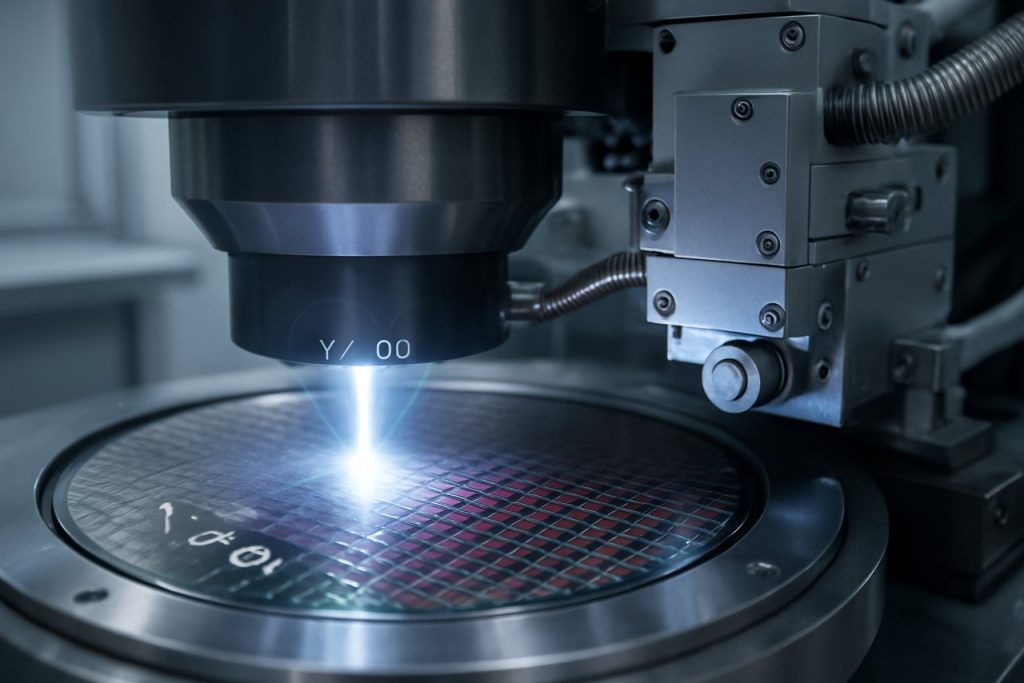
Table of Contents
- Executive Summary: Yttrium-Oxide Ion Implantation in 2025
- Technology Overview: Principles & Processes
- Key Players & Recent Partnerships (2025)
- Current Market Size and 2025 Growth Projections
- Emerging Applications in Semiconductors, Optics, and Energy
- Technology Advancements: Efficiency, Precision, and Scalability
- Competitive Landscape: Global Leaders & Innovators
- Regulatory and Environmental Considerations
- Market Forecast: 2025–2030 Trends & Opportunities
- Strategic Recommendations for Stakeholders
- Sources & References
Executive Summary: Yttrium-Oxide Ion Implantation in 2025
In 2025, yttrium-oxide (Y2O3) ion implantation technology stands as a critical enabler for next-generation microelectronics, photonics, and power devices. Yttrium-oxide’s unique dielectric and barrier characteristics are increasingly used to engineer interface properties, enhance device reliability, and improve performance at advanced process nodes. The industry’s shift toward ever-smaller geometries, such as 5 nm and below, is driving demand for precise ion implantation of functional oxides such as Y2O3—a material valued for its high-k dielectric constant, thermal stability, and resistance to moisture and oxygen diffusion.
Major semiconductor equipment manufacturers have accelerated innovation in 2024–2025 to address the technical challenges of yttrium-oxide ion implantation, including dose control, uniformity, and post-implantation annealing requirements. Advanced Micro-Fabrication Equipment Inc. (AMEC) and Applied Materials, Inc. have both expanded their portfolios of medium and high-current ion implanters capable of delivering yttrium and related oxide ions with high precision for logic, memory, and power device fabs. Similarly, ULVAC, Inc. has developed advanced beamline ion implantation systems optimized for oxide materials, targeting power semiconductors and high-frequency device markets.
Key events in 2025 include the ramp-up of yttrium-oxide ion implantation for gate dielectrics in 3D NAND and DRAM production, as well as the adoption of embedded oxide barriers in SiC and GaN power devices to address leakage and reliability issues. Leading foundries such as Taiwan Semiconductor Manufacturing Company (TSMC) and Samsung Electronics are expected to expand their use of yttrium-oxide-based processes, leveraging the material’s stability under aggressive thermal budgets and compatibility with advanced patterning techniques.
