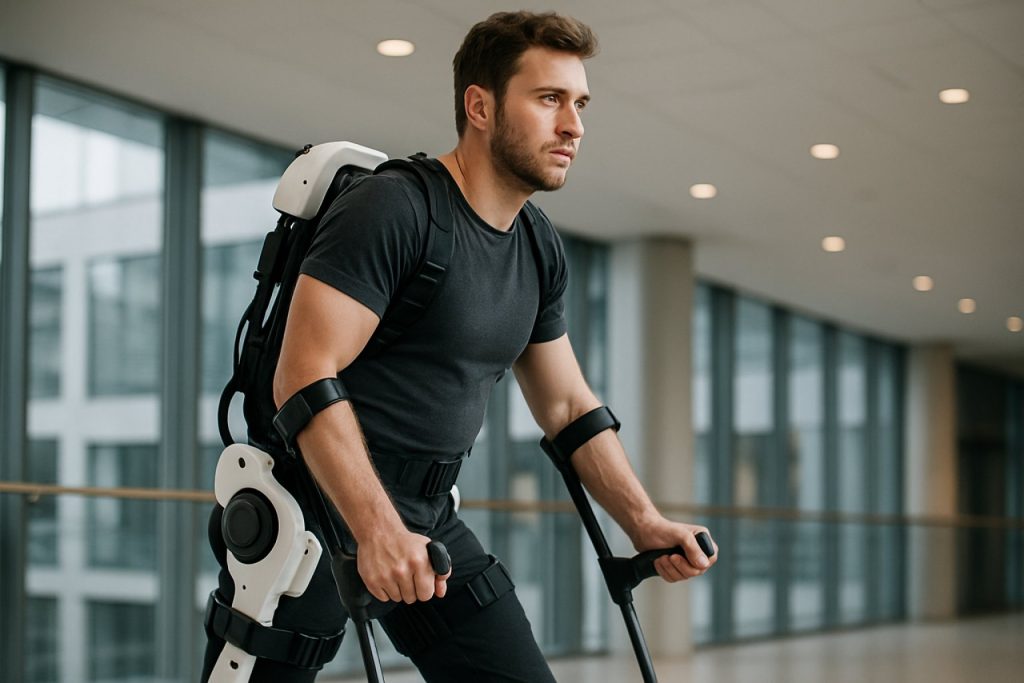
Revolutionizing Human Augmentation: The 2025 Outlook for Wearable Exoskeleton Actuators. Explore How Advanced Actuation is Driving a Projected 30% Market Growth and Transforming Mobility, Industry, and Healthcare.
- Executive Summary: Key Trends and 2025 Market Snapshot
- Market Size, Growth Rate, and Forecasts Through 2030
- Core Actuator Technologies: Electric, Hydraulic, Pneumatic, and Emerging Innovations
- Leading Players and Strategic Partnerships (e.g., suitx.com, rewalk.com, eksoBionics.com)
- Industrial, Medical, and Military Applications: Use Cases and Adoption Drivers
- Regulatory Landscape and Industry Standards (e.g., ieee.org, asme.org)
- Supply Chain, Materials, and Manufacturing Advances
- Challenges: Power Efficiency, Weight, and User Comfort
- Investment, M&A, and Funding Trends in Exoskeleton Actuation
- Future Outlook: Next-Gen Actuators, AI Integration, and Market Opportunities
- Sources & References
Executive Summary: Key Trends and 2025 Market Snapshot
The wearable exoskeleton actuator market is poised for significant growth and technological advancement in 2025, driven by increasing demand across medical rehabilitation, industrial ergonomics, and defense applications. Actuators—core components that enable movement in exoskeletons—are seeing rapid innovation, with a focus on improving power-to-weight ratios, energy efficiency, and user comfort. The sector is characterized by a shift from traditional electric motors to more advanced solutions such as compact hydraulic, pneumatic, and soft actuators, each tailored for specific use cases.
Key industry players are accelerating development and commercialization efforts. SUITX, now part of Ottobock, continues to refine its modular exoskeletons for industrial and medical use, leveraging lightweight electric actuators for enhanced mobility and reduced fatigue. Sarcos Technology and Robotics Corporation is advancing its Guardian XO full-body exoskeleton, which utilizes a combination of high-torque electric actuators and proprietary control systems to support heavy-lifting tasks in manufacturing and logistics. CYBERDYNE Inc. remains a leader in medical exoskeletons, with its HAL (Hybrid Assistive Limb) system employing bioelectrical signal-driven actuators to assist patients with mobility impairments.
