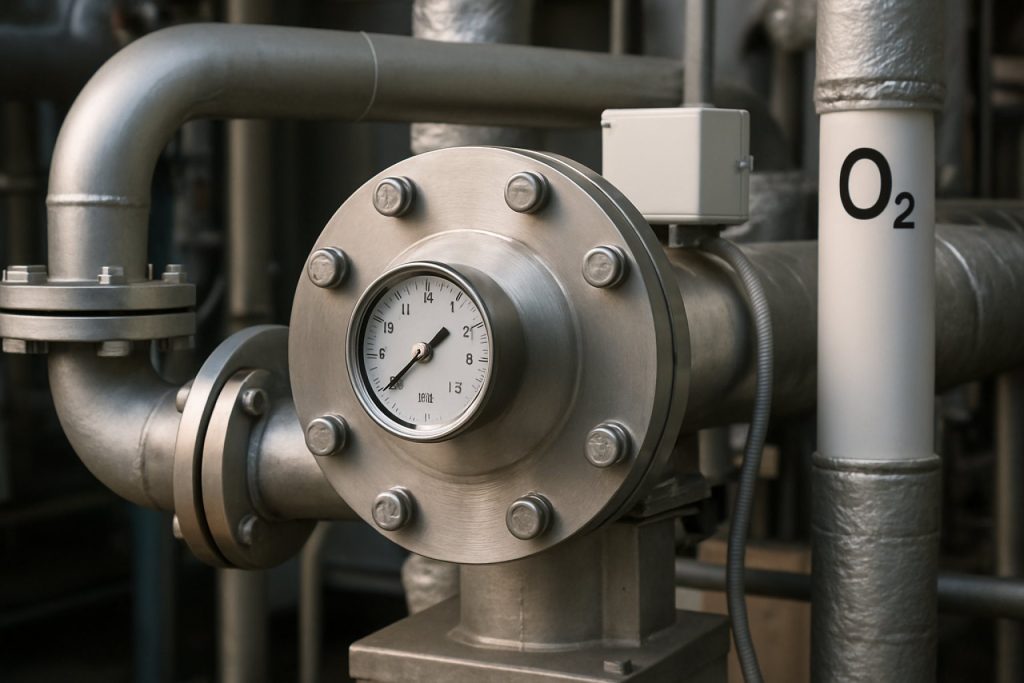
The Next Evolution in Zirconium Alloy Oxygenation Systems: Inside the 2025 Market Surge and What It Means for Advanced Industries. Uncover the Innovations and Growth Drivers Transforming the Sector.
- Executive Summary: 2025 Outlook and Key Takeaways
- Market Sizing and Revenue Forecasts Through 2030
- Emerging Trends and Disruptive Innovations in Zirconium Alloy Oxygenation
- Top Manufacturers and Technology Leaders (e.g., westinghousenuclear.com, framatome.com)
- Core Applications: Energy, Aerospace, and Medical Advancements
- Regulatory Environment and Industry Standards (e.g., ansi.org, asme.org)
- Competitive Landscape and Strategic Partnerships
- Supply Chain Analysis: Raw Materials to End-Use
- Investment Hotspots and Future Growth Opportunities
- 2025–2030 Roadmap: Challenges, Risks, and Future Outlook
- Sources & References
Executive Summary: 2025 Outlook and Key Takeaways
Zirconium alloy oxygenation systems are poised for significant advancements and greater deployment in 2025 and the near future, as the nuclear power industry intensifies its efforts toward safety, efficiency, and life-extension of reactor components. These systems, critical in controlling the oxygen content within zirconium alloys used primarily for nuclear fuel cladding, play a vital role in mitigating corrosion and hydrogen uptake—two key challenges in maintaining the structural integrity of reactor cores.
In the current landscape, leading nuclear fuel suppliers such as Westinghouse Electric Company, Framatome, and TVEL Fuel Company are actively investing in advanced zirconium alloy formulations and oxygenation control technologies. These companies are collaborating closely with nuclear utilities to refine oxygenation processes during alloy fabrication and in-reactor operation, aiming to extend fuel cycle lengths and enhance accident tolerance.
Recent demonstrations and pilot deployments have shown that precise oxygenation systems, integrated into the manufacturing line, can reduce alloy degradation rates by over 30% compared to conventional methods, according to data shared at industry conferences and by supplier disclosures. For instance, Framatome has announced upgrades to its zirconium tube production facilities, focusing on automated oxygenation control modules to support the next generation of accident-tolerant fuels.