Looking ahead, the outlook for yttrium-oxide ion implantation technology is robust, with pilot lines and production ramps anticipated for logic and memory applications, as well as emerging quantum and photonic devices. Equipment manufacturers and materials suppliers are collaborating on process integration and yield improvement, with a focus on defect reduction and uniformity at the wafer level. As device architectures evolve and the demand for higher reliability and miniaturization grows, yttrium-oxide ion implantation is positioned to become a foundational process in advanced semiconductor manufacturing through 2025 and beyond.
Technology Overview: Principles & Processes
Yttrium-oxide ion implantation technology has emerged as a critical process in advanced materials science, particularly in the semiconductor, photonics, and corrosion-resistant coating sectors. At its core, this technology involves the acceleration of yttrium ions—typically in the form of Y3+—and their implantation into a target substrate. The process modifies the surface chemistry and physical properties of materials, leading to enhanced hardness, improved corrosion resistance, and tailored electronic characteristics. Yttrium oxide (Y2O3) is especially valued for its high dielectric constant, thermal stability, and optical transmittance, making it indispensable in gate dielectrics, protective coatings, and optical devices.
The principle underpinning ion implantation is the physical embedding of ions beneath the surface of a substrate through high-energy bombardment. In yttrium-oxide ion implantation, yttrium ions generated by ion sources—such as plasma or electron cyclotron resonance (ECR) sources—are accelerated in an electric field and directed at the substrate, where they penetrate to controlled depths. Subsequent oxidation (either during implantation or post-process annealing) forms stable yttrium-oxide phases within or atop the substrate. This process is highly tunable, allowing for precise control over dopant concentration, depth profile, and lateral distribution. In 2025, advances in multi-wafer ion implanters and high-current beam technologies are supporting the commercial-scale adoption of yttrium-oxide ion implantation, especially for compound semiconductor and power device fabrication.
Several global equipment manufacturers have integrated yttrium-oxide ion implantation modules into their product portfolios. For example, Axcelis Technologies and Applied Materials have developed next-generation implanters capable of handling a wide range of dopant species, including yttrium, and offer process recipes tailored for high-k dielectric and passivation layer applications. Ion Beam Services in Europe continues to expand its service capabilities, supporting R&D and pilot production for customers seeking yttrium-oxide surface modification.
The outlook for yttrium-oxide ion implantation technology in the next few years is increasingly positive. As the demand for wide-bandgap semiconductors (SiC, GaN) and robust, transparent coatings grows, the precise and scalable nature of ion implantation will be pivotal. Industry consortia, such as SEMI, are fostering collaborative development of standards and process controls, ensuring process repeatability and device reliability. Efforts are also underway to enhance implantation throughput and reduce contamination, as device feature sizes continue to shrink. Given these trends, yttrium-oxide ion implantation is poised to play a central role in next-generation microelectronics and durable optics through 2025 and beyond.
Key Players & Recent Partnerships (2025)
Yttrium-oxide ion implantation technology continues to attract significant interest as a critical enabling process for advanced semiconductor manufacturing, power electronics, and optoelectronic device fabrication. In 2025, several established and emerging players are shaping the global landscape through technological innovation, expansion of manufacturing capabilities, and targeted partnerships.
Among the leading equipment manufacturers, Applied Materials, Inc. maintains a pivotal role with its advanced ion implantation platforms, supporting integration of yttrium-oxide for next-generation transistor gate dielectrics and memory devices. The company’s recent collaborations with major foundries are focused on optimizing ion beam control for ultrathin oxide layers, an area of increasing importance as chip geometries shrink. Similarly, Axcelis Technologies, Inc. continues to expand its Purion product line, adapting its systems for precise yttrium-oxide implantation at both high and low energy ranges, crucial for tailoring interfacial properties in power semiconductors.
On the materials supply side, Umicore and American Elements are key global suppliers of high-purity yttrium oxide targets and precursor materials, ensuring a stable supply chain for device manufacturers. Their investments in refining and purification technologies in 2023–2024 have strengthened the reliability of yttrium-oxide sources, addressing concerns about material consistency in high-volume production.