In 2025, the market is witnessing a surge in collaborative projects between exoskeleton manufacturers and actuator specialists. Festo, renowned for its expertise in pneumatic and soft robotics, is partnering with wearable robotics firms to integrate lightweight, compliant actuators that mimic natural muscle movement, improving safety and adaptability. Meanwhile, ReWalk Robotics is focusing on refining its electric actuator technology to deliver smoother gait assistance for spinal cord injury patients.
Data from industry sources indicate that actuator miniaturization and battery efficiency are top priorities, as these directly impact exoskeleton usability and market adoption. The integration of smart sensors and AI-driven control algorithms is also becoming standard, enabling actuators to respond more intuitively to user intent and environmental changes. This trend is expected to accelerate as companies like Lockheed Martin and Honda Motor Co., Ltd. invest in next-generation actuator platforms for both civilian and defense exoskeletons.
Looking ahead, the outlook for wearable exoskeleton actuators in 2025 and beyond is robust. The convergence of advanced materials, energy-dense batteries, and intelligent actuation is set to expand the range of applications and drive broader adoption. As regulatory pathways clarify and costs decrease, exoskeletons equipped with state-of-the-art actuators are expected to become increasingly prevalent in healthcare, industry, and public safety sectors worldwide.
Market Size, Growth Rate, and Forecasts Through 2030
The global market for wearable exoskeleton actuators is poised for robust growth through 2030, driven by increasing demand in medical rehabilitation, industrial ergonomics, and defense applications. As of 2025, the sector is witnessing accelerated adoption, particularly in North America, Europe, and parts of Asia-Pacific, where aging populations and workforce safety concerns are prominent. The market size for wearable exoskeletons—including actuator components—is estimated to be in the low single-digit billions (USD), with actuators representing a significant share due to their critical role in device performance and cost.
Key industry players such as ReWalk Robotics, Ekso Bionics, and SuitX (now part of Ottobock) are expanding their portfolios with advanced actuator technologies, including electric motors, hydraulics, and pneumatic systems. These companies are investing in lighter, more energy-efficient actuators to improve user comfort and extend battery life, which are critical factors for widespread adoption. For example, Ekso Bionics has focused on modular actuator designs that can be tailored for both medical and industrial exoskeletons, while ReWalk Robotics continues to refine its powered hip and knee actuators for rehabilitation devices.
Growth rates for the wearable exoskeleton actuator segment are projected to exceed 15% CAGR through 2030, outpacing the broader exoskeleton market due to ongoing innovation in actuator miniaturization, power density, and control algorithms. The industrial sector is expected to be a major driver, as companies seek to reduce workplace injuries and enhance productivity with assistive exoskeletons. Ottobock and Ekso Bionics are actively collaborating with automotive and logistics firms to deploy actuator-powered exosuits for lifting and repetitive tasks.
Looking ahead, the next few years will likely see further integration of smart sensors and AI-driven control systems with actuator modules, enabling more adaptive and intuitive exoskeletons. The entry of new players and cross-industry partnerships is expected to intensify competition and accelerate technological advancements. As regulatory frameworks mature and reimbursement pathways expand, especially in healthcare, the addressable market for wearable exoskeleton actuators is set to broaden significantly by 2030.
Core Actuator Technologies: Electric, Hydraulic, Pneumatic, and Emerging Innovations
Wearable exoskeleton actuators are at the heart of the rapid evolution in assistive and augmentative robotics, with 2025 marking a period of significant technological refinement and market expansion. The core actuator technologies—electric, hydraulic, and pneumatic—each offer distinct advantages and are being actively developed and deployed by leading industry players, while emerging innovations are beginning to reshape the landscape.
Electric actuators remain the dominant force in wearable exoskeletons, prized for their compactness, controllability, and energy efficiency. Companies such as SuitX (now part of Ottobock), Ottobock, and CYBERDYNE have commercialized electric-powered exoskeletons for both medical rehabilitation and industrial support. These systems typically use brushless DC motors paired with sophisticated control algorithms to deliver precise, responsive assistance. In 2025, ongoing improvements in battery energy density and motor miniaturization are enabling lighter, more ergonomic designs, with several companies reporting reductions in system weight by 10–20% compared to models from just a few years prior.
