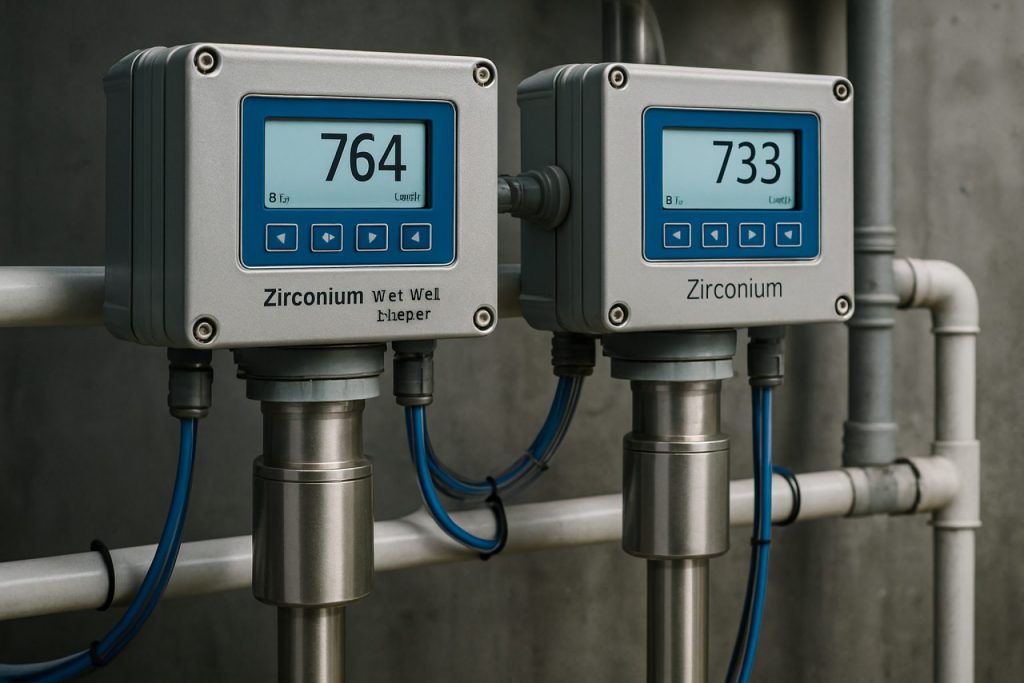
Table of Contents
- Executive Summary: Key Insights and 2025 Highlights
- Technology Overview: How Zirconium Wet-Well Analyzers Work
- Market Size & Growth Forecast: 2025–2030 Projections
- Leading Manufacturers and Industry Players
- Emerging Applications Across Sectors
- Comparative Analysis: Zirconium vs. Competing Analyzer Technologies
- Regulatory Trends and Compliance Landscape
- Innovation Pipeline: R&D and Next-Gen Features
- Regional Market Dynamics and Global Expansion
- Future Outlook: Opportunities, Challenges, and Strategic Recommendations
- Sources & References
Executive Summary: Key Insights and 2025 Highlights
Zirconium wet-well analyzers have emerged as a crucial technology for continuous oxygen measurement in harsh industrial settings, particularly in power generation, chemical manufacturing, and waste incineration. As of 2025, these analyzers are experiencing rising demand due to their robustness, real-time monitoring capability, and compliance support for tightening emissions regulations. Market activity in 2025 underscores the strategic investments by major manufacturers and utilities to upgrade legacy systems and prioritize operational efficiency.
Key industry players such as Emerson, Siemens, and ABB are at the forefront of technological advancements. Their latest zirconium-based analyzers offer enhanced sensor longevity, automatic calibration, and digital connectivity (including IIoT integration), addressing the needs of facilities seeking to minimize downtime and optimize combustion control. For example, ABB’s AZ100 zirconia oxygen analyzer now features improved wet-well compatibility and predictive maintenance diagnostics, allowing operators to preemptively address performance issues and reduce maintenance costs.
In 2025, new regulatory frameworks, especially in regions like the European Union and East Asia, are accelerating upgrades to wet-well oxygen analyzers. Stricter limits on NOx and CO emissions necessitate precise control over combustion processes, positioning zirconium wet-well analyzers as essential compliance tools. Utilities are prioritizing analyzer retrofits ahead of anticipated enforcement deadlines, while chemical and waste-incineration plants are standardizing on zirconium solutions for their reliability in high-moisture, high-temperature environments.