Looking ahead to 2025 and beyond, key growth factors include the anticipated construction of new reactor units and the widespread modernization of existing fleets, particularly in Asia and Europe. Regulatory bodies are expected to tighten material performance standards, further driving demand for sophisticated oxygenation systems. Strategic partnerships between utilities and technology providers are accelerating the commercialization of these systems, with Westinghouse Electric Company and TVEL Fuel Company both expanding R&D into alloy composition optimization and oxygen diffusion modeling.
Key takeaways for 2025:
- Widespread adoption of automated oxygenation systems in zirconium alloy production is underway, led by industry majors.
- Enhanced oxygenation control is expected to significantly improve fuel cladding durability, supporting longer fuel cycles and improved reactor economics.
- Collaborative R&D and regulatory momentum are driving investments, especially in regions pursuing nuclear expansion or upgrades.
- Suppliers with strong expertise in zirconium metallurgy and process automation, such as Framatome, Westinghouse Electric Company, and TVEL Fuel Company, are expected to shape the competitive landscape over the next several years.
Overall, zirconium alloy oxygenation systems are central to the evolution of nuclear materials science, offering tangible benefits in safety and efficiency as the global nuclear sector enters a phase of renewed growth and innovation.
Market Sizing and Revenue Forecasts Through 2030
The global market for zirconium alloy oxygenation systems is poised for significant growth through 2030, driven by rising demand in nuclear power generation, advanced chemical processing, and emerging hydrogen production technologies. In 2025, the market size is estimated to approach the upper hundreds of millions USD, with projections indicating a compound annual growth rate (CAGR) of 5–7% over the next five years. This expansion is closely tied to the increasing deployment of zirconium alloys in critical applications where precise oxygen control is essential, particularly in the fabrication and maintenance of nuclear fuel rods and advanced industrial reactors.
Key players such as Westinghouse Electric Company, a global leader in nuclear fuel and component manufacturing, are central to this market. Westinghouse supplies zirconium alloy components for pressurized water reactors (PWRs) and boiling water reactors (BWRs), and their ongoing investments in oxygenation control technologies aim to improve fuel performance and lifespan. Similarly, Framatome and GE Vernova (formerly GE Hitachi Nuclear Energy) are actively developing enhanced zirconium alloy solutions with advanced oxygenation systems designed to withstand higher burnup rates and more aggressive operating environments.
Market growth is further buoyed by the expansion of nuclear capacity in Asia, particularly in China and India, where new reactors are under construction and existing fleets are being upgraded. Chinese state-owned enterprises such as China National Nuclear Corporation (CNNC) and State Nuclear Power Technology Corporation (SNPTC) are increasing procurement of zirconium alloy systems with robust oxygenation control to support domestic fuel manufacturing. In tandem, there is a resurgence of interest in small modular reactors (SMRs), which require compact, high-performance zirconium alloy oxygenation systems—further expanding the addressable market.
Looking ahead, the market outlook through 2030 remains optimistic. European and North American utilities are extending the operating lifetimes of their nuclear plants, necessitating upgrades to zirconium alloy oxygenation systems for improved safety and efficiency. Innovations in coating and alloying technologies, aimed at enhancing corrosion resistance and minimizing hydrogen uptake, are expected to drive incremental revenue growth for established manufacturers and specialized suppliers. While supply chain constraints and regulatory hurdles may impact short-term growth, sustained investment in nuclear infrastructure and advanced materials science is anticipated to underpin a robust demand trajectory for zirconium alloy oxygenation systems worldwide.
Emerging Trends and Disruptive Innovations in Zirconium Alloy Oxygenation
Zirconium alloy oxygenation systems are at the forefront of materials engineering for nuclear power, chemical processing, and advanced manufacturing. As of 2025, the sector is experiencing significant innovation driven by demands for enhanced corrosion resistance, improved safety margins, and increased operational lifespans for critical components.
The primary application of zirconium alloys remains in nuclear fuel cladding, where precise oxygenation control is critical to limit hydrogen uptake and mitigate cladding degradation. This year, manufacturers are shifting towards advanced oxygen diffusion control methods, leveraging high-purity feedstocks and real-time monitoring systems. These advancements stem from sustained research and pilot programs led by major industry players such as Westinghouse Electric Company, a global supplier of nuclear fuel and fuel components, and Framatome, which has recently announced investments into next-generation alloy processing to improve in-reactor performance.