Hydraulic actuators are favored in applications demanding high force output, such as military or heavy industrial exoskeletons. Sarcos Technology and Robotics Corporation continues to advance its Guardian XO exoskeleton, which leverages a proprietary hydraulic system to enable users to lift and manipulate heavy loads with minimal effort. Recent developments focus on improving the efficiency and reliability of compact hydraulic pumps and valves, as well as integrating advanced safety features to ensure user protection. However, challenges remain in reducing the bulk and noise associated with hydraulic systems, which limits their adoption in some wearable scenarios.
Pneumatic actuators, while less common, are gaining traction due to their inherent compliance and safety. Soft robotics companies such as SuitX and research-driven startups are exploring pneumatic artificial muscles (PAMs) and other air-powered mechanisms for lightweight, flexible exosuits. These actuators are particularly well-suited for rehabilitation and assistive devices, where gentle, adaptive support is required. Advances in compact air compressors and smart pressure control are expected to make pneumatic systems more practical for daily use by 2025 and beyond.
Emerging innovations include the integration of shape memory alloys, electroactive polymers, and magnetorheological fluids as actuator materials. While still largely in the research or early commercialization phase, these technologies promise to deliver actuators that are lighter, quieter, and more biomimetic. Companies like CYBERDYNE are actively investigating hybrid actuator systems that combine electric and novel smart materials to optimize performance.
Looking ahead, the next few years are expected to see further convergence of actuator technologies, with modular, multi-modal systems offering tailored solutions for diverse user needs. The focus will remain on improving power-to-weight ratios, user comfort, and intuitive control, as exoskeletons transition from niche applications to broader adoption in healthcare, industry, and personal mobility.
Leading Players and Strategic Partnerships (e.g., suitx.com, rewalk.com, eksoBionics.com)
The wearable exoskeleton actuator market in 2025 is characterized by a dynamic landscape of established leaders, emerging innovators, and a growing web of strategic partnerships. These collaborations are accelerating the development and deployment of advanced actuator technologies, which are central to the performance, safety, and adaptability of wearable exoskeletons across medical, industrial, and military domains.
Among the most prominent players, Ekso Bionics continues to be a global leader, leveraging over a decade of experience in powered exoskeletons for rehabilitation and industrial applications. Their actuators, primarily based on electric motors with sophisticated control algorithms, are designed for both lower and upper limb support. In 2024 and 2025, Ekso Bionics has expanded its partnerships with rehabilitation centers and industrial safety organizations, aiming to refine actuator responsiveness and energy efficiency for longer operational periods.
Another key innovator, ReWalk Robotics, focuses on wearable exoskeletons for individuals with lower limb disabilities. Their systems employ a combination of high-torque electric actuators and advanced sensor arrays to enable natural gait patterns. In recent years, ReWalk has entered into strategic agreements with healthcare providers and insurance companies to broaden access to their devices, while also collaborating with actuator component suppliers to reduce device weight and improve battery life.
The acquisition of SuitX by Ottobock in late 2021 has further consolidated expertise in actuator design. Ottobock, a longstanding leader in prosthetics and orthotics, has integrated SuitX’s modular exoskeleton technology into its portfolio, focusing on lightweight, modular actuators that can be tailored for both industrial and medical use. This synergy is expected to yield new actuator architectures with improved adaptability and user comfort in the coming years.
Other notable players include Sarcos Technology and Robotics, which is advancing industrial exoskeletons with high-power actuators for heavy lifting, and Hocoma, specializing in rehabilitation robotics with precise, low-noise actuators for clinical environments. These companies are increasingly engaging in cross-sector partnerships, such as with automotive manufacturers and logistics firms, to pilot exoskeletons in real-world settings and gather data for actuator optimization.
Looking ahead, the next few years are expected to see intensified collaboration between actuator manufacturers, exoskeleton developers, and end-user organizations. The focus will be on miniaturization, energy efficiency, and the integration of smart materials, with the goal of making wearable exoskeleton actuators more affordable, reliable, and widely adopted across sectors.
Industrial, Medical, and Military Applications: Use Cases and Adoption Drivers
Wearable exoskeleton actuators are increasingly shaping the landscape of industrial, medical, and military sectors as of 2025, driven by advances in robotics, materials science, and sensor integration. These actuators—ranging from electric motors to pneumatic and hydraulic systems—are the core components enabling exoskeletons to augment human strength, endurance, and precision.