Industry data indicate that the average replacement cycle for wet-well oxygen analyzers is shortening from 12–15 years to around 8–10 years, driven by both regulatory mandates and rapid technological improvements. Additionally, digital service offerings—such as remote diagnostics and analytics dashboards—are becoming standard, as evidenced by product lines from Emerson and ABB. This digital shift is expected to further accelerate adoption through 2027, as facilities seek both compliance and operational intelligence.
Looking ahead, the zirconium wet-well analyzer sector is set for continued growth, with innovation focused on sensor durability, real-time data integration, and user-friendly interfaces. Industry stakeholders anticipate that the convergence of regulatory pressure and digital transformation will sustain strong demand, especially among utilities, waste incinerators, and large-scale chemical processors worldwide.
Technology Overview: How Zirconium Wet-Well Analyzers Work
Zirconium wet-well analyzers are advanced process instruments primarily used for real-time measurement of oxygen concentrations in liquid or wet gas environments, such as those found in power generation, chemical processing, and wastewater treatment facilities. Their core technology is based on the unique oxygen-ion conductivity of stabilized zirconium oxide (zirconia) when heated to elevated temperatures. The analyzers typically consist of a probe containing a zirconium oxide sensor, an internal reference (often ambient air), and associated electronics for signal processing and display.
In operation, the zirconium oxide element acts as a solid electrolyte between two electrodes, one exposed to the process sample and the other to the reference gas. When heated (often above 600°C), oxygen ions migrate through the zirconia in response to the difference in oxygen partial pressure across the sensor. This migration generates a voltage, as described by the Nernst equation, which is directly proportional to the logarithm of the oxygen concentration ratio between the process and reference sides. The analyzer’s electronics convert this voltage into a real-time oxygen concentration value, often displayed as a percentage.
Wet-well configurations are specifically engineered to function reliably in environments with high humidity, condensation, and possible contaminants. These analyzers incorporate features such as sensor heaters, protective coatings, and self-cleaning mechanisms to maintain sensor performance and longevity. Some recent models also include diagnostics to detect sensor degradation or process fouling, improving reliability and reducing maintenance interventions.
With the growing demand for tighter emissions control, process optimization, and energy efficiency, especially in sectors like power generation and incineration, zirconium wet-well analyzers are increasingly being deployed for continuous, in-situ monitoring. Industry leaders such as Yokogawa Electric Corporation and Siemens AG have introduced robust wet-well oxygen analyzers, featuring digital communication capabilities (such as HART and Modbus), modular design, and advanced self-diagnostics. These improvements facilitate integration into modern digital plant architectures, supporting predictive maintenance and remote monitoring.
Looking ahead to 2025 and beyond, the technology is expected to evolve further with enhanced sensor materials for greater resistance to chemical attack and fouling, miniaturization for easier installation in constrained spaces, and increased interoperability with plant automation systems. Additionally, compliance with new regulatory requirements for continuous emissions monitoring will likely drive further adoption and innovation in zirconium wet-well analyzer design and deployment, as evidenced by ongoing product development from major suppliers like ABB Group.
Market Size & Growth Forecast: 2025–2030 Projections
The market for zirconium wet-well analyzers is positioned for steady growth between 2025 and 2030, driven by ongoing industrial demand for improved process control in sectors such as power generation, chemical manufacturing, and wastewater treatment. These analyzers, which leverage the oxygen-sensitive properties of zirconium oxide sensors, are integral to optimizing combustion efficiency, reducing emissions, and ensuring operational safety in wet or saturated gas streams.
As of 2025, leading manufacturers are reporting a rise in adoption rates, underpinned by stricter global emissions standards and the modernization of legacy infrastructure. For instance, Emerson and AMETEK Process Instruments have both noted increased demand for their zirconium-based wet-well oxygen analyzers, especially in markets in North America, Europe, and parts of Asia-Pacific. The expansion of flue gas desulfurization (FGD) systems and the retrofitting of coal-fired and biomass power plants are significant market drivers.
