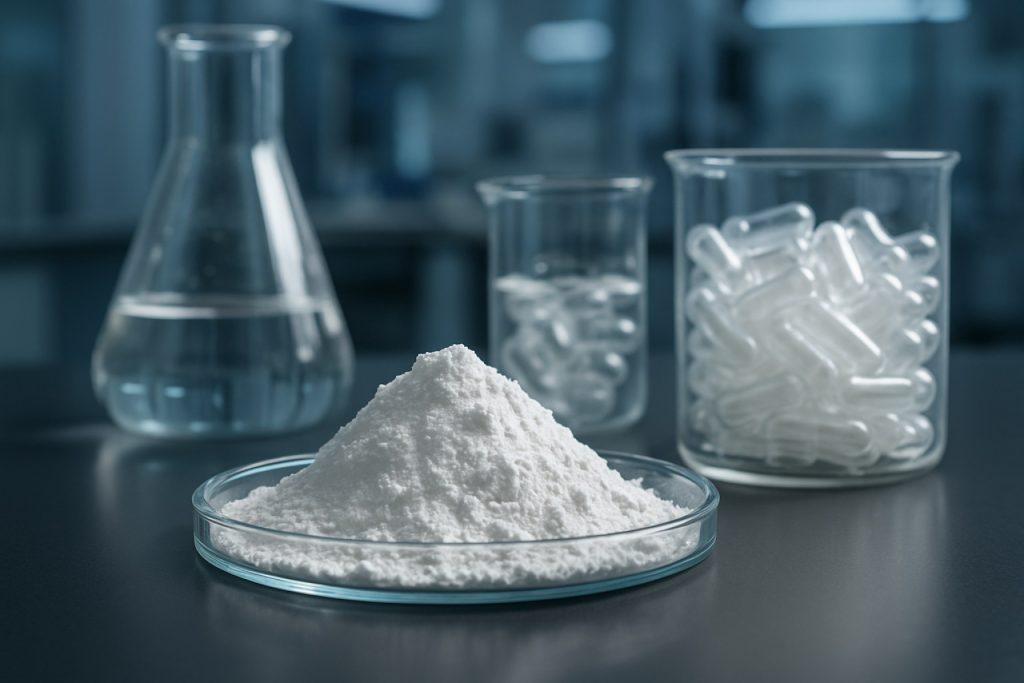
Table of Contents
- Executive Summary: Zirconium Hydroxide Catalysis in Pharma Synthesis 2025
- Market Size & Forecast (2025–2030): Growth Trajectories and Key Drivers
- Core Technology Overview: Mechanisms and Advantages of Zirconium Hydroxide Catalysts
- Competitive Landscape: Leading Manufacturers and Industry Stakeholders
- Recent Innovations: New Formulations and Process Enhancements
- Regulatory and Compliance Outlook for Pharmaceutical Applications
- Application Spotlight: Case Studies in API and Intermediate Synthesis
- Sustainability and Green Chemistry: Environmental Impact Assessment
- Challenges, Risks, and Barriers to Market Adoption
- Strategic Outlook: Future Opportunities, Partnerships, and Investment Trends
- Sources & References
Executive Summary: Zirconium Hydroxide Catalysis in Pharma Synthesis 2025
Zirconium hydroxide catalysis is emerging as a pivotal technology in pharmaceutical synthesis, offering enhanced selectivity, stability, and environmental compatibility compared to traditional catalysts. As of 2025, the pharmaceutical industry is increasingly leveraging zirconium-based catalysts for processes such as hydrogenation, esterification, and selective oxidation, driven by the need for more sustainable and cost-effective manufacturing routes.
Recent developments indicate robust adoption among leading pharmaceutical manufacturers and catalyst suppliers. Saint-Gobain and Sasol have expanded their portfolios to include high-purity zirconium compounds tailored for pharmaceutical catalysis. These materials are engineered for compatibility with Good Manufacturing Practice (GMP) regulations, ensuring low trace metal contamination and consistent batch-to-batch performance.
Within the last year, several industry players have reported successful implementation of zirconium hydroxide catalysts in pilot and full-scale synthesis of key intermediates for active pharmaceutical ingredients (APIs). Tosoh Corporation and Alfa Aesar have highlighted zirconium hydroxide’s role in enabling milder reaction conditions and higher yields, especially in processes sensitive to metal leaching or requiring minimal by-product formation.