In industrial settings, exoskeletons equipped with robust actuators are being adopted to reduce worker fatigue and injury, particularly in logistics, manufacturing, and construction. Companies such as Ottobock and SuitX (now part of Ottobock) have developed powered exoskeletons that support lifting and repetitive tasks, with actuators designed for high duty cycles and reliability. Sarcos Technology and Robotics Corporation is another key player, offering the Guardian XO, a full-body, battery-powered exoskeleton with advanced actuators that enable users to lift up to 200 pounds repeatedly without strain. These systems are being piloted and deployed in automotive assembly lines and warehouses, with adoption driven by the need to address labor shortages and comply with stricter occupational safety regulations.
In the medical field, exoskeleton actuators are central to rehabilitation and mobility assistance devices. Ekso Bionics and ReWalk Robotics are prominent manufacturers whose powered exoskeletons use precise actuators to assist patients with spinal cord injuries or stroke in regaining mobility. These devices are increasingly being integrated into hospital rehabilitation programs, with clinical studies demonstrating improved patient outcomes and reduced therapy times. The trend toward lighter, more responsive actuators—such as brushless DC motors and soft actuators—continues, enabling more natural gait patterns and user comfort.
Military applications are also advancing, with organizations like Lockheed Martin developing exoskeletons for soldier load carriage and endurance enhancement. Their ONYX exoskeleton, for example, uses a suite of actuators and sensors to support knee joints, reducing fatigue during long marches or heavy lifting. The U.S. Department of Defense and allied agencies are investing in next-generation actuator technologies that balance power, weight, and energy efficiency, aiming for field-ready systems by the late 2020s.
Looking ahead, the adoption of wearable exoskeleton actuators across these sectors is expected to accelerate, propelled by ongoing improvements in actuator miniaturization, battery life, and AI-driven control systems. As costs decrease and performance improves, exoskeletons are poised to become standard equipment in high-risk, high-demand environments, fundamentally transforming human capability and workplace safety.
Regulatory Landscape and Industry Standards (e.g., ieee.org, asme.org)
The regulatory landscape and industry standards for wearable exoskeleton actuators are rapidly evolving as these devices transition from research prototypes to commercial products in medical, industrial, and military sectors. As of 2025, the focus is on harmonizing safety, performance, and interoperability requirements to support widespread adoption and user trust.
A cornerstone in this domain is the work of the IEEE, which has developed the IEEE 802.1 Standard for Exoskeletons and Exosuits. This standard, first introduced in 2022 and updated through 2024, outlines definitions, performance metrics, and safety protocols for both powered and passive exoskeleton actuators. It addresses critical aspects such as actuator response time, fail-safe mechanisms, and user-initiated emergency stops. The IEEE standard is increasingly referenced by manufacturers and regulatory bodies as a baseline for product certification and market entry.
In parallel, the American Society of Mechanical Engineers (ASME) has advanced its own set of guidelines, focusing on the mechanical integrity and reliability of wearable exoskeleton actuators. ASME’s standards, particularly those related to actuator load testing, fatigue life, and human-machine interface safety, are being adopted by leading exoskeleton developers to ensure compliance with both U.S. and international regulations. These standards are also influencing procurement requirements for industrial and healthcare buyers.
On the regulatory front, the U.S. Food and Drug Administration (FDA) continues to play a pivotal role in the medical exoskeleton sector. Devices intended for rehabilitation or mobility assistance must comply with FDA’s Class II medical device requirements, which include rigorous testing of actuator reliability, electrical safety, and biocompatibility. The FDA’s Breakthrough Devices Program has accelerated the review of several exoskeleton systems, reflecting the agency’s recognition of their potential to address unmet medical needs.
Globally, the International Organization for Standardization (ISO) is finalizing the ISO 13482 standard, which covers safety requirements for personal care robots, including wearable exoskeletons. This standard is expected to be widely adopted in the European Union and Asia-Pacific markets by 2026, further aligning international regulatory expectations.
Looking ahead, industry stakeholders anticipate increased convergence between IEEE, ASME, and ISO standards, driven by cross-sector collaboration and the growing presence of multinational exoskeleton manufacturers. This harmonization is expected to streamline certification processes, reduce market entry barriers, and foster innovation in actuator technologies, ultimately accelerating the safe and effective deployment of wearable exoskeletons worldwide.
Supply Chain, Materials, and Manufacturing Advances
The supply chain and manufacturing landscape for wearable exoskeleton actuators is undergoing significant transformation as the sector matures and demand diversifies across medical, industrial, and defense applications. In 2025, the focus is on scaling up production, improving actuator efficiency, and securing robust supply chains for critical materials and components.