Industry data from SICK AG suggests that the push towards decarbonization and the transition to alternative fuels will sustain growth, as operators require precise oxygen monitoring to optimize new combustion processes and comply with environmental regulations. Additionally, developing economies in Southeast Asia and Latin America are investing in advanced process analyzers to upgrade aging industrial assets and meet tightening air quality standards.
From a technology perspective, the 2025–2030 period is expected to see incremental improvements in sensor durability and self-diagnostic capabilities, reducing maintenance costs and downtime. Companies like Yokogawa Electric Corporation are actively developing next-generation analyzers with enhanced resistance to corrosive wet environments and real-time connectivity for remote monitoring, in line with broader trends in industrial digitalization.
Growth projections for the zirconium wet-well analyzer market indicate a moderate but sustained compound annual growth rate (CAGR) through 2030, with the strongest demand anticipated in regions investing heavily in environmental compliance and energy efficiency. The outlook remains positive, with established players focusing on product innovation and service expansion to capture emerging opportunities in both developed and developing markets.
Leading Manufacturers and Industry Players
The zirconium wet-well analyzer market is currently defined by a select group of established instrumentation manufacturers and process control specialists with decades of expertise in gas analysis and environmental monitoring. As of 2025, key industry players are focusing on advancing sensor longevity, measurement accuracy, and digital integration to address the growing demand for robust in-situ oxygen measurement solutions in sectors such as power generation, incineration, and chemical processing.
- Emerson Electric Co. remains a global leader with its Rosemount 6888 In Situ Oxygen Analyzer, utilizing zirconium oxide sensors to provide real-time oxygen level measurement in wet-well and combustion applications. In 2025, Emerson continues to enhance its devices with improved diagnostics and network connectivity, catering to digital transformation initiatives in utilities and industrial facilities.
- Siemens AG offers comprehensive process analytics solutions, including zirconium-based oxygen analyzers designed for wet-well installations. Siemens emphasizes modularity and lifecycle support, recently integrating advanced self-cleaning mechanisms to extend sensor life and reduce maintenance in harsh process environments.
- ABB Ltd. continues to innovate with its zirconia oxygen analyzers, targeting emission control and combustion optimization. ABB’s solutions feature field-replaceable sensors and seamless integration with distributed control systems (DCS), aligning with the industry’s push for predictive maintenance and process optimization.
- AMETEK Process Instruments is recognized for its OxyMitters, which employ zirconium oxide technology for continuous oxygen measurement in wet-well and flue gas streams. AMETEK is investing in ruggedization and diagnostic capabilities, reflecting the industry’s move towards analyzer reliability in challenging environments.
- Systech Illinois also offers a portfolio of oxygen analyzers, including zirconium sensor options, targeting both process and safety applications. The company is adopting Industry 4.0 principles by enabling remote monitoring and data logging, a trend expected to accelerate over the next few years.
Looking ahead, these manufacturers are expected to intensify R&D efforts in sensor materials and digital interfaces, responding to stricter environmental regulations and industry demand for higher process efficiency. Collaborations with automation providers and increased focus on analyzer lifecycle management will likely shape the competitive landscape through 2025 and beyond.
Emerging Applications Across Sectors
Zirconium wet-well analyzers are increasingly recognized for their robust performance in challenging process environments, particularly where accurate and real-time oxygen measurement is critical. By 2025, the adoption of these analyzers is expanding beyond their traditional bases in power generation and wastewater management, driven by advances in sensor durability and digital integration.
One emerging application is in the hydrogen economy, where stringent control of oxygen levels is essential for safety and process efficiency. Companies involved in electrolyzer manufacturing and hydrogen fuel infrastructure are evaluating zirconium-based analyzers for continuous wet-well monitoring, benefitting from their ability to operate reliably in humid, corrosive atmospheres. Siemens AG and Endress+Hauser have both highlighted increased demand from hydrogen production and storage facilities in their recent product literature.
In wastewater treatment, the push for energy optimization and tighter regulatory standards is driving wider implementation of zirconium wet-well analyzers. These analyzers are being integrated into advanced process control systems, enabling utilities to fine-tune aeration rates and reduce energy usage without compromising water quality. Hach Company reports that municipalities in Europe and North America are piloting next-generation zirconium probes with enhanced digital communication protocols for real-time data analytics and remote diagnostics.
