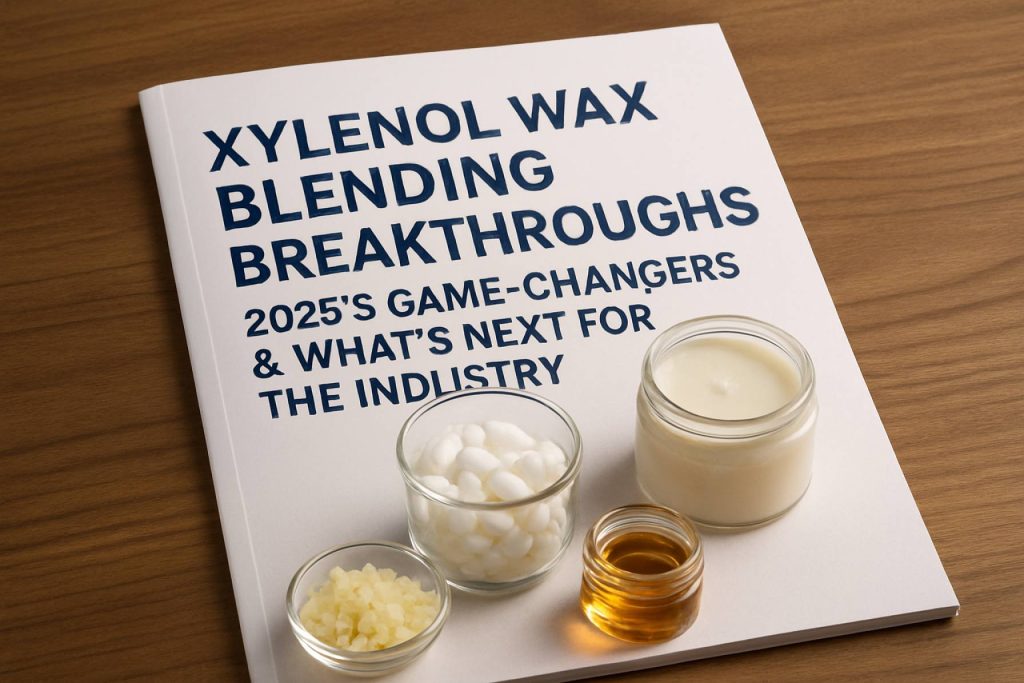
Table of Contents
- Executive Summary: Key Findings & Industry Outlook (2025–2030)
- Xylenol Wax Chemistry: Fundamentals and Recent Advancements
- Global Market Size, Segmentation, and Forecasts Through 2030
- Innovative Blending Technologies: Automation, Sustainability, and Efficiency
- Major Industry Players: Profiles, Strategies, and Official Insights
- Supply Chain Dynamics and Raw Material Trends
- Emerging Applications in Automotive, Electronics, and Healthcare
- Regulatory Landscape: Safety, Environmental, and Compliance Updates
- Investment Trends, M&A, and Partnership Highlights
- Future Opportunities: Growth Drivers, Challenges, and Roadmap for 2025–2030
- Sources & References
Executive Summary: Key Findings & Industry Outlook (2025–2030)
Xylenol wax blending technologies are positioned at the intersection of specialty chemical manufacturing and advanced materials science, addressing evolving demands for performance, sustainability, and process efficiency. The period from 2025 onward is marked by significant advancements in formulation techniques, raw material sourcing, and automation—factors driving both market expansion and industry transformation.
Key industry players are leveraging proprietary blending processes to enhance the compatibility and performance of xylenol-based waxes in applications ranging from electrical insulation and lubricants to high-value coatings. Companies such as Evonik Industries and Eastman Chemical Company have reported ongoing investments in R&D to tailor xylenol wax blends for improved thermal stability, reduced volatility, and increased biodegradability, aligning with stricter environmental regulations taking effect in 2025 and beyond.
Recent patent filings and product launches indicate a shift towards automation and in-line process monitoring, enabling tighter control over blend homogeneity and traceability. The adoption of digital twin technologies and AI-driven optimization is expected to become standard practice by 2027, as noted by innovation initiatives at ExxonMobil Chemical. These digital advances not only reduce production costs but also facilitate rapid formulation adjustments to meet client-specific needs in emerging sectors such as 5G electronics and advanced composites.
