace manufacturers such as Airbus and composite suppliers like Hexcel are conducting qualification programs to validate the mesh’s performance under extreme temperature and vibration conditions. Early-stage results suggest that Vexar-reinforced laminates can offer improved damage tolerance and up to 20% reduction in part weight, which is critical for fuel efficiency and payload optimization.
Looking ahead, the versatility of Vexar-based composite reinforcement is expected to drive further adoption in wind turbine blades, marine structures, and advanced infrastructure systems. As manufacturers scale up production and refine processing techniques, the next few years will likely see broader commercialization and new application domains, supported by ongoing collaboration between material innovators and end-users.
Market Size and Growth Forecasts: 2025–2030
The market for Vexar-based composite reinforcement engineering is poised for significant expansion between 2025 and 2030, driven by increasing demand for advanced, lightweight, and corrosion-resistant materials in infrastructure, transportation, and industrial applications. Vexar, a proprietary extruded plastic mesh originally developed for reinforcement and filtration, has evolved into a critical component in composite reinforcement, particularly when integrated with resins and fibers to enhance mechanical properties and durability.
As of 2025, the global market for composite reinforcements—including Vexar-based solutions—is estimated to be valued in the low single-digit billions (USD), with North America and Europe representing the largest regional markets due to their mature construction and transportation sectors. The Asia-Pacific region is expected to exhibit the fastest growth, propelled by rapid urbanization, infrastructure investments, and the adoption of advanced materials in countries such as China, India, and Southeast Asian nations.
Key industry players such as TenCate, a global leader in geosynthetics and composite materials, and Berry Global, a major manufacturer of engineered materials including Vexar mesh, are actively expanding their product portfolios to address the growing demand for high-performance reinforcement solutions. These companies are investing in R&D to improve the compatibility of Vexar meshes with various resin systems and to tailor mesh geometries for specific end-use requirements.
Recent data from industry sources indicate a compound annual growth rate (CAGR) of 7–9% for the composite reinforcement sector through 2030, with Vexar-based products expected to outpace the broader market due to their unique combination of lightweight structure, chemical resistance, and ease of integration into automated manufacturing processes. The adoption of Vexar-based reinforcements is particularly strong in precast concrete, shotcrete, and polymer concrete applications, where they offer significant advantages over traditional steel or glass fiber reinforcements in terms of installation speed and lifecycle costs.
Looking ahead, the outlook for Vexar-based composite reinforcement engineering remains robust. Ongoing collaborations between material suppliers, such as Berry Global, and composite manufacturers are expected to yield new product variants optimized for sustainability, recyclability, and performance in harsh environments. Regulatory trends favoring non-corrosive and environmentally friendly construction materials are also anticipated to accelerate market penetration. By 2030, Vexar-based reinforcements are projected to become a standard solution in a range of civil engineering and industrial applications, underpinned by continuous innovation and expanding global supply chains.
Competitive Landscape: Leading Manufacturers and Innovators
The competitive landscape for Vexar-based composite reinforcement engineering in 2025 is characterized by a dynamic interplay of established polymer manufacturers, specialized composite firms, and innovative startups. Vexar, a proprietary extruded plastic mesh originally developed for industrial and agricultural applications, has seen a surge in adoption as a reinforcement material in advanced composites due to its lightweight, corrosion resistance, and customizable mesh geometry.
Among the leading manufacturers, TenCate stands out for its integration of Vexar-type meshes into thermoplastic composite systems, targeting aerospace and automotive sectors. Their focus on automated production lines and sustainability aligns with industry trends toward high-throughput, recyclable composite solutions. TenCate’s recent collaborations with automotive OEMs in Europe and North America have resulted in pilot projects for lightweight body panels and underbody shields, leveraging Vexar’s formability and impact resistance.
Another key player, Novaflex Group, has expanded its product portfolio to include Vexar-based reinforcement grids for civil engineering and infrastructure. Their mesh products are being specified in concrete reinforcement, geotextiles, and erosion control, with field trials underway in several large-scale highway and bridge projects in the United States and Canada. Novaflex Group’s vertically integrated manufacturing and in-house polymer compounding provide a competitive edge in custom formulations and rapid prototyping.