Food and beverage industries represent another growth area, as manufacturers seek to minimize dissolved oxygen in fermentation and packaging processes to improve product stability and shelf life. Companies like Mettler-Toledo are adapting zirconium wet-well technology for Clean-in-Place (CIP) environments, emphasizing rapid response and chemical resistance.
Looking ahead, the integration of Internet of Things (IoT) connectivity and predictive maintenance algorithms is expected to further accelerate deployment across sectors. Industry leaders are investing in cloud-based platforms that aggregate analyzer data for fleet-wide health monitoring and process optimization. For example, ABB has outlined roadmaps for remote asset management and self-diagnosing zirconium analyzer modules. Given these trends, zirconium wet-well analyzers are poised to play a central role in industrial decarbonization, resource efficiency, and process safety initiatives through 2025 and beyond.
Comparative Analysis: Zirconium vs. Competing Analyzer Technologies
Zirconium wet-well analyzers remain a preferred technology for continuous oxygen measurement in challenging process environments, particularly in power generation and industrial combustion applications. As 2025 unfolds, comparative analysis between zirconium oxide-based analyzers and alternative sensor technologies—such as paramagnetic, electrochemical, and tunable diode laser (TDL) analyzers—highlights both enduring strengths and evolving limitations of each approach.
A core advantage of zirconium wet-well analyzers is their robust in-situ design, allowing them to operate reliably in high-temperature, high-particulate, and variable-moisture conditions. These analyzers utilize a solid-state zirconium oxide cell, which, when heated, becomes an oxygen ion conductor. This enables fast, direct measurement of oxygen concentration in process gas streams, often without the need for sample conditioning. Recent iterations, such as those from Yokogawa Electric Corporation and OMRON Corporation, emphasize enhanced sensor longevity and self-diagnostic capabilities, addressing historical concerns regarding sensor drift and maintenance requirements.
In contrast, paramagnetic analyzers, which exploit the paramagnetic properties of oxygen molecules, offer high linearity and accuracy at low oxygen concentrations. However, they are generally unsuitable for high-dust or high-temperature applications and typically require complex sample conditioning systems. Electrochemical sensors, while compact and cost-effective, tend to suffer from shorter operational lifespans and cross-sensitivity to interfering gases, making them less suitable for demanding wet-well environments. TDL analyzers, a newer entrant, provide high-selectivity and rapid response for oxygen and other gas measurements, particularly in clean gas streams. However, their initial capital costs and sensitivity to window fouling in wet or particulate environments currently limit broader adoption for in-situ wet-well monitoring.
- Maintenance & Reliability: Zirconium analyzers, such as ABB’s ZFG2 series, are engineered for minimal maintenance, with advanced self-cleaning and calibration features introduced in recent updates. This is a distinct edge over electrochemical sensors, which often require frequent cell replacement.
- Cost & Lifecycle: While initial investment for zirconium wet-well analyzers remains higher than basic electrochemical options, the total cost of ownership is mitigated by longer service intervals and reduced downtime. Competing technologies such as TDLs may surpass zirconium in specific clean gas scenarios but face cost and technical barriers in wet-well environments.
- Regulatory & Industry Trends: As industries confront tighter emissions regulations and prioritize process optimization, demand for robust, low-maintenance in-situ analyzers is projected to grow. Manufacturers like Siemens AG are focusing R&D on improving sensor durability and digital integration, signaling continued innovation in the zirconium segment through at least 2027.
Overall, while emerging technologies are gaining ground in select applications, zirconium wet-well analyzers are expected to maintain a significant share of the process oxygen analysis market, especially where process conditions remain challenging and operational reliability is paramount.
Regulatory Trends and Compliance Landscape
The regulatory landscape for zirconium wet-well analyzers in 2025 is shaped by increasingly stringent environmental and industrial process standards, driving both technological advancements and compliance requirements. These analyzers, primarily used for in-situ oxygen measurement in combustion and process applications, are critical for ensuring emissions are within permissible limits, especially in power generation, petrochemical, and waste-to-energy sectors.