Automated oxygenation monitoring—using AI-backed process controls and in-line sensors—is being introduced in several fabrication lines. This results in tighter control over interstitial oxygen levels, reducing defects and enhancing the mechanical integrity of zirconium alloys under high irradiation. Rolls-Royce, a supplier of nuclear systems, is actively exploring digital twins and predictive maintenance models that incorporate oxygenation data for lifetime prediction of reactor components.
From a materials perspective, researchers are exploring alloying additions—such as niobium and tin—that interact with oxygen to form more stable oxide layers, slowing detrimental oxygen ingress. These trends are evidenced by development efforts at Rosatom, which is piloting new zirconium-niobium alloys with tailored oxygenation properties for Russian and international reactor fleets.
On the equipment front, companies like Sandvik, recognized for their metallurgical equipment, are supplying advanced vacuum arc remelting and electron beam melting systems to achieve controlled oxygenation during ingot production. These technologies ensure homogeneous oxygen distribution, which is essential for both nuclear and non-nuclear high-performance applications.
Looking ahead, the next few years are expected to see widespread adoption of closed-loop oxygenation control, integration of digital manufacturing twins, and deeper collaboration between alloy producers and reactor operators. The drive for accident-tolerant fuels and longer operational cycles will further accelerate innovations in zirconium alloy oxygenation systems, positioning the sector for robust growth and technological advancement.
Top Manufacturers and Technology Leaders (e.g., westinghousenuclear.com, framatome.com)
The landscape of zirconium alloy oxygenation systems is shaped by a handful of established nuclear technology companies and materials specialists, each contributing to advancements in safety, efficiency, and reliability. As of 2025, these systems remain central to nuclear reactor operations, particularly in the management and mitigation of zirconium cladding oxidation, which is critical for fuel integrity and overall plant safety.
Westinghouse Electric Company stands as a prominent leader in the nuclear sector, providing zirconium alloy components and related oxygenation management systems for light water reactors globally. The company continues to push research on advanced zirconium alloys and surface treatments aimed at enhancing corrosion resistance and reducing hydrogen uptake, which is directly related to oxygenation phenomena in reactor environments. Their global supply chain and R&D investments position Westinghouse Electric Company as a key innovator in this segment.
Framatome, a French-based multinational, is another significant contributor, developing and supplying high-performance zirconium alloys for use in various fuel assembly designs. The company’s efforts focus on optimizing alloy composition and developing proprietary oxygenation control technologies that minimize oxide layer growth at elevated temperatures. Framatome integrates these advancements into their fuel manufacturing processes, with a particular emphasis on accident-tolerant fuels (ATFs) that offer improved oxygenation stability under both normal and off-normal reactor conditions.
TVEL Fuel Company, a subsidiary of Russia’s Rosatom, is also a leading player, supplying zirconium alloy products for VVER and other reactor types. TVEL Fuel Company continues to invest in alloy development and oxygenation system monitoring, aiming to extend fuel cycle lengths and improve operational safety margins. Their efforts are supported by extensive in-reactor testing and collaboration with reactor operators worldwide.
Nippon Steel Corporation in Japan is deeply involved in the production of high-purity zirconium and advanced alloy tubing, supplying both domestic and international reactor projects. Nippon Steel Corporation leverages its metallurgical expertise to develop materials with superior control over oxygen diffusion and oxide formation.
Looking ahead, the outlook for zirconium alloy oxygenation systems points to continued incremental innovation, driven by stricter regulatory requirements, the global push for extended fuel lifetimes, and the deployment of next-generation reactors. Manufacturers are expected to further refine alloy compositions, coating technologies, and real-time oxygenation monitoring systems to meet evolving industry standards and ensure reactor safety and efficiency.
Core Applications: Energy, Aerospace, and Medical Advancements
Zirconium alloy oxygenation systems have become pivotal in sectors where material performance under oxidative stress is critical, notably in energy, aerospace, and medical applications. The year 2025 marks a period of heightened innovation, with industry leaders focusing on enhancing system safety, longevity, and efficiency through advanced zirconium alloy technologies.
In the energy sector, zirconium alloys, particularly those optimized for controlled oxygenation, continue to underpin the safe operation of nuclear reactors. These alloys form protective oxide layers that limit further oxidation, ensuring cladding integrity for nuclear fuel rods. Major suppliers such as Westinghouse Electric Company and Framatome have disclosed ongoing improvements in zirconium alloy compositions and oxygenation control, aiming to further reduce hydrogen pickup and corrosion rates in high-burnup fuel assemblies. Such advancements are critical as next-generation reactors and extended fuel cycles demand even greater material reliability.