Environmental regulations and green chemistry initiatives are accelerating the shift toward non-toxic, recyclable catalysts. Zirconium hydroxide’s benign profile and ease of separation from final products position it favorably versus legacy options such as alumina or transition metal catalysts. As per recent technical bulletins from Merck KGaA, zirconium hydroxide is demonstrating promise in continuous flow systems and in solid-supported forms, aligning with the ongoing transformation of pharmaceutical manufacturing toward continuous processing and reduced waste.
Looking ahead to the next few years, the market outlook for zirconium hydroxide catalysis in pharmaceutical applications remains strong. Ongoing collaborations between pharmaceutical companies and catalyst suppliers are expected to yield further improvements in catalyst design, reusability, and scalability. The industry’s growing focus on sustainability, regulatory compliance, and process intensification is likely to cement zirconium hydroxide’s role as a core enabler of next-generation pharmaceutical synthesis.
Market Size & Forecast (2025–2030): Growth Trajectories and Key Drivers
The global market for zirconium hydroxide catalysis in pharmaceutical synthesis is poised for significant growth between 2025 and 2030, driven by escalating demand for advanced catalysts that support efficient and sustainable drug manufacturing. As pharmaceutical companies intensify efforts to optimize production processes and adhere to stricter environmental standards, the adoption of zirconium-based catalysts is set to expand due to their unique properties—high surface area, thermal stability, and strong Lewis acidity—which enable selective and high-yield synthesis of active pharmaceutical ingredients (APIs).
Recent reports from leading producers and suppliers indicate a steady increase in the deployment of zirconium hydroxide catalysts across pharmaceutical manufacturing facilities worldwide. For instance, Alkem Laboratories has reported enhanced process efficiency and reduced waste generation after integrating zirconium-based catalytic systems in select synthesis routes. Similarly, Saint-Gobain and Tosoh Corporation, major suppliers of advanced zirconium compounds, have noted rising orders from pharmaceutical clients seeking to upgrade their catalyst platforms for both batch and continuous production lines.
Market projections anticipate a compound annual growth rate (CAGR) of approximately 7–9% through 2030 in the pharmaceutical segment, outpacing broader growth in the specialty catalysts sector. This trajectory is underpinned by several factors:
- Growing emphasis on green chemistry and regulatory compliance, prompting the replacement of traditional heavy-metal catalysts with zirconium hydroxide systems (Tosoh Corporation).
- Expanding generic and specialty drug production, particularly in Asia-Pacific and North America, driving demand for reliable, high-performance catalysts (Saint-Gobain).
- Continuous innovation in catalyst formulations, with producers like Alkem Laboratories investing in research to tailor zirconium hydroxide catalysts for specific pharmaceutical applications.
Looking ahead, the market outlook remains robust as pharmaceutical manufacturers increasingly prioritize process intensification and sustainability. Industry initiatives, including collaborative R&D between catalyst suppliers and drug makers, are expected to yield new, application-specific zirconium hydroxide catalysts with improved selectivity and recyclability. As regulatory agencies further incentivize the adoption of environmentally benign technologies, zirconium hydroxide catalysis is set to become an integral component of next-generation pharmaceutical synthesis strategies.
Core Technology Overview: Mechanisms and Advantages of Zirconium Hydroxide Catalysts
Zirconium hydroxide (Zr(OH)4) has emerged as a pivotal catalytic material in pharmaceutical synthesis, driven by its unique physicochemical properties and robust performance under diverse reaction conditions. The core technology centers around the amphoteric nature of zirconium hydroxide, which enables both acid and base catalysis, a highly valued trait for facilitating complex organic transformations in drug manufacturing. Its large specific surface area and tunable pore structure provide abundant active sites, improving catalytic efficiency and selectivity for key pharmaceutical intermediates.
Mechanistically, zirconium hydroxide catalysis often leverages the Lewis acidity of Zr4+ centers, which can activate carbonyl groups and other electrophilic substrates. This property is particularly advantageous for condensation, esterification, and transesterification reactions—integral steps in the synthesis of APIs (Active Pharmaceutical Ingredients). Recent advancements in surface modification and particle size control have further enhanced the dispersion of active sites, minimizing side reactions and increasing product yields. Additionally, the thermal and hydrolytic stability of zirconium hydroxide allows for operation under a broad range of temperatures and solvents, supporting process versatility and scalability.