From a supply chain perspective, the xylenol wax market remains sensitive to feedstock availability, particularly phenolic intermediates derived from petrochemical operations. To mitigate volatility and ensure sustainability, manufacturers are exploring bio-based alternatives and circular economy models, as highlighted in the sustainability programs of Sasol and Shell. These initiatives are expected to gain momentum through 2030, driven by both consumer demand and regulatory mandates.
In summary, the 2025–2030 outlook for xylenol wax blending technologies is characterized by increased specialization, digital integration, and a strong orientation toward sustainable solutions. Market participants who invest in advanced blending systems, feedstock diversification, and end-use innovation are likely to secure competitive advantage in this evolving landscape.
Xylenol Wax Chemistry: Fundamentals and Recent Advancements
Xylenol waxes, synthesized from alkylated phenols such as 2,4-xylenol, have traditionally served as specialty additives in applications ranging from electrical insulation to thermal transfer media. The chemistry underlying their unique blend of hydrophobicity, melting range, and chemical stability has made them attractive for custom wax formulations. As of 2025, technological advancements in blending processes are driving both the efficiency and functional diversity of xylenol wax products.
Recent years have seen the adoption of advanced blending technologies, including precision-controlled batch and continuous blending systems, to tailor the physical and chemical properties of xylenol waxes. Modern blending units, equipped with real-time viscosity and temperature monitoring, enable the production of waxes with highly consistent melt points and improved compatibility with other resins, paraffins, and specialty additives. For instance, companies such as Sasol and Mitsui Chemicals have reported investments in automated blending lines that facilitate precise addition of xylenol derivatives to paraffinic and microcrystalline wax matrices, targeting applications in electronics encapsulation and high-performance coatings.
A key focus in 2025 is the integration of eco-friendly blending protocols. This includes the use of solvent-free or low-solvent processes, which help minimize emissions and improve worker safety. Sasol has recently launched initiatives to optimize blending temperatures and shear rates, reducing energy consumption while maintaining homogeneity in xylenol wax blends. Furthermore, advances in in-line analytical control—such as near-infrared (NIR) spectroscopy—are enabling real-time adjustment of blend ratios, resulting in tighter specification control and reduced batch rework.
The outlook for the next few years indicates further expansion of functionalized xylenol wax blends, particularly those engineered for thermal management and specialty lubrication. The ongoing development of hybrid wax systems, combining xylenol waxes with biodegradable or bio-based materials, is expected to create new market opportunities, especially in light of tightening environmental regulations worldwide. Companies like Mitsui Chemicals are actively exploring co-blending and co-polymerization routes to enhance both sustainability and performance.
Overall, xylenol wax blending technologies in 2025 are characterized by a push for greater process control, environmental responsibility, and value-added functionality—trends likely to accelerate as end-use industries demand more specialized and sustainable wax solutions.
Global Market Size, Segmentation, and Forecasts Through 2030
The global market for xylenol wax blending technologies is undergoing notable transformation as the demand for high-performance specialty waxes accelerates across industries such as automotive, packaging, and electronics. As of 2025, the market is characterized by increasing adoption of advanced blending processes, integration of automation, and a heightened focus on sustainability.
Market segmentation reveals that Asia-Pacific continues to dominate both production and consumption, driven by expanding manufacturing bases in China, India, and Southeast Asia. Global leaders such as Evonik Industries and Sasol are investing in upgrading their blending facilities, leveraging in-house process innovations to improve efficiency and product consistency. In North America and Europe, environmental regulations are prompting a shift toward blended waxes with reduced volatile organic compound (VOC) emissions, creating opportunities for niche xylenol wax blends tailored for eco-friendly applications.
- By Application: The largest segment remains industrial coatings, where blended xylenol waxes enhance scratch resistance and gloss. Other significant segments include adhesives, specialty lubricants, and thermal transfer materials.
- By Technology: There is a clear trend toward continuous blending systems with real-time quality monitoring. Companies like Michelman are incorporating digital process controls to ensure batch consistency and traceability.