Key actuator technologies in wearable exoskeletons include electric motors, pneumatic and hydraulic systems, and emerging soft actuators. Electric actuators, particularly brushless DC motors, remain dominant due to their compactness, controllability, and energy efficiency. Companies such as Ottobock and SuitX (now part of Ottobock) have integrated advanced electric actuators into their medical and industrial exoskeletons, focusing on lightweight materials and modular designs to streamline assembly and maintenance. Sarcos Technology and Robotics Corporation continues to refine its industrial exoskeletons with proprietary actuator systems designed for high payload and endurance, leveraging in-house manufacturing and strategic supplier partnerships to mitigate component shortages.
Material innovation is central to actuator advancement. The adoption of high-strength, lightweight alloys (such as titanium and advanced aluminum composites) and engineered polymers is reducing actuator weight while maintaining durability. CYBERDYNE Inc. utilizes proprietary actuator modules in its HAL exoskeletons, combining custom electronics with advanced materials to optimize power-to-weight ratios. Meanwhile, soft robotics companies are exploring electroactive polymers and textile-based actuators, aiming for greater flexibility and user comfort, though these remain in early-stage commercialization.
Supply chain resilience is a top priority in 2025, with manufacturers diversifying sources for rare earth magnets, precision gears, and electronic components. The global semiconductor situation continues to impact actuator controller availability, prompting companies to invest in long-term supplier agreements and, in some cases, vertical integration. Lockheed Martin Corporation and Panasonic Corporation are notable for their efforts to localize critical actuator component production, reducing lead times and exposure to geopolitical risks.
Manufacturing advances include increased automation, additive manufacturing for custom actuator parts, and digital twins for rapid prototyping and quality assurance. These approaches are enabling faster iteration cycles and more reliable actuator performance. Looking ahead, the sector is expected to see further integration of smart materials and embedded sensors, with a focus on sustainability and recyclability of actuator components as regulatory and customer expectations evolve.
Challenges: Power Efficiency, Weight, and User Comfort
Wearable exoskeleton actuators are at the heart of powered exoskeleton systems, directly influencing their efficiency, weight, and user comfort. As of 2025, the sector faces persistent challenges in balancing these factors, with ongoing innovation and incremental improvements shaping the outlook for the next several years.
Power efficiency remains a primary concern. Most exoskeletons rely on electric motors, hydraulic systems, or pneumatic actuators, each with inherent trade-offs. Electric actuators, favored for their controllability and compactness, are limited by battery energy density, which constrains operational time and increases the need for frequent recharging or battery swaps. Leading manufacturers such as SUITX (now part of Ottobock), CYBERDYNE, and ReWalk Robotics have focused on optimizing actuator efficiency and integrating regenerative braking to recapture energy during movement. However, even with these advances, most commercial exoskeletons offer only 4–8 hours of continuous use, which can be insufficient for industrial or clinical applications.
Weight is another critical challenge. Actuators and their associated power supplies contribute significantly to the overall mass of exoskeletons, directly impacting user fatigue and long-term wearability. Companies like Ottobock and Sarcos Technology and Robotics Corporation are investing in lightweight materials such as carbon fiber composites and advanced alloys to reduce system weight. Additionally, the miniaturization of actuator components and the development of soft actuators—such as those explored by SUITX and CYBERDYNE—are promising approaches to further decrease bulk without sacrificing performance.
User comfort is closely tied to both actuator design and system ergonomics. Rigid actuators can create pressure points and restrict natural movement, leading to discomfort or even injury over extended use. To address this, companies are refining actuator placement, improving harness designs, and incorporating adaptive control algorithms that synchronize actuator output with the user’s intent and biomechanics. For example, CYBERDYNE’s HAL exoskeleton uses bioelectrical signal detection to provide more intuitive and responsive assistance, while Ottobock emphasizes modularity and adjustability in its exoskeletons to accommodate a wider range of body types and movement patterns.
Looking ahead, the next few years are expected to bring incremental but meaningful improvements in actuator efficiency, weight reduction, and user-centered design. Advances in battery technology, soft robotics, and AI-driven control systems are likely to further mitigate current limitations, making wearable exoskeletons more practical for daily use in medical, industrial, and military settings.
Investment, M&A, and Funding Trends in Exoskeleton Actuation
The wearable exoskeleton actuator sector is experiencing robust investment and consolidation activity as of 2025, driven by the convergence of robotics, healthcare, and industrial automation. The global push for workforce augmentation, rehabilitation solutions, and aging population support has attracted both strategic investors and venture capital to companies developing advanced actuation technologies.