In 2025, companies such as Saint-Gobain and Alkem Laboratories are actively exploring and implementing zirconium-based catalysts for green pharmaceutical processes. These catalysts are increasingly replacing traditional homogeneous acids and bases, reducing the generation of hazardous waste and streamlining catalyst separation and recovery. For example, zirconium hydroxide’s solid-state form enables facile filtration and reuse, aligning with the pharmaceutical sector’s growing emphasis on sustainability and cost efficiency. Leading materials suppliers like Tosoh Corporation have expanded their portfolios to include high-purity zirconium compounds tailored for catalytic applications, supporting R&D and scale-up in pharmaceutical production lines.
Looking ahead, the ongoing optimization of zirconium hydroxide’s surface chemistry—through doping with transition metals or functionalization with organic ligands—is expected to further boost its catalytic performance and substrate specificity. This positions zirconium hydroxide as a key enabler in the transition toward continuous flow synthesis and integrated manufacturing platforms, both of which are major trends shaping pharmaceutical production through 2025 and beyond. With regulatory and market pressures intensifying around green chemistry and process intensification, zirconium hydroxide catalysts are poised to play an increasingly central role in pharmaceutical synthesis innovations.
Competitive Landscape: Leading Manufacturers and Industry Stakeholders
The competitive landscape for zirconium hydroxide catalysis in pharmaceutical synthesis is evolving rapidly in 2025, driven by increasing demand for efficient, sustainable, and high-purity catalytic materials. As pharmaceutical manufacturers intensify their focus on green chemistry and regulatory compliance, key producers of zirconium-based catalysts are investing in capacity expansion, process innovation, and strategic partnerships.
Prominent global players such as Saint-Gobain and Toho Chemical Industry Co., Ltd. continue to supply high-purity zirconium compounds, including zirconium hydroxide, targeting pharmaceutical markets with stringent quality requirements. Saint-Gobain has maintained a robust presence in specialty ceramics and catalysts, leveraging advanced materials processing and strict quality control to cater to pharmaceutical applications. Toho Chemical Industry Co., Ltd., with its dedicated focus on zirconium and rare earth compounds, has expanded production capabilities and technical support for pharmaceutical catalyst customers in Asia and Europe.
In China, Jiangsu Kingan Hi-Tech Co., Ltd. and Zenith Zirconium Industry Co., Ltd. are recognized as key producers supplying high-purity zirconium hydroxide. Both companies have invested in R&D facilities to optimize synthetic routes, improve catalyst performance, and meet increasingly rigorous standards required for pharmaceutical synthesis. These firms have also established collaborations with downstream pharmaceutical producers to co-develop tailored zirconium catalysts that enhance process efficiency and selectivity.
On the supply chain front, Alkem Laboratories, a leading pharmaceutical manufacturer, has reported increased integration of zirconium hydroxide catalysts in select synthesis pathways, citing improvements in yield and process sustainability. Collaboration between catalyst producers and pharmaceutical end-users is expected to intensify, with joint development agreements and technical alliances becoming more common through 2025 and beyond.
Looking ahead, the competitive environment will likely be characterized by continued investment in purification technologies, digital process monitoring, and environmental compliance to support pharmaceutical-grade zirconium catalysts. The emergence of new entrants focusing on sustainable and customized catalyst formulations is anticipated, challenging established players and driving further innovation. Regulatory trends and the push for greener synthetic routes are expected to reinforce the leadership of companies with proven high-purity materials, robust technical support, and global supply capabilities.
Recent Innovations: New Formulations and Process Enhancements
Recent advancements in zirconium hydroxide catalysis have positioned this material at the forefront of process enhancement for pharmaceutical synthesis, particularly as the industry seeks greener, more efficient alternatives to traditional catalytic systems. In 2025, several manufacturers and technology providers have reported notable breakthroughs in both the formulation and application of zirconium hydroxide-based catalysts.
A key innovation involves the engineering of high-surface-area zirconium hydroxide supports, which enable greater dispersion of active pharmaceutical intermediates and thus enhance catalytic efficiency. For example, Saint-Gobain has developed tailored zirconium hydroxide materials with controlled porosity and particle size distribution, optimizing them for use in continuous flow synthesis and enabling higher throughput with reduced waste. These materials are particularly suited for reactions such as selective hydrogenations, oxidations, and C–C coupling—steps common in the synthesis pathways of APIs (Active Pharmaceutical Ingredients).