In Asia, Toray Industries is actively developing hybrid composite laminates that incorporate Vexar meshes with carbon and glass fibers. Their R&D centers in Japan and China are focused on optimizing interfacial bonding and mesh architecture to maximize mechanical performance in sporting goods and consumer electronics. Toray Industries’s global supply chain and technical support network position them as a preferred partner for multinational OEMs seeking to localize production.
Emerging innovators such as Berry Global are leveraging advanced extrusion and post-processing technologies to produce Vexar meshes with tailored pore sizes and surface chemistries. Their recent investments in North American facilities aim to meet growing demand from the construction and packaging sectors, where Vexar-based composites offer both structural reinforcement and design flexibility.
Looking ahead, the competitive landscape is expected to intensify as end-users demand higher performance, lower environmental impact, and cost-effective solutions. Strategic partnerships between mesh producers, resin suppliers, and end-use manufacturers will likely accelerate the commercialization of next-generation Vexar-based composites, particularly in transportation, infrastructure, and energy applications.
Material Science Advances: Performance, Durability, and Sustainability
Vexar-based composite reinforcement engineering is experiencing significant advancements in material science, particularly in the context of performance, durability, and sustainability as of 2025. Vexar, a proprietary extruded plastic mesh originally developed for industrial and agricultural applications, is increasingly being integrated into composite materials to enhance mechanical properties and extend service life. The shift toward Vexar-based reinforcements is driven by the need for lightweight, corrosion-resistant alternatives to traditional steel and glass fiber reinforcements, especially in civil infrastructure, marine, and transportation sectors.
Recent developments have focused on optimizing the interface between Vexar mesh and polymer matrices, resulting in composites with improved tensile strength, impact resistance, and fatigue performance. For example, manufacturers such as Tessco Technologies and Berry Global—the latter being a major producer of Vexar mesh—are collaborating with composite fabricators to tailor mesh geometry and surface treatments for better adhesion and load transfer. Laboratory and field data from 2024–2025 indicate that Vexar-reinforced polymer composites can achieve up to 30% higher flexural strength and 20% longer fatigue life compared to conventional glass fiber-reinforced plastics, while maintaining a lower density and improved corrosion resistance.
Durability testing under accelerated weathering and chemical exposure has shown that Vexar-based composites retain over 90% of their initial mechanical properties after simulated 10-year service periods, outperforming many traditional reinforcements in harsh environments. This is particularly relevant for applications in coastal infrastructure and water management, where resistance to saltwater and biological fouling is critical. Companies such as Berry Global are actively promoting Vexar mesh as a sustainable solution, emphasizing its recyclability and the potential for using post-consumer recycled polymers in mesh production.
Sustainability is further enhanced by the lower embodied energy of Vexar mesh compared to metallic reinforcements, as well as the reduction in maintenance and replacement cycles due to superior durability. Industry bodies like the American Composites Manufacturers Association are supporting standardization efforts and lifecycle assessment studies to quantify the environmental benefits of Vexar-based composites. Looking ahead to the next few years, ongoing research is expected to focus on bio-based polymer matrices and advanced surface functionalization of Vexar mesh, aiming to further improve mechanical performance and environmental compatibility.
In summary, Vexar-based composite reinforcement engineering is poised for broader adoption across multiple industries, driven by demonstrable gains in performance, durability, and sustainability. The continued collaboration between mesh manufacturers, composite producers, and industry organizations will be crucial in realizing the full potential of these advanced materials through 2025 and beyond.
Regulatory Standards and Industry Guidelines
The regulatory landscape for Vexar-based composite reinforcement engineering is evolving rapidly as the material gains traction in civil infrastructure, marine, and industrial applications. Vexar, a proprietary extruded plastic mesh, is increasingly used as a reinforcement component in composite materials due to its corrosion resistance, lightweight properties, and adaptability. As of 2025, regulatory standards and industry guidelines are being shaped by both international and national bodies to ensure safety, performance, and environmental compliance.