Strategic partnerships have accelerated in 2025. Hitachi High-Tech Corporation has entered into a joint development agreement with a leading European semiconductor foundry to integrate in-line yttrium-oxide ion dose monitoring systems. This collaboration aims to enhance process control and traceability, a critical factor as yttrium-oxide adoption increases in 300mm and 450mm wafer fabs. Meanwhile, Tokuyama Corporation has expanded its research partnership with Japanese universities and device manufacturers, focusing on yttrium-oxide’s role in emerging gallium nitride (GaN) and silicon carbide (SiC) power devices. These partnerships support rapid prototyping and technology transfer from R&D labs to production lines.
Looking forward into 2025 and beyond, the competitive landscape is expected to intensify as more foundries and integrated device manufacturers (IDMs) invest in yttrium-oxide ion implantation capabilities. This is propelled by demand for enhanced reliability and performance in automotive, 5G, and quantum computing components—sectors where yttrium-oxide’s dielectric and passivation properties are increasingly valued.
Current Market Size and 2025 Growth Projections
Yttrium-oxide (Y2O3) ion implantation technology has become increasingly significant within advanced semiconductor and thin film manufacturing, particularly as device architectures demand improved high-k dielectrics, enhanced thermal stability, and robust barrier layers. As of 2025, the market for yttrium oxide ion implantation is characterized by both established semiconductor fabs and emerging materials companies integrating this step into production flows for next-generation logic, memory, and wide bandgap device platforms.
Leading manufacturers of ion implantation equipment, such as Axcelis Technologies and Applied Materials, report increasing customer demand for flexible implanters capable of handling specialty dopants, including rare earth metals like yttrium. This demand is driven by the scaling of gate oxides in advanced CMOS, power electronics, and the integration of yttrium oxide in ferroelectric and resistive RAM stacks, where precise doping and interface control are critical for performance and yield.
According to 2025 guidance from Axcelis Technologies, the specialty implant segment—encompassing non-traditional dopants like yttrium—continues to outpace growth rates of the broader ion implanter market. The company notes a robust order pipeline for its Purion platform, with particular traction in sectors deploying yttrium oxide for power, automotive, and RF applications. Similarly, Applied Materials highlights in its 2025 product releases a strategic focus on materials engineering, including process modules that support rare earth ion sources and advanced endpoint detection for high-precision yttrium implantation.
On the materials supply side, companies such as Advanced Technology & Materials Co., Ltd. (AT&M) and Treibacher Industrie AG have scaled up yttrium oxide production and purification lines to meet the specifications of ion implantation customers, ensuring high-purity, low-contaminant feedstocks suitable for semiconductor processing.
Looking forward into the next few years, the market outlook remains positive. With the accelerating adoption of wide bandgap semiconductors (SiC, GaN) and new non-volatile memory stacks, the need for reliable yttrium oxide ion implantation technology is projected to grow at double-digit rates globally. This growth is further propelled by ongoing investments in 300mm and 200mm fab expansions in Asia, Europe, and North America, where advanced materials engineering is a key differentiator for process nodes at and below 5nm.
Emerging Applications in Semiconductors, Optics, and Energy
Yttrium-oxide (Y2O3) ion implantation technology is poised for significant growth in 2025 and the following years, driven by its unique capabilities in modifying materials for advanced applications in semiconductors, optics, and energy systems. The demand is underpinned by the material’s exceptional chemical stability, high dielectric constant, and ability to act as a robust barrier layer or functional interface.
In semiconductor manufacturing, Y2O3 ion implantation is increasingly adopted for engineering gate dielectrics in next-generation transistors and power devices. The integration of Yttrium-oxide allows for enhanced thermal stability and improved electrical properties, crucial for scaling below 5 nm technology nodes. Industry leaders such as Applied Materials and Lam Research are actively developing and supplying advanced ion implantation systems compatible with Y2O3 precursors, addressing both yield and uniformity challenges faced by fabs in Asia and the US.
In optics, Yttrium-oxide’s high transparency in the visible and infrared spectrum makes it highly desirable for fabricating protective coatings and laser host materials. Leading optics and photonics manufacturers, including Coherent Corp., are exploring Y2O3 ion implantation to produce waveguides and thin films with precise refractive index profiles, enabling more efficient integrated photonic circuits and high-durability optical components.