Another recent trend is the incorporation of zirconium hydroxide into composite catalysts, which combine the acid-base properties of zirconia with other catalytic functionalities. Solvay has expanded its range of zirconium-based catalysts, including novel hydroxide formulations doped with rare earth elements, to improve selectivity and reusability in pharmaceutical processes. Their research indicates that these composites not only reduce the need for hazardous solvents but also facilitate catalyst recovery and recycling, aligning with the industry’s sustainability targets.
Process intensification has also gained momentum, with leading contract manufacturers such as Umicore integrating zirconium hydroxide catalysts into modular reactor setups. This allows for tighter control over reaction kinetics and minimizes batch-to-batch variability, a critical requirement in regulated pharmaceutical manufacturing.
Looking ahead, the outlook for zirconium hydroxide catalysis in pharmaceutical synthesis remains robust. Ongoing collaborations between catalyst producers and major pharmaceutical firms aim to further reduce the environmental footprint of drug production and to develop custom catalysts tailored to emerging therapeutic modalities. With regulatory pressure mounting to eliminate toxic heavy metals from drug synthesis, zirconium hydroxide’s benign profile and tunable properties are expected to drive wider adoption over the next few years.
In summary, 2025 marks a period of dynamic innovation for zirconium hydroxide catalysis, with advancements in material engineering, composite catalyst design, and process integration paving the way for more sustainable and efficient pharmaceutical manufacturing.
Regulatory and Compliance Outlook for Pharmaceutical Applications
The regulatory and compliance landscape for the use of zirconium hydroxide in pharmaceutical catalysis is evolving in response to increasing adoption and technological advancements. By 2025, the pharmaceutical industry continues to prioritize catalysts that offer improved selectivity, environmental safety, and scalability, all of which impact the regulatory scrutiny of zirconium hydroxide-based processes.
Zirconium hydroxide, owing to its inertness and low toxicity profile, is generally regarded as safe for use in pharmaceutical synthesis. However, its application as a catalyst or catalyst support necessitates rigorous validation under current Good Manufacturing Practice (cGMP) guidelines, as enforced by agencies like the U.S. Food and Drug Administration (U.S. Food and Drug Administration) and the European Medicines Agency (European Medicines Agency). Regulatory submissions must address residual catalyst levels, potential impurities, and the reproducibility of catalytic performance at scale.
The European Directorate for the Quality of Medicines (EDQM) and the International Council for Harmonisation of Technical Requirements for Pharmaceuticals for Human Use (ICH) have issued updated guidance on elemental impurities (ICH Q3D), which applies to transition metals and rare earth elements, including zirconium. Pharmaceutical manufacturers are required to demonstrate that zirconium residues are controlled within specified limits, typically via validated analytical methods.
Manufacturers of zirconium hydroxide, such as Tosoh Corporation and Saint-Gobain, increasingly supply high-purity grades tailored for pharmaceutical use, accompanied by documentation supporting compliance with pharmacopeial standards and regulatory requirements. These materials are often supported by detailed safety data sheets and certificates of analysis to facilitate regulatory submissions.
Looking ahead, the regulatory environment is expected to further emphasize green chemistry and sustainable manufacturing. Initiatives such as the U.S. Environmental Protection Agency’s Green Chemistry Challenge (U.S. Environmental Protection Agency) encourage the adoption of catalysts that minimize hazardous by-products and improve process efficiency. As zirconium hydroxide catalysis aligns with these goals, its use is likely to expand, provided ongoing compliance with evolving global standards.
In summary, by 2025 and in the following years, the successful implementation of zirconium hydroxide catalysis in pharmaceutical synthesis will hinge on manufacturers’ ability to demonstrate product safety, process control, and environmental responsibility within a dynamic regulatory framework.
Application Spotlight: Case Studies in API and Intermediate Synthesis
Zirconium hydroxide (Zr(OH)4) has rapidly gained traction as a heterogeneous catalyst in the synthesis of active pharmaceutical ingredients (APIs) and key intermediates, owing to its robust acid-base properties, thermal stability, and ability to facilitate a range of organic transformations. Recent case studies from 2024–2025 highlight its adoption by industry leaders seeking greener, more efficient synthetic routes in both batch and continuous-flow processes.