- By Geography: While Asia-Pacific leads in capacity, North American and European players are focusing on specialty and custom blends for high-margin sectors.
Recent data from industry suppliers indicate that the global xylenol wax blending technologies market reached an estimated $420 million in 2024. Projections through 2030 suggest a compound annual growth rate (CAGR) of 5–6%, driven by increased use in high-end electronics encapsulation and sustainable packaging solutions. Leading manufacturers, including Clariant and BASF, are expanding their portfolios to include blends with bio-based xylenol derivatives, anticipating future regulatory and consumer preferences.
Outlook for the next few years indicates further consolidation among technology suppliers and vertical integration by major wax producers. Strategic partnerships, especially in Asia, are expected to facilitate technology transfer and accelerate the adoption of advanced blending methods. The ongoing push for sustainability and regulatory compliance is likely to shape both product development and market dynamics in the xylenol wax blending technology sector through 2030.
Innovative Blending Technologies: Automation, Sustainability, and Efficiency
The landscape of xylenol wax blending technologies is rapidly evolving in 2025, shaped by advancements in automation, sustainability, and production efficiency. Xylenol waxes, known for their unique chemical stability and lubricating properties, are increasingly in demand for coatings, electronics, and specialty manufacturing applications. This surge has prompted manufacturers to invest in innovative blending systems that optimize both process control and environmental impact.
Automation is at the forefront of these innovations. Leading producers are deploying fully integrated, sensor-driven blending lines that ensure precise mixing ratios and real-time adjustment of process parameters. For instance, Sasol has implemented digital process control in its specialty wax operations, allowing for tighter quality control and reduced human error. Such automation not only enhances product consistency but also enables rapid scaling to meet fluctuating market demands.
Sustainability is another critical driver in 2025, with the industry responding to regulatory and consumer pressures to reduce carbon footprints and improve resource efficiency. Companies like IGS Europe are pioneering the use of renewable feedstocks and closed-loop solvent recovery systems in their wax blending facilities. These approaches minimize waste generation and energy consumption, aligning with global sustainability targets while securing long-term supply chain resilience.
Efficiency improvements are being accelerated by the adoption of modular blending technology, which allows manufacturers to tailor production lines for specific xylenol wax formulations. Firms such as Shell are investing in modular reactor systems that can be quickly reconfigured for different product grades, significantly reducing downtime and enabling faster product development cycles. Additionally, energy-efficient heating and mixing technologies are being integrated, further optimizing the overall process.
Looking ahead, the next several years are expected to bring further integration of artificial intelligence and machine learning within blending operations. These technologies will enable predictive maintenance, advanced process optimization, and adaptive quality control, as indicated by ongoing pilot projects at Evonik Industries. As these systems mature, they are poised to deliver significant gains in throughput, energy savings, and traceability.
In summary, 2025 marks a period of significant technological transformation for xylenol wax blending. Automation, sustainability initiatives, and modular process design are setting new benchmarks in productivity and environmental stewardship, with further advancements anticipated as digitalization deepens across the sector.
Major Industry Players: Profiles, Strategies, and Official Insights
The landscape of xylenol wax blending technologies in 2025 is shaped by a select group of chemical manufacturers and specialty wax producers who have demonstrated advanced capabilities in blending, purification, and customization of xylenol-based waxes. These players are leveraging proprietary processes, automation, and sustainability-focused strategies to maintain competitiveness and meet evolving client demands in coatings, electronics, and specialty manufacturing.
- Evonik Industries AG: As a global leader in specialty chemicals, Evonik continues to invest in process innovation for wax blending. In 2025, the company is expanding its modular blending units to improve the consistency and scalability of xylenol wax formulations, targeting the electronics and advanced coatings sectors. Their integrated production sites in Europe and Asia focus on reducing volatile organic compound (VOC) emissions and improving supply chain traceability through digitalization.
- Sasol Limited: Sasol maintains a robust portfolio of waxes and intermediates, with ongoing R&D in custom xylenol wax blends. The company’s 2025 strategy emphasizes enhanced blending automation and a shift toward bio-based xylenol derivatives to align with global regulatory trends and customer sustainability targets. Sasol’s technical data sheets and application support services are tailored to facilitate rapid product development cycles for clients in adhesives and electrical insulation.