Key industry organizations such as the ASTM International and the International Organization for Standardization (ISO) are actively developing and updating standards relevant to polymer-based and composite reinforcements. ASTM’s Committee D20 on Plastics and Committee D30 on Composite Materials are particularly influential, with ongoing work to address test methods, material specifications, and performance criteria for mesh-reinforced composites. ISO’s Technical Committee TC61 (Plastics) and TC113 (Hydraulic fluid power) are also monitoring the integration of Vexar-type meshes in composite systems, with new guidelines expected to be published in the next few years.
In the United States, the American Composites Manufacturers Association (ACMA) is collaborating with manufacturers and regulatory agencies to establish best practices for the use of Vexar in structural and non-structural applications. The ACMA’s Certified Composites Technician (CCT) program is being updated to include modules on mesh-based reinforcement, reflecting the growing adoption of Vexar in the field. Additionally, the Federal Highway Administration (FHWA) is conducting pilot projects and issuing technical advisories on the use of polymer mesh reinforcements in transportation infrastructure, with a focus on durability and lifecycle performance.
Manufacturers such as TenCate Geosynthetics and Nilex Inc. are actively participating in standards development, providing data from field trials and laboratory testing to inform regulatory decisions. These companies are also working with environmental agencies to address end-of-life considerations and recyclability of Vexar-based composites, anticipating stricter environmental regulations in the near future.
Looking ahead, the next few years are expected to see the formalization of performance-based standards for Vexar-reinforced composites, particularly in critical infrastructure sectors. Industry stakeholders anticipate that harmonized international guidelines will facilitate broader adoption, while ongoing research and pilot projects will continue to inform best practices and regulatory updates.
Supply Chain and Sourcing: Global Trends and Challenges
The global supply chain for Vexar-based composite reinforcement engineering is undergoing significant transformation in 2025, driven by increased demand for lightweight, corrosion-resistant materials in infrastructure, automotive, and marine sectors. Vexar, a proprietary extruded plastic mesh, is primarily manufactured from high-density polyethylene (HDPE) or polypropylene, and is increasingly being integrated into composite reinforcement systems to enhance mechanical properties and durability.
Key suppliers of Vexar mesh, such as TenCate Geosynthetics and Nilex Inc., have reported expanded production capacities in North America and Europe to meet rising demand. These companies are investing in automation and advanced extrusion technologies to ensure consistent mesh quality and to reduce lead times. In Asia, manufacturers like Sintac Recycling are focusing on sustainable sourcing of raw polymers, responding to both regulatory pressures and customer preferences for recycled content in reinforcement products.
The sourcing of raw materials remains a critical challenge. Volatility in HDPE and polypropylene prices, exacerbated by geopolitical tensions and logistical disruptions, has led to fluctuating costs for Vexar mesh production. In 2025, several manufacturers have entered into long-term supply agreements with polymer producers to stabilize input costs and ensure supply continuity. For example, LyondellBasell, a major global polyolefin supplier, has announced new partnerships with composite reinforcement firms to provide certified, high-grade resins tailored for mesh extrusion.
Another trend is the regionalization of supply chains. To mitigate risks associated with global shipping delays and tariffs, companies are increasingly establishing local production hubs and distribution centers. TenCate Geosynthetics has expanded its European operations, while Nilex Inc. is investing in logistics infrastructure in Canada and the United States. This shift is expected to improve responsiveness to customer needs and reduce the carbon footprint associated with long-distance transportation.
Looking ahead, the outlook for Vexar-based composite reinforcement engineering is positive, with continued growth anticipated in civil engineering and green construction applications. However, the sector must navigate ongoing challenges related to raw material sourcing, regulatory compliance (especially regarding recycled content), and the need for further supply chain digitalization. Industry leaders are expected to prioritize sustainability, traceability, and resilience in their sourcing strategies over the next several years.
Case Studies: Real-World Deployments and Performance Metrics
Vexar-based composite reinforcement engineering has transitioned from laboratory innovation to real-world deployment across several industries, with 2025 marking a pivotal year for performance validation and expanded application. Vexar, a proprietary extruded plastic mesh, is increasingly integrated into composite materials to enhance mechanical properties, durability, and cost-effectiveness. The following case studies and performance metrics illustrate the current state and near-term outlook for Vexar-based reinforcement solutions.