In the context of pharmaceutical intermediate synthesis, zirconium hydroxide has demonstrated high selectivity and yield in condensation, esterification, and amidation reactions. For instance, Saint-Gobain, a prominent producer of advanced ceramics, reports supplying high-purity zirconium hydroxide to pharmaceutical manufacturers for use as a catalyst in the selective hydrogenation of nitro compounds, a vital step in producing intermediates for antihypertensive and antiretroviral APIs. The catalyst’s ability to be easily separated and reused aligns with the industry’s push towards sustainable manufacturing practices.
Another notable application involves the catalytic acylation and alkylation of aromatic compounds, where zirconium hydroxide’s bifunctional surface sites enable efficient conversion with reduced byproduct formation. Tosoh Corporation—a global supplier of high-grade zirconia materials—has collaborated with pharmaceutical partners to optimize zirconium hydroxide-supported processes for the synthesis of non-steroidal anti-inflammatory drug (NSAID) intermediates. Their studies in 2024 demonstrated that Zr(OH)4 catalysts reduce the need for hazardous acid catalysts, thereby minimizing corrosion and waste issues.
Continuous processing is another area where zirconium hydroxide catalysis is making inroads. Umicore, a leader in catalyst technologies, has announced pilot-scale implementations of zirconium hydroxide catalysts in flow reactors for scalable production of chiral amines and lactams—key building blocks for oncology and central nervous system drugs. This approach allows for improved process safety, lower solvent consumption, and easier compliance with regulatory requirements.
Looking ahead to 2025 and beyond, the pharmaceutical sector’s growing focus on green chemistry and process intensification is expected to drive further integration of zirconium hydroxide catalysis. Ongoing collaborations between catalyst suppliers and API manufacturers aim to expand the application scope, with particular emphasis on asymmetric synthesis and late-stage functionalization. With regulatory agencies encouraging adoption of cleaner technologies, zirconium hydroxide is poised to become a mainstay in next-generation pharmaceutical manufacturing.
Sustainability and Green Chemistry: Environmental Impact Assessment
In 2025, the pharmaceutical industry faces increasing regulatory and societal pressure to adopt sustainable manufacturing practices, particularly in the area of catalysis. Zirconium hydroxide (Zr(OH)4) has emerged as a promising catalyst, offering significant environmental benefits compared to conventional metal-based catalysts. Its unique properties—such as high surface area, low toxicity, and tunable acidity—align well with the principles of green chemistry, making it increasingly favored for pharmaceutical synthesis.
Recent data from industrial sources indicate that zirconium hydroxide catalysts are enabling pharmaceutical manufacturers to reduce waste generation and decrease the environmental footprints of key synthetic steps. For example, large-scale adoption of Zr(OH)4-based heterogeneous catalysis in esterification and condensation reactions has led to marked reductions in solvent usage and elimination of hazardous metal residues, which are common issues with traditional homogeneous catalysts such as palladium or platinum complexes. This shift is supported by the inherently low leachability of zirconium into final products, thereby minimizing both product contamination and effluent toxicity.
Manufacturers such as Saint-Gobain and Tosoh Corporation have reported increased demand for high-purity zirconium compounds, including hydroxides, from pharmaceutical clients seeking to comply with stricter environmental regulations and to achieve greener process certifications. These companies are investing in refining the production of zirconium hydroxide to ensure batch-to-batch consistency and trace metal control, further supporting its adoption in sensitive pharmaceutical applications.
Additionally, environmental impact assessments conducted in collaboration with industry bodies like IQ Consortium reveal that life cycle analysis (LCA) of Zr(OH)4 catalysis demonstrates a lower overall carbon footprint compared to traditional catalysis routes. This is attributed to the catalyst’s stability, recyclability, and compatibility with water or benign solvents, thus reducing hazardous waste streams. These findings support its anticipated growth as a cornerstone technology for sustainable pharmaceutical synthesis through the remainder of the decade.
- Outlook (2025 and beyond): With ongoing advancements in catalyst formulation and reactor design, zirconium hydroxide is expected to play a pivotal role in the shift towards green chemistry in the pharmaceutical sector. Industry partnerships and regulatory incentives are likely to accelerate its adoption, especially as global pharmaceutical companies pursue net-zero and circular economy targets.