Key players in the exoskeleton actuator market, such as SuitX (now part of Ottobock), Sarcos Technology and Robotics Corporation, and ReWalk Robotics, have been at the center of recent funding rounds and acquisition activity. Ottobock’s acquisition of SuitX in late 2021 set a precedent for cross-sector M&A, combining medical device expertise with industrial exoskeleton innovation. This trend has continued, with established medical device manufacturers and robotics firms seeking to expand their portfolios through targeted acquisitions of actuator technology specialists.
In 2024 and into 2025, venture capital investment has remained strong, particularly for startups focusing on lightweight, energy-efficient actuators and AI-driven control systems. Companies like Sarcos Technology and Robotics Corporation have secured additional funding to accelerate commercialization of their Guardian XO and Guardian XT exoskeletons, which rely on proprietary actuator systems for heavy-duty industrial applications. Similarly, ReWalk Robotics has attracted new investment to advance its soft exosuit actuator technology for rehabilitation and mobility assistance.
Strategic partnerships are also shaping the funding landscape. For example, Ottobock has entered collaborations with automotive and logistics companies to pilot exoskeletons in workplace settings, often with co-investment from industry partners. These alliances are expected to drive further capital inflows as pilot programs transition to scaled deployments.
Looking ahead, the outlook for investment and M&A in exoskeleton actuators remains positive. The sector is anticipated to see continued inflows from both healthcare and industrial automation investors, with a focus on companies that can demonstrate scalable actuator solutions and integration with digital health platforms. As regulatory pathways for wearable robotics become clearer and reimbursement models evolve, additional funding is likely to target companies with proven clinical and commercial traction.
- Major exoskeleton actuator companies are attracting both strategic and venture capital investment.
- M&A activity is consolidating expertise across medical, industrial, and robotics domains.
- Strategic partnerships with end-user industries are catalyzing new funding rounds.
- Outlook for 2025 and beyond is strong, with emphasis on scalable, efficient actuator technologies.
Future Outlook: Next-Gen Actuators, AI Integration, and Market Opportunities
The future of wearable exoskeleton actuators is poised for significant transformation as the industry enters 2025 and looks ahead to the latter part of the decade. The convergence of advanced actuator technologies, artificial intelligence (AI), and expanding market applications is driving both innovation and commercial adoption.
A key trend is the shift from traditional electric motors to more compact, lightweight, and energy-efficient actuators. Companies such as SUITX (now part of Ottobock), Ottobock, and CYBERDYNE are actively developing exoskeletons that utilize brushless DC motors, high-torque actuators, and, increasingly, soft actuators based on pneumatic or hydraulic systems. These innovations aim to improve user comfort, reduce device weight, and extend battery life—critical factors for both industrial and medical exoskeletons.
AI integration is another major driver shaping the next generation of exoskeleton actuators. Real-time sensor data, combined with machine learning algorithms, enables adaptive control systems that can predict user intent and adjust actuator output accordingly. Sarcos Technology and Robotics Corporation and ReWalk Robotics are among the companies investing in AI-driven control architectures, which are expected to enhance safety, responsiveness, and personalization for users in both rehabilitation and workplace settings.
The market outlook for wearable exoskeleton actuators is robust, with demand expanding beyond healthcare and rehabilitation into logistics, manufacturing, and defense. Lockheed Martin continues to advance powered exoskeletons for military applications, focusing on actuators that deliver high power-to-weight ratios and rugged reliability. Meanwhile, Honda and Panasonic are exploring actuator solutions for assistive devices aimed at aging populations and workers in physically demanding roles.
- By 2025, expect to see broader adoption of soft actuators and hybrid systems that combine electric and pneumatic technologies for improved ergonomics.
- AI-powered exoskeletons will increasingly feature cloud connectivity, enabling remote diagnostics and performance optimization.
- Collaborations between actuator manufacturers and exoskeleton developers are likely to accelerate, with companies such as Festo and SMC Corporation providing advanced actuation components tailored for wearable robotics.
As actuator technologies mature and AI integration deepens, the next few years will likely see wearable exoskeletons become more accessible, versatile, and effective across a range of industries, unlocking new market opportunities and improving quality of life for users worldwide.
Sources & References
- SUITX
- Sarcos Technology and Robotics Corporation
- CYBERDYNE Inc.
- ReWalk Robotics
- Lockheed Martin
- Ekso Bionics
- Ekso Bionics
- Hocoma
- IEEE
- American Society of Mechanical Engineers (ASME)
- ISO
- SMC Corporation