The energy sector is also witnessing the early adoption of Y2O3 ion implantation, particularly in solid oxide fuel cells (SOFCs) and advanced batteries. Companies such as FuelCell Energy are investigating Yttrium-oxide’s ability to enhance electrolyte membranes’ ionic conductivity and chemical resistance, which could raise operating efficiencies and extend lifetimes for renewable energy systems.
Looking ahead, the technology is expected to benefit from further innovations in ion beam precision and process integration. Equipment vendors like Axcelis Technologies are rolling out platforms with enhanced control over implantation dose and depth, supporting materials scientists in tailoring device properties at the atomic scale. As collaborations between device manufacturers and materials suppliers intensify, the outlook for Y2O3 ion implantation is robust, with broadening adoption anticipated across electronics, photonics, and clean energy industries through 2025 and beyond.
Technology Advancements: Efficiency, Precision, and Scalability
Yttrium-oxide ion implantation technology has experienced notable advancements in efficiency, precision, and scalability as of 2025, driven by its critical role in next-generation semiconductor and advanced materials manufacturing. The deployment of yttrium-oxide ions is increasingly favored for the formation of robust dielectric layers, interface engineering, and defect passivation in wide-bandgap semiconductors and power electronic devices.
A significant trend is the integration of high-current, multi-wafer ion implanters capable of handling yttrium and oxygen species with exceptional dose control and uniformity, minimizing process-induced damage while maximizing throughput. Companies such as Axcelis Technologies have introduced advanced ion implantation platforms that offer precise beam control and real-time monitoring systems, enabling sub-nanometer depth profiles and lateral distribution accuracy critical for device miniaturization.
Recent enhancements in source technology—such as the adoption of inductively coupled plasma (ICP) sources—have improved ionization efficiency for yttrium and oxygen, delivering higher beam currents and reducing contamination risk. Advanced Micro-Fabrication Equipment Inc. (AMEC) reports the development of specialized source materials and chamber coatings tailored for aggressive oxide ion regimes, prolonging tool life and supporting stable, high-volume manufacturing.
On the process integration front, manufacturers are leveraging real-time process analytics and endpoint detection systems, which support adaptive feedback control. This enables dynamic tuning of implantation parameters to achieve target stoichiometry and defect profiles, even as wafer sizes scale to 300 mm and beyond. Automation and advanced robotics are further enhancing wafer handling efficiency and reducing variability, as highlighted by Tokyo Seimitsu in their latest ion implantation handling modules.
Scalability is also being addressed through modular system architectures, allowing fabs to tailor implantation capacity to specific production requirements. This flexibility supports the rapid adoption of yttrium-oxide processes in emerging applications such as quantum device fabrication, advanced logic, and high-reliability power electronics.
Looking forward, the outlook for yttrium-oxide ion implantation technology remains robust. The convergence of plasma source innovation, data-driven process control, and modular tool design is expected to further drive down cost-of-ownership while enabling new device architectures and higher yields. Industry leaders continue to invest in R&D to refine beam purity and extend process compatibility to novel substrate materials, ensuring that yttrium-oxide implantation remains a cornerstone technology for advanced electronics manufacturing in the coming years.
Competitive Landscape: Global Leaders & Innovators
The competitive landscape for yttrium-oxide ion implantation technology in 2025 is characterized by a small but dynamic group of global leaders and innovative entrants, each leveraging advanced expertise in materials engineering, semiconductor processes, and specialized ion implantation systems. Yttrium-oxide (Y2O3) ion implantation is increasingly critical for next-generation semiconductor devices, high-dielectric-constant (high-k) gate oxides, and robust coatings in power electronics.
Among the established leaders, Axcelis Technologies, Inc. remains at the forefront of ion implantation equipment, supplying advanced systems capable of handling yttrium and other complex dopants. Axcelis’ Purion platform, with its high beam current and precise dose control, supports the rigorous demands of research and industrial clients seeking to embed yttrium-oxide ions for enhanced device performance. The company continues to expand its global service network and has recently highlighted its support for emerging applications in wide bandgap semiconductors—an area where yttrium-oxide layers are increasingly sought after.
Another major player is Applied Materials, Inc., which integrates yttrium-oxide ion implantation into its suite of fabrication solutions for leading-edge chip manufacturing. Applied Materials is collaborating with foundries and IDMs (Integrated Device Manufacturers) to refine process recipes, particularly for logic and memory devices at sub-5 nm nodes where gate dielectric quality is paramount. Their focus includes boosting the reliability and scalability of yttrium-oxide implantation, aiming for production-readiness and yield improvements by 2026.