In aerospace, where high-temperature stability and oxidation resistance are paramount, zirconium alloy oxygenation systems have seen increased deployment in turbine engines and heat shields. Companies like General Electric are actively evaluating zirconium-based coatings and structural components for next-generation jet engines, leveraging the metal’s ability to maintain mechanical properties and form adherent oxide barriers at elevated temperatures. This is especially relevant as the industry pursues hypersonic flight and reusable space vehicles, which necessitate materials capable of withstanding extreme thermal cycling and oxidative environments.
Medical device manufacturers are also capitalizing on zirconium alloys’ biocompatibility and corrosion resistance. Firms such as Smith+Nephew and Stryker are exploring oxygenation-controlled zirconium alloys for orthopedic implants and surgical instruments. The oxide layer formed during oxygenation imparts not only wear resistance but also improved integration with biological tissues, reducing adverse reactions.
Looking ahead, the outlook for zirconium alloy oxygenation systems is robust. The push for safer, longer-lasting nuclear fuel, advanced aerospace propulsion, and more reliable medical devices is expected to drive further research and commercial adoption. Standardization efforts by industry bodies such as the American Society of Mechanical Engineers and ASTM International are likely to accelerate qualification and deployment of new zirconium alloy grades, supporting broader application in critical systems through the latter half of the decade.
Regulatory Environment and Industry Standards (e.g., ansi.org, asme.org)
The regulatory environment governing Zirconium Alloy Oxygenation Systems in 2025 is characterized by heightened scrutiny, ongoing standardization updates, and a growing emphasis on safety and environmental impact. These systems, integral to nuclear reactor fuel cladding and other high-performance applications, are subject to rigorous codes and standards set forth by international and national bodies, notably the American Society of Mechanical Engineers (ASME) and the American National Standards Institute (ANSI).
Currently, zirconium alloy oxygenation system design and operation are primarily regulated through ASME’s Boiler and Pressure Vessel Code (BPVC), which sets forth requirements for materials, fabrication, testing, and inspection of components used in nuclear facilities. The 2023 revision of the BPVC Section III—pertaining to nuclear facility components—continues to be the reference point in 2025, but the ASME is actively soliciting feedback and proposals for amendments in light of advances in zirconium alloy chemistry and oxygenation monitoring technologies. This is particularly relevant as utilities and manufacturers, such as Westinghouse Electric Company and Framatome, push for more precise oxygen control to mitigate corrosion and hydrogen uptake.
ANSI’s role is to accredit and coordinate the development of consensus standards relevant to zirconium alloy processing, including ASTM standards governing chemical composition, mechanical properties, and oxygen content measurement. In 2024, ANSI-accredited committees began reviewing updates to ASTM B353, which addresses specifications for wrought zirconium and zirconium alloys for nuclear applications. The results of these reviews are expected to influence procurement and quality assurance protocols by 2026, especially as the nuclear industry prepares for broader deployment of small modular reactors (SMRs) and advanced reactors that rely on next-generation zirconium alloys.
Internationally, the International Atomic Energy Agency (IAEA) continues to facilitate harmonization of safety standards, urging member states to align with evolving best practices in zirconium alloy oxygenation system management. This is particularly pertinent as countries such as China and India accelerate their nuclear programs and domestic suppliers like Bharat Forge and China General Nuclear Power Group seek compliance with both local and international benchmarks.
Looking ahead, regulatory bodies and industry groups are expected to place increased emphasis on digital monitoring, real-time oxygenation analytics, and advanced manufacturing traceability. This will likely be reflected in forthcoming ASME and ANSI standard revisions, setting a higher bar for system validation and lifecycle management in zirconium alloy oxygenation applications.
Competitive Landscape and Strategic Partnerships
The competitive landscape of zirconium alloy oxygenation systems in 2025 is marked by active involvement from major nuclear materials suppliers, strategic collaborations, and a focus on technological innovation. This sector is critical for nuclear reactor safety and efficiency, as zirconium alloys are widely used as fuel cladding due to their low neutron absorption and high corrosion resistance. Oxygenation systems, which control the oxygen content during alloy production and in operational environments, are essential in enhancing the performance and lifespan of these materials.