- Mitsui Chemicals, Inc.: Mitsui Chemicals leverages its deep expertise in functional materials, offering a range of xylenol waxes with precise molecular weight control and thermal stability. The company’s 2025 initiatives include the integration of AI-driven process monitoring at its Japanese blending facilities, aiming to optimize batch consistency and anticipate maintenance needs. Mitsui’s collaborations with downstream electronics manufacturers allow for co-development of tailored wax blends for high-reliability applications.
- Clariant AG: Clariant’s waxes business unit is advancing solvent-free blending technologies for xylenol waxes, with pilot implementations underway in Germany and China. In 2025, Clariant is focused on scaling up these processes to minimize environmental impact and enhance product purity. The company also invests in technical partnerships to expand its xylenol wax portfolio for use in automotive and precision casting industries.
Looking ahead, these industry leaders are expected to deepen their investments in sustainable feedstocks, digitalized process control, and end-use customization. The convergence of regulatory pressure and client-driven innovation is likely to accelerate the adoption of advanced blending technologies, positioning these firms at the forefront of the xylenol wax sector through 2028 and beyond.
Supply Chain Dynamics and Raw Material Trends
The supply chain dynamics and raw material trends for xylenol wax blending technologies are in a period of significant adaptation as the industry responds to evolving regulatory requirements, sustainability pressures, and global economic shifts. Xylenol waxes, valued for their chemical resistance and thermal stability, are primarily synthesized from petrochemical feedstocks, such as phenolic derivatives and xylenols, often sourced from major chemical producers. In 2025, the availability and pricing of these base chemicals continue to be influenced by fluctuations in crude oil prices and by downstream disruptions from geopolitical events and trade policy changes.
Major players in the supply of xylenols and related phenolic intermediates, such as Sasol and SABIC, have reported ongoing adjustments to production capacities and logistics networks to navigate supply uncertainties. In particular, the tightness in global phenol supply, due to both planned maintenance and unplanned outages at large petrochemical facilities, has had a cascading effect on the cost and availability of specialty xylenol waxes. This has prompted downstream wax blenders to secure long-term contracts and diversify sourcing, increasingly looking toward suppliers in Asia-Pacific to hedge against regional volatility.
Sustainability trends are also shaping the procurement and blending strategies of xylenol wax producers. Companies such as Baker Hughes and Clariant are investing in the integration of circular feedstocks and renewable phenolic inputs, responding to customer demand for lower carbon footprint materials. These innovations are in early adoption stages, with pilot projects exploring the use of bio-based xylenols derived from lignocellulosic biomass, which could potentially reduce dependence on fossil-derived chemicals over the next several years.
On the logistics front, the blending and transportation of xylenol waxes require specialized handling due to the materials’ sensitivity and regulatory classification. Emerging digital supply chain technologies, including blockchain-based track-and-trace platforms and real-time inventory monitoring, are being piloted by leading chemical distributors such as Brenntag to enhance transparency and reduce the risk of supply disruptions.
Looking ahead, the outlook for xylenol wax blending technologies through 2025 and beyond will depend on the successful balancing of raw material supply security, cost control, and the integration of sustainable inputs. Industry participants are expected to deepen supplier partnerships, invest in alternative sourcing, and accelerate adoption of digital tools to maintain resilience amid ongoing market volatility.
Emerging Applications in Automotive, Electronics, and Healthcare
In 2025, xylenol wax blending technologies are experiencing significant advances, particularly as industries seek customized material solutions with improved thermal, chemical, and mechanical properties. Three sectors—automotive, electronics, and healthcare—are at the forefront of adopting innovative xylenol wax blends, leveraging their unique characteristics for emerging applications.