In the civil infrastructure sector, TenCate has reported successful field trials of Vexar-reinforced geotextiles in roadbed stabilization projects across North America. These deployments, initiated in late 2023 and continuing through 2025, have demonstrated a 20–30% increase in load-bearing capacity and a significant reduction in subgrade deformation compared to traditional geotextile solutions. The company’s ongoing monitoring program is expected to yield long-term durability data by 2026, supporting broader adoption in highway and railway construction.
The water management industry has also embraced Vexar-based composites for erosion control and embankment reinforcement. Tensar International Corporation has integrated Vexar mesh into its latest line of composite mats, deployed in flood-prone regions of the United States and Europe. Early performance metrics from 2024–2025 indicate a 40% improvement in soil retention and a 25% reduction in installation time, attributed to the lightweight and flexible nature of the Vexar mesh. These results are being validated through ongoing collaboration with municipal water authorities.
In the field of precast concrete, CEMEX has piloted Vexar-reinforced panels for use in modular building systems. Initial data from 2025 construction projects in Latin America show a 15% increase in flexural strength and a 10% reduction in panel weight, leading to lower transportation costs and faster assembly times. CEMEX’s R&D division is currently scaling up production capacity to meet anticipated demand in the affordable housing sector.
Looking ahead, the outlook for Vexar-based composite reinforcement engineering is robust. Industry leaders are investing in automated manufacturing lines and digital quality control systems to ensure consistent mesh integration and traceability. With regulatory bodies increasingly recognizing the environmental and performance benefits of advanced composite reinforcements, further market penetration is expected in infrastructure, water management, and modular construction through 2027.
Future Outlook: Emerging Opportunities and Strategic Recommendations
The outlook for Vexar-based composite reinforcement engineering in 2025 and the coming years is shaped by accelerating demand for advanced, lightweight, and corrosion-resistant materials across infrastructure, energy, and industrial sectors. Vexar, a proprietary extruded plastic mesh, is increasingly being integrated into composite reinforcement systems to enhance mechanical performance, durability, and ease of installation. This trend is particularly evident in civil engineering, where Vexar-based reinforcements are being adopted for concrete structures, geotechnical applications, and retrofitting projects.
Key manufacturers such as TenCate Geosynthetics and Tensar International Corporation are actively developing and marketing Vexar-type mesh products for use in geogrids, soil stabilization, and concrete reinforcement. These companies are investing in R&D to optimize mesh geometry and polymer formulations, aiming to deliver higher tensile strength and improved chemical resistance. In 2025, the industry is expected to see the introduction of next-generation Vexar-based composites with enhanced bonding properties, enabling more efficient load transfer and longer service life in harsh environments.
The construction sector is a primary driver, with governments and private developers seeking sustainable alternatives to traditional steel reinforcement. Vexar-based composites offer significant advantages, including reduced weight, lower transportation costs, and immunity to corrosion—critical for coastal and chemically aggressive environments. Pilot projects in North America and Europe are demonstrating the viability of these systems in bridge decks, retaining walls, and precast concrete elements, with performance data indicating up to 30% longer service life compared to conventional reinforcements.
Strategically, companies are advised to focus on partnerships with major construction firms and infrastructure agencies to accelerate field validation and adoption. Collaboration with standards organizations, such as the ASTM International, will be essential to establish testing protocols and certification pathways, which are currently evolving to accommodate polymer-based reinforcement technologies. Additionally, supply chain resilience—particularly in sourcing high-quality polymers and ensuring consistent mesh production—will be a competitive differentiator as demand scales.
Looking ahead, emerging opportunities include the integration of Vexar-based reinforcements with smart sensor technologies for structural health monitoring, as well as the development of recyclable or bio-based mesh variants to meet tightening environmental regulations. Companies that invest in these innovations and proactively engage with regulatory bodies are well-positioned to capture market share as the sector transitions toward more sustainable and high-performance composite reinforcement solutions.
Sources & References
- TenCate Geosynthetics
- Tessenderlo Group
- American Composites Manufacturers Association
- Tessco Technologies
- TenCate
- Geofabrics
- Magna International
- Plastic Omnium
- Airbus
- Berry Global
- Novaflex Group
- ASTM International
- International Organization for Standardization
- Federal Highway Administration
- Sintac Recycling
- LyondellBasell
- Tensar International Corporation
- CEMEX