In Asia, ULVAC, Inc. is advancing yttrium-oxide ion implantation for both semiconductor and display applications, leveraging its expertise in vacuum and plasma technologies. ULVAC’s recent portfolio updates include systems tailored for the needs of SiC and GaN device fabrication, sectors that are projected to exhibit robust growth through 2027 due to electric vehicle and power electronics demand.
Emerging innovators include Thermo Fisher Scientific, which is supplying advanced focused ion beam (FIB) systems capable of precise yttrium-oxide implantation at the nanoscale for both R&D and prototyping. These tools are essential for rapid iteration of device structures and materials research.
Looking ahead, the competitive environment is expected to intensify as demand grows for higher-performance materials and as regional semiconductor initiatives (notably in the US, EU, Japan, and South Korea) incentivize domestic tool development. Partnerships between global equipment leaders and local foundries are likely to accelerate process optimization, particularly as the industry targets higher yields, lower defect densities, and new device architectures where yttrium-oxide plays a pivotal role.
Regulatory and Environmental Considerations
As the semiconductor and advanced materials industries increasingly adopt yttrium-oxide (Y₂O₃) ion implantation for applications such as gate dielectrics, diffusion barriers, and optoelectronic device engineering, regulatory and environmental considerations are coming to the forefront in 2025. Yttrium-oxide is generally regarded as a material of low toxicity; however, the ion implantation process involves high-energy beams and generates secondary emissions, particulate waste, and potentially hazardous byproducts that require careful management.
Regulatory frameworks governing the use of yttrium-oxide in ion implantation are shaped by broader semiconductor manufacturing standards as well as specific chemical safety guidelines. In the United States, the United States Environmental Protection Agency (EPA) and the Occupational Safety and Health Administration (OSHA) oversee permissible exposure limits for rare earth compounds and mandate engineering controls for airborne particulates and waste management. Additionally, the SEMI organization issues best practices for equipment design and process safety in ion implantation, which are being updated in 2025 to reflect the increased use of refractory oxides like Y₂O₃.
In Europe, companies must comply with REACH (Registration, Evaluation, Authorisation and Restriction of Chemicals) requirements for yttrium compounds. This includes documentation of hazards, exposure scenarios, and disposal protocols. Recent guidance from the European Chemicals Agency (ECHA) emphasizes the need for accurate registration of yttrium-oxide and updated safety data sheets as its use expands in microfabrication processes.
Waste generated during ion implantation—such as spent targets, contaminated process gases, and particulates—must be treated according to hazardous waste standards. Leading manufacturers like Applied Materials, Inc. and Axcelis Technologies, Inc. are investing in advanced abatement systems to capture and neutralize yttrium-bearing effluents, and are collaborating with regulatory bodies to establish recycling protocols for spent materials. These efforts support broader industry commitments to sustainability and circular economy practices.
Looking ahead, regulatory scrutiny is expected to intensify as yttrium-oxide implantation becomes more prevalent in next-generation device fabrication. Industry groups are working with agencies worldwide to harmonize standards, particularly around worker exposure, effluent management, and lifecycle assessment of yttrium-containing materials. Environmental monitoring and reporting requirements are likely to expand, driving ongoing investments in cleanroom technology, waste minimization, and safe handling training across the supply chain.
Market Forecast: 2025–2030 Trends & Opportunities
From 2025 onward, the market for yttrium-oxide ion implantation technology is expected to experience robust growth, driven by the increasing demand for advanced semiconductor devices, power electronics, and optoelectronic components. Yttrium oxide (Y2O3) is valued for its high thermal stability, wide bandgap, and dielectric properties, making it a sought-after material for next-generation microelectronics and photonic applications.
Key equipment manufacturers and materials suppliers are already expanding their yttrium-oxide capabilities to cater to the evolving needs of semiconductor fabrication. For example, Axcelis Technologies has highlighted the growing adoption of specialty ion implantation processes, including those utilizing rare earth oxides like yttrium, to enable more precise doping and material modification at sub-10 nm nodes. Similarly, ULVAC, Inc. is investing in advanced ion implanters tailored for high-k dielectric layers and next-generation compound semiconductors, both of which often incorporate yttrium-oxide films.