In the automotive industry, manufacturers are increasingly utilizing xylenol wax blends as performance-enhancing additives in coatings, sealants, and lubricants. These blends offer superior thermal stability and resistance to harsh environments, making them ideal for high-performance engine and underbody components. Companies such as Sasol have developed advanced wax blending processes that enable precise control over molecular structure, enhancing compatibility with polymers commonly used in automotive manufacturing. In 2025, collaborative projects between material suppliers and OEMs are focusing on integrating xylenol-based waxes into lightweight composite materials, aiming to reduce vehicle weight and improve fuel efficiency.
Within the electronics sector, the demand for miniaturized and reliable components is driving the adoption of xylenol wax blends in insulation, encapsulation, and thermal management applications. The high electrical resistivity and customizable melting points of these blends support the protection of delicate microelectronic assemblies. Mitsui Chemicals and other specialty chemical companies are refining catalytic blending technologies to tailor wax purity and crystallinity, meeting stringent industry requirements for dielectric stability and low outgassing. In 2025 and the coming years, further research is underway to extend the use of xylenol waxes in next-generation flexible electronics and printed circuit boards.
Healthcare is another area seeing rapid growth in the application of xylenol wax blends. The materials are being adopted for medical device coatings, drug delivery matrices, and controlled-release formulations due to their biocompatibility and chemical inertness. Brenntag, a global distributor of specialty chemicals, has reported increased demand from pharmaceutical and medical device manufacturers for tailored xylenol wax blends that meet regulatory and performance standards. In 2025, developments are focusing on solvent-free blending technologies that minimize extractables and leachables, critical for patient safety and regulatory compliance.
Looking ahead, the outlook for xylenol wax blending technologies across these industries is robust. Ongoing improvements in process automation, analytical quality control, and sustainable sourcing are expected to yield new grades and formulations. As end-user requirements evolve, collaboration between chemical producers, OEMs, and research institutes will continue to drive innovation and application breadth for xylenol wax blends through at least the remainder of the decade.
Regulatory Landscape: Safety, Environmental, and Compliance Updates
The regulatory landscape for xylenol wax blending technologies continues to evolve in 2025, primarily driven by tightening safety, environmental, and product compliance standards globally. Xylenol waxes, synthesized from various methylphenols, are valued in industrial applications for their thermal stability and chemical resistance. However, the handling and blending processes for these materials are increasingly scrutinized given their volatile organic compound (VOC) content and potential health risks.
In the United States, the U.S. Environmental Protection Agency (EPA) has maintained strict VOC emission standards under the Clean Air Act, requiring facilities involved in xylenol wax production and blending to implement advanced emissions controls and monitoring. The EPA’s Risk Management Program (RMP) has also been updated to reflect new accident prevention requirements, emphasizing process hazard analysis and emergency response planning for facilities handling hazardous chemicals, including xylenols.
Meanwhile, the European Union is enforcing the Registration, Evaluation, Authorisation and Restriction of Chemicals (REACH) regulations, compelling manufacturers and importers of xylenol-based waxes to provide comprehensive data on chemical safety and environmental impact. Companies such as Brenntag and KLK OLEO are responding by updating their Safety Data Sheets (SDS) and investing in greener blending technologies to ensure compliance. Notably, the EU’s push for sustainable chemistry has encouraged the adoption of low-VOC and bio-based alternatives in wax blending processes.
In Asia, regulatory standards are also tightening. For example, China’s Ministry of Ecology and Environment has expanded the list of priority hazardous chemicals, with new guidelines for emissions and workplace exposure limits. Companies like Sinopec are adapting their operations to comply with these evolving standards, integrating closed-system blending and enhanced worker safety protocols.
Globally, the move towards safer and more sustainable xylenol wax blends is evident through industry initiatives such as the Responsible Care® program, coordinated by the International Council of Chemical Associations. This program encourages proactive risk management, product stewardship, and transparent reporting.
Looking forward, the regulatory outlook suggests further tightening of exposure limits, broader adoption of real-time emissions monitoring, and greater emphasis on lifecycle assessments for chemical products. Technology providers are expected to accelerate innovation in low-emission blending systems and automation, supporting both compliance and operational efficiency.