A primary driver of regulatory focus is the enforcement of tighter emission controls on NOx, CO, and particulate matter, as dictated by frameworks such as the European Union’s Industrial Emissions Directive (IED) and the U.S. Environmental Protection Agency’s (EPA) Clean Air Act regulations. Such regulations necessitate real-time, accurate monitoring of oxygen concentrations in flue gases, a function for which zirconium oxide-based wet-well analyzers are well-suited due to their robustness and precise measurement capabilities even under challenging, moist conditions (Emerson).
In 2025, manufacturers are responding by enhancing the durability and self-diagnostic capabilities of wet-well zirconium analyzers to meet compliance demands. For instance, companies like Siemens AG and Yokogawa Electric Corporation have introduced models with improved sensor longevity, automated calibration routines, and digital communication protocols compatible with modern plant control systems. These features not only align with regulatory requirements for continuous emissions monitoring systems (CEMS), but also facilitate auditability and data integrity, which are increasingly scrutinized during environmental compliance inspections.
International standards such as ISO 12039:2019, which sets procedures for the measurement of oxygen in exhaust gases using zirconia sensors, are being referenced with greater frequency in regulatory documentation. Regulatory agencies are pushing for analyzer designs that incorporate features to prevent measurement drift and ensure rapid fault detection, thereby reducing the risk of non-compliance and associated penalties.
Looking ahead, the compliance landscape will likely see further evolution as digitalization and remote monitoring become more entrenched. Regulators are expected to mandate even higher data transparency and cybersecure communication links for analyzer networks. Manufacturers, in turn, are expanding remote diagnostics and predictive maintenance services to support operators in maintaining uninterrupted compliance (ABB).
In summary, the next several years will see zirconium wet-well analyzers at the forefront of regulatory compliance efforts, with technology and standards evolving in tandem to ensure industrial emissions remain within permissible thresholds and data reporting is robust, auditable, and secure.
Innovation Pipeline: R&D and Next-Gen Features
Zirconium wet-well analyzers, integral to precise oxygen measurement in challenging industrial environments, are experiencing a significant innovation drive as we enter 2025. Traditionally deployed in power generation, chemical processing, and wastewater treatment, these analyzers utilize robust zirconium oxide sensors to deliver reliable, real-time oxygen readings—even in high-moisture, corrosive, or particulate-laden process streams.
Recent research and development efforts are focused on enhancing both the durability and intelligence of these analyzers. Manufacturers such as Yokogawa Electric Corporation have introduced new sensor coatings and internal heater designs, extending operational lifespans and reducing calibration drift even under severe wet-well conditions. In parallel, Endress+Hauser is leveraging advanced ceramics and electronics to offer faster response times, improved sensitivity, and self-diagnosis capabilities that minimize downtime and maintenance intervention.
A major trend in the 2025 innovation pipeline is the integration of digital connectivity and analytics. Companies like Siemens AG have embedded Industrial Internet of Things (IIoT) readiness into their zirconium analyzers, enabling remote monitoring, predictive maintenance, and seamless data exchange with plant automation systems. Cloud-based diagnostics are expected to become standard within the next few years, allowing plant operators to access analyzer performance data and receive automated alerts for sensor degradation or process anomalies.
Additionally, sustainability and regulatory compliance are shaping next-generation feature sets. Enhanced analyzers are being designed to operate reliably with lower energy consumption and to meet stricter emissions controls in industries such as waste incineration and flue gas treatment. AMETEK Process Instruments has highlighted ongoing R&D into modular analyzer platforms that can be easily reconfigured or expanded to accommodate evolving process requirements and tighter environmental standards.
Looking ahead, the outlook for zirconium wet-well analyzers is marked by continued miniaturization, extended service intervals, and broader application suitability—including deployment in decentralized and remote facilities. With ongoing collaboration between sensor developers, automation providers, and end-users, 2025 is set to see the rollout of smarter, more adaptive analyzers that support both operational excellence and sustainability targets across critical process industries.