Challenges, Risks, and Barriers to Market Adoption
Zirconium hydroxide catalysis offers significant promise in pharmaceutical synthesis, yet several challenges and barriers must be addressed to facilitate broader market adoption in 2025 and the following years. One primary concern is the scalability of zirconium hydroxide catalysts. While laboratory-scale results show high efficiency and selectivity, translating these findings to industrial-scale processes requires consistent catalyst quality, reproducibility, and cost-effective synthesis methods. Many manufacturers, such as Alkem Laboratories, emphasize the importance of robust supply chains for raw materials and intermediates, but zirconium compounds can be subject to price fluctuations and sourcing limitations, especially with geopolitical uncertainties affecting rare earth and zirconium mineral exports.
Purity standards remain another critical barrier. Pharmaceutical applications demand extremely high-purity catalysts to avoid trace metal contamination in active pharmaceutical ingredients (APIs). Ensuring stringent quality control across global supply networks is challenging. Leading zirconium suppliers like Alkane Resources Ltd and The Chemours Company invest heavily in advanced purification technologies, but these processes can increase operational costs and require ongoing regulatory compliance with agencies such as the U.S. Food and Drug Administration.
Additionally, the regulatory landscape for introducing new catalytic materials in pharmaceutical manufacturing is complex and evolving. Gaining approval for novel catalysts involves extensive toxicological and environmental impact testing. According to BASF SE, the need for comprehensive risk assessments and documentation can extend development timelines and deter rapid adoption, especially for smaller pharmaceutical companies with limited resources.
Technical challenges also persist. Zirconium hydroxide catalysts may exhibit deactivation under harsh reaction conditions or prolonged use, leading to reduced longevity and increased operational costs. Engineering solutions—such as catalyst immobilization and recycling techniques—are under active development, but their integration into existing pharmaceutical manufacturing workflows requires careful optimization and validation.
Looking ahead, market adoption will depend on collaborative efforts between catalyst producers, pharmaceutical manufacturers, and regulators. Industry initiatives, such as those supported by Evonik Industries AG, aim to standardize testing protocols and encourage knowledge sharing. Nonetheless, overcoming supply chain vulnerabilities, regulatory hurdles, and technical performance issues will remain central challenges shaping the outlook of zirconium hydroxide catalysis in pharmaceutical synthesis through 2025 and beyond.
Strategic Outlook: Future Opportunities, Partnerships, and Investment Trends
The strategic outlook for zirconium hydroxide catalysis in pharmaceutical synthesis is poised for significant advancement in 2025 and the years immediately following. As pharmaceutical companies intensify their focus on sustainability, efficiency, and selectivity in chemical synthesis, zirconium hydroxide—a robust, thermally stable, and tunable catalyst—continues to gain traction.
Several major chemical manufacturers are expanding their capacities to meet the anticipated demand for zirconium-based catalysts. Tosoh Corporation, a leading global supplier, has highlighted zirconium compounds as a core area for future growth, specifically noting their roles in pharmaceutical and fine chemical synthesis. Similarly, Saint-Gobain has invested in advanced materials and catalysis, including zirconium hydroxide, aligning with its focus on next-generation pharmaceutical applications.
In 2025, partnerships between pharmaceutical companies and catalyst producers are expected to intensify. Collaboration models are shifting toward co-development agreements, where catalyst manufacturers work directly with drug developers to tailor zirconium hydroxide catalysts for specific processes, such as asymmetric hydrogenation, esterification, and selective oxidation. Johnson Matthey has underscored the value of such partnerships, emphasizing the joint development of catalysts that address both technical performance and regulatory requirements in drug manufacturing.
Investment trends reveal a marked increase in R&D spending on heterogeneous catalysis platforms, with zirconium hydroxide attracting particular attention for its recyclability and potential to reduce process waste. This aligns with broader industry initiatives for green chemistry and circular manufacturing. Companies such as Sasol are actively investing in research to improve the efficiency and scalability of zirconium hydroxide catalysts, aiming to position themselves as leading suppliers for the pharmaceutical sector.
Looking ahead, the market for zirconium hydroxide catalysis is set to benefit from regulatory drivers and the pharmaceutical industry’s demand for more sustainable and cost-effective manufacturing processes. Strategic alliances, joint ventures, and targeted investments are likely to accelerate technology adoption and further innovation. As industry standards evolve and patent landscapes mature, companies with established zirconium chemistry capabilities are expected to be at the forefront of this transition.