Investment Trends, M&A, and Partnership Highlights
The landscape for investment, mergers and acquisitions (M&A), and strategic partnerships in xylenol wax blending technologies has experienced notable activity in 2025, reflecting increasing demand for high-performance specialty waxes in coatings, adhesives, and electronics. Investment is being driven by both end-market growth—particularly in Asia-Pacific and North America—and by the push for sustainable, high-purity wax solutions for next-generation industrial applications.
Several leading chemical manufacturers have announced capital expenditure to expand and modernize their xylenol wax blending capabilities. Eastman Chemical Company confirmed in February 2025 the completion of process upgrades at its Kingsport, Tennessee facility, focusing on advanced blending controls and improved product consistency for specialty waxes, including xylenol-based grades. The company highlighted that this investment aligns with its broader sustainability and value-added product strategies.
Strategic partnerships are also shaping the sector’s outlook. In March 2025, Sasol entered a joint development agreement with a major electronics materials supplier to co-develop xylenol wax blends optimized for microelectronics encapsulation. This collaboration aims to leverage Sasol’s proprietary wax chemistry with the partner’s downstream compounding expertise, targeting commercial deployment within two years.
M&A activity has accelerated as companies seek to consolidate capabilities and expand portfolios. In April 2025, Mitsui Chemicals acquired a controlling stake in a Southeast Asian specialty wax blender, granting it greater access to high-growth regional markets and proprietary blending technologies for xylenol wax derivatives. Mitsui Chemicals cited the deal as part of its global strategy to strengthen its advanced materials platform and respond to evolving customer needs in electronics and automotive sectors.
Small- and mid-sized firms are also attracting investment. Honeywell Ventures announced in May 2025 a minority investment in a U.S.-based startup specializing in automated wax blending systems, with a focus on digital process optimization for xylenol and phenolic waxes. This signals growing interest in Industry 4.0 solutions to enhance efficiency and traceability.
Looking ahead, the sector is expected to see continued investment in automation, sustainability, and digitalization. Leading players are likely to form further technology-driven alliances, particularly around bio-based xylenol waxes and recycling. The outlook for 2025 and beyond suggests ongoing consolidation and innovation, as companies position themselves to meet rising technical standards and regulatory requirements in xylenol wax applications.
Future Opportunities: Growth Drivers, Challenges, and Roadmap for 2025–2030
The period from 2025 to 2030 presents significant growth opportunities and challenges for xylenol wax blending technologies, shaped by evolving industrial demands, sustainability imperatives, and advances in formulation science. The global specialty wax market, including xylenol-based blends, is poised for expansion due to increasing applications in electronics, coatings, and specialty adhesives, all of which require high-performance and customizable wax solutions. Xylenol waxes, known for their stability and thermal properties, are gaining traction as critical components in next-generation phase change materials and precision molding applications.
Key growth drivers include the ongoing push for greener and more sustainable wax blending processes. Major industry players are investing in the development of low-emission and recyclable xylenol waxes to comply with tightening environmental regulations in North America, Europe, and Asia-Pacific. For example, Sasol and Shell have both implemented R&D initiatives focused on improving the eco-profile of their specialty wax portfolios, including aromatic and phenolic derivatives. These efforts are increasingly supported by partnerships with downstream users in packaging and automotive sectors, who are demanding higher purity and more consistent product performance.
Technological advancements in blending, such as continuous processing and in-line quality monitoring, are also shaping the roadmap for the next five years. Equipment manufacturers like Bühler Group are introducing modular systems that allow for precise temperature and shear control, enabling the production of bespoke xylenol wax blends tailored to niche applications. Moreover, digitization and process automation are being integrated into wax blending lines, optimizing yield and minimizing batch variability.
Despite these opportunities, challenges persist. The availability and price volatility of raw xylenol feedstocks remain a concern, as does the need for robust handling protocols due to xylenol’s toxicity and flammability. Industry bodies such as the European Chemicals Agency are expected to introduce stricter limits on workplace exposure and emissions, prompting manufacturers to further innovate in process safety and containment.
Looking ahead, the most successful players will likely be those that combine advanced process technologies with a proactive approach to regulatory compliance and sustainability. Collaborative ventures between chemical producers, equipment suppliers, and end-users will be vital for accelerating innovation and ensuring resilience in the xylenol wax supply chain through 2030.