Regional Market Dynamics and Global Expansion
The market for zirconium wet-well analyzers is witnessing significant regional shifts and global expansion as industries emphasize process efficiency, environmental compliance, and advanced material monitoring. In 2025, North America and Western Europe remain leading adopters, driven by stringent regulatory frameworks governing water quality and emissions in power generation, chemical processing, and wastewater management. In the United States, the demand for robust, low-maintenance gas analysis instruments, including zirconium oxide-based analyzers for in-situ oxygen measurement, continues to drive investment, notably in energy and utilities sectors. Major players like Emerson Electric Co. and Siemens AG report increased deployment of zirconium wet-well analyzers in municipal and industrial applications, attributing growth to digital integration and predictive maintenance capabilities.
Asia-Pacific is emerging as the fastest-growing regional market, propelled by rapid industrialization, urban expansion, and tightening environmental standards, particularly in China, India, and Southeast Asian economies. Local governments’ initiatives to upgrade water treatment infrastructure and reduce industrial emissions are fueling demand for advanced analyzer technologies. Yokogawa Electric Corporation has expanded its presence in Asia through partnerships and localized manufacturing, supporting real-time process optimization for regional end-users. Furthermore, the integration of smart analyzer systems with industrial IoT platforms is boosting adoption in high-growth sectors such as petrochemicals and pharmaceuticals.
In Latin America and the Middle East, market growth is more moderate but picking up, spurred by infrastructural upgrades and increased investment in oil and gas processing. Regional utilities and process industries are beginning to replace legacy systems with new-generation zirconium analyzers that offer enhanced reliability in challenging wet-well environments. Companies like ABB Ltd. are targeting these markets with tailored solutions, including ruggedized designs for high-humidity and corrosive conditions.
Looking forward, the global outlook for zirconium wet-well analyzers is positive. Manufacturers are investing in R&D to deliver analyzers with improved accuracy, wireless connectivity, and lower total cost of ownership. Decarbonization efforts, stricter pollution controls, and digital transformation across process industries are expected to sustain strong demand through the late 2020s. As regional markets mature and harmonize regulations, leading suppliers are expanding distribution networks and enhancing support services, laying the groundwork for continued global expansion and technological innovation in zirconium wet-well analysis.
Future Outlook: Opportunities, Challenges, and Strategic Recommendations
The outlook for zirconium wet-well analyzers in 2025 and the coming years is shaped by evolving regulatory demands, technological advancements, and industry-specific operational needs. These analyzers, primarily deployed in power generation, petrochemical, and wastewater treatment sectors, are gaining traction for their robustness, selectivity, and suitability for harsh wet-well environments.
Opportunities arise from tightening environmental regulations and the ongoing push for process optimization. Power plants and industrial facilities are under increasing pressure to demonstrate precise control of oxygen and other critical parameters in wet-well systems, driving demand for advanced sensor technologies. Zirconium oxide-based sensors, known for their fast response and resilience, are expected to see broader adoption as facilities seek reliable real-time monitoring solutions. For example, ABB and Siemens continue to develop wet-well analyzers that integrate seamlessly with digital plant architectures, offering predictive maintenance and improved data analytics capabilities.
Another opportunity lies in the global shift toward digitization and automation. Integration of zirconium wet-well analyzers with industrial IoT platforms enables remote diagnostics, centralized monitoring, and enhanced reporting, which are increasingly valued by operators seeking to minimize downtime and labor costs. Companies such as Endress+Hauser are actively expanding their portfolio to support smart plant initiatives, reflecting a broader trend towards connected measurement devices.
Challenges include the need for ongoing calibration and maintenance in the demanding conditions typical of wet-well installations. Fouling, sensor drift, and exposure to aggressive chemicals can affect sensor longevity and accuracy, prompting suppliers to focus on self-cleaning designs and advanced diagnostics. Additionally, the relatively higher upfront cost of zirconium analyzers compared to traditional technologies may slow adoption in budget-constrained segments, necessitating clear demonstrations of long-term cost savings and reliability.
Looking forward, strategic recommendations for industry stakeholders include investing in R&D for sensor robustness and miniaturization, partnering with automation providers to ensure seamless integration, and prioritizing customer training and support to maximize system uptime. As regulatory scrutiny intensifies and industrial processes become more data-driven, suppliers that deliver both technical innovation and lifecycle value are likely to capture significant market share.
Overall, the future of zirconium wet-well analyzers appears promising, with opportunities linked closely to digital transformation, regulatory compliance, and the ongoing drive for operational excellence in complex industrial environments.