Key market participants such as Westinghouse Electric Company and Framatome continue to advance zirconium alloy technology. Westinghouse Electric Company, a global leader in nuclear fuel and services, has maintained a strong position through ongoing investments in zirconium metallurgy and the deployment of advanced oxygenation processes. Framatome, with its extensive experience in nuclear fuel fabrication, is leveraging expertise in materials science to optimize the oxygen control mechanisms in zirconium alloy production, aiming for improved operational reliability in pressurized water reactors (PWRs) and boiling water reactors (BWRs).
In 2025, strategic partnerships are shaping the direction of innovation. Companies are collaborating with research institutions and reactor operators to address challenges such as hydrogen pickup and corrosion under high-temperature, high-pressure conditions. For instance, China National Nuclear Corporation (CNNC) has partnered with domestic and international technology providers to enhance the oxygenation quality control in its rapidly expanding nuclear fleet, directly linking R&D efforts to deployment in new reactors.
Material suppliers like ATI (Allegheny Technologies Incorporated) and Cameco are also important, as they supply specialized zirconium products and collaborate with fuel fabricators to ensure alloy performance meets evolving regulatory and operational standards. These firms are investing in refining oxygenation system precision and traceability to comply with stringent quality assurance requirements.
Looking ahead, the market is likely to see further partnerships between reactor operators, alloy manufacturers, and advanced instrumentation providers to enable real-time oxygen monitoring and feedback control systems. This is expected to drive improvements in fuel rod longevity and reactor economics. Additionally, as new reactor designs such as small modular reactors (SMRs) gain traction, suppliers are positioning themselves to offer tailored zirconium alloy oxygenation solutions to meet the unique needs of these next-generation units.
Supply Chain Analysis: Raw Materials to End-Use
The supply chain for zirconium alloy oxygenation systems, integral to the nuclear and chemical processing industries, is characterized by specialized raw material sourcing, precise alloy fabrication, and stringent downstream quality controls. In 2025, the supply landscape is shaped by evolving procurement strategies, geopolitical factors, and growing demand for advanced reactor technologies.
Raw zirconium is primarily sourced from mineral sands, notably zircon (ZrSiO4), with major producers including Rio Tinto (through its Richards Bay Minerals operation), Iluka Resources, and The Chemours Company. These companies extract and process zircon concentrate, which is then converted to zirconium sponge or ingot through chlorination and reduction processes. In 2025, supply chain volatility is mitigated by long-term contracts and vertical integration, as seen in Iluka Resources’s expansion into downstream processing.
Fabricators such as Westinghouse Electric Company and Framatome (a key subsidiary of Électricité de France) are among the leading producers of zirconium alloys for nuclear fuel cladding and oxygenation systems. They typically source sponge from global suppliers and then perform alloying—adding elements like tin, niobium, or iron—to enhance corrosion resistance and mechanical strength under high-oxygen environments. Fabrication involves melting, extrusion, and tube drawing, with strict controls on impurity levels, especially to prevent excessive hydrogen and oxygen pickup during processing.
Oxygenation systems, often deployed in nuclear reactors to manage cladding oxidation and hydrogen generation, must meet exacting performance standards. End-users—predominantly nuclear plant operators—require consistent supply and traceability. Companies such as Westinghouse Electric Company and Framatome maintain close partnerships with utilities, offering not just materials but also integrated fuel management and system monitoring services.
In 2025 and the coming years, the outlook for zirconium alloy oxygenation systems is influenced by the global push for advanced nuclear reactors (such as small modular reactors), which often demand improved zirconium alloys and innovative oxygenation controls. Supply chain risks remain—especially regarding geopolitical tensions affecting mineral exports—but industry leaders are investing in recycling and alternative sourcing, as well as digital supply chain management for resilience. The sector’s focus is shifting toward sustainability, with companies like Rio Tinto and Iluka Resources adopting stricter environmental and social governance standards throughout the value chain.
Investment Hotspots and Future Growth Opportunities
The zirconium alloy oxygenation systems market is poised for significant shifts in investment patterns and technological advancement in 2025 and the following years, driven by the nuclear power sector’s demand for safer and more efficient reactor materials. Zirconium alloys, critical for fuel cladding due to their low neutron absorption and high corrosion resistance, are at the heart of ongoing research and commercial focus on oxygenation systems that enhance performance and longevity.
One of the primary investment hotspots remains in countries prioritizing nuclear energy expansion and modernization, such as China, the United States, France, and South Korea. State-owned enterprises and major nuclear fuel manufacturers, like China General Nuclear Power Group and Framatome, are actively pursuing zirconium alloy enhancements, including controlled oxygenation processes to mitigate hydrogen pickup and corrosion in next-generation reactors. These efforts are expected to accelerate in 2025 as new reactor builds and upgrades demand more advanced fuel cladding solutions.