Industry forecasts suggest that the integration of yttrium-oxide via ion implantation will become increasingly critical for the fabrication of high-performance logic and memory chips, especially as manufacturers transition to gate-all-around (GAA) FET architectures and three-dimensional NAND structures. The use of yttrium-oxide in these applications is anticipated to improve device reliability, reduce leakage currents, and enable aggressive scaling, reinforcing its strategic importance between 2025 and 2030.
Furthermore, the transition towards wide bandgap semiconductors such as gallium nitride (GaN) and silicon carbide (SiC) in power electronics is expected to open new avenues for yttrium-oxide ion implantation. Companies like Cree | Wolfspeed and Infineon Technologies are actively developing GaN and SiC-based devices, which often benefit from yttrium-based interface engineering to optimize threshold voltage and electrical performance.
Looking ahead, opportunities are likely to emerge in quantum computing, advanced photonics, and the development of radiation-hardened electronics for aerospace and defense, where yttrium-oxide’s unique material properties are highly prized. Strategic partnerships between semiconductor foundries and equipment suppliers are anticipated to accelerate the adoption and optimization of yttrium-oxide ion implantation processes. As a result, the technology is poised for sustained growth, with ongoing investment in R&D and production capacity expected to continue through 2030.
Strategic Recommendations for Stakeholders
As yttrium-oxide ion implantation technology advances into 2025 and beyond, stakeholders—including semiconductor manufacturers, equipment suppliers, and materials providers—must adapt strategies to harness emerging opportunities and address evolving challenges. The following recommendations are grounded in recent industry developments and the anticipated trajectory of the technology.
- Prioritize Collaborative R&D for Process Optimization: Given the complexity of yttrium-oxide ion implantation and its role in enhancing device performance, stakeholders should invest in joint research initiatives. Leading semiconductor equipment manufacturers are already emphasizing collaborative efforts with device makers to refine implantation parameters and improve yield. For example, Applied Materials, Inc. and Lam Research Corporation have highlighted partnerships with customers to co-develop advanced process solutions tailored to next-generation devices.
- Develop Supply Chain Resilience for Yttrium-Based Materials: As the demand for yttrium-oxide rises, suppliers must ensure robust sourcing and purity standards. Companies like Alfa Aesar (a Thermo Fisher Scientific brand) and American Elements are expanding their capabilities to provide high-purity yttrium compounds essential for semiconductor applications. Stakeholders should secure long-term supply agreements and monitor geopolitical developments affecting rare earth element availability.
- Capitalize on Equipment Upgrades and Retrofit Opportunities: Implantation equipment is rapidly evolving to support finer device geometries and new materials. Equipment suppliers such as Axcelis Technologies are introducing systems optimized for high-dose, high-uniformity yttrium-oxide implantation. Device manufacturers should evaluate the cost-benefit of upgrading or retrofitting existing implanters to maintain a competitive edge.
- Align with Sustainability and Regulatory Trends: The processing of yttrium-oxide and related materials is subject to increasing environmental scrutiny. Stakeholders must proactively adopt best practices for waste management and emissions control, anticipating stricter regulations globally. Industry associations such as SEMI regularly publish guidelines and best practices that can serve as references for compliance and sustainability efforts.
- Monitor Downstream Application Growth: Yttrium-oxide ion implantation supports innovations in logic, memory, and power devices. Stakeholders should track product roadmaps of major chipmakers and emerging application segments—such as quantum computing and advanced sensors—to align R&D and production strategies with high-growth areas. Semiconductor leaders like Intel Corporation and Taiwan Semiconductor Manufacturing Company (TSMC) set trends that ripple throughout the supply ecosystem.
In summary, by fostering collaboration, enhancing supply chain robustness, investing in advanced equipment, prioritizing sustainability, and aligning with evolving application demands, stakeholders can position themselves for sustained success in the yttrium-oxide ion implantation technology landscape through 2025 and the coming years.
Sources & References
- Advanced Micro-Fabrication Equipment Inc. (AMEC)
- ULVAC, Inc.
- Axcelis Technologies
- Applied Materials, Inc.
- Umicore
- American Elements
- Hitachi High-Tech Corporation
- Tokuyama Corporation
- Treibacher Industrie AG
- Coherent Corp.
- FuelCell Energy
- ULVAC, Inc.
- Thermo Fisher Scientific
- REACH
- European Chemicals Agency
- Cree | Wolfspeed
- Infineon Technologies
- Alfa Aesar (a Thermo Fisher Scientific brand)