In the U.S., Westinghouse Electric Company continues to invest in advanced zirconium alloy manufacturing, with a focus on oxygenation control to ensure cladding integrity under accident-tolerant fuel (ATF) programs. Similarly, Nuclear Fuel Industries, Ltd. (NFI), a key supplier in Asia, is expanding its R&D in oxygenation systems to address growing regional nuclear deployment and safety requirements.
The European Union’s funding for research consortia and public-private partnerships is also channeling capital into advanced zirconium alloy processing. Companies such as Norsk Hydro, with expertise in specialty metals, are exploring opportunities to supply high-purity zirconium and oxygenation technology to established and emerging nuclear markets.
Looking forward, the outlook for zirconium alloy oxygenation systems is closely tied to the global trajectory of nuclear reactor construction, particularly in Asia-Pacific and Eastern Europe. As more nations commit to carbon neutrality and energy security, investments are likely to surge in supply chain localization and next-generation alloy development. Moreover, regulatory drivers emphasizing accident tolerance and long-term waste reduction will spur adoption of proprietary oxygenation techniques by leading vendors.
- High-growth regions: Asia-Pacific (China, South Korea, India), Eastern Europe
- Leading firms: Framatome, Westinghouse Electric Company, Nuclear Fuel Industries, Ltd.
- Emerging opportunities: Advanced reactor concepts (SMRs, Gen IV reactors), accident-tolerant fuels, corrosion-resistant cladding
In sum, the period of 2025 and beyond will see escalating investment in zirconium alloy oxygenation systems, with growth fueled by nuclear expansion, technological innovation, and evolving safety standards.
2025–2030 Roadmap: Challenges, Risks, and Future Outlook
Between 2025 and 2030, the evolution of zirconium alloy oxygenation systems is set to shape the operational safety and longevity of nuclear reactors, especially as utilities worldwide focus on life extension and next-generation reactor designs. Oxygenation systems are pivotal in controlling the growth of oxide layers on zirconium alloys, which are widely used in nuclear fuel cladding due to their low neutron absorption and corrosion resistance. However, excessive oxidation can compromise cladding integrity and reactor safety, underscoring the importance of advanced oxygenation management.
One of the central challenges anticipated is the management of hydrogen pickup and oxide layer formation, particularly as plants push for longer fuel cycles and higher burnups. As of 2025, leading manufacturers such as Westinghouse Electric Company and Framatome are advancing proprietary zirconium alloy compositions and surface treatments to better control oxygenation kinetics and limit hydrogen ingress. These innovations are critical as utilities in North America, Europe, and Asia pursue reactor lifespans of 60 years or more.
Risks associated with oxygenation systems over the coming years include increased susceptibility to stress corrosion cracking, particularly at elevated temperatures or under accident conditions. Industry bodies like the Electric Power Research Institute are coordinating collaborative research to address these risks by modeling oxidation behavior and testing advanced alloy variants in simulated reactor environments.
The next five years will also see a growing emphasis on digital monitoring and predictive analytics for in-situ assessment of oxide growth rates and cladding health. Companies such as GE Vernova are investing in sensor technologies and AI-driven analytics platforms designed to deliver real-time feedback on oxygenation status, supporting proactive maintenance and reducing unplanned outages.
Internationally, the adoption of higher burnup fuels and accident-tolerant fuel (ATF) designs is expected to drive further innovation in zirconium alloy oxygenation systems. Collaborations among global suppliers, including Toshiba Energy Systems & Solutions Corporation and Rosatom, are likely to accelerate the development and qualification of new alloy chemistries and coatings. Regulatory bodies will play a key role in standardizing testing protocols and approving new materials, ensuring safety benchmarks keep pace with technological advances.
Looking ahead to 2030, the outlook for zirconium alloy oxygenation systems is characterized by cautious optimism. While technical hurdles remain, ongoing R&D and industry collaboration are expected to yield materials and system-level solutions that enhance reactor safety and performance, supporting the continued role of nuclear power in a low-carbon energy future.
Sources & References
- Framatome
- Westinghouse Electric Company
- GE Vernova
- Rolls-Royce
- Sandvik
- Westinghouse Electric Company
- Framatome
- Smith+Nephew
- American Society of Mechanical Engineers
- ASTM International
- ANSI
- IAEA
- Bharat Forge
- China General Nuclear Power Group
- Cameco
- Rio Tinto
- Electric Power Research Institute